
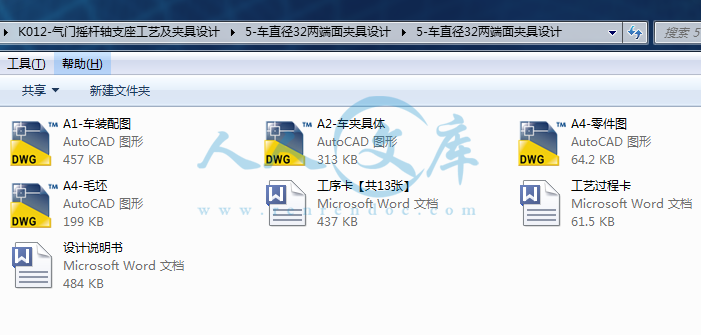
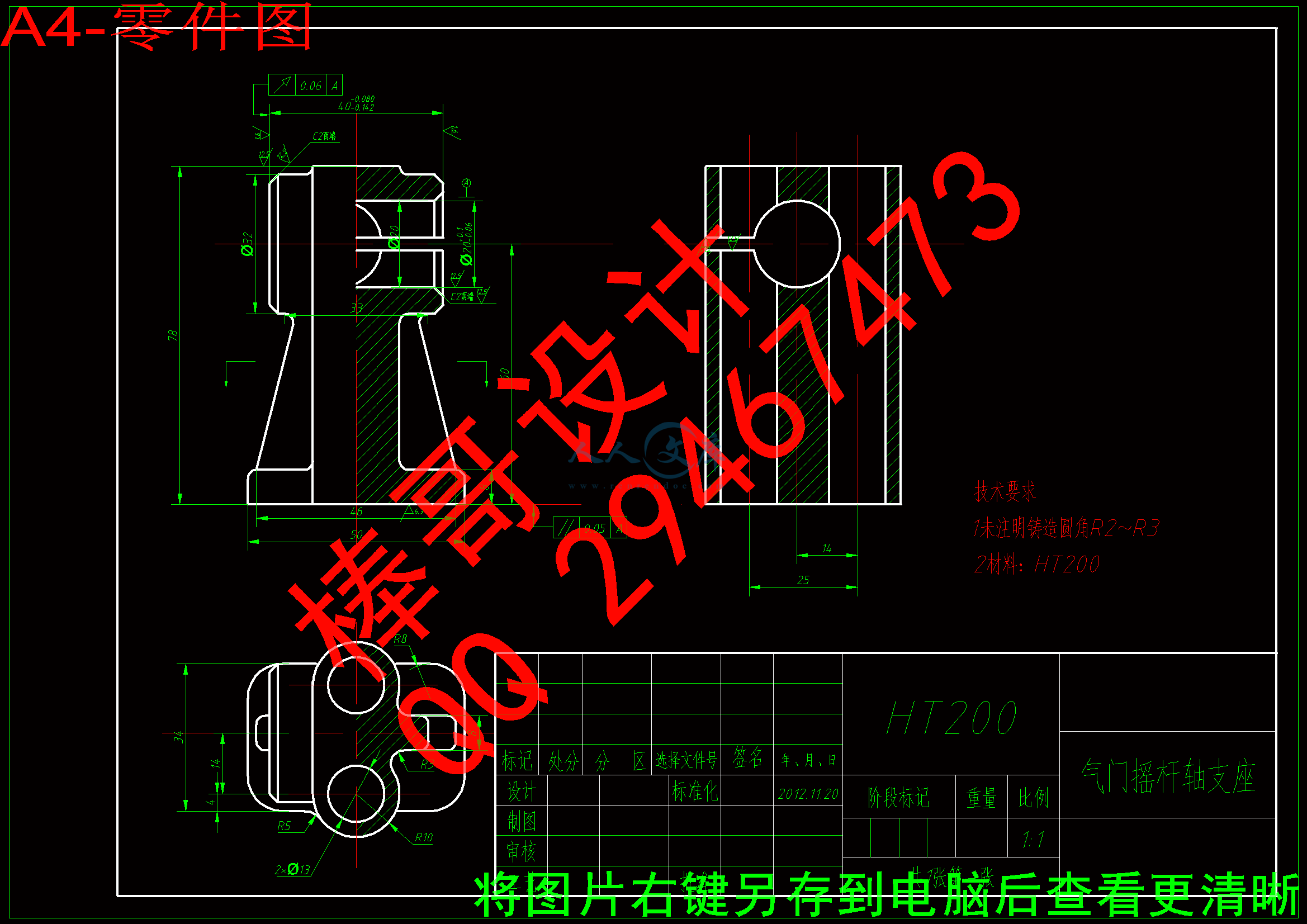

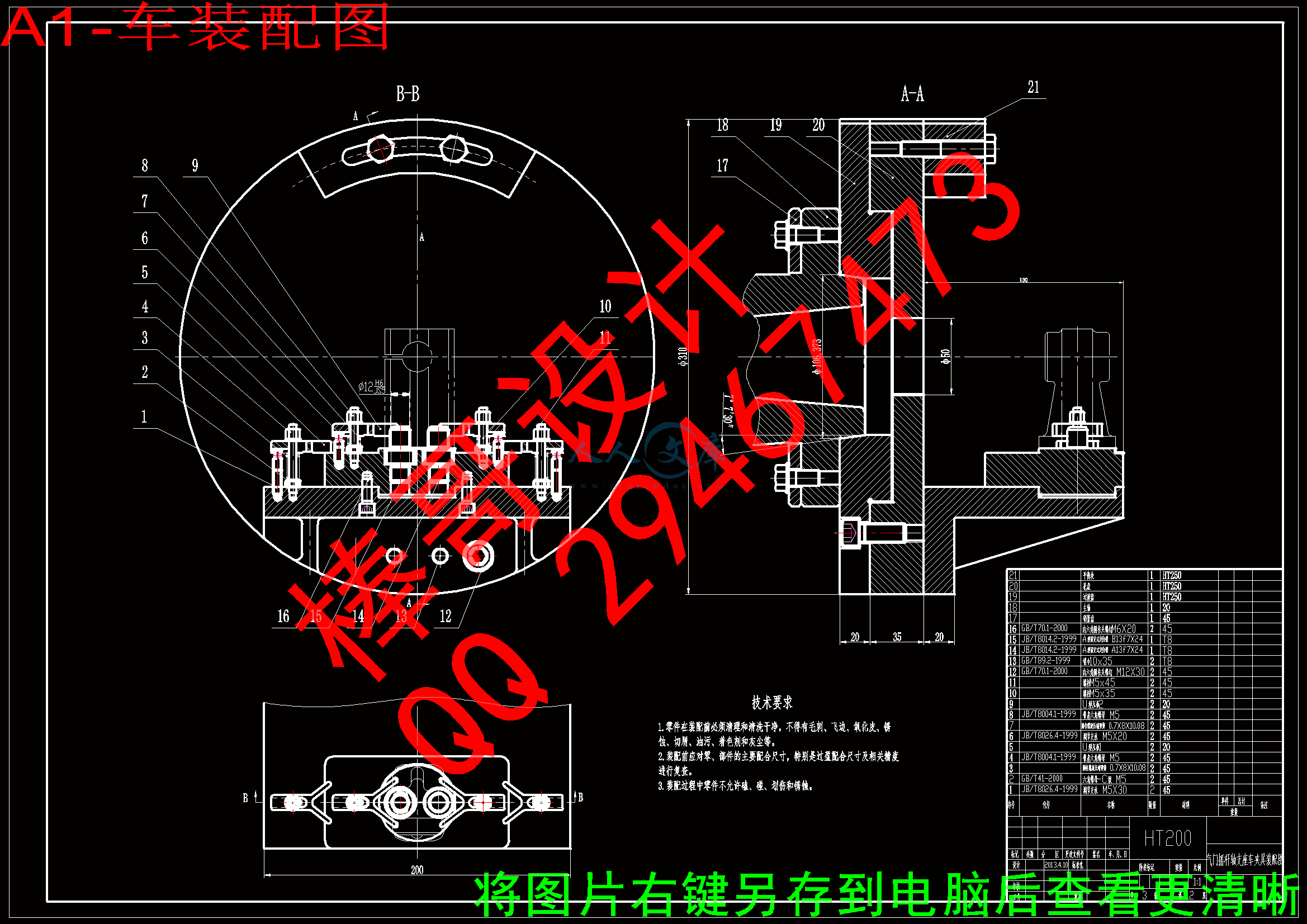
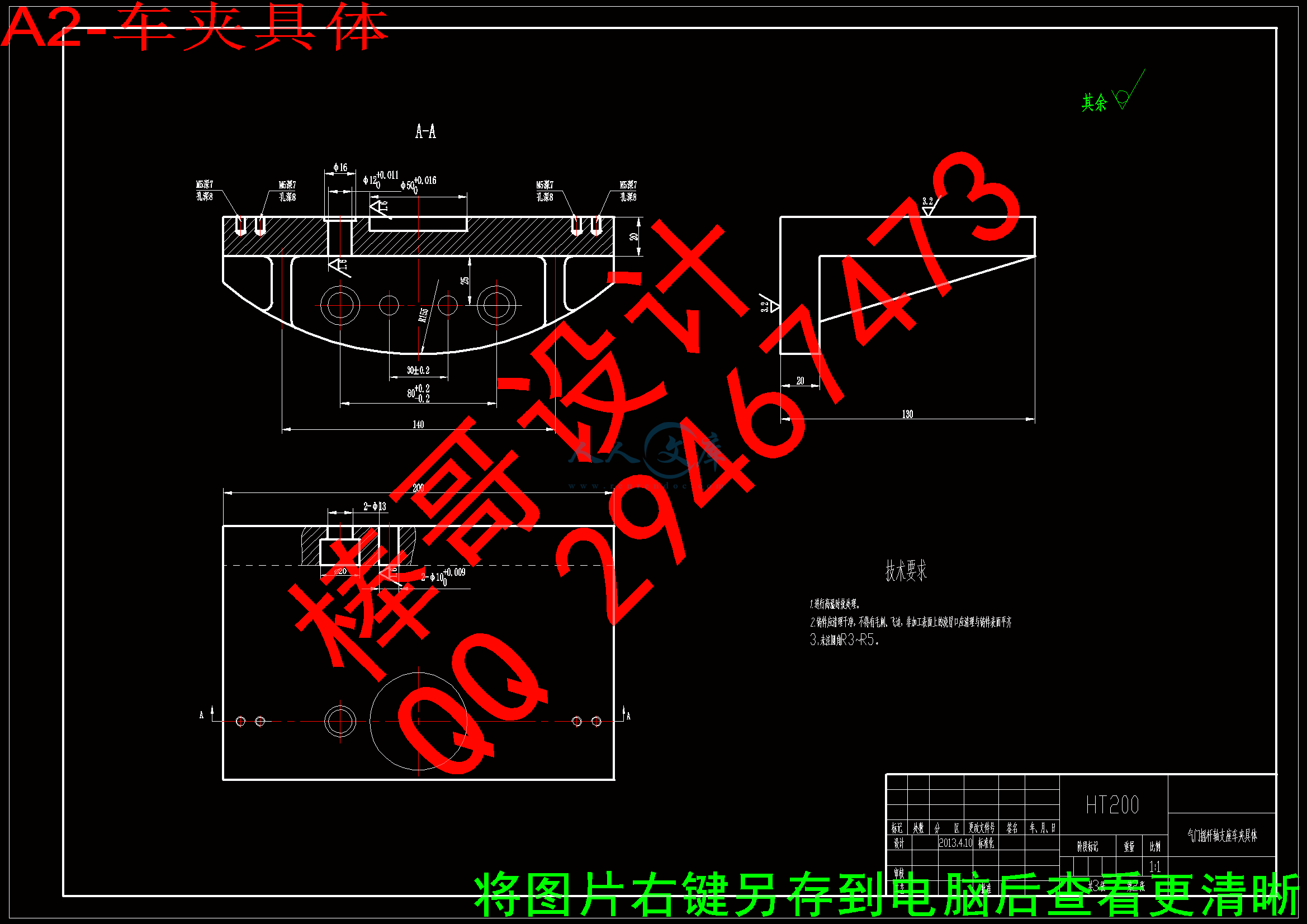
棒哥设计QQ 29467473
题目:气门摇杆轴支座零件机械加工工艺及其典型夹具设计
系 别: 机电信息系
专 业: 机械设计制造及其自动化
班 级:
学 生:
学 号:
指导教师:
2013年4月25日
气门摇杆轴支座零件机械加工工艺及其典型夹具设计
摘 要
气门摇杆轴支座是柴油机一个重要零件,是柴油机摇杆座的结合部。本毕业设计在气门摇杆轴支座工艺规程设计过程中,详细的分析了摇杆轴支座的加工工艺,通过工艺方案的比较与分析得到了符合技术要求的工序,形成了机械加工工艺过程卡和机械加工工序卡。并完成了铣削和车削以及钻孔夹具的设计,阐述了定位方案的选择、夹紧方案的确定、夹具体设计,运用AutoCAD完成了此典型夹具的装配图和夹具体的零件图。本设计的加工工艺合理,夹具可行、高效、省力,能满足零件的加工要求,保证其加工质量。
关键词:气门摇杆轴支座;机械加工;加工工艺;典型夹具
Bearing Parts Machining Process Valve Rocker Shaft and Its Typical Fixture Design
Abstract
Valve rocker shaft bearing is an important part of the diesel engine, is a combination of diesel engine rocker seat. This graduation design in valve rocker shaft bearing process design process, a detailed analysis of the process of the rocker shaft bearing, meet the technical requirements of the process was obtained through the comparison and analysis of the process, forming a machining process card and machining process card. And finish milling and turning and drilling fixture design, elaborated the localization scheme selection, clamping scheme, clamp design, AutoCAD is used to complete the assembly drawing of this typical fixture and clamp parts map specific. Processing technology of the design is reasonable, feasible, high efficiency, labor saving fixture, can meet the processing requirements of parts, ensure the machining quality.
Key Words: valve rocker shaft bearing; mechanical processing; processing
technology; typical jig
目 录
1绪论1
1.1题目背景及研究意义1
1.2国内外相关研究情况2
1.3本课题主要内容和拟采用的研究方案3
2零件的分析5
2.1零件的作用5
2.2零件的结构分析5
2.2零件的工艺分析6
2.3零件的生产类型6
3机械加工工艺规程设计8
3.1确定毛坯的制造形式8
3.2定位基准的选择8
3.3制定机械加工工艺路线9
3.4工艺方案的比较与分析9
3.5机械加工余量、工序尺寸及毛坯尺寸的确定10
3.6选择加工设备及刀、夹、量具11
3.7确定切削用量及基本工时11
4粗车、半精车、精车Φ 32两端面的夹具设计24
4.1车床夹具设计特点24
4.2定位部分设计25
4.2.1问题提出25
4.2.2定位基准的选择25
4.2.3定位元件的设计25
4.3切削力和夹紧力的计算25
4.4夹具设计及简要操作说明25
结论29
参考文献30
致谢31
1 绪论
1.1题目背景和研究意义
制造业是一个国家的立国之本,是一个国家的民族产业和支柱产业,也是反映一个国家经济实力的重要标志,是为国家创造财富的重要产业。
制造技术支持着制造业的发展,当今制造技术的发展使传统制造业革新了他原来的面目,制造工艺与夹具同样取得了较快发展。所谓工艺,是使各种原材料、半成品成为产品的方法和过程。进行机械加工工艺设计是保证产品质量、节约能源、降低成本的重要手段,是企业进行生产准备,计划调度、加工操作、生产安全、技术检测和健全劳动组织的重要依据,也是企业上品种、上质量、上水平,加速产品更新,提高经济效益的技术保证。机械零件加工精度是机械零件加工质量的核心部分。零件的加工精度是指零件完工后的实际几何参数(尺寸、形状和相互位置)对理想几何参数的符合程度,符合程度越高。机械加工工艺对加工精度的影响主要体现在加工工艺的受力变形、加工工艺的几何精度以及工艺系统的热变形三个方面。加工精度包括:尺寸精度,形状精度,位置精度。提高加工及高度的措施归纳为:减少误差法;误差补偿法(误差抵消法);误差转移法;就地加工法;误差平均法[1]。
夹具的出现可靠地保证加工精度,提高整体工作效率,减轻劳动强度,充分发挥和扩大机床的工艺性能。机床夹具设计是工艺装备设计中的一个重要组成部分,是保证产品质量和提高劳动生产率的一项重要技术措施。在设计过程中应深人实际,进行调查研究,吸取国内外的先进技术,制定出合理的设计方案,再进行具体的设计。
夹具是制造系统的重要组成部分,是机械制造中的一项重要工艺装备。工件在机床上进行加工时,为了保证加工精度和提高生产效率,必须使工件相对刀具占有正确位置,完成之一功能的辅助装置成为机床夹具。它的主要用于保证产品的加工质量、减轻劳动强度、辅助产品检测、展示、运输等。不论是传统制造,还是现代制造系统,夹具都是十分重要的。因此,好的夹具设计可以提高产品劳动生产率,保证和提高加工精度,降低生产成本等,还可以扩大机床的使用范围,从而使产品在保证精度的前提下提高效率、降低成本。当今激烈的市场竞争和企业信息化的要求,企业对夹具的设计及制造提出了更高的要求。
机床夹具按其使用范围可分为以下五种基本类型:1)通用夹具 通用夹具具有一定的通用性。2)专用夹具 专用夹具是针对某一种工件的某一个工序而
专门设计的。3)通用可调整夹具和成组夹具 通用可调整夹具和成组夹具的特点是夹具的部分元件可以更换,部分装置可以调整,以适应不同零件的加工。4)组合夹具 组合夹具是由一套完全标准化的元件,根据零件的加工要求拼装而成的夹具[3]。组合夹具的适用范围可以从不同角度来谈:从产品的批量来看,组合夹具最适于新产品研制、试制、单件和小批量生产。因此,对于产品变化频繁、该型周期短、产品类型多的企业选用组合夹具最为适宜,能收到最显着的经济效果;从加工工序来看,组合夹具应用极为广泛,它可以方便的组成各类机床使用的夹具;从加工工件的几何形状和尺寸看,组合夹具一般不受工件形状的限制。
工件的工艺分析及夹具设计是工艺工程师必备的专业素质。这次设计使我们能综合运用了械制图学,机械设计,机械制造工程学,互换性与测量技术中的基本理论和方法独立地分析和解决工艺与夹具设计中的问题,初步具备了设计一个中等复杂程度零件(气门摇杆轴支座)的工艺规程的能力和运用夹具设计的基本原理和方法,拟订夹具设计方案,完成家具结构设计的能力,也是熟悉和运用有关手册,图表等技术资料及编写技术文件技能的一次中和性实践机会,为今后从事的工作打下良好的基础。
1.2国内外相关研究情况
迄今为止,夹具仍是机电产品制造中必不可缺的四大工具(刀具、夹具、量具、模具)之一。夹具在国内外也正在逐渐形成一个依附于机床业或独立的小行业。
1.2.1 国内夹具发展史
我国国内的夹具始于20世纪60年代,当时建立了面向机械行业的天津组合夹具厂,和面向航空工业的保定向阳机械厂,以后又建立了数个生产组合夹具元件的工厂。在当时曾达到全国年产组合夹具元件800万件的水平。20世纪80年代以后,两厂又各自独立开发了适合NC机床、加工中心的孔系组合夹具系统,不仅满足了我国国内的需求,还出口到美国等国家。当前我国每年尚需进口不少NC机床、加工中心,而由国外配套孔系夹具,价格非常昂贵,现大都由国内配套,节约了大量外汇[5]。
1.2.2 国外夹具发展史
从国际上看俄国、德国和美国是组合夹具的主要生产国。当前国际上的夹具企业均为中小企业,专用夹具、可调整夹具主要接受本地区和国内订货,而通用性强的组合夹具已逐步成熟为国际贸易中的一个品种。有关夹具和组合夹具的产值和贸易额尚缺乏统计资料,但欧美市场上一套用于加工中心的夹具,而组合夹具的大型基础件尤其昂贵。由于我国在组合夹具技术上有历史的积累和性能价格比的优势,随着我国加入WTO和制造业全球一体化的趋势,特别是电子商务的日益发展,其中蕴藏着很大的商机,具有进一步扩大出口良好前景[16]。
1.2.3国内外机床夹具发展现状
研究协会的统计表明,目前中、小批多品种生产的工件品种已占工件种类总数的85%左右。现代生产要求企业所制造的产品品种经常更新换代,以适应市场的需求与竞争。然而,一般企业都仍习惯于大量采用传统的专用夹具,一般在具有中等生产能力的工厂,里约拥有数千甚至近万套专用夹具;另一方面,在多品种生产的企业中,每隔3~4年就要更新50~80%左右专用夹具,而夹具的实际磨损量仅为10~20%左右。特别是近年来,数控机床、加工中心、成组技术、柔性制造系统、(FMS)等新加工技术的应用,对机床夹具提出了如下新的要求:
1)能迅速而方便地装备新产品的投产,以缩短生产准备周期,降低生产成本;
2)能装夹一组具有相似性特征的工件;
3)能适用于精密加工的高精度机床夹具;
4)能适用于各种现代化制造技术的新型机床夹具;
5)采用以液压等为动力源的高效夹紧装置,以进一步减轻劳动强度和提高劳动生产率;
6)提高机床夹具的标准化程度。
总体来说现代机床的发展趋势是:1)、提高标准化通用化程度。2)、适应多品种、中小批生产企业的特点,发展可调整夹具,力求缩短生产准备周期,提高经济效果。3)、发展高效率夹具力求提高劳动生产率,减轻劳动强度4)、机床夹具的发展应向机床工作台技术转移[18]。
1.3本课题研究的主要内容和拟采用的研究方案
1.3.1课题研究主要内容
气门摇杆轴支座是柴油机一个主要零件。是柴油机摇杆座的结合部,mm孔装摇杆轴,轴上两端各装一进气门摇杆,摇杆座通过两个Φ 13mm孔用M12螺杆与汽缸盖相连,3mm轴向槽用于锁紧摇杆轴,使之不转动。汽缸盖内每缸四阀使燃烧室充气最佳,气门由摇杆凸轮机构驱动,摩擦力小且气门间隙由液压补偿。这种结构可能减小燃油消耗并改善排放。另外一个优点是减小噪音,这种结构使3.0升的TDI发动机运转极端平稳。
主要研究内容:1)对所给零件进行工艺分析,并建立该零件三维模型,设计该零件毛坯。 2)、所给零件的工艺分析,计算、编写加工工艺,有数控工序的并编写数控代码。3)、设计1-2个工序的机床夹具,有定位分析(自由度),夹具的定位误差计算等内容。4)、绘制各夹具的装配图及部分零件图;要求各夹具设计合理,符合工程实际。
1.3.2拟采用的研究方案
第一步、零件作用分析和工艺分析。第二步、零件工艺规程定性设计,包括毛坯制造方法的确定、基准面选择、工艺路线确定。第三步,零件工艺规程定量设计和计算,包括毛坯尺寸的确定、工艺尺寸、机械加工余量确定、切削用量和基本工时确定。第四步、夹具设计。第五步、绘制零件、夹具及装配二维图。2 零件的分析
2.1零件的作用
气门摇杆轴支座是柴油机一个主要零件,是柴油机摇杆座的结合部。孔装摇杆轴,轴上两端各装一进气门摇杆,摇杆座通过两个Φ13mm孔用M12螺杆与汽缸盖相连,3mm轴向槽用于锁紧摇杆轴,使之不转动。气缸盖内每缸四阀使燃烧室充气最佳,气门由摇杆凸轮机构驱动,摩擦力小且气门间隙由液压补偿。这种结构可以减少燃油消耗并改善排放。零件图见图2.1
图2.1气门摇杆轴支座三维建模
2.2零件的结构分析
该零件是属于箱体零件,典型通过对该零件的重新绘制,知道了得原图的视图正确、完整,尺寸、公差及技术要求齐全。该零件上主要加工面为上端面,下端面,左右端面,2×Φ13mm孔和mm以及3mm轴向槽的加工。
mm孔的尺寸精度以及下端面与Φ20mm 孔的中心轴线的平行度为0.05mm与左右两端面孔的尺寸精度等,直接影响到进气孔与排气门的传动精度及密封,以及2×Φ13mm孔的尺寸精度,和上下两端面的平行度0.05mm。
2.3零件的工艺分析
由零件毛坯图2.2得知,其材料为HT200,该材料为灰铸铁,具有较高的强度,耐磨性,耐热性及减振性,适用于承受较大应力,要求耐磨的零件。
该零件上主要加工面为上端面,下端面,左右端面,2×Φ13mm孔和mm以及3mm轴向槽的加工。mm孔的尺寸精度以及下端面0.05mm的平面度与左右两端面孔的尺寸精度,直接影响到进气孔与排气门的传动精度及密封,2-Φ13mm孔的尺寸精度,以上下两端面的平行度0.05mm。因此,需要先以下端面为粗基准加工上端面,再以上端面为粗基准加工下端面,再把下端面作为精基准,最后加工mm孔时以下端面为定位基准,以保证孔轴相对下端面的位置精度。零件毛坯图如图2.2所示
图2.2气门摇杆轴支座毛坯图
2.4零件的生产类型
(2.1)
依设计题目知:Q=6000台/年,n=2件/台;结合生产实际,备品率a和废品率b都为4%。带入公式得该零件的生产纲领
从此结果可知,该零件生产类型为大批生产。
?3 机械加工工艺规程设计
3.1确定毛坯的的制造形式
由零件图可知,其材料为HT200,该材料具有较高的强度、耐磨性、耐热性及减振性,适用于承受较大应力,要求耐磨的零件。该零件外形结构较复杂,因此确定毛坯为铸件,毛坯的铸造方法选用砂型机器造型,此外,为消除残余应力,铸造后安排人工时效处理。零件上主要加工面为上端面,下底面,左右两端面,2×Φ13孔,孔以及3mm宽的轴向槽。其中孔的尺寸精度以及下端面相对于孔轴线的平行度及左右端面的尺寸精度,直接影响到进气孔与排气门的转动精度和密封性。因此,需要先以上端面为粗基准加工下端面,再以下端面为精基准加工上端面,最后加工时以下端面为定位基准,以保证孔轴相对下端面的位置精度。由参考文献[17]中有关孔的加工的经济精度机床能达到的位置精度可知,上述要求是可以达到的零件结构的工艺性也是可行的。
根据零件材料确定毛坯为铸件,已知零件的类型为大批量生产,故毛坯的铸造方法用砂型机器造型。此外,为消除残余应力,铸造后安排人工时效处理。由参考文献[17]查得该种铸造公差等级为CT10—11,加工余量等级MA选择H级。
3.2定位基准的选择
在机械加工过程中,定位基准的选择合理与否决定零件质量的好坏,对能否保证零件的尺寸精度和相互位置精度要求,以及对零件各表面间的加工顺序安排都有很大影响,当用夹具安装工件时,定位基准的选择还会影响到夹具结构的复杂程度。因此,定位基准的选择是一个很重要的工艺问题。定位基准有粗基准和精基准之分。零件开始加工时,所有的面均为加工,只能以毛坯面作定位基准,这种以毛坯面为定位基准的,称为粗基准;以后的加工,必须以加工过的表面做定位基准,以加工过的表面作为定位基准的称为精基准。
3.2.1精基准的选择
气门摇杆轴支座的下端面既是装配基准又是设计基准,用它作为精基准,能使加工遵循基准重合的原则。孔及左右两端面都采用底面做基准,这使得工艺路线又遵循“基准统一”的原则,下端面的面积比较大,定位比较稳定,夹紧方案也比较简单,可靠,操作方便。
3.2.2粗基准的选择
选择零件的重要面和重要孔做基准。在保证各加工面均有加工余量的前提
下,使重要孔或面的加工余量尽量均匀,此外,还要保证定位夹紧的可靠性,装夹的方便性,减少辅助时间,所以粗基准为上端面。
3.3制定机械加工工艺路线
制定工艺路线时,必须充分考虑采用确保产品质量,并以最经济的办法达到所要求的生产纲领的必要措施,即应该做到:技术上先进,经济上合理,并有良好、安全的劳动条件。
(1)、工艺路线方案一:
工序1:铸造
工序2:时效
工序3:粗车、精车50底面
工序4:粗车上端面
工序5:钻Φ18的孔,扩孔至Φ19.8、铰孔至Φ20,倒角
工序6:粗车、半精车、精车左右两Φ32端面
工序7:铣轴向槽
工序8:钻Φ12的孔,扩孔至Φ12.8、铰孔至Φ13
工序9:清洗去毛刺
工序10:验收
工序11:入库
(2)、工艺路线方案二:
工序1:铸造
工序2:时效
工序3:粗、精铣50底面
工序4:粗铣上端面
工序5:钻Φ 18的孔,扩孔至Φ 19.8、铰孔至Φ 20,倒角
工序6:钻Φ12的孔,扩孔至Φ 12.8、铰孔至Φ 13
工序7:铣轴向槽
工序8:粗车、半精车、精车左右两Φ 32端面
工序9:清洗去毛刺
工序10:验收
工序11:入库
以上工艺过程详见“机械加工工艺过程卡综合片”
3.4工艺方案的比较与分析
上述前两个工艺方案的特点在于:两个加工方案都是按先加工面再加工孔的原则进行加工的。方案一用车削的方法加工上下底面,由于工件形状和尺寸原因本工件在车床上车削时比较困难,故改用铣床加工。且把钻2×Φ13孔放的相对靠前,这样做为后面工序的加工提供了定位基准,节约了夹具设计的时间,提高了生产效率,因此,选用方案二是比较合理的。
最后确定工艺方案如下表3.1:
表3.1 加工工艺路线
工序号工序内容简要说明
1一箱多件沙型铸造
2进行人工时效处理消除内应力
3粗、精铣50底面先加工面
4粗铣上端面
5钻Φ18的孔,扩孔至Φ19.8、铰孔至Φ20,倒角
6钻Φ12的孔,扩孔至Φ12.8、铰孔至Φ13
7铣轴向槽
8粗车、半精车、精车左右两Φ32端面
9清洗去毛刺
10验收
11入库
3.5机械加工余量、工序尺寸及毛坯尺寸的确定
“气门摇轴支座”零件材料HT200,毛坯的重量约为1.4kg,生产类型为大批量生产,采用砂型机铸造毛坯。
1、50底面,表面粗糙度为Ra6.3,查参考文献[6]表2-8得,单边总余量Z=2.0
粗铣 单边余量Z=1.5
精铣 单边余量Z=0.5
2、上端面,表面粗糙度为Ra12.5,查参考文献[6]表2-8得,单边总余量Z=2.0
粗铣 单边余量Z=1.5
精铣 单边余量Z=0.5
3、2×Φ13孔,因孔的尺寸不大,很难铸造成型,故采用实心铸造
4、轴向槽,因尺寸不大,很难铸造成型,故采用实心铸造
5、Φ32端面,表面粗糙度为Ra1.6,查参考文献[6]表2-8得,单边总余量Z=2.0
粗车 单边余量Z=1.5
半精车 单边余量Z=0.4
精车 单边余量Z=0.1
6、Φ20孔,因孔的尺寸不大,很难铸造成型,故采用实心铸造
7、不加工表面毛坯按照零件图给定尺寸为自由度公差,由铸造可直接获得。
3.6选择加工设备及刀、夹、量具
由于生产类型为大批生产,故加工设备适宜通用机床为主,辅以少量专用机床的流水生产线,工件在各机床上的装卸及各机床间的传动均由人工完成。
粗铣50底面:考虑到工件的定位夹紧方案及夹具结构设计等问题,采用立铣选择X51立式铣床,刀具为直径D为Φ60mm立铣刀,专用夹具及游标卡尺。
精铣50底面:采用上述相同的机床与铣刀,专用夹具及游标卡尺。
粗铣上端面:采用上述相同的机床,刀具为直径D为Φ30mm立铣刀,专用夹具和游标卡尺。
钻孔至Φ18:采用立式钻床选择Z525立式钻床,刀具为直柄麻花钻,专用夹具和游标卡尺
扩Φ18孔至Φ19.8:采用立式钻床选择Z525立式钻床,刀具为扩孔钻,专用夹具和游标卡尺
铰Φ19.8孔至Φ20:采用立式钻床选择Z525立式钻床,刀具为铰刀,专用夹具和游标卡尺
钻孔至Φ12:采用立式钻床选择Z525立式钻床,刀具为直柄麻花钻,专用夹具和游标卡尺
扩Φ12孔至Φ12.8:采用立式钻床选择Z525立式钻床,刀具为扩孔钻,专用夹具和游标卡尺
铰Φ12.8孔至Φ13:采用立式钻床选择Z525立式钻床,刀具为铰刀,专用夹具和游标卡尺
铣轴向槽:采用卧式铣床选择X62卧式铣床,刀具为直径D为Φ80mm锯片铣刀,专用夹具和游标卡尺。
粗车左右两Φ32端面:采用车床选择CA6140车床,刀具为端车刀,专用夹具和游标卡尺。
半精车左右两Φ32端面:采用上述相同的机床与车刀,专用夹具及游标卡尺。
精车左右两Φ32端面:采用上述相同的机床与车刀,专用夹具及游标卡尺。
3.7确定切削用量及基本工时
工序3:粗、精铣50底面
工步一:粗铣50底面
1.选择刀具
刀具选取端铣刀,刀片采用YG8,
,,,。
2. 决定铣削用量
1)决定铣削深度
因为加工精度相对较高,故分两次(即粗铣、精铣)完成,则
2)决定每次进给量及切削速度
根据X51型铣床说明书,其功率为为4.5kw,中等系统刚度。
根据表查出 ,则
:
按机床标准选取=475
3)计算工时
切削工时:,,,则机动工时为
工步二:精铣50底面
1. 选择刀具
刀具选取端铣刀,刀片采用YG8,
,,,。
2. 决定铣削用量
1)决定铣削深度
因为加工精度相对较高,故分两次(即粗铣、精铣)完成,则
2)决定每次进给量及切削速度
根据X51型铣床说明书,其功率为为4.5kw,中等系统刚度。
根据表查出 ,则
按机床标准选取=475
3)计算工时
切削工时:,,,则机动工时为
工序4:粗铣上端面
1. 选择刀具
刀具选取端铣刀,刀片采用YG8,
,,,。
2. 决定铣削用量
1)决定铣削深度
因为加工精度相对不高,故一次加工即可完成,则
2)决定每次进给量及切削速度
根据X51型铣床说明书,其功率为为4.5kw,中等系统刚度。
根据表查出 ,则
按机床标准选取=900
3)计算工时
切削工时:,,,则机动工时为
工序5:钻Φ18的孔,扩孔至Φ19.8、铰孔至Φ20,倒角
工步一:钻孔至Φ18
确定进给量:根据参考文献[6]表2-7,当钢的,时,。由于本零件在加工Φ18孔时属于低刚度零件,故进给量应乘以系数0.75,则
根据Z525机床说明书,现取
切削速度:根据参考文献[6]表2-13及表2-14,查得切削速度所以
根据机床说明书,取,故实际切削速度为
切削工时:,,,则机动工时为
工步二:扩孔
利用钻头将孔扩大至,根据有关手册规定,扩钻的切削用量可根据钻孔的切削用量选取
根据机床说明书,选取
则主轴转速为,并按机床说明书取,实际切削速度为
切削工时:,,,则机动工时为
工步三:铰孔
根据参考文献[6]表2-25,,,得
查参考文献[12]表4.2-2,按机床实际进给量和实际转速,取,,实际切削速度。
切削工时:,,,则机动工时为
工步四:倒角
工序6:钻Φ12的孔,扩孔至Φ12.8、铰孔至Φ13
工步一 :钻孔至Φ12
确定进给量:根据参考文献[6]表2-7,当钢的,时,。由于本零件在加工Φ12孔时属于低刚度零件,故进给量应乘以系数0.75,则
根据Z525机床说明书,现取
切削速度:根据参考文献[12]表2-13及表2-14,查得切削速度所以
根据机床说明书,取,故实际切削速度为
切削工时:,,,则机动工时为
工步二:扩孔
利用钻头将孔扩大至,根据有关手册规定,扩钻的切削用量可根据钻孔的切削用量选取
根据机床说明书,选取
则主轴转速为,并按机床说明书取,实际切削速度为
切削工时:,,,则机动工时为
工步三:铰孔
根据参考文献[6]表2-25,,,得
查参考文献[12]表4.2-2,按机床实际进给量和实际转速,取,,实际切削速度。
切削工时:,,,则机动工时为
工序7:铣轴向槽
1.选择刀具
刀具选取锯片铣刀,刀片采用YG8,
,,,。
2. 决定铣削用量
1)决定铣削深度
因为加工余量不大,故可在一次走刀内铣完,则
2)决定每次进给量及切削速度
根据X62型铣床说明书,其功率为为7.5kw,中等系统刚度。
根据表查出 ,则
按机床标准选取=275
当=275r/min时
按机床标准选取
3)计算工时
切削工时: ,,则机动工时为
工序8:粗车、半精车、精车左右两Φ32端面
工步一:粗车左右两Φ32端面
1) 车削深度,表面粗糙度为Ra1.6,故可以选择ap=1.5mm,三次走刀(粗车、半精车、精车)即可完成所需长度。
2)机床功率为7.5kw。查参考文献[17]f=0.14~0.24mm/z。选较小量f=0.14 mm/z。
3) 查后刀面最大磨损及寿命
查参考文献[17]表3.7,后刀面最大磨损为1.0~1.5mm。
查参考文献[17]表3.8,寿命T=180min
4) 计算切削速度 按参考文献[17],查得 Vc=98mm/s,n=439r/min,Vf=490mm/s
据CA6140卧式车床
车床参数,选择nc=475r/min,Vfc=475mm/s
则实际切削速度V c=3.1480475/1000=119.3m/min
实际进给量为f zc=V fc/ncz=475/(30010)=0.16mm/z。
5)校验机床功率 查参考文献[17]Pcc=1.1kw,而机床所能提供功率为Pcm>Pcc。故校验合格。
最终确定 ap=1.5mm,nc=475r/min,Vfc=475mm/s,V c=119.3m/min,f z=0.16mm/z。
6)计算基本工时
tm=L/ Vf=(16+1.5+3)/(4750.16)=0.2697min。
总的工时:T=2 tm =0.539min
工步二:半精车左右两Φ32端面
1) 车削深度,表面粗糙度为Ra1.6,故可以选择ap=0.4mm,三次走刀(粗车、半精车、精车)即可完成所需长度。
2)机床功率为7.5kw。查参考文献[17]f=0.14~0.24mm/z。选较小量f=0.14 mm/z。
3) 查后刀面最大磨损及寿命
查参考文献[17]表3.7,后刀面最大磨损为1.0~1.5mm。
查参考文献[17]表3.8,寿命T=180min
4) 计算切削速度 按参考文献[17],查得 Vc=98mm/s,n=439r/min,Vf=490mm/s
据CA6140卧式车床
车床参数,选择nc=475r/min,Vfc=475mm/s
则实际切削速度V c=3.1480475/1000=119.3m/min
实际进给量为f zc=V fc/ncz=475/(30010)=0.16mm/z。
5)校验机床功率 查参考文献[17]Pcc=1.1kw,而机床所能提供功率为Pcm>Pcc。故校验合格。
最终确定 ap=1.5mm,nc=475r/min,Vfc=475mm/s,V c=119.3m/min,f z=0.16mm/z。
6)计算基本工时
tm=L/ Vf=(16+0.4+3)/(4750.16)=0.2553min。
总的工时:T=2 tm =0.511min
工步三:精车左右两Φ32端面
1) 车削深度,表面粗糙度为Ra1.6,故可以选择ap=0.1mm,三次走刀(粗车、半精车、精车)即可完成所需长度。
2)机床功率为7.5kw。查参考文献[17]f=0.14~0.24mm/z。选较小量f=0.14 mm/z。
3) 查后刀面最大磨损及寿命
查参考文献[17]表3.7,后刀面最大磨损为1.0~1.5mm。
查参考文献[17]表3.8,寿命T=180min
4) 计算切削速度 按参考文献[17],查得 Vc=98mm/s,n=439r/min,Vf=490mm/s
据CA6140卧式车床
车床参数,选择nc=475r/min,Vfc=475mm/s
则实际切削速度V c=3.1480475/1000=119.3m/min
实际进给量为f zc=V fc/ncz=475/(30010)=0.16mm/z。
5)校验机床功率 查参考文献[17]Pcc=1.1kw,而机床所能提供功率为Pcm>Pcc。故校验合格。
最终确定 ap=1.5mm,nc=475r/min,Vfc=475mm/s,V c=119.3m/min,f z=0.16mm/z。
6)计算基本工时
tm=L/ Vf=(16+0.1+3)/(4750.16)=0.2513min。
总的工时:T=2 tm =0.503min
工步四:倒角
4 粗车、半精车、精车Φ32两端面的夹具设计
4.1车床夹具设计特点
4.1.1车床夹具的主要类型
在车床上用来加工工件内、外回转面及端面的夹具称为车床夹具。车床夹具多数安装在主轴上;少数安装在床鞍或床身上。后一类属机床改装范畴,应用较少,不做介绍。车床夹具按工件定位方式不同分为:定心式、角铁式和花盘式等。
? (1)定心式车床夹具
在定心式车床夹具上,工件常以孔或外圆定位,夹具采用定心夹紧机构。
? (2)角铁式车床夹具
在车床上加工壳体、支座、杠杆、接头等零件的回转端面时,由于零件形状较复杂,难以装夹在通用卡盘上,因而须设计专用夹具。这种夹具的夹具体呈角铁状,故称其为角铁式车床夹具。
? (3)花盘式车床夹具
这类夹具的夹具体称花盘,上面开有若干个T形槽,安装定位元件、夹紧元件和分度元件等辅助元件,可加工形状复杂工件的外圆和内孔。这类夹具不对称,要注意平衡。
4.1.2车床夹具设计要点
? (1)车床夹具与主轴的连接方式
由于加工中车床夹具随车床主轴一起回转,夹具与主轴的连接精度直接影响夹具的回转精度,故要求车床夹具与主轴二者轴线有较高的同轴度,且要连接可靠。通常连接方式有以下几种:a.夹具通过主轴锥孔与主轴连接b.夹具通过过渡盘与机床主轴连接
? (2)对定位及夹紧装置的要求
a.为保证车床夹具的安装精度,安装时应对夹具的限位表面进行仔细找正。
b.设置定位元件时应考虑使工件加工表面的轴线与主轴轴线重合。
c.车床夹具的平衡及结构要求
对角铁式、花盘式等结构不对称的车床夹具,设计时应采用平衡装置以减少由离心力产生的振动及主轴轴承的磨损。
车床夹具一般都是在悬臂状态下工作的,为保证加工过程的稳定性;夹具结构应力求简单紧凑,轻便且安全,悬伸长度尽量小,使重心靠近主轴前支承。
为保证安全,夹具体应制成圆形,加具体上的各元件不允许伸出夹具体直径之外。此外,夹具的结构还应便于工件的安装、测量和切屑的顺利排出或清理。
4.2定位部分设计
4.2.1问题提出
本夹具主要用来粗车、半精车、精车Φ32两端面,属于工序7。
4.2.2 定位基准的选择
以50底面及2×Φ13孔作为定位基准。
4.2.3定位元件的设计
本工序选用的定位基准为50底面及2×Φ13孔,工件被完全定,所选的定位元件为:分度盘表面、圆柱销、菱形销(即削边销)。
4.3切削力和夹紧力的计算
由于本道工序主要完成端面的车削加工,切削力。由参考文献[17]得:
切削力 (5.1)
切削力矩 (5.2)
式中:
代入公式(5-2)和(5-3)得
本道工序加工端面时,车削力方向与切削力方向相同。因此进行夹紧立计算无太大意义。
4.4夹具设计及简要操作说明
本工件采用分度盘,一个圆柱销、一个削边销来定位,通过两移动压板夹紧工件,这样操作更加简单,迅速,特别适合大批量生产,总体来说这套夹具是非常不错的。能满足批量生产要求。
7 结论
本设计完成了气门摇杆轴支座零件的机械加工工艺的设计和典型夹具的设计。首先,对气门摇杆轴支座零件进行了详细的分析,绘制了零件的三维图和二维图。确定了毛坯的种类及尺寸,绘制了毛坯图。其次,根据零件自身的特点来编制机械加工工艺路线,比较了两种工艺路线,最终确定了可行的工艺路线。在确定了工艺路线后,接着选择加工设备,确定切削用量,并计算了基本工时。在完成了这些的基础上填写了相应的工艺过程卡片。最后,针对其中的三步工序设计了三套典型夹具。第一套为铣端面夹具,此夹具先以上端面为基准定位,两个V形块夹紧,这种夹紧方便、迅速。第二套为车端面夹具,用下底面为基准定位,用四个U形压板和螺母夹紧,这种夹紧可靠,省力。第3套为钻Φ13孔夹具,以下底面为定位基准,再用销轴和螺母夹紧,这种夹紧可靠,方便。三套夹具,清晰、直观的表达了定位、夹紧方案。计算了加工时的切削力和夹紧所需的夹紧力,并进行了定位误差的分析与计算。所设计的夹具可以满足加工要求,准确的定位夹紧工件。
总体来说,此次设计中制定的工艺规程是比较合理的。保证了零件的加工质量,达到了零件的相关技术要求,并尽量提高生产率。夹具设计原理正确,夹具设计可行合理。该夹具确保了加工质量,不仅工艺结构简单,而且操作简便,定位准确,夹紧迅速省力,效率较高。因此,这个设计是成功的。
本设计对同类型中小零件的工艺编制、夹具设计有借鉴意义,同时我对工艺编制和夹具设计也有了更深的理解。
参考文献
[1] 唐耀红.面向大规模定制的计算机辅助夹具设计研究 [J].机械与电子.2005(8):17-20.
[2] 廖念钊,古莹蓭,莫雨松. 互换性技术与测量 [M] . 北京:中国计量出版社,2007.6
[3] 曾爱新.谈机械加工工艺的发展趋势[J].职园培地,2002(8):26-27.
[4] 熊平,孙慧峰,焦振营.车削厚壁圆体内孔夹具设计[J] .金属加工.2008(6):54
[5] 宋冬芳.组合夹具CAD技术的研究进展 [J].太原科技,2004(5):20-21
[6] 史全富. 金属切削手册 [M] . 上海:上海科学技术出版社,2000.
[7] 白婕静,万宏强. 机械制造工程学课程设计 [M] . 北京:兵器工业出版社,2008.
[8] Alex Alblas , Hans Wortmann. Impact of product platforms on lean production systems:
evidence from industrial machinery manufacturing. [J] . IJTM,2012 (2):69-71.
[9] Serope Kalpakjian. Manufacturing Engineering and Technology [M] . USA:Prentice Hall,
2001.
[10] 谢晓文,刘书华,郑蓓蓉.计算机辅助组合夹具设计系统的研究与实现 </Article/CJFD2005-ZHJC200507015.htm>[J].
组合机床 与自动化加工技术 </Journal/C-C2-ZHJC.htm>,2005(07) </Journal/C-C2-ZHJC-2005-07.htm>:41-43.
[11] 濮良贵,纪名刚. 机械设计 [M] . 北京:高等教育出版社,2010.
[12] 李宏. 机械加工工艺手册 [M] . 北京:北京出版社,1990.
[13] Leo Alting.Manufacturing Engineering Processes [M] .2nd ed.Boca Raton,FL,U,1994.
[14] 王先逵.机械制造工艺学[M].北京:机械工业出版社,2002.
[15] 狄瑞坤,潘晓弘,樊晓燕.机械制造工程[M].杭州:浙江大学出版社.2001.
[16] 薛源顺.机床夹具设计[M].北京:机械工业出版社,2000.
[17] 赵如富.机械加工工艺人员手册[M].上海:上海科学技术出版社,2006.10.
[18] 刘震.先进机械制造工艺的技术发展趋势[J].呼伦贝尔学报 2002,10(3):96-97.
致 谢
经过近半年的忙碌和工作,我的毕业设计已经接近尾声,作为一个本科生的毕业设计,由于经验的匮乏,难免有许多考虑不周全的地方,如果没有导师的督促指导,以及一起工作的同学们的帮助,想要完成这个设计是难以想象的。在这里首先要感谢我的导师姚老师。姚老师平日里工作繁多,但在我做毕业设计的每个阶段,从查阅资料到设计草案的确定和修改,中期检查,后期详细设计,工艺规程设计和夹具设计设计等整个过程中都给予了我悉心的指导。我平时的基础不好,很多基础问题都不太懂,姚老师细心指导我设计,帮助我解决一个个难题。除了敬佩姚老师的专业水平外,他的治学严谨和科学研究的精神也是我永远学习的榜样,并将积极影响我今后的学习和工作。其次要感谢我的同学对我无私的帮助,尤其是同组的同学,在设计方面给我提供了很大帮助,正因为如此我才能顺利的完成此次毕业设计,我要感谢我的母校,是母校给我们提供了优良的学习环境。在将要毕业的这一刻,我要感谢我的导师姚老师,还有系主任老师以及其他各位老师,四年生活中,您们不仅教会了我专业知识,更教会了我怎么做人。再次感谢您们!
QQ 29467473