大学生方程式赛车设计(制动与行走系统设计)
大学生方程式赛车制动与行走系统设计【优秀方程式赛车课程毕业设计含7张CAD图纸】
【51页@正文17700字】【详情如下】【需要咨询购买全套设计请加QQ1459919609】
A1-后轮主销-右.dwg
A2-前轮毂--右.dwg
A2-后轮毂--右.dwg
前轮轴装.dwg
后轮轴装.dwg
大学生方程式赛车制动与行走系统设计.doc
封皮.doc
液压系统布局图.dwg
翻译
踏板总成.dwg
大学生方程式赛车设计(制动与行走系统设计)
摘 要
Formula SAE 赛事1980年在美国举办第一次比赛,现在已经是为汽车工程学会的学生成员举办的一项国际赛事,其目的是设计、制造一辆小型的高性能方程式赛车,并使用这辆自行设计和制造的赛车参加比赛。中国大学生方程式赛车比赛的组织与开展始于2010年,至今已成功举办了三届。
本文主要阐述了在中国大学生方程式汽车大赛组委会制定的规则下,如何设计一辆Formula SAE 赛车的制动系统。设计采用的是前盘后盘的液压双回路制动系方案。它的工作原理是利用与车身(或车架)相连的非旋转元件和与车轮(或传动轴)相连的旋转元件之间的相互摩擦来阻止车轮的转动或转动趋势,亦即由制动踏板的踏板力通过推杆和主缸活塞,使主缸油液在一定压力下流入轮缸,并通过轮缸活塞推使制动衬片夹紧制动盘产生摩擦力矩,从而产生制动力,使车轮减速直至停车。
由于赛车本身质量较小,很多地方不能按常规的设计方法进行设计,我主要采用了市场调研的方法,先选取一些类似的车型,依据它们的制动系统结合赛车的实际情况反复验证,通过极限算法计算出完全制动时制动盘的最小尺寸。同时在极限工况下对几个危险截面的零件的强度进行了校核,使其满足要求。同时利用UG软件进行了建模,以辅助后续工作的顺利进行。
关键词:Formula SAE,赛车,制动,校核
FORMULA RACING BRAKE AND WALKING
SYSTEM DESIGN
ABSTRACT
Formula-SAE launched in the USA in 1980, Formula-SAE is now an international competition for Society of Automotive Engineers student members to form teams for the purpose of designing, building and competing in a small high-performance race car.
The article discusses how to design a Formula SAE car's braking system。My design uses a dual hydraulic disc front after-hours circuit brake system program.How does it work is using the friction between the non-rotating components which are connected to the body (or frame) and the rotation components which are connected to the wheels (or drive shaft) to prevent wheel spin or turn the trend.
That is, from the brake pedal for pedal force by Rod and master cylinder piston, the master cylinder oil flows into the wheel cylinders under some pressure, And through the wheel cylinder piston that brake lining clamping brake friction torque, so as to produce the braking force to the wheels to speed up to park.
As the quality of the car itself is small, many places are not design by the conventional method ,I mainly uses the market research methods, firstly I selected some similar models ,combinating their braking systems and the actual car,I repeatedly verified. by the limit of complete braking algorithm the minimum size of the brake disc.At the same time in extreme conditions,I verified the strength on several dangerous section of parts ,to meets the requirements. At the same time I made use of UG software modeling.
KEY WORD: Formula SAE, racing, brake,design
目 录
第一章 概述1
§1.1制动系统设计的意义1
§1.2制动系统研究现状1
§1.3大学生方程式赛车制动规则和要求2
§1.3.1 制动系统概况2
§1.3.2 制动测试2
第二章 制动系统方案论证分析与选择3
§2.1 制动器形式方案分析3
§2.1.1 鼓式制动器3
§2.1.2 盘式制动器4
§2.2 制动驱动机构的机构形式选择5
§2.2.1 简单制动系6
§2.2.2 动力制动系6
§2.2.3 伺服制动系7
§2.3 液压分路系统的形式的选择7
§2.4 液压制动主缸的设计方案9
第3章 制动系统设计计算11
§3.1 制动器主要零部件的结构设计11
§3.2 制动系统主要参数数值11
§3.2.1 同步附着系数的分析12
§3.2.2 地面对前、后轮的法向反作用力12
§3.2.3 盘式制动器主要参数确定13
第四章 盘式制动器的设计计算16
§4.1 盘式制动器制动力矩的计算16
§4.2制动力与制动力分配系数17
§4.3 制动器热容量和温升的核算21
§4.4摩擦衬片磨损特性的计算22
第五章 液压制动驱动机构的设计计算24
§5.1 制动轮缸直径与工作容积24
§5.2 制动主缸直径与工作容积25
§5.3 制动踏板力与踏板行程26
§5.4 制动性能计算28
第六章 行走系统的设计29
§6.1 汽车行驶系统概述29
§6.1.1 轮毂的设计30
§6.1.2 立柱的设计30
§6.2制动盘座体的设计32
§6.2.2 销的校核34
§6.2.3 花键的校核38
第七章 结 论41
参考文献42
致 谢 44
第一章 概 述
§1.1 制动系统设计的意义
汽车是现代交通工具中用得最多、最普遍、也是运用得最方便的交通工具。汽车制动系统是汽车底盘上的一个重要系统,它是制约汽车运动的装置,而制动器又是制动系中直接作用制约汽车运动的一个关键装置,是汽车上最重要的安全件。汽车的制动性能直接影响汽车的行驶安全性。随着公路业的迅速发展和车流密度的日益增大,人们对安全性、可靠性的要求越来越高,为保证人身和车辆安全,必须为汽车配备十分可靠的制动系统。本次毕业设计题目为大学生方程式赛车制动系与行走系统设计。
§1.1.1 制动系统的重要性
汽车作为陆地上的现代重要交通工具,有许多保证其使用性能的大部件,即所谓“总成”组成,制动系就是其中一个重要的总成。它既可以使行驶中的汽车减速,又可以保证停车后的汽车驻留原地不动。由此可见汽车制动系对于汽车行驶的安全性和停车的可靠性起着重要的保证作用。
当今,随着高速公路网的不断扩展、汽车车速的提高以及车流密度的增大,对汽车制动系的工作可靠性要求显得日益重要。因为只有制动性能良好、制动系工作可靠的汽车才能充分发挥出其高速行驶的动力性能并保证行驶的安全性。由此可见,制动系是汽车非常重要的组成部分,从而对汽车制动系的结构分析与设计计算也就显得非常重要了。
参考文献
[1] 王望予.汽车设计[M].第四版.北京:机械工业出版社,2004:12-16.
[2] 陈家瑞.汽车构造下册[M].第二版.北京:机械工业出版社,2005:42-45.
[3] 余志生.汽车原理[M].北京:机械工业出版社.第四版,2006:89-96.
[4] 刘惟信.汽车设计[M].第一版.北京:清华大学出版社,2001:24-26.
[5] 何小柏.机械设计手册新版[M].第一卷. 北京:机械工业出版社,2006:32-33.
[6] 过学迅.汽车设计[M].第一版.北京:人民交通出版社,2005:47-48.
[7] 周明衡.离合器、制动器[M]. 第一版.北京:化工工业出版社,2003.5:65-75.
[8] 张展.联轴器、离合器、制动器设计选用手册[M].北京:中国劳动社会保障出版社,1999:52-54.
[9] 李凤平,张士庆.机械制图[M].第三版.沈阳:东北大学出版社,2003:35-38.
[10] 李军.ADAMS实例教程[M].北京:北京理工大学出版社,2002:15-16.
[11] 濮良贵,纪名刚.机械设计[M] 第七版.北京:高等教育出版社,2004:214-225.
[12] 赵贵范,郑德林,郭岩.汽车设计[M].哈尔滨:哈尔滨工业大学出版社,1994:144-162.
[13] 吉林工业大学汽车教研室编.汽车设计[M].北京:机械工业出版社,1981:62-65.
[14] 吴宗泽.机械设计使用手册[M].北京:化学工业出版社,2001:227-230.
[15] [日]自动车技术会,小林明等.汽车工程手册[M] 第二分册.北京:机械工业出版社,1984:421-426.
[16] 徐灏.机械设计手册(3)[M].北京:机械工业出版社,1995:514-518.
[17] 金国栋.汽车概论[M].北京:机械工业出版社,2000:135-140.
[18] [美]L.鲁道夫编.汽车制动系统的分析与设计[M].张蔚林,陈名智译.北京:机械工业出版社,1985:54-58.
[19] [美]L.埃克霍恩,D.克林恩乔克著.汽车制动系统[M].北京:机械工业出版社,1998:32-35.
[20] 吴社强,吴政清,姜斯平.汽车构造[M].上海:上海科学技术出版社,2003:224-226.
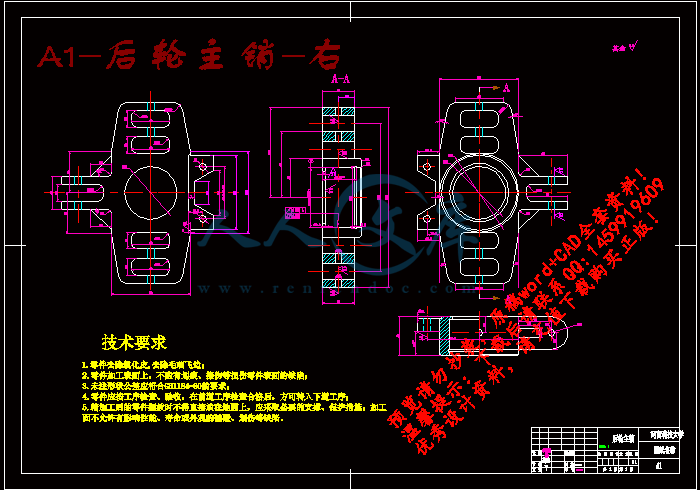



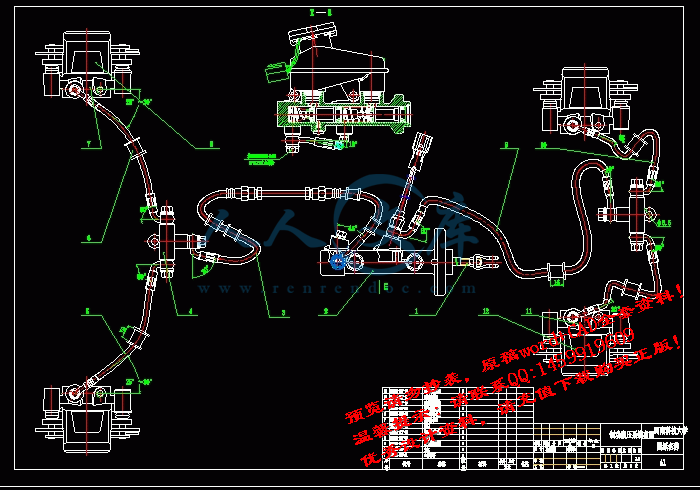
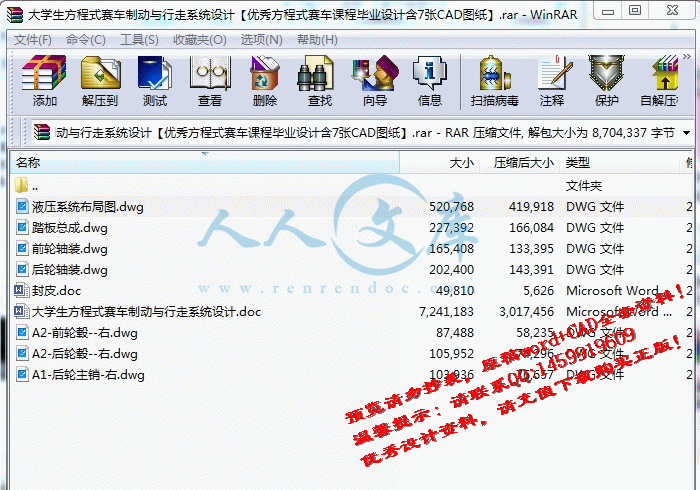
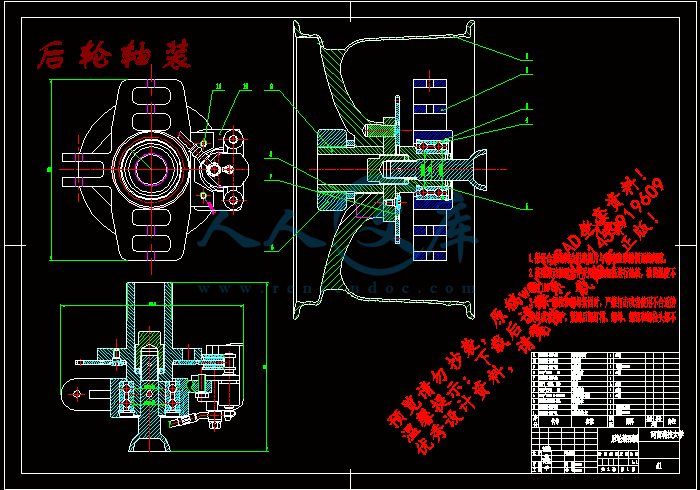

