48-车床拨叉(84008)加工工艺及其钻φ25H7和铣凹槽夹具设计
收藏
资源目录
压缩包内文档预览:(预览前8页/共20页)
编号:482358
类型:共享资源
大小:920.62KB
格式:RAR
上传时间:2015-11-03
上传人:qq77****057
认证信息
个人认证
李**(实名认证)
江苏
IP属地:江苏
20
积分
- 关 键 词:
-
48
车床
加工
工艺
及其
25
h7
以及
凹槽
夹具
车床拨叉(84008)加工工艺及其钻φ25H7和铣凹槽夹具设计
- 资源描述:
-
![7YP)28L]H)%S_`8{VQECXXC.jpg](/ueditor/net/upload/2015-11-03/35027e80-983a-4cdb-9dc4-e9f596a6b0d2.jpg)
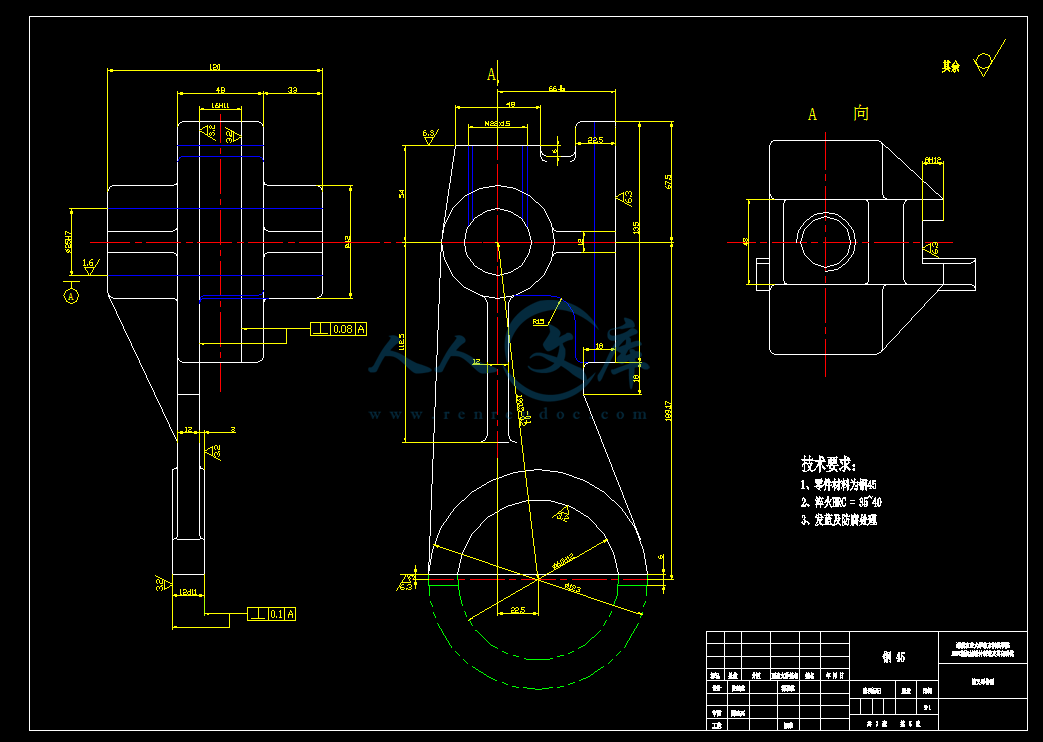

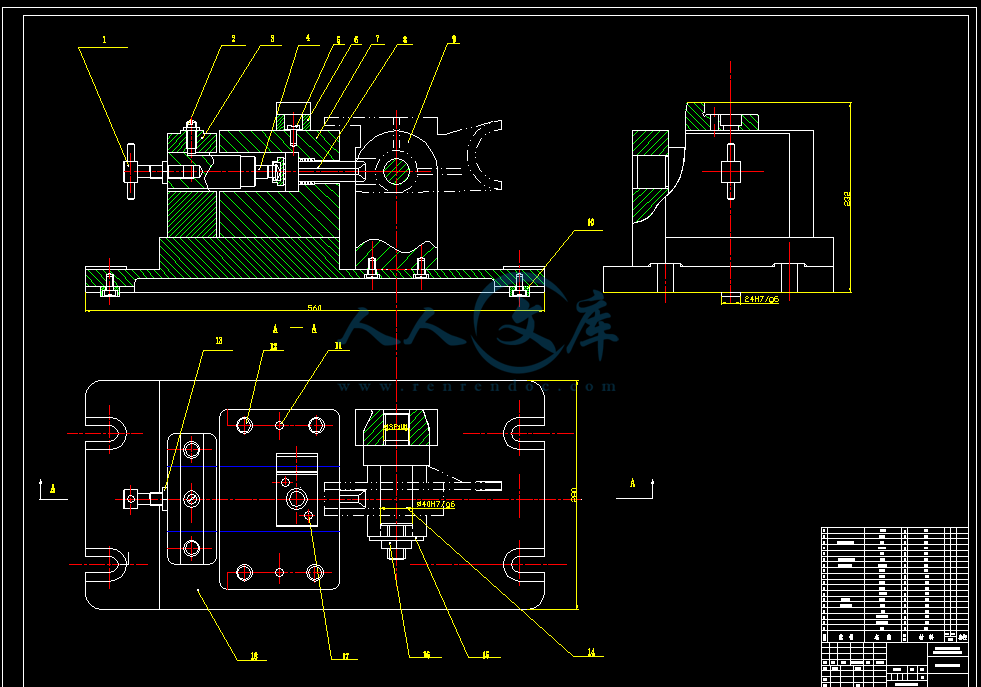
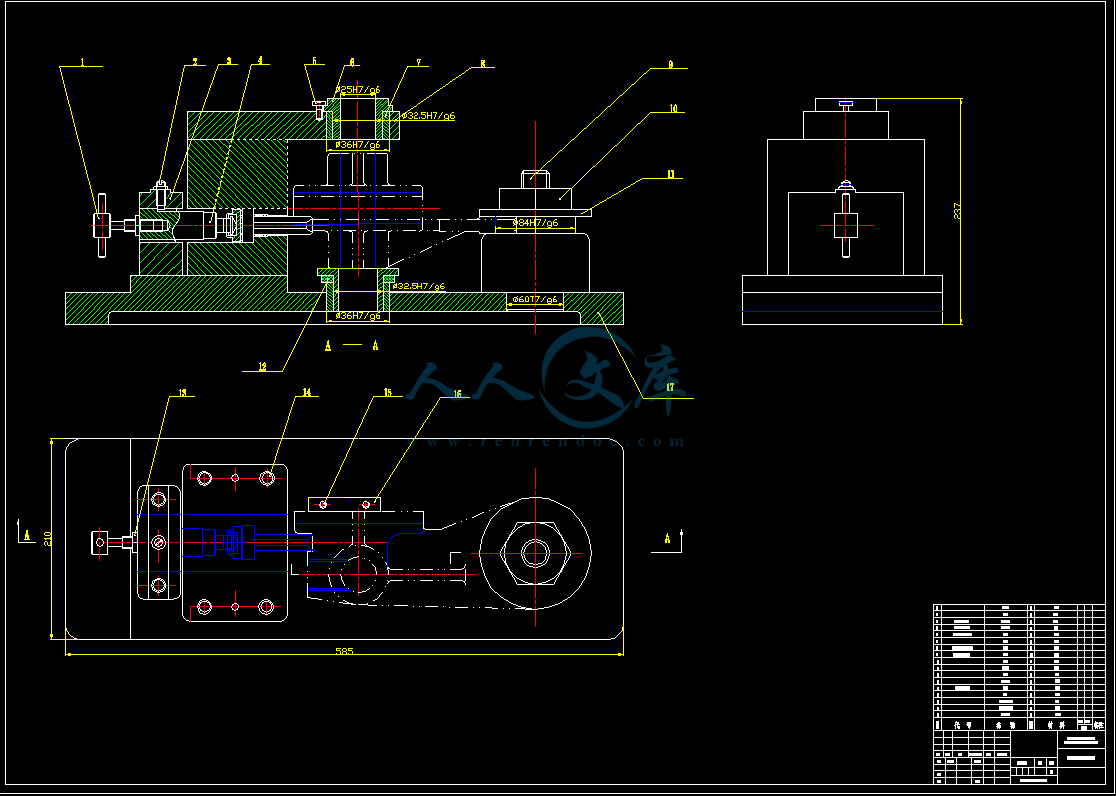

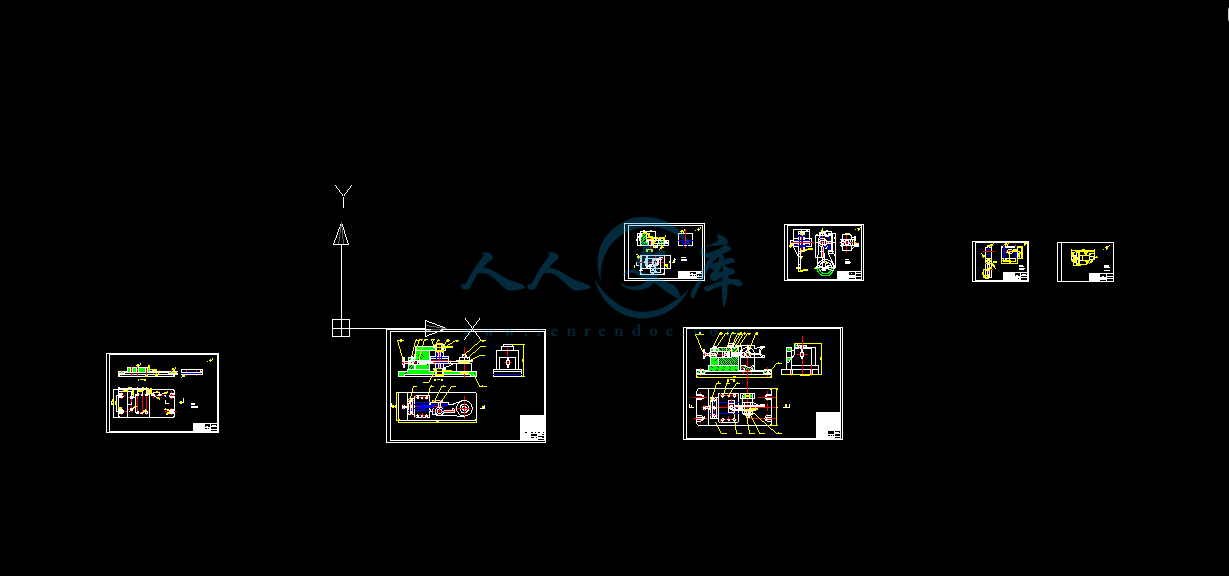
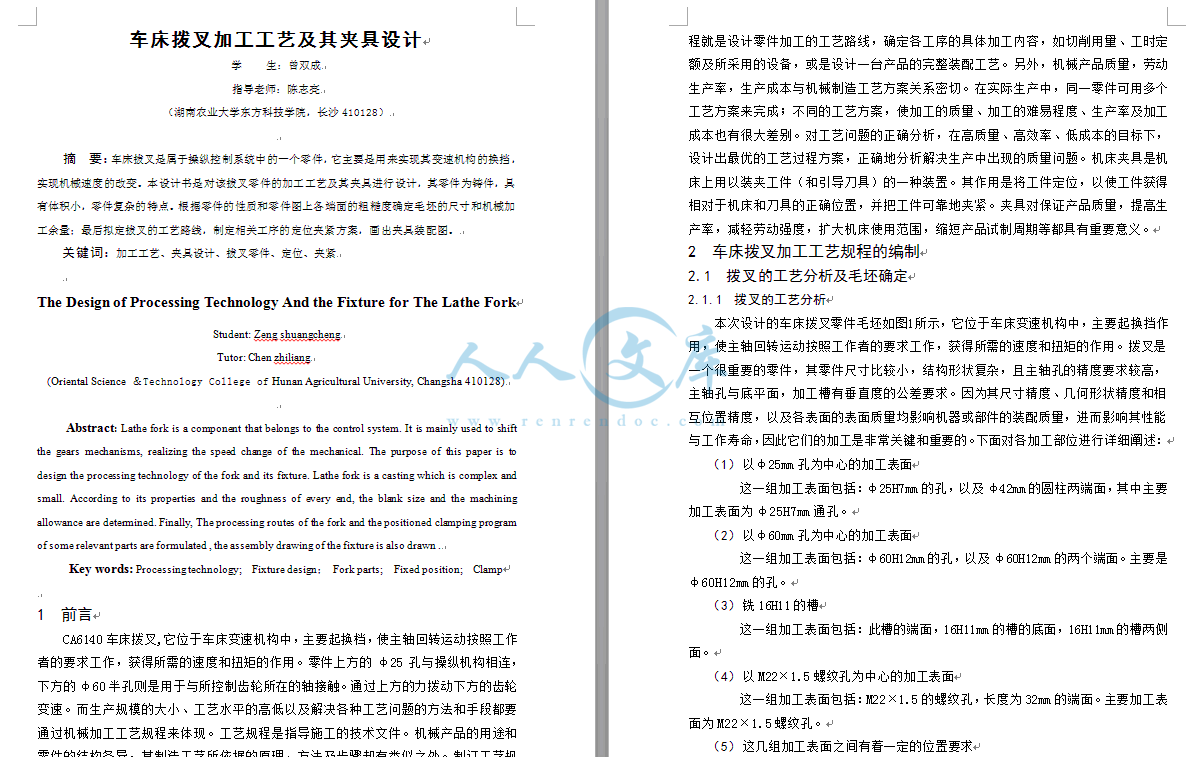
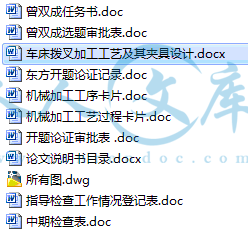
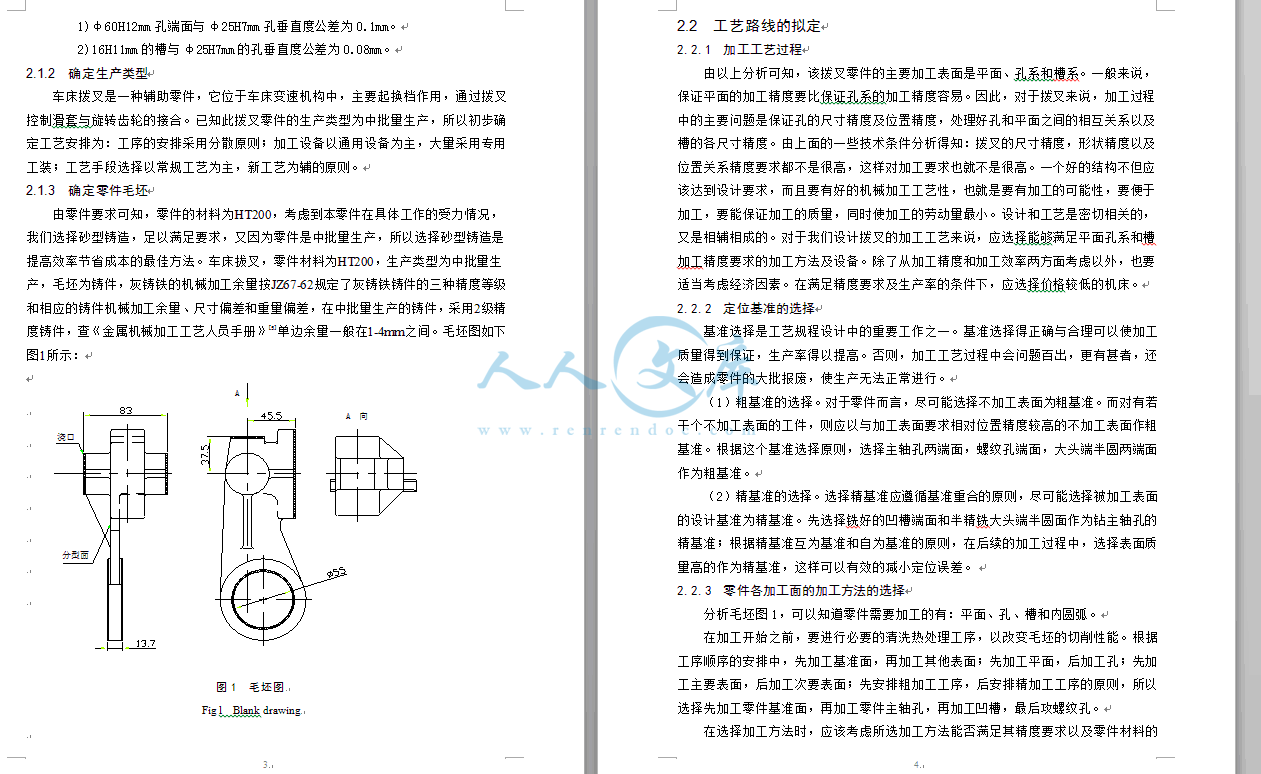
- 内容简介:
-
1 车床拨叉加工工艺及其夹具设计 学 生:曾双成 指导老师:陈志亮 (湖南农业大学东方科技学院,长沙 410128) 摘 要: 车床拔叉是属于操纵控制系统中的一个零件,它主要是用来实现其变速机构的换挡,实现机械速度的改变。本设计书是对该拔叉零件的加工工艺及其夹具进行设计,其零件为铸件,具有体积小,零件复杂的特点。 根据零件的性质和零件图上各端面的粗糙度确定毛坯的尺寸和机械加工余量;最后拟定拔叉的工艺路线,制定 相关工序 的 定位 夹紧方案,画出夹具装配图。 关键词: 加工工艺、夹具设计、拔叉零件、定位、夹紧 The Design of Processing Technology And the Fixture for The Lathe Fork Student: Zeng shuangcheng Tutor: Chen zhiliang (Oriental Science Technology College of Hunan Agricultural University, Changsha 410128) Abstract: Lathe fork is a component that belongs to the control system. It is mainly used to shift the gears mechanisms, realizing the speed change of the mechanical. The purpose of this paper is to design the processing technology of the fork and its fixture. Lathe fork is a casting which is complex and small. According to its properties and the roughness of every end, the blank size and the machining allowance are determined. Finally, The processing routes of the fork and the positioned clamping program of some relevant parts are formulated , the assembly drawing of the fixture is also drawn . Key words: Processing technology; Fixture design; Fork parts; Fixed position; Clamp 1 前言 CA6140车床拨叉 ,它位于车床变速机构中,主要起换档,使主轴回转运动按照工作者的要求工作,获得所需的速度和扭矩的作用。零件上方的 25 孔与操纵机构相连,下方的 60半孔则是用于与所控制齿轮所在的轴接触。通过上方的力拨动下方的齿轮变速。 而生产规模的大小、工艺水平的高低以及解决各种工艺问题的方法和手段都要通过机械加工工艺规程来体现。 工艺规程是指导施工的技术文件。机械产品的用途和零件的结构各异,其制造工艺所依据的原理、方法及步骤却有类似之处。制订工艺规nts2 程就是设计零件加工的工艺路线,确定各工序的具体加工内容,如切削用量、工时定额及所采用的设备,或是设计一台产品的完整装配工艺。另外,机械产品质量,劳动生产率,生产成本与机械制造工艺方案关系密切。在实际生产中,同一零件可用多个工艺方案来完成;不同的工艺方案,使加工的质量、加工的难易程度、生产率及加工成本也有很大差别。对工艺问题的正确分析,在高质量、高效率、低成本的目标下,设计出最优的工艺过程方案,正确地分析解决生产中出现的质量问题。 机床夹具是机床上用以装夹工件(和引导刀具)的一种装置。其作用是将工件定位,以使工 件获得相对于机床和刀具的正确位置,并把工件可靠地夹紧。 夹具对保证产品质量,提高生产率,减轻劳动强度,扩大机床使用范围,缩短产品试制周期等都具有重要意义。 2 车床拨叉加工工艺规程的编制 2.1 拨叉的工艺分析及毛坯确定 2.1.1 拨叉的工艺分析 本次设计的车床拨叉零件毛坯如图 1所示,它位于车床变速机构中,主要起换挡作用,使主轴回转运动按照工作者的要求工作,获得所需的速度和扭矩的作用。拨叉是一个很重要的零件,其零件尺寸比较小,结构形状复杂,且主轴孔的精度要求较高,主轴 孔与底平面,加工槽有垂直度的公差要求。因为其尺寸精度、几何形状精度和相互位置精度,以及各表面的表面质量均影响机器或部件的装配质量,进而影响其性能与工作寿命,因此它们的加工是非常关键和重要的。下面对各加工部位进行详细阐述: ( 1) 以 25mm孔为中心的加工表面 这一组加工表面包括: 25H7mm的孔,以及 42mm的圆柱两端面,其中主要加工表面为 25H7mm 通孔。 ( 2) 以 60mm孔为中心的加工表面 这一组加工表面包括: 60H12mm的孔,以及 60H12mm的两个端面。主要是 60H12mm的孔。 ( 3) 铣 16H11的槽 这一组加工表面包括:此槽的端面, 16H11mm的槽的底面, 16H11mm 的槽两侧面。 ( 4) 以 M22 1.5 螺纹孔为中心的加工表面 这一组加工表面包括: M22 1.5的螺纹孔,长 度为 32mm的端面。主要加工表面为 M22 1.5螺纹孔。 ( 5) 这几组加工表面之间有着一定的位置要求 nts3 A 向浇口分型面A1) 60H12mm 孔端面与 25H7mm孔垂直度公差为 0.1mm。 2)16H11mm的槽与 25H7mm的孔垂直度公差为 0.08mm。 2.1.2 确定生产类型 车床 拨叉是一种辅助零件, 它位于车床变速机构中,主要起换档作用, 通过拨叉控制滑套与旋转齿轮的接合。 已知此拨叉零件的生产类型为中批量生产,所以初步确定工艺安排为: 工序的安排采用分散原则 ; 加工设备以通用设备为主,大量采用专用工装; 工艺手段 选择 以常规工艺为主,新工艺为辅的原则。 2.1.3 确定零件毛坯 由零件要求可知,零件的材料为 HT200,考虑到本零件在具体工作的受力情况,我们选择砂型铸造,足以满足要求,又因为零件是中批量生产,所以选择砂型铸造是提高效率节省成本的最佳方法。车床拔叉,零件材料为 HT200,生产类型为中批量生产,毛坯为 铸件,灰铸铁的机械加工余量按 JZ67-62规定了灰铸铁铸件的三种精度等级和相应的铸件机械加工余量、尺寸偏差和重量偏差,在中批量生产的铸件,采用 2级精度铸件,查 金属机械加工工艺人员手册 5单边余量一般在 1-4mm之间。毛坯图如下图 1所示: 图 1 毛坯图 Fig l Blank drawing nts4 2.2 工艺路线的拟定 2.2.1 加工工艺过程 由以上分析可知,该拨叉零件的主要加工表面是平面、孔系和槽系。一般来说,保证平面的加工精度要比保证孔系的 加工精度容易。因此,对于拨叉来说,加工过程中的主要问题是保证孔的尺寸精度及位置精度,处理好孔和平面之间的相互关系以及槽的各尺寸精度。由上面的一些技术条件分析得知:拨叉的尺寸精度,形状精度以及位置关系精度要求都不是很高,这样对加工要求也就不是很高。一个好的结构不但应该达到设计要求,而且要有好的机械加工工艺性,也就是要有加工的可能性,要便于加工,要能保证加工的质量,同时使加工的劳动量最小。设计和工艺是密切相关的,又是相辅相成的。对于我们设计拨叉的加工工艺来说,应选择能够满足平面孔系和槽加工精度要求的加工方法及设 备。除了从加工精度和加工效率两方面考虑以外,也要适当考虑经济因素。在满足精度要求及生产率的条件下,应选择价格较低的机床。 2.2.2 定位基准的选择 基准选择是工艺规程设计中的重要工作之一。基准选择得正确与合理可以使加工质量得到保证, 生产率得以提高。否则,加工工艺过程中会问题百出,更有甚者,还会造成零件的大批报废,使 生产无法正常进行。 ( 1)粗基准的选择。对于零件而言,尽可能选择不加工表面为粗基准。而对有若干个不加工表面的工件,则应以与加工表面要求相对位置精度较高的不加工表面作粗基准。根据这个基准选择原则, 选择主轴孔两端面,螺纹孔端面,大头端半圆两端面作为粗基准。 ( 2)精基准的选择。 选择精基准 应遵循 基准重合的原则,尽可能选择被加工表面的设计基准为精基准。先选择铣好的凹槽端面和半精铣大头端半圆面作为钻主轴孔的精基准;根据精基准互为基准和自为基准的原则,在后续的加工过程中,选择表面质量高的作为精基准,这样可以有效的减小定位误差。 2.2.3 零件各加工面的加工方法的选择 分析毛坯图 1,可以知道零件需要加工的有:平面、孔、槽和内圆弧。 在加工开始之前,要进行必要的清洗热处理工序,以改变毛坯的切削性能。根据工序顺序的安排中,先加工基准面,再加工其他表面;先加工平面,后加工孔;先加工主要表面,后加工次要表面;先安排粗加工工序,后安排精加工工序的原则,所以选择先加工零件基准面,再加工零件主轴孔, 再加工凹槽, 最后 攻 螺纹孔。 在选择加工方法时,应该考虑所选加工方法能否满足其精度要求以及零件材料的nts5 可加工性能如何,还应该考虑生产率和工厂现有设备情况。由于 零件材料为 HT200,宜采用切削加工,而不宜采用磨削加工,因而,在安排工序过程中应尽量少安排磨削加工。在选择加工路线时,根据零件的工作环境和精度要求,可以不必经过精密或高精密加工即可。 参考机械制造工艺设计简明手册,其加工方法选择如下: ( 1)主轴两端面: 加工后零件达到的要求, 公差等级为 IT12, 表面粗糙度为 6.3,采用的加工方法为铣削 。 ( 2)螺纹端面:加工后零件达到的要求, 公差等级为 IT12, 表面粗糙度为 6.3,采用的加工方法为铣削 。 ( 3)凹槽端面:加工后零件达到的要求, 公差等级为 IT12, 表面粗糙度为 6.3,采用的加工方法为铣削 。 ( 4)主轴孔:加工后零件达到的要求, 公差等级为 IT7, 表面粗糙度为 1.6,采用的加工方法为 钻扩粗铰 精 铰 。 ( 5)凹槽: 加工后零件达到的要求, 公差等级为 IT9, 表面粗糙度为 3.2,采用的加工方法为 粗铣半精铣。 ( 6) 大头端半圆两端面 :加工后零件达到的要求, 公差等级为 IT9, 表面粗糙度为 3.2,采用的加工方法为 粗铣半精铣。 ( 7) 大头端 半圆面:加工后零件达到的要求, 公差等级为 IT9, 表面粗糙度为 3.2,采用的加工方法为 粗铣半精铣。 ( 8)螺纹孔:采用的加工 方法为 钻孔攻螺纹。 选择上述加工路线的好处是:由于零件是中批量生产,因此工序分散对于提高零件精度和生产效率都起着很大的作用。若选用工序集中,其优点是工作适应性强,转产相对容易,但设备昂贵。 2.2.4 加工工艺路线方案的比较 工艺路线方案一: 工序 10: 钻、扩、铰、精铰 主轴孔 、 大头端 孔 工序 20: 铣 主轴孔 、 大头端 孔 下端面 工序 30: 铣 主轴 孔上端面 工序 40: 铣 大头端 孔上端面 工序 50:切断 工序 60:铣螺纹孔端面 nts6 工序 70: 钻 22 孔 工序 80: 攻 M22 1.5螺纹 工序 90: 铣槽所在的端面 工序 100: 粗铣 、 半精铣 16H11的槽 工序 110:检查 上面的工序加工不太合理,因为由经验告诉我们大多数都应该先铣平面再加工孔,那样会更能容易满足零件的加工要求,效率不高,但同时钻两个孔,对设备有一定要求。且看另一个方案。 工艺路线方案二: 工序 10:铣 主轴孔上端面 工序 20:铣 主轴孔下端面 工序 30:钻 、 扩 、 铰 、 精铰 主轴孔 工序 40: 扩 、 铰 大头端孔 工序 50:粗 、 半 精铣 大头端 孔上端面 工序 60:粗 、 半 精铣 大头端孔下端面 工序 70: 切断 工序 80: 铣螺纹孔端面 工序 90:钻 22 孔 工序 100:攻 M22 1.5螺纹 工序 110:铣槽所在的端面 工序 120:粗 、 半精铣 16H11的槽 工序 130: 检查 上面工序可以适合大多数生产,但 是把主轴孔和大头端孔的上下两端面分开来铣,定位比较麻烦,再看另一方案。 工艺路线方案三: 工序 10: 铣 主轴孔上端面 工序 20: 铣 主轴孔下端面 工序 30: 钻 、 扩 、 铰 、 精铰 主轴孔 工序 40:扩、 铰 大头端孔 工序 50: 粗 、 半 精铣 大头端 孔上端面 工序 60: 粗 、 半 精铣 大头端孔下端面 nts7 工序 70:铣螺纹孔端面 工序 80: 钻 22 孔 工序 90: 攻 M22 1.5螺纹 工序 100:铣槽所在的端面 工序 110: 粗 、 半精铣 16H11的槽 工序 120:切断 工序 130:检查 此方案仍有先钻孔再铣平面的不足,所以这个方案仍不是最好的 工艺路线综合考虑以上各方案的各不足因素,得到以下 的工艺路线。 工艺路线方案四 : 工序 10:清砂 工序 20:退火 工序 30: 铣 主轴孔两端面 工序 40:钻工艺孔 工序 50: 铣 螺纹孔端面 工序 60:铣凹槽端面 工序 70:粗铣凹槽 工序 80:粗铣大头端半圆两端面 工序 90:粗铣大头端半圆面 工序 100:半精铣大头端半圆两端面 工序 110:半精铣大头端半圆面 工序 120:钻主轴孔 工序 130:扩主轴孔 工序 140:粗铰主轴孔 工序 150:钻螺纹孔 工序 160:半精铣凹槽 工序 170:精铰主轴孔 工序 180:攻螺纹孔 工序 190:清洗 工序 200:时效处理 工序 210:检查,入库 nts8 此方案符合大批量生产的工序分散原则,对于提高零件精度和生产效率都起着很大的作用。零件加工完成后,应进行时效处理,以减小切削加工时产生的变形和内应力影响。由于零件在整个工作过程中受力不大,且许多面根本不参与工作,所以,不必安排淬火等其他特殊的热处理工艺,以节省工作时间和提高生产效率。 2.3 机械加工余量、工序尺寸及公差的确定 根据工艺规程,加工主轴孔时分为钻,扩,粗铰,精铰。钻削加工时为实体,则毛坯的余量就是钻头的直径,通过查表选择钻头直径为 23,查表分别可得各工序加工余量、工序间尺寸及公差,见表 1: 表 1 加工孔的工序余量及公差 Table 1 Processing hole working procedure remainder and common difference 工序名称 工序余量 工序间精度 表面粗糙度 工序间尺寸 尺寸、公差 ( mm) ( mm) (um) ( mm) (mm) 粗铰、精铰 0.2 H7 Ra1.6 25 250.0210 扩 1.8 H8 Ra3.2 24.8 24.80.20 钻削 23 H11 Ra12.5 23 230.130 毛坯 实体 加工槽时同样也是毛坯为实体,所以毛坯的加工余量就是铣刀的宽度,通过查表分别可得下面的各工序的加工余量、工序尺寸及其公差,见表 2: 表 2 加工槽的工序余量及公差 Table 2 Processing the trough the working procedure remainder and common difference 工序名称 工序余量 工序间精度 表面粗糙度 工序间尺寸 尺寸、公差 ( mm) ( mm) (um) ( mm) (mm) 半精铣 1 H11 Ra3.2 16 160。 130 粗铣 15 H12 Ra12.5 15 150。 30 毛坯 实体 在铣削加工半圆面时,由于其本身的经济精度要求不是很高,所以选择的加工余量相对也就较大,具体选择见下表 3: 表 3 加工半圆的工序余量及 公差 Table 3 Processing semicircle working procedure remainder and common difference 工序名称 工序余量 工序间精度 表面粗糙度 工序间尺寸 尺寸、公差 ( mm) ( mm) (um) ( mm) (mm) 半精铣 1 H12 Ra3.2 60 600.30 粗铣 4 H12 Ra12.5 59 590。 30 毛坯 2 Ra25 55 55 nts9 2.4 切削用量及时间定额的确定 2.4.1 切削用量的确定 在保证加工质量的前提下,为了充分利用刀具和机床的性能,获得高生产效率和低加工成本的切削用量三要素的最佳组合,切削用量的选择得合理。而在选择合理切削用量时,必须考虑加工性质。由于粗加工和精加工要完成的加工任务和追求的目标不同,因而切削用量选择的基本原则也不完全相同。 粗加工时高生产效率是追求的基本目标,这个目标常用单件机动工时最少或单位时间切除金属体积最多来表示。而精加工时切削用量的选择首先要保证加工精度和表面质量,同时兼顾必要的刀具使用寿命和生产效率。 切削用量有三要素,即背吃刀量 切削深度 ap、进给量 f 和切削速度 vc。 因此,选择切削用量时,就是要确定具体工序的背吃刀量 ap、 进给量 f 和切削速度 vc。 根据切削用量的选择原则和工艺规程的编制中刀具的选择,通过查表,选择各工序的切削用量的确定参数如下: 工序 30、 50、 60:每齿进给量 sz=0.1,铣削速度 v=41,切削深度 t=3; 工序 40: n=534, s=0.2, v=40.3; 工序 70:每齿进给量 sz=0.1, 铣削速度 v=42, 切削深度 t=3.0 工序 80:每齿进给量 sz=0.05, 铣削速度 v=215, 切削深度 t=3.0 工序 90:每齿进给量 sz=0.1, 铣削速度 v=42, 切削深度 t=1.0 工序 100:每齿进给量 sz=0.05, 铣削速度 v=215, 切削深度 t=1.0 工序 110: 140:转速 n=575,进给量 s=0.18,切削速度 v=43.3; 工序 120:进给量 s=0.1, 切削深度 t=2.0 工序 130:进给量 s=0.1, 切削深度 t=0.5 工序 150:每齿进给量 sz=0.08, 铣削速度 v=102,切削深度 t=5.0 工序 160:每齿进给量 sz=0.08, 铣削速度 v=102,切削深度 t=3.0 工序 170:进给量 s=0.1, 切削深度 t=0.5 工序 180:每齿进给量 sz=0.6, 切削深度 t=20.3 根据以上各参数,通过计算或查表,选择各道工序的切削用量如下: 工序 30、 50、 60、 160、 100、 70、 80的切削用量为 3mm; 工序 40的切削用量为 8mm 工序 90、 100的切削用量为 1mm 工序 120的切削用量为 2mm nts10 工序 170的切削用量为 0.5mm 工序 180的切削用量为 1.5mm 2.4.2 时间定额 时间定额是工艺堆积的重要组成部分,需要根据实际的生产条件和情况来制定,以免产生不良后果。如果时间定额定得过紧,容易诱发忽视产品质量的倾向,或者会影响工人的主动性、创造性和积极行;若时间定额定得过松,就起不到指导生产和促进生产发展的积极作用。因此,合理的制定时间定额对保证产品的质量,提高劳动生产率,降低生产成本都十分重要。 时间定额的组成包括以下五个部分,基本时间 t 基 、 辅助时间 t 辅 、 布置工作 地时间 t 布置 、 休息 时间 t 休 及准备于终结时间 t 准终 , 基本时间 t 基 和 辅助 时间 t 辅 为操作时间。 在计算时间定额时先计算单件时间和单件工时定额。 单件时间: T 单件 = t 基 + t 辅 + t 布置 + t 休 (1) 单件工时定额: T 定额 = T 单件 + T 准终 /n (2) 由于此零件在生产过程中是大量生产,所以 T 准终 /n可忽略 即: T 定额 = T 单件 (3) 由于零件加工过程中,包括了 16道工序,其中包括钻、镗。铣和攻螺纹,查手册可得如下公式: 钻工艺孔: t 基 1 = (l + l1) / sn (4) 钻主轴孔时: t 基 2 = (l + l1+ l2) / sn t = D / 2 (5) 镗孔时 : t 基 3 = Li / sn 式中 L = l + l1+ l2+ l3 (6) 铣削加工时: t 基 4 = (l + l1+ l2) i / sM (7) 以上 式中, i = Z / ap (8) D 孔的直径 (毫米); L 工作台的行程长度 (毫米); l 加工长度 (毫米); l1 切入长度 (毫米); l2 超出长度 (毫米); nts11 l3 附加长度 (毫米) ,单件小批生产条件下的试刀长度 ; s 主轴每转的进给量(转 /分) ; sM 工作台的进给量(毫米 /分) ; n 刀具或零件每分钟的转数(转 /分) ; i 进给次数 ; Z 加工余量(毫米) ; ap 背吃刀量(毫米) ; 根据 各工序的前面给定加工情况,选择相应的值,算出每道工序的基本时间,计算得总的基本时间 t 基 为 72min,选择每道工序的辅助时间为 1min,则可得总的辅助时间 t 辅 为 16min。 布置工作地时间 t 布置 按操作时间的 4%来计算,休息时间 t 休 按操作时间的 2%来计算,则可以算出单件时间为: T 单件 = t 基 + t 辅 + t 布置 + t 休 =93.28 min 取整数则 T 单件 = 94 分钟,则可得时间定额 T 定额 为 94 分钟。 3 专用夹具的设计 3.1 钻床夹具的设计 3.1.1 精度与批量分析 本工序有一定位置精度要求,属于批量生产,使用夹具加工是适当的。但考虑到生产批量不是很大,又因为由前面的工艺流程设计中已经知道,零件的主要作用是拨动齿轮改变传动比,所以为了节省工时及减少夹具制造成本,夹具结构应尽可能的简单。 3.1.2 夹具装配图的绘制 nts12 图 2 钻 床夹具装配 图 Fig 2 Assembly drawing of the drilling fixture 3.1.3 夹具设计方案的确定 要确定夹具结构,先必须确定定位方案,并选择定位元件。由于本工序加工要求保证的位置精度主要是孔本身的精度 25H7孔内表面粗糙度为 1.6um。根据基准重合原则,应以凹槽端面,大头端半圆面作为定位面比较合适。此时理论上应限制的自由度为 5个,故采用心轴,挡板定位;用菱形销以及螺母,垫圈夹紧。 由于本工序加工精度高,又为后续工序的定位基准,所以采用快换钻套,又考虑到要求结构简单且能保证精度,采用固定式钻模板。 选择夹紧机构时,理论上的夹紧方式使夹紧力作用在主要定位面上,而在本设计中夹紧需要较大,所以选择螺母与心轴,垫圈锁紧以及菱形销配合的夹紧机构,因为其夹紧行程不受限制,而且增力比较大,菱形销夹紧机构装有快撤螺旋夹紧装置,所以便于工件快速装卸。 夹具体的设计应全盘考虑,使上述各部分通过夹具体能有机地联系起来,形成一个完整的夹具。此外,还应考虑夹具与机床的连接,因为是在摇臂钻床上使用,夹具体可固定安装在工作台上。 3.1.4 夹紧力的计算 nts13 在工件定位 夹紧以后,必须选择合理的夹紧力大小,若夹紧力不足,会使工件在切削 过程中产生位移并容易引起振动,而夹紧力过大,又会造成工件或夹具不应有的变形或表面损伤,因此,应对所需的夹紧力进行估算。 切削力的确定:此工序为加工主轴孔,其中,在工件夹紧后,工件夹紧力方向与切削力方向垂直,所以所需的夹紧力较大,在加工过程中,工件需要克服的切削力额工件自身的重力,只能靠摩擦力来实现。 查金属机械加工工艺人员手册 5可知,钻削轴向力大小为: P = 81.2Ds0.7 (8) D 孔径(毫米) s 进给量 (毫米 /转) 通过前面工艺的编制可知 D = 25 s = 0.8 计算可得 P = 1736 公斤力 Fj = 2M / d2tg(a + 6035) 式中: M =31 Ds0.8 (9) D 孔径(毫米) Fj 夹紧力( 公斤力) M 作用扭矩( 公斤力 *毫米) d2 螺纹中径(毫米) a 螺纹升角 d2 = 20 a = 4.50 D = 25 s =0.8 计算可得夹紧力 W = 1796公斤力 计算作用在扳手上的力:查机械制造工艺学 1可知: FJ = FS L / 0.5 do tg(a + 1) + r tg 2 (10) FJ 沿螺旋轴线作用的夹紧力( N) FS 作用在扳手上的力( N) L 作用的力臂( mm) do 螺纹中径( mm) a 螺纹升角( o ) 1 螺纹副的当量摩擦角( o ) 2 螺母端部与压块的摩擦角( o ) r 螺母端部的压块的当量半径( mm) 由于螺钉的螺纹形状为三角螺纹,所以 1 = arctg(1.15tg 1),其中 1为摩擦角,且1 = arctg ( u ) 选取 L = 20 mm再通过查表可得, do = 20 mm = 0.2 m a =4.5o 2 = 0o r = 0 mm 查表选取 u = 0.15 则可计算得 1 = 9.790 ,又根据夹具受力的情况,可知: nts14 u FJ P + G G 工件自重( N) 由于工件相比夹具来说比较小,这里将工件自重忽略。 将以上数值代入式中,可以得 FS = 1485.6N 则作用在扳手上的力(当力臂 L为 20mm时) FS 应大于 1474N才能保证 工件在加工过程中不发生移动。 3.2 铣床夹具的设计 3.2.1 精度与批量分析 本工序是铣 凹槽,其零件本身有一定的位置精度要求,但精度不高( IT11),零件属于批量生产,所以使用夹具加工是适当的,而且通过零件工作原理,可以知道凹槽是零件工作的主要表面,零件是以本工序加工的槽来拨打齿轮改变传动比的。凹槽的中心线与主轴孔有垂直度要求。同样,零件生产批量也不是很大,所以应将夹具简单化,以节省工时和减少夹具制造成本。 3.2.2 夹具装配图的绘制 图 3 铣 床夹具装配 图 Fig 3 Assembly drawing of the milling fixture nts15 3.2.3 夹具设计方案的确定 在夹具结构的确定时,应先确定零件定位,并选择定位元件,由于槽的中心线与上一道工序加工中心有垂直度要求,根据基准重合原则,则选取心轴定位比较合适,但此时限制的自由度为 5个,而且还有一个重要的自由度没有限制,无法满足零件精度要求,因此,根据零件此时的结构,选择一菱形销将零件完全定位。 由于本工序切削深度较深,一次装夹完成后,要分几次走刀才能达到零件深度要求,由于刀具安装不可能一次安装既可保证零件尺寸,所以,夹具应具备对刀元件,根据所加工零件的形状为槽,选择直角对刀块。 选择夹紧机构时,理论上的夹紧方式应使夹紧力作用在主要定位面上,采用心轴定位,夹紧力与方向一致,由于零件批量不是很大,所以,为了简化零件的结构,仍然采用螺纹夹紧,而且可以直接在心轴上作出一段螺纹,并用螺母和开口垫圈锁紧。 由于铣削加工的切削力较大,又是断续切削,加工中易引起振动,因此。其夹具体要承受较大的切削力,夹具体的设计应全盘考虑,使上述各部分能有机地联系起来,形成一个完整的夹具,此外,还应考虑夹具与机床的联接。 3.2.4 夹紧力的计算 铣床夹具与钻床夹具的夹紧方式大致相同,但采用心轴定位,铣削时受 到水平和垂直的二个力,而且心轴定位在平面内,切削力主要靠心轴的刚度来克服,在这里夹紧力起的主要作用是防止工件在心轴上的移动。 查表得夹紧力公式 1: Fj = 2M / d2tg(a + 6035 ) 式中: M = 31Ds0.8 D 孔径(毫米) M 作用扭矩( 公斤力 *毫米) d2 螺纹中径(毫米) a 螺纹升角 s 进给量 (毫米 /转) d2 = 16 a = 4.50 D = 16 s =0.8 计算可得夹紧力 W = 587公斤力 本夹具采用的也是螺纹夹紧机构,查表夹紧力公式 1为: FJ = FS L / 0.5 do tg(a + 1 ) + r tg 2 FJ 沿螺旋轴线作用的夹紧力( N) FS 作用在扳手上的力( N) L 作用的力臂( mm) nts16 do 螺纹中径( mm) a 螺纹升角( o ) 1 螺纹副的当量摩擦角( o ) 2 螺母端部与压块的摩擦角( o ) r 螺母端部的压块的当量半径( mm) 由于螺钉的螺纹形状为三角螺纹,所以 1 = arctg(1.15tg 1),其中 1为摩擦角,且1 = arctg ( u ) 通过查表可得: do = 16 mm a =4.5o 2 = 0o r = 0 mm 查表选取 u = 0.1 则可计算得 1 = 6.560 将以上数值代入式中,可以得 FS = 526N 3.2.5 心轴的强度校核 在铣床夹具上,心轴起到定位和夹紧的作用,为了保证铣凹槽的精度,需对心轴进行强度的校核。由铣床夹具装配图可知,心轴主要承受弯矩的作用,分别按水平和垂直面上的弯矩计算各力产生的弯矩, 并按下式计算总弯矩: M = MH2 +MV2 (11) MH = FH D/2 ( 12) MV = FV D/2 ( 13) 已知轴的弯矩后 ,可针对某些危险截面(即弯矩大而轴径可能不足的截 面)做弯矩合成强度校核计算。按第三强度理论,计算应力 ca = 2 +42 ( 14) 通常由弯矩所产生 所产生的弯曲应力 是对称循环变应力,而由扭矩所产生的扭转切应力 则常常不是对称循环变应力,为了考虑两者循环特性不同的影响,引入折合系数 a,则计算应力为 ca = 2 +42 ( 15) 式中的弯曲应力为对称循环变应力。当扭转切应力为静态时,取 a 0.3,当扭转切应力为脉动循环变应力时,取 a 0.6,若扭转切应力亦为对称循环变应力时,则取 a 1. 对于直径为 d的圆轴,弯曲应力为 = M/W,扭转切应力 =T/WT =T/2W,将 和 代入式( 14),则轴的弯扭合成强度条件为 ca = 2 +()2/W -1 ( 16) nts17 式中: ca 轴的计算应力, MPa; M 轴所受 的弯矩, N .mm T 轴所受 的弯矩, N .mm W 轴的抗弯截面系数, mm3,计算公式如下: W = 3/32 0.1d3 , WT = 3/16 0.2d3 , ( 17) -1 对称循环变应力时轴的许用弯曲应力, 其值按表( 15-1) 9选用, 查得其值 极限为 275MPa,即 -1 =275MPa, 由于心轴工作时只承受弯矩而不承受扭矩,所以在应用式( 16)时,应取 T = 0。 故 ca = M / W ,代入数值得 ca = 215.37,由此可知 ca -1 , 因此 心轴的强度满足设计的要求。 4 结论 从去年开始弄毕业设计 至今日,设计基本完成。从最初的茫然,到慢慢的进入状态,再到对思路逐渐的清晰,整个设计过程难以用语言来表达。历经了几个月的奋战,紧张而又充实的毕业设计终于落下了帷幕。回想这段日子的经历和感受,我感慨万千,在这次毕业设计的过程中,我拥有了无数难忘的回忆和收获。 通过这次毕业设计,使我对零件制造过程、加工工艺和夹具设计都有了更进一步的认识,也加深了对大学四年中所学基础知识的学习和理解。毕业设计是理论联系实际的最有效方法。在具体设计过程中,必须考虑到方方面面的问题,在理论上正确无误的设计,在实际中往往存在各种问题。 这样,在设计时就必须考虑所设计的机构是否合理,在实际运用中能否正常工作。这次毕业设计使我初步学会了从实际出发来加工零件和设计夹具。 在本次设计中,考虑到零件的加工难易、材料、成本等问题,所选用的零、部件都是操作简单,通用性较强的标准件,从现时以最低的成本实现最先进的加工。本次设计从零件的毛坯生产到最终成品,中间经过了铣、钻等工序。在夹具设计中,先确定工件的基准,然后将其定位好,再将工件固定夹紧在夹具上。计算夹紧力以及误差等,最后再通过 AutoCAD进行零件图和装配图的绘制。整个设计过程将我以前学过的机械制造 工艺、公差与配合、机械制图、工程材料与热处理工艺等知识很好的串联了起来,巩固了所学知识,提高了我的学习能力。在本次设计中已无大的问题,基本达到了要求。但是也有存在一些不足之处: ( 1)进行工艺设计时思路不够开阔,提出的方案较少,对零件的定位了解不够 ( 2)在夹具的设计中没有能提出多中方案进行分析比较,有所不足。 nts18 ( 3)对工艺规程相关知识了解欠缺,许多知识学习不到位; 综上所述,这次的毕业设计使我获益良多,在今后的工作和学习中,要把所学的知识和实际紧密的结合起来,不仅提高自己的理论知识,更要提高自己的动手能力 。 参考文献 1 王先逵 .机械制造工艺学 M.北京:机械工业出版社, 2010. 2 全腊珍,张淑娟 .画法几何与 机械制图 M北京: 中国农业 出版社, 2007. 3 朱张校 .工程材料 M.北京:清华大学出版社, 2008. 4 薛源顺机床夹具手册 M.北京:机械工业出版社, 2008. 5 赵如福 .金属机械加工工艺人员手册 M.上海:上海科学技术出版公司, 2008. 6 孙桓 .机械原理 M.北京:高等教育出版社, 2008. 7 成大先 .机械设计手册 第四卷 M.北京:化学工业出版社, 2007. 8 刘家仁 .机械设计常用元件手册 M.北京:机械工业出版社, 2007. 9 濮良贵,纪名刚 .机械设计 M.北京:高等教育出版社 , 2006.5 10 王光斗 .机床夹具设计手册 M.上海科学技术出版社, 2002 8 致 谢 本论文是在陈志亮老师的悉心指导和热情关怀下完成的。在毕业设计即将结束之际我向所有帮助过我的老师和同学说一声:谢谢!我想没有他们的帮助,毕业设计就会做得很困难。陈老师以其渊博的学识、严谨的治学风范、高度的责任感使我受益非浅。在做设计的过程中也遇到了不少的问题,陈老师给了我许多关怀和帮助,并且随时询问我毕业设计的进展情况、细心的指导我们,在此对陈老师表示衷心的感谢。 最后,在即将完成毕业设计之时,我再次感谢对我指导、关心和帮助过老师、领导及同学。 附录 附录 1:机械加工工艺过程卡片 附录 2:机械加工工序卡片 附录 3: CA6140车床拨叉的铣床夹具装配图 nts19 附录 4: CA6140车床拨叉的钻床夹具装配图 附录 5:铣床夹具体零件图 附录 6:对刀块零件图 附录 7:拨叉零件图 附录 7:螺纹导向元件零件图 nts湖南农业大学 东方科技学院 毕业论文(设计) 开题论证记录 系 部 : 工程技术系 学生姓名 学 号 年级专业及班级 200 级 机械设计制造及其自动化 ( ) 班 指导教师姓名 陈志亮 指导教师职称 副教授 论文(设计)题目 论证 小组质疑 及指导意见 : 学生 回答 简要记录: 论证 小组 成员签名 记录人 签名: 论证日期 : 年 月 日 注: 记录、签名栏必须用黑色笔手工填写。 nts湖南农业大学东方科技学院毕业论文(设计)中期检查表 学 部: 理工学部 学生姓名 曾双成 学 号 200741914225 年级专业及班级 2007级机械设计制造及其自动化 (2)班 指导教师及职称 陈志亮 副教授 毕业论文(设计)题目 车床拨叉加工工艺及其夹具设计 毕业论文(设计)工作进度 已完成的主要内容 尚需解决的主要问题 指导教师意见 指导教师签名: 年 月 日 检查(考核)小组意见 检查小组组长签名: 年 月 日 nts湖南农业大学东方科技学院毕业设计开题论证审批表 学生姓名 曾双成 学号 200741914225 年级专业及班级 2007 级机械设计制造及其自动化 (2)班 指导教师及职称 陈志亮 副教授 开题时间 年 月 日 毕业论文(设计)题目 车床拨叉加工工艺及其夹具设计 文献综述(选题研究意义、国内外研究现状、主要参考文献等) 选题研究意义 随着我国改革开放的不断深入,市场经济体系的不断完善,我国工业逐渐向成熟化发展。在整个机械工业中,设计在其中占有的地位日益显现出来。工业设计主要包括三个方面的内容。第一是产品设计 ,第二是与产品有关的视觉传达设计。第三是由产品设计扩展的环境设计。产品设计作为工业设计的核心,它涉及的面广,从人们的衣食住行,到社会的各行各业,产品设计无时不有,无时不在。产品设计的对象既包括一般的日用生活制品,也包括工业生产的机床,加工工具;既包括家用小电器产品,也包括专业的仪器,仪表;既包括私有的自行车,摩托车,也包括大型的汽车, 飞机等交通工具;“从口红到宇宙飞船”都是属于产品的设计的范畴,本论文主要针对加工工具设计,在一定范围内又称“加工辅助设计”,即机床夹具体的设计。机床夹具设计是工艺装备设计中的一个重要组成部分,是保证产品质量和提高劳动生产率的一项重要技术措施。本次夹具设计主要的目的在于缩短辅助时间,提高劳动生产率;可靠稳定定位,提高了加工精度的稳定性,便于实现工艺过程自动化;扩大机床使用范围;降低对工人技术等级要求和减轻工人劳动强度。 国内外研究现状 现在,各工业化国家都把制造技术视为当代科技发展为活跃的领域和国际间科技竞争的
- 温馨提示:
1: 本站所有资源如无特殊说明,都需要本地电脑安装OFFICE2007和PDF阅读器。图纸软件为CAD,CAXA,PROE,UG,SolidWorks等.压缩文件请下载最新的WinRAR软件解压。
2: 本站的文档不包含任何第三方提供的附件图纸等,如果需要附件,请联系上传者。文件的所有权益归上传用户所有。
3.本站RAR压缩包中若带图纸,网页内容里面会有图纸预览,若没有图纸预览就没有图纸。
4. 未经权益所有人同意不得将文件中的内容挪作商业或盈利用途。
5. 人人文库网仅提供信息存储空间,仅对用户上传内容的表现方式做保护处理,对用户上传分享的文档内容本身不做任何修改或编辑,并不能对任何下载内容负责。
6. 下载文件中如有侵权或不适当内容,请与我们联系,我们立即纠正。
7. 本站不保证下载资源的准确性、安全性和完整性, 同时也不承担用户因使用这些下载资源对自己和他人造成任何形式的伤害或损失。

人人文库网所有资源均是用户自行上传分享,仅供网友学习交流,未经上传用户书面授权,请勿作他用。