前言
本次毕业设计的课题是来源于盐城市江动集团的关于YZ4110柴油机气缸体三面钻削组合机床设计。YZ4110柴油机是该集团大批量生产的产品之一,为保证柴油机气缸体三面孔的加工和相应的位置精度,提高生产效率而设计一台三面钻孔的卧式组合机床。
组合机床是根据工件加工需要,以大量通用部件为基础,配以少量专用部件组成的一种高效专用机床[1]。这种机床既具有结构简单、生产率和自动化程度较高等特点,又具有一定的重新调整能力,以适应工件变化的需要,它还可以对工件进行多面、多主轴同时加工。组合机床应尽可能选用标准件,降低制造成本,同时需考虑实际生产条件,并从机床的合理性、经济性、工艺性、实用性及对被加工零件的具体要求出发,确定设计方案。本机床设计吸取了现有机床加工优点,设计布局合理。满足机体孔系加工质量要求。组合机床行业虽然取得了较大的进步与发展,但是,在制造技术高速发展的今天,由于自身的基础比较薄弱,从整体上看,国外的先进水平、与国内用户的要求还存在着一定的差距,满足不了用户要求。80年代以来,国外组合机床技术在满足精度和效率要求的基础上,正朝着综合成套和具备柔性的方向发展。
组合机床主要用于棱体类零件和复杂的孔面加工,生产率高。加工精度稳定,研制周期短,便于设计、制造和使用维护,成本低。因为通用化、系列化、标准化程度高,通用零部件占70%-90%,通用件可组织批量生产进行预定或外购。自动化程度高,劳动强度低。
组合机床的设计,目前基本上有两种情况:其一,是根据具体加工对象的具体情况进行专门设计,这是当前最普遍的做法。其二,随着组合机床在我国机械行业的广泛使用,广大工人总结自己生产和使用组合机床的经验,发现组合机床不仅在其组成部件方面有共性,可设计成通用部件,而且一些行业在完成一定工艺范围内组合机床是极其相似的,有可能设计为通用机床,这种机床称为“专能组合机床”。这种组合机床不需要每次按具体加工对象进行专门设计和生产,可以设计成通用品种,组织成批生产,然后按被加工零件的具体需要,配以简单的夹具及刀具,即可组成加工一定对象的高效率设备。组合机床的发展思路是以提高组合机床加工精度、组合机床柔性、组合机床工作可靠性和组合机床技术的成套性为主攻方向。一方面,加强数控技术的应用,提高组合机床产品数控化率;另一方面,进一步发展新型部件,尤其是多坐标部件,使其模块化、柔性化,适应可调可变、多品种加工的市场需求。复合、多功能、多轴化控制装备的前景亦被看好。然而更关键的是现代通信技术在机床装备中的应用,信息通信技术的引进使得现代机床的自动化程度进一步提高。在这些方面组合机床装备还有相当大的差距,因此组合机床技术装备高速度、高精度、柔性化、模块化、可调可变、任意加工性以及通信技术的应用将是今后的发展方向。目前,我国组合机床的研究涉及机床设计研究[2][3]、加工工艺[4][5] 、加工质量改进[6]等,在机床自动化、柔性化等方面的研究与国际发展水平相比还有不小的差距。
课题由4人来进行设计,本人主要进行组合机床的总体设计及右主轴箱设计。在对组合机床的主轴箱设计之前,需对被加工零件孔的分布情况及所要达到的技术要求进行具体分析[7],如各部件尺寸、材料、形状、硬度及加工精度和表面粗糙度等内容。充分了解组合机床的特点,通过分析主轴箱的工作原理,进行机床的总体方案设计。首先是总体方案论证,组合机床总体设计的具体工作是编制“三图一卡”,即绘制被加工零件工序图、加工示意图、机床联系尺寸图,编制生产率计算卡。其次是部件设计和零件设计,在主轴箱设计时,需要绘制主轴箱原始依据图,选择主轴箱的规格、型号,选择切削用量[8],计算切削功率,确定各轴的结构、排布、配合关系[9][10],轴的强度、刚度校核等。还需对主轴箱前盖、后盖、箱体及附件的设计[11][12]。在主轴箱设计中,设计的主要思路是把原有的多道工序的单孔加工改为多孔同时加工,这样设计主要是为了解决由多次装夹引起的定位误差问题,保证孔的位置精度。
2 组合机床总体设计
2.1 总体方案论证
2.1.1 工艺路线的确立
A.本机床被加工零件特点
该加工零件为柴油机机体。材料HT250,其硬度为HB190~240,在本工序之前各主要表面、主要孔已加工完毕。
B.本机床被加工零件的加工工序及加工精度
本道工序:钻左面、右、后三面的孔,由本设备“气缸体三面钻削组合机床”完成,因此,本设备的主要功能是完成柴油机机体左、右、后三个面上15个孔的加工。具体加工内容及加工精度是:
a) 左面5个孔:钻削3×φ6、φ8、φ4的孔,表面粗糙度12.5μm,各孔位置度公差为φ0.02mm。
b) 右面5个孔:钻削4×φ4、φ3的孔,表面粗糙度12.5μm,各孔位置度公差为φ0.02mm。
c)后面5个孔:钻削3×φ4、2×φ10孔,表面粗糙度12.5μm,各孔位置度公差为φ0.02mm。
2.1.2 机床配置型式的选择
机床的配置型式有立式和卧式两种。
立式机床的优点是占地面积小,自由度大,操作方便,其缺点是机床重心高,振动大。卧式机床的优点是加工和装配工艺性好,振动小,运动平稳,机床重心较低,精度高,安装方便,其缺点是削弱了床身的刚性,占地面积大。机床的配置型式在很大程度上取决于被加工零件的大小、形状及加工部位等因素。
通过以上的比较,针对YZ4110柴油机气缸体的结构特点和需要被加工的部位考虑钻孔工序是主要工序内容。为了保证钻孔的加工精度和符合被加工零件的加工特点, 我们选择用卧式组合机床。
2.1.3 定位基准的选择
箱体零件的定位方案一般有两种,“一面两销”和“三平面”定位方法。
A. “一面两销”的定位方法的特点是:
a)可以简便地消除工件的六个自由度,使工件获得稳定可靠定位。
b)有同时加工零件五个表面的可能,既能高度集中工序,又有利于提高各面上孔的位置精度。
c)“一面两销”可作为零件从粗加工到精加工全部工序的定位基准,使零件整个工艺过程基准统一,从而减少由基准转换带来的累积误差,有利于保证零件的加工精度。同时,使机床各个工序的许多部件实现通用化,有利于缩短设计、制造周期,降低成本。
d)易于实现自动化定位、夹紧,并有利于防止切削落于定位基面上。
B. “三平面”定位方法的特点是:
a)可以简便地消除工件的六个自由度,使工件获得稳定可靠定位。
b)有同时加工零件两个表面的可能,能高度集中工序。
在选择定位基准时,应尽量选择设计基准作为定位基准,即遵循基准统一原则。通过对零件的分析,最后选择柴油机机体的底面作为定位的基准面,这样就有利于保证了被加工孔相互间的位置精度。柴油机机体要很好的固定在机床上,就必须限制六个自由度,这样才可以保持加工精度。根据切削力的方向和夹具夹紧力的方向,选择柴油机机体的底面确立一个平面来限制3个自由度,侧面定位限制2个自由度,端面定位限制1个自由度,这样就更能保证工件的加工精度。在本次设计中我们采用的就是“三平面”定位。
2.1.4 滑台型式的选择
与机械滑台相比较,液压滑台的进给量可以无级调速;可以获得较大的进给力;零件磨损小,使用寿命长;工艺上要求多次进给时,通过液压换向阀,很容易实现;过载保护简单可靠;工作可靠。但采用液压滑台的不足之处在于进给量由于载荷的变化和温度的影响而不够稳定;液压系统漏油影响工作环境,浪费能源;调整维修比较麻烦。本课题的加工对象是YZ4110柴油机气缸体,为了提高加工效率,降低生产成本,所以选用了液压滑台。
2.2 切削用量的确定及刀具选择
2.2.1 选择切削用量
对于15个被加工孔,采用查表法选择切削用量,从文献[9]P.130表6-11中选取。由于钻孔的切削用量还与钻孔深度有关,随孔深的增加而逐渐递减,其递减值按文献[9]P.131表6-12选取。降低进给量的目的是为了减小轴向切削力,以避免钻头折段。钻孔深度较大时,由于冷却排屑条件都较差,是刀具寿命有所降低。降低切削速度主要是为了提高刀具寿命,并使加工较深孔时钻头的寿命与加工其他浅孔时钻头的寿命比较接近。
切削用量选择是否合理,对组合机床的加工精度、生产率、刀具耐用度、机床的布局形式及正常工作均有很大影响。组合机床多轴箱上所以的刀具共用一个进给系统,通常为标准动力滑台。查文献[9]得硬度HB190-240时,高速钢钻头的切削用量如表2-1:
表2-1高速钢钻头切削用量
加工材料加工直径 (mm)
切削速度 (m/min)
进给量 (mm/r)
铸铁200~241HBS
1~610~180.05~0.1
>6~12>0.1~0.18
A.对左面5个孔的切削用量选择:
a)钻孔1、2、3:Φ6孔,h=10mm 查上表高速钻头切削用量得:
由d=1-6,硬度大于200-241HBS,选择v=10~18m/min,f>0.05~0.1mm/r,取定v=10.48m/min,f=0.1mm



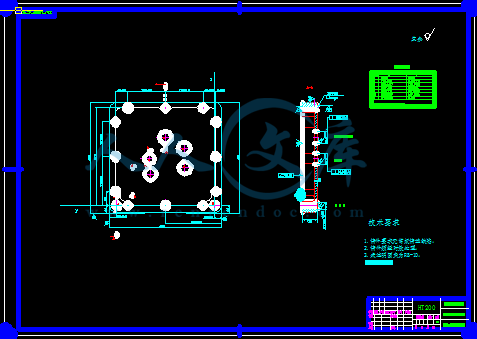


