大学生方程式赛车设计(总体设计)
FSAE大学生方程式赛车总体设计【优秀方程式赛车课程毕业设计含UG三维建模及2张CAD图纸】
【带开题报告+外文翻译】【60页@正文21000字】【详情如下】【需要咨询购买全套设计请加QQ1459919609】
cad图集(2张).dwg
FSAE大学生方程式赛车总体设计.doc
UGsanweijianmo
开题报告.doc
中英文翻译
大学生方程式赛车设计(总体设计)
摘 要
本次毕业设计为期两个多月,进行了方程式赛车的总体设计。在设计中,主要运用了对比分析的方法,各项参数通过优化设计和UG、MATLAB等进行优化。
初期阶段,我们根据2012年大学生方程式汽车大赛规则确定了赛车整体布置方案,并进行论证与分析,初步确定赛车主要参数。通过计算与对比,确定发动机型号,初选传动系最大传动比、最小传动比。
中期阶段,我们设计中使用UG7.0三维软件对各个零部件总成进行建模和整体装配,并进行悬架、转向的运动干涉分析。利用发动机动力特性曲线特点,用MATLAB软件绘制出赛车驱动力-行驶阻力平衡图、加速度曲线图等,并详细计算赛车燃油经济性。
最后阶段,利用UG7.5进行导出赛车总体布置二维工程图,并制成总体参数表,并将第三代赛车与第二代赛车进行对比分析。对于考虑到的实际生产中可能发生变化的悬架、车架和转向部件,预留方案。
通过本次毕业设计,了解和掌握了对汽车进行总体设计的步骤和方法,巩固了本专业的所学的专业知识,增强了搜集资料、整合资料的能力,这些将为我毕业以后从事汽车设计工作打下良好的基础。
关键词:FSAE,总体参数,参数确定,总布置,赛车动力性,燃油经济性
FORMULE SAE (OVERALL DESIGN)
ABSTRACT
For two months, My graduation design is the overall design of the formula racing. we used the contrast analysis method mainly in the design, through optimizing the parameters optimization design and optimization of UG MATLAB, etc.
Initial stage, we according to 2012 auto contest rules determine college equation overall layout of the car, and the demonstration and analysis, the main parameter is determined primarily racing. Through calculation and comparison, sure engine type, primaries drivetrain maximum transmission ratio, minimum transmission.
The intermediate stage, we design UG7.0 3d software used in various parts of assembly for modeling and whole assembly, and suspension, steering movement interference analysis. Use of engine power characteristic curve characteristic, MATLAB software mapped drive car driving forces - resistance balance figure, acceleration curve, and etc, and detailed calculation racing fuel economy.
The final stages UG7.5 are derived by car, general layout, and two-dimensional engineering graphics overall parameter table, and made the third generation and the second generation racing cars are compared and analyzed. For considering the actual production of may change suspension, frame and steering parts, obligate scheme.
Through the graduation design, I understand and master the overall design of car of the steps and method, the professional knowledge of professional knowledge, enhance the data collection and integration of information, these ability after my graduation will be engaged in car design lay a good foundation for the job.
KEY WORDS: FSAE, general parameters, parameter identification, general arrangement,the car power, fuel economy
目 录
第一章 FSAE赛车概述1
§1.1 FSAE赛车起源1
§1.2 FSAE赛车现状2
§1.2.1 国际赛车概述2
§1.2.2 国内及我校赛车概述2
§1.3 FSAE 总体设计概述3
§1.3.1 汽车设计的方法及过程3
§1.3.2 FSAE赛车的技术要求4
§1.3.3 我校第三代赛车设计目标4
§1.3.4 FSAE赛事意义5
第二章 FSAE赛车总体设计7
§2.1 总体设计目标7
§2.2 赛车目标参数的初步确定8
§2.2.1 发动机选择9
§2.2.2 轮胎的选择10
§2.2.3 传动系最小传动比的确定11
§2.2.4 传动系最大传动比的确定11
§2.3 赛车发动机选型12
§2.4 赛车主要设计参数的确定13
§2.4.1 尺寸参数13
§2.4.2 质量参数14
§2.4.3 性能参数15
§2.5 赛车各系统设计17
§2.5.1 悬架系统设计18
§2.5.2 转向系统设计19
§2.5.3 制动系统设计19
§2.5.4 电器系统设计21
§2.5.5 车身设计23
§2.5.6 车架设计23
第三章 赛车动力性与燃油经济性25
§3.1 赛车的动力性25
§3.1.1 动力性的评价指标25
§3.1.2驱动力—行驶阻力图25
§3.1.3 汽车的加速能力28
§3.1.4 动力特性图29
§3.1.5 功率平衡31
§3.2 燃油经济性32
第四章 赛车总体布置33
§4.1 整车布置的基准线(面)-零线的确定34
§4.2 各部件的布置35
§4.3 总体设计参数表38
第五章 结 论40
参考文献41
致 谢42
第一章 FSAE赛车概述
Formula SAE 赛事1980年在美国举办第一次比赛以来,现在已经成为汽车工程学会的学生成员举办的一项国际赛事,其目的是设计、制造一辆小型的高性能方程式赛车,并使用这辆自行设计和制造的赛车参加比赛。
出于此项比赛的宗旨是让学生针对业余高速穿障的车手开发制造一个原型车,该原行车应该具备有可小批量生产的能力,并且原型车的造价要低于25,000 美元。这项竞赛包含有3 个最主要的基本元素,分别是:工程设计、成本控制以及静态评估、单独的动态性能测试、高性能的耐久性测试。
Formula SAE 赛事的主要参与者通常都是来自高校的学生组成的车队。现在在美国、欧洲和澳大利亚每年都会举办Formula SAE 比赛。Formula SAE 向年轻的工程师们提供了一个参与有意义的综合项目的机会。由参与的学生负责管理整个项目,包括时间节点的安排,做预算以及成本控制、设计、采购设备、材料、部件以及制造和测试。
§1.1 FSAE赛车起源
第一届SAE Mini Baja比赛于1976 年举办,并且迅速成为一个地区性的年度比赛。比赛由三个评判标准组成,即静态比赛:设计、成本、陈述;接着是各自的性能竞赛2项目。 Mini Baja比赛重点强调了底盘的设计,因为每个队伍都使用一个8匹马力的引擎。在过去的20 多年里,SAE Mini Baja 的成功超乎了每个人的预期。
参考文献
[1] 张文春,汽车理论,机械工业出版社,2007.11,22-44
[2] 刘惟信,汽车设计,清华大学出版社,2001.7
[3] 陈家瑞,汽车构造(第二版下册),机械工业出版社,2005.1,98-116
[4] 王望予,汽车设计(第四版),机械工业出版社,2009.1,1-50
[5] 张洪欣,汽车设计,机械工业出版社,1983.3, 7-47
[6] 自动车技术会 小林 明,汽车工程手册(第二分册),机械工业出版社,
1984.4, 386-419
[7] 编辑委员会 ,汽车工程手册摩托车篇,人民交通出版社,2001.3 ,170-188
[8] 机械设计手册编委会,机械设计手册新编,机械工业出版社,2004.8,16-44--16-66
[9] 中国汽车技术研究中心,汽车设计标准资料手册(金属篇),河北抚宁印刷,1994.10, 357-358
[10] 长春汽车研究所编.悬架设计.汽车技术,1973,第五期 ,34-36
[11] 东北大学组编.机械零件·设计手册.,冶金工业出版社,1994,268-281
[12] 吴宗泽.机械设计实用手册.,化学工业出版社,2001,
[13]王昆,何小柏,汪信远.机械设计基础课程设计.,高等教育出版社,2004
[14] 汽车工程手册编委会编.汽车工程手册.设计篇.,人民交通出版社,2001
[15] 汽车工程手册编委会编.汽车工程手册.基础篇.,人民交通出版社,2001
[16] 神龙汽车有限公司编著.中国轿车丛书:富康.,北京理工大学出版社,1998
[17] 吴子牛,王兵,周睿,空气动力学(上册),清华大学出版社,2007.1
[18] 常思勤,汽车动力装置,机械工业出版社,2006.2
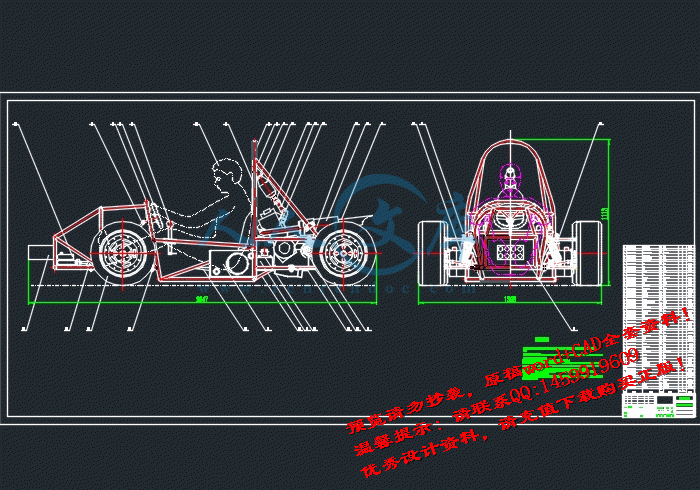

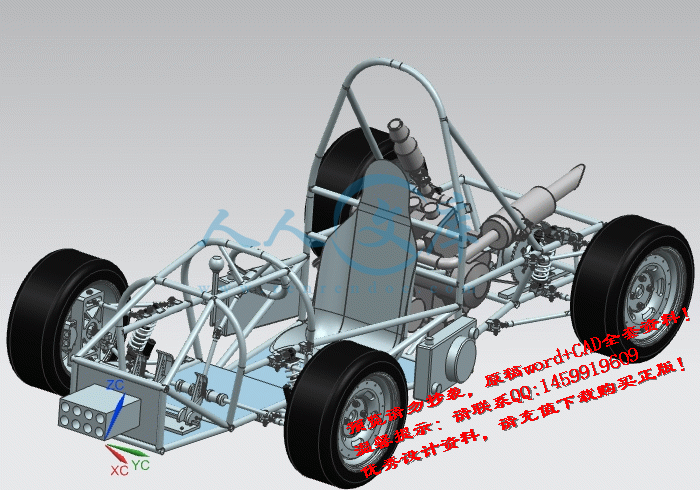
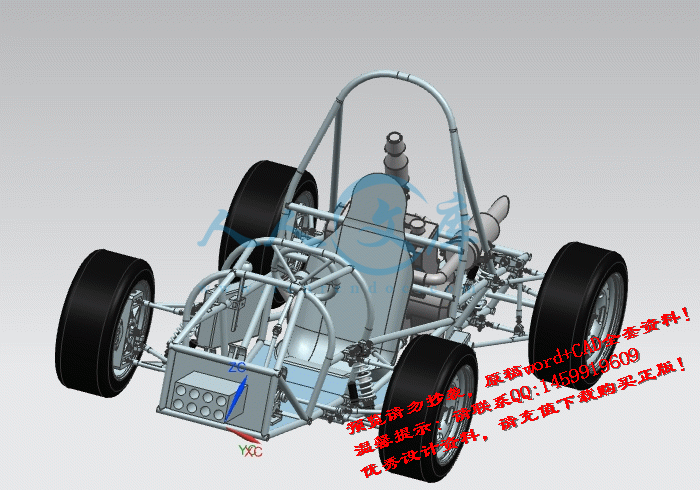

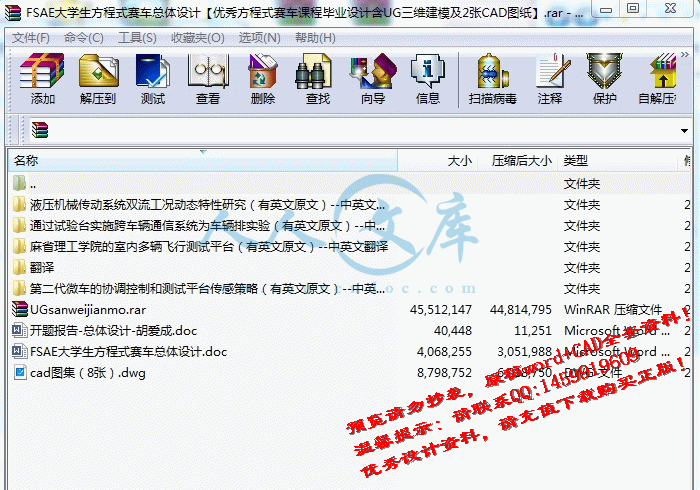