

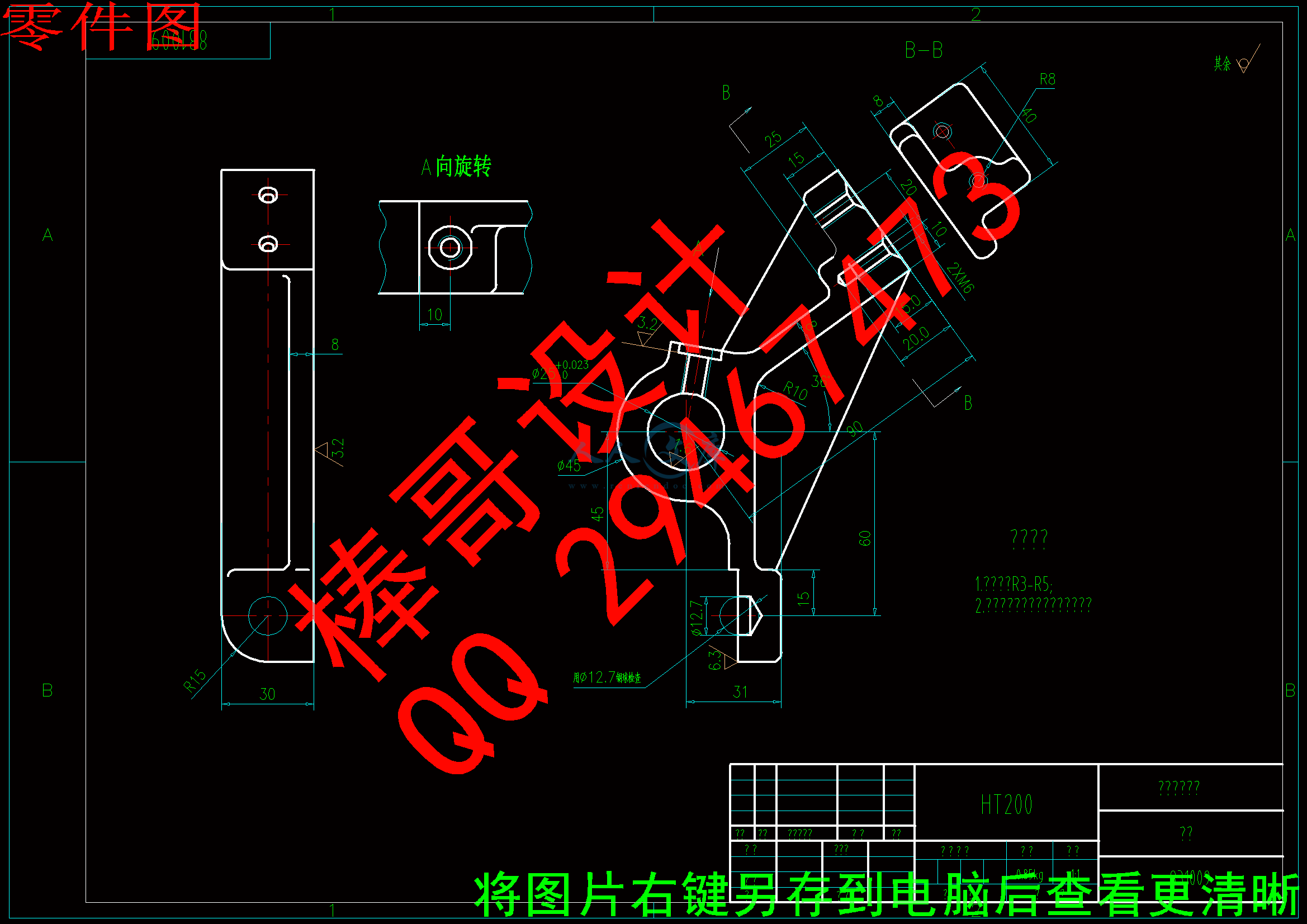
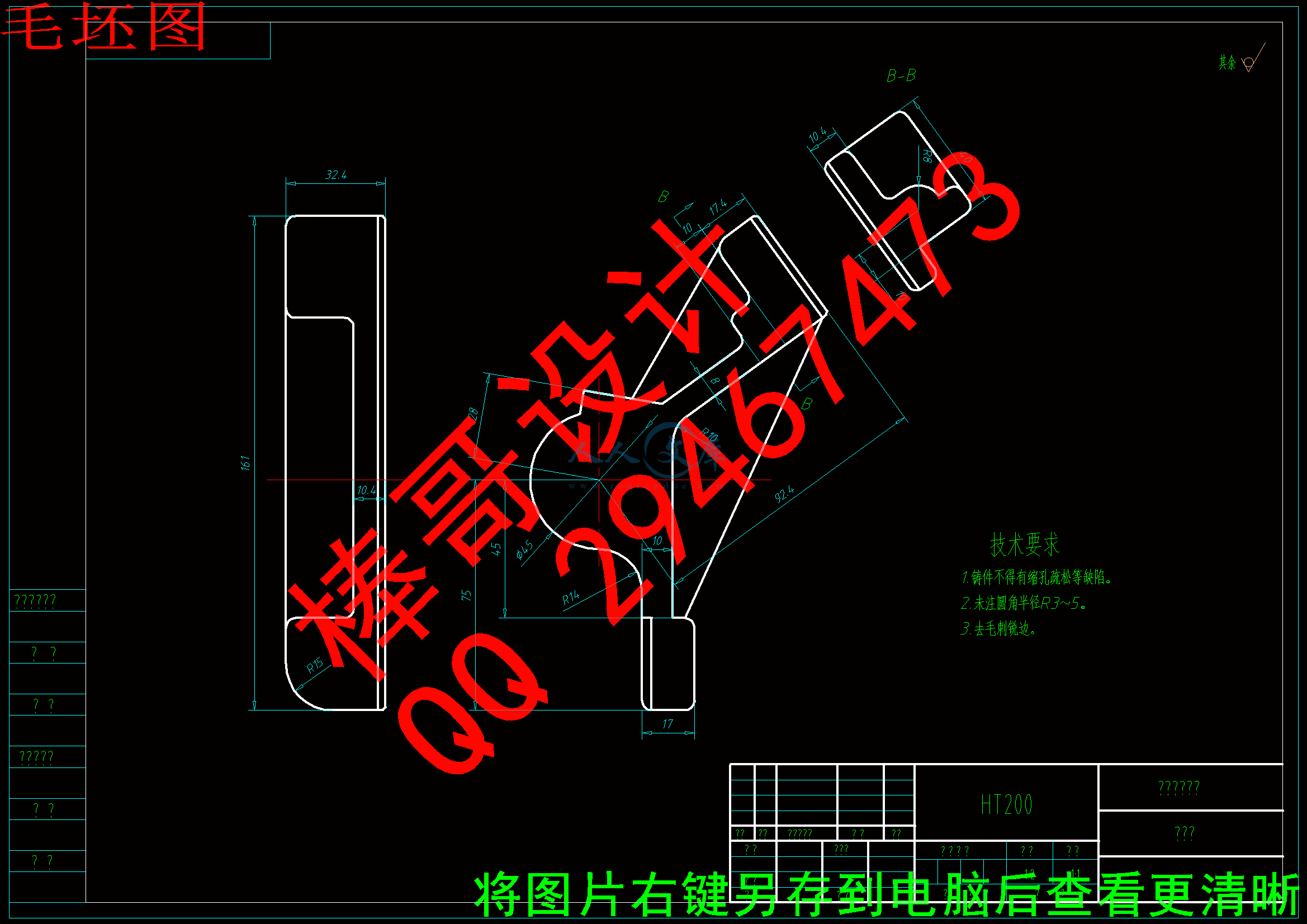

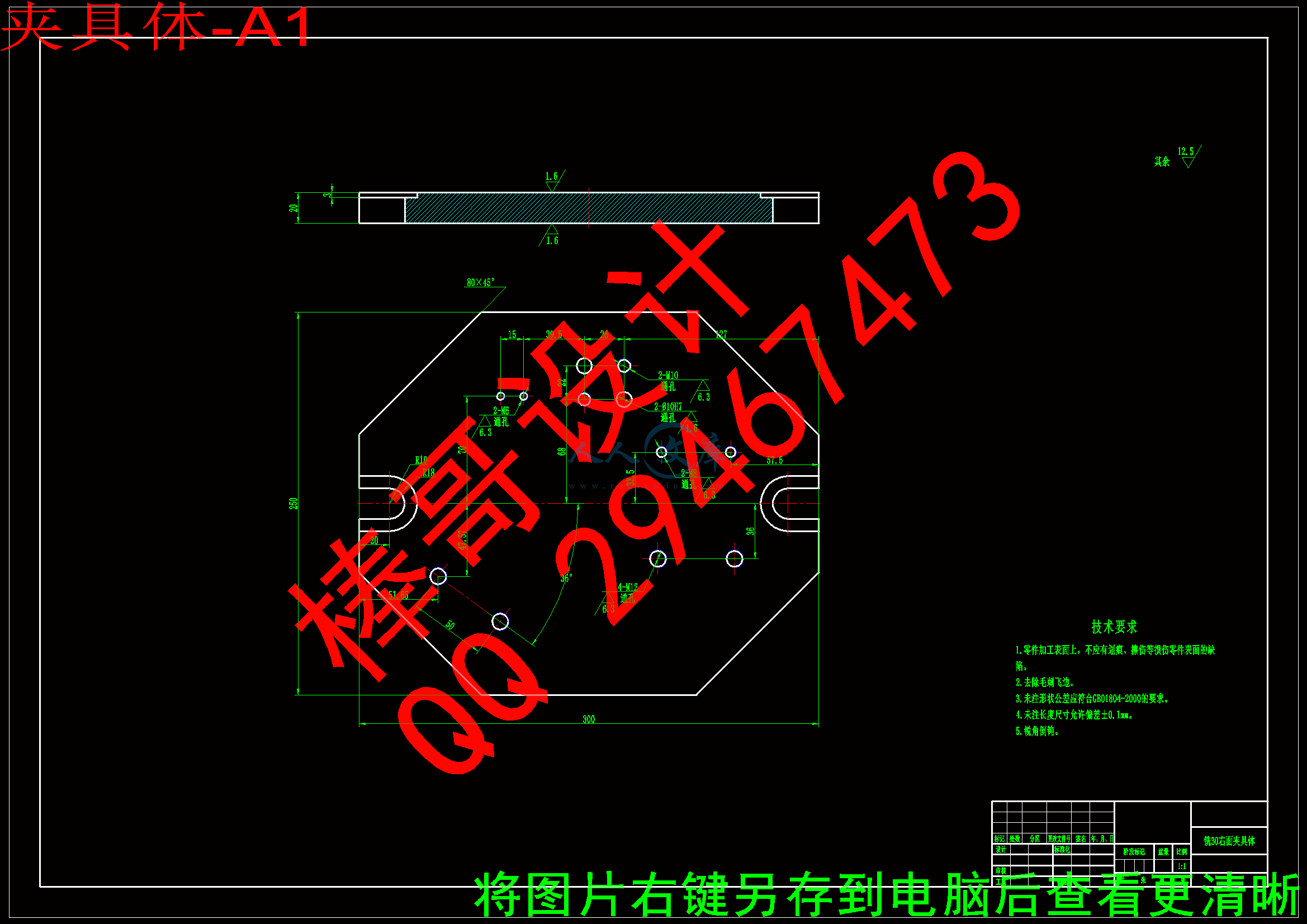
棒哥设计QQ 29467473
第1章 绪论
通过机床工艺及夹具设计,汇总所学专业知识如一体(如《公差于配合》、《机械零件设计》、《金属切削机床》、《机械制造工艺》等)。让我们对所学的专业课得以巩固、复习及实用,在理论与实践上有机结合;使我们对各科的作用更加深刻的熟悉与理解,并为以后的实际工作奠定坚实的基础!
本次设计是在我们学完了大学的全部基础课,技术基础课以及专业课之后进行的。这是我们在进行毕业设计之前对所学的各课程的一次深入的综合性的总复习,也是一次理论联系实际的训练。因此,它在我们四年的大学生活中占有重要的地位。因此,它在我们的大学生活中占有重要的地位。另外在做完这次毕业设计之后,我得到一次在毕业工作前的综合性训练,我在想我能在下面几方面得到锻炼:
(1)运用机械制造工艺学课程中的基本理论以及在生产实习中学到的实践知识,正确地解决一个零件在加工中的定位,夹紧以及工艺路线安排,工艺尺寸确定等问题,保证零件的加工质量。
(2)提高结构设计能力。通过设计夹具的训练,获得根据被加工零件的加工要求,设计出高效,省力,经济合理而能保证加工质量的夹具的能力。
(3)学会使用手册以及图表资料。掌握与本设计有关的各种资料的名称,出处,能够做到熟练的运用。
在些次设计中我们主要是设计CA6140杠杆的铣床夹具。在此次课程设计过程中,我小组成员齐心协力、共同努力完成了此项设计。在此期间查阅了大量的书籍,并且得到了有关老师的指点,尤其是我系郑陪文老师的大力帮助,在此表示感谢!
第2章 设计的目的
机械制造工艺学课程设计,是在学完机械制造工艺学及夹具设计原理课程,经过生产实习取得感性知识后进行的一项教学环节;在老师的指导下,要求在设计中能初步学会综合运用以前所学过的全部课程,并且独立完成的一项工程基本训练。同时,也为以后搞好毕业设计打下良好基础。通过课程设计达到以下目的:
1、能熟练的运用机械制造工艺学的基本理论和夹具设计原理的知识,正确地解决一个零件在加工中的定位,夹紧以及合理制订工艺规程等问题的方法,培养学生分析问题和解决问题的能力。
2、通过对零件某道工序的夹具设计,学会工艺装备设计的一般方法。通过学生亲手设计夹具(或量具)的训练,提高结构设计的能力。
3、课程设计过程也是理论联系实际的过程,并学会使用手册、查询相关资料等,增强学生解决工程实际问题的独立工作能力。
第3章 零件的分析
3.1 零件的作用
题目给出的零件是CA6140的杠杆。它的主要的作用是用来支承、固定的。它位于车床制动机构中,主要起制动作用。杠杆一端与制动带连接,另一端通过刚球与齿条轴的凸起(或凹槽)相接触,当离合器脱开时,齿条轴与杠杆下端接触,是起逆时针方向摆动,将制动带拉紧;当左右离合器中任一个接合时,杠杆都顺时针方向摆动,使制动带放松,从而达到制动的目的。要求零件的配合是符合要求。
3.2 零件的工艺分析
所加工零件立体图,零件图如下图所视图,
从零件图上可以看出,主要加工表面可以分为四个部分。
1.Ф25mm的圆柱内表面,加工时要保证Ф25 + 00.023的0.023公差要求,以及表面粗糙度Ra1.6,表面要求较高。
2.连杆的支撑底板底面,粗糙度要求Ra3.2,同时保证连杆的高度30mm。
3.连杆上端面及下端侧面;上端面40×30mm,粗糙度要求Ra3.2,同时保证与Ф25mm的圆柱轴线的距离90mm;下端侧面保证尺寸17mm,粗糙度要求Ra6.3;离Ф25mm的圆柱轴线45mm的侧面粗糙度要求Ra12.5。
4.钻孔及攻螺纹孔;上端面2×M6,保证尺寸10mm、20mm,沉头锥角120°,粗糙度要求Ra6.3;M8的螺纹孔,锪Ф14×3mm的圆柱孔,粗糙度Ra3.2;钻下端Ф12.7 + 00.1的锥孔,保证公差要求,以及中心线与Ф25mm的圆柱轴线的距离60 mm粗糙度要求Ra6.3。
根据各加工方法的经济精度及一般机床所能达到的位置精度,该零件没有很难加工的表面,上述各表面的技术要求采用常规加工工艺均可以保证。
杠杆的Φ25孔的轴线合两个端面有着垂直度的要求。现分述如下:
本夹具用于在立式铣床上加工杠杆的小平面和加工Φ12.7。工件以Φ250+0.023 孔及端面和水平面底为定位基准,在长销、支承板和支承钉上实现完全定位。加工表面。包括粗精铣宽度为30mm的下平台、钻Ф12.7的锥孔 ,由于30mm的下平台的表面、孔表面粗糙度都为Ra6.3um。其中主要的加工表面是孔Ф12.7,要用Ф12.7钢球检查。
第4章 工艺规程的设计
4.1 确定毛坯的制造形式。
零件的材料HT200。考虑到零件在工作中处于润滑状态,采用润滑效果较好的铸铁。由于年产量为4000件,达到大批生产的水平,而且零件的轮廓尺寸不大,铸造表面质量的要求高,故可采用铸造质量稳定的,适合大批生产的金属模铸造。又由于零件的对称特性,故采取两件铸造在一起的方法,便于铸造和加工工艺过程,而且还可以提高生产率。
4.2 基面的选择
粗基准的选择。对于本零件而言,按照粗基准的选择原则,选择本零件的不加工表面是加强肋所在的肩台的表面作为加工的粗基准,可用装夹对肩台进行加紧,利用一组V形块支承Φ45轴的外轮廓作主要定位,以消除z、z、y、y四个自由度。再以一面定位消除x、x两个自由度,达到完全定位,就可加工Φ25的孔。
精基准的选择。主要考虑到基准重合的问题,和便于装夹,采用Φ25的孔作为精基准。
4.3 确定工艺路线
1、工艺路线方案一:
工序1 钻孔使尺寸到达Ф25mm
工序2粗精铣宽度为30mm的下平台
工序3钻Ф12.7的锥孔
工序4钻Ф14孔,加工螺纹孔M8
工序5钻Ф16孔,加工螺纹孔M6
工序6粗精铣Φ16、M6上端面
工序7 检查
2、工艺路线方案二:
工序1 钻孔使尺寸到达Ф25mm
工序2粗精铣宽度为30mm的下平台
工序3钻Ф12.7的锥孔
工序4粗精铣Φ16、M6上端面
工序5钻Ф16孔,加工螺纹孔M6
工序6钻Ф14孔,加工螺纹孔M8
工序7 检查
3、工艺路线的比较与分析
第二条工艺路线不同于第一条是将“工序4钻Ф14孔,再加工螺纹孔M8”变为“工序6粗精铣Φ16、M6上端面”其它的先后顺序均没变化。通过分析发现这样的变动影响生产效率。而对于零件的尺寸精度和位置精度都没有太大程度的帮助。
以Ф25mm的孔子外轮廓为精基准,先铣下端面。再钻锥孔,从而保证了两孔中心线的尺寸与右端面的垂直度。符合先加工面再钻孔的原则。若选第二条工艺路线而先上端面, 再“钻Ф14孔,加工螺纹孔M8”不便于装夹,并且毛坯的端面与轴的轴线是否垂直决定了钻出来的孔的轴线与轴的轴线是非功过否重合这个问题。所以发现第二条工艺路线并不可行。
从提高效率和保证精度这两个前提下,发现第一个方案也比较合理想。所以我决定以第一个方案进行生产。
工序1 加工孔Φ25。扩孔Φ25的毛坯到Φ20。扩孔Φ20到Φ250+0.023 , 保证粗糙度是1.6采立式钻床Z535。
工序2 粗精铣宽度为30mm的下平台,仍然采用立式铣床X5032 用组合夹具。
工序3 钻Ф12.7的锥孔,采用立式钻床Z535,为保证加工的孔的位置度,采用专用夹具。
工序4 钻Ф14孔,加工螺纹孔M8。用回转分度仪组合夹具,保证与垂直方向成10゜。
工序5 钻Φ5、加工M6上端面用立式钻床Z535,为保证加工的孔的位置度,采用专用夹具
工序6 粗精铣Φ5、M6上端面。用回转分度仪加工,粗精铣与水平成
36゜的台肩。用卧式铣床X63,使用组合夹具。
工序7 检查
4.4机械加工余量、工序尺寸及毛坯尺寸的确定
杠杆的材料是HT200,毛坯的重量0.85kg,生产类型为大批生产,。
由于毛坯用采用金属模铸造, 毛坯尺寸的确定;
由于毛坯及以后各道工序或工步的加工都有加工公差,因此所规定的加工余量其实只是名义上的加工余量,实际上加工余量有最大加工余量及最小加工余量之分。
由于本设计规定有零件为大批量生产,应该采用调整法加工,因此计算最大与最小余量时应按调整法加工方式予以确定。
毛坯与零件不同的尺寸有:(具体见零件图与毛坯图)故台阶已被铸出,根据《机械制造工艺设计简明手册》的铣刀类型及尺寸可知选用6mm的铣刀进行粗加工,半精铣与精铣的加工余量都为0.5mm。
1.Φ25的端面考虑2mm,粗加工1.9m到金属模铸造的质量,和表面的粗糙度要求,精加工0.1mm,同理上下端面的加工余量都是2mm。
2.对Φ25的内表面加工。由于内表面有粗糙度要求1.6
可用一次粗加工1.9mm,一次精加工0.1mm就可达到要求。。
3.钻锥孔Φ12.7时要求加工一半,留下的装配时钻铰,为提高生产率起见,仍然采用Φ12的钻头,切削深度是2.5mm。
4.用铣削的方法加工台肩。由于台肩的加工表面有粗糙度的要求6.3,而铣削的精度可以满足,故采取分四次的铣削的方式,每次铣削的深度是2.5mm。
4.5 确定切削用量和基本工时
工序一:
1 钻孔。加工零件的中心孔,使其达到指定的尺寸要求
加工中心孔到Φ250+0.023 (先钻孔到Φ25在加工扩孔到Φ250+0.023)
工件材料:HT200 ,金属模铸造
加工要求:扩孔的加工精度是1.6。
机床:立式钻床,Z535
刀具:选用Φ22mm的标准高速钢麻花钻
计算钻削用量、
确定进给量f 根据表3.41可查出=(0.47-0.57),由于孔深和孔径之比L/d0 =30/22. k1f =1.0不用加上安全修正系数。故查立式钻床Z535,取f=0.53mm/r。根据表3.4-3,钻头强度所允许的进给量=1.75mm/r。机床进给机构允许的轴向力=15690N(由机床说明书查处),根据表3.4-4,允许的进给量 1.8mm/r。
由于所选择的进给量=0.53mm/r 远小于和,所以所选用的进给量是可以使用的。
确定切削速度v
根据所给出的条件按照表3.4-8和表3.4-10进行计算,直接按照表3.4-15可以查出相应的值
v=17m/min F=4732N T=51.69Nm P m=1.25KW
由于实际加工条件与上表所给的条件不是完全一样的,故应该对结果进行修正。由表3.4-9知,切削速度的修正系数=0.88
=0.75,故=17m/min0.880.75=11.22mm/min
查Z535型机床说明书,n=195r/min 那么实际切削速度为
由表3.4-11,切削力及转矩的休整系数是=1.06,故F=47321.06=5016N
检验机床的功率
切削功率为
机床有效功率为
由于,故所选的切削用量是可以的,既
相应的F=5016N ,T=54.8NM ,
2.扩孔
扩孔选择=24.5mm标准高速刚扩孔钻头。
确定扩孔进给量
根据表3.4-5,取=(0.7-0.8)0.7mm/r=0.9-0.56mm/r。
根据Z535型机床说明书,取=0.57mm/r 。
确定切削速度及
根据表3.4-34,取=25mm/min
由于切削条件跟上表有不同,切削速度尚需要乘以下修正系数
故
根据Z535 机型说明书,取n=275r/min ,实际扩孔速度
3.铰孔
1)铰刀
选用25mm 标准高速钢铰刀
确定铰孔切削用量
确定进给量根据表3.4-6查出,=1.3-2.6mm,按照该表注4,进给量取小值。
按照Z535型机床说明书,取=1.6mm/r
切削速度和n根据表3.4-40,取=8.2m/min 。
切削速度修正系数由表3.4-9查出
故
根据Z535型机床说明书,取n=100r/min ,实际铰孔速度
各个工序实际切削用量
根据以上计算,各工序切削用量如下:
钻孔:
扩孔:
铰孔:
工序二:
粗精铣宽度为30mm的下平台
1、工件材料:HT200,金属模铸造
加工要求:粗铣宽度为30mm的下平台,精铣宽度为30mm的下平台达到粗糙度3.2。
机床:X50322立式铣床
刀具:高速钢镶齿式面铣刀Φ225(z=20)
2、计算切削用量
粗铣宽度为30mm的下平台
以知条件:工件的形状如毛胚所市,工件为HT200铸造件,硬度180HBW,有外皮,用X50322立式铣床进行加工,机床的功率是7。5KW:所用的刀具是高速钢镶齿式面铣刀Φ225(z=20),试确定切削用量。
铣刀直径 根据机械加工工艺手册表2.1-32以及面铣刀标准GB/T 5342-1985, 选择铣刀直径 =225mm 齿数Z= 20
铣削用量
背吃刀量:由于加工余量为2m m故在一次走刀内切完,取=2mm
确定每齿的进给量:
根据机械加工工艺手册表2.1-73.得到每齿的进给量=0.20 – 0.29mm/齿 ,采用对称铣削。取=0.2mm。
确定铣削速度 及铣削功率
根据机械加工工艺手册表2.1-75和表2.1-76,铣刀后面最大磨损限度为2mm ,刀具寿命T=120min 。
根据给定的条件,查机械加工工艺手册表2.1-87得到
根据表中的数据可以得到:
给定的材料硬度是190HBW,铣削的宽度是 ;实际的工件的硬度是180HBW,实际的铣削的宽度是
根据机械加工工艺手册表2.1-79查出修正系数
考虑修正系数后的铣削速度
计算出刀具转速及进给速度
=
根据X5032型立式铣床说明书取
校验机床的功率 根据工作条件和选择的机床的条件经过计算和比较结果
数值大于加工工艺过程要求的功率,故所选用的机床X5032立式铣床是符合加工要求的。
4) 基本功时:1.58min
工序3 钻Ф12.7的锥孔
1、工件材料:HT200,金属模铸造,
加工要求:铣孔内表面,无粗糙度要求。机床:X5032立式铣床
刀具:高速钢钻头
2、计算切削用量
用Φ11扩孔Φ12.7的内表面。根据《切削手册》进给量f=0.64mm/z,切削速度0.193m/s,切削深度是1.5mm,机床主轴转速为195r/min。走刀长度是36mm。
基本工时:t1=2×36/(0.64×195)=0.58 min.
用Φ12扩孔Φ12.7的内表面。根据《切削手册》进给量f=0.64mm/z,切削速度0.204m/s,切削深度是0.5mm,机床主轴转速为195r/min。走刀长度是36mm。
基本工时:t2=2×36/(0.64×195)=0.58 min.
第四工序基本工时:t=t1+t2=1.16min.
工序4
1.钻孔
钻头:选择14的高速钢钻头,和6的标准高速钢钻头
确定钻削用量(大孔)
确定进给量根据机械加工工艺手册表3.4-1查处=0.61-0.75
根据孔深和孔的直径的比值=3/14=0.214
有表格给定的数值可的比值3,不有加修正系数
=0.61-0.75mm/r
根据机械加工工艺手册表3.4-3,钻头强度所允许的进给量=1.25mm/r.机床进给机构所允许的轴向力
根据机械加工工艺手册表3.4-4,允许的进给量1.8mm/r
由于所选择的进给量远小于和,故所选择的进给量是可用的。
确定切削速度
查机械加工工艺手册表3.4-8和表3.4-10可以直接找出相应的
=14mm/min根据机床说明书,N=195r/min
那么实际的切削速度是
基本功时:
t=L/fn=0.35min
(3)确定钻削用量(小孔)
1)确定进给量根据机械加工工艺手册表3.4-1可查出=0.36-0.44mm/r,由于孔深和孔直径的比值=12.5/6=2.083
所以不有加修正系数
根据机械加工工艺手册表3.4-3,钻头所允许的最大进给量
=0.72mm/r,机床进给机构所允许的最到轴向力根据机械加工工艺手册表3.4-4,允许的最大进给量1.8mm/r
由于所选择的进给量远小于和,故所选择的进给量是可用的。
确定切削速度
根据机械加工工艺手册,表3.4-15可以直接查速度
=12m/min
查Z535机床说明书,取n=195r/min,那么实际的切削速度
确定基本功时:t=L/fn=0.89min
加工此处的总的功时:
2.加工螺纹
因为螺纹孔为为细牙螺纹,所以螺纹孔加工到
(1)钻头选用mm标准高速钢麻花钻,磨出双锥和修磨横刀
(2)确定钻削用量
1)确定进给量,根据表3.4-1可查出,选用立式钻床Z5125A,取进给量为=0.20mm/r
根据表3.4-3,钻头强度所允许的进给量=0.78mm/r。
机床进给机构允许的轴向力=9000N
根据表3.4-4允许的进给量>1.9mm/r
由于所选择的进给量远小于及,故所选可用
确定切削速度v,轴向力F,转矩T以及切削功率,用不同刀具材料进行钻,扩,铰空的v,F,T,均可以按表3.4-8及表3.4-10进行计算。根据所给条件,可直接在表3.4-15中用插入法计算得:v=15m/min,F=3010N,T=10.03,=0.51kw,由于实际加工条件与上表所给条件不完全相同,故应对结果进行修正,由表3.4-9知,切削速度的修正系数
故
取N=375r/min.则实际切削速度v为
由表3.4-11,切削力及转矩的修正系数
故
校验机床功率
切削功率为
kw
机床有效功率为
因为>.故选择的切削用量可用
即
选用的细长柄机用丝锥,工件材料中碳钢,前角,后角,主偏角
选用切削速度
根据表7.2-13查得mm/min,选择v=10m/min
(3)扭矩的确定
根据表7.2-12得
查机械加工工艺手册表7.2-12
得,
(4)攻螺纹时的转速
r/min
取n=400r/min
m/min
选择丝锥退出时的转速为450r/min
基本时间的确定
==15.27s
式中 - 工件螺纹长度(mm)
- 丝锥切削锥长度(mm)
- 攻螺纹时的超切量,取=(2-3);
- 攻丝纹时的转速(r/min)
- 丝锥退出时的转速(r/mm )
- 工件螺纹距(mm )
工序5 钻Φ5、加工M6上端面用立式钻床Z535,为保证加工的孔的位置度,采用专用夹具
1.钻孔
钻头:选择5的高速钢钻头
1.确定钻削用量(通孔)
确定进给量根据机械加工工艺手册表3.4-1查处=0.14-0.18
根据孔深和孔的直径的比值=15/5=3.0
有表格给定的数值可的比值=3,不有加修正系数
=0.14-0.18 mm/r
根据机械加工工艺手册表3.4-3,钻头强度所允许的进给量=0.27mm/r.机床进给机构所允许的轴向力
根据机械加工工艺手册表3.4-4,允许的进给量1.8mm/r
由于所选择的进给量远小于和,故所选择的进给量是可用的。
确定切削速度
查机械加工工艺手册表3.4-8和表3.4-10可以直接找出相应的
=15mm/min根据机床说明书,N=195r/min
那么实际的切削速度是
3)基本功时:
t=L/fn=0.29min
2.确定钻削用量(盲孔)
1)确定进给量根据机械加工工艺手册表3.4-1可查出=0.18-0.22mm/r,由于孔深和孔直径的比值=20/6=3.33
所以有加修正系数
=(0.18-0.22)0.9=0.162-0.198mm/r
根据机械加工工艺手册表3.4-3,钻头所允许的最大进给量
=0.27mm/r,机床进给机构所允许的最到轴向力根据机械加工工艺手册表3.4-4,允许的最大进给量1.8mm/r
由于所选择的进给量远小于和,故所选择的进给量是可用的。
确定切削速度
根据机械加工工艺手册,表3.4-15可以直接查速度
=23m/min
查Z535机床说明书,取n=195r/min,那么实际的切削速度
确定基本功时:t=L/fn=0.38min
加工此处的总的功时:
2.加工螺纹
因为螺纹孔为为细牙螺纹,所以螺纹孔加工到
(1)钻头选用mm标准高速钢麻花钻,磨出双锥和修磨横刀
(2)确定钻削用量
1)确定进给量,根据表3.4-1可查出,选用立式钻床Z5125A,取进给量为=0.16mm/r
根据表3.4-3,钻头强度所允许的进给量=0.78mm/r。
机床进给机构允许的轴向力=9000N
根据表3.4-4允许的进给量>1.9mm/r
由于所选择的进给量远小于及,故所选可用
确定切削速度v,轴向力F,转矩T以及切削功率,用不同刀具材料进行钻,扩,铰空的v,F,T,均可以按表3.4-8及表3.4-10进行计算。根据所给条件,可直接在表3.4-15中用插入法计算得:v=15m/min,F=3010N,T=10.03,=0.51kw,由于实际加工条件与上表所给条件不完全相同,故应对结果进行修正,由表3.4-9知,切削速度的修正系数
故
取N=375r/min.则实际切削速度v为
由表3.4-11,切削力及转矩的修正系数
故
校验机床功率
切削功率为
kw
机床有效功率为
因为>.故选择的切削用量可用
即
选用的细长柄机用丝锥,工件材料中碳钢,前角,后角,主偏角
选用切削速度
根据表7.2-13查得mm/min,选择v=10m/min
(3)扭矩的确定
根据表7.2-12得
查机械加工工艺手册表7.2-12
得,
(4)攻螺纹时的转速
r/min
取n=520r/min
m/min
选择丝锥退出时的转速为450r/min
基本时间的确定
==12.2s
式中 - 工件螺纹长度(mm)
- 丝锥切削锥长度(mm)
- 攻螺纹时的超切量,取=(2-3);
- 攻丝纹时的转速(r/min)
- 丝锥退出时的转速(r/mm )
- 工件螺纹距(mm )
工序6 粗精铣Φ5、M6上端面。用回转分度仪加工,粗精铣与水平成36゜的台肩
由工件可以得到尺寸LB=40 30
1、工件材料:HT200,金属模铸造
加工要求:铣宽度为30mm长度是40mm的平台,精铣宽度为30mm的上平台面达到粗糙度3.2。
机床:X50322立式铣床
刀具:高速钢镶齿式面铣刀Φ225(z=20)
2、计算切削用量
粗铣宽度为30mm的上平面
以知条件:工件的形状如毛胚所示,工件为HT200铸造件,硬度180HBW,有外皮,用X50322立式铣床进行加工,机床的功率是7。5KW:所用的刀具是高速钢镶齿式面铣刀Φ225(z=20),试确定切削用量。
铣刀直径 根据机械加工工艺手册表2.1-32以及面铣刀标准GB/T 5342-1985, 选择铣刀直径 =225mm 齿数Z= 20
铣削用量
背吃刀量:由于加工余量为2m m故在一次走刀内切完,取=2mm
确定每齿的进给量:
根据机械加工工艺手册表2.1-73.得到每齿的进给量=0.20 – 0.29mm/齿 ,采用对称铣削。取=0.2mm。
确定铣削速度 及铣削功率
根据机械加工工艺手册表2.1-75和表2.1-76,铣刀后面最大磨损限度为2mm ,刀具寿命T=120min 。
根据给定的条件,查机械加工工艺手册表2.1-87得到
根据表中的数据可以得到:
给定的材料硬度是190HBW,铣削的宽度是 ;实际的工件的硬度是180HBW,实际的铣削的宽度是
根据机械加工工艺手册表2.1-79查出修正系数
考虑修正系数后的铣削速度
计算出刀具转速及进给速度=
根据X5032型立式铣床说明书取
校验机床的功率 根据工作条件和选择的机床的条件经过计算和比较结果
数值大于加工工艺过程要求的功率,故所选用的机床X5032立式铣床是符合加工要求的。
7)基本功时:1.466mm
4.5.1粗铣,精铣平台
1加工条件:
工件材料:HT200铸铁,σb=165MPa,
机床:XA6132万能机床
刀具:高速钢镶齿套式面铣刀
计算切削用量
<1>查得此铣刀的进给量fz=0.2mm/z由(《削用量简明手册》查得)
<2>切削速度:查得可以确定为Vc =15.27m/min
由于dw=80mm,齿数Z=10则Ns=1000Vc/3.14×80=61r/min
按机床说明书,得Ns=75r/min
实际切削速度V=Πdwn/1000=3.14×80×75/1000=19m/min
当n=75r/min时,工作台进给量为f=fz?Z?n=0.2×10×75=150mm/min
查机床说明书,这个进给量合乎实际.
工时:t=行程/进给量=20+30.5+6/150=0.37min
由于半精加工时只是涉及到切削深度的改变,所以要求的数据一般不变!
4.5.2钻孔(中心孔)
查《削用量简明手册》得:进给量f’=0.53mm/r
切削速度:Vc=15m/min钻头直径为22mm,得主轴转速为Ns=1000×15/3.14×22=217r/min
所以实际速度取Nw=250r/min
得实际切削速度为V=3.14×22×250/1000=17.3m/min
查机床说明书确定进量f=0.62mm/r
工时:切入3mm、切出1mm,t=80+3+1/0.62×250=0.54min
第5章 夹具设计
为了提高生产率,保证质量。经我组分工现在对第2、4道工序设计夹具。本夹具将用在立式X5032立式铣床。刀具是高速钢立铣刀。
5.1问题提出。
本夹具主要用来加工平面。这两个孔与上下端面有着垂直度的要求,设计夹具时,要求保证垂直度要求。
5.2 机床夹具介绍
夹具最早出现在1787年,至今经历了三个发展阶段。第一阶段表现为夹具与人的结合。在工业发展初期。机械制造的精度较低,机械产品工件的制造质量主要依赖劳动者个人的经验和手艺,而夹具仅仅作为加工工艺过程中的一种辅助工具;第二阶段是随着机床、汽车、飞机等制造业的发展,夹具的门类才逐步发展齐全。夹具的定位、夹紧、导向(或对刀)元件的结构也日趋完善,逐渐发展成为系统的主要工艺装备之一;第三阶段,即近代由于世界科学技术的进步及社会生产力的迅速提高,夹具在系统中占据相当重要的地位。这一阶段的主要特征表现为夹具与机床的紧密结合。夹具的现状几生产对其提出新的要求
现代生产要求企业制造的产品品种经常更新换代,以适应市场激烈竞争,尽管国际生产研究协会的统计表明中不批,多品种生产的工件已占工件种类数的85%左右。然而目前,一般企业习惯与采用传统的专用夹具,在一个具有只能感等生产的能力工厂中约拥有13000~15000套专用夹具。另一方面,在多品种生产的企业中,约隔4年就要更新80%左右的专用夹具,而夹具的实际磨损量只有15%左右,特别最近年来柔性制造系统(FMS)、数控机床(NC),加工中心(MC)和成组加工(GT)等新技术被应用和推广,使中小批生产的生产率逐步趋近于大批量生产的水平。
综上所述,现代生产对夹具提出了如下新的要求:
⑴、能迅速方便地装备新产品的投产以缩短生产准备周期
⑵ 、能装夹一组相似性特征的工件
⑶、适用于精密加工的高精度的机床
⑷、适用于各种现代化制造技术的新型技术
⑸、采用液压汞站等为动力源的高效夹紧装置,进一步提高劳动生产率
5.3现代夹具的发展方向
现代夹具的发展方向表现为精密化、高效化、柔性化、标准化等四个方面:
⑴精密化
随着机械产品精度的日益提高,势必也相应提高对其精度要求。精密化夹具的结构类型很多,例如用于精密分度的多齿盘,其分度可达正负0.1,用于精密车削的高精度三爪卡盘,其定心精度为5um,又如用于轴承套圈磨削的电磁无心夹具,工件的圆读可达0.2~0.5um。
⑵高效化
高效化夹具主要用来减少工件加工的机动时的和辅助时的,以提高劳动生产率,减少工人劳动强度,常见的高效化夹具有:自动化夹具、告诉化夹具、具有夹紧动力模块的夹具等。例如使用电动虎钳装夹工件,可使工件效率比普通虎钳提高了5倍左右;而高速卡盘则可保证卡爪在转速9000r/min的条件下能正常夹紧工件,使切削速度大幅度提高。
⑶、柔性化
夹具的柔性化与机床的柔性化相似,它是通过调组合等方式,以适应工艺可变因素的能力。工艺的可变因素主要有:工序特征、生产批量、工件的形状和尺寸等,具有柔性化特征的新型夹具种类主要有:组合夹具、通用可调夹具、成组夹具、模块夹具、数控夹具等,在较长时间内,夹具的柔性化趋向将是夹具发展的主要方向。
⑷、标准化
夹具的标准化与通用化是相互联系的两个方面,在制造典型夹具,结构的基础上,首先进行夹具元件和部件的通用化,建立典型尺寸系列或变型,以减少功能用途相近的夹具元件和不见的形成:舍弃一些功能低劣的结构,通用化方法包括:夹具、部件、元件、毛呸和材料的通用化夹具的标准化阶段是通用化的深入并为工作图的审查创造了良好的条件。目前,我国已有夹具零件、部件的国家标准:GB2148~2249-80,GB2262~2269-80以及通用夹具标准,组合夹具标准等。夹具的标准化也是夹具柔性化高效化的基础,作为发展趋势,这类夹具的标准化,有利于夹具的专业化生产和有利于缩短生产准备周期,降低生产总成本。
夹具是一种能够使工件按一定的技术要求准确定位和牢固夹紧的工艺装备,它广泛地运用于机械加工,检测和装配等整个工艺过程中。在现代化的机械和仪器的制造业中,提高加工精度和生产率,降低制造成本,一直都是生产厂家所追求的目标。正确地设计并合理的使用夹具,是保证加工质量和提高生产率,从而降低生产成本的重要技术环节之一。同时也扩大各种机床使用范围必不可少重要手段。
5.4机床夹具的定位及夹紧
1),概述
在机械制造中,用以装夹工件(和引导刀具)的装置,称为夹具。它是用来固定加工对象,使之占有正确位置,一接受施工或检测的装置。
机床夹具的概念
在机械加工过程中,为了保证加工精度,首先要使工件在机床上占有正确的位置,确定工件在机床上或夹具中占有正确的位置的过程,称为工件的定位。定位后将其固定,使其在加工过程中始终保持定位位置不变的操作称为夹紧。工件在机床或夹具上定位、夹紧的过程称为工件的装夹。用以装夹工件的装置称为机床夹具,简称夹具。
2)机床夹具的组成
(1)机床夹具的基本组成部分
①定位装置
该装置由定位元件组合而成,其作用是确定工件在夹具中的正确位置。
②夹具装置
该装置的作用是将工件压紧夹牢,并保证工件在加工的过程中正确位置不变。
③夹具体
夹具体是夹具的基本骨架,通过它将夹具所有的元件构成一个整体。
(2)机床夹具的其他特殊元件或装置
①连接元件
根据机床的特点,夹具在机床上的安装连接常有两种形式。一种是安装在机床工作台上,另一种是安装在机床主轴上。连接元件用以确定夹具本身在机床上的位置。如机床夹具所使用的过渡盘,铣床夹具所使用的定向键等,都是连接元件。
②对刀元件
常用在普通铣床夹具中,用对刀快调整铣刀加工前的位置。对刀时,铣刀不与对刀快直接接触,而用塞尺进行检查,以免碰伤铣刀的切削刃和对刀快工作表面。
③导向元件
常用在钻床、镗床夹具中,用钻套和镗套引导刀具加工中的正确位置。
④其他元件或装置
根据加工需要,有些夹具还分别采用分度装置、靠模装置、上下料装置、预出器个平衡快等。这些元件或装置需要专门设计。
随行夹具
3)机床夹具的分类
根据机床夹具的通用化程度,可将夹具氛围以下几种:通用夹具,
专用夹具,成组夹具,组合夹具,随行夹具。
其中专用夹具是针对某一种工件的某道工序专门设计的夹具。所以结构紧凑,操作迅速方便。专用夹具通常由使用厂根据要求自行设计与制造。专用夹具定位精度高,一批工件加工或所得尺寸稳定,互换性高,并且可以减轻劳动强度,节省工时,显着提高效率,另外利用专用夹具还可以扩大机床的工艺范围。但专用夹具是为满足某个工件某道工序的加工需要而专门设计的,所以它的适用范围较窄。此外、专用夹具的设计制造周期较长。当产品更换时,往往因无法再使用而报废,因此,专用夹具主要适用于产品品种相对稳定的大批大量生产。
机床夹具在机械加工中的作用
夹具是机械加工中的一种工艺装备,它在生产中起的作用很大,所以在机械加工中的应用十分广泛。归纳起来有以下几个方面的作用:
⑴保证工件的加工精度
由于采用夹具安装,可以准确地确定工件与机床、刀具之间的相互位置,所以在机械加工中,可以保证工件各个表面的相互位置精度,使其不受或不受各种主观因素的影响,容易获得较高的加工精度,并使一批工件的精度稳定。
⑵提高劳动生产率和降低加工成本
采用夹具使工件装夹方便,免去工件逐个找正对刀所花费的时间,因此可以缩短辅助时间。另外,采用夹具装夹或,产品质量稳定,对操作工人的技术水平的要求可以降低,有利于提高生产率和降低成本。
⑶扩大机床工艺范围和改变机床用途
使用专用夹具可以改变原机床的用途和扩大机床的使用范围,实现一机多能。这是在生产条件有限的也器中常用的一种技术改造措施。例如,在车床或摇臂钻床上安装镗摸夹具后,就可以对箱体孔系进行镗削加工,一充分发挥通用机床的作用。
⑷改善劳动条件和保证生产安全
使用专用机床夹具可减轻工人的劳动强度、改善劳动条件,保证安全生产。
5.5工件的装夹方式
工件在机床上的装方式有以下三种方法:
1)直接找正法
在机床上根据工件上有关基准直接找正工件,使工件获得加工的正确位置的方法。
直接找正法的定位精度和工作效率,取决于被找工件表面的精度、找正方法和所用工具及工人的技术水平。此法一般多用于单件小批生产和精度要求特别高的场合。
划线找正法
在机床上按毛坯或工件上所划线找正工件,使工件获得正确位置的方法。
此法由于受到划线精度的限制,定位精度比较低,多用于单件小批量生产、毛坯精度较低以及大型零件等不使用夹具的粗加工中。
用夹具装夹
即通过夹具上的定位元件使工件相对于刀具及机床获得正确位置的方法。
此法使工件定位迅速方便,定位精度较高,广泛用于成批和大量生产。
上述用装夹工件的方法有以下几个特点:
工件在夹具中的定位,是通过工件上的定位基准与夹具上的定位元件相接触而实现的。
⑵由于夹具预先在机床上已调整好位置(也有在加工过程中再进行找正的),因此,工件通过夹具相对于机床也就有了正确的位置。
⑶通过夹具上的对刀装置,保证了工件加工表面相对于刀具的正确位置。
5.6.基准及其分类
机器零件是由若干个表面组成的。这些表面之间的相对位置关系包括两方面的要求:表面见的位置尺寸精度和相对位置精度。研究零件表面的相对位置关系,是离不开基准的。不明确基准就不无法确定表面的位置。
基准是用来确定生产对象上几何要素间的几何关系所依据的那些点、线、面。根据基准的不同功能,基准分为设计基准和工艺基准两大类。
1)设计基准
在零件图样上所采用的基准,称为设计基准。
工艺基准
零件在工艺过程中所采用的基准,称为工艺基准。工艺基准按用途不同,又分为装配基准、测量基准、工序基准和定位基准。
装配基准
装配时用以确定零件在部件或产品中的位置的基准,称为装配基准。
测量基准
测量时用以检验已加工表面尺寸几 位置的基准,称为测量基准。
工序基准
在加工工序中,用以确定本工序被加工表面家工后的尺寸、形状及位置的基准,称为工序基准。
定位基准
工件定位时所采用的基准,称为定位基准。
需要说明的是,作为基准的点、线、面在工件上并不一定具体存在。如轴心线、对称面等,它们是由某些具体表面来体现的。用以体现基准的表面称为定位基准。
5.7.工件的定位
工件定位的基本原理
工件装夹在机床上必须使工件相对于刀具和机床处于正确的加工位置,它包括工件在夹具的定位、夹具在机床上的安装以及夹具相对于刀具和整个工艺系统的调整等工作过程。在使用夹具的情况下,就要使机床、刀具、夹具和工件之间保持正确的加工位置。显然,工件的定位是其中极为重要的一个环节。
六点定位原则
定位,就是限制自由度。通常是用一个支承点限制工件的一个自由度,用合理设置的六个支承点,限制工件的六个自由度,使工件在夹具中的位置完全确定,这就是工件定位的“六点定位原则” 。
工件定位中可能出现的集中情况
Ⅰ完全定位
六个支承点限制了工件的全部自由度,称为完全定位。
Ⅱ不完全定位
根据工件的加工要求,并不需要限制工件的全部自由度,这样的定位,称为不完全定位。
Ⅲ欠定位
根据工件的加工要求,应该限制的自由度没有被限制的定位,称为欠定位。器定位无法保证加工要求,所以是决不允许的。
Ⅳ过定位
夹具上的两个或两个以上的定位元件,重复限制工件的同一个或几个自由度的现象,称为过定位。过定位中常会出现干涉现象。
消除或减小过定位所引起的干涉,一般有两种方法:
一种是提高定位基准之间以及定位元件工作表面之间的位置精度。
一种是改变定位元件的结构,使定位元件在重复限制自由度的部分不起定位作用。
5.8.常见定位方式及定位元件
定位方式和定位元件的选择包括选择定位元件的结构、形状、尺寸及布置形式等,他们主要取决于工件的加工要求、工件定位基准和外力的作用等因素。
工件及平面定位
主要支承 主要支承用来限制工件的自由度,起定位作用
①固定支承
②可调支承
③自位支承
⑵辅助支承 提高工件的安装刚性和稳定性
①螺旋式辅助支承
②自位式辅助支承
③推引式辅助支承
④液压锁紧的辅助支承
2)工件以圆柱空定位
圆柱销
圆锥销
圆柱心轴
3)、工件以外圆柱面定位
(1)在V形块中定位
(2)在圆孔中定位
(3)在半圆孔和圆锥孔中定位
5.9工件的夹紧
在机械加工中,工件的定位和夹紧是相互联系非常密切的两个工作过程。工件定位以后需要通过一定的装置把工件压紧夹牢在定位元件上,使工件在加工过程中,不会由于切削力、工件重力、离心力或惯性力等的作用而发生位置变化或产生振动,以保证加工精度和安全生产。这样把工件压紧夹牢的装置,即称为夹紧装置。
夹紧装置的组成及基本要求
(1)、夹紧装置的组成
①力源装置
②中间传动机构 作用如下:
Ⅰ改变夹紧作用力的方向
Ⅱ改变夹紧作用力的大小
Ⅲ具有一定的自锁性能
③夹紧元件
(2)、对夹紧装置的基本要求
①夹紧时不能破坏工件在夹具中占有的正确位置
②夹紧力的大小要适当
③夹紧装置要操作方便
④结构要进凑简单,有良好的结构工艺性,尽量使用标准件
2)、夹紧力的确定
确定夹紧力就是确定夹紧力的大小、方向和作同点。在确定夹紧力的三要素时要分析工件的结构特点、加工要求、切削力及其他外力作用于工件的情况,而且必须考虑定位装置的结构形式和布置方式。夹紧力的三要素对夹紧结构的设计起着决定性的作用。只有夹紧力的作用点分布合理,大小适当,方向正确才能获得良好的效益。
(1)夹紧力方向的确定
①夹紧力方向应垂直于主要定位基准面
②夹紧力的方向最好与切削力、工件重力方向一致
(2)夹紧力作用点的选择
①应能够保持工件定位稳定可靠,在夹紧过程中不会引起工件产生位移或偏转。
②应尽量避免或减少工件的夹紧变形
③夹紧力作用点应尽量靠近加工部位
(3)夹紧力大小的估算
①首先假设系统为刚性系统,切削过程处于稳定状态。
②常规情况下,只考虑切削力(矩)在力系中的影响;切削力(矩)用切削原理公式计算。
③对重型工件应考虑工件重力的影响。在工件做高速运动场合,必须计入惯性力。
④分析对夹紧最不利的瞬时状态,按静力平衡方程计算此状态下所需的夹紧力即为计算夹紧力
⑤将计算夹紧力再乘以K,即得实际夹紧力。K为总安全系数,K=K0K1K2K3
各种因素的安全系数可查表2-3,一般K=1.5~2.5;
当夹紧力与切削力相反时,K=2.5~3 。
3)典型夹紧结构
⑴斜楔夹紧结构
⑵螺旋夹紧结构
①单个螺旋夹紧结构
②螺旋压板夹紧结构
③偏心夹紧机构
4),定心夹紧机构
当加工尺寸的工序基准是中心要素(轴线、中心平面等)撕,为使基准重合以减少定位误差,可以采用定位夹紧机构,所以,定心夹紧机构主要用于要求准确定心或对中的场合。
螺旋式定心夹紧机构
杠杆式定心夹紧机构
楔式定心夹紧机构
弹簧筒夹式定心夹紧机构
膜片卡盘定心夹紧机构
波纹套定心夹紧机构
液性塑料定心夹紧机构
5.10设计宗旨
设计必须保证零件的加工精度,保证夹具的操作方便,夹紧可靠,使用安全,有合理的装卸空间,还要注意机构密封和防尘作用,使设计的夹具完全符合要求。所以设计时要在满足精度的前提下提高劳动生产效率,降低劳动强度。
5.11夹具的设计
对机床专用夹具的基本要求可总括为以下几个方面:
稳定地保证工件的加工精度
提高机械加工的劳动生产率
结构简单,有良好的结构工艺性和劳动条件
应能够降低工件的制造成本
适当提高夹具元件的通用化和标准化程度,以缩短夹具制造周期,降低夹具成本
1、定位基准的选择
由零件图可知Φ25孔的轴线所在平面和右端面有垂直度的要求是10゜,从定位和夹紧的角度来看,右端面是已加工好的,本工序中,定位基准是右端面,设计基准是孔Φ25的轴线,定位基准与设计基准不重合,需要重新计算上下端面的平行度,来保证垂直度的要求。在本工序只需要确定右端面放平。
2、切削力及夹紧力的确定
本夹具是在铣\钻床上使用的,用于定位螺钉的不但起到定位用,还用于夹紧,为了保证工件在加工工程中不产生振动,必须对夹紧六角螺母和螺母螺钉施加一定的夹紧力。由计算公式
Fj=FsL/(d0tg(α+ψ1’)/2+r’tgψ2)
Fj-沿螺旋轴线作用的夹紧力
Fs-作用在六角螺母上的力
L-作用力的力臂(mm)
d0-螺纹中径(mm)
α-螺纹升角(゜)
ψ1-螺纹副的当量摩擦(゜)
ψ2-螺杆(或螺母)端部与工件(或压块)的摩擦角(゜)
r’-螺杆(或螺母)端部与工件(或压块)的当量摩擦半径(゜)
根据《工艺手册》其回归方程为
Fj=ktTs
其中Fj-螺栓夹紧力(N);
kt-力矩系数(cm-1)
Ts-作用在螺母上的力矩(N.cm);
Fj =5×2000=10000N
5.12 位误差分析
销与孔的配合0.05mm,铣/钻模与销的误差0.02mm,铣/钻套与衬套0.029mm
由公式e=(H/2+h+b)×△max/H
△max=(0.052+0.022+0.0292)1/2=0.06mm
e=0.06×30/32=0.05625
可见这种定位方案是可行的。
5.13夹具操作的简要说明
第一套夹具用于在立式铣床上加工杠杆的小平面和加工Φ12.7。工件以Φ250+0.023 孔及端面和水平面底为定位基准,在长销、支承板和支承钉上实现完全定位。采用螺母及开口垫圈手动夹紧工件。当加工完一边,可松开螺钉、螺母、支承钉来加工另一边。一次加工小平面和加工Φ12.7
夹具装配图,夹具零件图分别见附带图纸。
第二套夹具也是用于在立式铣床上加工杠杆的上平面,定位夹紧基本与第一套夹具类似,夹具装配图,零件图见附图。
第6章 小 结
为期两周的夹具课程设计已经接近尾声,回顾整个过程,我组五名同学在老师的指导下,取得了可喜的成绩,课程设计作为《机械制造工艺学》、《机床夹具设计》课程的重要环节,使理论与实践更加接近,加深了理论知识的理解,强化了生产实习中的感性认识。
本次课程设计主要经历了两个阶段:第一阶段是机械加工工艺规程设计,第二阶段是专用夹具设计。第一阶段我们运用了基准选择、切削用量选择计算、机床选用、时间定额计算等方面的知识;夹具设计的阶段运用了工件定位、夹紧机构及零件结构设计等方面的知识。
通过此次设计,使我们基本掌握了零件的加工过程分析、工艺文件的编制、专用夹具设计的方法和步骤等。学会了查相关手册、选择使用工艺装备等等。
总的来说,这次设计,使我们在基本理论的综合运用及正确解决实际问题等方面得到了一次较好的训练。提高了我们的思考、解决问题创新设计的能力,为以后的设计工作打下了较好的基础。
由于能力所限,设计中还有许多不足之处,恳请各位老师、同学们批评指正!
第7章 结束语
通过这次课程设计,我有了很大的收获学到了很多的东西本次课程设计是我们学完了大学的全部基础课,专业基础课后进行的这是我们即将离开学院走上工作岗位之前对所学各课进行的一次全面的、深入的、综合性的总复习,也是一次理论联系实际的训练,是我们在走上工作岗位之前一次极好的学习机会,因此它在望没的四年大学生活中占有积极重要的地位。
就我个人而言,我通过本次课程设计对自己在大学中所学的知识进行一次良好的回顾,并在次基础上有所提高,对自己将来从事的工作进行一次适应性的训练,无论是机械结构设计、零件加工工艺还是CAD画图能力都得到了大大的巩固和提高,从而锻炼自己发现问题、思考问题解决问题的能力,并培养认真、严谨的专业精神,为以后参加国家的工业化建设打下一个良好的基础,为早日实现国家的现代化贡献一份力量。
由于个人的能力有限,设计尚有诸多不足之处恳请老师大力支持,在次不胜感谢。
参考文献
1、杨叔子主编.机械加工工艺师手册.北京:机械工业出版社,2001
2、李益民主编.机械制造工艺设计简明手册.北京:机械工业出版社,1994
3、孙本绪、熊万武编.机械加工余量手册.北京:国防工业出版社,1999
4、机床夹具设计手册.北京:中国科学技术出版社
5、赵家齐主编.机械制造工艺学课程设计指导书.北京.机械工业出版社,2000
6、刘守勇主编.机械制造工业与机床夹具.北京:机械工业出版社,2000
7、田春霞主编.数控加工工艺.北京:机械工业出版社,2006
8、吴拓、方琼珊主编. 机械制造工艺与机床夹具课程设计指导书.北京:机械工业出版社,2005
9、李益民 机械制造工艺设计简明手册.北京:机械工业出版社,1994
10、孙本绪、熊万 机械加工余量手册.北京:国防工业出版社,1999
11、刘守勇 机械制造工业与机床夹具.北京:机械工业出版社,2000
12、黄云清 公差配合与测量技术.北京:机械工业出版社,2001
13、薛源顺 机床夹具设计. 北京:机械工业出版社, 2001
14、Morgan, M.N, Rowe, W.B., Black, S.C.E. and Alanson, D.R. Machining of Engineering Ceramics(J).Engineering Manufacture, 1998, 212(B8), 661-669
15、Rowe, W.B. Mechanical Engineering in the information(J). Engineering Manufacture, 2001, 215(B4), 473-491
致谢
本次毕业设计综合了大学里所学的专业知识,是理论与实际相结合的一次考验。通过这次设计,我的综合运用知识的能力有了很大的提高,尤其是看图、绘图、设计能力,为我今后的工作打下了良好的基础。在此过程中,我进一步加深了对课本知识的理解,进一步了解了零件的工艺以及夹具设计过程,收获颇丰。
本次设计是在郑培文老师的悉心指导和帮助下完成的。我的机械工艺知识有限,在设计中常常碰到问题,是郑老师不厌其烦的指导,不断的点拔迷津,提供相关资料,才使其顺利完成。郑老师耐心的讲解,使我如沐春风。不仅如此,郑培文老师严谨的治学态度和高尚的敬业情操深深打动了我。在此,我向郑老师表示最真诚的感谢。同时,感谢同组同学的支持和帮助,使我更好的完成毕业设计。
QQ 29467473