




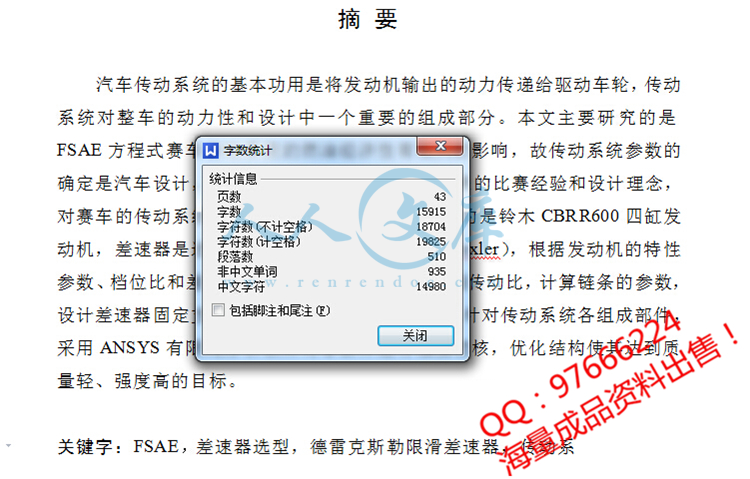
!【详情如下】【汽车车辆工程类课题】CAD图纸+word设计说明书.doc[15000字,43页]【需要咨询购买全套设计请加QQ97666224】.bat
差速器 总成.dwg
链轮法兰盘.dwg
链轮防护罩.dwg
齿圈.dwg
三维图
开题报告.doc
设计说明书.doc[15000字,43页]
翻译
摘 要
汽车传动系统的基本功用是将发动机输出的动力传递给驱动车轮,传动系统对整车的动力性和设计中一个重要的组成部分。本文主要研究的是FSAE方程式赛车传动系统的燃油经济性有很大的影响,故传动系统参数的确定是汽车设计,基于我院LS Racing车队三年来的比赛经验和设计理念,对赛车的传动系统进行优化和改造。本赛车选用的是铃木CBRR600四缸发动机,差速器是选用德雷克斯勒限滑差速器(Drexler),根据发动机的特性参数、档位比和差速器的工作原理,选择合适的链传动比,计算链条的参数,设计差速器固定支架,合理的布置整个传动系统。针对传动系统各组成部件,采用ANSYS有限元分析软件对零部件进行强度校核,优化结构使其达到质量轻、强度高的目标。
关键字:FSAE,差速器选型,德雷克斯勒限滑差速器,传动系
Formula SAE of china (transmission and final drive system)
ABSTRACT
The basic function of auto transmission system is transfer engine power to drive wheels .The transmission system has a great influence in dynamic performance .So the parameter of drive system is one of the important part in automobile design .The article mainly research is drive system design of FSAE racing car. The car drive system optimization and transformation is based on LS Racing team competition experience and design concept in the past three years .The racing car engine is choose SUZUKI GSX-R600 have four cylinder engine .The differential is choose Drexler limited slip differential. According to the characteristics of the engine parameters, gear ratio and differential working principle ,that choose the right chain transmission ratio, calculation chain parameters, design the differential fixed bracket, reasonable arrangement of the drive system. Aimed at the transmission system components, use the ANSYS finite element analysis to check intensity of the parts, that optimize structure enables it to achieve light weight, high strength goal.
KEY WORD: FSAE, Differential selection, Drexler limited slip differential, the ANSYS finite element analysis
目 录
第一章 大赛背景及发展现状1
§1.1 赛事背景1
§1.2 国外情况2
§1.3 国内情况2
第二章 绪论4
§2.1 传动系统的组成4
§2.2 传动系统的功能实现4
§2.3 FSAE大学生方程式赛车传动系统的特点5
§2.4 中国大学生方程式汽车大赛(FSC)传动规则和要求6
§2.5 本次传动系统设计任务6
第三章 赛车动力总成的选择与布置7
§3.1 整车参数与主要结构7
§3.2 赛车动力性计算9
§3.2.1 主减速比确定9
§3.2.2 赛车驱动力的计算9
§3.3 赛车动力性的验证与优化11
§3.3.1 拟合外特性曲线图11
§3.3.2 驱动力-行驶阻力平衡图12
§3.3.3 发动机功率-行驶阻力功率平衡图12
§3.3.4加速度特性曲线13
§3.3.5 动力因数图14
§3.4 传动方式确定14
第四章 动力总成与车架的连接及与驱动轮的传动设计17
§4.1 差速器固定17
§4.2 车轮法兰设计19
§4.3 大小链轮的设计20
§4.3.1 链轮齿数 、 和传动比i的计算与确定20
§4.3.2齿数的选取原则20
§4.3.3 传动比的确定20
§4.3.4 链轮的计算与选取20
§4.4 差速器的设计与选择25
§4.4.1 差速器原理25
§4.4.2 差速器的分类26
§4.4.3 方程式赛车的差速器结构选择30
§4.4.4 差速器选用说明31
§4.5 万向节的选择31
§4.5.1 万向节的工作原理32
§4.5.2 等速万向节的分类32
§4.6 此次设计选用的万向节类型35
参考文献37
结束语38
第一章 大赛背景及发展现状
随着我国汽车工业的崛起,赛车文化日益蓬勃发展,同时为号召十二五时期党中央提出的科技强国口号,在这样一个背景下,2010年首届中国大学生方程式汽车大赛在上海国际赛车场隆重举办。随后的第二届中国大学生方程式汽车大赛的引擎在此轰鸣在上海国际赛车场,规模比前一届扩大将近一倍,吸引了包括一支海外车队——慕尼黑工业大学在内的一共34支队伍参加。在此,我选择FSAE赛车动力及传动总成布置设计为我毕业设计的题目,希望通过此次设计优化让我校的赛车驰骋在2012年上海赛车场。