目 录
摘要2
Abstract:3
第一章 绪论4
§1.2 机械无级变速器的特征和应用5
§1.3机械无级变速器的选用和润滑密封7
§1.4 本文的主要内容及要求9
第二章摩擦无级变速器的机械特性加压装置和调速机构10
§2.1 机械特性10
§2.2 调速操纵机构11
§2.3 加压装置12
第三章摩擦式无级变速器设计说明和计算过程13
§3.1 摩擦机械无级变速器的工作原理13
§3.2 摩擦无级变速器的特点14
§3.3 锥轮的设计与计算14
§3.4 钢环的设计与计算18
1、钢环尺寸和参数的确定18
2、强度验算21
§3.5 轴系的设计21
§3.6 轴的结构设计22
第四章 主要零件的校核24
§4.1 .输出,输入轴的校核24
§4.2 . 轴承的校核25
总 结26
致 谢27
参考文献资料28
附 录: 文献翻译………………………………………………………29
摩擦式机械无级变速器结构设计
摘要
在某种控制的作用下,使机器的输出轴转速可在两个极值范围内连续变化的无级变速器传动随着机械、材质及加工工艺的高速发展和其需求量日益增多而得到广泛应用和发展。无级变速器的主动和从动两根轴通过传递转矩的中间介质(机械构件、流体、电磁流等)把两根轴直接或间接地联系起来并传递动力。当对主、从动轴的联系关系进行控制时,则两轴间的传动比发生变化(在两极值范围内连续而任意地变化)。用机械构件作为中间介质的为机械无级变速器,其包括摩擦式和脉动式。无级变速器与定传动比传动及有级变速传动(它只有有限的几种传动比)相比,其优点是能够根据工作需要在一定范围内连续变换速度,以适应输出转速和外界负载变化的要求,摩擦式机械无级变速器依靠传动元件之间的摩擦进行传动,钢材材质、加工工艺水平和润滑油料品质等因素是摩擦式机械式无级变速器不断发展的重要保证。本文通过查阅相关的诸多文献和书籍手册等进行钢环式无级变速器原理及其结构、变速原理的传动结构的实现的研究,并对摩擦式机械无级变速器进行结构设计,可直接作为设计文件或指导文件进行生产加工。
关键词:无级变速器;摩擦式;传动;润滑;
The structure design of CVT machine of friction type
Abstract:
Under the action of some kind of control which can make the output of the machine spindle speed in two extreme CVT within the framework of the continuous variation of the transmission with the high-speed development of machinery, materials and processing technology and its demand is growing and is widely used and CVT transmission of the driving and driven by passing two shaft torque in the middle of the medium (mechanical components, fluid, electromagnetic flow, etc.), the two shaft linked directly or indirectly, and transfer power.When were related to the Lord, driven shaft to control, is the ratio between the two axis change (within the scope of the two extreme consecutive and arbitrarily change).With mechanical components as a medium for mechanical CVT, among which include friction and pulsation.CVT and constant transmission ratio transmission and continuously variable transmission (it's only a limited number of transmission ratio), compared to its advantage is the ability to work according to the need to continuous transformation rate within a certain scope, to adapt the demand of output speed and external load, the friction type CVT depend on mechanical transmission device for transmission, the friction between the steel material, processing technology level and the quality of lubricating oil is factors such as friction type mechanical stepless transmission the important guarantee of continuous development.This article through the consult literature and books, manuals, etc for the steel ring type stepless transmission principle and structure, the realization of the principle of variable speed drive structure research, and the friction type mechanical CVT structure design, can be directly as a guide for design documents or files for production and processing.
Keyword:CVT;Friction type;Transmission;Lubrication;
第一章 绪论
§1.1机械无级变速器的发展背景及现状
无级变速器在输入转速不变的情况下,能实现输出轴的转速在一定范围内连续变化,以满足机器或生产系统在运转过程中各种不同工况的要求;其结构特征主要是由变速传动机构、调速机构以及加压装置或输出机构三部分组成,无级变速器分为机械无级变速器,液压传动无级变速器,电力传动无级变速器三种。本设计任务要求把无级变速器安装在自行车上,采用机械无级变速器,本文主要介绍机械无级变速器的发展概况。
机械无级变速器最早是出现在十九世纪九十年代,到二十世纪三十年代逐渐开始发展起来,由于材质与工艺等方面的技术发展缓慢导致了无级变速也发展迟缓,随着现代科学技术的高速发展,尤其是七十年代以后,随着先进的冶炼和热处理技术,精密加工和数控机床技术以及牵引传动理论与高品质油的出现和发展,解决了许多研制和生产无级变速器的限制因素,同时,生产工艺流程实现机械化、自动化以及机械工作性能的改进,都促进了无级变速器的快速发展,在不同的领域,大量机器设备需要采用无级变速,尤其在汽车行业需求更为突出,因此,机械无级变速器得到广泛迅速的发展。国内无级变速器大约在二十世纪六十年代前后起步,当时主要是作为专业机械配套零部件,用于专业机械厂进行仿制和生产,如用于纺织机械的齿链式,化工机械的多盘式以及切削机床的Kopp型无级变速器等,但品种规格不多,产量不大,年产量仅数千台。直至八十年代中期以后,随着国外先进设备的大量引进,工业生产现代化及自动流水线的迅速发展,对各种类型机械无级变速器的需求大幅度增加,专业厂才开始建立并进行规模化生产,一些高等院校也开展了该领域的研究工作,又经过二三十年的发展,由于真空冶炼技术的应用、超精密工艺的日臻完善以及润滑油料摩擦特性方面的改进,使得机械无级变速器已经系列化生产,并以通过部件的形式供应于市场,近十年来,由于能源危机的出现,人们对机械无级变速器在交通运输工具上应用又进行了大量的研究,并取得了一定的成效。
摩擦式无级变速器是机械无级传动系统中的常用部件之一,它依靠摩擦力传递转矩和运动,所以它基本上由传递运动和动力的摩擦变速传动机构、保证产生摩擦力所需的加压装置和实现变速的调速机构三部分组成。近年来摩擦式无级变速器在国外获得了较快的发展,其传动功率从几十到几千瓦,并可在接近于0~10000转/分的输出速度下工作,效率约为75%到95%,与传统的齿轮传动、链传动及皮带传动相比,不仅可实现无级变速而且传动零件的形状比较简单无需很高的精度因此加工费用较低,现已获得人们普遍地重视。目前国内使用的摩擦式无级变速装置大多属于直接传动式、中间元件式、行星传动式三种类型:主、从动摩擦元件直接接触传动的直接传动式,主、从动元件通过中间元件进行传动的中间元件式,以及中间元件作行星运动的行星传动式。调速结构则分为一元件相对于另一元件沿接触面移动和转动(或偏转)两种形式。因此,合理地设计传动机构的结构和形式是提高传动构件受力的均匀性和传动平稳性及效率的关键,其速比的变换则通过改变主动轮从动轮和中间构件三者的相对位置来获得,这些摩擦式无级变速器的缺点主要是传动效率低、运行中难以保持稳定的速比、变速操作困难在高速运行时变速易使传动零件过早的磨损以及对于低速大扭矩传动传动装置的体积与重量较大。
目前对摩擦无级变速器的传动机理研究得并不充分,有待深入研究。选择和发展新的润滑剂,以进一步提高摩擦拖动率;研究具体结构设计的合理性及其优化问题,突破瓶颈,实现无级变速器新的突破,真正做到广泛应用和产业化。
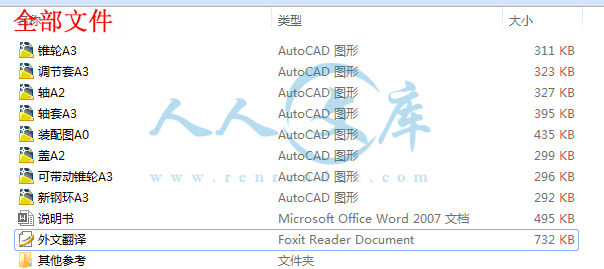

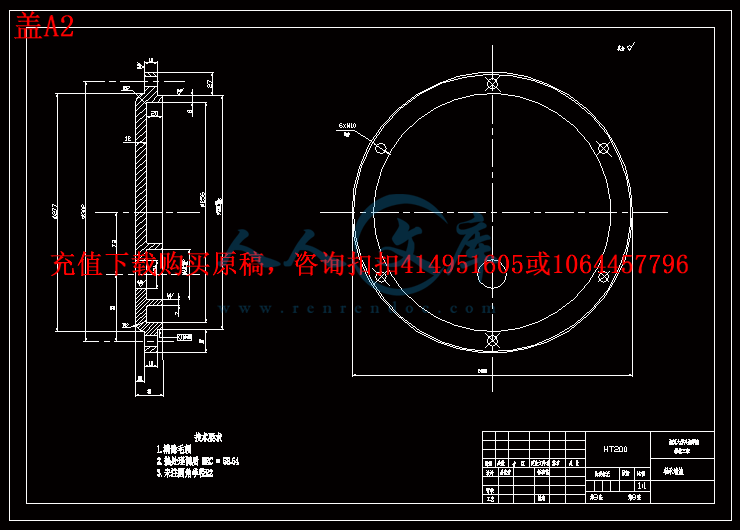
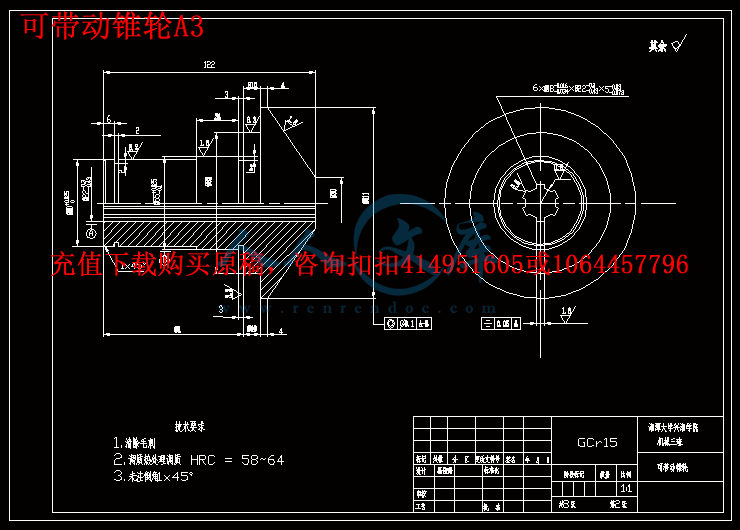
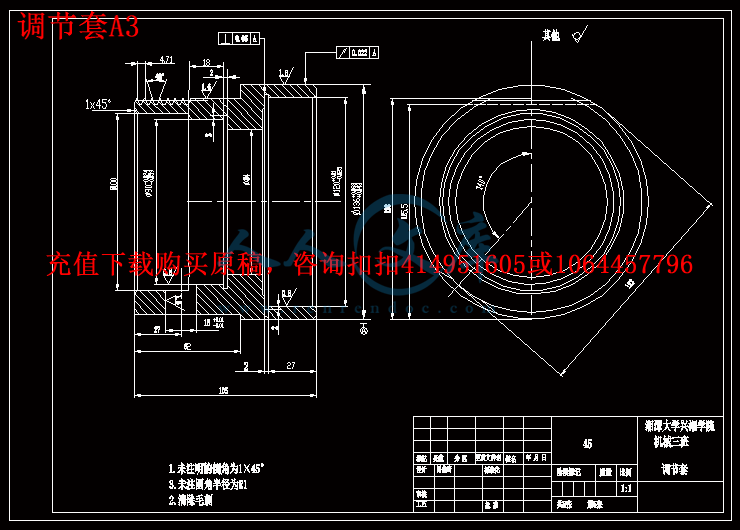
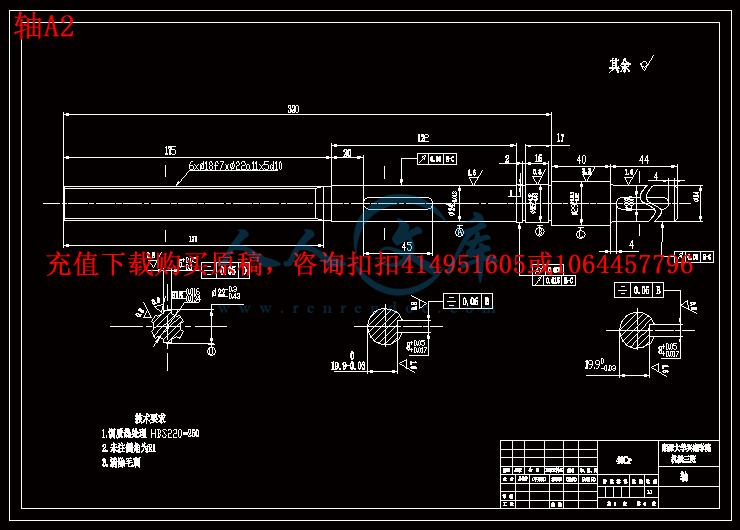
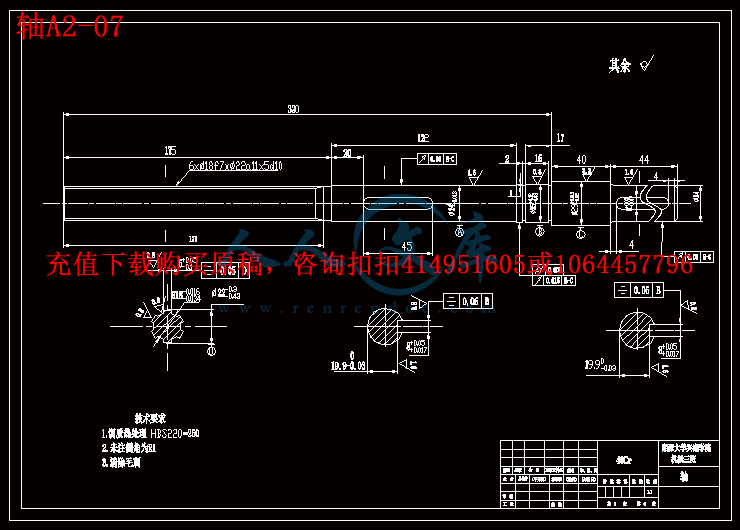
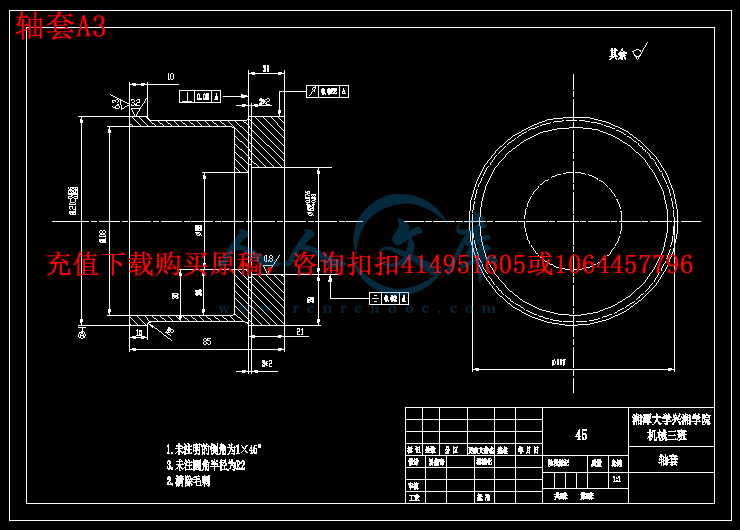

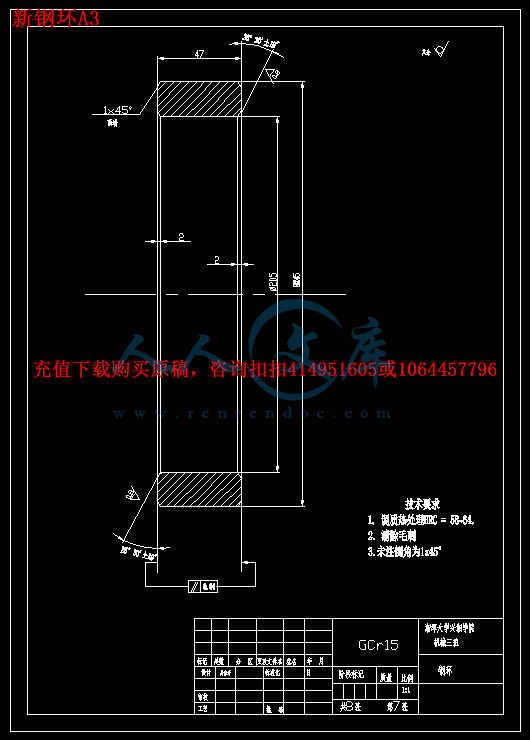