SC003-减速箱传动轴的数控车削工艺【优秀数控类课题】【带3张CAD图纸】
收藏
资源目录
压缩包内文档预览:(预览前5页/共22页)
编号:459896
类型:共享资源
大小:1.10MB
格式:ZIP
上传时间:2015-07-24
上传人:小***
认证信息
个人认证
林**(实名认证)
福建
IP属地:福建
40
积分
- 关 键 词:
-
sc003
减速
传动轴
数控
车削
工艺
优秀
优良
课题
cad
图纸
- 资源描述:
-
传动轴的数控加工工艺及编程【优秀数控类课题】【带3张CAD图纸】【详情如下】
CAD图纸+word设计说明书.doc[5400字,22页]【需要咨询购买全套设计请加QQ97666224】.bat
实习报告.doc
图.doc
外文翻译=数控机床的特点=中文1600字.doc
设计说明书.doc[5400字,22页]
工序图1.dwg
工序图2.dwg
零件图及装配图.dwg
摘 要
轴类零件是常见的典型零件之一。按轴类零件结构形式不同,一般可分为光轴、阶梯轴和异形轴三类;或分为实心轴、空心轴等。它们在机器中用来支承齿轮、带轮等传动零件,以传递转矩或运动。台阶轴的加工工艺较为典型,反映了轴类零件加工的大部分内容与基本规律。下面就以减速箱中的传动轴为例,介绍一般台阶轴的加工工艺。
关键词:传动轴、工艺分析、程序设计。
目 录
摘 要2
目 录3
引言3
1、传动轴零件图的分析5
2、确定毛坯7
3、确定主要表面的加工方法7
4、确定定位基准7
5、划分阶段8
6、热处理工序安排8
7、加工尺寸和切削用量9
8、拟定工艺过程9
9、传动轴机械加工工艺过程工序简图12
10、数控编程15
结束语20
致 谢21
参考文献22
减速箱传动轴的数控车削工艺
引言
减速器是原动机和工作机之间的独立的闭式传动装置,用来降低转速和增大转矩,以满足工作需要,在某些场合也用来增速,称为增速器。 选用减速器时应根据工作机的选用条件,技术参数,动力机的性能,经济性等因素,比较不同类型、品种减速器的外廓尺寸,传动效率,承载能力,质量,价格等,选择最适合的减速器。
减速器的类别、品种、型式很多,目前已制定为行(国)标的减速器有40余种。减速器的类别是根据所采用的齿轮齿形、齿廓曲线划分;减速器的品种是根据使用的需要而设计的不同结构的减速器;减速器的型式是在基本结构的基础上根据齿面硬度、传动级数、出轴型式、装配型式、安装型式、联接型式等因素而设计的不同特性的减速器。
与减速器联接的工作机载荷状态比较复杂,对减速器的影响很大,是减速器选用及计算的重要因素,减速器的载荷状态即工作机(从动机)的载荷状态,通常分为三类:
①—均匀载荷;
②—中等冲击载荷;
③—强冲击载荷。
正确的安装,使用和维护减速器,是保证机械设备正常运行的重要环节。 因此,在您安装减速器时,请务必严格按照下面的安装使用相关事项,认真地装配和使用。
第一步是安装前确认电机和减速器是否完好无损,并且严格检查电机与减速器相连接的各部位尺寸是否匹配,这里是电机的定位凸台、输入轴与减速器凹槽等尺寸及配合公差。
第二步是旋下减速器法兰外侧防尘孔上的螺钉,调整夹紧环使其侧孔与防尘孔对齐,插入内六角旋紧。之后,取走电机轴键。
第三步是将电机与减速器自然连接。连接时必须保证减速器输出轴与电机输入轴同心度一致,且二者外侧法兰平行。如同心度不一致,会导致电机轴折断或减速机齿轮磨损。



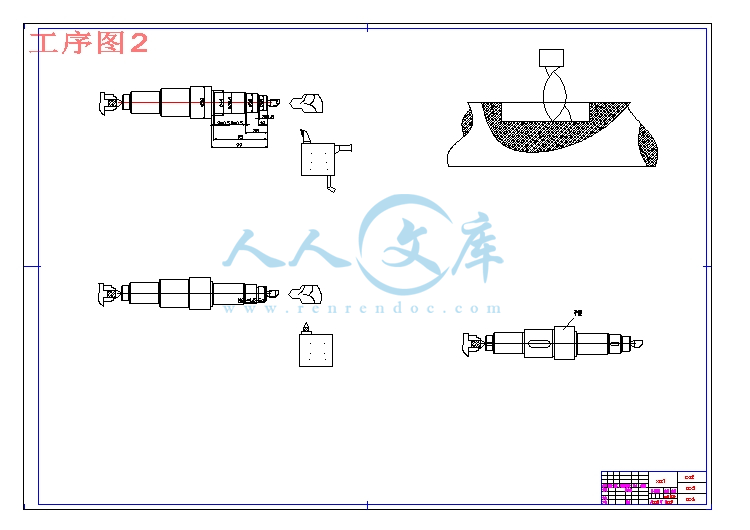



- 内容简介:
-
综合实践报告 姓名: 学号: 读了三年的大学,然而大多数人对本专业的认识还是不够 ,在大二期末学院曾为我们组织了 为期 几个月 的见习,但由于当时所学知识涉及本专业知识不多,所看到的东西与本专业很难联系起来 ,所以对本专业掌握并不是很理想 . 今年 暑假 ,学院为了使我们更多了解机电产品、设备,提高对机电工程制造技术的认识,加深机电在工业各领域应用的感性认识,开阔视野,了解相关设备及技术资料,熟悉典型零件的加工工艺,特意安排了我们到几个拥有较多类型的机电一体化设备,生产技术较先进的工厂进行生产操作实习 . 为期 23 天的生产实习,我们先后去过了杭州通用机床厂 ,杭州机密机床加工工厂 ,上海阀门加工工厂 ,上海大众汽车厂以及杭州发动机厂等大型工厂,了解这些工厂的生产情况,与本专业有关的各种知识,各厂工人的工作情况等等。第一次亲身感受了所学知识与实际的应用,传感器在空调设备的应用了,电子技术在机械制造工业的应用了,精密机械制造在机器制造的应用了,等等理论与实际的相结合,让我们大开眼界 ,也是对以前所学知识的一个初审 .通过这次生产实习,进一步巩固和深化所学的理论知识,弥补以前单一理论教学的不足 ,为后续专业课学习和毕业设 计打好基础 。 杭州通用机床厂 7 月 3 日 ,我们来到实习的第一站 ,隶属杭州机床集团的杭州通用机床厂 。 该厂主要以生产 M-级磨床 7130H,7132H,是目前国内比较大型的机床制造厂之一 .在实习中我们首先听取了一系列关于实习过程中的安全事项和需注意的项目 ,在机械工程类实习中 ,安全问题始终是摆在第一位的 .然后通过该厂总设计师的总体介绍 .粗略了解了该厂的产品类型和工厂概况 .也使我们明白了在该厂的实习目的和实习重点 。 在接下来的一端时间 ,我们分三组陆续在通机车间 ,专机车间和加工车间进行生产实习 。 在通机车间 ,该车间负责人 带我们参观了他们的生产装配流水线 ,并为我们详细讲解了平面磨床个主要零部件的加工装配工艺和整机的动力驱动问题以及内部液压系统的一系列构造 .我最感兴趣的应该是该平面磨床的液压系统 ,共分为供油机构 ,执行机构 ,辅助机构和控制机构 .从不同的角度出发,可以把nts液压系统分成不同的形式 .按油液的循环方式,液压系统可分为开式系统和闭式系统。开式系统是指液压泵从油箱吸油,油经各种控制阀后,驱动液压执行元件,回油再经过换向阀回油箱。这种系统结构较为简单,可以发挥油箱的散热、沉淀杂质作用,但因油液常与空气接触,使空气易于渗入系统,导 致机构运动不平稳等后果。开式系统油箱大,油泵自吸性能好。闭式系统中,液压泵的进油管直接与执行元件的回油管相连,工作液体在系统的管路中进行封闭循环。其结构紧凑,与空气接触机会少,空气不易渗入系统,故传动较平稳 ,但闭式系统较开式系统复杂,因无油箱,油液的散热和过滤条件较差。为补偿系统中的泄漏,通常需要一个小流量的补油泵和油箱 .由于闭式系统在技术要求和成本上比较高 ,考虑到经济性的问题 ,所以该平面磨床采取开始系统 ,外加一个吸震器来平衡系统 . 现代工程机械几乎都采用了液压系统,并且与电子系统、计算机控制技术结合,成为 现代工程机械的重要组成部分 ,怎样设计好液压系统 ,是提高我国机械制造业水平的一项关键技术 .在专机车间 ,对专用磨床的三组导轨 ,两个拖板等特殊结构和送料机构及其加工范围有了进一步的加深学习 ,比向老师傅讨教了动力驱动的原理问题 ,获益非浅 .在加工车间 ,对龙门刨床 ,牛头刨床等有了更多的确切的感性认知 ,听老师傅们把机床的五大部件 :床身 ,立柱 ,磨头 ,拖板 ,工作台细细道来 ,如孢丁解牛般地 ,它们的加工工艺 ,加工特点在不知不觉间嵌们我们的脑袋 。 在通机工厂的实习 ,了解了目前制造业的基本情况 ,只是由于机械行业特有的技术操作熟练性和 其具有的较大风险性 ,很遗憾地 ,不能多做一些具体实践的操作 ,但是观察了一台机床的各个零件的生产加工过程及其装配过程 ,使许多自己从书本上学的知识鲜活了起来 ,明白了本专业在一些技术制造上的具体应用 。 杭州精密机床厂 7月 8日 我 到了同属 杭州机床集团的杭州精密机床厂 ,顾名思义 ,杭州精密机床厂 是生产一些加工精度较高 ,技术要求高的机床设备的大型工厂 ,主要加工的是机床内部的一些精度等级较高的小部件或者一些高精度的机床 ,如 M 级 ,MM 级平面磨床 .由于加工要求较高 ,所以机器也比较精密 ,所以有些也要在恒温这个环境下伺候它们呢 .这样才能保证机床的工作性能 ,进而保证加工零件的加工精度要求 . 在听了工人师傅的讲解后 ,明白了一般零件的加工过程如下 : nts胚料 -划线 -刨床 (工艺上留加工余量 )-粗车 -热处理 ,调质 -车床半精加工 -磨 -齿轮加工 -淬火 (齿面 )-磨面 齿轮零件加工工艺 : 粗车 -热处理 -精车 -磨内孔 -磨芯 ,轴端面 -磨另一端面 -滚齿 -钳齿 -剃齿 -铡键槽 -钳工 -完工 精机公司有三个用于加工磨头体的加工中心和几台数控机床 ,数控机床的体积小 ,价格相对比较便宜 ,加工比较方便 ,加工中心有一个刀 床和多个工作台同时对多个工作面进行加工 ,不仅避免了由于基准不重合产生的误差 ,提高了加工精度 ,而且也大大提高了加工效率 ,但是加工中心体积大 ,价格昂贵 ,而且对环境要求较高 ,这就提高了产品的成本 ,一般选择加工经济性较高的零件或者精度要求高的关键零件 . 在精机公司的实习中 ,极大地丰富了自己关于零件加工工艺的知识 ,拓展了自己的知识面 .在这次实习中 ,感触最深的是了解了数控机床在机械制造业中的重要性 ,它是电子信息技术和传统机械加工技术结合的产物,它集现代精密机械、计算机、通信、液压气动、光电等多学科技术为一体,具有高效 率、高精度、高自动化和高柔性等特点,是尖端工业所不可缺少的生产设备 .目前我国绝大部分数控机床都是出自国外先进制造商 ,无论在数量上 ,精度 ,性能指标上 ,中国制造业都远远落后于发达国家 ,需要我们奋起直追 。 在此次实习中 ,在 杭州发动机厂的时间最长 ,历时 12 天 ,分别介绍了 X6130柴油缸体的加工工艺 (分为面加工和孔加工 ),凸轮轴孔的加工 ,数控设备的加工特点 ,分类及具体运用 ,曲轴的加工工序以及发动机的具体工作原理 .在最后一天 ,我们还参观了其铸造部 ,参观了其铸造生产过程 .在该厂的实习中 ,深刻明白了数控机床的生产中发挥的切 实作用 ,以及目前社会对数控机床及数控人才的急需 ,而在一些重要数控产品 ,如量大面广的数控车床、铣床、高速高精高性能数控机床等的需求上 ,决不能过于依赖进口 。 历时将近一个月的实习结束 ,该次实习 ,真正到达机械制造业的第一前线 ,了解了我国目前制造业的发展状况也粗步了解了机械制造也的发展趋势 .在新的世纪里 ,科学技术必将以更快的速度发展,更快更紧密得融合到各个领域中 ,而这一切都将大大拓宽机械制造业的发展方向 。 nts它的发展 趋势可以归结为 “ 四个化 ” :柔性化、灵捷化、智能化、信息化 .即使工艺装备与工艺路线能适用于生产各种产品 的需要,能适用于迅速更换工艺、更换产品的需要 ,使其与环境协调的柔性 ,使生产推向市场的时间最短且使得企业生产制造灵活多变的灵捷化 ,还有使制造过程物耗 ,人耗大大降低 ,高自动化生产 ,追求人的智能于机器只能高度结合的智能化以及主要使信息借助于物质和能量的力量生产出价值的信息化 。 当然机械制造业的四个发展趋势不是单独的,它们是有机的结合在一起的,是相互依赖,相互促进的。同时由于科学技术的不断进步,也将会使它出现新的发展方向。前面我们看到的是机械制造行业其自身线上的发展。然而,作为社会发展的一个部分,它也将和其它的行业 更广泛的结合。 2世纪机械制造业的重要性表现在它的全球化、网络化、虚拟化、智能化以及环保协调的绿色制造等。它将使人类不仅要摆脱繁重的体力劳动,而且要从繁琐的计算、分析等脑力劳动中解放出来,以便有更多的精力从事高层次的创造性劳动,智能化促进柔性化,它使生产系统具有更完善的判断与适应能力。当然这一切还需要我们大家进一步的努力 。 nts nts nts nts nts ntsnts ntsnts nts nts 附件一 : Characteristics of CNC machine tools CNC machine operation and monitoring of all completed in the numerical control unit, which is the brains of CNC machine tools. Compared with the general machine tools, CNC machine tools has the following characteristics: ( 1) high precision, stable processing quality; ( 2) can be multi-axis linkage, can process complex shape parts; ( 3) processing part changes, generally only need to change the NC program, saving the production time to prepare; ( 4) high precision machine tool itself, rigidity, can choose the amount of benefit processing, production rate (usually as an ordinary machine 3 to 5 times); ( 5) high degree of automation tools, can reduce labor intensity; ( 6) the quality of the operators require a higher technical requirements on higher maintenance staff. CNC machine tools generally consists of the following components: ( 1) host, he is the subject of CNC machine tools, including machine tools, column, spindle, feed mechanism and other mechanical parts. He is used to complete a variety of machining mechanical parts. ( 2) CNC equipment, CNC machine tools is the core, including the hardware (printed circuit boards, CRT monitors, key boxes, paper tape reader, etc.) and the corresponding software for digital input part program, and complete the input information storage, data transformation, interpolation operations and achieve a variety of control functions. ( 3) drive, he was the implementing agencies CNC drive components, including the spindle drive unit, feed unit, spindle motor and feed motor. He was nts 2 under the control of the NC device electrical or electro-hydraulic servo system to achieve through the spindle and feed drive. When several feed linkage, you can complete the position, line, plane curves and space curves processing. ( 4) assist device, the index control machine tools necessary supporting components to ensure the operation of CNC machine tools, such as cooling, chip removal, lubrication, lighting, monitoring. It consists of hydraulic and pneumatic devices, chip equipment, pallet, NC rotary table and CNC dividing head, including tools and monitoring detection devices. ( 5) Programming and other ancillary equipment, can be used to machine the part outside the programming and storage. Since 1952, Massachusetts Institute of Technology developed the world since the first CNC machine tools, CNC machine tools in manufacturing industry, especially in the automotive, aerospace, and military industries has been widely used, digital technology both in hardware and software have rapid development. Classification and application of CNC machine tools ( 1) use classification by technology Metal cutting type machine tools, including CNC lathes, CNC drilling, CNC milling, CNC grinding machines, CNC boring hair and processing center. These machines are suitable for single pieces, small batch and multiple varieties and parts processing, has good processing size consistency, high productivity and automation, and high equipment flexibility. CNC machine metal forming type; such machines, including CNC bending machines, CNC combined punch, CNC bending machine, CNC turret press and so on. CNC machine tools; such machines, including CNC wire (electrode) cutting machine, CNC EDM, CNC flame cutting machines, CNC laser cutting machine, special machine tool and so on. Other types of numerical control equipment; non-processing equipment using digital technology, such as automatic assembly machine, multi-coordinate measuring machines, automatic drawing machines and industrial robots. ( 2) classified according to movement pattern nts 3 Position control; point control of CNC machine tools is characterized by moving parts of the machine can be achieved only from one location to another precise movement and positioning of the process in motion without any processing operations. Such as CNC drilling machines, a few at coordinate boring machine, CNC welding and tube bending machines. Linear control; point linear control characteristic is not only moving parts of the machine coordinates to achieve a precise location to another movement and positioning, but also to achieve a straight line parallel to the axis feed movement or control of the two oblique axes to achieve line feed movement. Contour control; contour control the characteristics of CNC machine tools is the machine moving parts to achieve two axes simultaneously control linkage. It requires not only control the moving parts of machine starting and ending coordinates of the location, but also for control of the process the speed of each point and the displacement, which called for control of the trajectories of the part processed into the plane straight line, curve or surface in space . ( 3) Classification by control Open-loop control; that position feedback devices without control. Semi-closed loop control; refers to the open-loop control with servo motor shaft angular displacement detecting device, by detecting the servo motor to detect indirectly the corner of the displacement of moving parts back to the NC device comparator compares the input command, with the difference value controls the moving parts. Closed-loop control; is in the final of the moving parts of machine corresponding direct linear or rotary position detection device, will be directly measured value of displacement or angular displacement feedback to the CNC device with comparator compares the input command shift, with the difference value control moving parts, so that moving parts in strict accordance with the actual needs of the displacement movement. ( 4) control of machines by the number of performance categories Economical CNC machine tools; Mid-range of CNC machine tools; High-end CNC machine tools; ( 5) CNC equipment used by way of fractional composition of nts 4 Hard-line numerical control system; Soft-line numerical control system; nts 5 附件二 : 数控机床的特点 数控机床的操作和监控全部在这个数控单元中完成,它是数控机床的大脑。与普通机床相比,数控机床有如下特点: ( 1) 加工精度高,具有稳定的加工质量; ( 2) 可进行多坐标的联动,能加工形状复杂的零件; ( 3) 加工零件改变时,一般只需要更改数控程序,可节省生产准备时间; ( 4) 机床本身的精度高、刚性大 ,可选择有利的加工用量,生产率高(一 般为普通机床的 35倍); ( 5) 机床自动化程度高,可以减轻劳动强度; ( 6) 对操作人员的素质要求较高,对维修人员的技术要求更高。 数控机床一般由下列几个部分组成: ( 1) 主机,他是数控机床的主题,包括机床身、立柱、主轴、进给机构等机械部件。他是用于完成各种切削加工的机械部件。 ( 2) 数控装置,是数控机床的核心,包括硬件(印刷电路板、 CRT显示器、键盒、纸带阅读机等)以及相应的软件,用于输入数字化的零件程序,并完成输入信息的存储、数据的变换、插补运算以及实现各种控制功能。 ( 3) 驱动装置,他是数控机床执行机 构的驱动部件,包括主轴驱动单元、进给单元、主轴电机及进给电机等。他在数控装置的控制下通过电气或电液伺服系统实现主轴和进给驱动。当几个进给联动时,可以完成定位、直线、平面曲线和空间曲线的加工。 ( 4) 辅助装置,指数控机床的一些必要的配套部件,用以保证数控机床的运行,如冷却、排屑、润滑、照明、监测等。它包括液压和气动装置、排屑装置、交换工作台、数控转台和数控分度头,还包括刀具及监控检测装置等。 ( 5) 编程及其他附属设备,可用来在机外进行零件的程序编制、存储等。 nts 6 自从 1952 年美国麻省理工学院研制出世界上第一台 数控机床以来,数控机床在制造工业,特别是在汽车、航空航天、以及军事工业中被广泛地应用,数控技术无论在硬件和软件方面,都有飞速发展。 数控机床的分类和应用 ( 1) 按工艺用途分类 金属切削类数控机床 ,包括数控车床 ,数控钻床 ,数控铣床 ,数控磨床 ,数控镗床发及加工中心 .这些机床都有适用于单件、小批量和多品种和零件加工,具有很好的加工尺寸的一致性、很高的生产率和自动化程度,以及很高的设备柔性。 金属成型类数控机床;这类机床包括数控折弯机,数控组合冲床、数控弯管机、数控回转头压力机等。 数控特种加工机床;这类机床包 括数控线(电极)切割机床、数控电火花加工机床、数控火焰切割机、数控激光切割机床、专用组合机床等。 其他类型的数控设备;非加工设备采用数控技术,如自动装配机、多坐标测量机、自动绘图机和工业机器人等。 ( 2) 按运动方式分类 点位控制;点位控制数控机床的特点是机床的运动部件只能够实现从一个位置到另一个位置的精确运动,在运动和定位过程中不进行任何加工工序。如数控钻床、数按坐标镗床、数控焊机和数控弯管机等。 直线控制;点位直线控制的特点是机床的运动部件不仅要实现一个坐标位置到另一个位置的精确移动和定位,而且能实现平行 于坐标轴的直线进给运动或控制两个坐标轴实现斜线进给运动。 轮廓控制;轮廓控制数控机床的特点是机床的运动部件能够实现两个坐标轴同时进行联动控制。它不仅要求控制机床运动部件的起点与终点坐标位置,而且要求控制整个加工过程每一点的速度和位移量,即要求控制运动轨迹,将零件加工成在平面内的直线、曲线或在空间的曲面。 ( 3) 按控制方式分类 开环控制;即不带位置反馈装置的控制方式。 nts 7 半闭环控制;指在开环控制伺服电动机轴上装有角位移检测装置,通过检测伺服电动机的转角间接地检测出运动部件的位移反馈给数控装置的比较器,与输入的指 令进行比较,用差值控制运动部件。 闭环控制 : 是在机床的最终的运动部件的相应位置直接直线或回转式检测装置,将直接测量到的位移或角位移值反馈到数控装置的比较器中与输入指令移量进行比较,用差值控制运动部件,使运动部件严格按实际需要的位移量运动。 ( 4) 按数控制机床的性能分类 经济型数控机床; 中档数控机床; 高档数控机床; ( 5) 按所用数控装置的构成方式分类 硬线数控系统; 软线数控系统;nts 1 nts 毕业设计 (论文 )外文资料翻译 系 别: 机电信息系 专 业: 机械设计制造及其自动化 班 级: 姓 名: 学 号: 外文出处 : Int J Adv Manuf Technol 附 件: 1. 原文 ; 2. 译文 2013 年 01 月 ntsInt J Adv Manuf Technol (2001) 17:649653 2001 Springer-Verlag London Limited Real-Time Prediction of Workpiece Errors for a CNC Turning Centre, Part 1. Measurement and Identification X. Li Department of Manufacturing Engineering, City University of Hong Kong, Hong Kong This paper analyses the error sources of the workpiece in bar turning, which mainly derive from the geometric error of machine tools, i.e. the thermally induced error, the error arising from machineworkpiecetool system deflection induced by the cutting forces. A simple and low-cost compact measuring system combining a fine touch sensor and Q-setter of machine tools (FTSFQ) is developed, and applied to measure the work- piece dimensions. An identification method for workpiece errors is also presented. The workpiece errors which are composed of the geometric error, thermal error, and cutting force error can be identified according to the measurement results of each step. The model of the geometric error of a two-axis CNC turning centre is established rapidly based on the measurement results by using an FTSFQ setter and coordinate measuring machine (CMM). Experimental results show that the geometric error can be compensated by modified NC commands in bar turning. Keywords: Dimension measure; Error identification; Geo- metric error; Turning 1. Introduction In recent years, ultraprecision machining has made remarkable progress. Some special lathes have been able to make ultra- precision machining, to less than a submicron and nanomicron tolerances a possibility. A common second approach is that the grinding is used to achieve a high level of dimensional accuracy after turning. However, the condition of the cutting tool (diamond) and workpiece (aluminium) have restricted the application of ultraprecision lathes. The second approach increases the number of machine tools and machining processes used 1, which results in an increase in the manufacturing cost. At present, most CNC lathes are equipped with a positioning resolution of 1 urm. Various machining errors in finish turning, however, degrade the accuracy to a level of approximately10 urm, so that when turning carbon steel, a machining error predictably arises in excess of 2030 urm. For improving mach- ining accuracy, the method of careful design and manufacture has been extensively used in some CNC lathes. However, the manufacturing cost based on the above method will rapidly increase when the accuracy requirements of the machine tool system are increased beyond a certain level. For further improv- ing machine accuracy cost-effectively, real-time error prediction and compensation based on sensing, modelling and control techniques have been widely studied 2, so ultraprecision and finish tuning can be performed on one CNC lathe. The positioning resolution of the cutting tools and workpiece ntsis reduced so that it cannot maintain high accuracy during machining because of the cutting-force-induced deflection of the machineworkpiecetool system, and the thermally induced error, etc. In general, a positioning device using a piezo-eletric actuator is used to improve the working accuracy, but the method introduces some problems, such as, the feedback strat- egy, and the accuracy of sensors, which add to the manufactur- ing cost of the products. However, if the workpiece error can be measured by using a measuring instrument, or predicted by using a modelling, the turning program produced by modified NC commands can be executed satisfactorily on a CNC machine tool. Thus, a CNC turning centre can compensate for the normal machining error, i.e. the machine tool can machine a product with a high level of accuracy using modified NC commands, in real time. The workpiece error derives from the error in the relative movement between the cutting tool and the ideal workpiece. For a two-axis turning centre, this relative error varies as the condition of the cutting progresses, e.g. the thermal deflection of the machine tool is time variant, which results in different thermal errors. According to the various characters of the error sources of the workpiece, the workpiece errors can be classified as geometric error, thermally induced error, and cutting-force- induced error. The main affecting factors include the position errors of the components of the machine tool and the angular errors of the machine structure, i.e. the geometric error. The thermally induced errors of the machine tool (i.e. the thermal error), and the deflection of the machining system (including the machine tools, workpiece, and cutting tools) arising from cutting forces, are called the cutting-force error. This paper analyses the workpiece error sources in turning. The errors of a machined workpiece are mainly composed of the geometric error of the machine tools, the thermally induced error, and the error arising from machineworkpiecetool sys- tem deflection induced by the cutting forces. A simple and low-cost measuring instrument for the workpiece dimensions, which combines a fine touch sensor and machine tool Q-setter (FTSFQ), is described, and applied to measure the workpiece error. A new method for identifying the geometric error, the thermal error, and the cutting-force error is also presented for a two-axis turning centre. Finally, the modelling of the geo- metric error of a CNC turning centre is presented, based on the measurement results using the FTSFQ and CMM. The geometric error can be compensated by the modified NC command method. 2. Error Sources in Turning The machine tool system is composed of the drive servo, the machine tool structure, the workpiece and the cutting process. The major error sources derive from the machine tool (thermal errors, geometric errors, and forced vibrations), the control (drive servo dynamics and programming errors) and the cutting process (machine tool and cutting tool deflection, workpiece deflection, tool wear, and chatter) 3. Errors derived from the machine tool include thermal errors (machine thermal error and workpiece thermal errors), geo- metric errors, and forced vibrations, which dominate machining accuracy. The thermal errors and geometric errors are the dominant factors with respect to machining accuracy in fine cutting. However, machine tool errors can be decoupled from the other error sources and compensated 4. The error derived from forced vibration can be reduced through balanced dynamic components and vibration isolation 3. The errors derived from the controller/drive dynamics are related to the cutting force disturbances and the inertia of the drive and the machine table. These errors can be reduced by an interpolator with a deceleration function 5 or by an advanced feed drive controller 6, these errors, reduced by using the above methods, are small when compared with other error sources. Owing to the demand for high productivity, high feedrates and large depths of cut are required, which result in large cutting forces. Therefore, the cutting-force induced ntsdeflections of the machine tool (spindle), tool holder, workpiece, and cutting tool make significant contributions to machining accu- racy during the cutting process. In addition, tool wear and machine tool chatter are also important error sources in the cutting process. However, these effects are neglected here so as to focus on the main error sources. In short, the error of a machined workpiece, i.e. the total machining error (iTot), is composed mainly of the geometric errors of the machine tool(s) (iG), the thermally induced error (iT), and the error (iF) arising from the deflection of the machineworkpiecetool system induced by the cutting forces. Hence, iTot iG + iT + iF (1) In the next section, we present a novel compact measuring instrument and a new analytical approach for measuring and identifying workpiece errors in turning. 3. A Compact Measurement System Contact sensors, such as touch trigger probes, have been used to measure workpiece dimensions in machining. In machining practice, the measuring instrument is attached to one of the machines axes to measure a surface on the workpiece. A TP7M or MP3 associated with the PH10M range of motorised probe heads or a PH6M fixed head have been used widely in the automated CNC inspection environment owing to their high level of reliability and accuracy and integral autojoint. Though the probeheads are of adequate accuracy (unidirectional repeatability at stylus tip (high sensitivity): 0.25 urm; pre-travel variation 360 (high sensitivity): 0.25 urm), and versatile in application, they have clear drawbacks, including complexity of construction, high price ($4988), and the need for careful maintenance. To overcome these drawbacks of touch trigger probes, Ostafiev et al. 7 presented a novel technique of contact probing for designing a fine touch sensor. The cutting tool itself is used as a contact probe. The sensor is capable of yielding measurement accuracy comparable to that of the best touch trigger probe in use. Moreover, the principle of operation and construction of the sensor is extremely simple, the cost of the sensor is low, and the maintenance is very easy. In this paper, this sensor will be used to measure the diameter of a workpiece associated with the Q-setter. A touch sensor is mounted on a CNC turning centre. When we manually bring the tool nose into contact with it, an interrupt signal is generated for the NC unit to stop an axis. Moreover, it can write in an offset and a workpiece coordinate shift automatically. This function facilitates set-up when replac- ing a tool, and this convenient function is called the “Quick Tool Setter” or “Q-setter”. Based on the above principle, we can operate a switch, which is controlled by fine touch sensor, between the Q-setter and NC unit. When the tool tip touches the workpiece surface, the fine touch sensor can send a control signal to the switch, to turn it to the “off” state. See Fig. 1, the fine touch sensor replaces the Q-setter function, to stop an axis and write in an offset and a workpiece coordinate shift automatically. Therefore, the fine touch sensor associated with Fig. 1. Flow diagram of a fine touch sensor fixed on a CNC controller nts a Q-setter (FTSFQ) can be used to inspect the diameter of the workpiece, the method is shown in Fig. 2. When the cutting tool tip touches the workpiece surface, a “beep” sound is heard and the switching “OFF” signal appears and the axis stops automatically, as far the Q-setter. A new “tool offset” XT-W is obtained by the NC unit (display of CNC). Before touching the workpiece surface, the cutting tool tip touches the Q-setter, and the “tool offset” XT-Q is obtained. Thus, the on-machine workpiece diameter Don-machine is given by the following Eq.: Don-machine 2 H + XT-Q XT-W (2) where XT-Q is the tool offset when the cutting tool contacts the Q-setter XT-W is the “tool offset” when the cutting tool contacts the workpiece surface H is the distance from the centre of the Q-setter to the centre of the spindle in the x-axis direction and is provided by the machine tool manufacturer, for the Seiki-Seicos L II Turning centre, it is 85.356 mm. Ostafiev and Venuvinod 8 tested the measurement accuracy of the fine touch sensor, performing on-machine inspection of turned parts, and found that the method was capable of achiev- ing a measurement accuracy of the order of 0.01 urm under shop floor conditions. However, the measurement accuracy of the fine touch sensor together with the Q-setter obtained an accuracy of about urm because the results of the measurement system are displayed by the CNC system, and the readings accuracy of the CNC system is up to 1 urm. 4. Identification of Workpiece Errors From the above analysis of error sources of the workpiece, the total error iTot of machined parts is mainly composed of the following errors in a turning operation: . iG the geometric errors of machine tools. . iT the thermally induced error. Fig. 2. Inspection for the diameter of a workpiece by using the fine touch sensor with the Q-setter of a machine tool. . iF the cutting force induced error. To analyse the error sources of a machined workpiece, Liu & Venuvinod 9 used Fig. 3 to illustrate the relationship amongst dimensions associated with different error components in turning. In Fig. 3, Ddes is the desired dimension of the workpiece; Domw is the dimension obtained by ntson-machine measurement using FTSFQ immediately after the machining operation; Domc is the dimension obtained by on-machine measurement using FTSFQ after the machine has cooled down; and Dpp is the dimension obtained by post-process process measurement using a CMM after the workpiece has been removed from the machine. When the workpiece has been machined, and removed from the machine tool system, it is then sent for inspection of the dimensions using a CMM. This procedure is called post-process inspection, by which we obtain it Dpp value. As the positioning error of the CMM is very much smaller than the desired measurement accuracy, the total error is iTot (Dpp Ddes)/2 (3) The dimension Domw is obtained through on-machine measurement using FTSFQ immediately after machining, i.e. the machine is still in the same thermal state as at the time of machining. The measurement is made with the same positioning error as that which existed during machining. Hence, the positioning error in this state would be equal to (iG + iT), i.e. (Dpp Domw)/2 iG + iT (4) When the machine has completely cooled down, i.e. without thermal error, the dimension Domc can be obtained by on- machine measurement using FTSFQ. The measurement has a positioning error equal to the geometric error of the machine at the location of measurement. Hence, the positioning error in this state would be equal to (iG), i.e. (Dpp Domc)/2 iG (5) Combining Eqs (4) and (5), the thermally induced error iT is (Domc Domw)/2 iT (6) Hence, taking Eqs (1), (3), and (4) into account, the cutting- force-induced error owning to the deflection of the machine workpiecetool system iF is (Domw Ddes)/2 iF (7) Fig. 3. The relationships among dimensions. So far, the machining error is composed of the geometric error, the thermal error, and the cutting-force-induced error and can be identified using the above procedure. The thermal error and the force-induced error modellings is addressed in Li 10. Here, the geometric error of machine tool is measured and modelled. 5. Modelling of Geometric Error The geometric error of a workpiece is mainly affected by the offset of the spindle, and the linear error and the angular errors of the cross-slide for a two-axis CNC turning centre. Here, only the geometric error of workpiece in the x-axis direction is taken into account for a bar workpiece. This is expressed by the following ntsformula. iG i(s) (x) hT-Q ix(x) (8) where i(s) is the spindle offset along the x-axis direction (x) is the angular error (yaw) of the cross-slide in the x, y-plane ix(x) is the linear displacement error of the cross- slide along the x-axis direction The spindle offset is a constant value independent of the the machining position. The angular error term and the linear error term are functions of the cross-slide position x. In this paper, the FTSFQ is mounted on a Hitachi Seiiki, HITEC-TURN 20SII two-axis turning centre. The FTSFQ cali- bration instrument was developed to measure rapidly the dimen- sion of the workpiece in the x-axis direction on the two-axis CNC turning centre when the machine has completely cooled down, i.e. without the effect of thermal error. The geometric error can be computed by using Eq. (5) according to the measured results. First, the diameter of a precision ground test bar is measured at 10 positions, 20 mm apart, by a CMM, their values Dppi (i 1, 2, . . ., 10) are recorded. Then, the test bar is mounted on the spindle, and its diameter is also measured at 10 positions, 20 mm apart, by the FTSFQ. The measurement arrangement is shown in Fig. 4, the readings are Domcl (i 1, 2, . . ., 10). Thus, the geometric error at each point along the x-axis for the bar workpiece are computed as follows: iGi (Dppi DGi)/2 (9) From starting point B to point A, the results are shown in Fig. 5 for diameters of 30, 45, 60, and 75 mm. The workpiece Fig. 4. Diagram of the geometric error measurement of the workpiece using FTSFQ. Fig. 5. Geometric errors of the workpiece along the z-axis. geometr
- 温馨提示:
1: 本站所有资源如无特殊说明,都需要本地电脑安装OFFICE2007和PDF阅读器。图纸软件为CAD,CAXA,PROE,UG,SolidWorks等.压缩文件请下载最新的WinRAR软件解压。
2: 本站的文档不包含任何第三方提供的附件图纸等,如果需要附件,请联系上传者。文件的所有权益归上传用户所有。
3.本站RAR压缩包中若带图纸,网页内容里面会有图纸预览,若没有图纸预览就没有图纸。
4. 未经权益所有人同意不得将文件中的内容挪作商业或盈利用途。
5. 人人文库网仅提供信息存储空间,仅对用户上传内容的表现方式做保护处理,对用户上传分享的文档内容本身不做任何修改或编辑,并不能对任何下载内容负责。
6. 下载文件中如有侵权或不适当内容,请与我们联系,我们立即纠正。
7. 本站不保证下载资源的准确性、安全性和完整性, 同时也不承担用户因使用这些下载资源对自己和他人造成任何形式的伤害或损失。

人人文库网所有资源均是用户自行上传分享,仅供网友学习交流,未经上传用户书面授权,请勿作他用。