CA6140车床后托架831001机械加工工艺及钻M6底孔及攻螺纹和钻6孔的钻床夹具设计
收藏
资源目录
压缩包内文档预览:(预览前20页/共24页)
编号:475994
类型:共享资源
大小:1.74MB
格式:ZIP
上传时间:2015-09-02
上传人:小***
认证信息
个人认证
林**(实名认证)
福建
IP属地:福建
20
积分
- 关 键 词:
-
ca6140
车床
托架
机械
加工
工艺
m6
底孔
螺纹
罗纹
以及
钻床
夹具
设计
- 资源描述:
-
!【详情如下】【CA6140车床后托架831001课题】CAD图纸+word设计说明书.doc[7000字,24页]【需要咨询购买全套设计请加QQ97666224】.bat
lingjiantu.igs
lingjiantu_igs.prt
shui.prt
后托架毛坯图(完).dwg
夹具装配图.dwg
工序卡100(终检).dwg
工序卡10(铣).dwg
工序卡20(钻).dwg
工序卡30(钻).dwg
工序卡40(扩).dwg
工序卡50(钻).dwg
工序卡60(攻).dwg
工序卡70(半精镗).dwg
工序卡80(精镗).dwg
工序卡90(加工油槽去毛刺).dwg
机械加工工艺过程.doc
设计说明书.doc[7000字,24页]
前 言
机械制造工艺与机床夹具课程设计是在学完了机械制造工艺与机床夹具和大部分专业课,并进行了生产实习的基础上进行的一个教学环节。这是我们在进行毕业设计之前对所学课程的一次深入的全面总复习,也是一次理论联系实际的训练。因此,它在几年的学习中占有重要的地位。
就我个人而言,希望通过这次课程设计,对今后将从事的工作,进行一次适应性训练,通过设计锻炼自己分析问题、解决问题的能力,为回厂后的工作打下一个良好的基础。
由于能力所限,设计中尚有许多不足之处,希望各位教师给予批评指教。
一、零件的分析:
(一)计算生产纲领,确定生产类型:
零件图上为CA6140车床上的后托架,生产量为2000件,该产品属于轻型机械,根据表1-3生产类型与生产纲领等的关系,可确定其生产类型为中批生产。






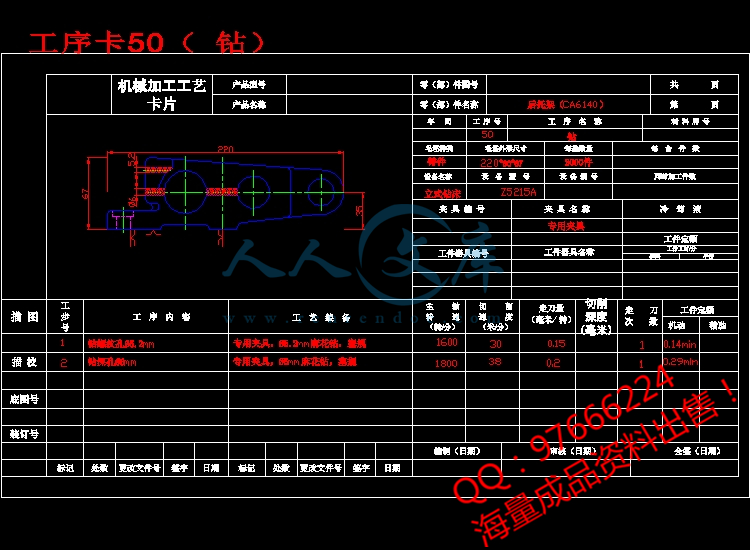









- 内容简介:
-
重庆工学院 机械加工工艺过程卡片 产品型号 产品型号 共页 产品名称 零件名称 后托架( CA6140 车床 ) 第 1 页 材料牌号 HT200 毛坯种类 铸件 毛坯外型尺寸 220 60 67mm 每毛坯件数 2000 每台件数 备注 工 序 号 工序 名称 工 序 内 容 车间 工段 设 备 工 艺 装 备 工 时 准终 单件 00 毛坯 10 铣 1、粗铣底面; 2、精铣底面,保证尺寸 120 60mm; 金工 X6132 专用夹具,高速钢 圆柱形铣刀,游标卡尺 1.49min 20 钻 1、 钻两个 13mm 的孔; 2、钻 两个 销孔 10mm; 3、锪两个沉头孔 20mm; Z5125A 专用夹具,高速钢 直 柄 麻花钻、高速钢 90度锪钻, 塞规 0.59min 30 钻 1、钻孔 到 28mm; 2、 钻孔 到 23.5mm; 3、锪 平孔 25.5mm 端面 ; Z575 专用夹具, 高速钢锥柄麻花钻、高速钢 90度锪钻,塞规 1.26min 40 扩 1、扩孔 到 38.7mm; 2、扩孔 到 29.5mm; 3、 扩孔 到 24.5mm; Z575 专用夹具,高速钢直柄麻花钻,塞规 1.41min 50 钻 1、钻螺纹孔 5.1mm; 2、钻深孔 6mm; Z5125A 专用夹具,高速钢直柄麻花钻 0.43min 60 攻 1、攻螺纹孔 M6; Z5125A 专用夹具, M6 丝锥 0.10min 70 镗 1、半精镗 到 39.7mm; 2、半精镗 到 30mm; 3、半精镗 到 25.3mm; T68 专用夹具,硬质合金镗刀,塞规 2.26min 80 镗 1、精镗孔到 40mm; 2、精镗孔到 30.2mm; 3、精镗孔到 25.5mm; T68 专用夹具,硬质合金镗刀,塞规 2.26min 90 钳 1、加工油槽; 2、去毛刺; 100 检 1、按图纸要求检验; 设计(日期) 审核(日期) 会签(日期) 曾智( 2005.7.1) 标记 处数 更改文件号 签字 日期 标记 处数 更改文件号 签字 日期 nts第 1 页 共 24 页 前 言 机械制造工艺与机床夹具课程设计是在学完了机械制造工艺与机床夹具和大部分专业课,并进行了生产实习的基础上进行的一个教学环节。这是我们在进行毕业设计之前对所学课程的一次深入的全面总复习,也是一次理论联系实际的训练。因此,它在几年的学习中占有重要的地位。 就我个人而言,希望通过这次课程设计,对今后将从事的工作,进行一次适应性训练,通过设计锻炼自己分析问题、解决问题的能力,为回厂后的工作打下一个良好的基础。 由于能力所限,设计中尚有许多不足之处,希望各位教师给予批评指教。 一、零件的分析: (一 )计 算生产纲领 ,确定生产类型: 零件图上为 CA6140 车床上的后托架 ,生产量为 2000 件 ,该产品属于轻型机械 ,根据表 1-3 生产类型与生产纲领等的关系 ,可确定其生产类型为中批生产。 (二)零件的作用: 后托架在 CA6140 车床床身的尾部,三个孔分别装丝杠、光杠、转向开关,起加强固定作用;在 40mm 与 30.2mm 之间的孔为毛线孔,用于导通油路;旁路的螺纹孔是连接油盖的;正面的四个孔将后托架固定于车床尾部。 (三)零件的工艺分析: CA6140 车床后托架共有两组表面,他们之间 有一定的位置要求。现叙述如下: 1、以 40mm 孔为中心的加工表面:这一组加工表面包括: 40 02500。mm, 30.2 200。mm及 25.5 0300。mm 的孔 ,两沉头孔为 20mm,两装配铰孔 13mm,深孔 6mm,螺纹 M6,两销孔。其中,主要加工表面为 40 02500。mm , 30.2 200。mm 及 25.5 300。 mm 的三个孔。 2、以底面 120 60mm 为中心的加工表面:这一组加工表面包括底面 120 60mm 和nts第 2 页 共 24 页 锪平面。这两组加工表面之间有一定的位置要求,主要是: 1 40 02500。mm 孔的轴线与底面的平行度为 100: 0.07; 2 30.2 200。mm 孔的轴线与底面的平行度为 100: 0.07; 3 30.2 200。mm 孔的轴线与底面的平行度为 100: 0.07; 4 下底面的平面度误差为 0.03; 5 毛线孔的中心线与底面的尺寸误差为 0.07; 由此可分析知 ,对于这两组加工表面而言 ,可以先加工其中一组表面,然后借助与专用夹具加工另一组表面,并且保证他们之间的位置精度要求。 二、工艺规程的设计: (一)确定毛坯的制造形式: 后托架是车床 CA6140 的后托起部分,该零件材料为 HT200,考虑到机床 运行中要经常使主轴正转与反转,此时,转向开关、丝杠、光杠也进行正转与反转的连续或瞬时运动。因此,扭矩最大 ,强度不高使用铸件,由于零件的年产量为 2000 件,已达到中批量生产水平,并且零件的轮廓尺寸不大,故可以采用砂型铸造,这从提高生产率,保证加工精度上考虑,也是比较合理的。 (二)基准的选择 基准的选择是工艺规程设计的重要工作之一,基准选择得正确与合理,可以使加工质量得到保证,生产率得以提高。否则,加工工艺过程中会问题百出,更有甚者,还会造成零件大批量报废,使生产无法正常运行。 1、粗基准的选择:对于一般的孔类零件,以孔作为粗基准完全合理,但对本零件来说,孔 40 02500。mm 为铸造孔,不易作为 精基准,故我们可以考虑以顶面加一个可调支撑作为粗基准,以此基准把底面 120 60mm 先加工出来,由于此顶面只限制了 X、 Y、nts第 3 页 共 24 页 Z 的转动和 Z 的移动 4 个自由度,故可以考虑选左端面为第二基准面,此二面可以限制6 个自由度,达到完全定位。 2、精基准的选择:主要应考虑到基准重合问题。当设计基准与工序基准不重合时,应尽量进行尺寸计算。这在后面还要专门计算, 此处不在重复。 (三 ) 制订工艺路线: 制订工艺路线的出发点 ,应当使零件的几何形状、尺寸精度及位置精度等技术要求能得到合理的保证。在用生产纲领确定为中批量生产的条件下 ,可以考虑用万能性机床配以专用夹具,并尽量使工序集中来提高生产率,但同时也要保证质量。除此之外,还要考虑到经济效果,在实际生产中还要考虑加工的设备,以尽量使成本降到最低。 1、工艺方案一: 工序 10:粗、精铣底面,保证尺寸 120 60mm; 工序 20:钻两个 13mm 的孔;钻两个 销孔 10mm;锪两个沉头孔 20mm; 工序 30: 钻孔 38mm; 钻孔 28mm; 钻孔 23.5mm;锪平孔 25.5mm端面; 工序 40: 扩孔 39.5mm; 扩孔 29.5mm; 扩孔 29.5mm; 工序 50: 半精镗 40mm; 30mm; 25mm; 工序 60: 精镗孔 40mm; 30.2mm; 25.5mm; 工序 70: 钻螺纹孔 5.1mm; 钻深孔 6mm; 工序 80: 攻螺纹孔 M6; 工序 90: 加工油槽,去毛刺; 工序 100: 按图纸要求检验; 2、工艺方案二: 工序 10: 钻孔 38mm; 钻孔 28mm; 钻孔 23.5mm;锪平孔 25.5mm 端面; nts第 4 页 共 24 页 工序 20: 扩孔 39.5mm; 扩孔 29.5mm; 扩孔 29.5mm; 工序 30:粗、精铣底面,保证尺寸 120 60mm; 工序 40:钻两个 13mm 的孔;钻两个销孔 10mm;锪两个沉头孔 20mm 工序 50: 半精镗 40mm; 30mm; 25mm; 工序 60: 精镗孔 40mm; 30.2mm; 25.5mm; 工序 70: 钻螺纹孔 5.1mm; 钻深孔 6mm; 工序 80: 攻螺纹孔 M6; 工序 90: 加工油槽,去毛刺; 工序 100:按图纸要求检验; 3、工艺方案的比较分析: 以上两个工艺方案的特点在于:方案一是先加工以底面为中心的表面,再以此为基准加工 3 个孔及其他相关的孔;方案二却恰恰相反,先加工 3 个孔,再以孔定位 加工底面。 根据后托架的作用和两个方案的比较分析,由于 40m, 30.2mm, 25.5mm这三个孔的轴线平行度要求较高。因此,选用底面为基准时,加工孔的精度一定的越高越好。因此,方案二的工序不太合适,我们采用方案一的大致顺序。经过分析,方案一的加工顺序是先粗加工、精加工一组表面,再粗加工、精加工另外一组平面。这看上去大致是合理的,但仔细推敲后,发现仍然有不太符合工艺原则,现将改进的工艺过程具体分析如下: 工序 10:粗、精铣底面,保证尺寸 120 60mm; 工序 20:钻两个 13mm 的孔;钻两个销孔 10mm;锪两个沉头孔 20mm; 工序 30: 钻孔 38mm; 钻孔 28mm; 钻孔 23.5mm;锪平孔 25.5mm端面; nts第 5 页 共 24 页 工序 40: 扩孔 39.5mm; 扩孔 29.5mm; 扩孔 29.5mm; 工序 50: 钻螺纹孔 5.1mm; 钻深孔 6mm; 工序 60: 攻螺纹孔 M6; 工序 70: 半精镗 40mm; 30mm; 25mm; 工序 80: 加工 油槽; 工序 90: 精镗孔 40mm; 30.2mm; 25.5mm; 工序 100: 去毛刺; 工序 110: 按图纸要求检验; (四)机械加工余量、工序尺寸及毛坯尺寸的确定 : CA6140 车床后托架零件材料为 HT200,硬度为 200HBS,毛坯余量为 3.05kg,生产类 型为中批生产 ,采用铸造毛坯。 根据上述原始资料及加工工艺,分别确定各加工表面的机械加工余量、工序尺寸和毛坯尺寸如下: 1、底面( 120 60mm) 考虑其表面粗糙度比较高,故需粗、精铣底面,其加工余量 Z=2mm。 2、其余各铸造孔加工余量如下: 零件尺寸 单边 毛坯 40 02500。mm 1.5mm 37mm 3、其余各孔由于直径较小,故只能为实心孔 ,其毛坯不能铸造出孔 ,参照机械加工工艺手 册后确定: 25.5mm 孔 钻孔到 23.5mm;扩孔到 24.7mm; 半精镗到 24.9;精镗到 25.5mm; nts第 6 页 共 24 页 30.2mm 孔 钻孔到 28mm;扩孔到 29.3mm 半精镗到 29.8mm;精镗到 30.2mm; 40mm 孔 扩孔到 38.7mm; 半精镗到 39.6mm;精镗到 40mm; (五 )确定切削 用量及基本工时 : 工序 10:粗、精铣底面: 1、加工条件 工件材料: HT200,b=200HBS,铸造; 加工需求:粗、精铣底面,保证尺寸 120 60mm 和台阶高 18mm; 机床: X6132 型铣床; 刀具:高速钢圆柱形铣刀,根据金属切削手册表 6-4 取铣刀直径d=100mm,根据金属切削手册表 6-7 查得铣刀 齿数 Z=14; 2、确定铣削深度: 参考有金属切削手册确定粗加工的铣削深度 ap=2.5mm;精加工的铣削深度 ap=0.5mm; 3、确定每齿进给量: 参考机械加工工艺手册(软件版)取粗铣时的每齿进给量fz =0.15(mm/z);精铣时的每转进给量 f=0.8( mm/z); 4、确定主轴转速: 参考实用金属切削加工工艺手册表 8-4,取粗铣时的主轴转速为 150r/min,精铣时的主轴转速为 190r/min; 5、计算铣削速度: nts第 7 页 共 24 页 前面已经确定铣刀直径 d=100mm 和主轴转速(粗铣刀时为300r/mm)。所以,相应的铣削速度分别为: 粗铣时:)( m in/1.471000 15010014.31000 mdnv 精铣时: )( m in/601000 19010014.31000 mdnv 6、校核机床功率(只需校核粗加工即可): 关由手册查得功率 pmpzem Z n Kafadp 72.086.014.05104.92 ; 取 Z=14, srn /5.260150 , 60ea , ap=2.5mm, zmmf z /15.0 而FZvpm KKK 由手册查得 vK =1, FZK =1 故 pmK1,所以:KWp m 32.115.2145.215.060100104.92 72.086.014.05 起所耗功率远小于机床功率,故可用。 7、计算基本工时: 参考机械加工工艺手册(软件版)确定切入和切出的行程长度)( mmll 1021 ,而工件的长度为 )( mm120ml ,故铣刀的工作行程为 )( mml 13012010 。所以,基本工时为: 1501415.0 13021nf lllT 基本0.41( m/min)(粗铣时); 1508.0 13021nf lllT 基本1.08( m/min)(精铣时); 工序 20:钻四个定位孔( 2-10mm 和 2- 13mm);锪两个 沉头孔 20mm,深 2mm; 工步 1:钻两个 13mm 孔 1、 加工条件 工件材料: HT200,b=200HBS,铸造; 加工需求:钻锥度孔 10mm,保证零件图上的精度要求; nts第 8 页 共 24 页 机床: Z5125A 型钻床; 刀具:,钻头直径 13mm, 2、确定切削进给量: 根据实用金属切削加工工艺手册中表 5-6,取进给量 f=0.3( mm/r); 3、确定切削速度: 根据实用金属切削加工工艺手册中表 5-6,取切削速度min/30 mvc ; 4、计算转速: )( min/9.7951314.3 3010001000 rD vn ,按机床实际转速取)( min/750 rn ; 5、计算基本时间: )(基本 m in14.03.0750 472021 nf lllT工步 2:钻两个 10mm 孔 1、 加工条件 工件材料: HT200,b=200HBS,铸造; 加工需求:钻锥度孔 10mm,保证零件图上的精度要求; 机床: Z5125A 型钻床; 刀具:高速钢麻花钻,钻头直径 10mm; 2、确定切削进给量: 根据实用金属 切削加工工艺手册中表 5-6,取进给量 f=0.2( mm/r); nts第 9 页 共 24 页 3、确定切削速度: 根据实用金属切削加工工艺手册中表 5-6,取切削速度min/30 mvc ; 4、计算转速: )( m i n/4.9551014.3 3010001000 rD vn ,按机床实际转速取)( min/1000 rn ; 5、计算基本时间: nf lllT 21基本 )( m in3.02.010 0 04650 工步 3:锪两个沉头孔 20mm,深 12mm 1、 加工条件: 工件材料: HT200,b=200HBS,铸造; 加工需求:锪孔 20mm 机床: Z5125A 型钻床; 刀具:高速钢麻花钻,钻头直径 20mm; 2、确定切削进给量: 根据实用金属切削加工工艺手册中表 5-6,取进给量 f=0.3( mm/r); 3、确定切削速度: 根据实用金属切削加工工艺手册中表 5-6,取切削速度min/30 mvc ; 4、计算转速: nts第 10 页 共 24 页 )( m i n/4772014.3 3010001000 rD vn ,按机床实际转速取)( min/500 rn ; 5、计算基本时间: nf lllT 21基本 )( m in16.03.050005.1112 工序 30:钻 孔到 28mm; 23.5mm;锪平 25.5mm 端面,深 2mm; 工步 1:钻 孔到 28mm 1、 加工条件: 工件材料: HT200,b=200HBS,铸造; 加工需求: 钻 孔 28mm; 机床: Z575 型钻床; 刀具:高速钢麻花钻,钻头直径 28mm; 2、确定切削进给量: 根据实用金属切削加工工艺手册中表 5-6,取进给量 f=0.4( mm/r); 3、确定切削速度: 根据实用金属切削加工工艺手册中表 5-6,取切削速度min/28 mvc ; 4、计算转速: )( m i n/5.3182814.3 2810001000 rD vn ,按机床实际转速取)( min/320 rn ; 5、计算基本时间: nts第 11 页 共 24 页 nf lllT 21基本 )( m in62.04.032041560 工步 2:钻 孔到 23.5mm 1、 加工条件: 工件材料: HT200,b=200HBS,铸造; 加工需求: 钻 孔 23.5mm; 机床: Z575 型钻床; 刀具:高速钢麻花钻,钻头直径 23.5mm; 2、确定切削进给量: 根据实用金属切削加工工艺手册中表 5-6,取进给量 f=0.4( mm/r); 3、确定切削速度: 根据实用金属切削加工工艺手册中表 5-6,取切削速度min/28 mvc ; 4、计算转速: )( m i n/5.3795.2314.3 2810001000 rD vn ,按机床实际转速取 )( min/380 rn ; 5、计算基本时间: nf lllT 21基本 )( m in54.04.038041860 工步 3: 锪平 25.5mm 端面 1、 加工条件: nts第 12 页 共 24 页 工件材料: HT200,b=200HBS,铸造; 加工需求: 锪 平 25.5mm 端面 ; 机床: Z575 型钻床; 刀具:高速钢 90 度锪钻,锪钻直径 25.5mm; 2、确定切削进给量: 根据实用金属切削加工工艺手册中表 5-6,取进给量 f=0.4( mm/r); 3、确定切削速度: 根据实用金属切削加工工艺手册中表 5-6,取切削速度min/28 mvc ; 4、计算转速: )( m i n/7.3495.2514.3 2810001000 rD vn ,按机床实际转速取 )( min/350 rn ; 5、 计算基本时间: nf lllT 21基本 )( m in1.04.035005.212 工序 40: 扩孔到 38.7mm; 29.5mm; 24.5mm; 工步 1: 扩孔到 38.7mm 1、 加工条件: 工件材料: HT200,b=200HBS,铸造; 加工需求: 扩孔 39.5mm; 机床: Z575 型钻床; nts第 13 页 共 24 页 刀具:高速钢 扩孔钻,扩孔钻直径 38.7mm; 2、确定切削进给量: 根据实用金属切削加工工艺手册中表 5-6,取进给量 f=0.5( mm/r); 3、确定切削速度: 根据实用金属切削加工工艺手册中表 5-6,取切削速度min/26 mvc ; 4、计算转速: )( m i n/63.2097.3814.3 2610001000 rD vn ,按机床实际转速取 )( min/210 rn ; 5、计算基本时间: nf lllT 21基本 )( m in63.05.021045.260 工步 2: 扩孔到 29.5mm 1、 加工条件: 工件材料: HT200,b=200HBS,铸造; 加工需求: 扩孔 29.5mm; 机床: Z575 型钻床; 刀具:高速钢扩孔钻,扩孔钻直径 29.5mm; 2、确定切削进给量: 根据实用金属切削加工工艺手册中表 5-6,取进给量 f=0.6( mm/r); nts第 14 页 共 24 页 3、确定切削速度: 根据实用金属切削加工工艺手册中表 5-6,取切削速度min/32 mvc ; 4、计算转速: )( m i n/5.3455.2914.3 3210001000 rD vn ,按机床实际转速取 )( min/350 rn ; 5、计算基本时间: nf lllT 21基本 )( m in32.06.03 5 045.260 工步 3: 扩孔到 24.5mm 1、 加工条件: 工件材料: HT200,b=200HBS,铸造; 加工需求: 扩孔 24.5mm; 机床: Z575 型钻床; 刀具:高速钢扩孔钻,扩孔钻直径 24.5mm; 2、确定切削进给量: 根据实用金属切削加工工艺手册中表 5-6,取进给量 f=0.4( mm/r); 3、确定切削速度: 根 据实用金属切削加工工艺手册中表 5-6,取切削速度min/28 mvc ; 4、计算转速: nts第 15 页 共 24 页 )( m i n/97.3635.2414.3 2810001000 rD vn ,按机床实际转速取 )( min/360 rn ; 5、计算基本时间: nf lllT 21基本 )( m in46.04.03 6 045.260 工序 50: 钻螺纹孔 5.2mm; 钻深孔 6mm; 工步 1: 钻螺纹孔 5.2mm 1、 加工条件: 工件材料: HT200,b=200HBS,铸造; 加工需求: 钻孔 5.1mm; 机床: Z5125A 型钻床; 刀具:高速钢麻花钻,钻头直径 5.2mm; 2、确定切削进给量: 根据实用金属切削加工工艺手册中 表 5-6,取进给量 f=0.15( mm/r); 3、确定切削速度: 根据实用金属切削加工工艺手册中表 5-6,取切削速度min/30 mvc ; 4、计算转速: )( m i n/18612.514.3 3010001000 rD vn ,按机床实际转速取)( min/1600 rn ; 5、 计算基本时间: nts第 16 页 共 24 页 nf lllT 21基本 )( m in14.015.016004425 工步 2: 钻深孔 6mm 1、 加工条件: 工件材料: HT200,b=200HBS,铸造; 加工需求: 钻孔 6mm; 机床: Z5125A 型钻床; 刀具:高速钢麻花钻,钻头直径 6mm; 2、确定切削进给 量: 根据实用金属切削加工工艺手册中表 5-6,取进给量 f=0.2( mm/r); 3、确定切削速度: 根据实用金属切削加工工艺手册中表 5-6,取切削速度min/38 mvc ; 4、计算转速: )( m i n/98.2016614.3 3810001000 rD vn ,按机床实际转速取 )( min/1800 rn ; 5、计算基本时间: nf lllT 21基本 )( m in29.02.0180045.495 工序 60:攻螺纹孔 M6; 1、 加工条件: nts第 17 页 共 24 页 工件材料: HT200,b=200HBS,铸造; 加工需求:攻螺纹孔 M6; 机床: Z5125A 型钻床; 刀具:高速钢麻花钻,钻头直径 6mm; 2、确定切削进给量: 根据实用金属切削加工工艺手册中表 5-6,取进给量 f=0.2( mm/r); 3、确定切削速度: 根据实用金属切削加工工艺手册中表 5-6,取切削速度min/38 mvc ; 4、计算转速: )( m i n/98.2016614.3 3810001000 rD vn ,按机床实际转速取 )( min/1800 rn ; 5、计算基本时间: nf lllT 21基本 )( m in10.02.01 8 0 04425 工序 70: 半精镗到 39.7mm; 30mm; 25.3mm; 工步 1:半精镗到 39.7mm; 1、 加工条件: 工件材料: HT200,b=200HBS,铸造; 加工需求: 半精镗到 39.7mm; 机床: T68 镗床; nts第 18 页 共 24 页 刀具:硬质合金镗刀; 2、确定切削进给量: 根据实用金属切削加工工艺手册,取进给量 f=0.37( mm/r); 3、确定切削速度: 根据实用金属切削加工工艺手册,取切削速度min/48 mvc ; 4、计算转速: )( m i n/3857.3914.3 4810001000 rD vn ,按机床实际转速取)( min/400 rn ; 5、计算基本时间: nf lllT 21基本 )( m in45.037.04004260 工步 2:半精镗到 30mm; 1、 加工条件: 工件材料: HT200,b=200HBS,铸造; 加工需求: 半精镗到 30mm; 机床: T68 镗床; 刀具:硬质合金镗刀; 2、确定切削进给量: 根据实用金属切削加工工艺手册,取进给量 f=0.13( mm/r); 3、确定切削速度: 根据实用金属切削加工工艺手册,取切削速度nts第 19 页 共 24 页 min/48 mvc ; 4、计算转速: )( min/6.5093014.3 4810001000 rD vn ,按机床实际转速取 )( min/500 rn ; 5、计算基本时间: nf lllT 21基本 )( m in0.113.05004260 工步 3:半精镗到 25.3mm; 1、 加工条件: 工件材料: HT200,b=200HBS,铸造; 加工需求: 半精镗到 25.3mm; 机床: T68 镗床; 刀具:硬质合金镗刀; 2、确定切削进给量: 根据实用金属切削加工工艺手册,取进给量 f=0.13( mm/r); 3、确定切削速度: 根据实 用金属切削加工工艺手册,取切削速度min/50 mvc ; 4、计算转速: )( m i n/4.6293.2514.3 5010001000 rD vn ,按机床实际转速取 )( min/630 rn ; 5、计算基本时间: nts第 20 页 共 24 页 nf lllT 21基本 )( m in81.013.06 3 04260 工序 80: 精镗到 40mm; 30.2mm; 25.5mm; 工步 1:精镗到 40mm; 1、 加工条件: 工件材料: HT200,b=200HBS,铸造; 加工需求: 精镗到 40mm; 机床: T68 镗床; 刀具:硬质合金镗刀; 2、确定切削进给量: 根据实用金属切削加工工艺手册,取进给量 f=0.37( mm/r); 3、确定切削速度: 根据实用金属切削加工工艺手册,取切削速度min/48 mvc ; 4、计算转速: )( min/2.3824014.3 4810001000 rD vn ,按机床实际转速取 )( min/400 rn ; 5、计算基本时间: nf lllT 21基本 )( m in45.037.04004260 工步 2:精镗到 30.2mm; 1、 加工条件: nts第 21 页 共 24 页 工件材料: HT200,b=200HBS,铸造; 加工需求: 精镗到 30.2mm; 机床: T68 镗床; 刀具:硬质合金镗刀; 2、确定切削进给量: 根据实用金属切削加工工艺手册,取进给量 f=0.13( mm/r); 3、确定切削速度: 根据实用金属切削加工工艺手册,取切削速度min/48 mvc ; 4、计算转速: )( m i n/2.5062.3014.3 4810001000 rD vn ,按机床实际转速取 )( min/500 rn ; 5、计算基本时间: nf lllT 21基本 )( m in0.113.05004260 工步 3:精镗到 25.3mm; 1、 加工条件: 工件材料: HT200,b=200HBS,铸造; 加工需求: 精镗到 25.5mm; 机床: T68 镗床; 刀具:硬质合金镗刀; 2、确定切削进给量: nts第 22 页 共 24 页 根据 实用金属切削加工工艺手册,取进给量 f=0.13( mm/r); 3、确定切削速度: 根据实用金属切削加工工艺手册,取切削速度min/50 mvc ; 4、计算转速: )( m i n/5.6245.2514.3 5010001000 rD vn ,按机床实际转速取 )( min/630 rn ; 5、 计算基本时间: nf lllT 21基本 )( m in81.013.06 3 04260 六 专用夹具设计 为了提高劳动生产效率,保证加工质量,降低劳动强度和生产成本通常需要设计专用夹具,我 设计的是该道工序的专用夹具设计 钻 M6 底孔及攻螺纹和钻 6 油池孔 的钻床夹具,本夹具将用于 Z525 钻床 。刀具为直柄 麻花钻。 (一)问题的提出 此夹具主要来加工油
- 温馨提示:
1: 本站所有资源如无特殊说明,都需要本地电脑安装OFFICE2007和PDF阅读器。图纸软件为CAD,CAXA,PROE,UG,SolidWorks等.压缩文件请下载最新的WinRAR软件解压。
2: 本站的文档不包含任何第三方提供的附件图纸等,如果需要附件,请联系上传者。文件的所有权益归上传用户所有。
3.本站RAR压缩包中若带图纸,网页内容里面会有图纸预览,若没有图纸预览就没有图纸。
4. 未经权益所有人同意不得将文件中的内容挪作商业或盈利用途。
5. 人人文库网仅提供信息存储空间,仅对用户上传内容的表现方式做保护处理,对用户上传分享的文档内容本身不做任何修改或编辑,并不能对任何下载内容负责。
6. 下载文件中如有侵权或不适当内容,请与我们联系,我们立即纠正。
7. 本站不保证下载资源的准确性、安全性和完整性, 同时也不承担用户因使用这些下载资源对自己和他人造成任何形式的伤害或损失。

人人文库网所有资源均是用户自行上传分享,仅供网友学习交流,未经上传用户书面授权,请勿作他用。