!【详情如下】CAD图纸+word设计说明书.doc[12000字,48页]【需要咨询购买全套设计请加QQ97666224】.bat
上阀盖A2.dwg
下阀盖用A1打印.dwg
导轨套A3.dwg
球体A2.dwg
装配图A0.dwg
轴套A3.dwg
轴承压盖A3.dwg
阀体A0.dwg
阀杆A2.dwg
英语翻译.doc
设计说明书.doc[12000字,48页]
无摩擦球阀设计
摘要:该设计是为了改善传统球阀的缺点而做的,传统球阀的缺点是摩擦大、使用寿命短、密封性能不好。此设计可以根据流体冲蚀磨损、腐蚀程度和工作压力来调整密封比压。轨道式无摩擦球阀是一种新型的球阀,它利用阀杆头部的斜面凸轮与导轨套螺旋槽的配合来实现球阀的无摩擦开启、关闭和金属密封的新型阀门;所以设计中的关键问题是要避免产生摩擦,密封要紧,最终达到高效率、高质量、耐用性等要求。本论文研究对轨道式无摩擦球阀的运动和动力分析方法,完成了球阀启闭运动轨迹、球体运动空间以及主要零部件的受力分析设计。该球阀具有启闭无磨损,关闭时压力可调节和启闭省力的优点;克服了普通球阀因密封比压大而使密封面容易磨损的缺点,延长了球阀的使用寿命。
关键词:无摩擦;球阀;轨道式;凸轮
Design of Non-Friction Ball Valve
Abstract: The design is to improve the shortcomings of traditional ball valve , and the shortcomings of traditional ball valve is friction, short life, sealing performance bad. According to this design`s fluid erosion, corrosion and pressure then the pressure was adjust sealed .Orbit Non-Friction Ball Valve is a new type of valve and realizes non-friction switching and metal pressurization of the valve by cam mechanism.This paper researches the design of Orbit Non-Fraction Ball Valve’s move and the analysis of dynamically. The paper puts forward the kinetic analysis method of Orbit Non-Fraction Ball Valve, analysising the track and motion space of the conglobulation for switching etc, and bring forward rule of its configuration design, designing its assembling body and main parts. This valve has a series of advantage, such as non-friction, the adjusting of pressure and laborsaving when it switches .Its pressurization is different from the usual whose pressurization is easy to destroy, which overcome the fault of the usual valves. So it has a longer life-span.
KeyWords: Orbit, Non-Friction, Ball Valve, Cam
目录
第1章 引言1
1.1课题来源1
1.2选题目的和意义1
1.3球阀的发展趋势2
1.4本文研究的主要内容2
第2章 主要结构参数4
2.1.轨道式无摩擦球阀技术要求4
2.1.1技术参数4
2.1.2技术要求4
2.1.3型号及其含义4
2.2主要结构尺寸4
2.2.1球体直径4
2.2.2密封面宽度及压紧比压5
2.2.3密封比压6
2.2.4球阀结构长度及连接法兰尺寸6
第3章 运动轨迹设计7
3.1球阀启闭运动轨迹7
3.1.1滚动启闭7
3.1.2球阀摆动7
3.1.3凸轮的轮廓8
3.2球阀下支承外形10
3.2.1滚动柱面与倒角半径10
3.2.2倒角中心点位置11
3.3.3滚动空间12
第4章 结构设计和计算13
4.1阀杆机构受力状况13
4.1.1球阀受力状况13
4.1.2阀杆支承反力与支承结构型式选择14
4.1.3摩擦阻力扭矩16
4.1.4阀杆承受的轴向力18
4.2操作扭矩和手轮选择21
4.2.1操纵扭矩Mc21
4.2.2径D选择22
4.3零件设计与计算22
4.3.1具有螺旋导轨槽衬套的主要结构尺寸22
4.3.2球阀销轴接触强度23
4.3.3球阀下支承的接触强度24
第5章 工作能力校核31
5.1工作寿命31
5.2实际工作压力的潜力估计31
5.2.1阀体壁厚承压能力31
5.2.2阀体与阀盖连接螺栓33
5.2.3阀盖连接法兰承载能力35
5.2.4阀杆头部承载能力37
5.3寿命和实际工作潜力估计38
5.3.1寿命估计38
5.3.2承压能力估计39
结 论40
致 谢41
参考文献42
参考文献
[1]郑文纬,吴克坚.机械原理.北京:高等教育出版社,1997.7
[2]杨明忠,朱家诚.机械设计.武汉:武汉理工大学出版社,2001.1
[3]成都乘分阀门有限责任公司.轨道式无摩擦球阀技术要求,2000.9.5
[4]沈阳高中压阀门厂.阀门制造工艺. 北京:机械工业出版社,1984.6
[5]《机械设计手册》联合编写组.机械设计手册(二版).北京:化学工业出版社,1979.2
[6]成大先.机械设计手册(常用工程材料)北京:化学工业出版社,2004.1
[7]机械工业部合肥通用机械研究所.阀门.北京:机械工业出版社,1981.12
[8]机械工程手册电机工程手册编辑委员会.机械工程手册(离心机 阀门). 北京:机械工业出版社,1979.1
[9]樊炳辉,云江.MDT.北京:清华大学出版社,1999.3
[10]汤从心.凸轮与凸轮机构基础.北京:国防工业出版社,1985.8
[11]莱昂斯.阀门技术手册. 北京:机械工业出版社,1991.2
[12]马祖达,吴剑武.轨道球阀的特性与设计.阀门.1999年第四期
[13]姜钢琳.球阀材质与密封.阀门.2001.6
[14]王加新.球阀密封结构的分析与研究.阀门.2000.7
[15]王舟一.球阀金属密封副高温压力密封的探讨.流体机械.1999.4
[16]卜丹霞.如何延长球阀的使用寿命.阀门.1999.4
[17]杨源泉.阀门设计手册[M].北京:机械工业出版社.1992
[18]Paul E Allaire,Roger Fittro,et al.Eddy currents,magnetic flux and force in solid magnetic Zthrust bearing [C].In:proc.of the international Symposium on Magnetic Bearing , urich,1994:157-163.
[19]Yanhua Sun,Lie Yu.Eddy currents effects on radical active magnetic bearings with solid rotor [C].In:Proc.of The International Symposium on Magetic Bearing ,Japan,2002:361-367.








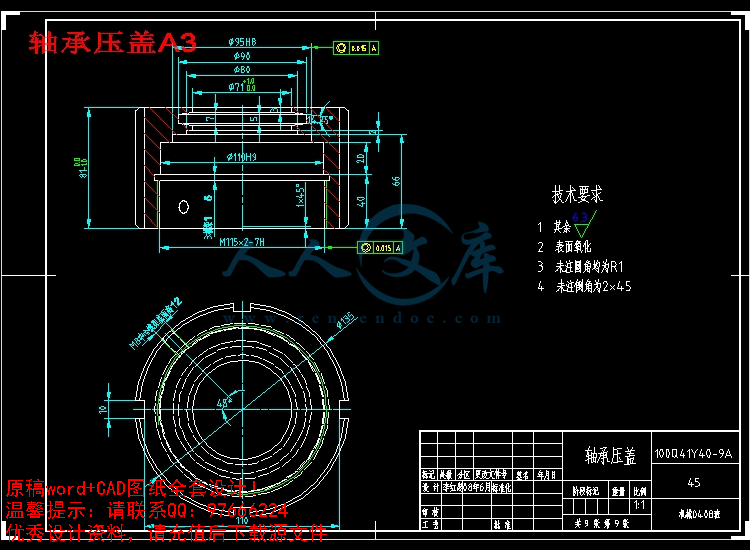

