

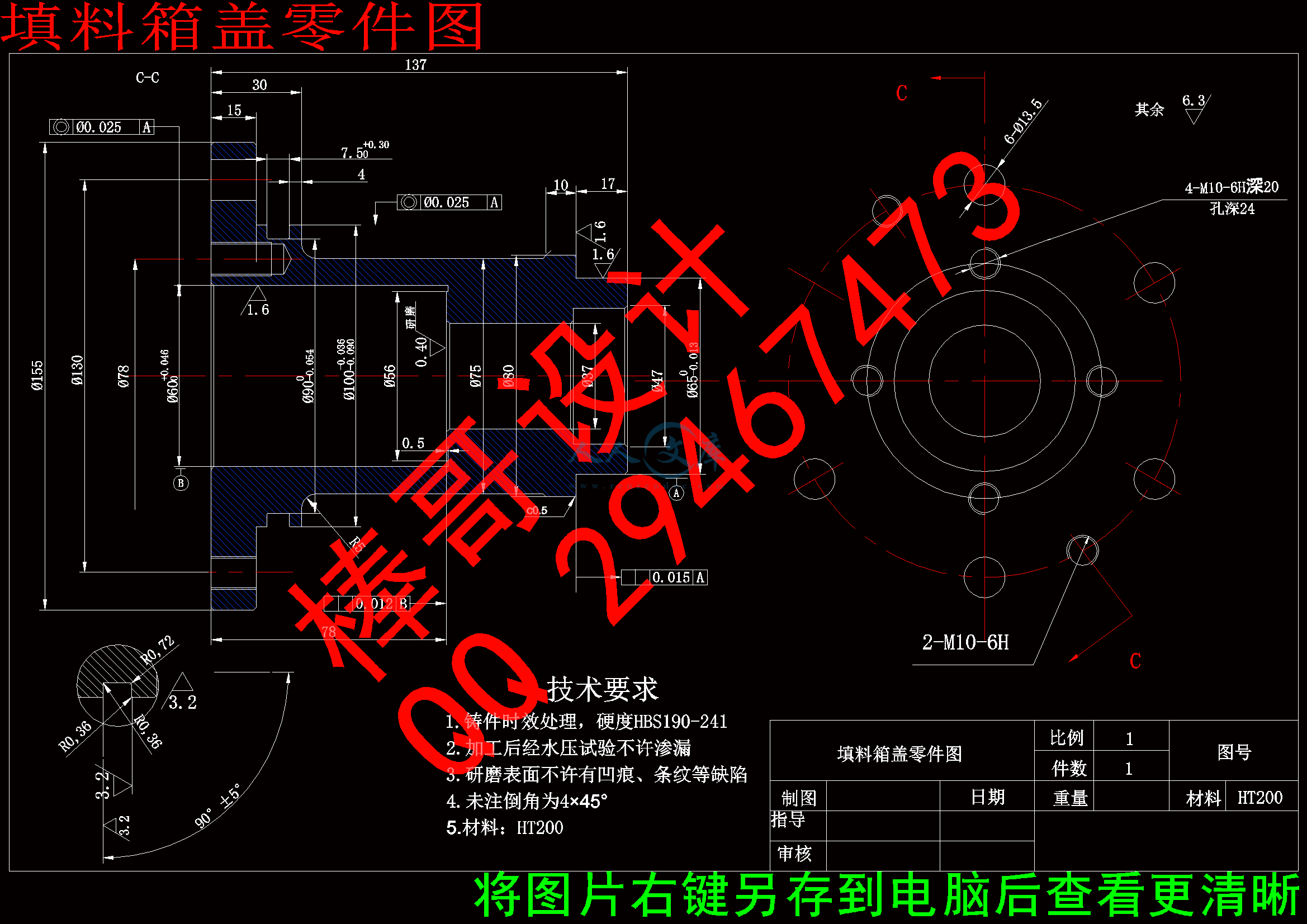




棒哥设计QQ 29467473
第1章 课题提出的背景和意义
1.1 课题的研究背景
箱体类零件是机器和部件的基础零件,它把机器和部件中的所有零件连接成一个整体, 并使机器和部件中的零件相互保持正确位置, 完成必需的运动。因此, 箱体零件的加工质量直接影响着机器的性能、精度和寿命。箱体类零件结构一般比较复杂, 箱壁薄, 表面和孔比较多。但箱体零件主要加工的对象是一些平面和孔。对于平面大多采用铣削和磨削, 对于轴承孔多采用镗削, 对于连接孔多采用钻、扩、铰等。另外, 在箱体类零件加工安排时, 工艺顺序一般为先面后孔, 先粗后精, 并在各个工序间安排时效处理,通过对箱体零件的研究,自动编程能够优化箱体零件加工工艺,提高箱体零件质量,缩短了加工时间,减少了工人的劳动强度,提高企业生产效率就是本次研究的目的。
箱体类零件的主要结构特点:
1、形状较复杂
2、体积较大
3、壁薄比较容易变形
4、孔和平面的精度要求较高
总而言之,箱体类零件在整个机械制造业当中占有相当重要的地位,它的精度高低直接影响到机器性能的好坏。因此讨论研究箱体零件的加工工艺和自动编程是很有现实意义。
1.2 UG的应用前景及UG软件应用的意义
UG是Unigraphics的缩写,这是一个交互式CAD/CAM计算机辅助设计 </view/76137.htm>与计算机辅助制造系统,它功能强大,可以轻松实现各种复杂实体及造型的建构。它在诞生之初主要基于工作站,但随着PC硬件的发展和个人用户的迅速增长,在PC上的应用取得了迅猛的增长,目前已经成为模具行业三维设计的一个主流应用。
UG的开发始于1990年7月,它是基于C语言开发实现的。UG NX是一个在二和三维空间无结构网格 </view/10755.htm>上使用自适应多重网格方法开发的一个灵活的数值求解偏微分方程的软件工具。其设计思想足够灵活地支持多种离散方案。因此软件可对许多不同的应用再利用。
一个给定过程的有效模拟需要来自于应用领域(自然科学或工程)、数学(分析和数值数学)及计算机科学的知识。然而,所有这些技术在复杂应用中的使用并不是太容易。这是因为组合所有这些方法需要巨大的复杂性及交叉学科的知识。最终软件的实现变得越来越复杂,以致于超出了一个人能够管理的范围。一些非常成功的解偏微分方程的技术,特别是自适应网格 </view/2937965.htm>加密和多重网格方法在过去的十年中已被数学家研究,同时随着计算机技术的巨大进展,特别是大型并行计算机的开发带来了许多新的可能。
UG的目标是用最新的数学技术,即自适应局部网格加密、多重网格和并行计算,为复杂应用问题的求解提供一个灵活的可再使用的软件基础。
随着我国改革开放步伐的进一步加快,中国正逐步成为全球制造业的基地,特别是加入WTO后,作为制造业基础的模具行业近年来得到了迅速发展。模具是工业生产的基础工艺装备,在电子、汽车、电机、电器、仪表、家电和通信等产品中,60%—80%的零部件都依靠模具成型。国民经济的五大支柱产业,即机械、电子、汽车、石化、建筑,都要求模具工业的发展与之相适应。模具是“效益放大器“,用模具生产的最终产品的价值,往往是模具自身价值的几十倍、上百倍。模具生产水平的高低,己成为衡量一个国家产品制造水平高低的重要标志,在很大程度上决定着产品的质量、效益和新产品的开发能力。因此,我国要从一个制造业大国发展成为一个制造业强国,必须要振兴和发展我国的模具工业,提高模具工业的整体技术水平。同时,模具工业的发展也日益受到人们的重视和关注,国务院颁布的《关于当前产业政策要点的决定》也把模具列为机械工业改造序列的第一位,生产和基本建设序列的第二位。
随着CAD/CAM软件加工及快速成型等先进制造技术的不断发展,以及这些技术在模具行业中的普及应用,模具设计与制造领域正发生着一场深刻的技术革命,传统的二维设计及模拟量加工方式正逐步被基于产品三维数字化定义的数字化制造方式所取代。在这场技术革命中,逐步掌握三CAD/CAM软件的使用,并用于模具的数字化设计与制造是其中的关键。 我国模具工业发展前景非常广阔。国内外模具及模具加工设备厂商己普遍看好中国市场。随着对模具设计质量与制造要求的不断提高,以及CAD/CAM技术在模具制造业中的大规模推广应用,急需大批熟悉CAD/CAM技术应用的模具设计与制造的技术人才。这是企业最为宝贵的财富,也是企业走向世界、提高产品竞争力最根本的基础。而目前这方面的专业人才非常缺
1.3 本章小结
在本章介绍了箱体类零件的主要作用以及结构特点,在机械制造业中占有相当重要的地位;同时也介绍UG软件的前景,目前已经成为模具行业三维设计的一个主流应用;UG软件的应用,在模具制造业中大规模推广应用。
第2章 填料箱盖零件的分析
2.1 零件的作用
箱体类是机器或部件的基础零件,它将机器或部件中的轴、套、齿轮等有关零件组装成一个整体,使它们之间保持正确的相互位置,并按照一定的传动关系协调地传递运动或动力。因此,箱体的加工质量将直接影响机器或部件的精度、性能和寿命。
箱体类零件有:机床主轴箱、机床进给箱、变速箱体、减速箱体、发动机缸体和机座等。根据箱体零件的结构形式不同,可分为整体式箱体,如图2-1(a、b、d)所示和分离式箱体,如图2-1(c)所示两大类。前者是整体铸造、整体加工,加工较困难,但装配精度高;后者可分别制造,便于加工和装配,但增加了装配工作量。
2-1 几种箱体的结构
题目所给的零件是CA6140车床填料箱盖(如图2-2),主要作用是保证与填料箱体联接后保证密封。对平面要求有较高的平面度和较小的粗糙度值;对孔的尺寸精度、形状精度、和表面粗糙度都要求较高;对同一轴线的孔应有一定的同轴度要求和各支承孔之间也应有一定的孔距尺寸精度及平行度要求。
图2.2 填料箱盖
2.2 填料箱盖的技术要求分析
箱体类零件是机器及其部件的基础零件。它将机器及其部件中的轴、轴承套和齿轮等零件按一定的相互关系装配成一整体,并按预定的传动关系协调运动。因此,箱体的加工质量,直接影响着机器的性能,精度和寿命。
箱体的结构形式虽然多种多样,但仍有共同的主要特点:形状复杂、壁薄且不均匀,内部呈腔形,加工部位多,加工难度大,既有精度要求较高的孔系和平面,也有许多精度要求较低的紧固孔。因此,一般中型机床制造厂用于箱体类零件的机械加工劳动量约占整个产品加工量的15%~20%。
1、以Φ65H5()轴为中心的表面进行加工
包括:尺Φ寸为Φ65h5()的轴,表面粗糙度为1.6,尺寸为Φ80的与Φ65h5()相接的肩面, 尺寸为Φ100f8()与Φ65h5()同轴度为0.025的面,尺寸为Φ60H8 ()与Φ65h5()同轴度为0.025的孔。
2、以Φ60H8()孔为中心的表面进行加工
尺寸为78与Φ60H8()垂直度为0.012的孔底面,表面粗糙度为0.4,须研磨。
3、以Φ60H8()孔为中心均匀分布的12孔,6-ф13.5,4-M10-6H深20孔深24及2-M10-6H的孔进行加工
2.3 本章小结
在本章节中对题目所给的零件进行了简要的工艺分析,注明了各个孔的同轴度、面的粗糙度。
第3章 工艺规程设计
3.1 零件机械加工工艺规程的制定
零件机械加工工艺规程是规定零件机械加工工艺过程和方法等的工艺文件。它是在具体的生产条件下,将最合理或者比较合理的工艺过程,用图表(或文字)的形式制成用来指导生产、管理生产的文件。
3.1.1 机械加工工艺规程的内容及作用
工艺规程的内容,一般有零件的加工工艺路线、各工序基本加工内容、切削用量、工时定额及采用的机床和工艺装备(刀具、夹具、量具、模具)等。
工艺规程的主要作用如下:
1、工艺规程是指导生产的主要技术文件。合理的工艺规程是建立在正确的工艺原理和实践基础上的,是科学技术和实践经验的结晶。因此,它是获得合格产品的技术保证,一切生产和管理人员必须严格遵守。
2、工艺规程是生产组织管理工作、计划工作的依据。原材料的准备、毛坯的制造、设备和工具的购置、专用工艺装备的设计制造、劳动力的组织、生产进度计划的安排等工作都是依据工艺规程来进行的。
3、工艺规程是新建或扩建工厂或车间的基本资料。在新建扩建或改造工厂或车间时,需依据产品的生产类型及工艺规程来确定机床和设备的数量及种类,工人工种、数量及技术等级,车间面积及机床的布置等。
3.1.2 制定工艺规程的原则、原始资料
1、制定工艺规程的原则
制定工艺规程的原则是:在保证产品质量的前提下,以最快的速度、最少的劳动消耗和最低的费用,可靠加工出符合设计图纸要求的零件。同时,还应在充分利用本企业现有生产条件的基础上,尽可能保证技术上先进、经济上合理、并且有良好的劳动条件。
2、制定工艺规程的原始资料
⑴ 产品零件图样及装配图样。零件图样标明了零件的尺寸和形位精度以及其他技术要求,产品的装配图有助于了解零件在产品中的位置、作用,所以,它们是制定工艺规程的基础。
⑵ 产品的生产纲领。
⑶ 产品验收的质量标准。
⑷ 本厂现有生产条件,如机床设备、工艺装备、工人技术水平及毛坯的制造生产能力等。
⑸ 国内、外同类产品的生产工艺资料。
3.1.3 制定工艺规程的步骤
1、零件图样分析
零件图样分析的目的在于:
⑴ 分析零件的技术要求,主要了解各加工表面的精度要求、热处理要求,找出主要表面并分析它与次要表面的位置关系,明确加工的难点及保证零件加工质量的关键,以便在加工时重点加以关注。
⑵ 审查零件的结构工艺性是否合理,分析零件材料的选取是否合理。
2、毛坯选择
毛坯的选择主要依据以下几方面的因素:
⑴ 零件的材料及机械性能 零件的材料一旦确定,毛坯的种类就大致确定了。例如材料为铸铁,就应选铸造毛坯;钢质材料的零件,一般可用型材;当零件的机械性能要求较高时要用锻造;有色金属常用型材或铸造毛坯。
⑵ 零件的结构形状及尺寸 例如,直径相差不大的阶梯轴零件可选用棒料作毛坯,直径相差较大时,为节省材料,减少机械加工量,可采用锻造毛坯;尺寸较大的零件可采用自由锻,形状复杂的钢质零件则不宜用自由锻。对于箱体、支架等零件一般采用铸造毛坯,大型设备的支架可采用焊接结构。
⑶ 生产类型 大量生产时,应采用精度高、生产率高的毛坯制造方法,如机器造型、熔模铸造、冷轧、冷拔、冲压加工等。单件小批生产则采用木模手工造型、焊接、自由锻等。
⑷ 毛坯车间现有生产条件及技术水平以及通过外协获得各种毛坯的可能性。
3、拟订工艺路线
⑴ 定位基准的选择 正确选择定位基准,特别是主要的精基准,对保证零件加工精度、合理安排加工顺序起决定性的作用。所以,在拟定工艺路线时首先应考虑选择合适的定位基准。基准的选择方法见第一章。
⑵ 零件表面加工工艺方案的选择 由于表面的要求(尺寸、形状、表面质量、机械性能等)不同,往往同一表面的加工需采用多种加工方法完成。某种表面采用各种加工方法所组成的加工顺序称为表面加工工艺方案。
⑶ 加工阶段的划分 对于那些加工质量要求高或比较复杂的零件,通常将整个工艺路线划分为以下几个阶段:
① 粗加工阶段 主要任务是切除毛坯的大部分加工余量,并制出精基准。该阶段最关键的问题是怎样提高生产率。
② 半精加工阶段 主要任务是减小粗加工时造成的误差,为主要表面的精加工做好准备,同时完成零件上各次要表面的加工。
③ 精加工阶段 主要任务是保证各主要表面达到图样规定要求。这一阶段的问题是如何保证加工质量。
④ 光整加工阶段 主要任务是减小表面粗糙度值和进一步提高精度。
划分加工阶段的好处是按先粗后精的顺序进行加工,可以分配合理的加工余量以及选择合理的切削用量,使加工机床冲分发挥其效率,并且能长期保持精加工机床的精度;减少工件在加工过程中的变形,避免精加工表面受到损伤;粗精加工分开,还便于及时发现毛坯缺陷,同时有利于安排热处理工序。
4、加工顺序的安排
加工顺序的安排对保证加工质量,提高生产率和降低成本都有重要作用,是拟定工艺路线的关键之一。可按下列原则进行。
⑴ 切削加工顺序的安排
① 先粗后精 先安排粗加工,中间安排半精加工,最后安排精加工。
② 先主后次 先安排零件的装配基面和工作表面等主要表面的加工,后安排如键槽、紧固用的光孔和螺纹孔等次要表面的加工。
③ 先面后孔 对于箱体、支架、连杆、底座等零件,其主要表面的加工顺序是先加工用作定位的平面和孔的端面的加工,然后再加工孔。
④ 先基准面后其它面 即选作精基准的表面应在一开始的工序中就加工出来,以便为后续工序的加工提供定位精基准。
⑵ 热处理工序的安排
零件加工过程中的热处理按应用目的,大致可分为预备热处理和最终热处理。
预备热处理 预备热处理的目的是改善机械性能、消除内应力、为最终热处理作准备,它包括退火、正火、调质和时效处理。铸件和锻件,为了消除毛坯制造过程中产生的内应力,改善机械加工性能,在机械加工前应进行退火或正火处理;对大而复杂的铸造毛坯件(如机架、床身等)及刚度较差的精密零件(如精密丝杠),需在粗加工之前及粗加工与半精加工之间安排多次时效处理;调质处理的目的是获得均匀细致的索氏体组织,为零件的最终热处理作好组织准备,同时它也可以作为最终热处理,使零件获得良好的综合机械性能,一般安排在粗加工之后进行。
最终热处理 最终热处理的目的主要是为了提高零件材料的硬度及耐磨性,它包括淬火、渗碳及氮化等。淬火及渗碳淬火通常安排在半精加工之后、精加工之前进行;氮化处理由于变形较小,通常安排在精加工之后。
⑶ 辅助工序的安排
辅助工序包括:检验、清洗、去毛刺、防锈、去磁及平衡去重等。其中检验是最主要的、也是必不可少的辅助工序,零件加工过程中除了安排工序自检之外,还应在
下列场合安排检验工序:
① 粗加工全部结束之后、精加工之前;
② 工件转入、转出车间前后;
③ 重要工序加工前后;
④ 全部加工工序完成后。
3.2 箱体零件的材料、毛坯和热处理
箱体材料一般选用HT200~400的各种牌号的灰铸铁,而最常用的为HT200。灰铸铁不仅成本低,而且具有较好的耐磨性、可铸性、可切削性和阻尼特性(减震性)。在单件生产或某些简易机床的箱体,为了缩短生产周期和降低成本,可采用钢材焊接结构。
毛坯的加工余量与生产批量、毛坯尺寸、结构、精度和铸造方法等因素有关。有关数据可查有关资料及根据具体情况决定。
毛坯铸造时,应防止砂眼和气孔的产生。为了减少毛坯制造时产生残余应力,应使箱体壁厚箱体浇铸后应安排时效或退火工序。
某些单件、小批量生产的箱体零件,为了缩短毛坯制造的周期和降低成本,可采用钢板焊接结构
普通精度的箱体零件,一般在铸造之后安排一次人工时效处理。对一些高精度或形状特别复杂的箱体零件,在粗加工之后还要安排一次人工时效处理,以消除粗加工时所造成的残余应力。
3.3 基准面的选择
3.3.1 粗基准的选择。
对于零件而言,尽可能选择不加工表面为粗基准。而对于有若干个不加工表面的工件,则应以与加工表面要求相对位置精度较高的不加工表面作粗基准。
3.3.2 精基准的选择。
主要要考虑基准重合的问题。
当设计基准与工序基准不重合时,应该进行尺寸换算。
3.4 制订工艺路线
按照先基准面后其它、先面后孔、先粗后精、先主后次的原则。
布置工艺路线如下:
3.4.1 工艺路线方案一
工序I:铣小端端面,粗车φ65外圆及台阶端面及各倒角。
工序II:铣大端面、粗车φ155外圆面、粗车左端台阶面、粗镗φ60内孔、底面及沟槽,粗车环槽、粗车φ75、φ100、φ80外圆面及各倒角。
工序III:扩孔φ37、锪孔φ47。
工序IV:钻6-φ13.5小孔、钻M10螺纹孔及攻丝。
工序V:半精车φ65外圆及台阶面。
工序VI:半精车φ155、φ75、φ100、φ80、环槽及各倒角。
工序VII:精细车φ65外圆。
工序VIII:精、细镗φ60内孔。
工序IX:研磨孔φ60内端面、倒角。
工序X:去毛刺。
工序XI:终检。
3.4.2 工艺路线方案二
工序I:粗车小端端面,粗车φ65外圆及台阶端面及各倒角。
工序II:粗车大端面、粗车φ155外圆面、粗车左端台阶面、粗镗φ60内孔、底面及沟槽,粗车环槽、粗车φ75、φ100、φ80外圆面及各倒角。
工序III:扩孔φ37、锪孔φ47。
工序IV:半精车φ65外圆及台阶面。
工序V:半精车φ155、φ75、φ100、φ80、环槽及各倒角。
工序VI:精细车φ65外圆。
工序VII:精、细镗φ60内孔。
工序VIII:研磨孔φ60内端面、倒角。
工序IX:钻6-φ13.5小孔、钻M10螺纹孔及攻丝。
工序X:去毛刺。
工序XI:终检。
3.4.3 工艺方案的比较与分析
上述两个方案的特点在于:
方案一是采用铣削方式加工端面,且是先加工12个孔后再精加工外圆面和Φ60H8()孔。
方案二是使用车削方式加工两端面,12个孔的加工放在最后。两相比较起来可以看出,由于零件的端面尺寸不大,端面用车削较好。
在大批生产中,综合考虑,我们选择工艺路线二。
但是仔细考虑,在工艺路线二中,是先精车Φ65外圆及台阶面然后再钻12个孔及攻螺纹。这样由于钻孔属于粗加工,精度要求不高,而且切削力较大,也可能造成已加工表面变形,表面粗糙度值增大。
因此,最后的加工工艺路线确定如下:
工序I:粗车小端端面,粗车φ65外圆及台阶端面及各倒角;粗镗孔φ37、φ47。
工序II:粗车大端面、粗车φ155外圆面、粗车左端台阶面、粗镗φ60内孔、底面及沟槽,粗车环槽、粗车φ75、φ100、φ80外圆面及各倒角。
工序III:钻6-φ13.5小孔、钻M10螺纹孔及攻丝。
工序IV:半精车φ65外圆及台阶面。
工序V:精、细镗φ60内孔。
工序VI:研磨孔φ60内端面、倒角。
工序VII:去毛刺。
工序VIII:终检。
3.4.4 最后的加工工艺路线确定如下:
工序I:以φ155mm外圆及端面定位,粗车小端端面,粗车φ65外圆及台阶端面及各倒角。
工序II:以粗车后的φ65mm外圆及端面定位,粗车大端面、粗车φ155外圆面、粗车左端台阶面。
工序III:以φ155mm外圆及端面定位,粗镗孔φ37、φ47。
工序IV:以粗车后的φ65mm外圆及端面定位,粗镗φ60内孔、底面及沟槽。
工序V:以粗车后的φ65mm外圆及端面定位,粗车φ75、φ100、φ80外圆面及各倒角。
工序VI:以粗车后的φ65mm外圆及端面定位,粗车环槽。
工序VII:钻6-φ13.5小孔。
工序VIII:钻M10螺纹孔及攻丝。
工序IX:以粗车后的φ155mm外圆及端面定位,半精车φ65外圆及台阶面。
工序X:以φ65mm外圆定位,半精车φ155、φ75、φ100、φ80、环槽及各倒角。
工序XI:以φ155mm外圆及端面定位,精车、精细车φ65mm外圆。
工序XII:以φ65mm外圆及端面定位,精、细镗φ60内孔。
工序XIII:研磨孔φ60内端面、倒角。
工序XIV:去毛刺。
工序XV:终检。
3.5 机械加工余量、工序尺寸及毛坯尺寸的确定
填料箱盖零件材料为HT200,硬度190~210HB,生产类型为大批生产,采用机器造型铸造毛坯。
1.根据《机械制造技术基础课程设计指导教程》的规定:
除非另有规定,否则要求的机械加工余量适用于整个毛坯铸件,即对所有需要机械加工的表面只
规定值。查《机械制造技术基础课程设计指导教程》书中表2-1、2-5取毛坯铸件的公差等级为10级,机械加工余量等级G级
2.根据《机械制造技术基础课程设计指导教程》的规定 查书中表2-4
取毛坯铸件的机械加工余量为2mm,根据毛坯铸件各个尺寸所
在的范围,查《机械制造技术基础课程设计指导教程》书中表2-3得各个尺寸的公差,再根据公式R=F+2RMA+CT/2(3-1)与公式R=F-2RMA-CT/2 (3-2)即可计算出毛坯的基本尺寸。
3.根据所确定的毛坯尺寸画出毛坯图(如图3.1)
图3.1 毛坯图
3.6 本章小结
本章介绍了机械加工工艺规程的内容及作用,制定工艺规程的原则、原始资料、步骤.然后对于本课题“填料箱盖”加工的工艺规程进行了说明,如毛皮的选择、热处理和基准面的选择。又制定了两种工艺路线,并进行对比,选出了最佳的工艺路线。最后根据书本资料确定了毛坯尺寸、机械加工余量及工序尺寸
第4章 数控机床的选择与加工方案
4.1 选择机床
1、工序I - X是粗车粗镗和半精车。选用卧式车床就能满足要求。本零件尺寸不大,精度要求不高,选用最常用的CA6140型卧式车床(如图4-1)。
图4-1 CA6140型卧式车床
2、工序XI、XII是精细车精镗。由于要求的精度较高,表面粗糙度较小选用精密的车床才能满足要求。故选用C616A型车床(如图4-2)。
图4-2 C616A型车床
3、工序XII、 VIII是钻孔。可采用专用夹具在立式钻床上加工,可选用Z302型摇臂钻床(如图4-3)。
图4-3 Z302型摇臂钻床
4、工序XIII是研磨内孔,精度较高,选用M7232B型立轴矩台磨床(如图4-4)。
图4-4 M7232B型立轴矩台磨床
4.2 选择夹具
本零件除外圆及两端面加工用三爪自定心卡盘(图4-5)外,其他的工序都用专用夹具。
图4-5 三爪自定心卡盘
4.3 选择刀具
1、在车床上加工的工序,一般都用硬质合金车刀(图4-6)和镗刀,加工灰铸铁零件采用YG型硬质合金,粗加工用YG6,半精加工用YG8,精加工和精细加工用YG10,切槽宜用高速钢,磨削用砂轮。
图4-6 硬质合金车刀
2、钻孔用麻花钻,攻螺纹用丝锥。
4.4 确定工序尺寸(见表5-1)
表5-1 工序尺寸
加工表面工序双边余量工序尺寸及公差表面粗糙度
粗半精精粗半精精粗半精精
外圆2155+0.166.3
210.2566.5-0.3065.5+0.0665+0.0136.31.6
437+0.0396.3
447+0.0396.3
275+0.0466.3
280+0.0466.3
21164+0.3062+00.1560+0.0466.31.6
7.5×417.5+1.306.3
1372137+0.306.3
78278+0.30
4.5 确定切削用量及基本工时
4.5.1 工序I:粗车小端端面,粗车φ65外圆及台阶端面及各倒角。
1、切削用量
本工序为粗车(车端面、外圆及镗孔)。已知加工材料为HT200,铸件。机床为CA6140型卧式车床,工件装夹在三爪自定心卡盘。
⑴ 确定φ65mm外圆的切削用量 所选刀具为YG6硬质合金可转位车刀,根据《切削用量简明手册》表1.1,由于CA6140机床的中心高为200mm,故选用刀杆尺寸B×H=16mm×25mm,刀片厚度为4.5mm根据《切削用量简明手册》书中,表1.3,选择车刀几何形状为卷槽带倒棱型前刀面,前角γo=12°,后角αo=6°、主偏角Kr=90°、,副偏角Kr’=10°、刃倾角λs=0°、刀尖圆弧半径=0.8mm。
⑵ 确定切削深度ap 由于粗车单边余量仅为1mm,可一次走刀完成,故
(4-1)
⑶ 确定进给量f 根据《切削用量简明手册》书中,表1.4,在粗车灰铸铁、刀杆尺寸为16 mm×25 mm、ap≤3 mm、工件直径为100 mm ——400 mm时,f=0.6-1.2 mm/r
按C620-1机床的进给量选择f=0.65 mm/r。
确定的进给量尚需满足机床进给强度的要求,故需进行校验。
根据《切削用量简明手册》书中,表1.30,C620-1机床进给机构允许的进给力Fmax=3530N。
根据《切削用量简明手册》书中,表1.23,当灰铸铁170—212HBS,ap≤2 mm,f≤0.75 mm/r,Kr=45°,v=65m/min(预计)时,进给力Ff=950N.
Ff的修正系数为,,,故实际进给力为Ff=950×1.17=1111.5N,由于切削时的进给力小于机床进给允许的进给力,所选的f=0.65 mm/r可用。
⑷ 选择车刀磨钝标准及耐用度 根据《切削用量简明手册》书中,表4-1,车刀后刀面最大磨损量取为1mm,可转位车刀耐用度T=30min。
⑸ 确定切削速度v 切削速度v可根据公式计算,也可直接由表中查出。现采用查表法确定切削速度。
根据《切削用量简明手册》书中,表1.11,当用YG6硬质合金车刀加工灰铸铁时,ap≤1.8 mm,f≤0.75 mm/r时,切削速度v=71m/min。
切削速度的修正系数为KSV=0.8,Ktv=1.0,KTV=1.12,,KMV=0.85,故
V=71×0.8×1.0×0.73×1.12×0.85×0.85=33.55m/min
(4-2)
按CA6140机床的转速选择n=90r/min=1.5r/s
则实际切削速度v=44.4m/min。
最后确定切削用量为:
,f=0.65 mm/r,n=90r/min=1.5r/s,v=44.4m/min
确定车端面及台阶面的ap=1.25mm,f=0.52 mm/r,主轴转速与车φ65mm外圆相同。
2、确定粗车外圆φ65mm的基本时间
⑴ 根据表6.2-1确定车外圆基本时间为:
(4-3)
式中 l=17mm, kr=90°,l1=2mm,l2=0,l3=0,f=0.65mm/r,
n=1.5r/s,i=1,则
⑵ 确定粗车端面的基本时间
(4-4)
式中 d=65mm,d1=43mm,l1=2mm,l2=4mm,l3=0,f=0.52mm/r,n=2.0r/s,i=1
则
4.5.2 工序II:粗镗孔φ37、φ47。
1、确定粗镗孔φ37mm和φ47mm的切削用量 所选刀具为YG6硬质合金、直径为20 mm的圆形镗刀。
⑴ 确定切削深度ap
Φ47mm: ap=(47-43)/2=2mm φ37mm: ap=(37-33)/2=2mm
⑵ 确定进给量f
根据表1.5,当粗镗灰铸铁时、镗刀直径为20mm,镗刀伸出长度为100 mm
时按CA6140机床的进给量,选择f=0.20 mm/r。
⑶ 确定切削速度v
(4-5)
式中CV=189.8,m=0.20,xv=0.15,yv=0.20,T=60min,kv=0.9×0.8×0.65=0.468,
则 (4-6)
对φ37mm内孔: (4-7)
对φ47mm内孔: (4-8)
3、确定粗镗φ37mm、φ47mm孔的基本时间
选镗刀的主偏角xr=45°,则l1=2.5mm,l=17mm,l2=3.5mm,l3=0,f=0.2mm/r,对φ37mm孔n=5.48r/s,对φ47mm孔n=6.98r/s,i=1
对φ37mm孔 (4-9)
4.5.3 工序III-VI : 粗车大端面、粗车φ155外圆面、粗车左端台阶面、粗镗φ60内孔、底面及沟槽,粗车环槽、粗车φ75、φ100、φ80外圆面及各倒角。
车端面、车台阶、车环槽、车外圆、镗孔、倒角切削用量及基本时间的确定:
1、加工条件
工件材料:HT200, σb =0.16GPa HBS=200-217,铸造。
加工要求:粗车端面保证尺寸、车台阶保证15和30、车环槽保证尺寸、粗车外圆保证尺寸、粗车外圆保证和。
机床与刀具与工序1相同
2、切削用量的选择与计算方法与工序1基本相同,如表4-2所示:
表4-2 切削用量
工 步主轴转速F/min切削速度m/min进给量mm/r切削深度mm进给次数工时
粗车大端面12035.40.651.25122s
粗车外圆12045.60.651.5118s
车台阶车环槽480150.70.22130s
和12035.40.651122s
4.5.4 工序VII:钻6-φ13.5小孔。
1、选择钻头
选择高速钢麻花钻钻头,粗钻时do=4mm,后角αo=16°,二重刃长度 ° ° °
2、确定切削用
⑴ 确定进给量
查《切削用量简明手册》
按钻头强度选择 按机床强度选择
最终决定选择机床已有的进给量 经校验校验成功。
⑵ 钻头磨钝标准及寿命
后刀面最大磨损限度,查《切削用量简明手册》为0.5~0.8mm,寿命.
⑶ 钻头切削速度
查《切削用量简明手册》 修正系数
故。
(4-10)
查《切削用量简明手册》,机床实际转速为
故实际的切削速度
⑷ 校验扭矩功率
故满足条件。
3、 计算工时
(4-11)
4.5.5 工序VIII:钻M10螺纹孔及攻丝(装配时钻铰锥孔)。
以φ37孔为精基准,钻一个φ4孔,攻M10螺纹。
1、选择钻头
选择高速钢麻花钻钻头,粗钻时do=4mm,后角αo=16°,二重刃长度 ° ° °
2、确定切削用
⑴ 确定进给量
查《切削用量简明手册》
按钻头强度选择 按机床强度选择
最终决定选择机床已有的进给量 经校验校验成功。
⑵ 钻头磨钝标准及寿命
后刀面最大磨损限度,查《切削用量简明手册》为0.5~0.8mm,寿命.
⑶ 确定切削速度
查《切削用量简明手册》 修正系数
故。
(4-12)
查《切削用量简明手册》机床实际转速为
故实际的切削速度 (4-13)
⑷ 校验扭矩功率
故满足条件。
3、计算工时
(4-14)
攻螺纹由于没有手册可查,故以钻削切削用量及其他钻螺纹工序估算。
4.5.6 工序IX:半精车φ65外圆及台阶面。
此序为半精车外圆,保证尺寸:,已知条件与粗加工工序相同。
1、 确定半精车外圆的的切削用量。 所选用的刀具为YG6硬质合金刀,车刀形状、刀杆尺寸及刀片厚度为:B×H=16mm×25mm,刀片厚度为4.5mm根据《切削用量简明手册》表1.3,选择车刀几何形状为卷槽带倒棱型前刀面,前角γo=12°,后角αo=6°、主偏角Kr=90°、,副偏角Kr’=10°、刃倾角λs=0°、刀尖圆弧半径=0.8mm。
⑴ 确定切削深度ap =0.75mm。
⑵ 确定进给量f 根据《切削用量简明手册》书中,表1.4,在粗车灰铸铁、刀杆尺寸为16 mm×25 mm、ap≤3 mm、工件直径为d<100 mm时及按CA6140机床的进给量选择f=0.3 mm/r。由于是半精加工,切削力小,故不需要校核机床进给机构强度。
⑶ 确定车刀磨钝标准及耐用度 根据《切削用量简明手册》书中,表1.9,车刀后刀面最大磨损量取为0.4mm,可转位车刀耐用度T=30min。
⑷ 确定切削速度v 切削速度v可根据公式计算,也可直接由表中查出。采用查表法确定切削速度。
根据《切削用量简明手册》书中,表1.11,用YG6硬质合金车刀加工灰铸铁时,ap≤0.8 mmf≤0.5 6mm/r时,切削速度v=128m/min。
切削速度的修正系数为KSV=0.8,Ktv=1.0,KTV=1.12,,KMV=0.85,故
V=71×0.8×1.0×0.73×1.12×0.85×0.85=33.55m/min
(4-15)
按CA6140机床的转速选择n=380r/min=6.3r/s
所以实际切削速度v=41.6m/min。
2、车刀耐用度T=30min。
基本时间
确定半精车外圆φ65mm的基本时间 根据表6.2-1车外圆基本时间为
(4-16)
式中 l=17mm
(4-17)
kr=90°,l1=2mm,l2=0,l3=0,f=0.65mm/r,
n=1.5r/s,i=1,则
4.5.7 工序X:以φ65mm外圆定位,半精车φ155、φ75、φ100、φ80、环槽及各倒角。
表4-3 切削用量及基本时间的确定
工 步主轴转速F/min切削速度m/min进给量mm/r切削深度mm进给次数工时
粗车外圆7602118s
车环槽760283.20.11930s
φφ 760283.20.11122s
4.5.8 工序XI:以φ155mm外圆及端面定位,精车、精细车φ65mm外圆。
表4-4 切削用量及基本时间的确定
工序主轴转速F/min切削速度m/min进给量mm/r切削深度mm进给次数工时
XI (精)工步1760183.20.11120s
工步214004760.050.5130s
XI (精细)工步1140044.40.030.5140s
工步2手动
4.5.9 工序XII:精、细镗φ60内孔。
1、确定精、细镗φ60mm孔的切削用量
所选刀具为YG10硬质合金、直径为20 mm的圆形镗刀。
⑴ 确定切削深度ap
Φ60mm: ap=(60-49)/2=0.5mm
⑵ 确定进给量f
根据《切削用量简明手册》书中,表1.5,当粗镗灰铸铁时、镗刀直径为20mm,镗刀伸出长度为100 mm
时按C620-1机床的进给量,选择f=0.20 mm/r。
⑶ 确定切削速度v
按计算公式:
(4-18)
式中CV=189.8,m=0.20,xv=0.15,yv=0.20,T=60min,kv=0.9×0.8×0.65=0.468,
则 (4-19)
对φ60mm内孔:
2、确定精、细镗φ60mm孔的基本时间
选镗刀的主偏角xr=45°,则l1=2.5mm,l=17mm,l2=3.5mm,l3=0,f=0.2mm/r,对φ60mm孔n=13.96r/s,i=1
对φ60mm孔: (4-20)
4.5.10 工序XIII:磨Φ60孔底面、倒角。
1、选择磨床:
选用M7232B型立轴矩台磨床。
2、选择砂轮:
查《工艺手册》第三章中磨料选择各表,选用I-30x10x10-A60P6V
3、切削用量的选择:
砂轮转速 n砂=970r/min,
轴向进给量 fr=0.017mm/r
径向进给量
4、切削工时基本时间计算:
当加工一个表面时:
Tj=(2*b*L*k)/(1000r*fa*fr)(见《工艺手册》表6.2-8)
式中 L:加工长度 L=30mm
b:加工宽度 b=30mm
:单面加工余量 =0.5mm
K: 系数 K=1.1
r: 工作台移动速度(m/min)
:工作台往返一次砂轮轴向进给量
: 工作台往返一次砂轮径向进给量
则:
Tj= (2*30*30*0.5*1.1)/(1000*10*3*0.017)
=1.94min
5、辅助时间的计算:
辅助时间tf与基本时间tj之间的关系为tf=(0.15~0.2)tj,取tf=0.15tj,则辅助时间为:
tf=0.15*1.94=17.46s
6、其他时间的计算:
其他时间可按关系式tb+tx=6%*(tj+tf)计算
则tb+tx=6%*(116.4+17.46)=8s
7、工序时间:
tdj=116.4+17.46+8=141.86s
4.5.11 工序XIV:去毛刺。
4.5.12 工序XV:终检。
其余工序详见附录1
4.6 本章小结
本章内容根据已经确定的工艺,通过计算和查阅书籍资料,确定每道工序的工序尺寸、切削用量及基本工时。
第5章 数控程序编制—CA6140填料箱盖的车削加工
零件的径向和轴向尺寸较大,要求加工外圆、端面几内孔,有时还要求调头加工。为保证加工要求和数控车削时工件装夹的可靠性,应注意加工顺序和装夹方式。如为保证两端内孔的同轴度要求,采取先加工右端面和内孔,并在内孔预留精加工余量0.3mm,然后将工件掉头安装;。为保证两孔的同轴度,应在镗完左端内孔后,反向镗右端内孔。
所用刀具及刀位号和毛坯图如图6-1,6-2:
图5-1 刀具及刀位号
图5-2 毛坯图
5.1 数控程序编制
通过分析零件的材料、形状、尺寸、精度以及毛坯的形状和热处理的要求等等,来确定正确的加工方法、加工顺序、所用刀具和切削用量,主要目的是为了确定数控加工的工艺路线;其次是刀具的选择,合理选择加工刀具;然后是加工顺序的安排,要在确定的工艺过程中,要做到加工路线短,进给、换刀次数少,充分的发挥数控机床功能,使加工安全、可靠、效率高.
根据零件加工的尺寸要求、加工路线和设定的坐标系,进行运动轨迹坐标值的计算.对于数控加工的零件,为了方便编程和尺寸间的协调,所有尺寸最好用一个基准引注.
根据计算出来的运动轨迹坐标值和已经确定的加工顺序、刀具号、切削参数,按照规定的指令代码和程序格式,逐段边写加工程序.在编程是要注意使程序简单,方便和直观。
程序内容由三部分组成(见表5-1)
表5-1 程序内容组成
5.1.1 右端加工过程:
O0022 /程序编号0022
N0 G50 X200.0 Z60.0 /设置工件原点在小(右)端面
N3 G00 X30.0 Z5.0 /直接回第二参考点
N6 S800 T01 M03 /转速为800r/min;调01号车刀;开主轴
N9 G00 X70.0 Z-1.0 /快速走到右端面粗车起始点
N12 G01 X42.0 Z-1.0 /右端面粗车
N15 G00 X201.0 Z1.0 /快速退刀
N18 T02 /调02号精车刀
N21 G00 X70.0 Z-1.25 /快速走到右端面精车起始点
N24 G01 X42.0 Z-1.25 /右端精车
N27 G00 X201.0 Z1.0 /快速退刀
N30 T01 /调01号车刀
N33 G00 X68.0 Z1.0 /快速走到粗车起始点
N36 P39 Q48 U1.0 W0 D1.0 F100 S500
/粗车ф65及台阶面循环
N39 G00 X65.0 Z0 S800
N42 G01 W-17 F60
N45 X80.0
N48 W-10
N51 G70 P39 Q48 /精车ф65及台阶面循环
N54 G00 X201.0 Z1.0 /快速退刀
N57 T03 /调03号粗镗刀
N60 G00 X48.0 Z1.0 /倒角起始点
N63 G01 X46.0 Z-1.0 /倒角
N66 G01 Z-17 /粗镗ф47内孔
N69 X36.0 /台阶粗镗
N72 Z-27 /粗镗ф37内孔
N75 G00 X30.0 Z1.0
N78 X201.0 /退刀
N81 T04 /调04号精镗刀
N84 G00 X47.0 Z1.0
N87 G01 Z-17 /精镗ф47内孔
N90 X37.0
N93 Z-27 /精镗ф37内孔
N96 G00 X30.0 Z1.0
N99 X201.0 Z60.0 /退刀,回起始点
N102 M05 /主轴关
5.1.2 左端加工过程:
O0023 /程序号0023
N0 G50 X200.0 Z60.0 /设置工件原点在大(右)端面
N3 G00 X30.0 Z5.0 /回第二参考点
N6 S1500 T01 M03 /转速1500r/min;调01号车刀;开主轴
N9 G00 X30.0 Z-1.0 /快速走到粗车大端面起点
N12 G01 X157.0 /粗车大端面
N15G00 X201.0 /快速退刀
N18 T02 /调02号车刀
N21 G00 X3.0 Z5.0
N24 Z-1.25
N27 G01 X157.0 /精车大端面
N30 G71 P33 Q55 U1.0 W0 D1.0 F100 S500
/粗车外圆循环
N33 G01 Z-15.0 /粗车ф155
N36 X100.0
N39 Z-32.0 /粗车台阶
N42 X91.0
N45 G03 X75.0 Z-37.0 R5.0
/粗车R5圆弧
N48 Z-109.0 /粗车ф75
N52 X80.0 Z-110.0 /倒角
N55 Z-120.0 /粗车ф80
N58 G00 X201.0 Z1.0 /快速退刀
N61 T05 /调05号切槽刀
N64 G00 X201.0 Z-18.5
N67 X101.0 /快速定位到切槽点
N70 G71 P73 Q76 U1.0 W0 D3.0 F100 S500
/切槽循环
N73 G00 X101.0
N76 G01 X91.0
N79 G70 P73 Q76 /精切循环
N82 G00 X201.0
N85 Z60.0 /回起始点
N88 M05 /主轴停
5.2 本章小结
在本章内容中,主要讲述了“填料箱盖”数控程序编制的思路、方法并编制出工件加工的数控程序。
第6章 专用夹具设计
为了提高劳动生产率,保证加工质量,降低劳动强度,需要设计专用夹具。在这里只设计了工序VI :磨φ60内孔底面的专用夹具。本夹具将用于立轴矩台平面磨床,刀具为砂轮。
6.1 问题的指出
本夹具主要用来加工φ60内孔底面,由于工艺要求不高,因此,在本道工
序加工时,主要应考虑如何提高劳动生产率,降低劳动强度。
6.2 夹具设计
6.2.1定位基准的选择
由零件图可知,要加工φ60内孔底面,原本只需限制工件的3.个自由度,但由于在孔内加工,为了不使加工影响其他表面,需要限制工件的5个自由度,且φ60内孔底面对φ60内孔有垂直度要求,要求的加工精度较高,因此,应选择φ65外圆和与φ80外圆相连的台阶面作为基准进行加工。
6.2.2切削力和夹紧力计算
本步加工可按磨削估算夹紧力。实际效果可以保证可靠的卡紧。
轴向力 (6-1)
扭矩
(6-2)
由于扭矩很小,计算时可忽略。
夹紧力为 (6-3)
取系数 S1=1.5 S2=S3.=S4=1.1
则实际卡紧力为 F’=S1*S2*S3.*S4*F=10.06N (6-4)
6.3 定位误差的分析
工件以台阶面和外圆面定位,工件的设计基准为其轴线,故不存在基准不重合误差,误差即为φ65外圆面公差的一半。即0.0065mm,此误差在允许的范围内,因此符合要求。
6.4 夹具设计及操作的简要说明
该夹具是以端面和外圆定位基准加工φ60内孔底面,可以用一带端面的定位套来定位,由于磨削时的夹紧较大,因此加了四根柱以加强其强度,本夹具通过楔块的移动使铰链轴带动螺栓下移从而带动压板下移压紧工件。铰链机构能迅速夹紧和松开,达到了提高生产力和降低劳动强度的目的,因此能满足要求。
6.5 基于UG的夹具建模过程概述
根据上述计算与设计,确定夹具体的设计,最终确立夹具的结构。
基于UG NX7.0的夹具体的建模过程:
第一步,新建一个文件名为“jiajuti"文件类型为(*prt),单位:mm的文件如图6.1所示:
图6.1 创建新文件
第二步,插入一个长为310mm,宽280mm,25mm的长方体。生成实体模型如图6.2所示:
图6.2 长方体特征
第三步,选择成形特征下的凸垫,选择生成长方体的一个棱边为水平参考,凸垫的长250mm,宽280mm,高度为185mm。生成特征如下6.3图示
图6.3 凸垫特征
第四步,创建长210mm,宽度190mm,深度310mm腔体特征如下6.4图所示
图6.4 腔体特征
第五步,创建拉伸异形定位孔,具体做法如下
⑴ 在草绘环境下,绘出孔的草绘图;
⑵ 进入建模环境下,拉伸草绘完成的草图剖面完成结果如下6.5图所示:
图6.5 异形孔特征
第六步,创建夹具体的其他的三个异形定位孔,具体做法如下:
⑴ 创建XOZ和YOZ平面;
⑵ 点击UG菜单中的插入命令中的关联复制中镜像特征;
⑶ 选择上一步生成的异形定位孔,然后选择镜像平面XOZ,确定完成;
⑷ 选择生成的两个异形定位孔,选择镜像平面YOZ,确定完成四个定位孔的绘制如下6.6图所示:
图6.6 异形孔特征
第七步,生成夹具体的四个夹紧定位孔并插入螺纹特征。
⑴利用UG中的简单孔功能,根据孔的定位参数绘制一个孔;
⑵在绘制好的孔中插入螺纹特征;
⑶插入基准轴Z轴;
⑷利用UG工具栏中的环形特征生成其余3个孔,
选择生成的孔简单孔和孔内螺纹,
选择Z轴,输入数量4,角度为90度,生成4个螺纹孔如下6.7图示。
图6.7 螺纹孔特
第八步,在夹具体上创建一个夹紧拉杆的孔创建如6.8图。
图6.8 拉杆孔特征
最后创建完成的实体模型如下6.9所示:
图6.9 夹具体型特征
经过一系列的设计和零件装配,最终夹具与零件的装配图如图6.10所示:
图6.10 装配图
爆炸组件如图7.11所示:
图6.11 爆炸图
6.6 本章小结
在前文中提到了,填料箱盖的加工中,除外圆及两端面加工用三爪自定心卡盘外,其余工序全用专用夹具。本章主要说明了为什么要设计专用的夹具来加工,专用夹具定位基准的选择,切削力、夹紧力的计算,定位误差的分析,并且详细的阐述了该专用夹具在UG上建模的过程。
结 论
箱体类零件是机器和部件的基础零件,它把机器和部件中的所有零件连接成一个整体, 并使机器和部件中的零件相互保持正确位置, 完成必需的运动。箱体零件的加工质量直接影响着机器的性能、精度和寿命。箱体类零件结构一般比较复杂, 箱壁薄, 表面和孔比较多。箱体的结构形式虽然多种多样,但仍有共同的主要特点:形状复杂、壁薄且不均匀,内部呈腔形,加工部位多,加工难度大,既有精度要求较高的孔系和平面,也有许多精度要求较低的紧固孔。本次设计CA6140车床填料箱盖,主要作用是保证与填料箱体联接后保证密封,对内表面的加工精度要求比较高,对配合面的表面粗糙度要求也较高。基于对箱体零件的调查、了解。从毛坯的选择到工艺规程的设计、工艺路线的安排、每道工序的安排和夹具的设计,一切都保证了该零件在加工完成后具有较高的精度。经过大量的计算和在书籍上查阅的资料,计算出每道工序刀具的切削用量、切削速度和切削深度.最后,通过分析零件的材料、形状、尺寸、精度以及毛坯的形状和热处理的要求等等,来确定正确的加工方法、加工顺序、所用刀具和切削用量。保证了数控程序加工路线短,进给、换刀次数少,充分的发挥数控机床功能,使加工安全、可靠、效率高。
致 谢
毕业论文暂告收尾,这也意味着我在西南科技大学的四年的学习生活既将结束。回首既往,自己一生最宝贵的时光能于这样的校园之中,能在众多学富五车、才华横溢的老师们的熏陶下度过,实是荣幸之极。在这四年的时间里,我在学习上和思想上都受益非浅。这除了自身努力外,与各位老师、同学和朋友的关心、支持和鼓励是分不开的
论文的写作是枯燥艰辛而又富有挑战的。在老师的谆谆诱导、同学的出谋划策及家长的支持鼓励,是我坚持完成论文的动力源泉。在此,我特别要感谢我的导师马有凉老师。从论文的选题、文献的采集、框架的设计、结构的布局到最终的论文定稿,从内容到格式,从标题到标点,她都费尽心血。没有马有良老师的辛勤栽培、孜孜教诲,就没有我论文的顺利完成。
感谢机械制造及其自动化专业的各位同学,与他们的交流使我受益颇多。最后要感谢我的家人以及我的朋友们对我的理解、支持、鼓励和帮助,正是因为有了他们,我所做的一切才更有意义;也正是因为有了他们,我才有了追求进步的勇气和信心。
时间的仓促及自身专业水平的不足,整篇论文肯定存在尚未发现的缺点和错误。恳请阅读此篇论文的老师、同学,多予指正,不胜感激!
参考文献
[1]孙丽媛.机械制造工艺及专用夹具设计指导[M].第2次.北京.冶金工业出版社.2002 .11-39
[2]李益民.机械制造工艺设计简明手册[S].第1版.北京.机械工业出版社.1994.25-29
[3]上海市金属切削手册 .上海市金属切削技术协会[S].上海.上海科学技术出版社.2000.37-45
[4]张世昌.机械制造基础[M].第1版.北京.高等教育出版社.2006.18-26
[5]李旦 </mn/searchApp?searchWord=%E6%9D%8E%E6%97%A6%E7%AD%89%E8%91%97> .机床专用夹具设计图册[M].第2版.哈尔滨.哈尔滨工业大学出版社 .1998.39-56
[6]邹慧君.机械原理课程设计手册[S].第1版.北京.高等教育 </search/book_search.jsp?cbs=%E9%AB%98%E7%AD%89%E6%95%99%E8%82%B2>出版社 .1998.36-55
[7]张世昌.机械制造基础[M].第1版.北京.高等教育出版社.2006.37-57
[8]王光斗.机床夹具设计手册[S].第3版.上海.上海科技出版社.32-46
[9]邹青.机械制造工艺学课程设计指导书[M].第1版.北京.机械工业出版社.200.28-42
[10]肖继德 . 机床夹具设计[S].第2版.北京.机械工业出版社.2004.26-35
[11]江洪.UG NX4.0基础教程[M].第2版.北京.机械工业出版社.2007.35-60
[12] Goetsch,D.l.,Advanced Manufactureing Technology先进制造技术.Delmar Pulisher Inc.1990.19-39
[13]Dorf,R.C.and Kuisiak,A.,Handbook of Design Manufacturing and Automation制造业和自动化设计手册 .John Wiley &Sons.1994.8-26
[14] Dimarogonas,A.D.,Machine Design for Manufacturing,Prentice-Hall,1996.11-19
附录一
QQ 29467473