制定后钢板弹簧吊耳零件的加工工艺,设计钻Ø37孔的钻床夹具.doc
制定后钢板弹簧吊耳零件的加工工艺,设计钻;#216;37孔的钻床夹具
收藏
资源目录
压缩包内文档预览:
编号:492649
类型:共享资源
大小:282.49KB
格式:RAR
上传时间:2015-11-07
上传人:qq77****057
认证信息
个人认证
李**(实名认证)
江苏
IP属地:江苏
20
积分
- 关 键 词:
-
制定
制订
钢板
弹簧
零件
加工
工艺
设计
37
钻床
夹具
- 资源描述:
-

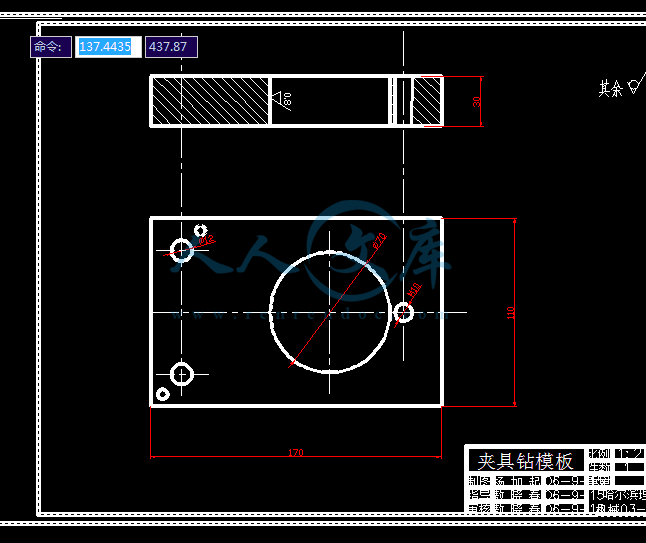
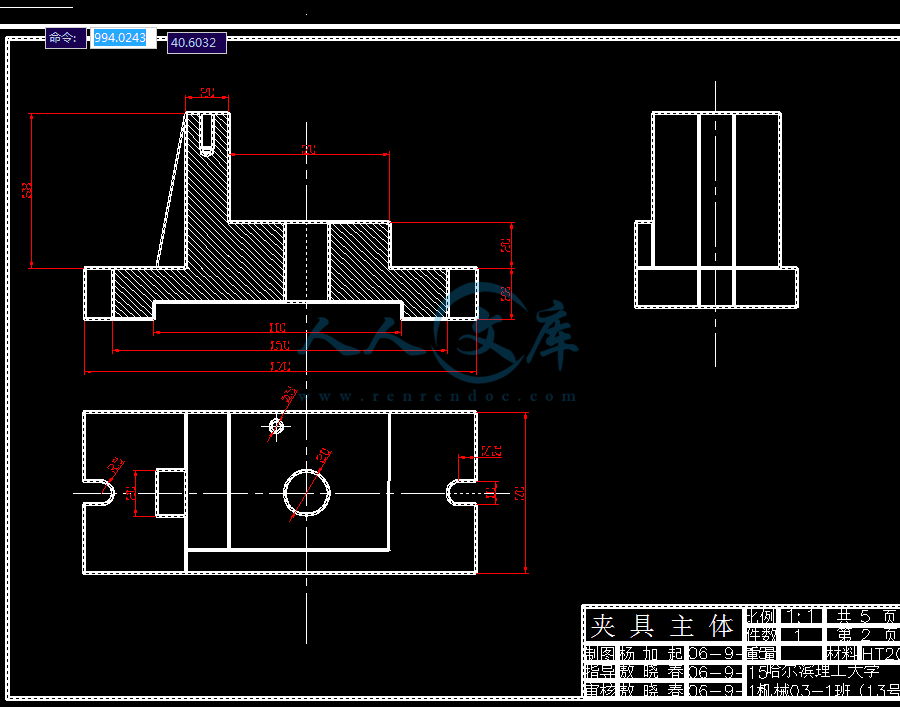
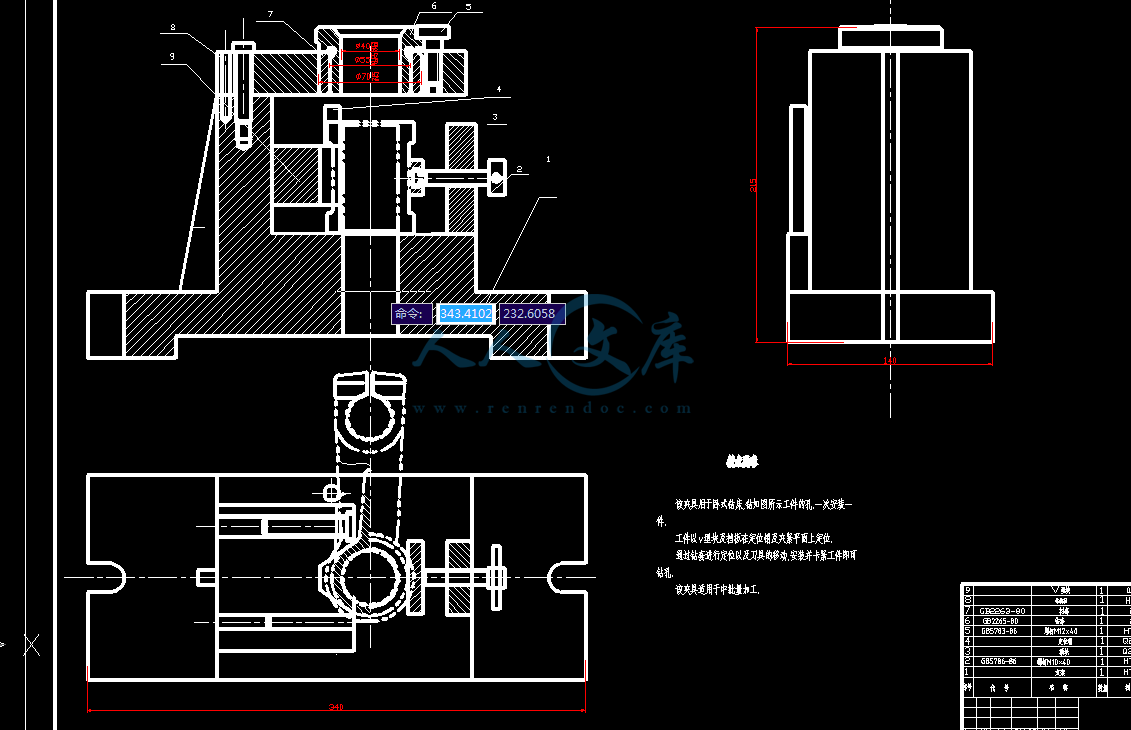


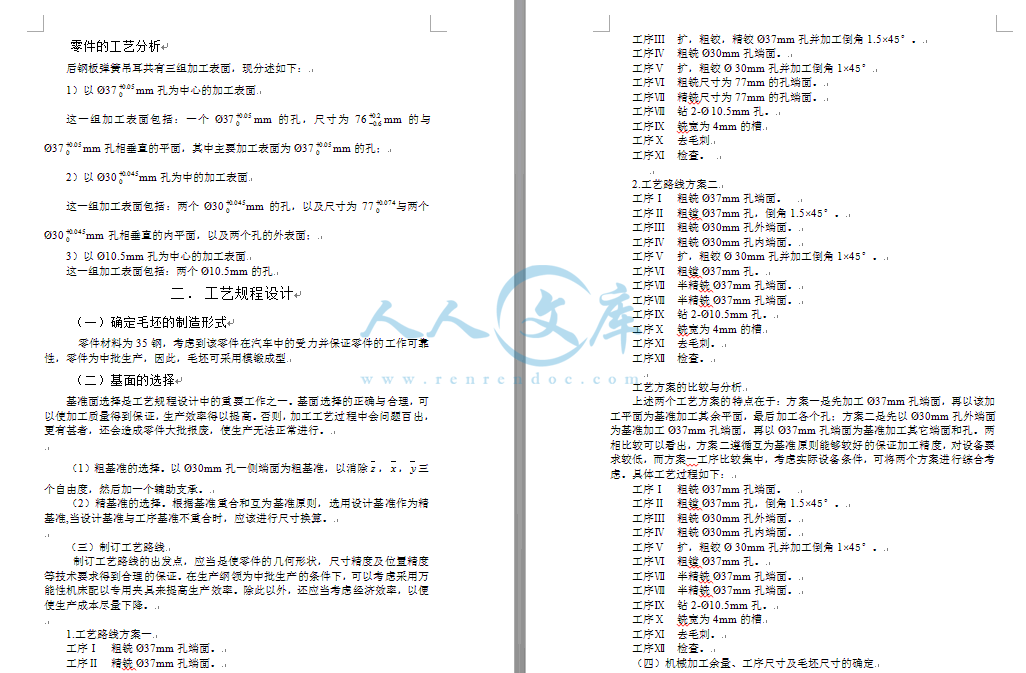
- 内容简介:
-
机械制造基础课程设计 设计题目 : 制定后钢板弹簧吊耳零件的加工工艺,设计钻 37 孔的钻床夹具 班 级: 机械 03-1 班 学 生: 杨加起 指导教师: 敖晓春 哈尔滨理工大学 2006-9-26 nts 哈尔滨理工大学 机械制造工艺及夹具课程设计任务书 设计题目: 制定后钢板弹簧吊耳的加工工艺,钻 37 孔 的钻床夹具 设计要求: 1.中批生产; 2.尽量选用通用夹具。 设计内容: 1.填写设计任务书; 2.制订一个中等零件的加工工艺过程,填写工 艺过程卡和工序卡各一张; 3.设计指导教师指定的工序夹具,绘制全套夹 具图纸,要求用计算机绘图; 4.编写设计说明书一份,按照毕业 论文的格式 写,要求打印文稿。 班 级: 机械 03-1 班 学 生: 杨加起 指导教师: 敖晓春 2006 年 9 月 10 日 一 零件的分析 nts零件的工艺分析 后钢板弹簧吊耳共有三组加工表面,现分述如下: 1)以 37 05.00mm 孔为中心的加工表面 这一组加工表面包括:一个 37 05.00mm 的孔, 尺寸为 76 2.06.0mm 的与37 05.00mm 孔相垂直的平面,其中主要加工表面为 37 05.00mm 的孔; 2)以 30 045.00mm 孔为中的加工表面 这一组加工表面包括:两个 30 045.00mm 的孔,以及尺寸为 77 074.00与两个30 045.00mm 孔相垂直的内平面,以及两个孔的外表面; 3)以 10.5mm 孔为中心的加工表面 这一组加工表面包括:两个 10.5mm 的孔 二 工艺规程设计 (一) 确定毛坯的制造形式 零件材料为 35 钢,考虑到该零件在汽车中的受力并保证零件的工作可靠性,零件为中批生产,因此,毛坯可采用模锻成型 (二) 基面的选择 基准面选择是工艺规程设计中的重要工作之一。基面选择的正确与合理,可以使加工质量得到保证,生产效率得以提高。否则,加工工艺过程中会问题百出,更有甚者,还会造成零件大批报废 ,使生产无法正常进行。 ( 1)粗基准的选择。以 30mm 孔一侧端面为粗基准,以消除 z , x , y 三个自由度,然后加一个辅助支承。 ( 2)精基准的选择。根据基准重合和互为基准原则,选用设计基准作为精基准 ,当设计基准与工序基准不重合时,应该进行尺寸换算。 (三)制订工艺路线 制订工艺路线的出发点,应当是使零件的几何形状,尺寸精度及位 置精度等技术要求得到合理的保证。在生产纲领为中批生产的条件下,可以考虑采用万能性机床配以专用夹具来提高生产效率。除此以外,还应当考虑经济效率,以便使生产成本尽量下降。 1.工艺路线方案一 工序 粗铣 37mm 孔端面。 工序 精铣 37mm 孔端面。 nts 工序 扩,粗铰,精铰 37mm 孔并加工倒角 1.545 。 工序 粗铣 30mm 孔端面。 工序 扩,粗铰 30mm 孔并加工倒角 145 工序 粗铣尺寸为 77mm 的孔端面。 工序 精铣尺寸为 77mm 的 孔端面。 工序 钻 2- 10.5mm 孔。 工序 铣宽为 4mm 的槽 工序 去毛刺 工序 检查。 2.工艺路线方案二 工序 粗铣 37mm 孔端面。 工序 粗镗 37mm 孔,倒角 1.545。 工序 粗铣 30mm 孔外端面。 工序 粗铣 30mm 孔内端面。 工序 扩,粗铰 30mm 孔并加工倒角 145 。 工序 粗镗 37mm 孔。 工序 半精铣 37mm 孔端面。 工序 半精铣 37mm 孔端面。 工序 钻 2-10.5mm 孔。 工序 铣宽 为 4mm 的槽 工序 去毛刺。 工序 检查。 工艺方案的比较与分析 上述两个工艺方案的特点在于:方案一是先加工 37mm 孔端面,再以该加工平面为基准加工其余平面,最后加工各个孔;方案二是先以 30mm 孔外端面为基准加工 37mm 孔端面,再以 37mm 孔端面为基准加工其它端面和孔。两相比较可以看出,方案二遵循互为基准原则能够较好的保证加工精度,对设备要求较低,而方案一工序比较集中,考虑实际设备条件,可将两个方案进行综合考虑。具体工艺过程如下: 工序 粗铣 37mm 孔端面。 工序 粗镗 37mm 孔,倒角 1.545。 工序 粗铣 30mm 孔外端面。 工序 粗铣 30mm 孔内端面。 工序 扩,粗铰 30mm 孔并加工倒角 145 。 工序 粗镗 37mm 孔。 工序 半精铣 37mm 孔端面。 工序 半精铣 37mm 孔端面。 工序 钻 2-10.5mm 孔。 工序 铣宽为 4mm 的槽 工序 去毛刺。 工序 检查。 (四)机械加工余量、工序尺寸及毛坯尺寸的确定 nts “后钢板弹簧吊耳”零件材料为 35 钢,毛坯重量约为 2.6Kg,生产 类型为中批生产, 采用锻造。 根据上述原始资料及加工工艺,分别确定各加工表面的饿机械加工余量 工序尺寸及毛坯尺寸如下: 1.37mm 孔 毛坯为空心,参照 机械加工工艺手册 ,确定工序尺寸为 Z=2.6mm。 由锻件复杂系数为 S1,锻件材质系数取 M1, 毛坯尺寸为 34.4 6.12.1。根据 机械加工工艺手册 加工余量分别为: 粗镗: 36mm 2Z=1.6mm 精镗: 36mm 2Z=1.0mm 2.30mm 孔 毛坯为空心,参照 机械加工工艺手册 ,确定工序尺寸为 Z=2.0mm。 由锻件复杂系数为 S1,锻件材质系数取 M1, 毛坯尺寸为 26 5.01.1根据 机械加工工艺手册 加工余量分别为: 扩孔: 29.8mm 2Z=1.8mm 铰孔: 30mm 2Z=0.2mm 3. 37mm 孔、 30mm 孔端面的加工余量 参照 机械加工工艺手册 ,取加工精度 F2 ,由锻 件复杂系数为 S3, 两孔外侧单边加工余量为 Z=2mm。锻件材质系数取 M1, 复杂系数为 S3, 确定锻件偏差为 2.16.0mm 和 1.15.0mm。 根据 机械加工工艺手册 加工余量分别为: 37mm 孔端面: 粗铣 2Z=3.0mm 精铣 2Z=1.0mm 30mm 孔端面: 粗铣 2Z=4.0mm 4. 10.5mm 孔 毛坯为实心,不出孔 ,为自由工差。根据 机械加工工艺手册 加工余量分别为: 钻孔: 10.5mm 2Z=10.5mm 由于本设计规定的零件为中批生产,可采用调整法加工,因此在计算最大、最小加工余量时,可按调整法加工方式予以确定。 毛坯名义尺寸: 122+2 2=126mm 毛坯最大尺寸: 126+2 1.3=128.6mm 毛坯最小尺寸: 126-2 0.7=124.6mm 铣后最大尺寸: 122+0=122mm 铣后最小尺寸: 122-0.17=121.83mm nts 将以上计算的工序间尺寸及公差整理成下表: ( mm) 锻造毛坯 铣削加工 30mm 孔处 加工前 最大 128.6 mm 最小 124.6 mm 加工后 最大 128.6 mm 112 mm 最小 124.6 mm 121.83 mm 加工余量 (单边) 2 mm 最大 3.65 mm 最小 1.435 mm 加工公差 1.15.0 mm -0.17/2 mm (五) 确定切削用量及基本工时 工序:粗铣 37mm 孔端面。本设计采用查表法确定切削用量。 1. 加工条件 工件材料: 35 钢,锻造。 加工要求:铣 37mm 端面, Ra6.3m。 机床: X51 立式铣床。 刀具: YT15 硬质合金面 铣刀,齿数 Z=5,wd=100mm。 2. 计算切削用量 根据切削手册 20.0zf mm/z 切削速度:根据相关手册 取 118v m/min 8.375100 11810001000 dw vn s( r/min) 现采用 X51立式铣床,根据机床说明书,取 nw=375 r/min。 故实 际切削速度 5.1171000 3751001000 ww ndv( m/min) 当 nw=375 r/min 时,工作台每分钟进给量mf应为 37537552.0 wzm znff( mm/min) 查机床说明书,取 375mfmm/min 工 序 工 尺 加 寸 nts 切削工时 27.037510021 mm flllt ( min) mt为加工一侧端面的时间,总工时 528.0264.02 t ( min) 工序 .粗镗 37mm 孔、倒角 455.1 。 根据机械加工工艺手册查得镗 37mm 孔的进给量 =0.3 1.0mm,按机床 规格 取 f =0.6mm, 切削速度,根据相关手册及机床说明书,取 v=30mm/s,加工孔径0d=36mm。则 4.26536 3010001000 0 d vn s( r/min) 根据机床选取 nw=300 r/min。 实际切削速度 9.33100 0 30036100 00 vdv( m/min) 切削工时 48.06.0300107621 fnllltw( min) 工序:粗铣 30mm孔外端面 。 根据切削手册 20.0zf mm/z 切削速度:根据相关手册 取 118v m/min 刀具与工序所使用刀具相同 125wdmm 4z 3001251181 0 001 0 00 dw vn s( r/min) 现采用 X51立式铣床,根据机床说明书,取 nw=300 r/min。 故实际切削速度 1181000 3001251000 ww ndv( m/min) 当 nw=300 r/min 时,工作台每分钟进给量mf应为 24030042.0 wzm znff( mm/min) nts查机床说明书,取 2.235mfmm/min 切削工时 45.02.235406521 mm flllt ( min) mt为加工一侧端面的时间,总工时 90.045.02 t ( min) 工序:粗铣 30mm孔内端面。 根据切削手册 20.0zf mm/z 切削速度:根据相关手册 取 118v m/min 刀具与工 序所使用刀具相同 125wdmm 4z 3001251181 0 001 0 00 dw vn s( r/min) 现采用 X51立式铣床,根据机床说明书,取 nw=300 r/min。 故实际切削速度 1181000 3001251000 ww ndv( m/min) 当 nw=300 r/min 时,工作台每分钟进给量mf应为 24030042.0 wzm znff( mm/min) 查机床说明书,取 2.235mfmm/min 切削工时 45.02.235406521 mm flllt ( min) mt为加工一侧端面的时间,总工时 90.045.02 t ( min) 工序: 1.扩 29.8mm 孔 。 确定进给量 f :根据机械加工工艺手册 f =0.81 mm/r。 切削速度:根据相关手册,查得切削速度 2.13v m/min ,所以 1418.29 2.1310001000 ws d vn( r/min) 根 据 机 床 说 明 书 选 取 nw=140 r/min , 故 实 际 切 削 速 度nts1.131000 1408.291000 vdv w ( m/min) 切削工时 30.081.0140 122221 fn llltw( min) 2.铰 30mm 孔 。 确定进给量 f :根据机械加工工艺手册 f =1.17 mm/r。 切削速度:根据相关手册,查得切削速度 4.5v m/min ,所以 3.5730 4.510001000 ws d vn( r/min) 根 据 机 床 说 明 书 选 取 nw=63 r/min , 故 实 际 切 削 速 度9.51000 63301000 vdv w ( m/min) 切削工时 46.017.163 122221 fn llltw( min) 工序 :精镗孔至 36mm 根据机械加工工艺手册查 得 f=0.5mm/r nw=1000r/min=16.6r/s 切削速度 v=40m/min=0.67m/s 切削工时 14.06.01000107621 fnllltw( min) 工序:半精铣 30mm孔端面 根据切削手册 20.0zf mm/z 切削速度:根据相关手册 取 118v m/min 8.375100 11810001000 dw vn s( r/min) 现采用 X51立式铣床,根据机床说明书,取 nw=375 r/min。 nts故实际切削速度 5.1171000 3751001000 ww ndv( m/min) 当 nw=375 r/min 时,工作台每分钟进给量mf应为 37537552.0 wzm znff( mm/min) 查机床说明书,取 375mfmm/min 切削工时 27.037510021 mm flllt ( min) mt为加工一侧端面的时间,总工时 528.0264.02 t ( min) 工序 :半精铣 30mm孔端面。 根据切削手册 20.0zf mm/z 切削速度:根据相关手册 取 118v m/min 刀具与工序所使用刀具相同 125wdmm 4z 3001251181 0 001 0 00 dw vn s( r/min) 现采用 X51立式铣床,根据机床说明书,取 nw=300 r/min。 故实际切削速度 1181000 3001251000 ww ndv( m/min) 当 nw=300 r/min 时,工作台每分钟进给量mf应为 24030042.0 wzm znff( mm/min) 查机床说明书,取 2.235mfmm/min 切削工时 45.02.235406521 mm flllt ( min) mt为加工一侧端面的时间,总工时 90.045.02 t ( min) nts工序 :钻 2-10.5mm 孔 确定进给量 f :根据机械加工工艺手册 锻件硬度 149-187HBS mmd 5.100 取 f =0.234 mm/r。 切削速度:根据 相关手册,查得切削速度 6.12v m/min ,所以 3825.10 6.121 0 001 0 00 ws d vn( r/min) 根 据 机 床 说 明 书 选 取 nw=394 r/min , 故 实 际 切 削 速 度0.131000 3945.101000 vdv w ( m/min) 切削工时 65.0234.0394 124821 fn llltw( min) 工序 : 铣宽 为 4mm 的槽 根据切削手册 01.0zf mm/z 切削速度:根据相关手册 取 146v m/min 刀具采用 YT15 硬质合金面铣刀, 80wdmm 4z 581801461 0 001 0 00 dw vn s( r/min) 根 据 机 床 说 明 书 , 取 nw=600 r/min 。 故 实 际 切 削 速 度 1481000 600801000 ww ndv ( m/min) 当 nw=600r/min 时,工作台每分钟进给量mf应为 24600401.0 wzm znff( mm/min) 查机床说明书,取 52.23mfmm/min 切削工时 45.152.23122221 mflllt ( min) 最后,将以上各工序切削用量、工时定额的计算结果,连同其他加工数据一并填入机械加工工序过程综合卡片。 nts 三 .夹具设计 为了提高劳动生产率,保证加工质量,降低劳动强度,需要设计专用夹具。 经过与指导老师协商,决定设计第道工序 钻 37mm 孔的钻床夹具。本夹具将用于 Z3040 摇臂钻床,刀具为高速钢锥柄麻花钻 (一) 提出问题 本夹具用来钻 37mm 孔加工本道工序时,该孔有过 高的精度要求。因此,在本道工序加工时,主要考虑如何保证孔的定位,如何降低劳动强度、提高劳动生产率。 (二) 夹具设计 1. 定位基准的饿选择 由零件图可知,以 37mm 孔和 37mm 孔的一个端面为定位基准,采用支承钉为辅助支承,同时为了缩短本工序的辅助时间,应设计一个可以快速更换工件的夹紧装置。 2. 切削力和夹紧力的计算 刀具:高速钢锥柄麻花钻, 37mm 轴向力: 303133.1234.05.10600 7.010 FYFXFF KfdCF( N) 扭距: 93.111033.123 4.05.1054.33 310 38.09.130 MYFXFM KfdCMNm 在计算切削力时必须把安全系 数考
- 温馨提示:
1: 本站所有资源如无特殊说明,都需要本地电脑安装OFFICE2007和PDF阅读器。图纸软件为CAD,CAXA,PROE,UG,SolidWorks等.压缩文件请下载最新的WinRAR软件解压。
2: 本站的文档不包含任何第三方提供的附件图纸等,如果需要附件,请联系上传者。文件的所有权益归上传用户所有。
3.本站RAR压缩包中若带图纸,网页内容里面会有图纸预览,若没有图纸预览就没有图纸。
4. 未经权益所有人同意不得将文件中的内容挪作商业或盈利用途。
5. 人人文库网仅提供信息存储空间,仅对用户上传内容的表现方式做保护处理,对用户上传分享的文档内容本身不做任何修改或编辑,并不能对任何下载内容负责。
6. 下载文件中如有侵权或不适当内容,请与我们联系,我们立即纠正。
7. 本站不保证下载资源的准确性、安全性和完整性, 同时也不承担用户因使用这些下载资源对自己和他人造成任何形式的伤害或损失。

人人文库网所有资源均是用户自行上传分享,仅供网友学习交流,未经上传用户书面授权,请勿作他用。
2:不支持迅雷下载,请使用浏览器下载
3:不支持QQ浏览器下载,请用其他浏览器
4:下载后的文档和图纸-无水印
5:文档经过压缩,下载后原文更清晰
|