大型制药厂热电冷三联供工程设计研究
摘 要:热电冷系统利用吸收式制冷技术给设备供暖和制冷。利用现有热电联产系统发展集中供热,供电和供冷为一体的能源综合利用系统。该系统将溴化锂吸收式制冷机引入到热电厂的热电联产系统中,可增加热电厂的夏季热负荷,从而使冬夏热负荷平衡,保证热电厂更经济高效地运行。本文根据热电冷三联供节约能源的原理,对一座较大型的药厂进行工程设计研究,结合药厂对温度,湿度要求高的特点,进行详细计算,仔细论证,对制冷设备参数提出要求。通过调查和计算,将热、电、冷联产与热电和冷量分供系统加以比较,表明该系统不但可节能,而且具有增加电能生产和保护环境的效益。
主题词:热、电、冷三联供;吸收;环保
Electricity Heat and Chilled Water Congenerating System in large-scale pharmaceutical factory is provided in the engineering design research.
Abstract: Combined heat and power(CHP) systems often use absorption technology to supply heating and cooling to a facility.This paper puts forward an energy comprehensive utilization system, Electricity Heat and Chilled Water Congenerating System(EHCWCS).This system introduces H2O-LiBr Absorption Refrigenerating Machine into Heat and Power Plant to increase the heat load of the plant in summer,which can balance the heat load in summer and winter, so Heat and Power Plant can run in a high efficiency. This text is according to the thermo-electricity cold triple-generation system provide the principle that economize the energy, proceeding to a large pharmaceutical factory the engineering design study, joining together the pharmaceutical factory to the temperature, the degree of humidity requests the high characteristics, proceeding the detailed calculation, carry on detailed calculation, put forward the request to the refrigeration equipments in system parameter. The result of analysis states that this system can not only save energy, but also increase the output of electricity of Heat and Power Plant and protect environment.
Theme words: electricity heat and chilled water congenerating; absorption; ervironmental protection
目录
第一章 绪论…………………………………………………………1
第二章 工程概述……………………………………………………2
第三章 设计参数……………………………………………………3
第一节 室外设计参数……………………………………………3
第二节 室内设计参数……………………………………………3
第四章 负荷计算……………………………………………………4
第一节 冷负荷计算………………………………………………4
第二节 热负荷计算………………………………………………8
第五章 空调方案的选择及空气处理过程的确定…………10
第一节 空调房间送风量和送风状态参数的确定……………10
第二节 空调方案的选择………………………………………12
第六章 空气风系统设计及气流组织计算…………………14
第七章 方案比较…………………………………………………17
第八章 空调水系统设计…………………………………………18
第九章 设备选型及安装…………………………………………20
第十章 空气风系统设计及气流组织计算……………………27
第十一章 能效分析…………………………………………29
设计总结及收获………………………………………………33
致谢……………………………………………………………………34
参考文献………………………………………………………………35
第一章 绪论
热电冷联产系统在大幅度提高能源利用率及降低碳和污染空气的排放物方面具有很大的潜力。有关专家做了这样的估算,如果从2000年起每年有4%的现有建筑的供电、供暖和供冷采用热电冷联产,从2005年起25%的新建建筑及从2010年起50%的新建建筑均采用热电冷联产的话,到2020年的二氧化碳的排放量将减少19%。如果将现有建筑实施热电冷联产的比例从4%提高到8%,到2020年二氧化碳的排放量将减少30%。
热电冷联供系统与远程送电比较,可以大大提高能源利用效率。大型发电厂的发电效率为35%-55%,扣除厂用电和线损率。终端的利用效率只能达到30-47%,而热电冷联产的效率可达到90%,没有输电损耗。热电冷联产系统与大型热电联产比较,大型热电联产系统的效率也没有热电冷联产高,而且大型热电联产还有输电线路和供热管网的损失。显然热电冷联产可以减少输配电系统和供热管网的投资,无论从减少投资成本和减轻污染来讲都是十分有利的。
(1)经济效益:热、电、冷三联供解决了热电厂冬夏季热负荷不均造成的热经济性低的问题,降低了发电煤耗率,提高了经济效益。
(2)环保效益:以溴化锂吸收式制冷机取代压缩式制冷机,避免了CFC类氟利昂制冷剂的大量使用和排泄,起到环保的作用。
(3)节电:溴化锂吸收式制冷机较压缩式有明显的节电效益,可以大大缓解夏季用电紧张的问题。
(4)投资少:溴化锂吸收式制冷机的基建投资仅为压缩式制冷机的50%--60%左右,年运行费用也较压缩式少。
热电冷三联产技术是一种能源综合利用技术不仅可以节约能源,还可以减轻对环境的污染,因而在全世界范围内得到了发展。日本和歌山马里拿弟区开发了以海南发电厂抽汽作为蒸汽吸收式制冷机热源的三联产系统,建立了热源分厂和冷暖站,向用户集中供热、供冷和供生活热水。意大利的拉波利综合医院采用从中央热源厂生产的180℃高温水、冷水和蒸汽三种热媒的方式进行集中三联供。我国的热电冷三联产系统是最近几年才发展起来的。山东省淄博市率先利用张店热电厂的低压蒸汽的热源,实现了热电冷三联产。哈尔滨制药厂采用蒸汽两效溴化锂吸收式制冷机制取低温水;在冬季采暖期间,以大自然空气为冷源,采用玻璃钢冷却塔制取低温水。随后,济南、南京、上海等城市也相继设置了热电冷三联产系统。
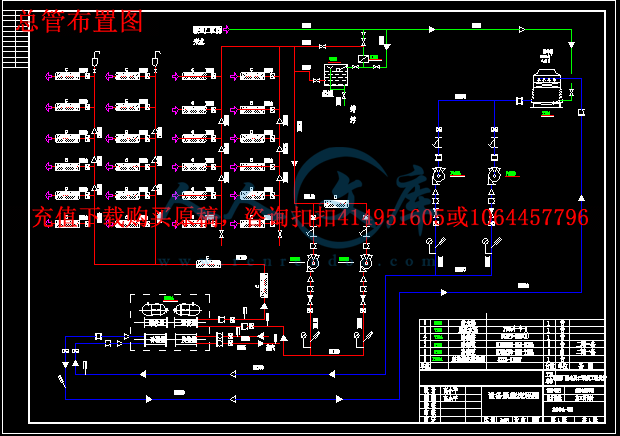
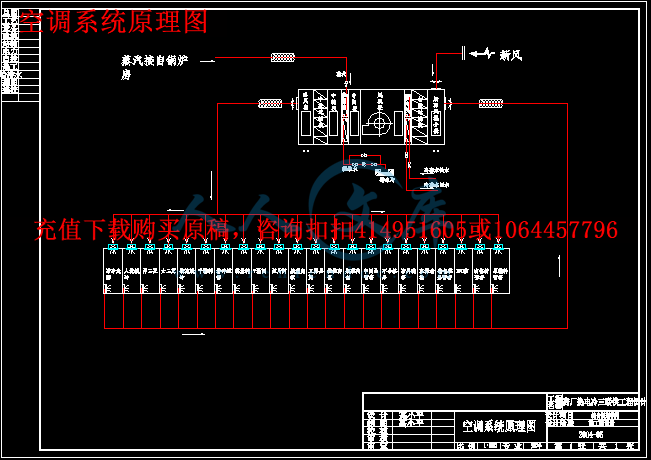
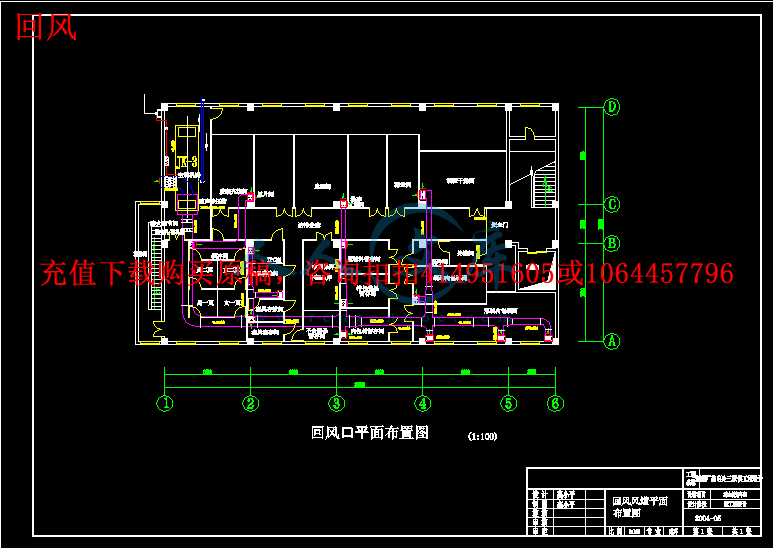
