KCSJ-06角板加工工艺与铣面夹具设计【CAD图纸和说明书】
收藏
资源目录
压缩包内文档预览:
编号:457133
类型:共享资源
大小:1MB
格式:RAR
上传时间:2015-07-16
上传人:好资料QQ****51605
认证信息
个人认证
孙**(实名认证)
江苏
IP属地:江苏
20
积分
- 关 键 词:
-
kcsj
06
加工
工艺
夹具
设计
cad
图纸
以及
说明书
仿单
- 资源描述:
-
目 录
目 录2
1.序 言1
2 计算生产纲领、确定生产类型1
3 审查零件图样的工艺性1
4 选择毛坯3
5 工艺过程的设计3
5.1 定位基准的选择3
5.2 零件表面加工方法的选择4
5.3 制订工艺路线4
6 确定机械加工余量及毛坯尺寸5
7 工序设计6
7.1 选择机床6
7.2 夹具选择6
7.3 选择刀具6
7.4 确定工序尺寸6
8 确定切削用量及基本工时7
9 专用夹具设计13
9.1定位基准的选择14
9.2 定位方案和元件设计14
9.3 夹紧机构的设计14
9.4 定位误差的计算14
9.5夹具设计说明14
参考文献15
角板的机械加工工艺规程及典型夹具
1.序 言
角板的加工工艺规程是在学完了机械制图、机械制造技术基础、机械设计、机械工程材料等进行课程设计之后的下一个教学环节。正确地解决一个零件在加工中的定位,夹紧以及工艺路线安排,工艺尺寸确定等问题,保证零件的加工质量。本次设计也要培养自己的自学与创新能力。因此本次设计综合性和实践性强、涉及知识面广。所以在设计中既要注意基本概念、基本理论,又要注意生产实践的需要,只有将各种理论与生产实践相结合,才能很好的完成本次设计。本次设计水平有限,其中难免有缺点错误,敬请老师们批评指正。
2 计算生产纲领、确定生产类型
课程设计的产品为一个角板零件。该产品的年产量为5000台,其设备品率为10%,机械加工废品率为1%,现制订该角板零件的机械加工工艺规程。
角板零件的年产量为5550件,可确定其生产类型为中批生产。
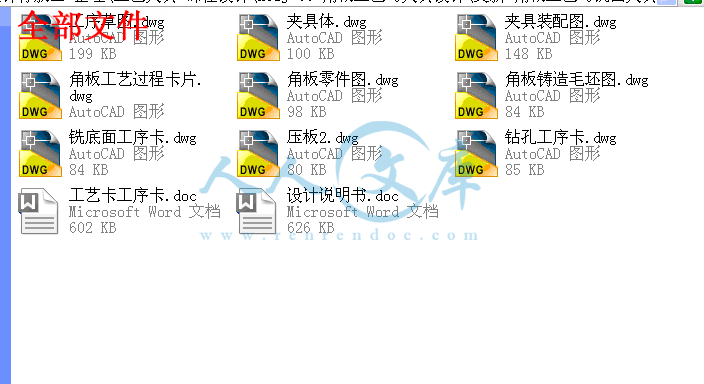

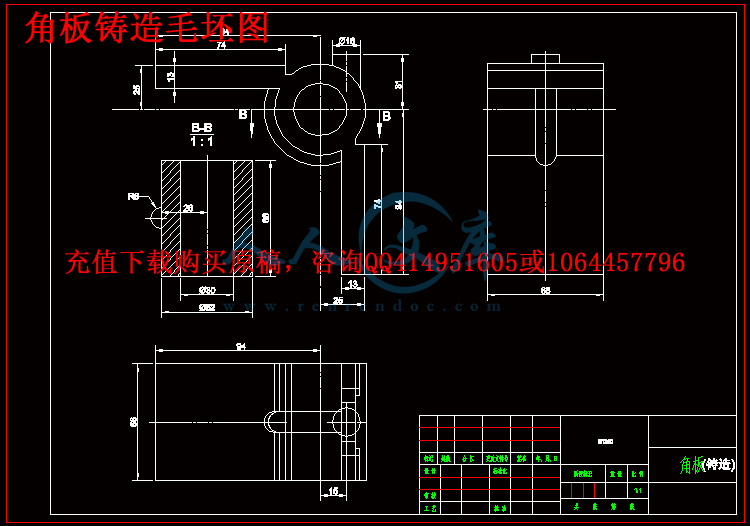

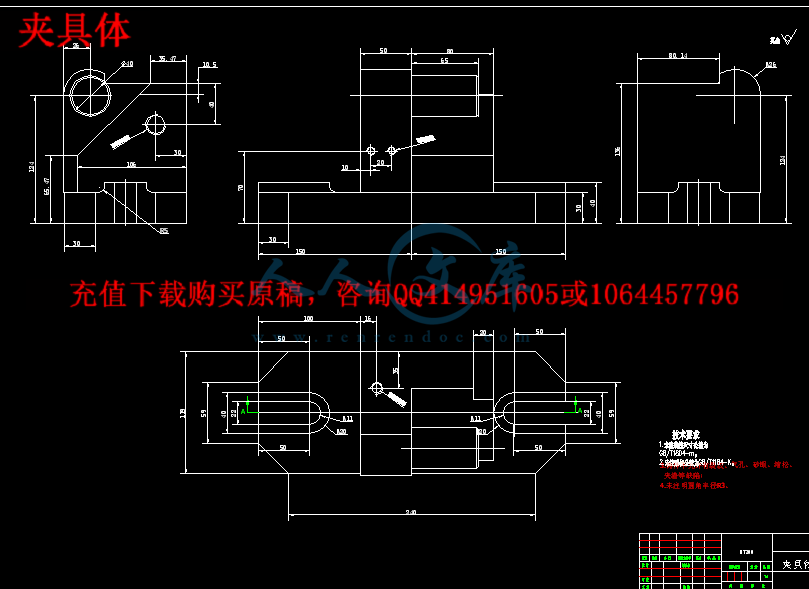
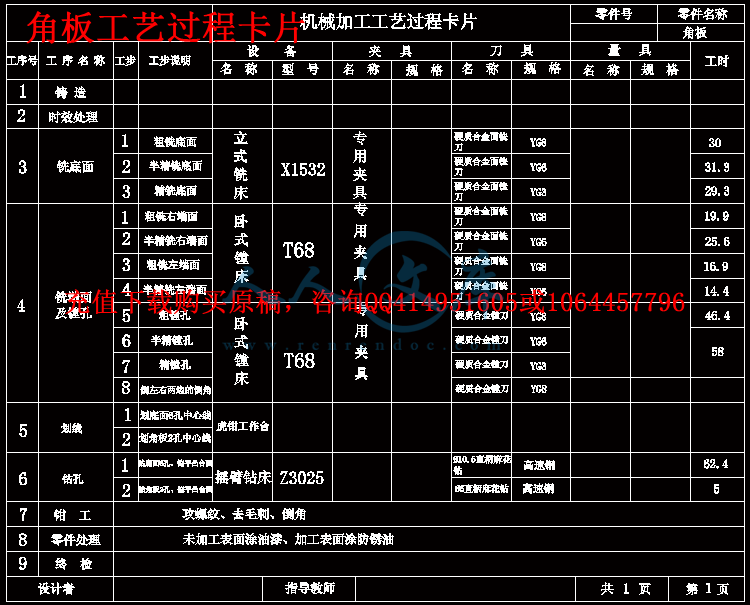

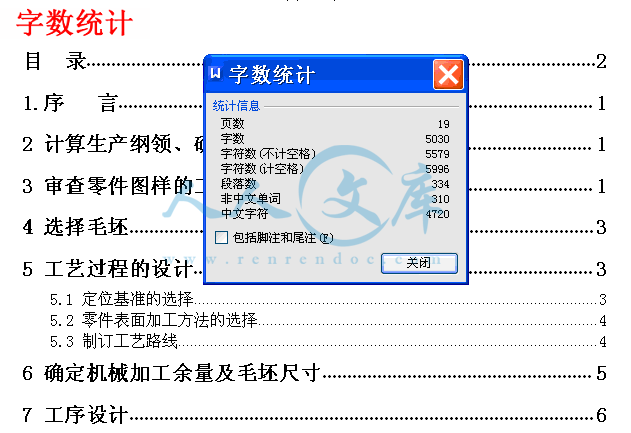
- 内容简介:
-
1 机械制造 课程设计 (论文 ) 题 目 :角板的机械加工工艺规程及典型夹具 所在学院 专 业 班 级 姓 名 学 号 指导老师 年 月 日 nts 2 目 录 目 录 . 2 1.序 言 . 3 2 计算生产纲领、确定生产类型 . 3 3 审查零件图样的工艺性 . 3 4 选择毛坯 . 5 5 工艺过程的设计 . 5 5.1 定位基准的选择 . 5 5.2 零件表面加工方法的选择 . 6 5.3 制订工艺路线 . 6 6 确定机械加工余量及毛坯尺寸 . 7 7 工序设计 . 8 7.1 选择机床 . 8 7.2 夹具选择 . 8 7.3 选择刀具 . 8 7.4 确定工序尺寸 . 8 8 确定切削用量及基本工时 . 9 9 专用夹具设计 . 15 9.1定位基准的选择 . 16 9.2 定位方案和元件设计 . 16 9.3 夹紧机构的设计 . 错误 !未定义书签。 9.4 定位误差的计算 . 错误 !未定义书签。 9.5夹具设计说明 . 错误 !未定义书签。 参考文献 . 16 nts 3 角板的机械加工工艺规程及典型夹具 1.序 言 角板 的加工工艺规程是在学完了机械制图、机械制造技术基础、机械设计、机械工程材料等进行课程设计之后的下一个教学环节。正确地解决一个零件在加工中的定位,夹紧以及工艺路线安排,工艺尺寸确定等问题,保证零件的加工质量。 本次设计也要培养自己的自学与创新能力。因此本次设计综合性和实践性强、涉及知识面广。所以在设计中既要 注意基本概念、基本理论,又要注意生产实践的需要,只有将各种理论与生产实践相结合,才能很好的完成本次设计。本次设计水平有限,其中难免有缺点错误,敬请老师们批评指正。 2 计算生产纲领、确定生产类型 课程设计的产品为一个角板零件。该产品的年产量为 5000台,其设备品率为 10%,机械加工废品率为 1%,现制订该角板零件的机械加工工艺规程。 5550%)1%101(15000%)%1( QnN 件 /年 角板零件的年产量为 5550件,可确定其生产类型为中批生产。 3 审查零件图样的工艺性 角板零件图样的视图正确、完整, 尺寸、公差及技术要求齐全。基准孔 mmH 740要求 mRa 6.1较高,可以通过粗镗、半精镗、精镗进行加工;本零件各表面要求的加工精度低,加工并不困难;角板上的 4个沟槽加工精度不高,可以直接用立铣刀铣出;角板凸台的螺纹孔,需经过钻底孔,再攻丝。角板加工表面和 mmH 740 有一定的位置要求,主要是上表面与 mmH 740 轴线的平行度为 0.06。 经过以上的分析,我们可以先选定粗基准,加工 精基准所在的加工表面,然后借nts 4 助夹具对其他表面进行加工,从而保证相应的位置精度。 角板 (铸件 )图 nts 5 角板加工图 4 选择毛坯 角板有 HT250铸造,轮廓尺寸不大,形状也不复杂,又属成批生产,故毛坯可以采用铸造成型。零件的形状不复杂,因而毛坯形状可以与零件的形状尽量接近,用砂型铸造,上下分模铸造出来。毛坯的尺寸通过确定加工余量后决定。 5 工艺过程的设计 5.1 定位基准的选择 本零件是带孔的角板,孔是设计基准,为避免由于基准不重合而产生的误差,应选孔为定位基准,即遵循“基准重合”的原则。由于角板除去下底面不需要加工,其他均需要加工,选定角板外圆 52 端面为粗基准,加工孔 mmH 740 ,此后选用孔mmH 740 为精基准,加工其余的表面以及铣槽。 nts 6 5.2 零件表面加工方法的选择 本零件的的加工面有内孔、上表面、槽及螺纹孔等,材料为 HT250。参阅手册,其加工方法选择如下: ( 1) mmH 740 的内孔,表面的粗糙度为 mRa 6.1,公差等级为 IT7,需要粗镗、半精镗、精镗。 ( 2)角板端面的粗糙度为 mRa 5.12,只需要粗铣即可达到要求。 ( 3)角板上表面的粗糙度为 mRa 3.6,公差等级为 IT10,需要经过粗铣、半精铣才能达到要求。 ( 4)角板上的槽的内表面的粗糙度为 mRa 3.6,公差等级为 IT10,需要经过粗铣、 半精铣才能达到要求。 ( 5)凸台 16 粗糙度为 mRa 5.12,只需要粗铣即可达到要求。 ( 6)螺纹孔 8M 需要经过钻孔、攻丝。 5.3 制订工艺路线 铣削加工在排列加工工序时,一般遵循基准先行、先主后次、先粗后细、先面后孔的原则,因而角板的加工工艺路线先加工角板端面,再加工孔 mmH 740 ,最后加工角板的上表面。按照上述的原则以及工序集中的特点,角板的加工可按下述工 艺路线进行: 010:以 mm52 处外圆及上端面定位,粗铣外圆的另外一个端面,粗镗孔mmH 740 。 020:以 mm52 外圆及粗铣后的端面定位,粗铣另外一个端面,半精镗孔mmH 740 。 030:以 mm52 外圆及端面定位,精镗孔 mmH 740 。 040:以 mmH 740 的 孔及端面定位,粗铣角板的一个表面。 050:以 mmH 740 的孔及端面定位,粗铣角板的另一表面以及凸台。 nts 7 060:以 mmH 740 的孔及端面定位,半精铣角板的一表面。 070:以 mmH 740 的孔及端面定位,半精铣角板的另一表面。 080:以 mmH 740 的孔及端面定位,粗铣角板的一表面的槽。 090:以 mmH 740 的孔及端面定位,粗铣角板的另一表 面的槽。 100:以 mmH 740 的孔及端面定位,半精铣铣角板的一表面的槽。 110:以 mmH 740 的孔及端面定位,半精铣铣角板的另一表面的槽。 120:以外圆端面定位,钻底孔。 130:以外圆端面定位,攻丝 8M 。 140:钳工去毛刺。 150:终检。 6 确定机械加工余量及毛坯尺寸 角板毛坯尺寸数据表 零件尺寸 单面加工余量 铸件尺寸 03.0040 28 10 2.5 3 3 35 31 13 60 3 及 2.5 65.5 角板毛坯尺寸允许公差数据表 铸件尺寸 公差 35 1.8 31 13 65.5 1.8 1.6 2.2 nts 8 7 工序设计 7.1 选择机床 ( 1)工序 010、 020、 040、 050、 080、 090 是粗铣, 060、 070、 100、 110 是半精铣。各工序额工步数不多,成批生不要求很高的生产率,选用卧式铣床就能满足要求。本零件的外形轮廓不大,精度 要求不是很高,选用 X61W即可满足要求。 ( 2)工序 030 是精镗,表面粗造的 6.1aR,加工精度要求高,选用 T740K即可满足要求。 ( 3)工序 120 是钻孔后攻丝,可选用 Z525 型立式钻床。 7.2 夹具选择 本零件角板出铣角板表面及铣槽需要专用的夹具外,其他的用通用夹具即可。镗孔和铣端面选用三爪自定心卡盘,钻孔和攻丝选用短销固定即可。 7.3 选择刀具 ( 1)铣削角板表面、端面和凸台时,选用高速钢镶齿圆柱铣刀,直径 80 。 ( 2) 铣削槽时,选用直柄键槽铣刀,直径 8 。 ( 3)钻孔 8.6 时,选用直柄麻花钻,直径 8.6 。 7.4 确定工序尺寸 ( 1) 740H 的工序尺寸及公差 用查表确定各道工序的加工余量及毛坯余量总余量如下:精镗加工余量 0.5mm;半精镗加工余量 1.0mm;粗镗加工余量 3.5mm,则毛坯的总余量为 5mm。 各工序的尺寸的基本尺寸如下:半精镗尺寸 mm5.395.040 ;粗镗尺寸mm5.3815.39 ;毛坯的尺寸 mm355.35.38 。 工序尺寸的公差及其偏差:精镗前的半精镗取 IT11 级,得 mmT 16.02 ;粗镗取 IT12级,得 mmT 25.01 ;毛坯公差取 mmT 8.10 。 工序尺寸偏差按“入体原则”标注:精镗 mm03.0040 ;半精镗 mm16.005.39 ; nts 9 粗镗 mm25.005.38 ;毛坯 mm8.135 。 ( 2)确定各加工表面的工序加工余量 工序 加工表面 总加工余量 工序加工余量 010 020 040 050 060 070 080 090 100 下端面 上端面 角板表面 角板表面 角板表面 角板表面 槽 槽 槽 5.5 5.5 3 3 3 3 10 10 10 2.5 3 2 2 1 1 10 10 10 110 槽 10 10 8 确定切削用量及基本工时 工序一:铸造 工序二:时效处理 工序三: 铣宽 60mm2 端面, 60mm2 端面粗糙度要求为 12.5.一次粗铣加工即可满足要求,我们选用 X51 立式铣床,高速钢端铣刀加工 工步一: 铣 60mm 上端面, 1. 选择刀具 刀具选取高速钢端铣刀,刀片采用 YG8, mma p 5.1 , mmd 600 , min/125 mv , 4z 。 2. 决定铣削用量 1) 决定铣削深度 因为加 工余量不大,一次加工完成 mma p 5.1 2) 决定每次进给量及切削速度 nts 10 根据 X51 型铣床说明书,其功率为为 7.5kw,中等系统刚度。 根据表查出 齿/2.0 mmf z ,则 m in/5.6216012510001000 rd vn s 按机床标准选取wn 750 min/r m in/3.1521 0 0 0 750601 0 0 0 mdnv w 当wn 750r/min 时 rmmznff wzm /60075042.0 按机床标准选取 rmmfm /6003) 计算工时 切削工时: mml 120 , mml 51 , mml 32 ,则机动工时为 m in8 5 3 3.02.0750 3512021 xfn llltwm. 工步二铣 60mm 下端面的切削用量及基本工时的计算如上在此不再累述: 工序四:钻,扩,绞 40孔 工步一钻孔至 39 确定进给量 f :根据参考文献 表 2-7,当钢的 MPab 800, mmd 390 时, rmf /47.039.0 。由于本零件在加工 31 孔时属于低刚度零件,故进给量应乘以系数 0.75,则 rmmf /35.029.075.047.039.0 根据 Z525 机床说明书,现取 rmmf /25.0 切削速度:根据参考文献 表 2-13 及表 2-14,查得切削速度 min/18 mv 所以 m in/15239 181 0 0 01 0 0 0 rd vnws 根据机床说明书,取 min/175 rnw ,故实际切削速度为 nts 11 m in/98.711 0 0 0 1 7 5391 0 0 0 mndv ww 切削工时: mml 60 , mml 91 , mml 32 ,则机动工时为 m in768.025.0375396021 fnllltwm工步二:扩孔 mm85.39 利用钻头将 mm39 孔扩大至 mm85.39 ,根据有关手册规定,扩钻的切削用量可根据钻孔的切削用量选取 rmmff/87.0585.075.065.08.12.18.12.1 钻 根据机床说明书,选取 rmmf /57.0 m i n/461231213121 mvv 钻则主轴转速为 m in/346.51 rn ,并按车床说明书取 min/68 rnw ,实际切削速度为 m in/8.61 0 0 0 6885.391 0 0 0 mndv ww 切削工时: mml 60 , mml 61 , mml 32 ,则机动工时为 m in78.157.068366021 fnllltwm工步 3:铰 mmH1140 孔 根据 参考文献 表 2-25, rmmf /4.02.0 , min/128 mv ,得 m in/65.2 5 48.1 6 9 rns 查参考文献 表 4.2-2,按机床实际进给量和实际转速,取 rmmf /35.0 ,min/198 rn w ,实际切削速度 min/33.9 mv 。 nts 12 切削工时: mml 60 , mml 91 , mml 32 ,则机动工时 为 m in038.135.0198396021 fnllltwm工序五: 铣 2 个 74x60mm 端面, 60mm2 端面粗糙度要求为 6.3 一次粗铣加工即可满足要求,我们选用 X51 立式铣床,高速钢端铣刀加工 工步一: 铣 74x60 上端面, 1. 选择刀具 刀具选取高速钢端铣刀,刀片采用 YG8, mma p 5.1 , mmd 600 , min/125 mv , 4z 。 2. 决定铣削用量 4) 决定铣削深度 因为加工余量不大,一次加工完成 mma p 5.1 5) 决定每次进给量及切削速度 根据 X51 型铣床说明书,其功率为为 7.5kw,中等系统刚度。 根据表查出 齿/2.0 mmf z ,则 m in/5.6216012510001000 rd vn s 按机床标准选取wn 750 min/r m in/3.1521 0 0 0 750601 0 0 0 mdnv w 当wn 750r/min 时 rmmznff wzm /60075042.0 按机床标准选取 rmmfm /6006) 计算工时 切削工时: mml 74 , mml 51 , mml 32 ,则机动工时为 nts 13 m in5 4 6 7.02.07 5 0 357421 xfn llltwm. 工步二:铣 74x60 右端面的切削用量及基本工时的计算如上,在此不再累述 工序六:铣长为 12 的 R4 的半圆槽 选择刀具 刀具选 取高速钢三面刃铣刀,刀片采用 YG8, mma p 5.1 , mmd 80 , min/25 mv , 4z 。 2. 决定铣削用量 7) 决定铣削深度 因为加工余量不大,故可在一次走刀内铣完,则 mma p 5.1 8) 决定每次进给量及切削速度 根据 X51 型铣床说明书,其功率为为 7.5kw,中等系统刚度。 根据表查出 齿/2.0 mmf z ,则 m in/9958 2510001000 rd vn s 按机床标准选取wn 1450 min/r m in/424.361000 145081000 mdnv w 当wn 1450r/min 时 rmmznff wzm /1 1 6 01 4 5 042.0 按机床标准选取 rmmfm /11609) 计算工时 切削工时: mml 121 ,则机动工时为 m in0 4 2.04 7 5121 fn ltwm铣削其余机床的切削用量及基本工时的计算,如上在此不再累述。 工序 VII: 15 端面 . 选择刀具 刀具选取不重磨损硬质合金套式端铣刀,刀片采用 YG8, nts 14 mma p 5.1 , mmd 200 , min/75 mv , 4z 。 2. 决定铣削用量 10) 决定铣削深度 因为加工余量不大,故可在一次走刀内铣完,则 mma p 5.1 11) 决定每次进给量及切削速度 根据 X51 型铣床说明书,其功率为为 7.5kw,中等系统刚度。 根据表查出 齿/2.0 mmf z ,则 m in/37.119420 7510001000 rd vn s 按机床标准选取wn 1450 min/r m in/35.1591000 1450351000 mdnv w 当wn 1450r/min 时 rmmznff wzm /1 1 6 01 4 5 042.0 按机床标准 选取 rmmfm /116012) 计算工时 切削工时: mml 15 , mml 51 , mml 32 ,则机动工时为 m in0 4 8 4 2.0475 351521 fn llltwm工序 VIII:钻 M8 螺纹孔的切削用量及基本工时的确定: 选用 Z525 立式钻床,选用 d= 6.8的麻花钻, M8的机用丝锥 选用 mm8.6 高速钢 锥柄麻花钻(工艺表 3.1 6) 由切削表 2.7 和工艺表 4.2 16查得 mm/r28.0f 机min/m8Vc (切削表 2.15) nts 15 m in/r6 3 6.86x 16x1 0 0 0Dv1 0 0 0 c 机机n按机床选取 5 4 5 / m innr机m i n/m8 5 4 2.61 0 0 0 545. 8 x6x1 0 0 0Dn 机机cV基本工时: 17.028.05453320f 21 xnlllt机机min 攻螺纹 M8mm: 选择 M8mm 高速钢机用丝锥 f 等于工件螺纹的螺距 p ,即 1 .2 5 /f m m r 7 .5 / m i ncVm机1000 1 0 0 0 7 . 5 2 9 8 ( / m i n )8cVnrD 查按机床选取 2 7 2 / m innr机6 .8 / m i ncVm机基本工时: 10.025.1x27 53320fnlllt 21 机9 专用夹具设计 由于大批量加工 ,为了提高劳动生产率和降低生产成本,保证加工质量,降低劳动强度,需要设计铣床专用夹具。由于对加工精度要求不是很高,所以在本道工序加工时,主要考虑如何降低降低生产成本和降低劳动强度。 本夹具是铣角板夹具上表面 60X74夹具设计 nts 16 9.1 定位基准的选择 在加工中用作确定工件在夹具中占有正确位置的基准,称为定位基准。据夹具手册知定位基准应尽可能与工序基准重合,在同一工件的各道工序中,应尽量采用同一定位基准进行加工。根据本道工序,选侧面为定位基准。 9.2 定位方案和元件设计 根据工序图及对零件的结构的分析,本道工序需限制 4个自由度,为了增加定位的可靠行,实际限制了其 6个自由度。本夹具采用 6点定位原则,用两个固定的支撑板作为一大平面,限制了工件的两个旋转自由度和一个移动自由度;用一个侧向支撑板作为一 参考文献 1 李 洪 机械加工工艺手册 M 北京出版社, 1996 1 2 陈宏钧 实用金属切削手册 M 机械工业出版社, 2005 1 3 上海市金属切削技术协会 金属切削手册 M 上海科学技术出版社, 2002 4 杨叔子 机械加工工艺师手册 M 机械工业出版社, 2000 5 徐鸿本 机床夹具设计手册 M 辽宁科学技术出版社, 2003 10 6 都克勤 机床夹具结构图册 M 贵州人民出版社, 1983 4 7 胡建新 机床夹具 M 中国劳动社会保障出版社, 2001 5 8 冯 道 机械零件切削加工工艺与技术标准实用手册 M 安徽文化音像出版社, 2003 9 王先逵 机械制造工艺学 M 机械工业出版社, 2000 10 马贤智 机械加工余量与公差手册 M 中国标准出版社, 1994 12 11 刘文剑 夹具工程师手册 M 黑龙江科学技术出版社, 1987 12 王光斗 机床夹具设计手册 M 上海科学技术出版社, 2002 8 nts 17 致谢词 非常感谢 XXX老师对我机械制造技术基础课程设计的指导,他给了我耐心的指导和无私的帮助。在此我向她们表示我诚挚的谢意。同时,感谢所有任课老师和所有同学在这四年来给自己的指导和帮助,是他们教会了我专业知识,教会了我如何学习,教会了我如何做人。正是由于他们,我才能在各方面取得显著的进步,在此向他们表示我由衷的谢意,并祝所有的老师培养出越来越多的优秀人才,桃李 满天下! 通过这一阶段的努力,我的 课程设计 终于完成了, 经过这一段时间, 我在学习上和思想上都受益非浅,这除了自身的努力外,与各位老师、同学和朋友的关心、支持和鼓励是分不开的。 从接触这次课程设计论文的题目到完成,我对自己大学几年的知识进行了重新的学习与巩固,使自己的专业知识更加牢固可靠,从而也更加明确了自己的努力方向,找到了自身的不足,在以后的学习和工作中,我会更加努力。 nts机械制造 课程设计 (论文 ) 题 目 :角板的机械加工工艺规程及典型夹具 所在学院 专 业 班 级 姓 名 学 号 指导老师 年 月 日 nts 2 目 录 目 录 . 2 1.序 言 . 3 2 计算生产纲领、确定生产类型 . 3 3 审查零件图样的工艺性 . 3 4 选择毛坯 . 5 5 工艺过程的设计 . 5 5.1 定位基准的选择 . 5 5.2 零件表面加工方法的选择 . 6 5.3 制订工艺路线 . 6 6 确定机械加工余量及毛坯尺寸 . 7 7 工序设计 . 8 7.1 选择机床 . 8 7.2 夹具选择 . 8 7.3 选择刀具 . 8 7.4 确定工序尺寸 . 8 8 确定切削用量及基本工时 . 9 9 专用夹具设计 . 15 9.1定位基准的选择 . 16 9.2 定位方案和元件设计 . 16 9.3 夹紧机构的设计 . 16 9.4 定位误差的计算 . 16 9.5夹具设计说明 . 16 参考文献 . 18 nts 3 角板的机械加工工艺规程及典型夹具 1.序 言 角板 的加工工艺规程是在学完了机械制图、机械制造技术基础、机械设计、机械工程材料等进行课程设计之后的下一个教学环节。正确地解决一个零件在加工中的定位,夹紧以及工艺路线安排,工艺尺寸确定等问题,保证零件的加工质量。 本次设计也要培养自己的自学与创新能力。因此本次设计综合性和实践性强、涉及知识面广。所以在设计中既要注 意基本概念、基本理论,又要注意生产实践的需要,只有将各种理论与生产实践相结合,才能很好的完成本次设计。本次设计水平有限,其中难免有缺点错误,敬请老师们批评指正。 2 计算生产纲领、确定生产类型 课程设计的产品为一个角板零件。该产品的年产量为 5000台,其设备品率为 10%,机械加工废品率为 1%,现制订该角板零件的机械加工工艺规程。 5550%)1%101(15000%)%1( QnN 件 /年 角板零件的年产量为 5550件,可确定其生产类型为中批生产。 3 审查零件图样的工艺性 角板零件图样的视图正确、完整,尺 寸、公差及技术要求齐全。基准孔 mmH 740要求 mRa 6.1较高,可以通过粗镗、半精镗、精镗进行加工;本零件各表面要求的加工精度低,加工并不困难;角板上的 4个沟槽加工精度不高,可以直接用立铣刀铣出;角板凸台的螺纹孔,需经过钻底孔,再攻丝。角板加工表面和 mmH 740 有一定的位置要求,主要是上表面与 mmH 740 轴线的平行度为 0.06。 经过以上的分析,我们可以先选定粗基准,加工精 基准所在的加工表面,然后借助夹具对其他表面进行加工,从而保证相应的位置精度。 nts 4 角板 (铸件 )图 nts 5 角板加工图 4 选择毛坯 角板有 HT250铸造,轮廓尺寸不大,形状也不复杂,又属成批生产,故毛坯可以采用铸造成型。零件的形状不复杂,因而毛坯形状可以与零件的形状尽量接近,用砂型铸造,上下分模铸造出来。毛坯的尺寸通过确定加工余量后决定。 5 工艺过程的设计 5.1 定位基准的选择 本零件是带孔的角板,孔是设计基准,为避免由于基准不重合而产生的误差,应选孔为定位基准,即遵循“基准重合”的原则。由于角板除去下底面不需要加工,其他均需要加工,选定角板外圆 52 端面为粗基准,加工孔 mmH 740 ,此后选用孔mmH 740 为精基准,加工其余的表面以及铣槽。 nts 6 5.2 零件表面加工方法的选择 本零件的的加工面有内孔、上表面、槽及螺纹孔等,材料为 HT250。参阅手册,其加工方法选择如下: ( 1) mmH 740 的内孔,表面的粗糙度为 mRa 6.1,公差等级为 IT7,需要粗镗、半精镗、精镗。 ( 2)角板端面的粗糙度为 mRa 5.12,只需要粗铣即可达到要求。 ( 3)角板上表面的粗糙度为 mRa 3.6,公差等级为 IT10,需要经过粗铣、半精铣才能达到要求。 ( 4)角板上的槽的内表面的粗糙度为 mRa 3.6,公差等级为 IT10,需要经过粗铣、半 精铣才能达到要求。 ( 5)凸台 16 粗糙度为 mRa 5.12,只需要粗铣即可达到要求。 ( 6)螺纹孔 8M 需要经过钻孔、攻丝。 5.3 制订工艺路线 铣削加工在排列加工工序时,一般遵循基准先行、先主后次、先粗后细、先面后孔的原则,因而角板的加工工艺路线先加工角板端面,再加工孔 mmH 740 ,最后加工角板的上表面。按照上述的原则以及工序集中的特点,角板的加工可按下述工艺 路线进行: 010:以 mm52 处外圆及上端面定位,粗铣外圆的另外一个端面,粗镗孔mmH 740 。 020:以 mm52 外圆及粗铣后的端面定位,粗铣另外一个端面,半精镗孔mmH 740 。 030:以 mm52 外圆及端面定位,精镗孔 mmH 740 。 040:以 mmH 740 的孔 及端面定位,粗铣角板的一个表面。 050:以 mmH 740 的孔及端面定位,粗铣角板的另一表面以及凸台。 nts 7 060:以 mmH 740 的孔及端面定位,半精铣角板的一表面。 070:以 mmH 740 的孔及端面定位,半精铣角板的另一表面。 080:以 mmH 740 的孔及端面定位,粗铣角板的一表面的槽。 090:以 mmH 740 的孔及端面定位,粗铣角板的另一表面 的槽。 100:以 mmH 740 的孔及端面定位,半精铣铣角板的一表面的槽。 110:以 mmH 740 的孔及端面定位,半精铣铣角板的另一表面的槽。 120:以外圆端面定位,钻底孔。 130:以外圆端面定位,攻丝 8M 。 140:钳工去毛刺。 150:终检。 6 确定机械加工余量及毛坯尺寸 角板毛坯尺寸数据表 零件尺寸 单面加工余量 铸件尺寸 03.0040 28 10 2.5 3 3 35 31 13 60 3 及 2.5 65.5 角板毛坯尺寸允许公差数据表 铸件尺寸 公差 35 1.8 31 13 65.5 1.8 1.6 2.2 nts 8 7 工序设计 7.1 选择机床 ( 1)工序 010、 020、 040、 050、 080、 090 是粗铣, 060、 070、 100、 110 是半精铣。各工序额工步数不多,成批生不要求很高的生产率,选用卧式铣床就能满足要求。本零件的外形轮廓不大,精度要 求不是很高,选用 X61W即可满足要求。 ( 2)工序 030 是精镗,表面粗造的 6.1aR,加工精度要求高,选用 T740K即可满足要求。 ( 3)工序 120 是钻孔后攻丝,可选用 Z525 型立式钻床。 7.2 夹具选择 本零件角板出铣角板表面及铣槽需要专用的夹具外,其他的用通用夹具即可。镗孔和铣端面选用三爪自定心卡盘,钻孔和攻丝选用短销固定即可。 7.3 选择刀具 ( 1)铣削角板表面、端面和凸台时,选用高速钢镶齿圆柱铣刀,直径 80 。 ( 2)铣 削槽时,选用直柄键槽铣刀,直径 8 。 ( 3)钻孔 8.6 时,选用直柄麻花钻,直径 8.6 。 7.4 确定工序尺寸 ( 1) 740H 的工序尺寸及公差 用查表确定各道工序的加工余量及毛坯余量总余量如下:精镗加工余量 0.5mm;半精镗加工余量 1.0mm;粗镗加工余量 3.5mm,则毛坯的总余量为 5mm。 各工序的尺寸的基本尺寸如下:半精镗尺寸 mm5.395.040 ;粗镗尺寸mm5.3815.39 ;毛坯的尺寸 mm355.35.38 。 工序尺寸的公差及其偏差:精镗前的半精镗取 IT11 级,得 mmT 16.02 ;粗镗取 IT12级,得 mmT 25.01 ;毛坯公差取 mmT 8.10 。 工序尺寸偏差按“入体原则”标注:精镗 mm03.0040 ;半精镗 mm16.005.39 ; nts 9 粗镗 mm25.005.38 ;毛坯 mm8.135 。 ( 2)确定各加工表面的工序加工余量 工序 加工表面 总加工余量 工序加工余量 010 020 040 050 060 070 080 090 100 下端面 上端面 角板表面 角板表面 角板表面 角板表面 槽 槽 槽 5.5 5.5 3 3 3 3 10 10 10 2.5 3 2 2 1 1 10 10 10 110 槽 10 10 8 确 定切削用量及基本工时 工序一:铸造 工序二:时效处理 工序三: 铣宽 60mm2 端面, 60mm2 端面粗糙度要求为 12.5.一次粗铣加工即可满足要求,我们选用 X51 立式铣床,高速钢端铣刀加工 工步一: 铣 60mm 上端面, 1. 选择刀具 刀具选取高速钢端铣刀,刀片采用 YG8, mma p 5.1 , mmd 600 , min/125 mv , 4z 。 2. 决定铣削用量 1) 决定铣削深度 因为加工 余量不大,一次加工完成 mma p 5.1 2) 决定每次进给量及切削速度 nts 10 根据 X51 型铣床说明书,其功率为为 7.5kw,中等系统刚度。 根据表查出 齿/2.0 mmf z ,则 m in/5.6216012510001000 rd vn s 按机床标准选取wn 750 min/r m in/3.1521 0 0 0 750601 0 0 0 mdnv w 当wn 750r/min 时 rmmznff wzm /60075042.0 按机床标准选取 rmmfm /6003) 计算工时 切削工时: mml 120 , mml 51 , mml 32 ,则机动工时为 m in8 5 3 3.02.0750 3512021 xfn llltwm. 工步二铣 60mm 下端面的切削用量及基本工时的计算如上在此不再累述: 工序四:钻,扩,绞 40孔 工步一钻孔至 39 确定进给量 f :根据参考文献 表 2-7,当钢的 MPab 800, mmd 390 时, rmf /47.039.0 。由于本零件在加工 31 孔时属于低刚度零件,故进给量应乘以系数 0.75,则 rmmf /35.029.075.047.039.0 根据 Z525 机床说明书,现取 rmmf /25.0 切削速度:根据参考文献 表 2-13 及表 2-14,查得切削速度 min/18 mv 所以 m in/15239 181 0 0 01 0 0 0 rd vnws 根据机床说明书,取 min/175 rnw ,故实际切削速度为 nts 11 m in/98.711 0 0 0 1 7 5391 0 0 0 mndv ww 切削工时: mml 60 , mml 91 , mml 32 ,则机动工时为 m in768.025.0375396021 fnllltwm工步二:扩孔 mm85.39 利用钻头将 mm39 孔扩大至 mm85.39 ,根据有关手册规定,扩钻的切削用量可根据钻孔的切削用量选取 rmmff/87.0585.075.065.08.12.18.12.1 钻 根据机床说明书,选取 rmmf /57.0 m i n/461231213121 mvv 钻则主轴转速为 m in/346.51 rn ,并按车床说明书取 min/68 rnw ,实际切削速度为 m in/8.61 0 0 0 6885.391 0 0 0 mndv ww 切削工时: mml 60 , mml 61 , mml 32 ,则机动工时为 m in78.157.068366021 fnllltwm工步 3:铰 mmH1140 孔 根据 参考文献 表 2-25, rmmf /4.02.0 , min/128 mv ,得 m in/65.2 5 48.1 6 9 rns 查参考文献 表 4.2-2,按机床实际进给量和实际转速,取 rmmf /35.0 ,min/198 rn w ,实际切削速度 min/33.9 mv 。 nts 12 切削工时: mml 60 , mml 91 , mml 32 ,则机动工时为 m in038.135.0198396021 fnllltwm工序五: 铣 2 个 74x60mm 端面, 60mm2 端面粗糙度要求为 6.3 一次粗铣加工即可满足要求,我们选用 X51 立式铣床,高速钢端铣刀加工 工步一: 铣 74x60 上端面, 1. 选择刀具 刀具选取高速钢端铣刀,刀片采用 YG8, mma p 5.1 , mmd 600 , min/125 mv , 4z 。 2. 决定铣削用量 4) 决定铣削深度 因为加工余量不大,一次加工完成 mma p 5.1 5) 决定每次进给量及切削速度 根据 X51 型铣床说明书,其功率为为 7.5kw,中等系统刚度。 根据表查出 齿/2.0 mmf z ,则 m in/5.6216012510001000 rd vn s 按机床标准选取wn 750 min/r m in/3.1521 0 0 0 750601 0 0 0 mdnv w 当wn 750r/min 时 rmmznff wzm /60075042.0 按机床标准选取 rmmfm /6006) 计算工时 切削工时: mml 74 , mml 51 , mml 32 ,则机动工时为 nts 13 m in5 4 6 7.02.07 5 0 357421 xfn llltwm. 工步二:铣 74x60 右端面的切削用量及基本工时的计算如上,在此不再累述 工序六:铣长为 12 的 R4 的半圆槽 选择刀具 刀具选取 高速钢三面刃铣刀,刀片采用 YG8, mma p 5.1 , mmd 80 , min/25 mv , 4z 。 2. 决定铣削用量 7) 决定铣削深度 因为加工余量不大,故可在一次走刀内铣完,则 mma p 5.1 8) 决定每次进给量及切削速度 根据 X51 型铣床说明书,其功率为为 7.5kw,中等系统刚度。 根据表查出 齿/2.0 mmf z ,则 m in/9958 2510001000 rd vn s 按机床标准选取wn 1450 min/r m in/424.361000 145081000 mdnv w 当wn 1450r/min 时 rmmznff wzm /1 1 6 01 4 5 042.0 按机床标准选取 rmmfm /11609) 计算工时 切削工时: mml 121 ,则机动工时为 m in0 4 2.04 7 5121 fn ltwm铣削其余机床的切削用量及基本工时的计算,如上在此不再累述。 工序 VII: 15 端面 . 选择刀具 刀具选取不重磨损硬质合金套式端铣刀,刀片采用 YG8, nts 14 mma p 5.1 , mmd 200 , min/75 mv , 4z 。 2. 决定铣削用量 10) 决定铣削深度 因为加工余量不大,故可在一次走刀内铣完,则 mma p 5.1 11) 决定每次进给量及切削速度 根据 X51 型铣床说明书,其功率为为 7.5kw,中等系统刚度。 根据表查出 齿/2.0 mmf z ,则 m in/37.119420 7510001000 rd vn s 按机床标准选取wn 1450 min/r m in/35.1591000 1450351000 mdnv w 当wn 1450r/min 时 rmmznff wzm /1 1 6 01 4 5 042.0 按机床标准选 取 rmmfm /116012) 计算工时 切削工时: mml 15 , mml 51 , mml 32 ,则机动工时为 m in0 4 8 4 2.0475 351521 fn llltwm工序 VIII:钻 M8 螺纹孔的切削用量及基本工时的确定: 选用 Z525 立式钻床,选用 d= 6.8的麻花钻, M8的机用丝锥 选用 mm8.6 高速钢锥 柄麻花钻(工艺表 3.1 6) 由切削表 2.7 和工艺表 4.2 16查得 mm/r28.0f 机min/m8Vc (切削表 2.15) nts 15 m in/r6 3 6.86x 16x1 0 0 0Dv1 0 0 0 c 机机n按机床选取 5 4 5 / m innr机m i n/m8 5 4 2.61 0 0 0 545. 8 x6x1 0 0 0Dn 机机cV基本工时: 17.028.05453320f 21 xnlllt机机min 攻螺纹 M8mm: 选择 M8mm 高速钢机用丝锥 f 等于工件螺纹的螺距 p ,即 1 .2 5 /f m m r 7 .5 / m i ncVm机1000 1 0 0 0 7 . 5 2 9 8 ( / m i n )8cVnrD 查按机床选取
- 温馨提示:
1: 本站所有资源如无特殊说明,都需要本地电脑安装OFFICE2007和PDF阅读器。图纸软件为CAD,CAXA,PROE,UG,SolidWorks等.压缩文件请下载最新的WinRAR软件解压。
2: 本站的文档不包含任何第三方提供的附件图纸等,如果需要附件,请联系上传者。文件的所有权益归上传用户所有。
3.本站RAR压缩包中若带图纸,网页内容里面会有图纸预览,若没有图纸预览就没有图纸。
4. 未经权益所有人同意不得将文件中的内容挪作商业或盈利用途。
5. 人人文库网仅提供信息存储空间,仅对用户上传内容的表现方式做保护处理,对用户上传分享的文档内容本身不做任何修改或编辑,并不能对任何下载内容负责。
6. 下载文件中如有侵权或不适当内容,请与我们联系,我们立即纠正。
7. 本站不保证下载资源的准确性、安全性和完整性, 同时也不承担用户因使用这些下载资源对自己和他人造成任何形式的伤害或损失。

人人文库网所有资源均是用户自行上传分享,仅供网友学习交流,未经上传用户书面授权,请勿作他用。