!【详情如下】CAD图纸+word设计说明书.doc[14000字,49页]【需要咨询购买全套设计请加QQ97666224】.bat
主轴A1-H.dwg
装配A0-H.dwg
轴1A2-H.dwg
轴2A2-H手工图.dwg
轴2与轴1配对齿轮A3-H.dwg
轴3A2-H.dwg
轴4齿轮大A3-H.dwg
轴4齿轮小A3-H.dwg
轴一齿轮A4-H.dwg
轴三与轴二配对齿轮1A3-H.dwg
轴三与轴二配对齿轮二A3-H.dwg
目 录
前 言……………………………………………………………………………....1
1、珩齿加工的基本介………………………………………………............ ....... ….3
2、 运动设计……………………………….…………………………………….. ....13
2.1 给定条件……………………………….…………………………………….. ...13
2.2 确定结构式……………………………….………………………………….. .14
2.3 计算各级转速……………………………….…………………………………15
2.4 电机选型……………………………….…………………………………….. ..15
2.5 拟定转速图……………………………….…………………………………….16
3、 确定各级传动副齿轮的………………………………………………………….17
3.1确定齿轮的齿数........................................................................................ ...............17
3.2各轴及齿轮的计算转速的确定……………………………………………………21
4、 传动零件的初步计算................................................................ .............................26
4.1 传动轴直径初定......................................................................... ..........................26
4.2 主轴主要结构参数的确定....................................................................................27
4.3 齿轮模数计算和齿轮中心距的计算............................................................... .....28
4.4 轴的结构设计........................................................................................... ........... 29
4.5 皮带的相关计算.................................................................... ..............................31
5、 主要零件的验算............................................................................................ .......36
5.1 齿轮的强度验算......................................................................... .........................36
5.2 主轴的验算............................................................................................ ............ .39
5.3 花键的验算............................................................................................ ............ .44
结束语........................................................................................................................46
致 谢……………………………………………………………………................48
参考文献……………………………………………………………………................49
摘要
这篇毕业设计的论文主要阐述的是珩齿加工机床主轴箱的设计方法。珩齿加工机床是一种高精度加工机床.这个方法是以加工过程和珩齿加工机床的使用条件的数学和物理公式为基础的。
在论文中,首先,对珩齿加工机床作了简单的介绍,接着,阐述了主轴箱的设计原理和理论计算。然后按照设计准则和设计理论设计了主轴箱。接着对主轴箱的各部分组成进行了尺寸计算和校核。
目前,在珩齿加工机床的设计、制造及应用上,国内与国外先进水平相比仍有较大差距,国内在设计制造珩齿加工机床过程中存在着较多缺点。
关键字:珩齿加工,主轴箱,机床。
Abstract
This paper of graduation project mainly presents a systematic approach for the design of the headstock of plover machining tool, The plover machining tool is one of the members in the special high precision type machine family . the approach is based on the mathematical formulations and physical formulation on the generation process and conditions for the type of the plover machining tool.
In the paper , first of all , it is introduction about the plover machining tool .then , it is the principles about choose component parts of headstock. After that the headstock is designed abase on the principle. Then, it is checking computations about main component parts of headstock.
At present, we still fall far short of abroad advanced technology in design, manufacture and using. There are a lot of fault in the design of plover machining tool.
Key word: plover machining, headstock, machine.
参考文献
【1】机械工程手册,机械工程手册编委会编,机械工业出版社,1980
【2】机械课程设计手册,许高燕主编,中国地址大学出版社,1989
【3】齿轮制造手册,齿轮制造手册编委会编,北京,机械工业出版社,1997
【4】机械制造工艺手册,王绍竣主编,哈尔滨工业大学出版社,1984
【5】机械制造工程系统自动化,方明伦主编,上海工业大学出版社,1982
【6】机械振动,郑兆昌主编,机械工业出版社,1980
【7】小磨数齿轮加工,国防工业出版社,1972
【8】机械零件课程设计,毛振杨主编,浙江大学出版社,1985
【9】机械零件设计手册,东北工学院编,冶金工业出版社,1982
【10】机械工程师实用数据简明手册,张庆如主编,天津大学出版社,1992
【11】金属切削机床设计,戴署主编,机械工业出版社,1981
【12】工程材料,郑明新主编,北京,清华大学出版社,1983
【13】圆柱齿轮加工,上海工业大学编,上海科学技术出版社,1979


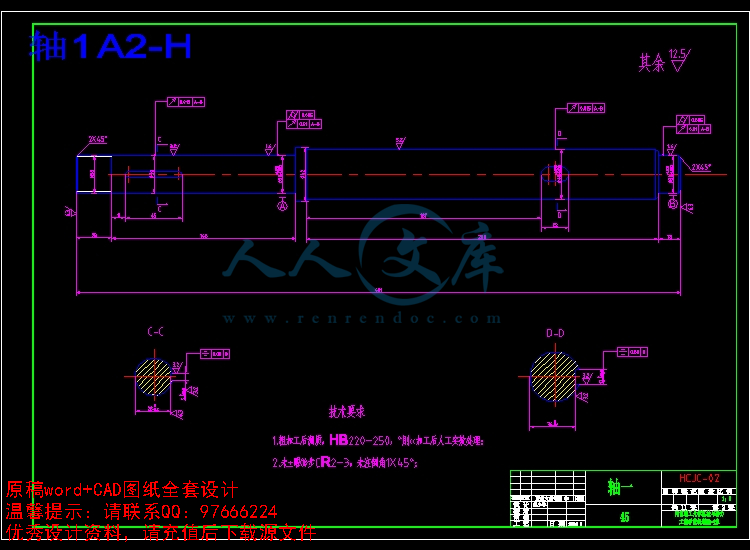



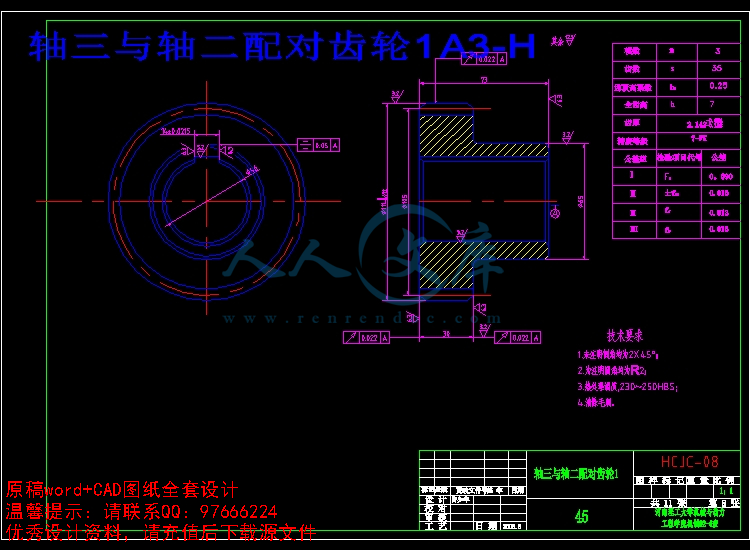
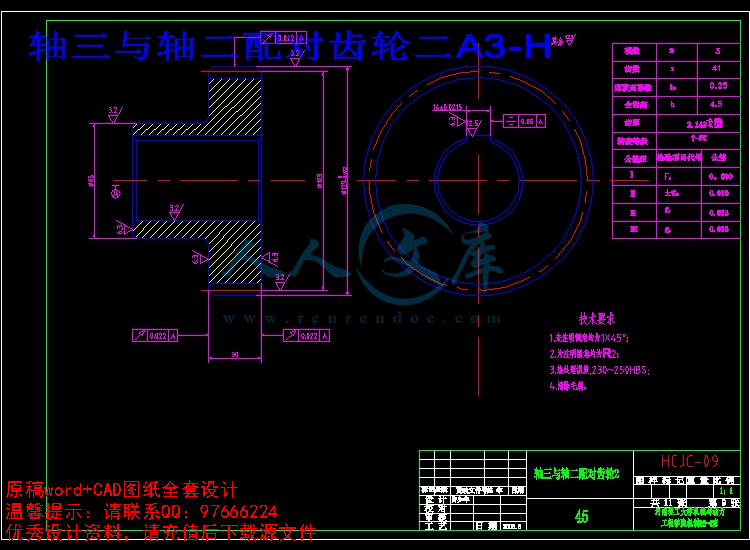
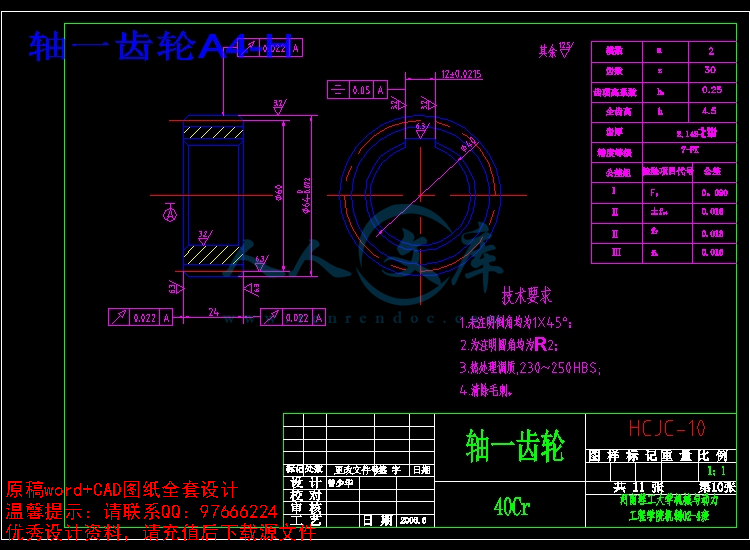

