


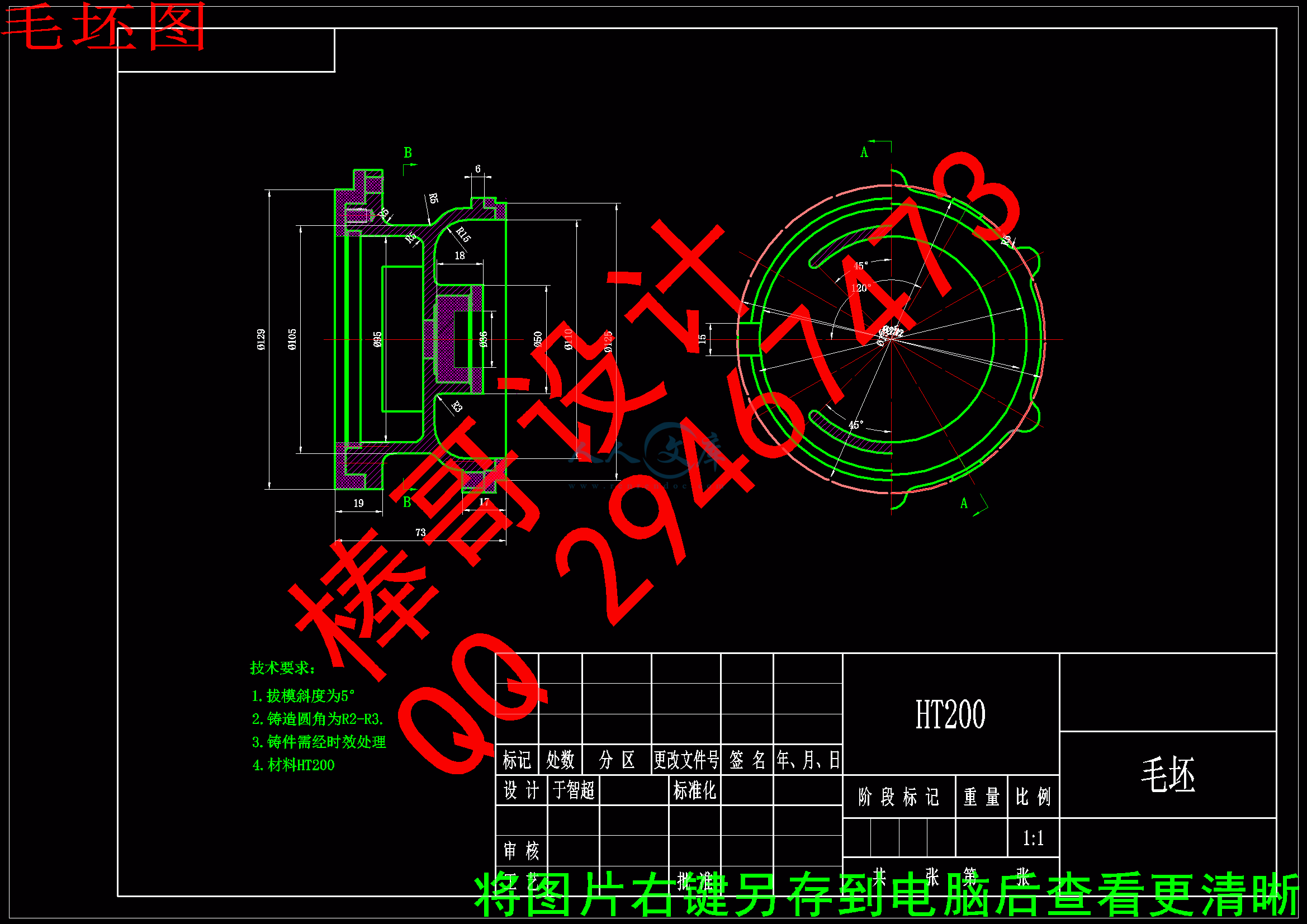
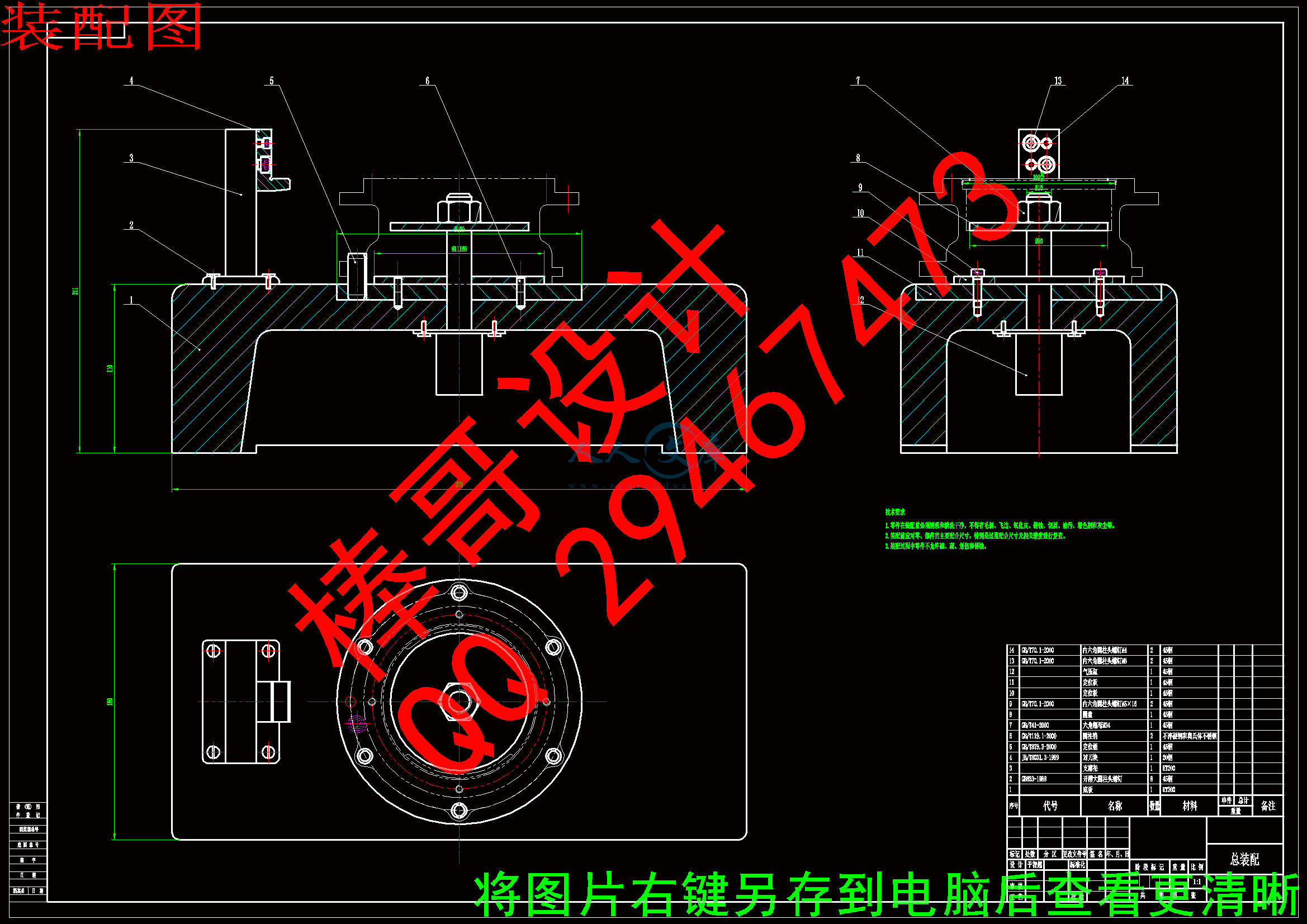

棒哥设计QQ 29467473
辽宁工程技术大学
机 械 制 造 技 术 基 础
课 程 设 计
题 目:连接座加工工艺及左端面铣削夹具设计
班 级: 加工09-1 班
姓 名: 于智超
学 号: 0907070123
指导教师: 张兴元
完成日期: 2012-9-11
任 务 书
一、设计题目:连接座加工工艺及左端面铣削夹具设计
二、原始资料
(1) 被加工零件的零件图 1张
(2) 生产类型:(中批或大批大量生产)
三、上交材料
1.所加工的零件图 1张
2.毛坯图 1张
3.编制机械加工工艺过程卡片 1套
4.编制所设计夹具对应的那道工序的机械加工工序卡片 1套
5.绘制夹具装配图(A0或A1) 1张
6.绘制夹具中1个零件图(A1或A2。装配图出来后,由指导教师为学生指定需绘制的零件图,一般为夹具体)。 1张
7.课程设计说明书,包括机械加工工艺规程的编制和机床夹具设计全部内容。(约5000-8000字) 1份
四、进度安排
本课程设计要求在3周内完成。
1.第l~2天查资料,绘制零件图。
2.第3~7天,完成零件的工艺性分析,确定毛坯的类型、制造方法,编制机械加工工艺规程和所加工工序的机械加工工序卡片。
3.第8~10天,完成夹具总体方案设计(画出草图,与指导教师沟通,在其同意的前提下,进行课程设计的下一步)。
4.第11~13天,完成夹具装配图的绘制。
5.第14~15天,零件图的绘制。
6.第16~18天,整理并完成设计说明书的编写。
7.第19天~21天,完成图纸和说明书的输出打印。答辩
五、指导教师评语
该生设计的过程中表现 ,设计内容反映的基本概念及计算 ,设计方案 ,图纸表达 ,说明书撰写 ,答辩表现 。
综合评定成绩:
指导教师
日 期
摘要
本次课程设计的目的是通过课程设计,对所学习的知识进行一次综合性的应用,通过在课程设计中,不断发现问题,并且解决问题来提高自己的水平。
本次设计主要内容:设计连接座的机械加工工艺规程和铣削座端面的工艺装备并绘制出支架零件图、毛坯图、夹具装配图,夹具中的一个零件图,填写工艺卡片,编制课程设计说明书。
我主要铣削连接座的左端面,通过气压缸与圆盘对工件进行夹紧,用定位板以及定位销对工件进行定位,这样工件就会在稳定的状态下被加工。
Abstract
This course is designed through the curriculum design, to study the knowledge on a comprehensive application, through in the curriculum design, and constantly find out problems, and solves the problem to improve their level.
This design main contents: the design of the seat connection machining process planning and milling seat face of process equipment and draw the support part drawing, blank drawing, clamp assembly drawing, fixture of one of the part drawing, fill in process card, compile curriculum design specification.
I mainly milling connection seat left face, through the pneumatic cylinder and disc to workpiece clamping, with locating plate and positioning pin on the location, so that the workpiece will be in the stable state is processing.
目录
1.零件的工艺分析及生产类型的确定5
1.1零件的工艺分析5
1.2确定零件的生产类型7
2选择毛坯,确定毛坯尺寸,设计毛坯图8
2.1选择毛坯8
2.2确定毛坯尺寸8
2.3设计毛坯图9
3工艺规程的设计10
3.1选择定位基准10
3.2零件表面加工方法的选择10
4机械加工余量、工序尺寸的确定15
五、确立切削用量及基本工时17
5.1工序六17
5.2工序八19
5.3工序十21
5.4车φ40H7的端面及孔至φ39H821
5.5工序十四23
5.6工序十五24
六、夹具的设计25
心得体会26
参考文献27
1.零件的工艺分析及生产类型的确定
1.1零件的工艺分析
题目所给的零件是离心式微电机水泵上的连接座。该零件的作用由其名称可知,是在两个机器部件中间起连接过渡作用的。通过连接座传递扭矩,以达到带动相连零件转动目的。零件图如下所示
根据零件图,可以初步拟定零件的加工表面其间有一定位置要求。为此以下是此连接座需要机械加工的表面以及加工表面之间相对位置要求的分析,分述如下:
1、在零件图中,主视图上φ40H7的孔表面粗糙度上限值均为3.2um,有尺寸公差要求,其轴线为该零件形位公差的基准A;
2、在零件图中,主视图上的φ40H7的孔右端面的表面粗糙上限值为25um,无尺寸公差要求,且都无形位公差要求;
3、在零件图中,主视图上的φ121h7的外圆面,其表面粗糙度上限值为3.2um,与基准A之间有跳动要求,其公差为0.04mm;其左端台阶面的表面粗超度上限值为6.3um,与基准A之间有跳动要求,其公差为0.05mm;
4、在零件图中,主视图上φ17.5的孔,其表面粗糙度上限值为25um,无尺寸公差要求,也无形位公差要求;其孔的右端为深度1mmφ32的沉孔,其表面粗超度上限值为25um;
5、在零件图中,主视图上,φ125h6的外圆面,表面粗糙度上限值为3.2um,有尺寸公差要求,也有相对于基准A的形位公差跳动要求,公差值为0.05mm;其左端面和右端台阶面的表面粗糙度上限值都为6.3um,都有相对于基准A跳动形位公差要求,公差值为0.05mm;
6、在零件图中,主视图上,φ100H7的内孔面,表面粗糙度上限值为3.2um,有尺寸公差要求,也有相对于基准A的形位公差跳动要求,公差值为0.05mm;其孔的右端台阶面,表面粗糙度值上限值为25um;
7、在零件图中,左视图上,有6个φ7mm的孔,其表面粗糙度上限值为25um,无尺寸公差要求,也无位置度要求;
8、在零件图中,左视图上,有3个φ7mm的孔,其表面粗糙度上限值为25um,无尺寸公差要求,也无位置度要求;
9、在零件图中,左视图上,有4个7级精度的M5螺纹孔,螺纹底孔深度为12mm,螺纹深度为10mm,其表面粗糙度上限值为25um,无尺寸公差要求,也无位置度要求;
10、有零件的使用情况和加工要求可知,该零件的不加工表面为不去出材料,其表面粗糙度质量由铸造工艺保证;
11、零件的材料为 HT200灰铸铁;
12、零件毛坯通过铸造得到,不许有气孔、疏松、夹渣、裂纹等缺陷,并要求铸造后进行时效处理。
根据各加工方法的经济精度及一般机床所能达到的位置精度,该零件没有很难加工的表面尺寸,上述表面的技术要求采用常规加工工艺均可以保证,对于这两组加工表面而言,可以先加工其中一组表面,然后借助于专用夹具加工另一组表面,并且保证它们的位置精度要求。
1.2确定零件的生产类型
零件材料为HT200。考虑零件在使用过程中所受冲击不大,零件结构又比较简单,故选择铸件毛坯。假定该零件的生产纲领是5000件每年。
假设:Q=5000台/年,m=1件/台;结合生产实际,备品率a%和废品率b%分别取4%和7%。代入公式N=Qm(1+a%)(1+b%)得:
N=5000台/年1件/台(1+10%)(1+1%)=5237件/年
该连接座的重量约为3kg,由附表(1)知,连接座属轻型零件;由附表(2)知,该拨叉的生产类型为大批生产。
附表(1)不同机械产品的零件质量型别表
机械产品类型加工零件的质量/kg
重型零件中型零件轻型零件
电子工业机械>304~30<4
机床>5015~50<15
重型机械>2000100~2000<100
附表(2)机械加工零件生产类型的划分
零件特征 年生产纲 领/件 生产类型 产品类型
重型零件中型零件轻型零件
单件生产5以下20以下100以下
成 批 生 产小批5~1020~200100~500
中批100~300200~500500~5000
大批300~1000500~50005000~50000
大量生产1000以上5000以上50000以上
2选择毛坯,确定毛坯尺寸,设计毛坯图
2.1选择毛坯
该零件材料为HT200,参照零件图上所给的该零件不加工表面的粗糙度要求,对于不进行机械加工的表面的粗糙度由铸造工艺保证,又由于该零件年产量为5000件,属大批生产,且该零件的外形尺寸不复杂,故采用金属型铸造。这从提高生产率,保证加工精度上考虑也是应该的。
2.2确定毛坯尺寸
由参考文献[1]表5-1可知,该种铸件的尺寸公差等级CT为8~10级,加工余量等级由表5-5查得MA为D~F级,故取CT为10级,MA为E级。
参阅文献资料可知,可用查表得方法确定各加工表面的总余量,但由于查表确定的总余量值各不相同,一般情况下,除非有另有规定,要求的机械加工余量适用于整个毛坯铸件,即对所有需要机械加工的表面只规定一个值,且该值应根据最终机械加工后成品铸件的最大轮廓尺寸,在相应的尺寸范围内选取。
由尺寸图可知,该零件的最大轮廓尺寸为156mm,由参考文献[1]表5-3查得,CT为3.6mm,由表5-4查得RMA为1.1mm。故取所有加工表面额单边余量为4mm。
本零件的毛坯,虽然根据标准设计要求来说,机械加工余量应该是4mm,但有几个尺寸,根据零件的结构特征需要需要适当调整,比如φ125h6的毛坯外圆尺寸,由零件图可知,应该设计为φ138mm,φ121h7的毛坯外圆尺寸,由零件图可知,应该设计为φ130mm,φ17.5mm的孔,有铸造技术要求可知,应该铸造成实心的。9个φ7mm的孔及4个M5的螺纹孔,都铸造成实心的。无需考虑机械切削余量的设计。
其毛坯图外型尺寸的公差要求及公差值详见毛坯图。
2.3设计毛坯图
根据上面毛坯尺寸的确定,将零件图转变为毛坯图。详见毛坯零件图
3工艺规程的设计
3.1选择定位基准
基面选择是工艺规程设计中的重要工作之一。基面选择得正确与合理可以使加工质量得到保证,生产率得以提高。
1、粗基准的选择:对于零件而言,尽可能选择不加工表面为粗基准。而对有若干个不加工表面的工件,则应以与加工表面要求相对位置精度较高的不加工表面作粗基准。根据这个基准选择原则,选取零件的φ125h6mm外圆的左端端面为粗基准。
2、精基准的选择:主要应该考虑基准重合的问题。当设计基准与工序基准不重合时,应该进行尺寸换算。
3.2零件表面加工方法的选择
由上诉的零件分析和查阅有关文献,根据本零件的加工面要求,主要用到的机床有铣床和钻床,铣床主要是用来铣削端面的,钻床是用来钻孔和攻丝的!
根据零件的表面粗糙度质量要求和尺寸公差要求,对需要机械加工的各端面和孔,现制定加工方法如下:
1、对于φ125h6的左端面和φ121h6的右端面,其表面粗糙度上限值分别为6.3um和12.5um,根据附表(3)、(4)可知,这些端面可通过粗铣和半精铣能获得要求的表面粗糙度质量,这里采用铣削的原因是考虑到基准的确定及工艺方面的需求;
2、对于φ40H7的孔,其内表面的表面粗糙度上下值为3.2um,根据由附表(3)、(4)可知,此孔可通过粗车、半精车的加工方法,获得要求的表面粗糙度质量和尺寸公差要求;
3、对于φ17.5的孔,其内表面的表面粗糙度上限值为25um,根据由附表(3)、(4)可知,此孔可通过钻的加工方法,获得要求的表面粗糙度质量和尺寸公差要求;
4、对于φ32深1mm的沉孔,其内表面的表面粗糙度上限值为25um,根据由附表(3)、(4)可知,此孔可通过扩孔的加工方法,获得要求的表面粗糙度质量和尺寸公差要求;
5、对于φ121h7的外圆,其表面的表面粗糙度上限值为3.2um,根据由附表(3)、(4)可知,此外圆表面可通过粗车、半精车的加工方法,获得要求的表面粗糙度质量和尺寸公差要求;
6、对于φ121h7外圆的左端台阶面,其表面的表面粗糙度上限值为6.3um,根据由附表(3)、(4)可知,此面可通过粗车、半精车的加工方法,获得要求的表面粗糙度质量和尺寸公差要求;
7、对于φ125h6的外圆,其表面的表面粗糙度上限值为3.2um,根据由附表(3)、(4)可知,此外圆表面可通过粗车、半精车的加工方法,获得要求的表面粗糙度质量和尺寸公差要求;
8、对于φ125h6外圆的右端台阶面,其表面的表面粗糙度上限值为6.3um,根据由附表(3)、(4)可知,此面可通过粗车、半精车的加工方法,获得要求的表面粗糙度质量和尺寸公差要求;
9、对于φ100H7的内圆,其表面的表面粗糙度上限值为3.2um,根据由附表(3)、(4)可知,此外圆表面可通过粗车、半精车的加工方法,获得要求的表面粗糙度质量和尺寸公差要求;
10、对于6-φ7的孔,其表面的表面粗糙度上限值为25um,根据由附表(3)、(4)可知,此孔可通过一次钻削的加工方法,获得要求的表面粗糙度质量和尺寸公差要求;
11、对于3-φ7的孔,其表面的表面粗糙度上限值为25um,根据由附表(3)、(4)可知,此孔可通过一次钻削的加工方法,获得要求的表面粗糙度质量和尺寸公差要求;
12、对于4-M5-7H的螺纹孔,可先用钻床钻削底孔,然后钳工攻丝获得。
附表(3)平面加工的经济精度与表面粗糙度
序号加工方法经济精度(IT)表面粗糙度选用范围
1粗车11~1312~6.3未淬硬钢、铸铁、有色金属端面加工
2粗车-半精车8~96.3~3.2
3粗车-半精车-精车6~71.6~0.8
4粗车-半精车-磨削7~90.8~0.2钢、铸铁端面加工
5粗刨(粗铣)-半精刨(半精铣)11~126.3~1.6不淬硬的表面
6粗刨(粗铣)-半精刨(半精铣)7~96.3~1.6
7粗刨(粗铣)-半精刨(半精铣)-精刨(精铣)7~83.2~1.6
8粗铣-拉6~90.8~0.2大量生产未淬硬的小平面
9粗刨(粗铣)-精刨(精铣)-宽刃精刨6~70.8~0.2未淬硬的钢件、铸铁件及有色金属件
10粗刨(粗铣)-半精刨(半精铣)-精刨(精铣)-宽刃精刨50.8~0.2
附表(4)内圆表面加工的经济精度与表面粗糙度
序号加工方法经济精度(IT)表面粗糙度 Ra(μm)适用范围
1钻12~1312.5加工未淬硬钢及铸铁的实心毛坯,孔径<15-20mm
2钻-铰8~103.2~1.6
3钻-粗铰-精铰7~81.6~0.8
4钻-扩10~1112.5~6.3同上,孔径>(15-20)mm
5钻-扩-粗铰-精铰7~81.6~0.8
6钻-扩-铰8~93.2~1.6
7钻-扩-机铰-手铰6~70.4~0.1
8钻-(扩)-拉7~91.6~0.1大批量生产,精度视拉刀精度决定
9粗镗(或扩孔)11~1312.5~6.3毛坯有铸孔或锻孔的未淬火钢及铸件
10粗镗(粗扩)-半精镗(精扩)9~103.2~1.6
11扩(镗)-铣9~103.2~1.6
12粗镗(扩)-半精镗(精扩)-精镗(铰)7~81.6~0.8
3.3制定工艺路线
制定工艺路线,在生产纲领确定的情况下, 根据零件的几何形状、尺寸精度及位置精度等技术要求来制定工艺路线。可以考虑采用万能性机床配以专用工卡具,并尽量使工序集中来提高生产率。除此之外,还应当考虑经济效果,以便使生产成本尽量下降。
根据老师给的参考工艺,现制定两种工艺路线:
工艺路线一:
工序一 铸造
工序二 喷砂
工序三 人工时效
工序四 铣 以左端面为粗基准 粗铣右端面;
工序五 铣 以右端面为精基准 铣左端面,保证总长70mm;
工序六 半精铣 以左端面为精基准半精铣右端面;
工序七 半精铣 以右端面为精基准半精铣左端面;
工序八 车 以左端面及φ125h6的毛坯外圆定位夹紧,钻φ17.5的孔至图示尺寸,车φ40H7的端面及孔至图示尺寸。车φ32×1mm的沉台,倒角;
工序九 车 以φ40H7的孔及其端面为定位基准,车φ125h6的端面及外圆至图示尺寸,车阶梯左端面9mm,车φ100H7的孔至图示尺寸,倒角;
工序十 以φ100H7的孔及端面定位夹紧,车φ121h7的端面,保证总长69mm,车φ121h7的外圆及5mm的沉台,倒角;
工序十一 以φ100H7的孔及端面定位,钻6-φ7的孔;
工序十二 以φ121h7的孔及端面定位,钻3-φ7的孔;
工序十三 以φ100H7的孔,钻4-M5的螺纹底孔,攻4-M5-7H深10的螺纹;
工序十四 按图纸检验各部尺寸;
工序十五 入库。
工艺路线二:
工序一 铸造
工序二 喷砂
工序三 人工时效
工序四 对非加工表面涂刷防锈漆;
工序五 划线 照顾各部尺寸,划线;
工序六 铣 以左端面为粗基准,根据划线粗铣右端面;
工序七 铣 以右端面为精基准,根据划线铣左端面,保证总长73mm;
工序八 半精铣 以左端面为精基准半精铣右端面;
工序九 半精铣 以右端面为精基准半精铣左端面,保证总长70mm;
工序十 车 以左端面及φ125h6的毛坯外圆定位夹紧,钻φ17.5的孔至图示尺寸,车φ40H7的端面及孔至φ39H8;
工序十一 车 以φ39H8的孔及右端面定位,车左端面,车φ125h6的外圆至φ128h8,并车其深度为8.5mm(同时车右端台阶面),车φ100H7的孔至φ99H8保证深度7mm;
工序十二 车 调头,以φ99H8的孔定位,车φ121h7的右端面,保证总长69mm,车φ40H7的右端面,保证尺寸16mm及mm,车φ40H7的孔至尺寸,车φ32深度为1mm的沉孔,车φ121h7的外圆至尺寸,车其左台阶面至尺寸,倒角;
工序十三 车 调头,以φ40H7的孔及其端面为定位基准,车φ125h6的端面及外圆至图示尺寸,车阶梯左端面9mm,车φ100H7的孔至图示尺寸,倒角;
工序十四 以φ100H7的孔及端面定位,钻6-φ7的孔;
工序十五 以φ121h7的孔及端面定位,钻3-φ7的孔;
工序十六 以φ100H7的孔,钻4-M5的螺纹底孔,攻4-M5-7H深10的螺纹;
工序十七 按图纸检验各部尺寸;
工序十八 入库。
对比工艺路线一和工艺路线二,显然是工艺路线二较为合理和细致,在工艺路线一中,很明显,对于基准A,是φ40H7的轴线,这个基准没有很好的进行确定。因为,在以φ125h6的毛坯外圆定位时,是以粗基准来确定基准A的,这样的基准由于装夹和加工误差较大,之后再以此基准加工其他表面时,必然会造成误差。而工艺路线二,采用了互为基准的原则,安排了粗精加工过程,这样先是粗基准的表面在一次互换后就变成了精基准,这样保证了各自的精度,从而保证了零件的质量。
4机械加工余量、工序尺寸的确定
连接座,零件材料为HT200,硬度157~236HB,生产类型大批量,砂型铸造属型铸造毛坯。据以上原始资料及加工路线,分别确定各加工表面的机械加工余量、工序尺寸如下:
4.1查《机械制造工艺设计简明手册》得:
铣削加工余量为:
粗铣 2-4mm
半精铣 1-2mm
精铣 0-1mm
车削加工余量为:
粗 车 1-2mm
半精车 0.8mm
精车 0.3mm
圆孔拉削余量为:
D>18-25 0.6mm
D>25-30 0.7mm
D>30-40 0.8mm
镗孔加工余量为:
粗镗 0.3mm
半精镗 0.2mm
精镗 0.1mm
4.2根据查《机械制造工艺设计简明手册》所得的加工余量可以确定毛配总加工余量如下表:
工序号工步号加工内容加工余量/mm精度等级工序尺寸/mm表面粗糙度
1铸造
2喷砂
3人工时效
4对非加工表面涂刷防锈漆
5照顾各部尺寸,划线
6以左端面为粗基准,按划线粗铣右端面2.5IT974.512.5
7以右端面为精基准,按划线粗铣左端面2.5IT97212.5
8以左端面为粗基准,半精铣铣右端面1IT97112.5
9以右端面为精基准,半精铣铣左端面1IT97012.5
1001以左端面及φ125h6的毛坯外圆定位夹紧,钻φ17.5的孔至图示尺寸8.75IT9φ17.525
02车φ40H7的端面及孔至φ39H83.5IT8φ39H86.3
1101以φ39H8的孔及右端面定位,车左端面0.5IT769.56.3
02车φ125h6的外圆至φ128h8,并车其深度为8.5mm(同时车右端台阶面)5IT8φ128h86.3
03车φ100H7的孔至φ99H8保证深度7mm2IT8φ99H86.3
1201调头,以φ99H8的孔定位,车φ121h7的右端面,保证总长69mm0.5IT7696.3
02车φ40H7的右端面,保证尺寸16mm及mm,4TI91612.5
03车φ40H7的孔至尺寸,0.5IT7φ40H73.2
04车φ32深度为1mm的沉孔,1IT9φ3212.5
05车φ121h7的外圆至φ122,车其左台阶面至尺寸,倒角4.5IT8φ121h76.3
1301调头,以φ40H7的孔及其端面为定位基准,车φ125h6的端面及外圆至图示尺寸1.5IT7φ125h63.2
02车阶梯左端面9mm,车φ100H7的孔至图示尺寸,倒角0.5IT7φ100H73.2
14以φ100H7的孔及端面定位,钻6-φ7的孔;3.5IT9φ725
15以φ121h7的孔及端面定位,钻3-φ7的孔3.5IT9φ725
16以φ100H7的孔,钻4-M5的螺纹底孔,攻4-M5-7H深10的螺纹
17钳工去毛刺
18按图纸检验各部尺寸
19入库
五、确立切削用量及基本工时
5.1工序六
1 加工条件
工件材料:HT200,σb=157~236MPa,铸造;
加工要求:以零件的上左端面(在尺寸图中,主视图的左面)为定位基准,粗铣右端面;
机 床:铣床,X62W卧式铣床。
刀 具:高速钢圆柱铣刀。铣刀直径d=100mm,齿数为10,刀宽160mm,铣削宽度ae=8mm,铣削深度ap=160mm。故据参考文献[1]表5-143查得刀具的基本形状,由于加工铸铁σb>150HBS,故选前角γo=+10°后角αo=12°,副后角αo’=6°。已知铣削宽度ae=2.5mm,铣削深度ap=142mm。机床选用X62W型卧式万能铣床。
2 切削用量
(1)确定每齿的进给量fz
根据参考文献[1]表5-144,X62W型卧式铣床的功率为7.5kW,工艺系统刚性为中等,细齿盘铣刀加工铸铁,查得每齿的进给量fz=0.15~0.3mm/z,现取fz=0.2mm/z。
(2)选择铣刀磨钝标准及耐用度
根据参考文献[1表]5-148,用高速圆柱铣刀粗加工铸铁,铣刀刀齿后刀面最大磨损量为0.8mm,铣刀直径d=100mm,耐用度T=180min。
(3)确定切削速度和工作台每分钟进给量fMZ
其中 Cv=35,qv=0.2,xv=0.1,yv=0.4,uv=0.5,pv=0.1,m=0.2,kv=1.0。
将上述数据带入公式可得
V=13.1404m/min
根据参考文献[1]表5-75,X62W型卧式铣床主轴的转速表,选择n=37.5r/min=0.625r/s,则实际切削速度v=0.19625m/s,工作台每分钟的进给量
fMZ=0.2×10×37.5=75mm/min
根据参考文献表[1]5-76,X62型卧式铣床工作台进给量表,选择fMZ=75mm/min,则实际每齿的进给量。
(4)校验机床功率
根据参考文献[1]表2-18中的计算公式,铣削是的功率(kW)为
式中CF=650,xF=0.10,yF=0.72,uF=0.86,qF=0.86,ap=142mm,ae=2.5mm,fz=0.2,z=10,d=100mm,n=37.5r/min,kFC=0.63。
将上述数据带入公式可得
Fc=88.4N
V=0.19625m/s,则
Pc=0.0173kW
X62W型卧式铣床主电动机功率为7.5kW,故所选用切削用量可以采用,所确定的切削用量为fz=0.2mm/z,fMZ=75mm/min,n=37.5r/min,v=0.19625m/s。
3基本时间
根据参考文献[1]表2-28,圆柱铣刀铣面的基本时间为
则l1=19mm,l2=4mm,fMZ=75mm/min,i=1;
Ti=2.2min,辅助时间5min。
5.2工序八
1、 加工条件
工件材料:HT200,σb=157~236MPa,铸造;
加工要求:以零件的上左端面(在尺寸图中,主视图的左面)为定位基准,精铣右端面;
机 床:铣床,X62W卧式铣床。
刀 具:高速钢圆柱铣刀。铣刀直径d=100mm,齿数为10,刀宽160mm,铣削宽度ae=8mm,铣削深度ap=160mm。故据参考文献[1]表5-143查得刀具的基本形状,由于加工铸铁σb>150HBS,故选前角γo=+10°后角αo=12°,副后角αo’=6°。已知铣削宽度ae=1mm,铣削深度ap=142mm。机床选用X62W型卧式万能铣床。
2、 切削用量
(1)确定每齿的进给量fz
根据参考文献[1]表5-144,X62W型卧式铣床的功率为7.5kW,工艺系统刚性为中等,细齿盘铣刀加工铸铁,查得每齿的进给量fz=0.15~0.3mm/z,现取fz=0.2mm/z。
(3)选择铣刀磨钝标准及耐用度
根据参考文献[1表]5-148,用高速钢盘铣刀粗加工铸铁,铣刀刀齿后刀面最大磨损量为0.8mm,铣刀直径d=100mm,耐用度T=180min。
(3)确定切削速度和工作台每分钟进给量fMZ
其中 Cv=35,qv=0.2,xv=0.1,yv=0.4,uv=0.5,pv=0.1,m=0.2,kv=1.0。
将上述数据带入公式可得
V=28.667m/min
根据参考文献[1]表5-75,X62W型卧式铣床主轴的转速表,选择n=95r/min=1.583r/s,则实际切削速度v=0.4972m/s,工作台每分钟的进给量
fMZ=0.2×10×95=190mm/min
根据参考文献表[1]5-76,X62型卧式铣床工作台进给量表,选择fMZ=190mm/min,则实际每齿的进给量。
(5)校验机床功率
根据参考文献[1]表2-18中的计算公式,铣削是的功率(kW)为
式中CF=650,xF=0.10,yF=0.72,uF=0.86,qF=0.86,ap=142mm,ae=1mm,fz=0.2,z=10,d=100mm,n=95r/min,kFC=0.63。
将上述数据带入公式可得
Fc=40.2N
V=0.4972m/s,则
Pc=0.02kW
X62W型卧式铣床主电动机功率为7.5kW,故所选用切削用量可以采用,所确定的切削用量为fz=0.2mm/z,fMZ=190mm/min,n=95r/min,v=0.4972m/s。
3、基本时间
根据参考文献[1]表2-28,圆柱铣刀铣面的基本时间为
则l1=19mm,l2=4mm,fMZ=190mm/min,i=1;
Ti=0.8684min,辅助时间5min。
5.3工序十
1、 加工条件
工件材料:HT200,σb=157~236MPa,铸造;
加工要求:以左端面及φ125h6的毛坯外圆定位夹紧,钻φ17.5的孔至图示尺寸,车φ40H7的端面及孔至φ39H8;
机 床: C620-1车床
刀 具: YG6硬质合金车刀,根据参考文献[1]表5-112,由于C620-1车床中心高为200mm,故选刀杆尺寸B×H=16mm×25mm(镗孔时,使用相同的刀片不同的刀杆),刀片厚度4.5mm。根据表5-113,选择刀具前角γo=12°后角αo=6°,主偏角Kr=90°,副偏角Kr‘=10°,刃倾角λs=0°,刀尖过渡圆弧半径R=0.8mm。及φ17.5mm的锥柄高速钢麻花钻头。
5.4车φ40H7的端面及孔至φ39H8
1)、切削用量
(1)确定被吃刀量
粗车单边余量为ap=3.5mm
(2)确定进给量
根据表5-114,镗刀刀杆尺寸为φ16mm, 工件孔的直径为30~40mm时,根据参考文献[1]表5-115查得的进给量选择f=0.15~0.25mm/r。取进给量为f=0.25mm/r。
(3)确定的进给量善需满足机床进给机构强度的要求,故需进行校验。
根据表参考文献[1]5-55,车床进给机构允许的进给力F=3530N。
根据参考文献[1]表5-124, 、、、、时,进给力。
的修正系数1 , 1,1.17,故实际进给力为
=1140×1.17=1333.8N
,所选的进给量=0.25mm/r可用。
(4)选择刀具磨钝标准及耐用度
根据参考文献[1]表5-119,车刀后刀面最大磨损量取 1mm,车到耐用度T=30min。
(5)确定切削速度
根据参考文献[1]表5-121 ,当用YG6硬质合金车刀加工 , ,切削速度。
根据参考文献[1]表2-8,切削速度的修正系数为0.8,0.65,0.81,,,故
=90×0.8×0.65×0.81×1.15×1=43.594m/min
=355.99r/min
按参考文献[1]表5-56车床转速,选择C620-1车床的标准转速,则实际切削速度。
(6)校验机床功率
由表5-126,当、、、时,
切削功率的修正系数为,, ,,,故实际切削时的功率为。
根据参考文献[1]表5-59,当时,机床主轴允许功率,,故所选切削用量可在C620-1车床上进行。
最后确定的切削用量为
,,,
2)、基本时间
根据参考文献[1]表2-21,车削基本时间为
则=14.3s,辅助时间3min。
5.5工序十四
1、 加工条件
工件材料:HT200,σb=157~236MPa,铸造;
加工要求:钻6-φ7mm的孔;
机 床:摇臂钻床Z3025。
刀 具:φ7mm的高速钢麻花钻钻头。
2、选择切削用量
(1)决定进给量
根据参考文献[1]表5-127,可查得进给量f=0.36~0.44mm/r,现取f=0.4mm/r
(2)选择钻头磨顿标准及耐用度
根据参考文献[1]表5-130,钻头后刀面的最大磨损量为0.8mm,耐用度T=60min。
(3)确定切削速度
根据参考文献[1]表5-133,查得v=13m/min,n=591.45r/min。根据Z3025摇臂钻床说明书选择主轴实际转速n=600r/min。则实际切削速度为v=13.188m/min
3、基本时间
根据参考文献表[1]2-26中的计算公式
i
L=8+5=13mm,f=0.4mm/r,n=600r/min,带入上式得
,辅助时间5min。
5.6工序十五
1、 加工条件
工件材料:HT200,σb=157~236MPa,铸造;
加工要求:钻3-φ7mm的孔;
机 床:摇臂钻床Z3025。
刀 具:φ7mm的高速钢麻花钻钻头。
2、选择切削用量
(1)决定进给量
根据参考文献[1]表5-127,可查得进给量f=0.36~0.44mm/r,现取f=0.4mm/r
(2)选择钻头磨顿标准及耐用度
根据参考文献[1]表5-130,钻头后刀面的最大磨损量为0.8mm,耐用度T=60min。
(4)确定切削速度
根据参考文献[1]表5-133,查得v=13m/min,n=591.45r/min。根据Z3025摇臂钻床说明书选择主轴实际转速n=600r/min。则实际切削速度为v=13.188m/min
3、基本时间
根据参考文献表[1]2-26中的计算公式
i
L=10+5=15mm,f=0.4mm/r,n=600r/min,带入上式得
,辅助时间5min。
将前面进行的工作所得的结果,填入工艺文件。
六、夹具的设计
6.1夹具设计原理
工件定位定位如图所示,Z轴方向,在夹具内部有气压缸,与气压缸连杆上有一圆盘,通过气压缸带动圆盘上下移动,可以限制Z轴方向的移动,在工件下方有一定位板,与工件间隙配合,限制工件X,Y的移动以及旋转,定位板与下方定位板通过销连接在夹具底板上,下方定位板上有两个定位销,以限制工件Z方向的旋转。这样就限制了工件的6个自由度。
6.2受力分析
(见《切削手册》表3.28)
其中,=650,=3.1mm,=1.0,=0.08mm,=0.72,=40mm(在加工面上近似测量值),=0.86,=125mm,=0.86,=0,z=20
所以 N
由于是垂直铣削,所以水平分力=0N
垂直分力=1456N
在计算切削力时,必须把安全系数考虑在内。安全系数K=K1K2K3K4。
其中K1为基本安全系数1.2
K2为加工性质系数1.0
K3为刀具钝化系数1.0
K4为断续切削系数1.0。
所以 F′=KFH=1.2×1.1×476=628.32N
心得体会
通过这次机械课程设计,我经历了一次完整的将二维图纸上的图形曲线化为在国家工业生产中可以使用的真正零件的设计过程。该课程设计所涉及的问题是一个机械专业的大学生所必须掌握的。这将使我们脱离纸上谈兵,得以真正将自己设计的东西化为看得见,摸得着的实体。
十年的纸上谈兵也比不上一次真刀真枪的实战训练,这次课程设计对我的专业知识及实际动手能力,考虑问题能力,把握全局能力都是一次很好的锻炼。
在相当长的一个可以预见的历史时期内,机械工业仍然是衡量一个国家现代化程度与工业化进程的最主要标准,微电子工业与生物技术等产业要做到彻底脱离机械工业而独立目前看来还没有可能。而机械工业的最基本组成部分——零件的加工制造,当然的成为衡量机械发展水平的重要指标。
即使经过几十年的积累,我国在零部件制造方面也只是在低端徘徊,产品也以低端为主。精密性和工艺性水平仍远远没有达到国际先进水平。即使在一些名为国产的设施上,进口件扮演的往往是核心角色。此次汶川地震中救灾的直升机主力——20世纪80年代中美蜜月期时购买的“黑鹰”直升机——至今仍然需要每年从美国进口零备件以维持运转。这可以看做我国机械工业的一个缩影。
当前,随着中国“龙芯”的问世,本为美国与日本控制的计算机处理器核心技术首次被第三世界国家掌握,计算机技术的发展必然带动高精密机械加工技术。在可以预见的范围内,机械零件加工制造将向着一台机床加工多种零件的集成化,以纳米技术为前沿的精密化等方向发展。但对于我国来讲,机械制造行业尚不具备一次就整体性的跳跃到高端的世界领先水平的条件。
如果把机械制造行业比作一个人,美国与日本掌握着最高技术而坐在“头”的位置上,西欧与俄罗斯等国正坐在“腰”上。我国就是低端的脚部。而世界的大部分产品实际上正是由技术成熟且成本可以接受的“腰”部技术水准建立的。我国摊子大,底子薄,正在进行一次极为重要的产业升级。汽车行业的成果和大飞机计划重新上马就是标志。我国要从坐“脚”望“腰”变成坐“腰”望“头”,是需要巩固整体性的技术水平。
作为机械技术的基础,零件加工需要更多的人才与创新。这是每一个机械专业的大学生的必然追求。
参考文献
[1]哈尔滨工业大学 .《机床夹具设计》[M].上海科学技术出版社 .1990。
[2]顾崇衡 .《机械制造工艺学》[M].陕西科学出版社.1995。
[3]邹青 .《机械制造技术基础课程设计指导教程》[M] . 机械工业出版社,200.8。
[4]崇凯 .《机械制造技术基础课程设计指南》[M].化学工业出版社 .2006.12。
[5]周开勤 .《机械零件手册》[M].高等教育出版社 .1994。
[6]大连组合机床研究所 .《组合机床设计》[M].机械工业出版社 .1978。
[7]李云..《机械制造及设备指导手册》[M].北京:机械工业出版社 .1997.8。
[8]孟少农..《机械加工工艺手册》[M].北京:机械工业出版社.1991.9。
[9]李庆寿.《机床夹具设计》[M].北京:机械工业出版社 .1984。
QQ 29467473