人人文库网 > 图纸下载 > 毕业设计 > 东方之子1.8轿车5挡变速器设计【汽车毕业设计含7张CAD图+说明书论文2.1万字68页,带三维图,开题报告,任务书】
东方之子1.8轿车5挡变速器设计【汽车毕业设计含7张CAD图+说明书论文2.1万字68页,带三维图,开题报告,任务书】
收藏
资源目录
压缩包内文档预览:
编号:484175
类型:共享资源
大小:14.83MB
格式:ZIP
上传时间:2015-11-05
上传人:小***
认证信息
个人认证
林**(实名认证)
福建
IP属地:福建
50
积分
- 关 键 词:
-
东方
之子
轿车
变速器
设计
汽车
毕业设计
cad
说明书
仿单
论文
68
三维
开题
报告
讲演
呈文
任务书
- 资源描述:
-
CL055-东方之子1.8轿车5挡变速器设计【汽车毕业设计含7张CAD图+说明书论文2.1万字68页,带三维图,开题报告,任务书】
【包含文件如下】【汽车车辆工程类】CAD图纸+word设计说明书.doc[21000字,68页]【需要咨询购买全套设计请加QQ97666224】.bat
一档从动齿轮.dwg
三档主动齿轮.dwg
三档从动齿轮.dwg
三维图纸全套
倒挡从动齿轮.dwg
装配图.dwg
输入轴.dwg
输出轴.dwg
任务书.doc
03.开题报告.doc
设计说明书.doc[21000字,68页]
目 录
摘要Ⅰ
AbstractⅡ
第1章 绪 论1
1.1选题目的及意义1
1.2国内外研究现状1
1.3国内外研究方法2
1.4设计内容及方法3
1.5汽车变速器的设计要求4
第2章 变速器总体方案设计5
2.1变速器传动机构布置方案分析5
2.1.1变速器选择5
2.1.2档位布置6
2.2倒挡布置方案7
2.3零、部件结构方案分析8
2.3.1齿轮形式8
2.3.2变速器轴承的选择8
2.3.3操纵机构的布置8
2.3.4 换挡机构形式9
2.3.5自动脱挡9
2.4本章小结10
第3章 变速器的设计与计算11
3.1变速器主要参数的选择11
3.1.1传动比范围11
3.1.2 初选中心距13
3.1.3变速器的外形尺寸13
3.1.4齿轮参数选择13
3.2各挡齿轮齿数的分配及传动比的计算14
3.2.1一挡齿数及传动比的确定14
3.2.2二挡齿数及传动比的确定15
3.2.3计算三挡齿轮齿数及传动比15
3.2.4计算四挡齿轮齿数及传动比16
3.2.5计算五挡齿轮齿数及传动比16
3.2.6计算倒挡齿轮齿数及传动比16
3.3齿轮变位系数选择和螺旋角的修正17
3.3.1计算一挡齿轮变位系数及螺旋角修正18
3.3.2计算二挡齿轮变位系数及螺旋角修正18
3.3.3计算三档齿轮变位系数及螺旋角修正19
3.3.4计算四档齿轮变位系数及螺旋角修正20
3.3.5计算五档齿轮变位系数及螺旋角修正20
3.3.6计算倒档齿轮变位系数及螺旋角修正21
3.4各挡齿轮主要参数的确定22
3.4.1一挡齿轮参数22
3.4.2二挡齿轮参数23
3.4.3三挡齿轮参数23
3.4.4四挡齿轮参数25
3.4.5五挡齿轮参数26
3.4.6倒挡齿轮参数27
3.5齿轮的校核29
3.5.1齿轮材料的选择原则29
3.5.2变速器齿轮的材料及热处理30
3.5.3变速器齿轮弯曲强度校核30
3.5.4齿轮接触应力校核34
3.6本章小结38
第四章 轴的设计及轴的强度校核39
4.1轴的结构尺寸设计39
4.2轴的校核40
4.2.1轴的刚度校核40
4.2.2轴的强度校核47
4.3轴承选择与寿命计算50
4.3.1变速器输入轴工作时51
4.3.2变速器输出轴工作时52
4.4本章小结53
第五章 变速器同步器及壳体的设计54
5.1同步器的功用及分类54
5.1.1惯性式同步器54
5.2 同步器主要尺寸的确定56
5.2.1 摩擦因数56
5.2.2同步环主要尺寸的确定57
5.2.3 锁止角58
5.3变速器壳体58
5.4本章小结58
第6章 变速器操纵机构59
6.1直接操纵手动换挡变速器59
6.2远距离操纵手动换挡变速器59
6.3本章小结60
结 论61
参考文献62
致 谢63
附 录64
附录1 PRO/E实体建模64
附录2英文文献69
附录3文献翻译71
摘 要
变速器是汽车传动系统中比较关键的部件,它的设计好坏将直接影响到汽车的实际使用性能。变速器用来改变发动机传到驱动轮上的转矩和转速,目的是在原地起步,爬坡,转弯,加速等各种行驶工况下,使汽车获得不同的牵引力和速度,同时使发动机在最有利工况范围内工作。变速器设有空挡和倒挡。需要时变速器还有动力输出功能。
因为变速箱在低档工作时作用有较大的力,所以一般变速箱的低档都布置靠近轴的后支承处,然后按照从低档到高档顺序布置各档位齿轮。这样做既能使轴有足够大的刚性,又能保证装配容易。变速箱整体结构刚性与轴和壳体的结构有关系。一般通过控制轴的长度即控制档数,来保证变速箱有足够的刚性。
本文设计研究了两轴式五挡手动变速器,对变速器的工作原理做了阐述,变速器的各挡齿轮和轴做了详细的设计计算,并进行了强度校核,对一些标准件进行了选型。变速器的传动方案设计并讲述了变速器中各部件材料的选择。
关键字:变速器;传动比;齿轮;轴;强度校核






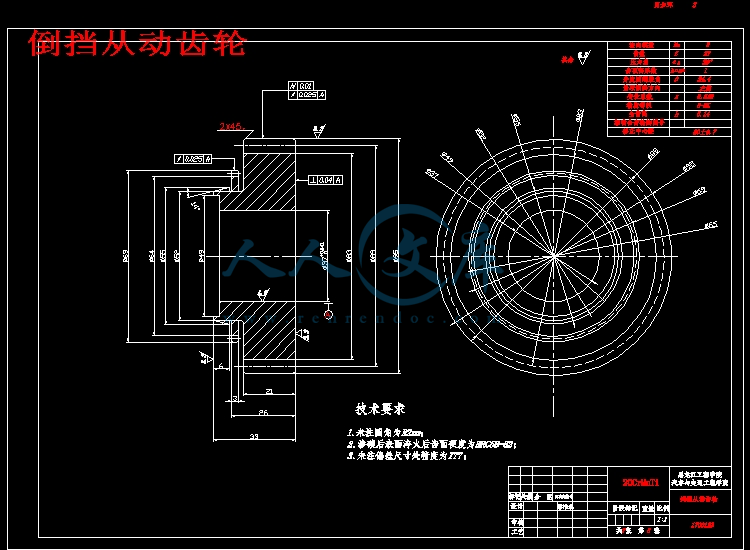

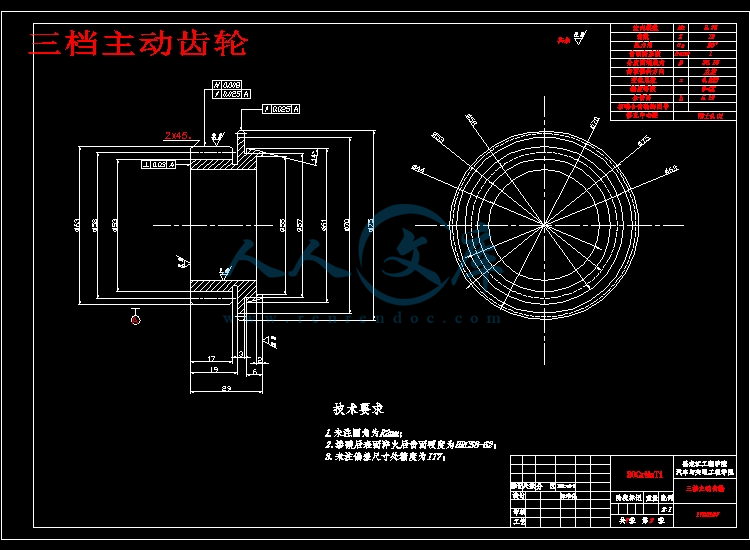



- 内容简介:
-
1 第 1 章 绪 论 随着科学技术的不断进步,汽车工业相应得到了迅速发展。 特别是从汽车的大批量生产及汽车工业的大发展以来,汽车已为世界经济的发展、为人类进入现代生活,产生了无法估量的巨大影响, 为人类社会的进步做出了不可磨灭的巨大贡献,掀起了一场划时代的革命 ElI。 1.1 选题目的及意义 自从汽车采用内燃机作为动力装置开始,变速器就成为了汽车重要的组成部分, 现代汽车上广泛采用的往复活塞式内燃机具有体积小、质量轻、工作可靠和使用方便等优点,但其转矩和转速变化范围较小,而复杂的使用条件则要求汽车的牵引力和车速能 在相当大的范围内变化,故其性能与汽车的动力性和经济性之间存在着较大的矛盾,这对矛盾靠现代汽车的内燃机本身是无法解决的。因此,在汽车传动系中设置了变速器和主减速器,以达到减速增矩的目的。 变速器设有空挡和倒挡。需要时变速器还有动力输出功能。 本次设计车型 变速器可以在汽车行驶过程中在发动机和车轮之间产生不同的变速比,换档可以使得发动机工作在其最佳的动力性能状态下。变速器通过离合器与发动机相连,变速器的输入轴就可以和发动机达到同步转速。 通过本次变速器的设计可以使我们更好的了解变速器的构造和设计方法,把我们大学所学的 知识连成线,穿在一起,让我们运用的更加熟练;并根据所确定的参数设计出了变速器的结构,在设计的过程中注重了变速器的合理性与实用性,最后画出了变速器的工程图,同时也为我们以后的工作打下了良好的基础,锻炼了我们的动手和实践能力,让我们的学习生活变的更有意义。 1.2 国内外研究现状 近年来,随着微电子技术的飞速发展,电子控制自动变速器的问世,给汽车带来了更理想的传动系统。机电一体化技术进入汽车领域,推动汽车变速器装置的重大变革。自动变速器装置出现了电子化趋势,特别是大规模集成电路技术的发展,使由微机控制发动机和变速 器换挡成为可能。 目前,在汽车上所使用的自动变速器主要有以下几类:液力自动变速器、电子控制机械自动变速器和机械无级自动变速器。液力自动变速器( Automatic Transmission 或 Automatic Transaxle, AT)的基本形式是液力变矩器与动力换档的旋转轴式机械变速器串联。从 50 年代起,装备液力自动变速器的轿nts 2 车开始增多,但由于其效率明显低于机械变速器,而且结构复杂,成本高,从而限制了它的发展。 60 年代的研究重点是采用多元件工作轮来提高液力变矩器的效率。 70年代是使用闭锁离合器提高变速器在高 速时的效率。 80 年代则采用增加行星齿轮变速器档位的方法及使用电子控制。 90 年代,大量电子技术的应用,使液力自动变速器的发展进入了一个新的时期,综合性能有了较大的提高。如今,液力自动变速器在汽车上的装备率,美国为 90%,日本为 80%11。 电子控制机械自动变速器是一种由普通齿轮式机械变速器组成的有级机械自动变速器。作为汽车关键总成之一,变速器技术在汽车诞生的百年历史中在不断地与时俱进。手动变速器由于其传递动力的直接与高效性,加上制作技术的成熟与低成本,现代汽车中装备手动变速器的汽车仍然占有很大比例。但随着人 们对汽车舒适性要求越来越高,现代汽车自动变速器装备率越来越高却是一个不争的事实,尤其是当自动变速器也逐渐能够兼顾操控性的时候。但,传统自动变速器技术却由于其效率的低下而在等待一场革命 4。 1.3 国内外研究方法 我国的汽车及各种车辆的零部件产品在性能和质量上和发达国家存在着一定的差距,发达国家再机械产品设计上早已进入了分析阶段,他们利用计算机辅助设计技术,将现代设计方法,如有限元分析、优化设计、可靠性设计等应用到产品设计中,采用机械 CAD 系统在计算机上进行建模、分析、仿真、干涉检查、实现三维设计,大大地提 高产品设计的一次成功率,减少了试验费用,缩短了产品更新周期。而我们的设计手段仍处于以经验设计为主的二维设计阶段,设计完成后在投产中往往要进行很大的改动,使得产品开发周期很长,性能质量低等。为改变我国的车辆零部件的生产和设计手段的落后状况,缩短新产品的开发周期,提高市场竞争力,有必要开发一些适合中国国情的汽车及零部件的 CAD 系统,对已开发的 CAD 系统需进一步提高和完善。 美国的 CAD 技术一直处于领先地位,其主要目标就是建立完善的 CAD/CAM 集成系统。美国汽车工业最早应用了 CAD 系统。美国通用汽车公司 、福特汽车公司等都已广泛应用 CAD 技术。他们将结构、强度、刚度等计算、三维实体造型应用于汽车的设计开发中,将 CAD、 CAM、 CAPP、 CAE 集成,是生产效率提高,产品质量得到保证,市场响应速度提高,从而大大地提高了他们的竞争力,为他们带来了巨大的经济效益。他们应用的 CAD 软件主要有 PRO/E、 UG、 CATIA、 IGES 等 11。 手动变速器的许多最近的发展集中在为降低成本和体积的新制造方法上。传统来说,变速器制造包含大量昂贵的机器,以及为机械加工和装配操作所需留出的空间限制的设计 15。最新的技术包括, 如在最新的 Ford Getra96 档变速器中可以看到的激光焊接冲压钢滑动齿轮选择轴套。为替代前一代变速器的铸铁拨叉,这种精致而坚固nts 3 的设计方案可以导致更少的对内部的损害。齿轮盘片的激光和摩擦焊接同时保证了所需机器设计空间的降低,这是一种由雷诺公司在 5 档副轴圆型变速器设计中发明的技术,命名为 EMI,曾在 2000 年展出并因为它的简单和轻便仅 22 公斤却能提供 140Nm的转矩而出名。另一方面,设计人员也在其齿轮提供转矩输出的设计上进行了认真的研究,提高了耐久性和低噪声水平 14。 1.4 设计内容及方法 根据车辆 的已知条件,运用汽车理论的知识进行设计。主要内容如下:图 1.1 图 1.1 设计系统 ( 1)对变速器传动机构的分析与选择 通过比较两轴和中间轴式变速器各自的优缺点,以及所涉及车辆的特点,确定传动机构的布置形式。 ( 2) 变速器主要参数的选择 齿轮变位系数确定 参数选择、零件设计 强度计算 轴的设计 同步器的设计 操纵机构、箱体设计 完成工程图纸 变速器的功用 结构方案的确定 变速器主要参数选择 传动比及齿数确定 布置方案的确定 齿轮 的损坏原因及形式 齿轮强度计算与校核 布置形式与主要参数 刚度和强度校核 nts 4 变速器主要参数的选择:挡数、传动比、中心距、齿轮参数等。 ( 3)变速器齿轮强度的校核 变速器齿轮强度的校核主要是针对变速器的齿根弯曲疲劳强度和齿面接触疲劳强度进行校核。 ( 4)轴的基本尺寸的确定及强度计算 对于轴的强 度计算原则是对轴的刚度和强度分别进行校核。 ( 5)轴承的选择和同步器的设计 对变速器轴的支撑部分选用圆锥滚子轴承,根据车辆的载质量和使用要求选择锁销式同步器,并确定同步器的尺寸参数。 ( 6)设计变速器的操纵机构 参考多方资料,设计了典型的操纵机构及其互锁装置。 ( 7)对变速器进行三维建模 利用利用 AutoCAD 软件完成装配图、零件图的绘制。 1.5 汽车变速器的设计要求 汽车变速器的基本设计要求:保证汽车有必要的动力性和经济性;设置空档,用来切断发动机动力向驱动轮的传输;设置倒挡,使汽车能倒退行驶;换挡迅速、 省力、方便;工作可靠,汽车行驶过程中,变速器不得有跳挡、乱挡,以及换挡冲击等现象出现;工作效率高,噪声小;结构简单、方案合理;在满载及冲击载荷条件下,使用寿命长;除此之外,变速器还应当满足轮廓尺寸和质量小、制造成本低、维修方便等要求。 nts 5 第 2 章 变速器总体方案设计 2 1 变速器传动机构布置方案分析 按其轴中心线的位置又分为固定轴线式、螺旋轴线式和综合式的。其中 固定轴式应用广泛,有 两轴式和三轴式之分, 前者多用于发动机前置前轮驱动的汽车上,而后者多用于发动机前置后轮驱动的汽车上。 2.1.1变速器选择 ( 1) 两轴式变速器 两轴式变速器如图 2-1 所示:因轴和轴承数少,所以有结构简单、轮廓尺寸小和容易布置等优点,此外,各中间档位因只经一对齿轮传递动力,故传动效率高同时工作噪声小。因两轴式变速器不能设置直接挡,所以在高档工作时齿轮和轴承均承载,不仅工作噪声增大,且易受损。对与前进挡,两轴式变速器输入轴的转动方向与输出轴的转动方向相反;而中间轴式变速器的第一轴与输出轴的转动方向相同。 当发动机纵置时,主减速器可用螺旋锥齿轮或双面齿轮;当发动机横置时则可用圆柱齿轮,从而简化了制 造工艺,降低了成本。除倒 挡 常用滑动齿轮(直齿圆柱齿轮)外,其他 挡均采用常啮合斜齿轮传动;各 挡 的同步器多装在第二轴上,这是因为一档的主动齿轮尺寸小,装同步器有困难;而高 挡 的同步器也可以装在第一轴的后端 1。 图 2.1 两轴式变速器 ( 2) 中间轴式变速器 nts 6 三轴式变速器如图 2.2 所示,其第一轴的常啮合齿轮与第二轴的各 挡 齿轮分别与中间轴的相应齿轮相啮合,且第一、第二轴同心。将第一、第二轴直接连接起 来传递扭矩则称为直接 挡 。此时,齿轮、轴承及中间轴均不承载,而第一、第二轴也传递转矩。因此,直接 挡 的传递效率高,磨损及噪音也最小,这是三轴式变速器的主要优点。其他前进档需依次经过两对齿轮传递转矩。因此。在齿轮中心距(影响变速器尺寸的重要参数)较小的情况下仍然可以获得大的一 挡 传动比,这是三轴式变速器的另一优点。其缺点是:处直接 挡 外其他各 挡 的传动效率有所下降 3。 图 2.2 轿车三轴式四档变速器 由于本次设计的东方之子变速器是中档轿车变速器,驱动形式属于发动机前置前轮驱动,且设计车速高,要求运行噪声低,故 选用二轴式变速器作为传动方案。 2.1.2 档位布置 二轴式变速器传动方案的特点是:变速器输出轴与主减速器主动齿轮做成一体,发动机纵置时,主减速器采用弧齿锥齿轮或准双面齿轮,发动机横置时则采用斜齿圆柱齿轮;多数方案得倒挡传动常采用滑动齿轮,其他挡位均采用常啮合齿轮传动。图2-3f) 中的倒挡齿轮为常啮合齿轮,并采用同步器换挡;同步器多数装在输出轴上,这是因为一挡主动齿轮尺寸小,同步器装在输入轴上又困难,而高挡的同步器可以装在输出轴后端,如图 2-3d)、 e) 所示;图 2-3d) 所示方案的变速器有辅助支撑,用来提升轴 的刚度,减少齿轮磨损和降低工作噪声 3。 nts 7 图 2.3 两轴式变速器传动方案 综上所述,本次设计选择五挡变速器如图 2-3f)所示。 2.2 倒挡布置方案 常见的倒 挡 结构方案有以下几种: 图 2-4( a) 为常见的倒挡布置方案。 在前进 挡 的传动路线中,加入一个传动,使结构简单,但齿轮处于正负交替对称变化的弯曲应力状态下工作。此方案广泛用于轿车和轻型货车的四 挡 全同步器式变速器中。 图 2-4(b)所示方案的优点是换倒挡时利用了中间轴上的一挡齿轮,因而缩短了中间轴的 长度。但换挡时有两对齿轮同时进入啮合,使换挡困难。 某些轻型货车四 挡 变速器采用此方案。 图 2-4(c)所示方案能获得较大的倒挡传动比,缺点是换挡程序不合理。 图 2-4(d)所示方案针对前者的缺点做了修改, 因而经常在货车变速器中使用。 图 2-4(e)所示方案是将中间轴上的一,倒挡齿轮做成一体,将其齿宽加长。 图 2-4(f)所示方案适用于全部齿轮副均为常啮合齿轮,换挡更为轻便。 为了充分利用空间,缩短变速器轴向长度,有的货车倒挡传动采用图 2-4(g)所示方案。其缺点是一、倒挡须各用一根变速器拨叉轴,致使变速器上盖 中的操纵机构复杂一些。 nts 8 (a) 小客车常用 (b) 直齿滑动啮合四挡 (c) 多数五挡采用 (d) c 方案的改进 (e) 前进挡常啮合 (f) 前进挡常啮合 (g) 一、倒挡各用一跟拨叉轴 图 2.4 倒挡布置方案 综合以上因素,为了换挡轻便,减小噪声,倒挡传动采用图 2-4( f) 所示方案。 2.3 零、部件结构方案分析 2.3.1 齿轮形式 齿轮形式有直齿圆柱齿轮和斜齿圆柱齿轮两种。 与直齿圆柱齿轮比较,斜齿圆柱齿轮有使用寿命长,工作时噪声低等优点;缺点是制造时稍复杂,工作时有轴向 力。变速器中的常啮合齿轮均采用斜齿圆柱齿轮,尽管这样会使常啮合齿轮数增加,并导致变速器的转动惯量增大。直齿圆柱齿轮仅用于低挡和倒挡。 但是,在本设计中由于倒 挡 采用的是常啮合方案,因此倒 挡 也采用斜齿轮传动方案,各挡均采用斜齿轮传动 3。 2.3.2 变速器轴承的选择 变速器轴承常采用圆柱滚子轴承、球轴承、滚针轴承、圆锥滚子轴承、滑动轴套等。 滚针轴承、滑动轴承套主要用在齿轮与轴不是固定链接,并要求两者有相对运动的地方。变速器中采用圆锥滚子轴承虽然有直径较小、宽度较大因而容量大、可承受高负荷等优点,但也有需要调整 预紧、装配麻烦、磨损后轴易歪斜而影响齿轮正确啮合的缺点 12。 由于本设计的变速器为两轴式变速器,具有较大的轴向力,所以设计中变速器输入轴输出轴的前后轴承按直径系列均选用圆锥滚子轴承。 2.3.3 操纵机构的布置 nts 9 1直接操纵手动换挡变速器 当变速器布置在驾驶员座椅附近,可将变速杆直接安装在变速器上,并依靠驾驶员手力和通过变速杆直接完成换挡功能的手动换挡变速器,称为直接操纵变速器。 2远距离操纵手动换挡变速器 平头式汽车或发动机后置后轮驱动汽车的变速器,受总体布置限制变速器距驾驶员座位较远 ,这时需要在变速杆与拨叉之间布置若干传动件,换挡手力经过这些转换机构才能完成换挡功能。这种手动换挡变速器称为远距离操纵手动换挡变速器。 3电控自动换挡变速器 80 年代以后,在固定轴式机械变速器基础上,通过应用计算机和电子控制技术,使之实现自动换挡,并取消了变速杆和离合器踏板。驾驶员只需控制油门踏板,汽车在行驶过程中就能自动完成换挡时刻的判断,接着自动实现收油门、离合器分离、选 挡、换挡、离合器接合和回油门等一系列动作,使汽车动力性、经济性有所提高,简化操纵并减轻了驾驶员的劳动强度。 由于本设计的变速 器为两轴式变速器,采用发动机前置前轮驱动,变速器离驾驶员座椅较近,所以采用直接操纵式手动换挡变速器。 2.3.4 换挡机构形式 换档机构分为直齿滑动齿轮、啮合套和同步器三种。 直齿滑动齿轮换档的特点是结构简单、紧凑,但由于换档不轻便、换档时齿端面受到很大冲击、导致齿轮早期损坏、滑动花键磨损后易造成脱档、噪声大等原因,初一档、倒档外很少采用。 啮合套换档型式一般是配合斜齿轮传动使用的。由于齿轮常啮合,因而减少了噪声和动载荷,提高了齿轮的强度和寿命。啮合套有分为内齿啮合套和外齿啮合套,视结构布置而选定,若齿轮副 内空间允许,采用内齿结合式,以减小轴向尺寸。结合套换档结构简单,但还不能完全消除换档冲击,目前在要求不高的档位上常被使用。 采用同步器换档可保证齿轮在换档时不受冲击,使齿轮强度得以充分发挥,同时操纵轻便,缩短了换档时间,从而提高了汽车的加速性、经济性和行驶安全性,此外,该种型式还有利于实现操纵自动化。其缺点是结构复杂,制造精度要求高,轴向尺寸有所增加,铜质同步环的使用寿命较短。目前,同步器广泛应用于各式变速器中 1。 在本设计中所采用的是锁环式同步器,该同步器是依靠摩擦作用实现同步的。但它可以从结构上保证 结合套与待啮合的花键齿圈在达到同步之前不可能接触,以免齿间冲击和发生噪声。 2.3.5 自动脱挡 nts 10 目前在结构上采取措施比较有效的方案有以下几种: 1.将两接合齿的啮合位置错开,这样在啮合时,使接合齿端部超 过被接合齿约 1 3mm。使用中接触部分挤压和磨损。 2.将啮合套齿座上前齿圈的齿厚切薄(切下 0.3 0.6mm),这样,换挡后啮合套的后端面被后齿圈的前端面顶住,从而减少自动脱档。 3.将接合齿的工作面加工成斜面,形成倒锥角(一般倾斜 2 3),使接合齿面产生阻止自动脱档的轴向力 7。 2.4 本章 小结 本章主要介绍了变速器传动机构和操纵机构的类型,并简要分析各类型机构的优缺点,针对本次设计变速器类型、特点及功用,对变速器的传动机构操纵机构的布置方案,主要零件的形式进行选择,为后期的设计工作打下基础。 nts 11 第 3 章 变速器的设计与计算 3.1 变速器主要参数的选择 本次设计是在给定主要整车参数的情况下进行设计,东方之子 1.8L 5 挡手动变速器整车主要技术参数如表 3.1 所示: 表 3.1 整车主要技术参数 发动机最大功率 97kw 车轮型号 205/65R15 发动机最大转 矩 170Nm 最大功率转速 5750r/min 最大转矩转速 4500r/min 最高车速 190km/h 总质量 1440kg 前轴载荷 864kg 3.1.1 传动比范围 变速器传动比范围是指变速器最高档与最低档传动比的比值。目前乘用车的传动比范围在 3.0 4.5之间,总质量轻些的商用车在 5.0 8.0 之间,其他商用车则更大。 1、变速器传动比的确定 发动机转速与汽车行驶速度之间的关系式为: 00 .3 7 7 garnu ii ( 3.1) 式中: au -汽车行驶速度 (km/h); n -发动机转速( r/min) ; r -车轮滚动半径( m) ; gi -变速器传动比; 0i -主减速器传动比; 车轮半径 由所选用的轮胎规格所得 r=0.324( mm) gi 为 0.7 0.8,本设计最高档传动比选为 0.8. 0 xma0 . 3 7 7 0 .3 2 4 5 7 5 0= 0 .3 7 7 0 . 8 1 7 0ugi rni =4.621 nts 12 m a x 0 m a x m a x m a x( c o s s i n )e g I TrT i i m g f m gr m a x 2e gI TrTi Gr 2、最低档、最高档传动比的确定 选择最低档传动比,应根据汽车最大爬坡度、驱动轮与路面的附着力、汽车的最低稳定车速以及主减速比和驱动轮的滚动半径等来综合考虑、确定 2。 汽车爬陡坡时车速不高,空气阻力可忽略,则最大驱动力用于克服轮胎与路面间的滚动阻力及爬坡阻力。故有 ( 3.2) 式中 m-汽车总质量; g-重力加速度; f-滚动阻力系数; rr-驱动轮的滚动半径; Temax-发动机最大转矩; i0-主减速比; -汽车传动系的传动效率。 max=0.7 0.8 取 0.95 f=0.0076+0.000056 au ( 3.3) =0.018 根据则由最爬坡度要求的变速档传动比为 igI 1.866 驱动车轮与路面的附着条件 : 求得的变速器 I档传动比为: igIm a x 01 4 4 0 9 . 8 0 . 8 0 . 3 2 4 0 . 6= = 2 .9 41 7 0 4 . 6 2 1 0 .9 5reTGrTi ( 3.4) 式中 :G2-静止于水平路面时驱动桥给路面的载荷; -着系数 (良好干燥路面 0.7 0.8)取 0.8 本设计传动比范围为 1.866 igI 2 .94 ig1 取 2.8 3、变速器各挡传动比的确定 按等比级数分配其它各挡传动比,即: qiiiiiiiiiigggggggggg 6554433221 nts 13 式中: q 常数,也就是各挡之间的公比;因此,各挡的传动比为 51 qig , 42 qig , 33 qi g 24 qi g , qig 5 115gngiqi=1.368 ( 3.5) 所以各挡传动比与 挡传动比的关系 : 2gi=5 41gi=2.048,3gi=5 31gi=1.497,4gi=5 21gi=1.094,5gi=q =0.8 3.1.2 初选中心距 A= 31max geA iTK ( 3.6) = 3.9 3 1 7 0 2 .8 0 .9 6 =71.6mm 中心距圆整为 72mm 式中: A 为中心距( mm) ; AK 为中心距系数,轿车: AK =8.99.3; maxeT为发动机最大转矩( mN ); 1i 为变速器一挡传动比; g为变速器传动效率 0.96; 轿车变速器的中心距在 6080mm 变化范围。初取 A=72mm 3.1.3 变速器的外形尺寸 变速器的横向外形尺寸,可根据齿轮直径以及倒档中间齿轮和换 挡 机构的布置初步确定。 影响变速器壳体的轴向尺寸的因素有挡数、换挡机构形式以及齿轮形式。 轿车四档变速器壳体的轴向尺寸 3.03.4A。 即 L=( 3.03.4) 72=216 244.8mm 3.1.4 齿轮参数选择 1、齿轮模数选取的一般原则 13: 1)为了减少噪声应合理减小模 数,同时增加齿宽; 2)为使质量小些,应该增加模数,同时减少齿宽; 3)从工艺方面考虑,各挡齿轮应该选用一种模数; 4)从强度方面考虑,各挡齿轮应有不同的模数。 对于轿车,减少工作噪声较为重要,因此模数应选得小些; nts 14 综上所述:一挡二挡倒挡模数为 3,三挡四挡五挡模数为 2.75; 2、压力角 压力角较小时,重合度大,传动平稳,噪声低;较大时可提高轮齿的抗弯强度和表面接触强度。对轿车,为加大重合度已降低噪声,取小些;对货车,为提高齿轮承载力,取大些。在本设计中变速器齿轮压力角 取 20; 3、螺旋角 斜齿轮在变 速器中得到广泛的应用。从提高低 挡 齿轮的抗弯强度出发,不希望用过大的螺旋角;而从提高高 挡 齿轮的接触强度着眼,应选用较大螺旋角。 乘用车变速器: 两轴式变速器为 2025 中间轴式变速器为 2234 商用车车变速器: 1826 斜齿轮螺旋角 取 25; 4、齿宽 应注意齿宽对变速器的轴向尺寸,齿轮工作平稳性,齿轮强度和齿轮工作时受力的均匀程度均有影响。 通常根据齿轮模数 m 的大小来选定齿宽: 斜齿: b=KcMn, Kc 取 6.08.5 第一轴常啮 合齿轮副的齿宽系数 KC可取大些,使接触线长度增加、接触应力降低,以提高传动平稳性和齿轮寿命。 一挡 b=21mm 二挡 b=18mm 三挡 b=16.5mm 四挡 b=16.5mm 五档 b=16.5mm 倒挡 b=21mm 5、 齿顶高系数 现在规定取 1.00 或 更大 3.2 各挡齿轮齿数的分配及传动比的计算 在初选了中心距、齿轮的模数和螺旋角后,可根据预先确定的变速器档数、传动比和结构方案来分配各 挡 齿轮的齿数。 3.2.1 一挡齿数及传动比的确定 nts 15 2 c o s2532 7 2 c o s 2 54 3 .53hnnhAzmmzo( 3.6) 取整得 43, 轿车 1z 取 12, 则2z=31。则一 挡 传动比为: 21131 2 .5 812ziz ( 3.7) 对中心距 A 进行修正 cos2 hnzmA ( 3.8) 3 4 3 7 1 . 1 62 c o s 2 5A m m 取整得0 72A mm,0A为标准中心矩。 3.2.2 二挡齿数及传动比的确定 342 zzi cos2)( 430zzmA n 已知:0A=72mm, 2i =2.048,nm=3, 25 o ; 将数据代入上 ( 3.7)、( 3.8) 两式,齿数取整得:3 14z ,4 29z ,所以二 挡 传动比为: 42329 2 . 0 7 114ziz 3.2.3 计算三挡齿轮齿数及传动比 563 zzints 16 cos2)( 650zzmA n 已知:0A=72mm,3i=1.497,nm=2.75, 25 o ;将数据代入上 ( 3.7)、( 3.8) 两式,齿数取整得:5 19z ,6 28z ,所以 三 挡 传动比为: 63528 1 . 4 7 419ziz 3.2.4 计算四挡齿轮齿数及传动比 784 zzi cos2)( 870zzmA n 已知:0A=72mm, 4i =1.094,nm=2.75, 25 o ;将数据代入上 ( 3.7)、( 3.8)两式,齿数取整得:7 23z ,8 24z , 所以四 挡 传动比为: 84724 1 . 0 4 323ziz 3.2.5 计算五挡齿轮齿数及传动比 9105 zzi cos2)( 1090zzmA n 已知:0A=72mm,5i=0.80,nm=2.75, 25 o ;将数据代入上 ( 3.7)、( 3.8) 两式,齿数取整得:9 26z ,10 21z , 所以五 挡 传动比为: 105921 0 . 826ziz 3.2.6 计算倒挡齿轮齿数及传动比 初选倒 挡 轴上齿轮齿数为 12z =22,输入轴齿轮齿数 11z =12,为保证倒 挡 齿轮的啮nts 17 合不产生运动干涉齿轮 11 和齿 轮 13 的齿顶圆之间应保持有 0.5mm 以上的间隙,即满足以下公式: 1 1 1 3 011() 2 0 . 52 c o s n nz z m mA ( 3.9) 已知:11 25 o, 75.2nm,0 72A ,把数据代入( 3.9)式,齿数取整,解得:13 27z ,则倒 挡 传动比为: 131127 2 . 2 512Rziz 输入轴与倒 挡 轴之间的距离: 1 1 1 211() 3 (1 2 2 2 ) 5 6 . 2 72 c o s 2 c o s 2 5nm z zA omm 输出轴与倒 挡 轴之间的距离: 1 3 1 211() 3 ( 2 7 2 2 ) 8 1 . 0 92 c o s 2 c o s 2 5nm z zA omm 3.3 齿轮变位系数选择和螺旋角的修正 变位系数的选择原则 : 1) 对于高 挡 齿轮,应按保证最大接触强度和抗胶合及耐磨损最有利的原则选择变位系数。 2) 对于低 挡 齿轮,为提高小齿轮的齿根强度,应根据危险断面齿厚相等的条件来选择大、小齿轮的变位系数。 3) 总变位系数越小,齿轮齿根抗弯强度越低。但易于吸收冲击振动,噪声要小一些。 为了降低噪声,对于 变速器中除去一、二 挡 以外的其它各 挡 齿轮的总变位系数要选用较小一些的数值。一般情况下,随着 挡 位的降低,总变位系数应该逐 挡 增大。一、二 挡 和倒 挡 齿轮,应该选用较大的值。 采用变位齿轮的原因:配凑中心距;提高齿轮的强度和使用寿命;降低齿轮的啮合噪声 17。 为了降低噪声,对于变速器中除去一、二 挡 以外的其它各 挡 齿轮的总变位系数要选用较小一些的数值。一般情况下,随着 挡 位的降低,总变位系数应该逐档增大。一、二 挡 和倒 挡 齿轮,应该选用较大的值。 nts 18 为了减小轴向力, 低 挡 选用较小的螺旋角,一档 、倒挡 选 22 ,二 挡 选 23o ;为了增加重合度,减小噪声,三 挡 、四 挡 、五 挡 选用较大的螺旋角,都选为 24 。 3.3.1 计算一挡齿轮变位系数及螺旋角修正 修正中心距 12 4 3 3 6 9 . 5 62 c o s 2 c o s 2 2nz z mA mm ( 3.10) 螺旋角的修正 13 4 3c o s a r c c o s 2 6 . 3 82 2 7 2nhmza r c A ( 3.11) 端面压力角 t=arctan tancos n= t a n 2 0a r c t a nc o s 2 6 .3 8 =22.11 ( 3.12) 端面 啮合角 06 9 . 5 6a r c c o s ( c o s ) a r c c o s ( c o s 2 2 . 1 1 2 6 . 4 872AA ) ( 3.13) 齿轮总变位系数为 ,122 t a n1 2 3 1 2 6 . 4 8 2 2 . 1 12 t a n 2 00 . 9tz z i n v i n vxi n v i n v ( 3.14) 经查表: 1x =0.471 2x = x 1x =0.9 0.471=0.429 3.3.2 计算二挡齿轮变位系数及螺旋角修正 根据公式 ( 3.10)、( 3.11)、( 3.12)、( 3.13)、( 3.14) 可得: 修正中心距 34 4 3 3 7 0 . 0 72 c o s 2 c o s 2 3nz z mA mm 螺旋角的修正 nts 19 23 4 3c o s a r c c o s 2 6 . 3 82 2 7 2nhmza r c A 端面压力角 t=arctan tancos n= t a n 2 0a r c t a nc o s 2 6 .3 8 =22.11 端面 啮合角 07 0 . 0 7a r c c o s ( c o s ) a r c c o s ( c o s 2 2 .1 1 2 6 . 4 872AA ) 齿轮总变位系数为 ,342 t a n1 4 2 9 2 6 . 4 8 2 2 . 1 12 t a n 2 00 . 6 9tz z i n v i n vxi n v i n v 经查表: 3x=0.35 4x= x 3x=0.69 0.35=0.34 3.3.3 计算三档齿轮变位系数及螺旋角修正 根据公式 ( 3.10)、( 3.11)、( 3.12)、( 3.13)、( 3.14) 可得: 修正中心距 56 4 7 2 . 7 5 7 0 . 7 42 c o s 2 c o s 2 4nz z mA mm 螺旋角的修正 32 . 7 5 4 7c o s a r c c o s 2 6 . 1 62 2 7 2nhmza r c A 端面压力角 t=arctan tancos n= t a n 2 0a r c t a nc o s 2 6 .1 6 =22.07 端面 啮合角 07 0 . 7 4a r c c o s ( c o s ) a r c c o s ( c o s 2 2 . 0 7 2 4 . 4 272AA ) 齿轮总变位系数为 nts 20 ,562 t a n1 9 2 8 2 4 . 4 2 2 2 . 0 72 t a n 2 00 . 3 6 8tz z i n v i n vxi n v i n v 经查表: 5x=0.223 6x= x 5x=0.368 0.223=0.145 3.3.4 计算四档齿轮变位系数及螺旋角修正 根据公式 ( 3.10)、( 3.11)、( 3.12)、( 3.13)、( 3.14) 可得: 修正中心距 78 4 7 2 . 7 5 7 0 . 7 42 c o s 2 c o s 2 4nz z mA mm 螺旋角的修正 42 . 7 5 4 7c o s a r c c o s 2 6 . 1 62 2 7 2nhmza r c A 端面压力角 t=arctan tancos n= t a n 2 0a r c t a nc o s 2 6 .1 6 =22.07 端面 啮合角 07 0 . 7 4a r c c o s ( c o s ) a r c c o s ( c o s 2 2 . 0 7 2 4 . 4 272AA ) 齿轮总变位系数为 ,782 t a n2 3 2 4 2 4 . 4 2 2 2 . 0 72 t a n 2 00 . 3 6 8tz z i n v i n vxi n v i n v 经查表: 7x=0.192 8x= x 7x=0.368 0.192=0.176 3.3.5 计算五档齿轮变位系 数及螺旋角修正 根据公式 ( 3.10)、( 3.11)、( 3.12)、( 3.13)、( 3.14) 可得: 修正中心距 nts 21 9 1 0 4 7 2 . 7 5 7 0 . 7 42 c o s 2 c o s 2 4nz z mA mm 螺旋角的修正 52 . 7 5 4 7c o s a r c c o s 2 6 . 1 62 2 7 2nhmza r c A 端面压力角 t=arctan tancos n= t a n 2 0a r c t a nc o s 2 6 .1 6 =22.07 端面 啮合角 07 0 . 7 4a r c c o s ( c o s ) a r c c o s ( c o s 2 2 . 0 7 2 4 . 4 272AA ) 齿轮总变位系数为 ,9 1 02 t a n2 1 2 6 2 4 . 4 2 2 2 . 0 72 t a n 2 00 . 3 6 8tz z i n v i n vxi n v i n v 经查表: 9x=0.19 10x= x 9x=0.368 0.19=0.178 3.3.6 计算倒档齿轮变位系数及螺旋角修正 根据公式 ( 3.10)、( 3.11)、( 3.12)、( 3.13)、( 3.14) 可得: 输入 轴与倒挡轴中心距修正 1 1 1 2 3 4 3 552 c o s 2 c o s 2 2nz z mA mm 螺旋角的修正 3 3 4c o s a r c c o s 2 4 . 42 2 5 6nhmza r c A 倒端面压力角 t=arctan tancos n= ta n 2 0a rc ta nc o s 2 4 .4=21.78 端面 啮合角 nts 22 055a r c c o s ( c o s ) a r c c o s ( c o s 2 1 . 7 8 2 4 . 2 156AA ) 齿轮总变位系数为 ,1 1 1 22 t a n1 2 2 2 2 4 . 2 1 2 1 . 7 82 t a n 2 00 . 3 5 5 8tz z i n v i n vxi n v i n v 经查表: 11x=0.233 12x= x 11x=0.3558 0.233=0.1228 输出轴与倒挡轴中心距修正 1 3 1 2 4 9 3 7 9 . 2 72 c o s 2 c o s 2 2nz z mA mm 端面压力角 t=arctan tancos n= ta n 2 0a rc ta nc o s 2 4 .4=21.78 端面 啮合角 07 9 . 2 7a r c c o s ( c o s ) a r c c o s ( c o s 2 1 . 7 8 2 4 . 8 683AA ) 齿轮总变位系数为 ,1 3 1 22 t a n2 9 2 2 2 4 . 2 1 2 1 . 7 82 t a n 2 00 . 6 7 2tz z i n v i n vxi n v i n v 经查表: 12x=0.1228 13x= x 12x=0.672 0.1228=5492 3.4 各挡齿轮主要参数的确定 3.4.1 一挡齿轮参数 理论中心距 121 7 1 . 9 9 72 c o s nZZA m m m(3.15) nts 23 中心距变动系数 01 0 . 0 0 3n nAAm (3.16) 齿顶降低系数 0 . 8 9 7nn (3.17) 分度圆直径 111cosnzmd =40.18mm (3.18) 221cosnzmd =103.81mm 齿顶高 1 a n 1 nhanhm =1.722mm (3.19) 2 a n 2 nhanhm =1.597mm 齿根高 1 a n n 1 nhfh c m =2.337mm (3.20) 2 a n n 2 nhfh c m =2.463mm 齿顶圆直径 a1 1 12 ad d h=43.624mm (3.21) 2 2 a 22ad d h=107.004mm 齿根圆直径 1 1 12ffd d h=35.506mm (3.22) 2 2 22ffd d h=98.884mm 当量齿数 13 17c o snZZ (3.23) 23 41c o snZZ 基圆直径 1bd = cos1d =37.76mm (3.24) 2bd = cos2d =97.55mm 节圆直径 1d = cos1bd =40.18mm (3.25) 2d = cos1bd =103.81mm 3.4.2 二挡齿轮参数 根据公式 ( 3.15)、( 3.16)、( 3.17)、( 3.18)、( 3.19)、( 3.20)、( 3.21)、( 3.22)、( 3.23)、( 3.24)、( 3.25) 可得 nts 24 理论中心距 342 7 1 . 9 9 72 c o s nZZA m m m中心距变动系数 02 0 . 0 0 3n nAAm 齿顶降低系数 0 . 6 8 7nn 分度圆直径 332cosnzmd =46.88mm 442cosnzmd =97.11mm 齿顶高 3 a n 3 nhanhm =1.898mm 4 a n 4 nhan =1.959mm 齿根高 3 a n n 3 nhfh c m =2.7mm 4 a n n 4 nhfh c m =2.73
- 温馨提示:
1: 本站所有资源如无特殊说明,都需要本地电脑安装OFFICE2007和PDF阅读器。图纸软件为CAD,CAXA,PROE,UG,SolidWorks等.压缩文件请下载最新的WinRAR软件解压。
2: 本站的文档不包含任何第三方提供的附件图纸等,如果需要附件,请联系上传者。文件的所有权益归上传用户所有。
3.本站RAR压缩包中若带图纸,网页内容里面会有图纸预览,若没有图纸预览就没有图纸。
4. 未经权益所有人同意不得将文件中的内容挪作商业或盈利用途。
5. 人人文库网仅提供信息存储空间,仅对用户上传内容的表现方式做保护处理,对用户上传分享的文档内容本身不做任何修改或编辑,并不能对任何下载内容负责。
6. 下载文件中如有侵权或不适当内容,请与我们联系,我们立即纠正。
7. 本站不保证下载资源的准确性、安全性和完整性, 同时也不承担用户因使用这些下载资源对自己和他人造成任何形式的伤害或损失。

人人文库网所有资源均是用户自行上传分享,仅供网友学习交流,未经上传用户书面授权,请勿作他用。
2:不支持迅雷下载,请使用浏览器下载
3:不支持QQ浏览器下载,请用其他浏览器
4:下载后的文档和图纸-无水印
5:文档经过压缩,下载后原文更清晰
|