【温馨提示】 购买原稿文件请充值后自助下载。
以下预览截图到的都有源文件,图纸是CAD,文档是WORD,下载后即可获得。
预览截图请勿抄袭,原稿文件完整清晰,无水印,可编辑。
有疑问可以咨询QQ:414951605或1304139763
摘要
开式曲柄压力机是板料冲压生产中的主要设备,可用于冲孔、落料、切边、弯曲、浅拉伸和成型等工序,并广泛应用于国防、航空、汽车、拖拉机、电机、电器、轴承、仪表、农机、农具、自行车、缝纫机、医疗器械、日用五金等部门中。在中、小型压力机中,开式压力机得到了广泛的发展,目前在我国机器制造业中,开式曲柄压力机的年产量约占整个锻压机械年产量的49.5%,而在通用曲柄压力机的生产中约占95%。
关键词:压力机;曲柄滑块机构;机械制造;
Abstract
Open front mechanical power presses sheet metal stamping production is the main equipment, can be used for punching, blanking, trimming, bending, shallow tensile and molding process, and widely used in national defense, aerospace, automotive, tractor, motor, electric appliance, bearings, instrument, agricultural machinery, tools, bicycles, sewing machines, medical equipment, daily hardware and other departments. In the medium and small press, open press a wide range of development, at present in our country in manufacturing machines, off the output of crank press accounts for about 49.5% of the whole forging machinery production, and in general crank press in the production of about 95%.
Keywords: press; Slider-crank mechanism; Mechanical manufacturing;
目 录
摘要Ⅰ
AbstractⅡ
1 绪论1
1.1锻压机械设备简介及其发展过程1
1.2曲柄压力机的发展和特点2
1.3曲柄压力机的基本参数3
1.4曲柄压力机的工作原理4
1.5曲柄压力机的反求设计与改型5
1.5.1反求设计5
1.5.2开式压力机的改进6
2 电动机的选择和飞轮设计9
2.1压力机电力拖动特点9
2.2电动机的选择9
2.2.1选择电动机的类型9
2.2.2选择电动机的功率10
2.2.3确定电动机的转速11
2.2.4计算总传动比和分配传动比11
2.2.5计算传动装置的运动和动力参数11
2.3飞轮转动惯量及尺寸计算12
2.3.1压力机一次工作循环所消耗的能量12
2.3.2飞轮转动惯量计算16
2.3.3飞轮尺寸计算17
2.3.4飞轮轮缘线速度验算17
2.3.5飞轮起动时间核算18
3 机械传动系统19
3.1传动系统的类型及系统分析19
3.1.1传动系统类型19
3.1.2传动系统的布置方式19
3.1.3离合器和制动器的位置20
3.1.4传动级数和各级传动比的分配20
3.2三角皮带传动设计21
3.3齿轮传动的设计24
3.3.1选择齿轮材料、热处理、齿轮精度等级和齿数24
3.3.2开式齿轮按齿轮弯曲疲劳强度设计24
3.4转轴的设计26
3.4.1轴的概述26
3.4.2JG23-40开式曲柄压力机的转轴设计27
3.5平键连杆30
4 曲柄滑块机构32
4.1曲柄滑块机构的运动分析与受力分析32
4.2曲柄轴的设计计算34
4.2.1曲轴的结构示意图34
4.2.2曲轴强度设计计算34
4.2.3曲轴刚度计算36
4.3连杆和封闭高度调节装置37
4.3.1连杆和封闭高度调节装置的结构37
4.3.2连杆的计算37
4.3.3连杆及球头调节螺杆的强度计算38
4.3.4调节螺杆的螺纹40
4.3.5调节螺杆的螺纹计算40
4.3.6连杆上的紧固螺栓40
4.4曲柄滑块机构中的滑动轴承41
4.4.1滑动轴承的结构41
4.4.2滑动轴承的润滑及轴瓦结构41
4.4.3滑动轴承的计算41
4.5曲柄滑块机构中的滚动轴承43
4.5.1滚动轴承概述43
4.5.2滚动轴承型号选择43
5 离合器与制动器45
5.1离合器与制动器的作用原理45
5.2离合器的设计46
5.2.1离合器的类型、工作特性及其选用原则46
5.2.2双转键离合器的结构47
5.3制动器的设计49
5.3.1制动器的类型、工作特性及其选用原则49
5.3.2带式制动器的结构50
6 机身设计50
6.1机身结构51
6.2 身计算52
7 过载保护装置设计55
7.1剪切破坏式过载保护装置的结构55
7.2剪切块的设计计算 56
8 润滑系统58
8.1曲柄压力机常用润滑剂58
8.1.1稀油润滑58
8.1.2干油润滑59
小结60
致谢61
参 考 文 献62
1 绪论
1.1锻压机械设备简介及其发展过程
人们为了制造工具,最初是用人力、畜力转动轮子来举起重锤锻打工件的,这是最古老的锻压机械。14 世纪出现了水力落锤。15~16 世纪航海业蓬勃发展,为了锻造铁锚等,出现了水力驱动的杠杆锤。18世纪出现了蒸汽机和火车(见机车),因而需要更大的锻件。1842年英国的J.内史密斯创制第一台蒸汽锤,开始了蒸汽动力锻压机械的时代。
1795年英国的J.布拉默发明水压机,但直到19世纪中叶由于大锻件的需要才应用于锻造。随着电动机的发明,19世纪末出现了以电为动力的机械压力机和空气锤,并获得迅速发展。第二次世界大战以来,750000千牛的模锻水压机、1500千焦的对击锤、60000 千牛的板料冲压压力机、160000千牛的热模锻压力机等重型锻压机械和一些自动冷镦机相继问世,形成了门类齐全的锻压机械体系。
20世纪 60年代以后,锻压机械改变了从 19世纪开始的向重型和大型方向发展的趋势,转而向高速、高效、自动、精密、专用、多品种生产等方向发展。于是出现了每分种行程 2000次的高速压力机、60000千牛的三坐标多工位压力机,25000 千牛的精密冲裁压力机,能冷镦直径为48毫米钢材的多工位自动冷镦机和多种自动机、自动生产线等。各种机械控制的、数字控制的和计算机控制的自动锻压机械以及与之配套的操作机、机械手和工业机器人也相继研制成功。现代化的锻压机械可生产精确制品,有良好的劳动条件,环境污染很小。
随着大型多工位压力机的技术成熟和实用化,大型多工位压力机开始替代单动压力机进入自动冲压生产线,代表了先进的组合方式。大型多工位压力机自动冲压生产线,经历了三个阶段的完善与发展。
较原始的组合是,一台双动拉深压力机与一台单动大型多工位压力机为主机,二者之间配备一套翻转装置和同步装置,提高了生产节拍,减少了占地面积。此后,带双动拉深工位的多工位压力机问世,催生了第二代自动冲压生产线。第二代生产线仅以一台带双动拉深工位的多工位压力机为主机,在其前后分别配备拆垛装置和码垛装置,便组成了一条自动冲压生产线,配置大为简化。此类多工位压力机多为四柱三滑块结构,第一工位是双动拉深工位,其余工位为单动冲压工位。由于拉深工位采取了反向拉深的方式,从而避免了工件的翻转,因此不需要翻转装置,使生产率进一步提高,占地面积进一步减小。第三阶段,出现了带数控液压气垫的大型多工位压力机,抛弃了传统的双动拉深工艺理念,真正将拉深与其他冲压工艺组合到一台压力机上完成。自动冲压生产线的主机是带数控液压气垫的多工位压力机,主机前后配备拆垛装置和码垛装置。数控液压气垫是该类生产线的技术核心,气垫通过四角控制,可调节拉深工件的压边力,从而实现单动深拉深。由于采用数控液压气垫使单动压力机代替了传统的双动压力机,简化了压力机的结构,取消了生产线中的翻转装置,实现了压边力的优化控制,提高了拉深件的质量,降低了工件的废品率。从技术角度上讲,带数控液压气垫的大型多工位压力机自动冲压生产线,代表了自动冲压生产线的最高水平。但是,由于造价、技术及应用等诸多方面的因素,大型冲压生产线多样化组合的局面还将长期存在。










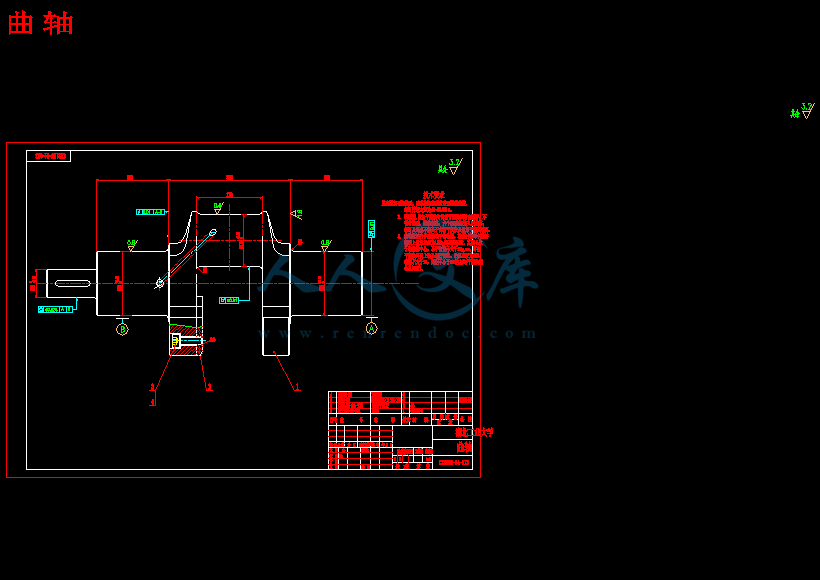

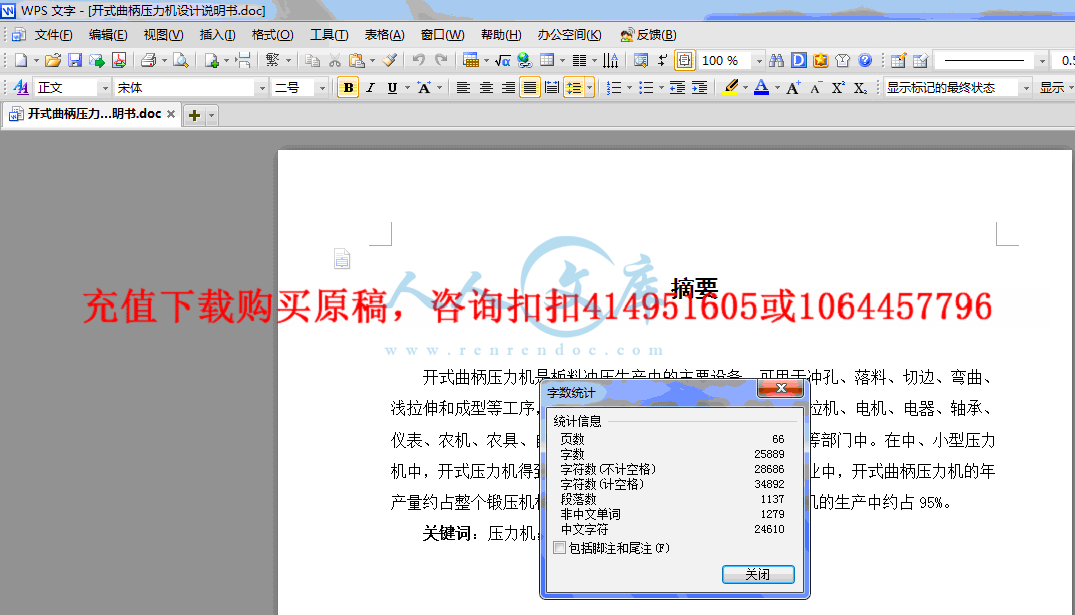
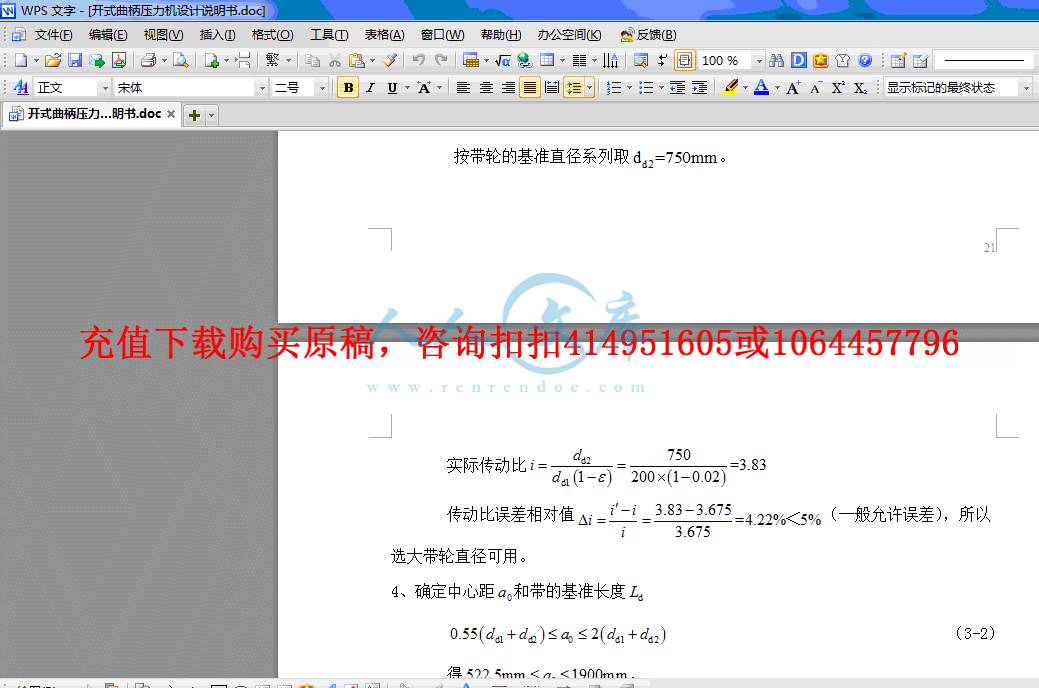
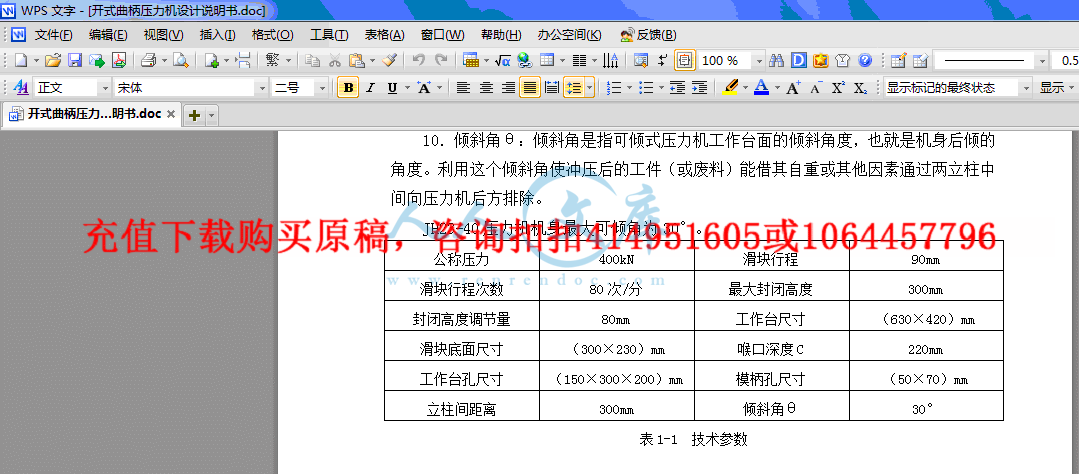