摘 要
铁丝缠绕包装机的设计主要包括铁丝包装机缠绕盘机构的设计,滚筒机构的结构设计,及安装上述两部分机构的机架部分的设计,以及对这些机构中主要受力元件进行受力分析。本设计主要对铁丝包装机的缠绕盘机构部分进行设计,包括带动缠绕盘转动的传动方案的设计和在传动方案中包含的主要零部件的选择、设计及校核及电动机的选择。另外,还对主要的轴,轴承,齿轮,带轮,螺钉等零件运用Pro-e完成其三维图的绘制,并对其进行装配,最后完成对铁丝缠绕包装机的设计。最终设计出成本较低,可靠性强,使用寿命长,节省劳动力,节省时间的自动铁丝缠绕包装机。
关键词: 铁丝缠绕包装机,缠绕盘,电动机, Pro-e绘图
The design of packaging machine about the iron wire circle
------The design of winding wire ring
Abstract
Wire winding machine designed packaging includes all the packing machine wire winding plate body design, roller structure design, and installation of the above two parts, body parts of the rack design, and of these institutions by force by the force components analysis. The main design of the packaging machine wire winding plate of the body parts of the design, including rotating disk drive winding drive program design and program in the drive that contains the main components of the selection, design and verification and motor choice. In addition to the main shaft, bearings, gears, pulleys, screws and other parts to use Pro-e to complete its three-dimensional mapping, and its assembly, the final completion of the winding wire packaging machine design. Ultimately lower the cost of design, reliability, long life, saving labor, time-saving automatic packing machine wire winding.
Keywords: Packing wire winding machine, Winding plate, Motor, Pro-e Drawing
目 录
1 绪论1
2 设计要求1
3铁丝包装机缠绕盘传动方案设计2
3.1铁丝包装机传动方案选择2
3.2铁丝包装机缠绕盘传动方案示意图2
3.3电动机的选择3
3.3.1选择电动机的类型3
3.3.2选择电动机的功率3
3.3.3确定电动机的转速及类型4
4铁丝包装机主要传动零件的设计5
4.1锥齿轮的设计5
4.2同步带及同步带轮的设计9
4.3轴的结构设计及受力分析10
4.3.1轴的结构设计10
4.3.2轴的受力分析11
4.3.3校核轴的强度12
5装配图及其他主要零件图13
6 结束语15
致谢15
参考文献16
1 绪论
机械设计(machine design),根据使用要求对铁丝缠绕包装机的工作原理、结构、运动方式、力和能量的传递方式、各个零件的材料和形状尺寸、润滑方法等进行构思、分析和计算并将其转化为具体的描述以作为制造依据的工作过程。
传统的铁丝包装存在着一些缺点:一是包装的方法老旧,二是包装浪费时间,还有就是包装的手动占很大的部分,造成劳动力的浪费,所以现存的铁丝包装机不能快速高科技节省劳动力的对铁丝进行自动化包装,因此我们就此对铁丝包装机进行设计.
经本设计完成的铁丝缠绕包装机能完成铁丝的自动包装,并且能达到节省劳动力,节省时间,从而利用高新科技达到节省成本,完成铁丝的缠绕包装.这样使包装机的使用寿命也能大大加强,铁丝缠绕包装的可靠性也会大大加强,达到社会上要求的标准,并且提高社会生产力.
目前在我国,受经济条件和技术水平的限制,手动和半自动进行铁丝缠绕包装仍是我国中最常用的铁丝包装方式。由于投资成本较低,我国劳动力丰富.且操作简单,所以在中小型企业获得了广泛应用。
随着铁丝包装技术的不断发展,传统的铁丝包装技术难以满足现今铁丝缠绕包装要求。国外普遍利用自动铁丝包装机等来替代老旧的铁丝包装技术,这种自动铁丝缠绕包装在工业发达国家已开始推广使用。在国内铁丝缠绕包装行业中,近年来开始尝试采用自动机械铁丝包装机代替传统的手工铁丝包装的方法,目前还没有推广。自动铁丝缠绕包装机在完成铁丝包装技术的同时也能节能环保,同时使用时间长久.但是鉴于它的设备体积大、功率因数低、费用较高等原因,在中小型铁丝缠绕工厂上多不用。把传统的铁丝包装机改成更加节能,占地小.功率高.铁丝包装质量优良.价格合理包装机器是铁丝包装机发展的一个重要项目。
Pro/Engineer是一套由设计至生产的机械自动化软件,是新一代产品造型系统,是一个参数化、基于特征的实体造型系统,并且具有单一数据库功能。Pro/Engineer是采用参数化设计的、基于特征的实体模型化系统,工程设计人员采用具有智能特性的基于特征的功能去生成模型,如腔、壳、倒角及圆角.基于此绘图软件的这些优点,本次设计使用PRO-E绘制设计图.
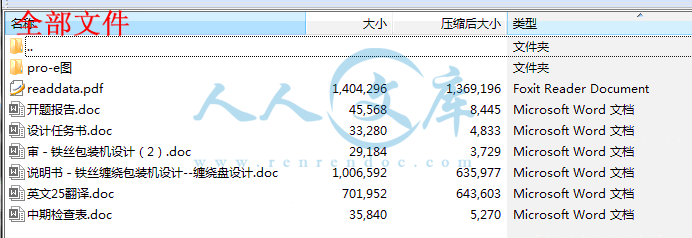
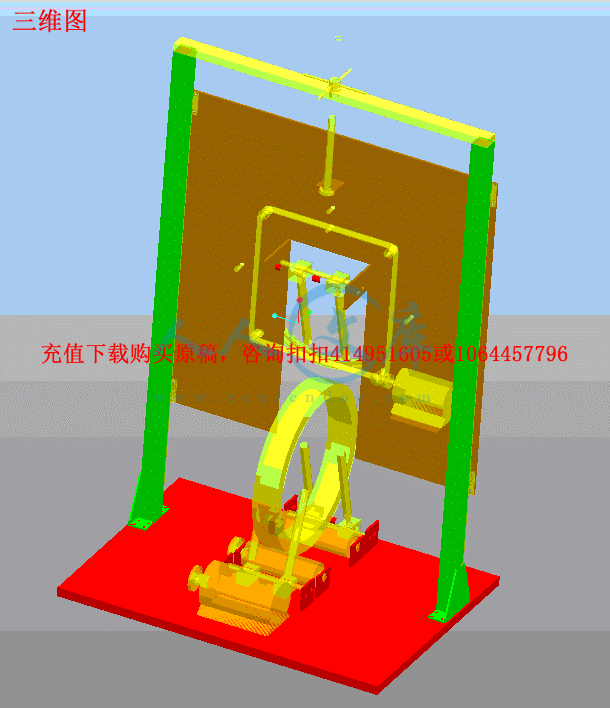
