CA6140填料箱盖工艺过程卡及数控编程设计
CA6140填料箱盖的工艺规程及磨φ60内孔底面的专用夹具设计全套课程毕业设计
CA6140填料箱盖的工艺规程及磨φ60内孔底面夹具设计【含数控编程】【优秀专用夹具设计含5张CAD图纸】
【带工艺过程及工序卡片全套+外文翻译】【26页@正文9900字】【详情如下】【需要咨询购买全套设计请加QQ1459919609】
CA6140填料箱盖工艺过程卡及数控编程设计.doc
夹具体装配图.dwg
夹具体零件图.dwg
工艺分析.doc
工艺过程卡(数控).dwg
工艺过程卡(普通).dwg
数控加工工艺与普通加工工艺的区别及特点.doc
数控程序编制.doc
文献翻译
机械加工工序卡片(普通).doc
机械加工工序卡片(数控).doc
毛胚图.DWG
零件图.dwg
目 录
1.零件的分析1
1.1、零件的作用1
1.2、零件的工艺分析1
2.工艺规程设计2
2.1、毛坯的制造形式2
2.2、基准面的选择2
2.3、制订工艺路线2
2.3.1、工艺路线方案一2
2.3.2、工艺路线方案二3
2.3.3、工艺方案的比较与分析3
2.4、机械加工余量、工序尺寸及毛坯尺寸的确定4
3.选择加工设备与工艺装备(普通)5
3.1、选择机床5
3.2、选择夹具5
3.3、选择刀具5
3.4、确定工序尺寸5
3.5、确定切削用量及基本工时6
工序I:粗车小端端面,粗车φ65外圆及台阶端面及各倒角。6
工序II:粗镗孔φ37、φ47。7
工序III-VI : 粗车大端面、粗车φ155外圆面、粗车左端台阶面、粗镗φ60内孔、底面及沟槽,粗车环槽、粗车φ75、φ100、φ80外圆面及各倒角。8
工序VII:钻6-φ13.5小孔。8
工序VIII:钻M10螺纹孔及攻丝(装配时钻铰锥孔)。9
工序IX:半精车φ65外圆及台阶面。10
工序X:以φ65mm外圆定位,半精车φ155、φ75、φ100、φ80、环槽及各倒角。11
工序XI:以φ155mm外圆及端面定位,精车、精细车φ65mm外圆。11
工序XII:精、细镗φ60内孔。12
工序XIII:磨Φ60孔底面、倒角。12
4.选择加工设备与工艺装备(数控)13
4.1、选择机床13
4.2、选择夹具13
4.3、选择刀具13
4.4、确定工序尺寸14
4.5、确定切削用量及基本工时16
工序I:粗车小端端面,粗车φ65外圆及台阶端面及各倒角;粗镗孔φ37、φ47。16
工序II:粗车大端面、粗车φ155外圆面、粗车左端台阶面、粗镗φ60内孔、底面及沟槽,粗车环槽、粗车φ75、φ100、φ80外圆面及各倒角。17
工序III:钻6-φ13.5小孔、钻M10螺纹孔及攻丝。(与普通加工相同)17
工序IV:半精车φ65外圆及台阶面。19
工序V:精、细镗φ60内孔。19
工序VI:研磨孔φ60内端面、倒角。(与普通加工相同)19
5.数控程序编制—CA6140填料箱盖的车削加工20
6. 夹具设计23
6.1、问题的指出24
6.2、夹具设计24
6.3、定位误差的分析24
6.4、夹具设计及操作的简要说明24
参考文献
致谢
序 言
毕业设计是我们学完了大学的全部基础课、技术基础课以及专业课之后进行的。这是我们对所学各课程的一次深入的综合性的总复习,也是一次理论联系实际的训练。因此,它在我们四年的大学生活中占有重要的地位。
就我个人而言,我希望能通过这次毕业设计对自己未来将从事的工作进行一次适应性训练,从中锻炼自己分析问题、解决问题的能力。
由于能力所限,设计尚有许多不足之处,恳请各位老师给予指导。
1.零件的分析
1.1、零件的作用
题目所给的零件是CA6140车床填料箱盖(见附图1)主要作用是保证与填料箱体联接后保证密封,对内表面的加工精度要求比较高,对配合面的表面粗糙度要求也较高。
参考文献
1.《机械制造技术基础》北京:机械工业出版社 2004.1于俊一、邹青
2.《金属切削手册(第三版)》上海:上海科学技术出版社2000 史全富、汪麟
3..《机械制造技术基础课程设计指导教程》北京:机械工业出版社 2004.8 邹青
4.《机床夹具设计》北京:机械工业出版社 1991 刘友才、肖继德
5.《工艺师手册》机械工业出版社 杨叔子
6. 王光斗、王春福主编,《机床夹具设计手册》,上海科技出版社
7. 南京市机械研究所主编,《机床专用夹具设计图册》 ,机械工业出版社
8. 邹慧君主编,《机械原理课程设计手册》,机械工业出版社
9. 上海市金属切削技术协会,《金属切削手册》第三版,上海科学技术出版社
10. 甘永立主编,《几何量公差与检测》第五版,上海科学技术出版社
11.机械工业出版社,《机械制造工艺学课程设计指导书》
12.王启平主编,《机床夹具设计》,哈工大出版社
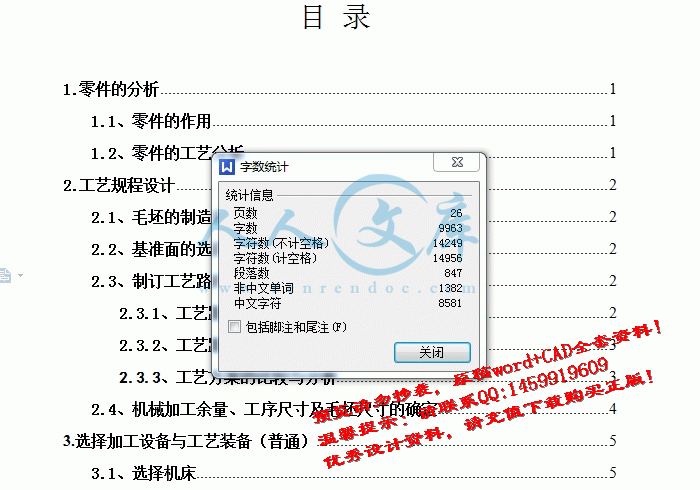
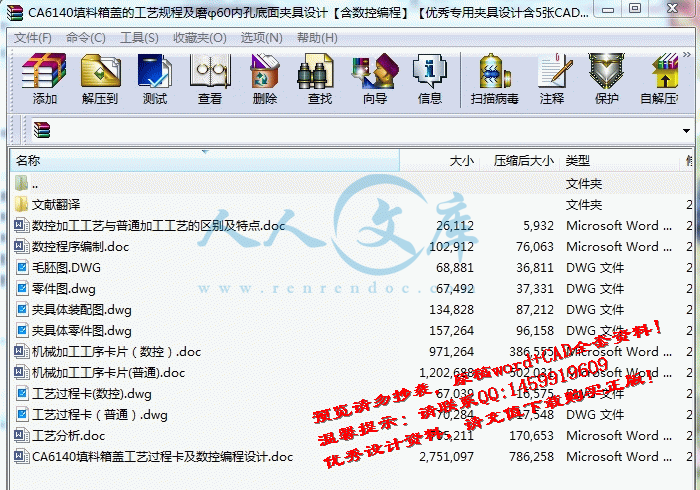

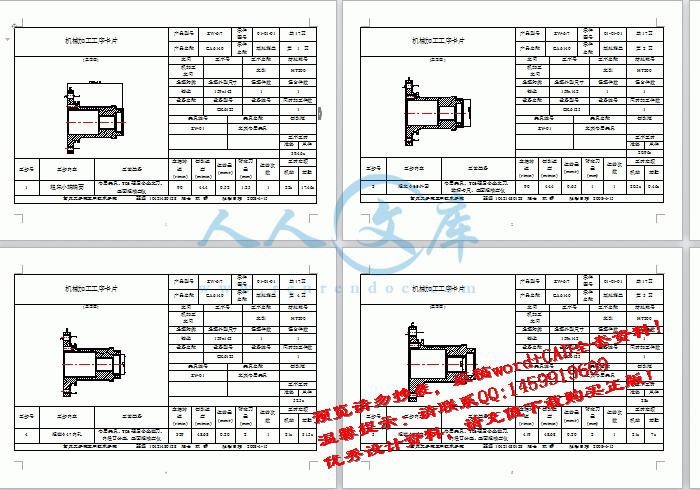

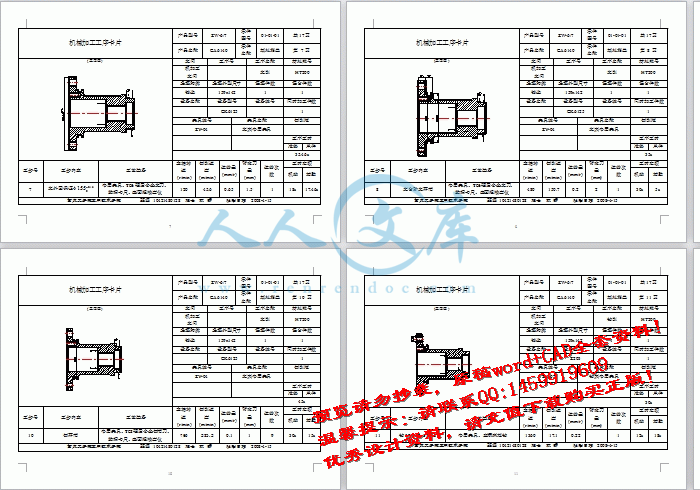



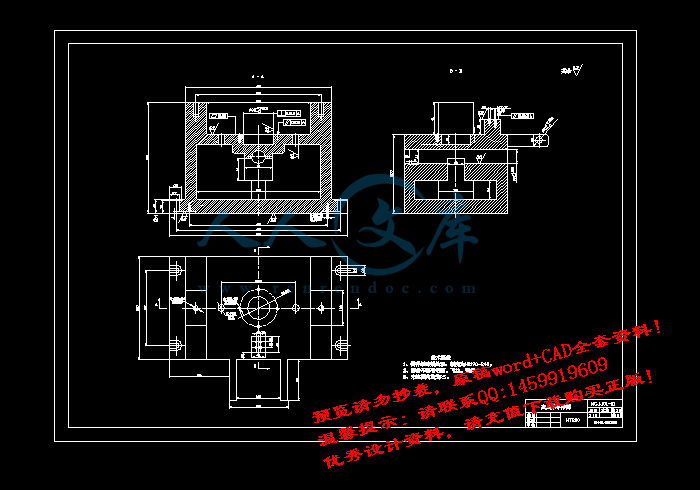
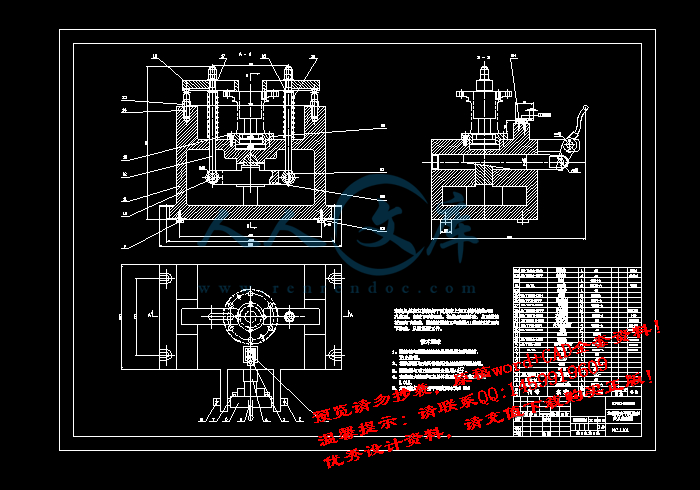
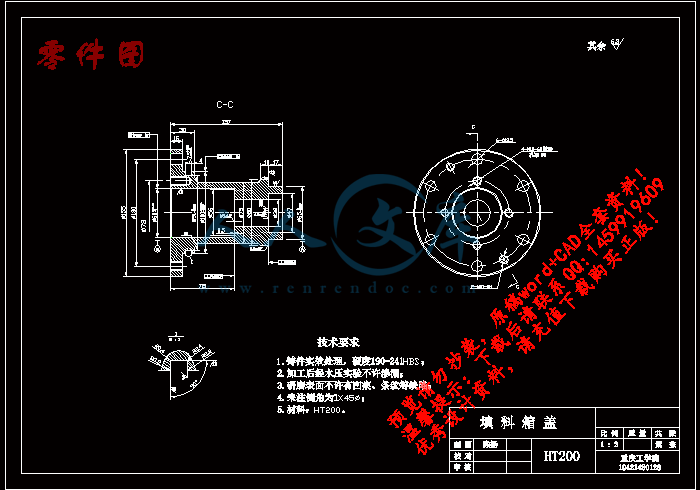
