连杆零件加工工艺及铣斜槽夹具设计【全套CAD图纸+毕业论文】【原创资料】
收藏
资源目录
压缩包内文档预览:
编号:465139
类型:共享资源
大小:1.25MB
格式:RAR
上传时间:2015-08-03
上传人:好资料QQ****51605
认证信息
个人认证
孙**(实名认证)
江苏
IP属地:江苏
45
积分
- 关 键 词:
-
连杆
零件
加工
工艺
斜槽
夹具
设计
全套
cad
图纸
毕业论文
原创
资料
- 资源描述:
-
摘 要
连杆零件加工工艺及铣床夹具设计是包括零件加工的工艺设计、工序设计以及专用夹具的设计三部分。在工艺设计中要首先对零件进行分析,了解零件的工艺再设计出毛坯的结构,并选择好零件的加工基准,设计出零件的工艺路线;接着对零件各个工步的工序进行尺寸计算,关键是决定出各个工序的工艺装备及切削用量;然后进行专用夹具的设计,选择设计出夹具的各个组成部件,如定位元件、夹紧元件、引导元件、夹具体与机床的连接部件以及其它部件;计算出夹具定位时产生的定位误差,分析夹具结构的合理性与不足之处,并在以后设计中注意改进。
关键词:工艺,工序,切削用量,夹紧,定位,误差
目 录
摘 要1
第1章 绪论3
第2章 加工工艺规程设计4
2.1 零件的分析4
2.1.1 零件的作用4
2.1.2 零件的工艺分析4
2.2 连杆加工的主要问题和工艺过程设计所应采取的相应措施5
2.2.1 孔和平面的加工顺序5
2.2.2 孔系加工方案选择5
2.3 连杆加工定位基准的选择6
2.3.1 粗基准的选择6
2.3.2 精基准的选择6
2.4 连杆加工主要工序安排6
2.5 机械加工余量、工序尺寸及毛坯尺寸的确定8
2.6确定切削用量及基本工时(机动时间)9
第3章 铣斜槽夹具设计20
3.1设计要求20
3.2夹具设计20
3.2.1 定位基准的选择20
3.2.2 切削力及夹紧力的计算20
3.3定位误差的分析23
3.4夹具设计及操作的简要说明23
总 结25
参考文献26
致 谢27
第1章 绪论
机械制造业是制造具有一定形状位置和尺寸的零件和产品,并把它们装备成机械装备的行业。机械制造业的产品既可以直接供人们使用,也可以为其它行业的生产提供装备,社会上有着各种各样的机械或机械制造业的产品。我们的生活离不开制造业,因此制造业是国民经济发展的重要行业,是一个国家或地区发展的重要基础及有力支柱。从某中意义上讲,机械制造水平的高低是衡量一个国家国民经济综合实力和科学技术水平的重要指标。
连杆零件加工工艺及钻床夹具设计是在学完了机械制图、机械制造技术基础、机械设计、机械工程材料等的基础下,进行的一个全面的考核。正确地解决一个零件在加工中的定位,夹紧以及工艺路线安排,工艺尺寸确定等问题,并设计出专用夹具,保证尺寸证零件的加工质量。本次设计也要培养自己的自学与创新能力。因此本次设计综合性和实践性强、涉及知识面广。所以在设计中既要注意基本概念、基本理论,又要注意生产实践的需要,只有将各种理论与生产实践相结合,才能很好的完成本次设计。
本次设计水平有限,其中难免有缺点错误,敬请老师们批评指正。
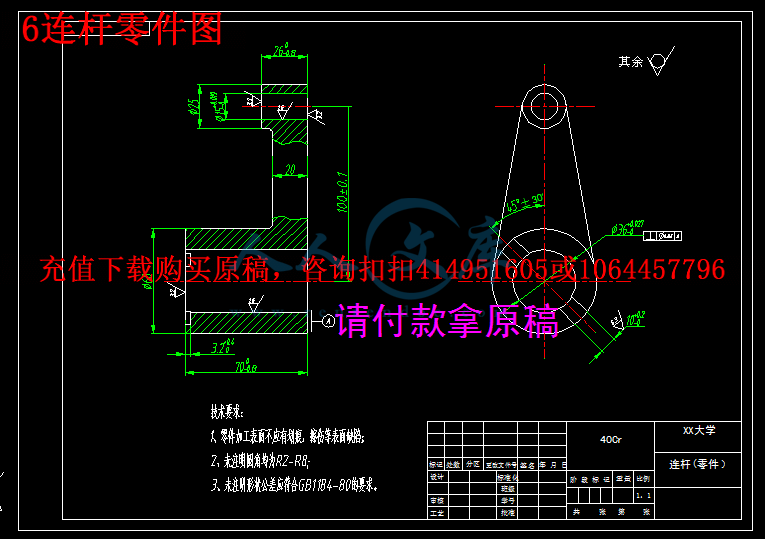
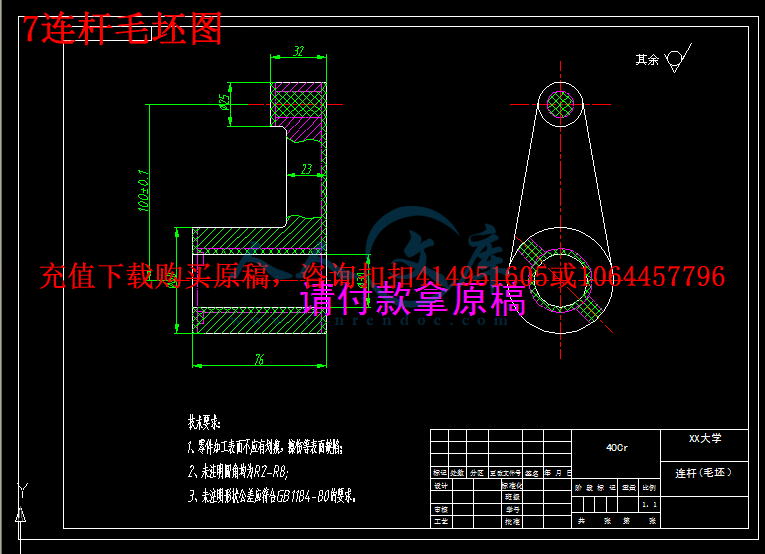
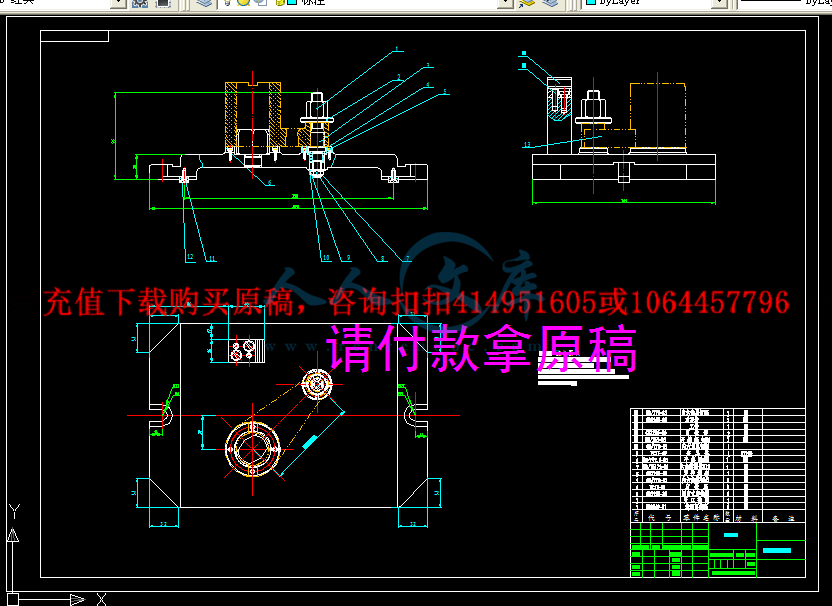
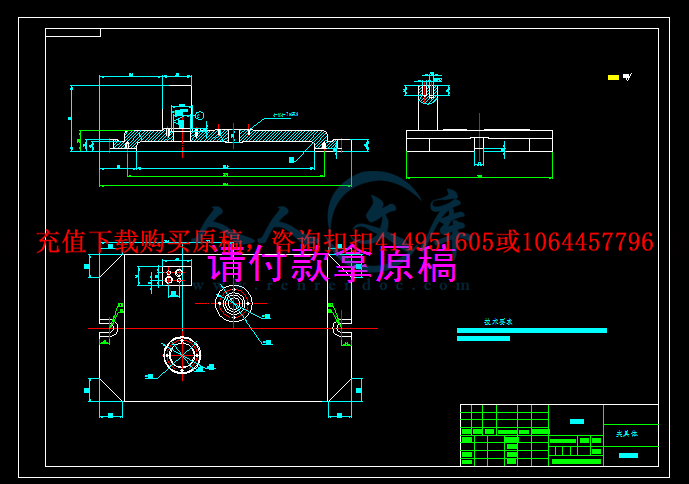
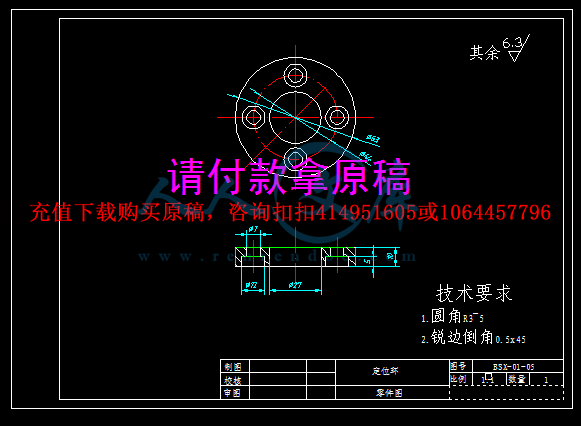
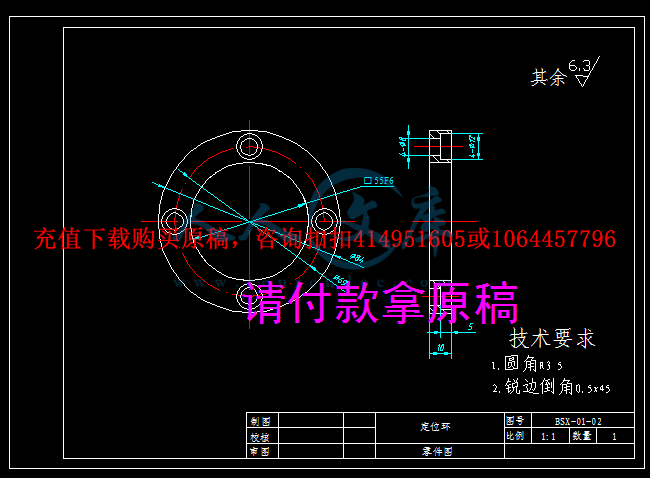
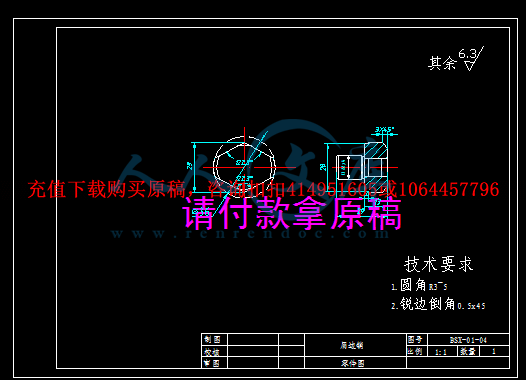
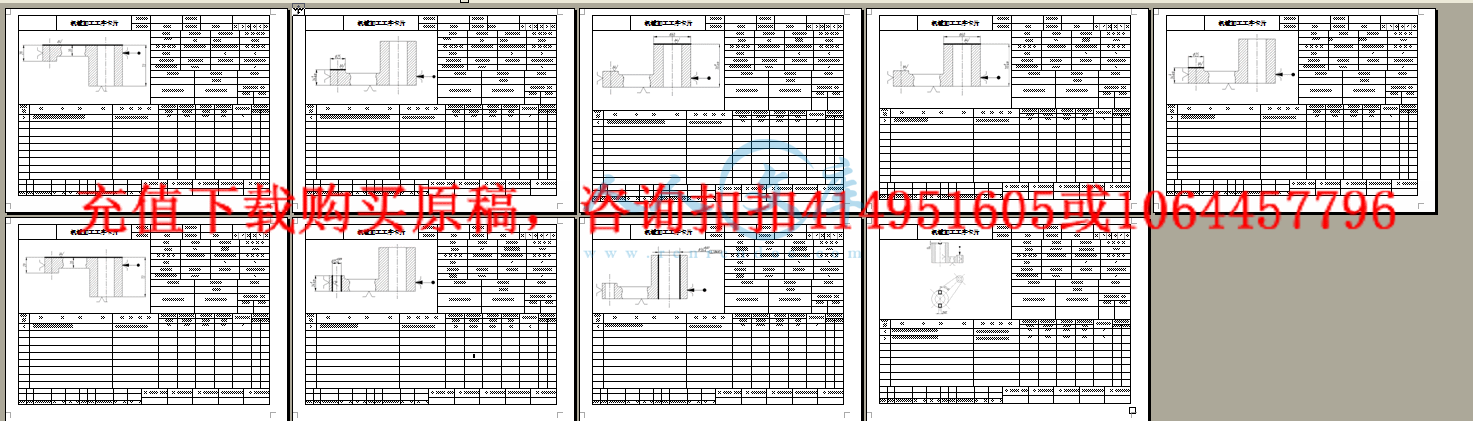
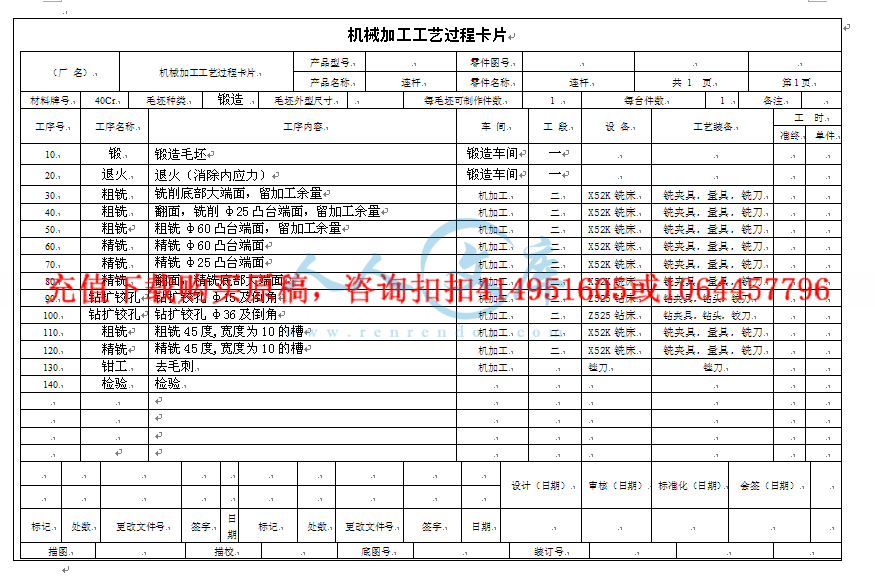
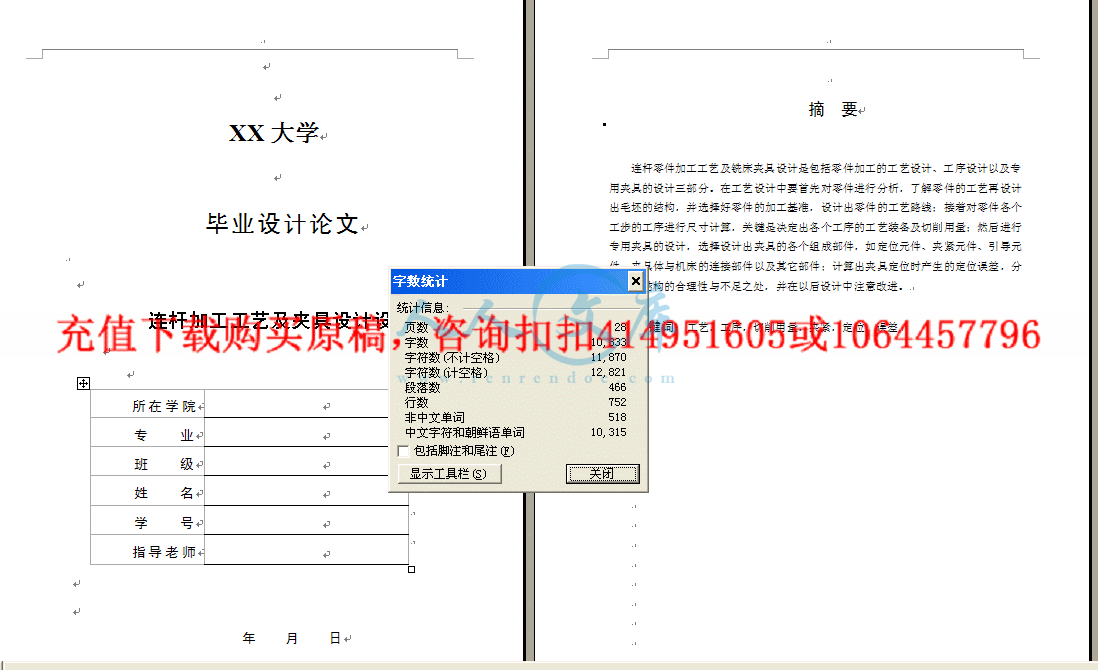
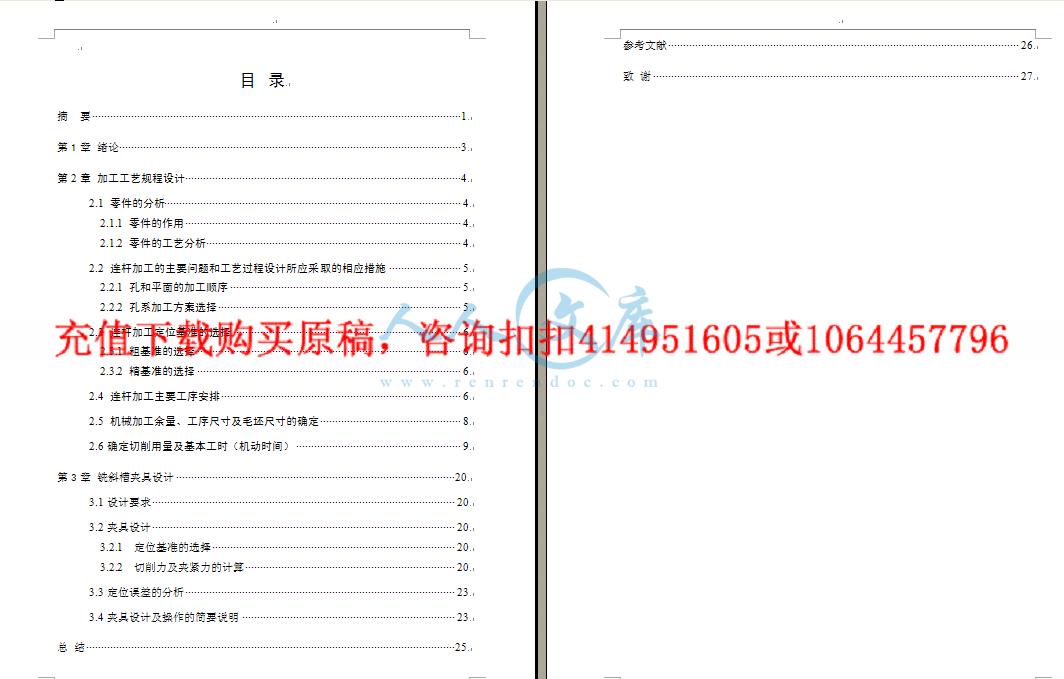

- 内容简介:
-
机械加工工艺过程卡片 (厂 名) 机械加工工艺过程卡片 产品型号 零件图号 产品名称 连杆 零件名称 连杆 共 1 页 第 1 页 材料牌号 40Cr 毛坯种类 锻造 毛坯外型尺寸 每毛坯可制作件数 1 每台件数 1 备注 工序号 工序名称 工序内容 车 间 工 段 设 备 工艺装备 工 时 准终 单件 10 锻 锻造毛坯 锻造 车间 一 20 退火 退火(消除内应力) 锻造 车间 一 30 粗 铣 铣削 底部 大 端面,留加工余量 机加工 二 X52K 铣床 铣夹具,量具,铣刀 40 粗 铣 翻面, 铣削 25 凸台 端面,留加工余量 机加工 二 X52K 铣床 铣夹具,量具,铣刀 50 粗 铣 粗 铣 60 凸台端面 ,留加工余量 机加工 二 X52K 铣床 铣夹具,量具,铣刀 60 精 铣 精铣 60 凸台端面 机加工 二 X52K 铣床 铣夹具,量具,铣刀 70 精铣 精铣 25 凸台端面 机加工 二 X52K 铣床 铣夹具,量具,铣刀 80 精铣 翻面, 精铣底部大端面 机加工 二 X52K 铣床 铣夹具,量具,铣刀 90 钻 扩铰孔 钻 扩铰孔 15 及倒角 机加工 二 Z525 钻床 钻夹具,钻头,铰刀 100 钻 扩铰孔 钻 扩铰孔 36 及倒角 机加工 二 Z525 钻床 钻夹具,钻头,铰刀 110 粗 铣 粗 铣 45 度 ,宽度为 10 的槽 机加工 二 X52K 铣床 铣夹具,量具,铣刀 120 精铣 精铣 45 度 ,宽度为 10 的槽 机加工 二 X52K 铣床 铣夹具,量具,铣刀 130 钳工 去毛刺 机加工 锉刀 锉刀 140 检验 检验 设计(日期) 审核(日期) 标准化(日期) 会签(日期) 标记 处数 更改文件号 签字 日期 标记 处数 更改文件号 签字 日期 描图 描校 底图号 装订号 nts 0 XX 大学 毕业 设计论文 连杆 加工工艺及夹具设计设计 所在学院 专 业 班 级 姓 名 学 号 指导老师 年 月 日 nts 摘 要 连杆 零件加工工艺及 铣 床夹具设计 是包括零件加工的工艺设计、工序设计以及专用夹具的设计三部分。在工艺设计中要首先对零件进行分析,了解零件的工艺再设计出毛坯的结构,并选择好零件的加工基准,设计出零件的工艺路线;接着对零件各个工步的工序进行尺寸计算,关键是决定出各个工序的工艺装备及切削用量;然后 进行专用夹具的设计,选择设计出夹具的各个组成部件,如定位元件、夹紧元件、引导元件、夹具体与机床的连接部件以及其它部件;计算出夹具定位时产生的定位误差,分析夹具结构的合理性与不足之处,并在以后设计中注意改进。 关键词: 工艺 , 工序 , 切削用量 , 夹紧 , 定位 , 误差 nts 目 录 摘 要 1 第 1章 绪论 4 第 2 章 加工工艺 规程设计 5 2.1 零件的分析 5 2.1.1 零件的作用 5 2.1.2 零件的工艺分析 5 2.2 连杆加工的主要问题和工艺过程设计所应采取的相应措施 6 2.2.1 孔和平面的加工顺序 6 2.2.2 孔系加工方案选择 6 2.3 连杆加工定位基准的选择 7 2.3.1 粗基准的选择 7 2.3.2 精基准的选择 7 2.4 连杆加工主要工序安排 7 2.5 机械加工余量、工序尺寸及毛坯尺寸的确定 9 2.6 确定切削用量及基本工时(机动时间) 10 第 3章 铣斜槽夹具设计 20 3.1 设计要求 20 3.2 夹具设计 20 3.2.1 定位基准的选择 20 3.2.2 切削力及夹紧力的计算 20 3.3 定位误差的分析 23 3.4 夹具设计及操作的简要说明 23 总 结 25 参考文献 26 nts 致 谢 27 nts 第 1 章 绪论 机械制造业是制造具有一定形状位置和尺寸的零件和产品,并把它们装备成机械装备的行业。机械制造业的产品既可以直接供人们使用,也可以为其它行业的生产提供装备,社会上有着各种各样的机械或机械制造业的产品。我们的生活离不开制造业,因此制造业是国民经济发展的重要行业,是一个国家或地区发展的重要基础及有力支柱。从某中意义上讲,机械制造水平的高低是衡量一个国家国民经济综合实力和科学技术水平的重要指标。 连杆 零件加工工艺及 钻床夹具设计 是在学完了机械制图、 机械制造技术基础、机械设计、机械工程材料等 的基础下,进行的一个全面的考核 。正确地解决一个零件在加工中的定位,夹紧以及工艺路线安排,工艺尺寸确定等问题,并设计出专用夹具, 保证尺寸 证零件的加工质量。 本次设计也要培养自己的自学与创新能力。因此本次设计综合性和实践性强、涉及知识面广。所以在设计中既要注意基本概念、基本理论,又要注意生产实践的需要,只有将各种理论与生产实践相结合,才能很好的完成本次设计。 本次设计水平有限,其中难免有缺点错误,敬请老师们批评指正。 nts 第 2 章 加工工艺规程设计 2.1 零件的分析 2.1.1 零件的作用 题目给出的零件是 连杆 。 连杆 的主要作用 是保证各轴之间的中心距及平行度,并保证部件 正确安装。因此 连杆 零件的加工质量,不但直接影响的装配精度和运动精 度,而且还会影响 工作精度、使用性能和寿命。 2.1.2 零件的工艺分析 由 连杆 零件图可知。 连杆 是一个 连杆 零件,它的外表面上有 4个平面需要进行加工。支承孔系在前后端面上。此外各表面上还需加工一系列螺纹孔。因此可将其分为三组加工表面。它们相互间有一定的位置要求。现分析如下: ( 1) 以 底 面为主要加工表面的加工面。这一组加工表面包括: 底 面 的 底 削加工;其中 底 面 有表面粗糙度要求为 mRa 2.3 , ( 2) 以 15 的孔为主要加工表面的加工面。这一组加工表面包括: 2 个前后端面;15 的孔。 nts ( 2)以 36 的孔为主要加工表面的加工面。这一组加工表面包括: 2 个前后端面;36 的孔。 ( 4) 以 45 度 槽 面为主要加工平面的加工面,包括 45 度槽面 2.2 连杆 加工的主要问题和工艺过程设计所应采取的相应措施 由以上分析可知。该 连杆 零件的主要加工表面是平面及孔系。一般来说,保证平面的加工精度要比保证孔系的加工精度容易。因此,对于 连杆 来说,加工过程中的主要问题是保证孔的尺寸精度及位置精 度,处理好孔和平面之间的相互关系。 由于的生产量很大。怎样满足生产率要求也是加工过程中的主要考虑因素。 2.2.1 孔和平面的加工顺序 连杆 类零件的加工应遵循先面后孔的原则:即先加工 连杆 上的基准平面,以基准平面定位加工其他平面。然后再加工孔系。 连杆 的加工自然应遵循这个原则。这是因为平面的面积大,用平面定位可以确保定位可靠夹紧牢固,因而容易保证孔的加工精度。其次,先加工平面可以先切去铸件表面的凹凸不平。为提高孔的加工精度创造条件,便于对刀及调整,也有利于保护刀具。 连杆 零件的加工工艺应遵循粗精加工分开的原则, 将孔与平面的加工明确划分成粗加工和精加工阶段以保证孔系加工精度。 2.2.2 孔系加工方案选择 连杆 孔系加工方案,应选择能够满足孔系加工精度要求的加工方法及设备。除了从加工精度和加工效率两方面考虑以外,也要适当考虑经济因素。在满足精度要求及生产率的条件下,应选择价格最底的机床。 根据 连杆 零件图所示的 连杆 的精度要求和生产率要求,当前应选用在组合机床上用镗模法镗孔较为适宜。 ( 1) 用镗模法镗孔 在大批量生产中, 连杆 孔系加工一般都在组合镗床上采用镗模法进行加工。镗模夹具是按照工件孔系的加工要求设计制造的。当镗刀杆 通过镗套的引导进行镗孔时,镗模的精度就直接保证了关键孔系的精度。 采用镗模可以大大地提高工艺系统的刚度和抗振性。因此,可以用几把刀同时加工。所以生产效率很高。但镗模结构复杂、制造难度大、成本较高,且由于镗模的制造和装配误差、镗模在机床上的安装误差、镗杆和镗套的磨损等原因。用镗模加工孔系所能获得的加工精度也受到一定限制。 ( 2) 用坐标法镗孔 在现代生产中,不仅要求产品的生产率高,而且要求能够实现大批量、多品种以及nts 产品更新换代所需要的时间短等要求。镗模法由于镗模生产成本高,生产周期长,不大能适应这种要求,而坐标 法镗孔却能适应这种要求。此外,在采用镗模法镗孔时,镗模板的加工也需要采用坐标法镗孔。 用坐标法镗孔,需要将 连杆 孔系尺寸及公差换算成直角坐标系中的尺寸及公差,然后选用能够在直角坐标系中作精密运动的机床进行镗孔。 2.3 连杆 加工定位基准的选择 2.3.1 粗基准的选择 粗基准选择应当满足以下要求: ( 1) 保证各重要支承孔的加工余量均匀; ( 2) 保证装入 连杆 的零件与箱壁有一定的间隙。 为了满足上述要求,应选择的主要支承孔作为主要基准。即以 连杆 的输入轴和输出轴的支承孔作为粗基准。也就是以前后端面上距顶平面最近的孔 作为主要基准以限制工件的四个自由度,再以另一个主要支承孔定位限制第五个自由度。由于是以孔作为粗基准加工精基准面。因此,以后再用精基准定位加工主要支承孔时,孔加工余量一定是均匀的。由于孔的位置与箱壁的位置是同一型芯铸出的。因此,孔的余量均匀也就间接保证了孔与箱壁的相对位置。 2.3.2 精基准的选择 从保证 连杆 孔与孔、孔与平面、平面与平面之间的位置 。精基准的选择应能保证连杆 在整个加工过程中基本上都能用统一的基准定位。从 连杆 零件图分析可知,它的顶平面与各主要支承孔平行而且占有的面积较大,适于作精基准使用。但用 一个平面定位仅仅能限制工件的三个自由度,如果使用典型的一面两孔定位方法,则可以满足整个加工过程中基本上都采用统一的基准定位的要求。至于前后端面,虽然它是 连杆 的装配基准,但因为它与 连杆 的主要支承孔系垂直。如果用来作精基准加工孔系,在定位、夹紧以及夹具结构设计方面都有一定的困难,所以不予采用。 2.4 连杆 加工主要工序安排 对于大批量生产的零件,一般总是首先加工出统一的基准。 连杆 加工的第一个工序也就是加工统一的基准。具体安排是先以孔定位粗、精加工顶平面。第二个工序是加工定位用的两个工艺孔。由于顶平面加工完成后一 直到 连杆 加工完成为止,除了个别工序外,都要用作定位基准。因此,顶面上的螺孔也应在加工两工艺孔的工序中同时加工出来。 后续工序安排应当遵循粗精分开和先面后孔的原则。先粗加工平面,再粗加工孔系。螺纹底孔在多轴组合钻床上钻出,因切削力较大,也应该在粗加工阶段完成。对于 连杆 ,nts 需要精加工的是支承孔前后端平面。按上述原则亦应先精加工平面再加工孔系,但在实际生产中这样安排不易于保证孔和端面相互垂直。因此,实际采用的工艺方案是先精加工支承孔系,然后以支承孔用可胀心轴定位来加工端面,这样容易保证零件图纸上规定的端面全跳动公差 要求。各螺纹孔的攻丝,由于切削力较小,可以安排在粗、精加工阶段中分散进行。 加工工序完成以后,将工件清洗干净。清洗是在 c9080 的含 0.4% 1.1%苏打及0.25% 0.5%亚硝酸钠溶液中进行的。清洗后用压缩空气吹干净。保证零件内部杂质、铁屑、毛刺、砂粒等的残留量不大于 mg200 。 根据以上分析过程,现将 连杆 加工工艺路线确定如下: 工艺路线一: 10 锻 锻造毛坯 20 退火 退火(消除内应力) 30 粗铣 铣削底部大端面,留加工余量 40 粗铣 翻面,铣削 25 凸台端面,留加工余量 50 粗铣 粗铣 60 凸台端面,留加工余量 60 精铣 精铣 60 凸台端面 70 精铣 精铣 25 凸台端面 70 精铣 翻面,精铣底部大端面 90 钻扩铰孔 钻扩铰孔 15 及倒角 100 钻扩铰孔 钻扩铰孔 36 及倒角 110 粗铣 粗铣 45 度 ,宽度为 10 的槽 120 精铣 精铣 45 度 ,宽度为 10 的槽 130 钳工 去毛刺 140 检验 检验 工艺路线二: 10 锻 锻造毛坯 20 退火 退火(消除内应力) 30 粗铣 铣削底部大端面,留加工余量 40 粗铣 翻面,铣削 25 凸台端面,留加工余量 50 粗铣 粗铣 60 凸台端面,留加工余量 60 精铣 精铣 60 凸台端面 70 精铣 精铣 25 凸台端面 nts 70 精铣 翻面,精铣底部大端面 90 钻扩铰孔 钻扩铰孔 15 及倒角 100 钻扩铰孔 钻扩铰孔 36 及倒角 110 粗铣 粗铣 45 度 ,宽度为 10 的槽 120 精铣 精铣 45 度 ,宽度为 10 的槽 130 钳工 去毛刺 140 检验 检验 以上加工方案大致看来合理,但通过仔细考虑,零件的技术要求及可能采取的加工手段之后,就会发现仍有问题, 方案 二 把 钻孔 工序调整到后面 了,这样导致 加工斜面无法找到合适的定位基准 ,无法满足零件公差要求 。 以上工艺过程详见机械加工工艺过程综合卡片。 综合选择方案一: 工艺路线一: 10 锻 锻造毛坯 20 退火 退火(消除内应力) 30 粗铣 铣削底部大端面,留加工余量 40 粗铣 翻面,铣削 25 凸台端面,留加工余量 50 粗铣 粗铣 60 凸台端面,留加工余量 60 精铣 精铣 60 凸台端面 70 精铣 精铣 25 凸台端面 70 精铣 翻面,精铣底部大端面 90 钻扩铰孔 钻扩铰孔 15 及倒角 100 钻扩铰孔 钻扩铰孔 36 及倒角 110 粗铣 粗铣 45 度 ,宽度为 10 的槽 120 精铣 精铣 45 度 ,宽度为 10 的槽 130 钳工 去毛刺 140 检验 检验 2.5 机械加工余量、工序尺寸及毛坯尺寸的确定 “ 连杆 ”零件材料采用 为锻造件,对毛坯的结构工艺性有一定要求: 由于模锻件尺寸精度较高和表面粗糙度值低,因此零件上只有与其它机件配合的表面才需要进行机械加工,其表面均应设计为非加工表面。 为了使金属容易充满模膛和减少工序,模锻件外形应力求简单、平直的对称,nts 尽量避免模锻件截面间差别 过大,或具有薄壁、高筋、高台等结构。 模锻件的结构中应避免深孔或多孔结构。 模锻件的整体结构应力求简单。 工艺基准以设计基准相一致。 便于装夹、加工和检查。 结构要素统一,尽量使用普通设备和标准刀具进行加工。 在确定毛坯时,要考虑经济性。虽然毛坯的形状尺寸与零件接近,可以减少加工余量,提高材料的利用率,降低加工成本,但这样可能导致毛坯制造困 难,需要采用昂贵的毛坯制造设备,增加毛坯的制造成本。因此,毛坯的种类形状及尺寸的确定一定要考虑零件成本的问题但要保证零件的使用性能。在毛坯的种类 形状及尺寸确定后,必要时可据此绘出毛坯图。 ( 1) 斜 面的加工余量。 根据工序要求,顶面加工分粗、精铣加工。各工步余量如下: 粗铣:参照机械加工工艺手册第 1 卷表 3.2.23。其余量值规定为 mm4.37.2 ,现取 mm0.3 。表 3.2.27 粗铣平面时厚度偏差取 mm28.0 。 精铣:参照机械加工工艺手册表 2.3.59,其余量值规定为 mm5.1 。 ( 2) 前后端面加工余量。 根据工艺要求,前后端面分为粗铣、精铣加工。各工序余量如下: 粗铣:参照机械加工工艺手册第 1 卷表 3.2.23,其加工余量规定为 mm5.37.2 ,现取 mm0.3 。 半精铣:参照机械加工工艺手册第 1 卷,其加工余量值取为 mm5.2 。 精铣:参照机械加工工艺手册,其加工余量取为 mm5.0 。 铸件毛坯的基本尺寸为 mm37135.25.0365 ,根据机械加工工艺手册表2.3.11,铸件尺寸公差等级选用 CT7。再查表 2.3.9 可得铸件尺寸公差为 mm6.1 。 毛坯为实心,不冲孔。参照机械加工工艺手册表 2.3.71,现确定螺孔加工余量为: 2.6 确定切削用量及基本工时(机动时间) 工序 30: 铣削底部大端面,留加工余量 机床:铣床 X52K 刀具:硬质合金端铣刀(面铣刀) mmdw 400齿数 14Z 10 ( 1) 粗铣 连杆 底面 粗铣夹轴承孔两侧毛坯,粗铣轴承底面,注意尺寸 66mm 和表面粗糙度,留 1mm 精 加工余量 nts 铣削深度pa: mmap 2每齿进给量fa:根据机械加工工艺手册表 2.3.73,取 Zmmaf /25.0铣削速度 V :参照机械加工工艺手册 表 2.3.81,取 smV /4 机床主轴转速 n : m in/19140014.3 6041 0 0 01 0 0 0 0 rd Vn ,取 min/200 rn 实际铣削速度 V : smndV /19.4601000 20040014.31000 0 进给量fV: smmZnaVff /67.1160/2001425.0 工作台每分进给量mf: m in/2.700/67.11 mmsmmVffm a:根据机械加工工艺手册表 2.3.81, mma 240被切削层长度 l :由毛坯尺寸可知 mml 341 刀具切入长度 1l : mmaDDl 42)31()(5.0 221 刀具切出长度 2l :取 mml 22 走刀次数为 1 机动时间1jt: m in55.02.700242341211 mj flllt 工序 40: 翻面,铣削 25凸台端面,留加工余量 。 已知工件材料为 HT200,选择高速钢圆柱铣刀直径 d=60mm,齿数 z=10。根据资料选择铣刀的基本形状 ,rn=10, a0=12, =45已知铣削宽度 ae=2.5mm,铣削深度aP =50mm 故机床选用 X52K 立式铣床。 1.确定每齿进给量 fZ 根据资料所知, X52K 立式卧式铣床的功率为 7.5kw,工艺系统刚性为中等。查得每齿进给量 fZ =0.16 0.24mm/z、现取 fZ =0.16mm/z。 2.选择铣刀磨损标准及耐用度 根据资料所知,铣刀刀齿后刀面的最大磨损量为 1.5mm, 铣刀直径 d=60mm,耐用度 T=180min。 3.确定切削速度 根据资料所知,依据铣刀直径 d=60mm, 齿数 z=10,铣削宽度 ae=2.5mm,铣 削 深 度 a P =50mm , 耐 用 度 T=180min 时 查 取 Vc 98mm/s ,n=439r/min,Vf=490mm/s。 根据 X52K 立式 铣床 主轴转速表查取, nc=300r/min,Vfc=475mm/s。 nts 则实际切削 : Vc =10000 cndVc=1000 3006014.3 =56.52m/min 实际进给量 : fzc=znvccf fzc=10300475=0.16mm/z 3.校验机床功率 根据 资料所知 ,铣削时的功率(单位 kw)为 :当 fZ =0.16mm/z, aP =50mm, ae=2.5mm, Vf=490mm/s时由 切削功率的修正系数 kmpc=1,则 Pcc= 3.5kw, Pct=0.8 kw。 根据 X52K 型立式铣床 说明书可知:机床主轴主电动机允许的功率 Pcm= PcmPctPcm=7.5 0.8=6 Pcc= 3.5kw 因此机床功率能满足要求。 基本时间 根据 资料所知高速钢圆柱铣刀 铣面基本时间为: tm=zc fnl2 tm=16.0300 )6050(2 =3.6min 工序 50: 粗铣 60凸台端面,留加工余量 机床: 铣床 X52K 刀具:硬质合金端铣刀(面铣刀) mmdw 400齿数 14Z 10 ( 1)粗铣 铣削深度pa: mmap 3每齿进给量fa:根据机械加工工艺手册表 2.3.73,取 Zmmaf /25.0铣削速度 V :参照机械加工工艺手册表 2.3.81,取 smV /4 nts 机床主轴转速 n : m in/19140014.3 6041 0 0 01 0 0 0 0 rd Vn ,取 min/200 rn 实际铣削速度 V : smndV /19.4601000 20040014.31000 0 进给量fV: smmZnaVff /67.1160/2001425.0 工作台每分进给量mf: m in/2.700/67.11 mmsmmVffm a:根据机械加工工艺手册表 2.3.81, mma 240被切削层长度 l :由毛坯尺寸可知 mml 341 刀具切入长度 1l : mmaDDl 42)31()(5.0 221 刀具切出长度 2l :取 mml 22 走刀次数为 1 机动时间1jt: m in55.02.700242341211 mj flllt ( 2)精铣 铣削深度pa: mmap 1每齿进给量fa:根据机械加工工艺手册表 2.3.73,取 Zmmaf /15.0铣削速度 V :参照机械加工工艺手册表 2.3.81,取 smV /6 机床主轴转速 n : m in/28840014.3 6061 0 0 01 0 0 0 0 rd Vn ,取 min/300 rn 实际铣削速度 V : smndV /28.6601000 30040014.31000 0 进给量fV: smmZnaVff /5.1060/3 0 01415.0 工作台每分进给量mf: m in/6 3 0/5.10 mmsmmVffm 被切削层长度 l :由毛坯尺寸可知 mml 341 刀具切入长度 1l :精铣时 mmDl 4001 刀具切出长度 2l :取 mml 22 走刀次数为 1 机动时间2jt: m in18.16302400341212 mj flllt 本工序机动时间 m in73.118.155.021 jjj ttt 工序 60: 精铣 60凸台端面 nts 机床: 铣床 X52K 刀具:硬质合金端铣刀(面铣刀) mmdw 400齿数 14Z 10 ( 1)粗铣 铣削深度pa: mmap 3每齿进给量fa:根据机械加工工艺手册表 2.3.73,取 Zmmaf /25.0铣削速度 V :参 照机械加工工艺手册表 2.3.81,取 smV /4 机床主轴转速 n : m in/19140014.3 6041 0 0 01 0 0 0 0 rd Vn ,取 min/200 rn 实际铣削速度 V : smndV /19.4601000 20040014.31000 0 进给量fV: smmZnaVff /67.1160/2001425.0 工作台每分进给量mf: m in/2.700/67.11 mmsmmVffm a:根据机械加工工艺手册表 2.3.81, mma 240被切削层长度 l :由毛坯尺寸可知 mml 341 刀具切入长度 1l : mmaDDl 42)31()(5.0 221 刀具切出长度 2l :取 mml 22 走刀次数为 1 机 动时间1jt: m in55.02.700242341211 mj flllt 工序 60 精铣 25 凸台端面 铣削深度pa: mmap 1每齿进给量fa:根据机械加工工艺手册表 2.3.73,取 Zmmaf /15.0铣削速度 V :参照机械加工工艺手册表 2.3.81,取 smV /6 机床主轴转速 n : m in/28840014.3 6061 0 0 01 0 0 0 0 rd Vn ,取 min/300 rn 实际铣削速度 V : smndV /28.6601000 30040014.31000 0 进给量fV: smmZnaVff /5.1060/3 0 01415.0 工作台每分进给量mf: m in/6 3 0/5.10 mmsmmVffm 被切削层长度 l :由毛坯尺寸可知 mml 341 刀具切入长度 1l :精铣时 mmDl 4001 nts 刀具切出长度 2l :取 mml 22 走刀次数为 1 机动时间 2jt : m in18.16302400341212 mj flllt 本工序机动时间 m in73.118.155.021 jjj ttt 工序 100 精铣 翻面,精铣底部大端面 铣削深度pa: mmap 1每齿进给量fa:根据机械加工工艺手册表 2.3.73,取 Zmmaf /15.0铣削速度 V :参照机械加工工艺手册表 2.3.81,取 smV /6 机床主轴转速 n : m in/28840014.3 6061 0 0 01 0 0 0 0 rd Vn ,取 min/300 rn 实际铣削速度 V : smndV /28.6601000 30040014.31000 0 进给量fV: smmZnaVff /5.1060/3 0 01415.0 工作台每分进给量mf: m in/6 3 0/5.10 mmsmmVffm 被切削层长度 l :由毛坯尺寸可知 mml 341 刀具切入长度 1l :精铣时 mmDl 4001 刀具切出长度 2l :取 mml 22 走刀次数为 1 机动时间 2jt : m in18.16302400341212 mj flllt 本工序机动时间 m in73.118.155.021 jjj ttt 工序 110 精铣 精铣距离为 9.5 的侧面 铣削深度pa: mmap 1每齿进给量fa:根据机械加工工艺手册表 2.3.73,取 Zmmaf /15.0铣削速度 V :参照机械加工工艺手册表 2.3.81,取 smV /6 机床主轴转速 n : m in/28840014.3 6061 0 0 01 0 0 0 0 rd Vn ,取 min/300 rn 实际铣削速度 V : smndV /28.6601000 30040014.31000 0 进给量fV: smmZnaVff /5.1060/3 0 01415.0 nts 工作台每分进给量mf: m in/6 3 0/5.10 mmsmmVffm 被切削层长度 l :由毛坯尺寸可知 mml 341 刀具切入长度 1l :精铣时 mmDl 4001 刀具切出长度 2l :取 mml 22 走刀次数为 1 机动时间 2jt : m in18.16302400341212 mj flllt 本工序机动时间 m in73.118.155.021 jjj ttt 工序 3:钻、扩、铰 15孔。 机床: 立式钻床 Z525 刀具:根据参照参考文献 3表 4.3 9 选 高速钢 锥柄麻花钻头。 进给量 f :根据参考文献 3表 2.4 38,取 rmmf /33.0 。 切削速度 V :参照参考文献 3表 2.4 41,取 0.48 /V m s 。 机床主轴转速 n : 1 0 0 0 1 0 0 0 0 . 4 8 6 0 5 3 9 . 5 3 / m i n3 . 1 4 1 7vnrd , 按照参考文献 3表 3.1 31,取 630 / m innr 所以实际切削速度 v : 3 . 1 4 1 7 6 3 0 0 . 5 6 /1 0 0 0 1 0 0 0 6 0dnv m s 切削工 时 被切削层长度 l : 42l mm 刀具切入长度 1l : 1 17( 1 2 ) 1 2 0 1 5 . 9 622rDl c t g k c t g m m m m 刀具切出长度 2l : mml 412 取 mml 32 走刀次数为 1 机动时间1jt:14 2 6 3 0 . 2 5 m i n0 . 3 3 6 3 0jLt fn 扩孔 刀具:根据参照参考文献 3表 4.3 31 选择硬质合金锥柄麻花 扩孔钻头。 片型号: E403 切削深度pa: 1.35pa mmnts 进给量 f :根据参考文献 3表 2.4 52,取 0.6 /f mm r 。 切削速度 V :参照参考文献 3表 2.4 53,取 0.44 /V m s 。 机床 主轴转速 n : 1 0 0 0 1 0 0 0 0 . 4 4 6 0 4 2 6 . 7 8 / m i n3 . 1 4 1 9 . 7vnrD 按照参考文献 3表 3.1 31,取 500 / m innr 所以实际切削速度 v : 3 . 1 4 1 9 . 7 5 0 0 0 . 5 2 /1 0 0 0 1 0 0 0 6 0dnv m s 切削工时 被切削层长度 l : 42l mm 刀具切入长度 1l 有: 11 1 9 . 7 1 7( 1 2 ) 1 2 0 2 2 . 8 6 322rDdl c t g k c t g m m m m 刀具切出长度 2l : mml 412 , 取 mml 32 走刀次数为 1 机动时间2jt:24 2 3 3 0 . 1 6 m i n0 . 6 5 0 0jLt fn 铰孔 刀具:根据参照参考文献 3表 4.3 54,选择硬质合金锥柄机用铰刀。 切削深度pa: 0.15pa mm。 进给量 f :根据参考文献 3表 2.4 58, rmmf /0.20.1 取 rmmf /0.2 。 切削速度 V :参照参考文献 3表 2.4 60,取 smV /32.0 。 机床主轴转速 n : 1 0 0 0 1 0 0 0 0 . 3 2 6 0 3 0 5 . 7 3 / m i n3 . 1 4 2 0VnrD 按照参考文献 3表 3.1 31取 315 / m innr 实际切削速度 v : 3 . 1 4 2 0 6 0 0 0 . 6 3 /1 0 0 0 1 0 0 0 6 0Dnv m s 切削工时 被切削层长度 l : 42l mm 刀具切入长度 1l , 01 2 0 1 9 . 7( 1 2 ) 1 2 0 2 2 . 0 922rDdl c t g k c t g m m 刀具切出长度 2l : mml 412 取 mml 32 nts 走刀次数为 1 机动时间3jt:34 2 2 . 0 9 3 0 . 0 7 m i n2 3 1 5jLt nf 该工序的加工机动时间的总和是jt: 0 . 2 5 0 . 1 6 0 . 0 7 0 . 4 8 m i njt 工序 170 钻扩铰孔 钻扩铰孔 钻扩铰孔 36 及倒角 钻孔选用机床为 Z525 摇臂机床,刀具选用 GB1436-85 直柄短麻花钻,机械加工工艺手册第 2 卷。 根据机械加工工艺手册第 2 卷表 10.4-2 查得钻头直径小于 10mm 的钻孔进给量为 0.20 0.35 rmm 。 则取 rmmf 30.0 确定切削速度,根据机械加工工艺手册第 2 卷表 10.4-9 切削速度计算公式为 m in0 mkfaT dcv vyxpmzvvvv( 3-20) 查得参数为 125.0,55.0,0,25.0,1.8 myxzc vvvv ,刀具耐用度 T=35min 则 v = 55.0012 5.025.03.0535 71.8 =1.6 minm 所以 n = 714.3 6.11000 =72 minr 选取 min120 rn 所以实际切削速度为 1000 714.3120 v =2.64 minm 确定切削时间(一个孔) t = s203.02 228 工序 110: 粗铣精铣 45度 ,宽度为 10的槽 。 已知工件材料为 HT200,选择高速钢圆柱铣刀直径 d=60mm,齿数 z=10。根据资料选择铣刀的基本形状 ,rn=10, a0=12, =45已知铣削宽度 ae=2.5mm,铣削深度aP =50mm 故机床选用 X52K 立式铣 床。 1.确定每齿进给量 fZ 根据资料所知, X52K 立式卧式铣床的功率为 7.5kw,工艺系统刚性为中等。nts 查得每齿进给量 fZ =0.16 0.24mm/z、现取 fZ =0.16mm/z。 2.选择铣刀磨损标准及耐用度 根据资料所知,铣刀刀齿后刀面的最大磨损量为 1.5mm, 铣刀直径 d=60mm,耐用度 T=180min。 3.确定切削速度 根据资料所知,依据铣刀直径 d=60mm, 齿数 z=10,铣削宽度 ae=2.5mm,铣 削 深 度 a P =50mm , 耐 用 度 T=180min 时 查 取 Vc 98mm/s ,n=439r/min,Vf=490mm/s。 根据 X52K 立式 铣床 主轴转速表查取, nc=300r/min,Vfc=475mm/s。 则实际切削 : Vc =10000 cndVc=1000 3006014.3 =56.52m/min 实际进给量 : fzc=znvccf fzc=10300475=0.16mm/z 3.校验机床功率 根据 资料所知 ,铣削时的功率(单位 kw)为 :当 fZ =0.16mm/z, aP =50mm, ae=2.5mm, Vf=490mm/s时由 切削功率的修正系数 kmpc=1,则 Pcc= 3.5kw, Pct=0.8 kw。 根据 X52K 型立式铣床 说明书可知:机床主轴主电动机允许的功率 Pcm= PcmPctPcm=7.5 0.8=6 Pcc= 3.5kw 因此机床功率能满足要求。 基本时间 根据 资料所知高速钢圆柱铣刀 铣面基本时间为: tm=zc fnl2 tm=16.0300 )6050(2 =3.6min nts 第 3 章 铣 斜槽 夹具设计 3.1 设计要求 为了提高劳动生产,保证加工质量,降低劳动强度,需要设计专用夹具。下面即为 铣 斜槽 的专用夹具,本夹具将用于 X52K 铣床 。 本夹具无严格的技术要求,因此,应主要考虑如何提高劳动生产率,降低劳动强度,精度不是主要考虑的问题。 3.2 夹具设计 3.2.1 定位基准的选择 为了提高加工效率及方便加工,决定材料使用高速钢,用于对进行加工,准备采用手动夹紧。 由零件图可知:在对 铣 斜槽 进行加工前,底平面进行了粗、精铣加工, 进行了粗、精加工。 因此 ,定位、夹紧方案有: 方案 :选底平面、和侧面定位夹紧方式用操作简单,通用性较强的移动压板来夹紧。 方案 :选一面两销定位方式, 2 销,夹紧方式用操作简单,通用性较强的 螺旋 压板来夹紧。 为了使定位误差达到要求的范围之内, 这种定位在结构上简单易操作。 3.2.2 切削力及夹紧力的计算 刀具: 立 铣刀(硬质合金) 刀具有关几何参数: 00 15 00 10 顶 刃0n 侧 刃 60010 15 30rK 20.5L mm 22Z 0 .0 8 /fa m m z mma p 0.2 由 参考文献 55 表 1 2 9 可得铣削切削力的计算公式: 0 . 9 0 . 8 0 1 . 1 1 . 1 0 . 12335 pzF a f D B z n 有: 0 . 9 0 0 . 8 0 1 . 1 1 . 1 0 . 12 3 3 5 2 . 0 0 . 0 8 2 8 2 0 . 5 2 2 2 . 4 8 3 6 . 2 4 ( )FN 根据工件受力 切削力、夹紧力的作用情况 ,找出在加工过程中对夹紧最不利的瞬间状态,按静力平衡原理计算出理论夹紧力。最后为保证夹紧可靠,再乘以安全系数作为实际所需夹紧力的数值,即: FKWK 安全系数 K可按下式计算: nts 6543210 KKKKKKKK 式中:60 KK为 各种因素的 安全系数, 查参考文献 51 2 1 可知其公式参数: 1 2 34 5 61 . 0 , 1 . 0 , , 1 . 0 ,1 . 3 , 1 . 0 , 1 . 0 .K K KK K K 由此可得: 1 . 2 1 . 0 1 . 0 1 . 0 1 . 3 1 . 0 1 . 0 1 . 5 6K 所以 8 3 6 . 2 4 1 . 5 6 1 3 0 4 . 5 3 ( )KW K F N 由计算可知所需实际夹紧力不是很大,为了使其夹具结构简单、操作方便,决定选用手动螺旋夹紧机构。 夹紧力的确定 夹紧力方向的确定 夹紧力应朝向主要的定位基面 。 夹紧力的方向尽可能与切 削力和工件重力同向。 (1) 夹紧力作用点的选择 a. 夹紧力的作用点应落在定位元 件的支承范围内。 b. 夹紧力的作用点应落在工件刚性较好的部位上,这样可以防止或减少工件变形变形对加工精度的影响。 c. 夹紧力的作用点应尽量靠近加工表面。 (3)夹紧力大小的估算 理论上确定夹紧力的大小,必须知道加工过程中,工件所受到的切削力、离心力、惯性力及重力等,然后利用夹紧力的作用应与上述各力的作用平衡而计算出。但实际上,夹紧里的大小还与工艺系统的刚性、夹紧机构的传递效率等有关。而且,切削力的大小在加工过程中是变化的,因此,夹紧力的计算是个很复杂的问题,只能进行粗略的估算。 估算的方法: 一是找出对夹紧最不利的瞬时状态,估算此状态下所需的夹紧力;二是只考虑主要因素在力系中的影响,略去次要因素在力系中的影响。 估算的步骤: a.建立理论夹紧力 FJ理 与主要最大切削力 FP的静平衡方程: FJ理 = (F P)。 b.实际需要的夹紧力 FJ需 ,应考虑安全系数, FJ需 =KFJ理 。 c.校核夹紧机构的夹紧力 FJ是否满足条件: FJFJ需 。 夹具的夹紧装置和定位装置 1 2 夹具中的装夹是由定位和夹紧两个过程紧密联系在一起的。定位问题已在前面研究nts 过,其目的在于解决工件的定位方法和保证必要的定位精度。 仅仅 定好位在大多数场合下,还无法进行加工。只有进而在夹具上设置相应的夹紧装置对工件进行夹紧,才能完成工件在夹具中装夹的全部任务。 夹紧装置的基本任务是保持工件在定位中所获得的即定位置,以便在切削力、重力、惯性力等外力作用下,不发生移动和震动,确保加工质量和生产安全。有时工件的定位是在夹紧过程中实
- 温馨提示:
1: 本站所有资源如无特殊说明,都需要本地电脑安装OFFICE2007和PDF阅读器。图纸软件为CAD,CAXA,PROE,UG,SolidWorks等.压缩文件请下载最新的WinRAR软件解压。
2: 本站的文档不包含任何第三方提供的附件图纸等,如果需要附件,请联系上传者。文件的所有权益归上传用户所有。
3.本站RAR压缩包中若带图纸,网页内容里面会有图纸预览,若没有图纸预览就没有图纸。
4. 未经权益所有人同意不得将文件中的内容挪作商业或盈利用途。
5. 人人文库网仅提供信息存储空间,仅对用户上传内容的表现方式做保护处理,对用户上传分享的文档内容本身不做任何修改或编辑,并不能对任何下载内容负责。
6. 下载文件中如有侵权或不适当内容,请与我们联系,我们立即纠正。
7. 本站不保证下载资源的准确性、安全性和完整性, 同时也不承担用户因使用这些下载资源对自己和他人造成任何形式的伤害或损失。

人人文库网所有资源均是用户自行上传分享,仅供网友学习交流,未经上传用户书面授权,请勿作他用。