摘 要
在机械制造业中,机械手已被广泛应用,大大地改善了工人的劳动条件,显著地提高劳动生产率,加快了实现工业生产机械化和自动化的步伐。
本文通过对机械手的组成和分类,及国内外的发展状况的了解,对本课题任务进行了总体方案设计。确定了机械手用三自由度和圆柱坐标型式。设计了机械手的夹持式手部结构;以及设计了机械手的总体结构,以实现机械手伸缩,升降,回转三个自由度及手爪的开合。驱动方式由气缸来实现手臂伸缩和升降,异步电机来实现机械手的旋转。
运用了FX 系列可编程序控制器(PLC)对上下料机械手进行控制, 论述了电气控制系统的硬件设计, 控制软件结构以及手动控制程序和自动控制程序的设计。
关键词:机械手,气缸,可编程序控制器
Abstract
In mechanical manufacturing industry, manipulator has been applied extensively so that the labor condition of worker has been greatly improved , labor productivity raised notably, the step of industrial production mechanization and automation realized rapidly.
This article through to manipulator's composition and the classification, and the domestic and foreign development condition's understanding, has carried on the overall concept design to this topic duty. Had determined the manipulator uses three degrees-of-freedom and the circular cylindrical coordinate pattern. Has designed manipulator's clamp type hand structure; As well as has designed manipulator's gross structure, realizes the manipulator to expand and contract, the fluctuation, rotates three degrees-of-freedom and hand fingernail's opening and closing. The drive type realizes the arm expansion and the fluctuation by the air cylinder, the asynchronous machine realizes manipulator's revolving.
The paper illustrates that the control of the upper and lower material by means of the PLC and also includes the hardware design of the electric control system, the control software structure and the design of the manual and automatic control program.
Key words: manipulator, air cylinder, Programmable controller(PLC)
目 录
1 绪言1
1.1 机械手的概述1
1.2 我国机械手的发展1
1.3 气动机械手的应用现状及发展前景3
1.4 本课题设计要求5
2 机械手的总体设计方案7
2.1 机械手的系统工作原理及组成7
2.2 机械手基本形式的选择8
2.3 驱动机构的选择9
2.4 机械手的技术参数列表9
3 机械手的机械系统设计11
3.1 机械手的运动概述11
3.2 机器人的运动过程分析12
4 机械手手部结构设计及计算13
4.1 手部结构13
4.2 手部结构设计及计算14
4.3 夹紧气缸的设计16
5 机械手手臂机构的设计22
5.1 手臂的设计要求22
5.2 伸缩气压缸的设计22
5.3 导向装置27
6 机械手腰部和基座结构设计及计算29
6.1 结构设计29
6.2 控制手臂上下移动的腰部气缸的设计29
6.3 导向装置33
6.4 平衡装置33
6.5 基座结构设计34
7 气动系统设计37
7.1 气压传动系统工作原理图37
8 机械手的PLC控制系统设计39
8.1 可编程序控制器的选择及工作过程39
8.2 可编程序控制器的使用步骤40
8.3 机械手可编程序控制器控制方案40
9 结论52
参考文献53
致谢54



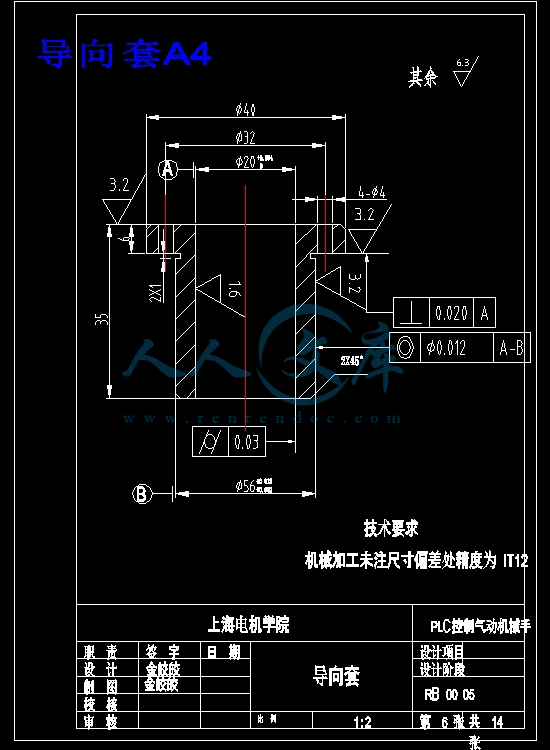
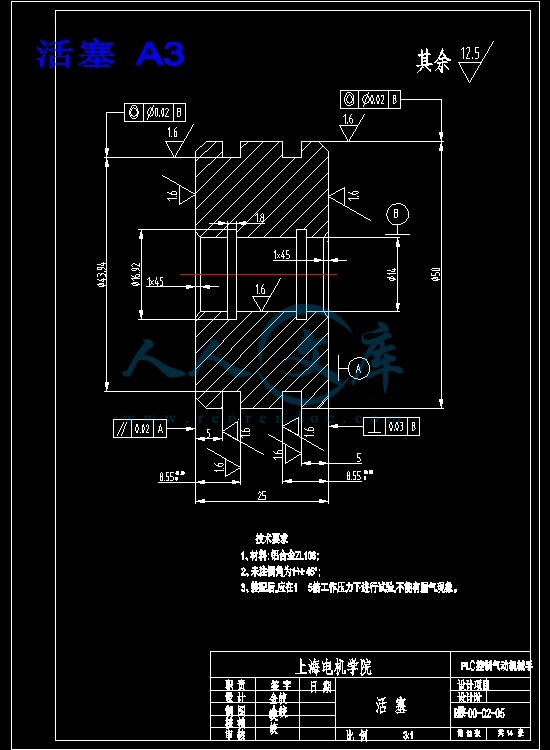








