!【详情如下】CAD图纸+word设计说明书.doc[26000字,65页]【需要咨询购买全套设计请加QQ97666224】.bat
A型活动挡料销.dwg
上垫板.dwg
上模座板.dwg
下垫板.dwg
下模座板.dwg
冲孔凸模.dwg
凸凹模.dwg
凸凹模固定板.dwg
凸模固定板.dwg
卸料板.dwg
导柱.dwg
打杆.dwg
推件块.dwg
模柄.dwg
空心垫板.dwg
落料凹模板.dwg
装配图.dwg
中文翻译.doc
中期检查表.doc
开题报告1.doc
设计说明书.doc[26000字,65页]
英文文献.doc
止 动 板 冲 裁 模 设 计
摘 要
本文介绍了止动件的冷冲压模具设计,文章介绍了冷冲压模具设计的全过程。对冷冲压模具的设计进行了全面的介绍和分析,并在此基础上进行了模具的设计,设计包括分析工艺性、拟定零件的工艺方案及模具结构、排样裁板、计算工具压力选取压力机及确定压力中心、确定模具结构和绘制模具总装草图,冲裁刃口尺寸及公差的计算、冲模刃口尺寸及公差的计算、确定各主要的零件结构尺寸、设计并绘制总图和选取标准件、绘制出部分非标零件图等一系列的工作。
关键词:冷冲压 止动件 模具设计
THE STAMPING AND PUNCHING MOLD DESIGN FOR STOPPER PLATE
ABSTRACT
This paper describes the stop moving pieces of cold stamping mould design, this paper introduces the whole process of cold stamping mould design. On cold stamping mould design a comprehensive introduction and analysis, and on this basis the die design, the design includes analysis of the technology of technological scheme, drew up parts die structure, arrangement and cutting board, computational tool pressure pressure center and confirming the selected press mould structure and rendering, identify sketch, punching mould assembly blade dimensions and tolerances of calculation, punching the blade dimensions and tolerances of computing, confirm the main parts structure size, design and drawing layout, and select the standard parts, and draw the part of non-standard parts graph, and a series of work
Keywords: cold stamping, stop moving parts, mold design
目 录
前言…………………………………………………………………………1
第一章:引言…………………………………………………………………2
1.1 模具行业的发展现状及市场前景……………………………………2
1.2 冲压工艺介绍……………………………………………………………3
1.3 冲压工艺的种类…………………………………………………4
1.4 冷冲压模具发展简介……………………………………………5
1.4.1 冷冲模工业在历史上的背景………………………………………5
1.4.2冷冲模工业现状…………………………………………………5
1.4.3冷冲模的发展方向…………………………………………………7
1.5冲压行业阻力和障碍与突破…………………………………………9
1.6相关研究的最新成果及动态…………………………………………12
1.7 毕业设计的意义…………………………………………………………14
第二章:必备理论知识……………………………………………………17
2.1冲裁变形过程……………………………………………………………..17
2.2冲裁件的质量……………………………………………………18
2.3冲裁间隙……………………………………………………………….19
2.4凸凹模尺寸计算…………………………………………………………21
2.5冲压力的计算……………………………………………………………26
2.6压力中心的计算…………………………………………………………27
2.7冲裁排样设计……………………………………………………………28
第三章止动件的设计…………………………………………………………31
3.1 设计题目一止动板………………………………………………31
3.2冲压件工艺分析………………………………………………………32
3.2.1材料性能……………………………………………………………….32
3.2.2冲裁件的形状和尺寸…………………………………………32
3.2.3冲裁件的尺寸精度……………………………………………………..32
3.2.4尺寸标注………………………………………………………33
3.3 方案及模具结构类型…………………………………………………33
3.3.1工艺方案分析……………………………………………………33
3.3.2模具结构类型的选定…………………………………………………33
3.4 排样计算………… ……………………………………………………....35
3.4.1材料利用率…………………………………………………37
3.4.2排样方式…………………………………………………38
3.4.3搭边……………………………………………………38
3.5压力计算 … …………………………………………………………… .38
3.5.1冲裁力的计算………………………………………………………..38
3.5.2卸料力和推件力的计算……………………………………………39
3.6 模具压力中心计算……………………………………………………40
3.7 零件刃口尺寸计算………………………………………………41
3.7.1计算原则………………………………………………41
3.7.2冲孔刃口计算………………………………………………42
3.7.3落料刃口计算…………………………………………………43
3.8 凸凹模刃口尺寸计算…………………………………………45
3.8.1刃口尺寸计算…………………………………………………45
3.8.2落料凹模板尺寸…………………………………………………45
3.8.3凸凹模尺寸……………………………………………………46
3.8.4冲孔凸模尺寸……………………………………………………46
3.8.5冲孔刃口尺寸计算…………………………………………………47
3.9 弹性元件的设计计算…………………………………………………47
3.10其它模具零件结构尺寸………………………………………………48
3.10.1模架的选择……………………………………………………48
3.10.2闭合高度………………………………………………………..48
3.11 模具的零件设计与计算……………………………………………49
3.11.1凸模的外形尺寸……………………………………………………49
3.11.2凹模尺寸结构……………………………………………………….50
3.11.3卸料设计与计算……………………………………………………51
3.11.4卸料螺钉……………………………………………………51
3.11.5卸料螺钉尺寸关系…………………………………………………51
3.12 冲床选用………………………………………………………………52
3.12.1冲压设备的选择依据…………………………………………52
3.12.2压力机的选择……………………………………………………53
致谢…………………………………………………………………………………54
参考文献………………………………………………………………………55
设计总结…………………………………………………………………………56
附录…………………………………………………………………………..57
附表…………………………………………………………………………57
冲压工艺制作……………………………………………………………60
参考文献
1:冷冲压工艺及模具设计 作者 曾文霞/徐振 出版社: 中南大学出版社
2: 冷冲压模具设计与制造 作者 王秀凤/张永 出版社: 北京航空航天大学出版社
3:冷冲压模具设计 作者 刘庚武 出版社: 西安电子科技大学出版社
4:冷冲压模具设计指导 作者 王芳 出版社: 机械工业出版社
5:机械实用手册 作者 赵文珍 出版社: 科学出版社
6:机械加工实用手册 作者 夏祖印/张能武 出版社: 安徽科技出版社
8:模具课程设计指导 作者 梅伶 出版社: 机械工业出版社
9:冷冲压模具设计 作者 李双义 出版社: 清华大学出版社
10:冷冲压工艺与模具设计 作者 刘靖岩 出版社: 轻工业出版社
11 黄毅宏主编.模具制造工艺. 北京:机械工业出版社,2008
12 邓明主编.实用模具设计简明手册. 北京:机械工业出版社,2006
13 史铁粱主编.模具设计指导. 北京:机械工业出版社,2008
14 模具实用技术丛书编委会.冲模设计应用实例.北京:机械工业出版2002
15 郑家贤编.冲压模具设计实用手册. 北京:机械工业出版社,2008
16 彭建生编.模具设计与加工速查手册. 北京:机械工业出版社,2005
17 肖亚慧主编.模具工工作手册. 北京:化学工业出版社,2008
18 王新华主编.冲模设计与制造实用计算手册.北京:机械工业出版社,2003
19 陈于萍等主编.互换性与测量技术基础. 北京:机械工业出版社,2007
20青主编.机械制造技术基础课程设计指导教程.北京:机械工业出版社2007
21 邓文英主编.金属工艺学. 北京:高等教育出版社,2000
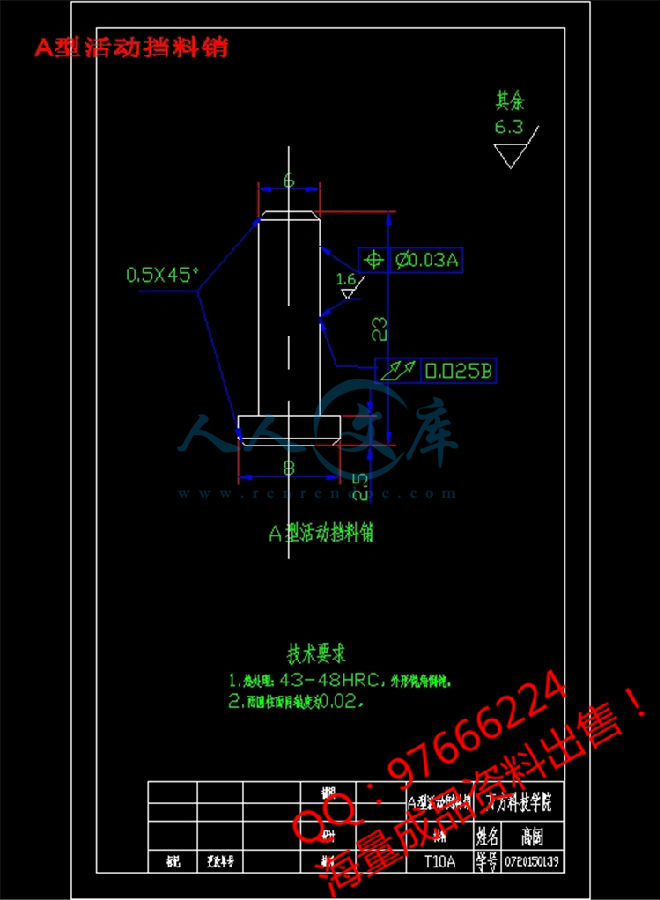
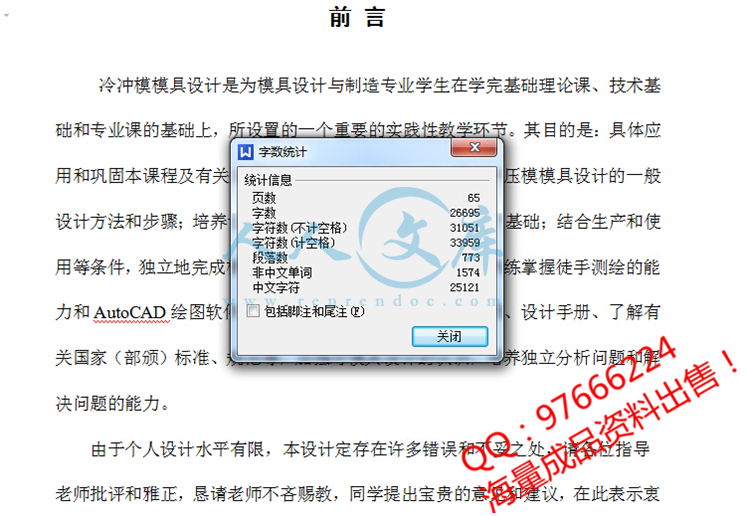


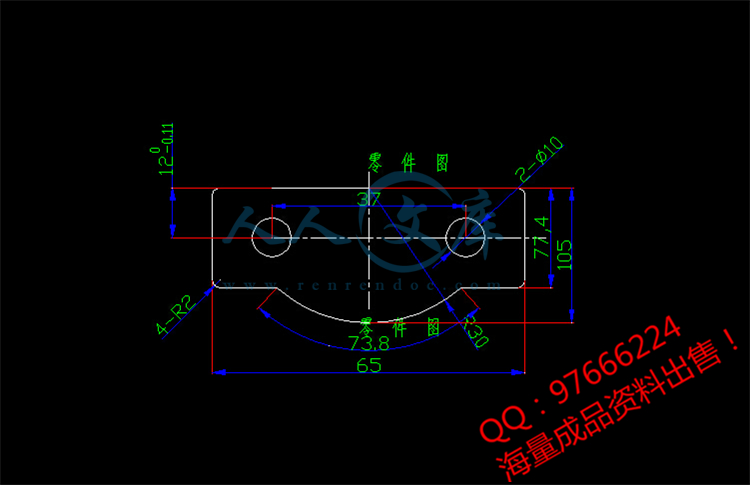










