

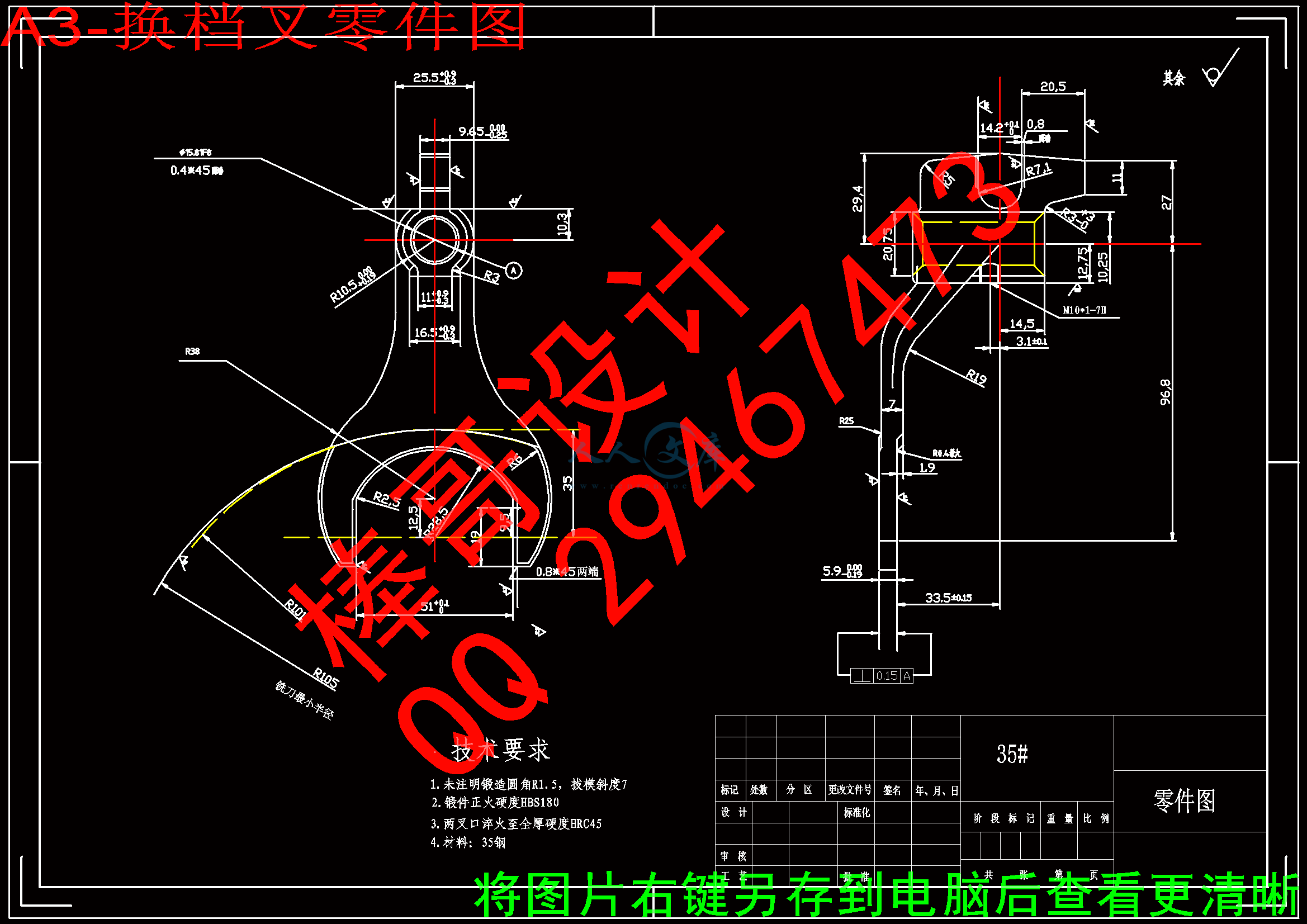
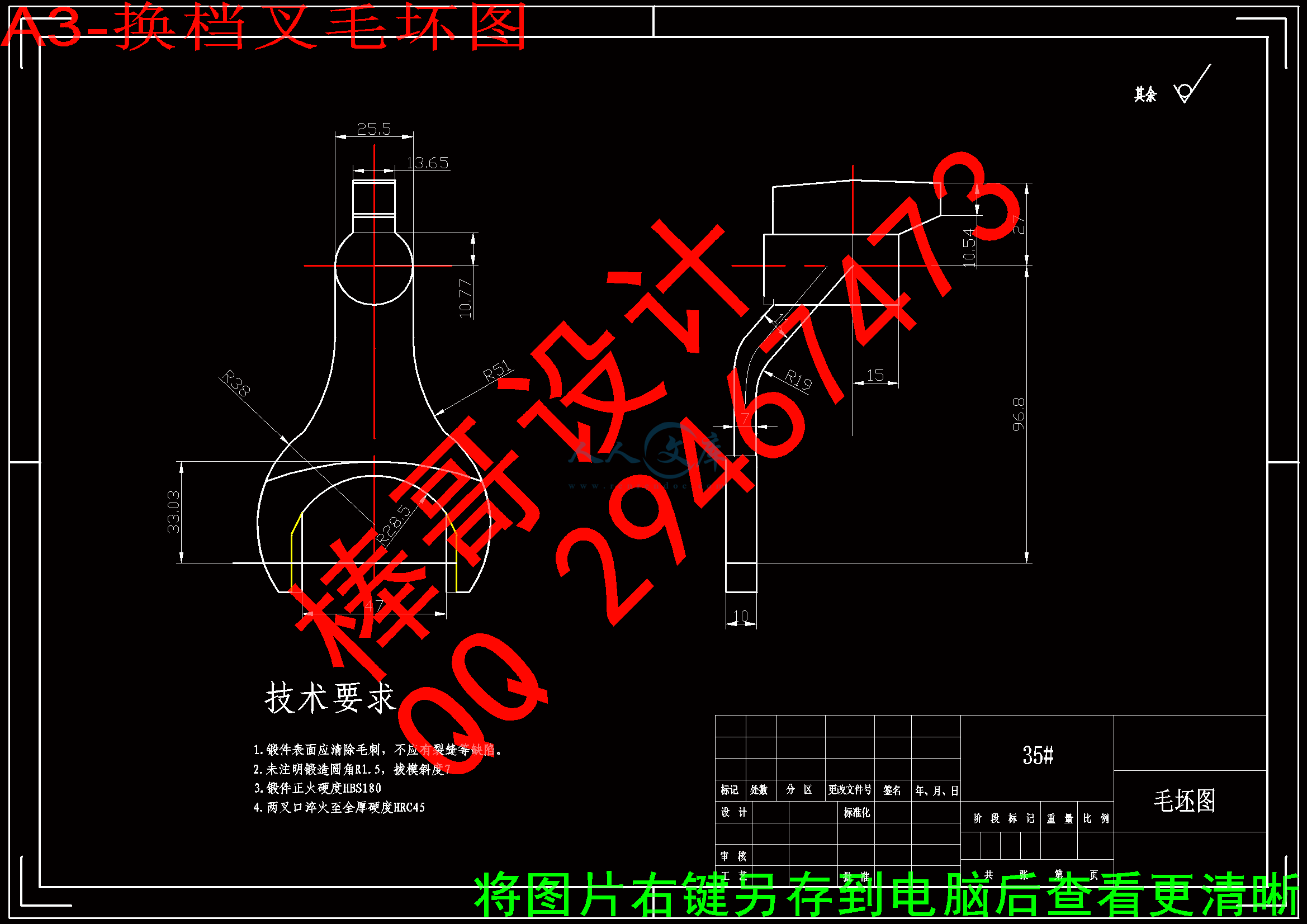
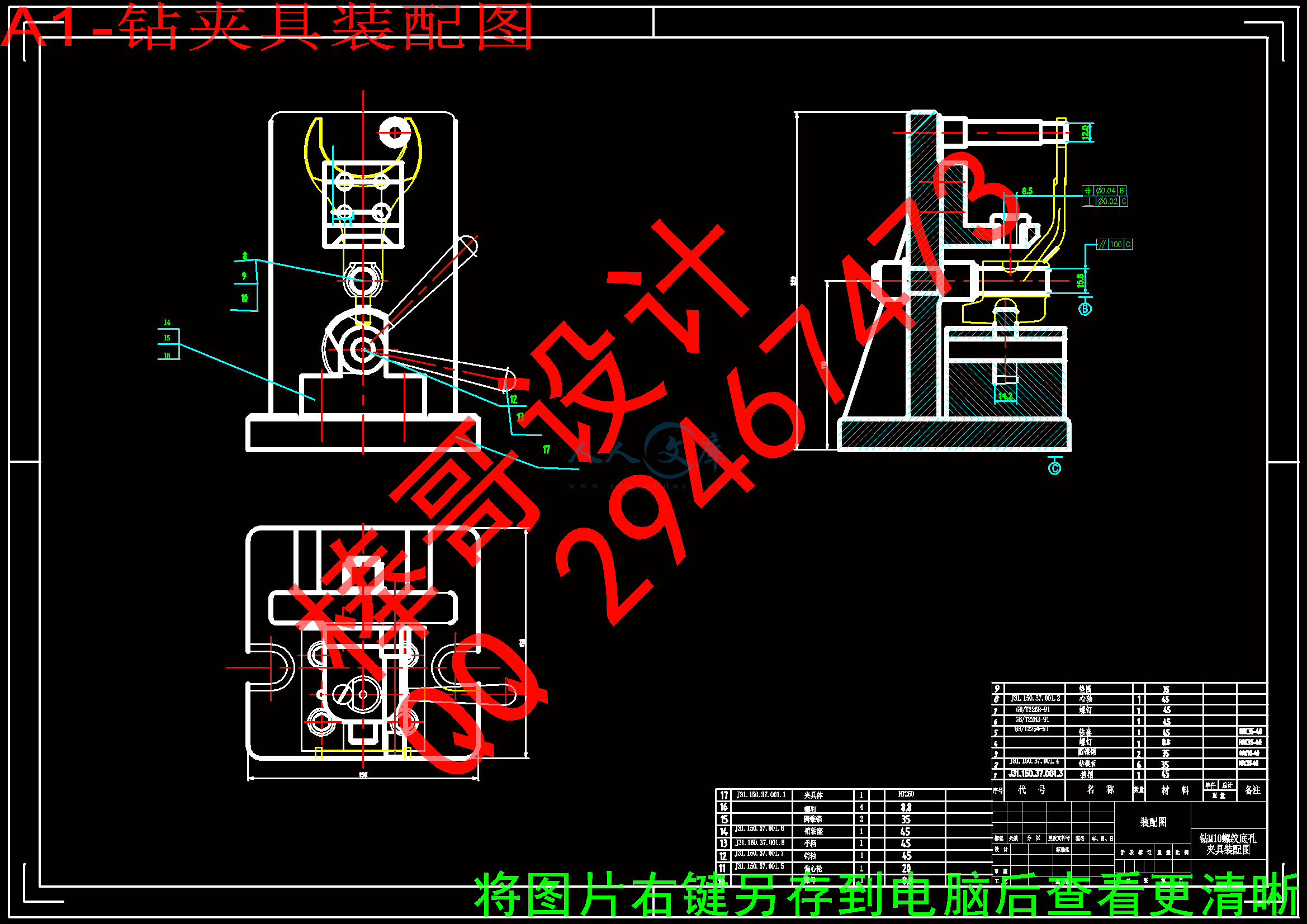
![工艺卡[1张].gif](/ueditor/net/upload/2015-07-10/0f46993f-3291-47ef-9bc1-53ae0f95f211.gif)
![工序卡[共8张].gif](/ueditor/net/upload/2015-07-10/bba05071-1cc4-4749-a80e-dc9d298809fe.gif)
棒哥设计QQ 29467473
机械制造工艺学
设计说明书
题目:换档叉零件的机械加工工艺规程制订及其中一道工序专用夹具的设计
设 计 人: 陈 真
指导教师: 周 星 元
武汉科技学院
机械制造及其自动化系
2008年 05 月 19 日
武汉科技学院
机械制造工艺学课程设计任务书
题目:换档叉零件的机械加工工艺规程制订及第一道工序专用夹具的设计
内容:
(1)零件图1张
(2)毛坯图1张
(3)机械加工工艺卡片1套
(4)夹具总装图1张
(5)夹具零件图1张
(6)课程设计说明书1份
班 级: 机械设计045
学 号: 0402051224
姓 名: 陈 真
指导教师: 周 星 元
2008年 05月 19 日
序言
机械制造工艺学课程设计使我们学完了大学的全部基础课、技术基础课以及大部分专业课之后进行的.这是我们在进行毕业设计之前对所学各课程的一次深入的综合性的总复习,也是一次理论联系实际的训练,因此,它在我们四年的大学生活中占有重要的地位。
就我个人而言,我希望能通过这次课程设计能巩固、扩大和强化自己所学到的理论知识与技能,对自己未来将从事的工作进行一次适应性训练,从中锻炼自己分析问题、解决问题的能力。
一、零件的分析
(一)零件的作用
课题所给的零件是变速器的换档叉。换档叉头上方的孔Φ15.81F8与操纵机构相连,而下方的换档叉脚夹在双联交换齿轮的槽中,用于与所控制齿轮所在的轴接触。通过上方的力拨动下方的齿轮变速。两件零件铸为一体,加工时分开。
(二)零件的工艺分析
零件图上的主要技术要求为:两叉脚口表面淬火至全厚硬度为45HRC。零件正火硬度 180HBS。去毛刺。
1、加工表面及其要求
1)Φ15.81F8孔:孔径Φ15.81mm,两端倒脚0.4mm×45°,表面粗糙度R3.2。
2)换档叉脚端面:保证尺寸56,表面粗糙度R12.5。
3)操纵槽:宽度为14.2mm ,深度为18mm,对称面与换档叉头端面的距离为20.5mm,两侧面几底面的表面粗糙度为R12.5。
4)换档叉脚端面:厚度尺寸为5.9mm,表面粗糙度R6.3,对孔Φ15.81F8的垂直度为0.15mm,外端面与操纵槽的距离为33.5mm。
5)换档叉脚内侧面:宽度尺寸为51mm,表面粗糙度为R6.3。两端倒角0.8mm×45°。
二、工艺规程设计
(一)零件材料
零件为35钢,是中碳钢,其强度和球铁接近,其铸造工艺性介于低碳钢和高碳钢之间,可进行热处理,以获得所需要的机械性能。
(二)毛坯选择
1、确定毛坯的类型及制造方法
由于零件的材料为35钢,零件形状不规则,因此应选用铸造毛坯。零件的轮廓尺寸不大,而且工件上有许多表面不切削加工,所以选用砂型机器造型。
2、毛坯的形状,尺寸及公差
毛坯的形状及尺寸如图1所示。选择过零件最高线且平行与换档叉脚对称面的平面作分型面,铸件采用带型芯的分模造型,多件同时浇注,钢水经两拔叉脚位置经横浇口流入.
由于该零件属特形零件,且利用不加工表面进行定位的情形较多, 所以确定铸件尺寸公差等级为GB6414-86的CT9,机械加工余量等级为AM-H.
3、确定毛坯的技术要求
1)铸件无明显的铸造缺陷
2)未注圆角为R3~5
3)拔摸斜度为7°
4)机加工前正火,消除内应力
4、绘毛坯图
根据零件图所示的零件结构形状,在各加工表面加上加工余量,绘制毛坯图
(三)基准选择
由于附图1所示的换档叉零件图多数尺寸及形位公差以φ15.81F8孔及其端面为设计基准,因此必须首先将φ15.81F8孔及其端面加工好,为后续工序准备基准.根据粗,精基准选择的原则,确定各加工表面的基准如下:
1)φ15.81F8孔及其端面:拔叉头的外轮廓及端面(粗基准)
2)换档叉脚端面(粗加工): φ15.81F8孔及其端面
3)换档叉脚端面(精加工): φ15.81F8孔及换档叉脚端面
4)换档叉脚内侧面: φ15.81F8孔, 换档叉脚端面及换档叉脚外侧面
5)操纵槽: φ15.81F8孔,操纵槽, 换档叉脚内侧面
(四)拟订机械加工工艺路线
1、确定各加工表面的加工方法及加工路线
该换档叉的加工表面为: φ15.81F8孔及端面, 换档叉脚的两侧面及内侧面,操纵槽, φ15.81F8孔.根据各加工表面的精度要求和表面粗糙度要求, 孔的加工路线为钻—樘—饺,端面的加工方法为车, 换档叉脚端面的加工路线为粗铣—磨, 换档叉脚内侧面的加工方法为铣削,操纵槽的加工方法铣削, φ15.81F8孔的加工方法为钻削.
2、拟订加工工艺路线
1)工艺路线方案一
工序一 车换档叉头端面,钻,镗,铰φ15.81F8孔,孔口倒角.
工序二 校正换档叉脚
工序三 粗铣换档叉脚两端面
工序四 铣换档叉脚内侧面
工序五 铣操纵槽
工序六 钻φ15.81F8孔
工序七 去毛刺
工序八 换档叉脚局部淬火
工序九 校正换档叉脚
工序十 磨换档叉脚两端面
工序十一 清洗
工序十二 清洗检验
2)工艺路线方案二
工序一 车换档叉头端面
工序二 钻,镗,铰φ15.81F8孔
工序三 φ15.81F8孔口倒角.
工序四 校正换档叉脚
工序五 粗铣换档叉脚两端面
工序六 铣换档叉脚内侧面
工序七 铣操纵槽
工序八 φ15.81F8孔
工序九 去毛刺
工序十 换档叉脚局部淬火
工序十一 校正换档叉脚
工序十二 磨换档叉脚两端面
工序十三 清洗
工序十四 清洗
工艺路线方案一是按工序集中原则组织工序, φ15.81F8孔及端面需要用采用六角车床和专用夹具加工,优点是工艺路线短, φ15H8孔及其端面的加工在一台机床上完成,减少工件装夹次数,易于保证加工面相互位置精度,需要的机床数量少,减少工件在工序间的运输,减少辅助时间和准备终结时间.工艺路线方案二是按序分散原则组织工序,换档叉头端面可在普通车床上用通用卡盘装夹加工, φ15.81F8孔可在普通钻床上用钻模加工,孔口倒角在另一台车床上加工.优点是可以采用通用机床和通用夹具,缺点是工艺路线太长,增加了工件的装夹次数,而且工序一和工序二重复使用粗基准.由于本零件形状不规则,加工面分散,可以采用万能性机床配以专用夹具,并尽量使工序集中,提高生产率.综合上述两个工艺路线方案的优缺点,选择第一个方案.
(五) 确定机械加工余量,工序尺寸及公差
根据上述原始资料及加工工艺, 《查机械制造工艺设计简明手册》(以下简称《工艺手册》),分别确定各加工表面的加工余量,工序尺寸及公差如下:
工序 工序内容 单位余量 工序尺寸 表面粗糙度Ra
工序一 1.车换档叉头端面 2.5mm 30mm 12.5
2.钻φ15.81F8孔 7mm φ14mm 12.5
3.镗φ15.81F8 孔 0.8mm φ14.8mm 6.3
4.铰φ15.81F8 孔 0.2mm φ15.81mm 3.2
5.倒孔口角 0.4mm 0.4mm×45° 12.5
工序三 粗铣换档叉脚两端面 3.2mm 6.3 mm 12.5
工序四 铣换档叉脚内侧面 3.5mm 51mm 6.3
工序五 铣操纵槽 6.5mm 14.2mm 12.5
工序六 钻φ10H7孔 2.5mm φ10H7mm 12.5
工序七 磨换档叉脚端面 0.3mm 5.9mm 6.3
(六) 选择机床设备及工艺装备
根据一般工厂先有的生产条件,为了满足生产需要,现选用各工序所用的设备为:
工序一 C336-1回转式六角车床,YT15外圆车刀, φ14mm标准锥柄麻花钻, φ14.8YT15扩孔刀及φ15H8YT15锥柄机用绞刀,0~200/0.02mm游标卡尺,钢直尺, φ15H8孔用塞规.
工序二 钳工台,校正工具
工序三 X62W卧式铣床,YT15三面刃铣刀,专用夹具,0~200/0.02mm游标卡尺
工序四 X62W卧式铣床,YT15三面刃铣刀,专用夹具,0~200/0.02mm游标卡尺
工序五 X62W卧式铣床,YT15三面刃铣刀,专用夹具,0~200/0.02mm游标卡尺
工序六 Z515钻床, φ5锥柄麻花钻,专用夹具,0~200/0.02mm游标卡尺
工序七 钳工台,校正工具,0~200/0.02mm游标卡尺
工序八 M7120A平面磨床,砂轮,专用夹具,0~200/0.02mm游标卡尺
(七) 确定切削用量及基本工时
1、工序一 车换档叉头端面,钻、镗、铰孔,孔口倒角
加工条件:C336-1回转式六角车床,YT15外圆车刀, mm标准锥柄麻花钻, φ14.8YT15扩孔刀及φ15H8YT15锥柄机用绞刀,专用夹具,柴油冷却。
(1)车换档叉头端面
a. 确定背吃刀量 端面的总加工余量为2.5mm,一次走刀加工,a =2.5mm。
b. 确定进给量 根据《切削用量简明手册》(以下简称《切削手册》)表1.4,刀杆尺寸为20mm×20mm, a≤30mm以及工件直径为20~50mm时,f=0.3~0.4mm/r,查《工艺手册》表4.2-3,根据机床的横向进给量取f=0.39mm/r。
c. 计算切削速度 根据《切削手册》表1.27、表1.28,C=242,m=0.2,x=0.15,y=0.35,修正系数k=1.44,k=0.8,k=1.04,k=0.81,刀具寿命选T=60min
v==
=126.8(r/min)
d.确定机床主轴转速
n=(r/min)
根据《工艺手册》表4.2-2,与807。3r/min相近的机床转速为760r/min及1000r/min.现选n=760 r/min,所以实际切削速度 m/min
e.计算基本时间 按《工艺手册》表6.2-1,L=24mm,L=2mm,L=0,L=0。
(min)
(2) 钻φ15.81F8孔至φ14mm
a. 确定进给量 根据《切削手册》表2.7,f=0.31~0.37mm/r,查《工艺手册》表4.2-3,根据机床实际进给量取f=0.35mm/r。
b. 选择钻头磨钝标准及耐用度 根据《切削手册》表2.12,取钻头后面上午最大磨损量为0.8mm;耐用度T=45min。
c. 计算切削速度 根据《切削手册》表2.30及表2.31,C=6.6,z
=0.4,x=0,y=0.5,m=0.2,k=1,k=1,k=0.95。
==14.22(m/min)
n=(r/min)
根据《工艺手册》表4.2-2,按机床实际转速取n=285r/min,实际切削速度
V=dn/1000=12.686(m/min)
d. 计算基本时间 根据《工艺手册》表6.2-5,l =30mm, l=D/2ctgk+(1~2)=5.2~6.2mm,取l=6mm,l=4mm
t=(l+ l+ l)/nf=0.401min
(3) 扩φ15.81F8孔至φ14.8
a. 确定进给量 根据《切削手册》表2.10,f=0.5~0.6mm/r,查《工艺手册》表4.2-3,根据机床实际纵进给量取f=0.35mm/r.
b. 确定切削速度 为减少辅助时间,参照钻孔取n=285r/min,v=13.25m/min.
c. 计算基本时间 根据《工艺手册》表6.2-5,l =30mm,l=(D-d)/2 ctgk+(1~2)=1.23~2.33mm, 取l=3mm, l=4mm
t=(l+ l+ l)/nf=0.37min
(4) 铰φ15.81F8孔
a. 确定进给量和切削速度 根据《切削手册》表2.25,f=0.2~0.4 mm/r,v=8~12m/min,计算得n=169.8~254.65r/min, 查《工艺手册》表4.2-2,按机床实际进给量和实际转速,取f=0.35mm/r, n=198r/min,实际切削速度v=9.33m/min.
b. 计算基本时间 根据《工艺手册》表6.2-5, l =30mm, l=2mm,
t=(l+ l+ l)/nf=0.49min
(5) 倒φ15.81F8孔口角
参照车端面,取n=760,实际切削速度v=40.59 m/min.
2. 工序三 粗铣拔叉角两端面
加工条件:X62W卧式铣床,两把三面刃直齿铣刀,YT15刀片,刀盘直径125mm,宽12mm,齿数20,专用夹具,柴油冷却。
(1) 确定背吃刀量 由毛坯图已知铣削宽度a=20mm,铣削深度a=32.mm.
(2) 确定每齿进给量 根据《切削手册》表3.5,每齿进给量f=0.09~0.18mm/z.因工件刚性差,取f=0.09mm/z.
(3) 选择铣刀磨钝标准及耐用度 根据《切削手册》表3.7,铣刀刀齿后面最大磨损量为1.2mm;耐用度为T=150min.
(4) 确定切削速度和工作台每分钟进给量 根据《切削手册》表3.27,C=600,q=0.21,=0.4,x=0,y=0.12,u=0.4,P=0,m=0.35,k=1.1.
=126.86m/min
n=(1000×126.86)/(×125)=323r/min
根据《工艺手册》表4.2-39,与323r/min相近的主轴转速为300r/min和375r/min,取n=300r/min,实际切削速度v=117.8m/min
工作台每分钟进给量为f=0.09×20×60=108mm/min, 根据《工艺手册》表4.2-40, X62W铣床与108mm/min相近的进作台进给量为 95mm/min和118mm/min。选择f=95mm/min,则实际的每齿进给量为f=95/(20×60)=0.079mm/z
(5) 计算基本时间
根据《工艺手册》表6.2-7, l =2×≈71mm, l=+(1~3),a=20mm,d=125mm,l=48mm,l=4mm, f=95mm/min,i=1
t=(l+ l+ l)i/ f=1.3mm
3. 工序四 铣拔叉脚内侧面
加工条件: X62W卧式铣床,两把三面刃直齿铣刀,YT15刀片,刀盘直径125mm,宽12mm,齿数20,专用夹具,柴油冷却。
(1) 确定被吃刀量 由毛坯图已知铣削宽度a=20mm,铣削深度a=3.5mm.
(2) 确定切削速度和工作台每分钟进给量 取n=300r/min,实际切削速度v=117.8m/min, 工作台每分钟进给量f=118mm/min,实际每齿进给量f=118/(20×60)=0.099mm/z.
(3) 计算基本时间 l=7.6mm, l=48mm,l=4mm, f=118mm/min,i=1
t=(7.6+48+4)/95=0.63min
4.工序五 铣操纵槽
加工条件:X62W卧式铣床,三面刃直齿铣刀,YT15刀片,刀盘直径125mm,宽12mm,齿数20,专用夹具,柴油冷却。
(1) 确定背吃刀量 由毛坯图已知铣削宽度a=12mm,铣削深度a=13mm.
(2) 确定每齿进给量 取f=0.06mm/z.
(3) 确定切削速度和工作台每分钟进给量根据表3.27,C=270,q=0.21,x=0.1,y=0.4,u=0.3,P=0,m=0.35,k=1.1.
V c==201.51 m/min
n=(1000×201.51)/(×125)=513r/min
根据《工艺手册》表4.2-39,取与513r/min相近的主轴转速n=475 r/min实际切削速度v=186.5m/min
工作台每分钟进给量为f=0.06×20×60=72 mm/min, 根据《工艺手册》表4.2-40,取X62W铣床与72 mm/min相近的进作台进给量f=75 mm/min
则实际的每齿进给量为f=75/(20×60)=0.0625 mm/z.
(4) 计算基本时间 l=22mm, l=48mm,l=4mm, f=72mm/min,
t=(22+48+4)/72=1.03 min
5、工序六,钻10H7孔
加工条件:Z515钻床,10mm ,标准麻花钻,专用夹具。
(1) 确定进给量 由于孔径很小,宜采用手动进给。
(2) 选择钻头磨钝标准及耐用度 根据《切削手册》表2.12,取钻头后面的最大磨损量为0.8mm;耐用度T=15mim
(3) 确定切削速度 根据根据《切削手册》表2.14,表2.7及表2.13,按5类加工性暂定f=0.16mm/r,查得=17m/min,n=1082,查《工艺手册》表4.2-18,按机床实际转速选取n=1100r/min.实际切削速度 =17.3m/min.
(4) 计算基本时间《切削手册》表6.2-5 , L=23mm,L=2.5ctg59+(1~2)=1.5~3.5mm,取L=4mm,L=4mm
t===0.18min
4、工序十 磨换档叉脚端面
加工条件:M7130平面磨床,砂轮,专用夹具.
(1) 选择砂轮 根据《工艺手册》第三章中磨料选择各表,选择WA46KVP35040127砂轮,即砂轮磨料为白刚玉,粒度为46,硬度为中软1级,陶瓷结合济,6号组织,平型砂轮,其尺寸为35040127(DBd).
(2) 选择切削用量 砂轮转速n=1500r/min,=27.5m/s,工件速度=10m/min,径向进给量f=0.015mm/双行程.
(3) 计算基本时间 根据《工艺手册》表6.2-8,加工长度L=71mm,10件一起加工,单面加工余量Z=0.3mm,系数K=1.1,磨削一面的机动时间为
t==3.12min
基本时间为t=min
(八) 填写工艺文件
按上述确定的工艺过程填写机械加工工艺卡片和机械加工工序卡片
二、夹具设计
(一)问题的提出
为了提高劳动生产率,保证加工质量,降低劳动强度,需要设计专用夹具.经过与指导老师协商,决定设计第六道工序---钻5H14孔的钻床夹具.
10H7孔为螺纹孔,用于圆锥销连接拔叉头和轴.本工序的加工要求为:孔径10×1H7mm,表面粗糙度为R12.5m。
本工序的加工条件为Z515钻床, 10标准麻花钻.工件上拔叉头端面, 10H7,操纵槽,拔叉头内侧面均已加工,达设计图样要求,拔叉脚端面已粗加工.
为淬硬钢实心毛坯上钻孔的经济精度为IT11~12,表面粗糙度为R12.5m,在钻夹具上加工时适当控制切削用量,可以保证孔的尺寸精度要求和表面粗糙度要求.因此在本序加工时,主要应考虑要如何保证孔轴线与15.81F8孔轴线的位置度要求.
(二) 夹具设计
1、定位方案及定位元件选择,设计
(1)定位方案的选择 根据工序加工要求,工件在夹具中的定位有两种方案可供选择.
方案一:以15.81F8孔为只要定位基准,限制4个自由度,以操纵槽为止推基准,限制一个自由度,以拔叉脚内侧面为防转基准,限制一个自由度.夹紧操纵槽.
方案二:以 15.81F8孔为只要定位基准,限制4个自由度, 15H8孔端面为止推基准,限制一个自由度,以拔叉脚内侧面为防转基准,限制一个自由度,夹紧15.81F8的另一端面.
方案一是按照基准重合原则确定的,不存在基准不重合误差,有利于保证加工精度,而且夹紧点靠近加工面,夹紧力方向与切削力方向相反,可以抵消部切切削力,有利于提高夹紧刚性.确定是,夹紧力过大容易引起定位元件变形.
方案二是按照基准统一原则确定的,有利于夹具的设计制造,夹紧力方向指向定位元件刚性较大的方向.缺点是不容易保证孔的轴线与操纵槽对称面重合,钻头进给的轴向力完全有定位元件承受,会引起定位元件变形.
本工序加工的10H7孔是穿过15.81F8孔的通孔,在定位销上必须开一个直径大于10mm的径向孔,以便加工时钻头通过定位销,而定位销的直径仅为15mm,开孔后定位销轴向的强度较小,定位销不宜承受夹紧力.另外钻孔加工的切削力主要是钻头进给的轴向力和钻削扭矩,沿工件轴向几乎没有切削力,所需要的夹紧力不大.综合考虑两个方案的优缺点,及本工序加工的具体情况,采用选用方案一.
2、定位元件设计
根据定位方案一,设计定位元件的结构如图, 15H8孔采用圆柱心轴定位,操纵槽才用圆偏心轮式的定心夹紧装置,拔叉脚内侧面采用圆柱挡销定位.圆柱心轴的直径及公差为15.81mm。
3、定位误差计算
圆柱心轴与工件15H8孔的配合为15,影响位置度的定位误差为:
=D-d=(15+0.027)-(15-0.034)=0.061mm
此件小于工件相应位置度公差的三分之一,即 =0.061<mm
所以定位方案能够满足加工要求。
4、导向方案及导向元件的选择和设计
① 导向方案选择 导向方案如附图所示。由于零件的生产类型为大批生产,考虑钻套磨损后可以更换,选择标准结构的可换钻套。根据《夹具手册》表2.5-7,钻套至工件表面的距离按(1-1.5)d=5~7.5mm选取,考虑本工序加工时钻头较细,防止切宵钻头憋断,应该有足够的排屑空间,钻套至工件表面的距离取6mm。
② 导向元件设计 根据《夹具手册》表2.5-5, 衬套与钻模板的配合选H7/n6,
根据《夹具手册》表3.2-118确定衬套为:A10×20GB/T2263-91(d=,D=
③导向误差计算 根据《夹具手册》表1.7-8,导向误差为
式中:d---可换钻套内孔最大直径,
---钻头最小直径,根据GB3136-85,=;
---可换钻套外径的最小直径,=;
--固定衬套内径的最大直径,=;
e---可换钻套内外径轴线的偏心量,(按同轴度公差算得);
l---可换钻套的导向长度,l=28mm;
h---钻套与工件之间的距离,h=6mm;
b---钻孔深度;b=23mm;
K—配合间隙的概率系数,K=0.5;
m—可换钻套安装偏心的概率系数,m=0.4;
p—?钻头偏斜的概率系数,p=0.35.
将各种参数代入上式得:△T=0.036<(1/3)×0.2mm,可以保证位置度要求.
5、设计夹具体、绘制夹具草图
在上述定位、引导、夹具方案的基础上,设计夹具,将各个部分连接成整体,并绘出夹具草图.
6、绘制夹具装配图
夹具装配图如附图所示
7、绘制夹具体零件图
按照夹具装配图,绘制所有非标准零件的零件图
三、小结
为期两周的工艺、夹具课程设计基本结束,回顾整个过程,我觉得受益匪浅,课程设计作为《机械制造工艺学》、《机床夹具设计》课程的重要教学环节,使理论与实践更加接近,加深了理论知识的理解,强化了生产实习中的感性认识.
通过这次设计,我基本上掌握了一个中等复杂零件的加工过程分析、工艺文件的编制、专用夹具设计的方法和步骤等.学会查阅手册,选择使用工艺装备图等.
由于自己能力所限,设计中还有许多不足这处,恳请各位老师、同学们批评指正.
QQ 29467473