CA6140车床主轴箱的加工工艺及工装设计【含CAD图纸、说明书】
收藏
资源目录
压缩包内文档预览:(预览前20页/共28页)
编号:49447782
类型:共享资源
大小:2.78MB
格式:ZIP
上传时间:2020-02-14
上传人:机****料
认证信息
个人认证
高**(实名认证)
河南
IP属地:河南
50
积分
- 关 键 词:
-
含CAD图纸、说明书
CA6140
车床
主轴
加工
工艺
工装
设计
CAD
图纸
说明书
- 资源描述:
-
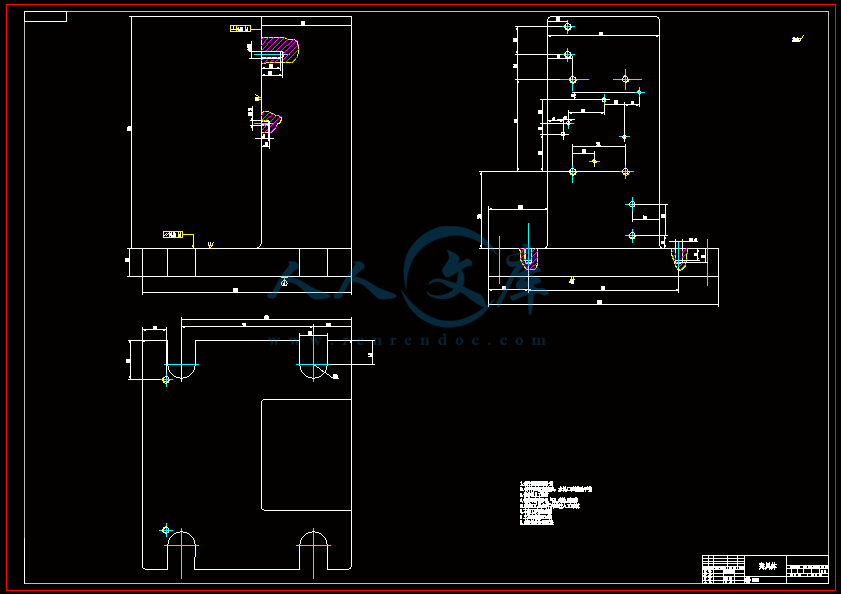
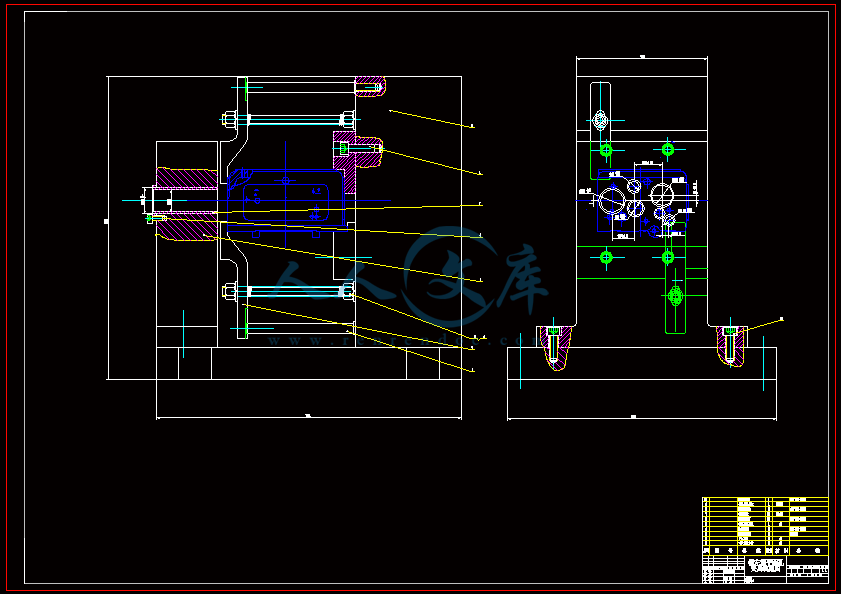
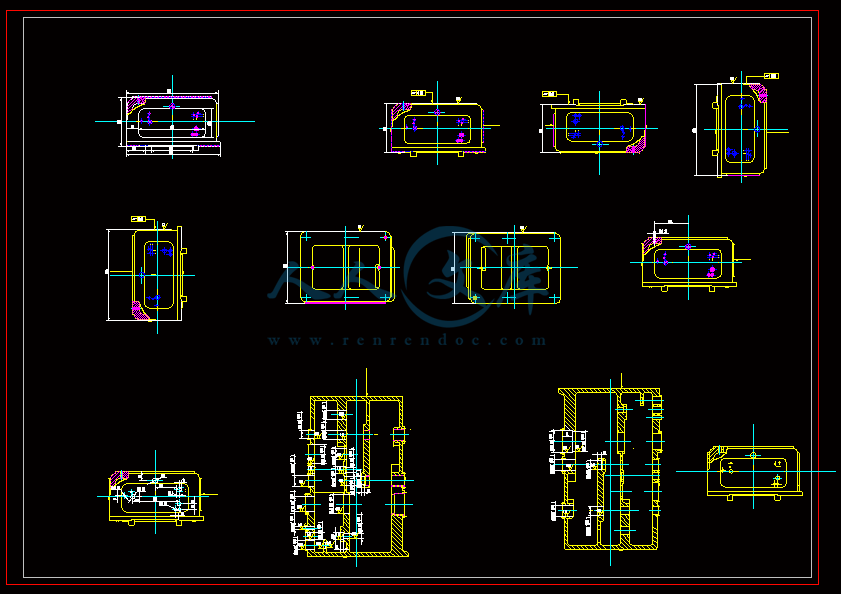
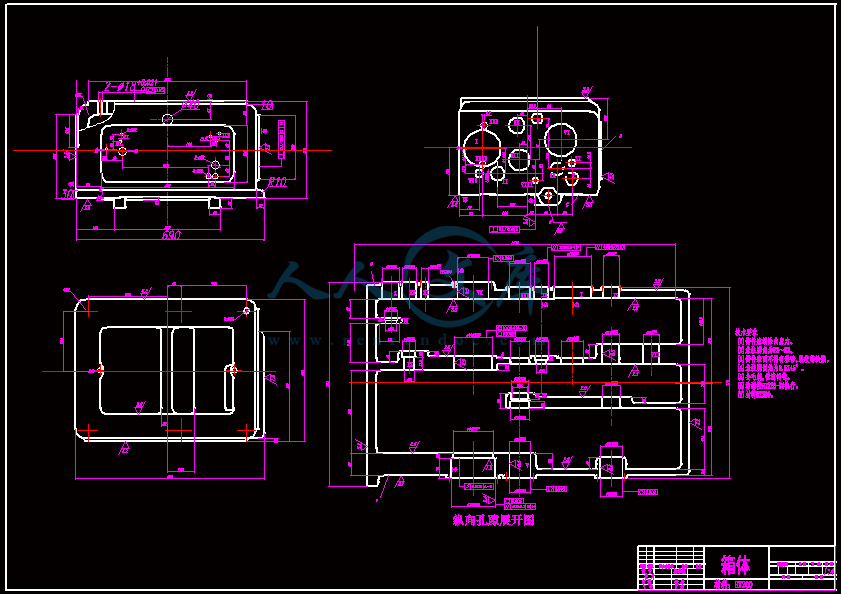
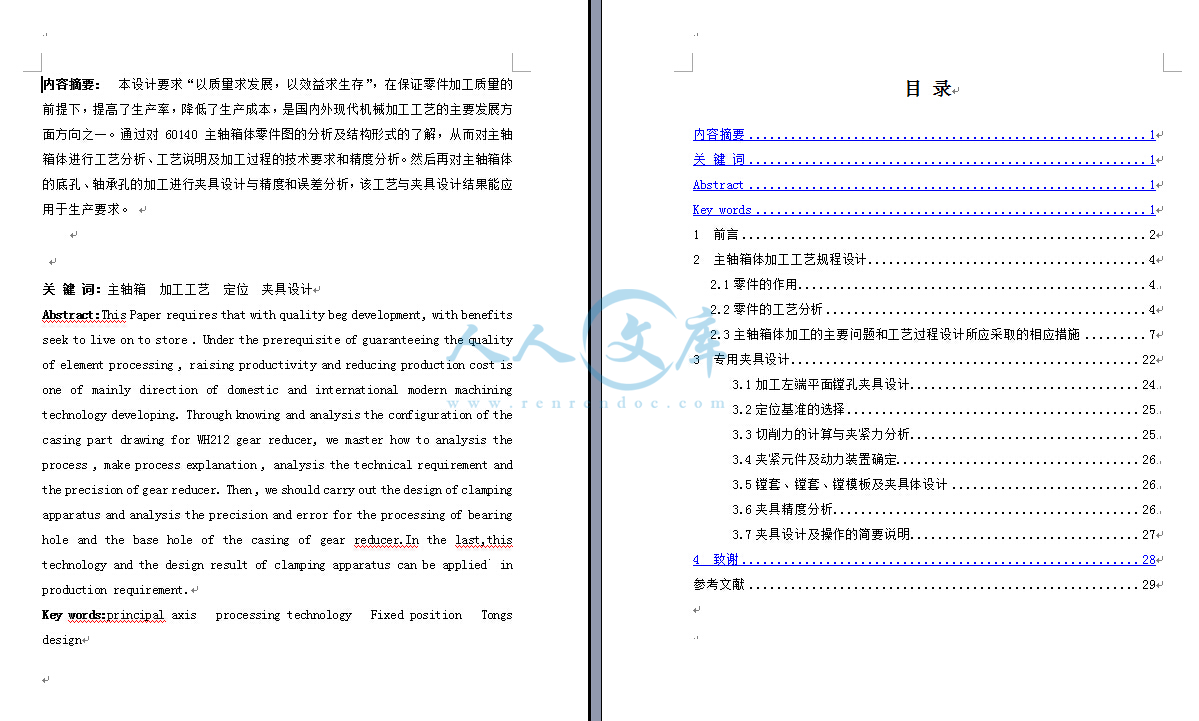
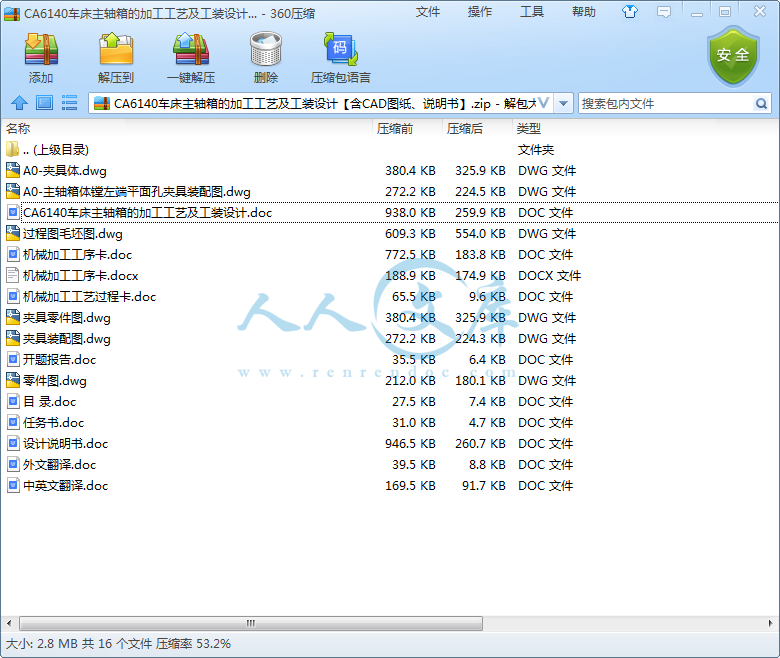
- 内容简介:
-
外文资料翻译 Mold CoolingOne fundamental principle of injection molding is that hot material enters the mold, where is cools rapidly to a temperature at which it solidifies sufficiently to retain the shape of the impression. The temperature of the mold is therefore important as it governs a portion of the overall molding cycle. While the meld flows more freely in a hot mold, a greater cooling period is required before the solidified molding can be ejected. Alternatively, while the meld solidifies quickly in a cold mold it may not reach the extremities of impression. A compromise between the two extremes must therefore be accepted to obtain the optimum molding cycle.The operating temperature for a particular mold will depend on a number of factors which include the following: type and grade of material to be molded; length of flow within the impression; wall section of the molding; length of the feed system, etc. It is often found advantageous to use a slightly higher temperature than is required just to fill the impression, as this tends to improve the surface finish of the molding by minimizing weld lines, flow marks and other blemishes.To maintain the required temperature differential between the mold and plastic material, water (or other fluid) is circulated through holes or channels within the mold. These holes or channels are termed flow-ways and the complete system of flow ways is termed the circuit.During the impression filling stage the hottest material will be in the vicinity of the entry point, i.e. the gate, the coolest material will be at the point farthest from the entry. The temperature of the coolant fluid, however, increases as it passes through the mold. Therefore to achieve an even cooling rate over the molding surface it is necessary to locate the incoming coolant fluid adjacent to hot molding surface and to locate the channels containing heated coolant fluid adjacent to cool molding surface. However as will be seen from the following discussion, it is not always practicable to adopt the idealized approach and the designer must use a fair amount of common sense when laying out coolant circuits if unnecessarily expensive molds are to be avoided.Units for the circulation of water (or other fluid) are commercially available. These units are simply connected to the mold via flexible hoses, with these units the molds temperature can be maintained within close limits. Close temperature control is not possible for using the alternative system in which the mold is connect to a cold water supply. It is the mold designers responsibility to provide an adequate circulating system within the mold. In general, the simplest systems are those in which holes are bored longitudinally through the mold plates. However, this is not necessarily the most efficient method for a particular mold.When using drillings for the circulation of the coolant, however, these must not be positioned too close to the impression (say closer than 16mm) as this is likely to cause a marked temperature variation across the impression, with resultant molding problems.The layout of a circuit is often complicated by the fact that flow ways must not be drilled too close to any other holes in the same mold plate. It will be recalled that the mold plate has a large number of holes or recesses, to accommodate ejector pins, guide pillars, guide bushes, sprue bush, inserts, etc. How close it is safe to position in a flow way adjacent to another hole depends to a large extent on the depth of the flow way drilling required. When drilling deep flow ways there is a tendency for the drill to wander off its prescribed course. A rule which is often applied is that for drillings up to 150mm deep the flow way should not be closer than 3mm to any other hole. For deeper flow ways this allowance is increased to 5mm.To obtain the best possible position for a circuit it is good practice to lay the circuit in at the earliest opportunity in the design. The other mold items such as ejector pins, guide bushes, etc. can then be positioned accordingly. Mold Cavities and CoresThe cavity and core give the molding its external shapes respectively, the impression imparting the whole of the form to the molding. When then proceeded to indicate alternative ways by which the cavity and core could be incorporated into the mold and we found that these alternatives fell under two main headings, namely the integer method and the insert method. Another method by which the cavity can be incorporated is by means of split inserts or splits.When the cavity or core is machined from a large plate or block of steel, or is cast in one piece, and used without bolstering as one of the mold plates, it is termed an integer cavity plate or integer core plate. This design is preferred for single-impression molds because of characteristics of the strength, smaller size and lower cost. It is not used as much for multi-impression molds as there are other factors such as alignment which must be taken into consideration.Of the many manufacturing processes available for preparing molds only two are normally used in this case. There are a direct machining operation on a rough steel forging or blank using the conventional machine tool, or the precision investment casting technique in which a master pattern is made of the cavity and core. The pattern is then used to prepare a casting of the cavity or core by or special process.A 4.25% nickel-chrome-molybdenum steel (BS 970-835 M30) is normally specified for integer mold plates which are to be made by the direct machining method.The precision investment casting method usually utilizes a high-chrome steel.For molds containing intricate impressions, and for multi-impression molds, it is not satisfactory to attempt to machine the cavity and core plates from single blocks of steel as with integer molds. The machining sequences and operation would be altogether too complicated and costly. The inset-bolster assembly method is therefore used instead.The method consists in machining the impression out of small blocks of steel. These small blocks of steel are known, after machining, as inserts, and the one which forms the male part is termed the core insert and, conversely, the one which forms the female part the cavity inserts. These are then inserted and securely fitted into holes in a substantial block or plate of steel called a bolster. These holes are either sunk part way or are machined right through the bolster plate. In the latter case there will be a plate fastened behind the bolster and this secures the insert in position.Both the integer and the insert-bolster methods have their advantages depending upon the size, the shape of the molding, the complexity of the mold, whether the single impression or a multi-impression mold is desire, the cost of making the mold, etc. It can therefore be said that in general, once the characteristics of the mold required to do a particular job which have been weighed up, the decision as to which design to adopt can be made.Some of these considerations have already been discussed under various broad headings, such as cost, but to enable the reader to weigh them up more easily, when faced with a particular problem, the comparison of the relative advantages of each system is discussed under a number of headings.Unquestionably, for single impression molds integer design is to be preferred irrespective of whether the component form is a simple or a complex one. The resulting mold will be stronger, smaller, less costly, and generally incorporate a less elaborate cooling system than the insert-bolster design. It should be borne in mind that local inserts can be judiciously used to simplify the general manufacture of the mold impression.For multi-impression molds the choice is not so clear-cut. In the majority of cases the insert-bolster method of construction is used, the ease of manufacture, mold alignment, and resulting lower mold costs being he overriding factors affecting the choice. For components of very simple form it is often advantageous to use one design for one of the mold plate and the alternative design for the other. For example, consider a multi-impression mold for a box-type component. The cavity plate could be of the integer design to gain the advantages of strength, thereby allowing a smaller mold plate, while the core plate could be of insert-bolster design which will simplify machining of the plate and allow for adjustments for mold alignment. Feed SystemIt is necessary to provide a flow-way in the injection mold to connect the nozzle (of the injection machine) to each impression. This flow-way is termed the feed system. Normally the feed system comprises a sprue runner and gate. These terms apply equally to the flow-way itself, and to the molded material which is removed from the flow-way itself in the process of extracting the molding.A typical feed system for a four-impression, it is seen that material passes through the sprue, main runner, branch runners and gate before entering the impression. As the temperature of molten plastic is lowered while going through the sprue and runner, the viscosity will rise; therefore, the viscosity is lowered by shear heat generated when going through the gate to fill the cavity. It is desirable to keep the distance that the material has to travel down to a minimum to reduce pressure and heat losses. It is for this reason that careful consideration must be given to the impression layout and gates design. 1. Sprue A spru is a channel through to transfer molten plastic injected from the nozzle of the in injector into the mold. 2. RunnerA runner is a channel that guides molten plastic into the cavity of a mold. 3. Gate A gate is an entrance through which molten plastic enters the cavity. The gate has the following functions: restricts the flow and the direction of molten plastic; simplifies cutting of a runner and molding to simplify finishing of parts; quickly cools and solidifies to avoid backflow after molten plastic has filled up in the cavity. 4. Cold Slug WellThe purpose of the cold slug well, shown opposite the sprue, is theoretically to receive the material that has chilled at the front of the nozzle during the cooling and ejection phase. Perhaps of greater importance is the fact that it provides positive means whereby the sprue can be pulled from the sprue bush for ejection purposes. The sprue, the runner, and the gate will be discarded after a part is complete. However, the runner and the gate are important items that affect the quality or the cost of pats. 模具冷却系统注塑生产的基本原理是把高温熔体注入模具型腔,熔体在型腔内迅速冷却到固化温度,并保持一定形状。由于模具温度在一定程度上控制塑件的整个成型周期,因此在生产中非常重要。熔体在高温模具内流动顺畅,但固化塑件推出前,一定的冷却阶段是比不可少的,另一方面,熔体在温度较低额模具中固化较快,又可能造成塑件末端填充不满。因此必须在这两种对立的条件中选择一个平衡点,以获得最佳的生产循环。模具的工作温度与几种因素有关,包括成型材料的等级与分类、熔体在型腔内的流动路线、塑件壁厚以及浇注系统长度等。使用比充模要求稍高的温度注塑比较有利,这样生产的塑件熔接痕少、流痕不明显,其他缺陷也较少,因此可提高塑件表面质量。为保持模具和塑料熔体之间所需的温差,水(或其他液体)在模具上的通道或通孔中循环。这些通道或通孔称为流道或水道,整个水道系统称为冷却循环系统。在充模阶段,温度最高的熔体位于进入口,即浇口附近;温度最低的熔体位于距进入口最远的地方。冷却介质在模具内循环时,介质温度将升高。因此,为使塑料表面获得均匀的冷却速率,冷却通道的入口应开设在高温塑件附近,受热后冷却介质温度升高,出口开设在低温塑件附近,设计者往往凭借经验设计冷却水道。 冷却水(或其他冷却介质)回路所需的部件在市场上就可以买到。这些部件通过软管与模具直接连在一起,通过这些部件形成的冷却回路,模具温度便控制在要求的范围内。但是,使用这种直接与冷水相连的冷却回路是不可能精确的控制模具的温度的。为模具提供合适的冷却系统是设计者的责任。通常,最简单的冷却系统是在模板上纵向钻出通孔。然而对于精密模具,这不是最有效的冷却方法。 使用钻孔的方法加工冷却水道时,冷却通道与塑件距离一定不能太近(即距离小于16mm),如果距离太近,有可能引起整个型腔的温度发生显著的变化,使塑件出现问题。冷却水道不能距离同一模板上任何其他的孔道太近,这使得冷却回路的布局通常比较复杂。,模板上存在大量的孔道或凹陷,用来安装推杆、导柱、导套、浇口套以及镶件等。冷却水道与其他孔道之间的安全距离在很大程度上取决于所需冷却水道的钻入深度。流道深度较深时, 钻头有偏离预定加工路线的趋势。常用的规则是钻入深度达到150mm的冷却水道与其他孔道距离不小于3mm,比这更深的流道所需的距离增加到5mm。 为获得最佳的冷却回路,设计初期就考虑冷却回路的位置不失为一种好方法。其他模具零件,如推杆、导套等,可相应的确定安装位置。 型腔和型芯模具的型腔和型芯分别形成塑件内部和外部形状,型腔形状决定了塑件外部形状,接下来我们简要说明选择哪种方式把型腔和型芯安装在模具中,这些方式可归纳为两大类,即整体式和镶拼式。另一种组成型腔的方式是加入拼块或滑块。当型腔或型芯由一块大的钢板或刚块加工而成,或者铸成一体,不需使用支承板件而形成一块模板时,就构成整体式型腔板或型芯板。这种设计因具有强度高、尺寸小和成本低的特性,而主要应用在单型腔模具中。整体式型腔和型芯一般不用在多用于多型腔模具中,因为多型腔模具设计时必须考虑一些其他因素,例如安装组合镶件等。 在模具制造的众多方法中,用于加工整体式型腔板或型芯板的方法主要有两种:使用传统机床对粗锻钢胚料直接加工,或利用精确的熔模铸造技术将胚料加工成型腔和型芯。用于制造型腔和型芯的胚料经常需要特殊工艺的处理。 通常,4.25%的镍铬钼合金钢(BS970-835M30)是生产整体模板的制定材料,选用这种材料时采用直接的机加工方式。精确的熔模铸造常常用来加工高铬钢。对于成型部模具和位复杂的多腔模,也像整体式模具那样用一块钢材加工型腔和型芯并不容易。如果采用整体式结构,则加工顺序和操作过程将变得非常复杂,成本也高,因此镶拼式装配方式替代了整体式。镶拼式型腔由小钢块加工而成。加工后的小钢块作为镶件,形成型芯部分的称为型芯嵌块,相反的,形成型腔部分的称为型腔嵌件。然后,把这些嵌件牢固的安装在被称为垫板的孔中,垫板有实心钢板或钢块加工而成。这些安装孔有的是由垫块的局部凹陷形成,有的是在垫板上直接加工而成的。在后一种方式中,垫板后部还要加一块模板,起加固作用,确保镶件安装到位。 整体式和镶拼式结构均有优点,这取决于塑件尺寸和形状、模具的复杂程度、所需的是单型腔模具还是多型腔模具以及模具的制造成本等。通常,塑件的形状、尺寸等特性确定后,采用哪种形式的型腔和型芯就已经确定了。在不同的章节中,我已经讨论过型腔和型芯的安装方式所涉及的问题,例如成本等。但为使读者在处理特殊问题时更容易知道重点所在,我们将用一定的章节再次讨论每种结构优缺点的对比。毫无疑问,对于单型腔模具,无论是简单还是复杂,整体式型腔是首选方式。若选择整体式,则模具的强度高、体积小、成本低,而冷却系统的设计却比镶拼式简单、方便。设计时需要常记于心的是,适当的使用镶件可以简单化模具型腔的加工制造难度。对于多型腔模具选择哪种方式不是很明显。大多数多型腔模具采用镶拼式结构,这种结构加工简单、装配容易、模具成本低,这些是影响选择哪种结构形式的最重要因素。一种非常简单且具有很多优点的设计形式是采用一种形式设计模板,而采用另一种形式设计模具的其他部分。例如,采用箱型组件设计多型腔模具。型腔板设计成小型整体式模板,以满足模具高强度的要求;型芯板则设计成镶拼式,可以简化模板加工过程,并且能根据模具需要进行调整。 浇注系统在注塑模具中,连接注塑机喷嘴和各个分流道型腔的流动通常是非常必要的,这种进料通道称为浇注系统。 通常,浇注系统由主流道、分流道和浇口组成。这些术语应用在相应的进料通道本身,以及取出塑件时从进一同取出的料通道中浇注系统凝料。可以看出,原料通过主流道、第一分流道、第二分流道和浇口注入型腔中。熔融塑料通过主流道和分流道时温度降低而使熔体粘度升高,然而当熔体通过浇口填入型腔时,由于剪切作用产生的热量又使粘度降低。浇注系统要保持适当长度,使熔体的压力减少且热量损失降到最低。因此,设计时必须充分考虑型腔分布和浇口形式。1、 主流道 主流道是将熔融塑料从注塑机喷嘴传递到模具型腔的通道。主流道是浇口套的一部分,浇口套是独立于模具的单独零件。2、 分流道分流道是引导熔融塑料进入模具型腔的通道。3、 浇口 浇口是熔融塑料进入型腔的入口。浇口有以下作用:约束熔体流动;引导熔体的流动方向;使分流道和塑件末端易于分离;快速冷却固化以防止熔融塑料充满型腔后倒流。4、 冷料井冷料井正对着主流道。理论上,冷料井的作用是用来储存在塑件冷却和推出过程中注塑机喷嘴处形成的熔体前锋冷料。也许冷料井更重要的作用是开模时帮助浇道凝料脱出浇口套。塑件成型后,主流道、分流道和浇口部分凝料将被遗弃。然而,分流道和浇口是影响塑件质量和成本的重要因素。外文资料翻译The Injection MoldingInjection molding ( British Engish : Molding ) is a manufacturing process for producing parts form both thermoplastic and thermosetting plastic materials.Material is fed into a heated brarel, mixed, and forced into a mold cavity where it cools and hardens to configuration of the mold cavity. After a product is designed, usually by an industrial designer or an engineer, molds aer made by a moldmaker ( or a toolmaker ) from metal, usually either steel or aluminium, and precision-machined to form the features of the desired part. Injection molding is widely used for manufacturing a varitey of parts, from the smallest compenent to entire body panels of cars.As shown in Fig.2-1, injection molding machines consist of a material hopper, an injection ram of screw-type plunger, and a heating unit. They are also known as presses. They hold the molds in which the compenents are shaped. Presses are rated by tonnage, which expresses the amount of clamping force that the machine can exert. This force keeps the mold closed during the injection process. Tonnage can vary from less than 5 tons to 6000 tons, with the higher figures used in determined by the projected area of the part being molded.This projected area is multiplied by a champ force of 2 to 8 tons for each square inch of the projected area. As a rule of thumb, 4 or 5 t/in can be used for most products. If the plastic material is very stiff, it will require more injection pressure to fill the mold, thus more clamp tonnage to hold the mold closed. The required force can also be determined by the material used and the size of the part, larger parts require higher clamping force. Actual injection molding is shown in Fig 2-2.Mold or die are the common terms used to describe the tooling used to produce plastic parts in molding.Traditionally, molds have been expensive to manufacture. They were usually only used in mass production where thousands of parts were being produced. Molds are typically constructed from hardened steel, pre-hardened steel, aluminium, and/or beryllium-copper alloy. The chioce of material to build a mold from is primarily one of economics. Steel molds generally cost more to construct, but their longer number of parts made before wearing out. Pre-hardened steel molds are less wear resistant and are used for lower volume requirements or large compenents. The steel hardness is tyoically 38-45 on the Rockwell-C scale ( HRC). Hardened steel molds are heat treated after machining. These are by far the superior in terms of wear resistance and lifespan. Typical hardness ranges between 50 to 60 Rockwell scale. Aluminium molds can cost substantially less , and when designed and machined with morden computerized equipment, can be economical for molding tens or even hundreds of thousands of parts. Beryllium copper is used in areas of the mold which require fast removal or area that see the most shear heat generated. The molds can be manufactured by either CNC or by using Electrical Discharge Machining processes.Standard two plates tooling: core and cavity are inserts in a mold base “Family mold ” of 5 different parts.The mold consists of two primary compenents, the injection mold ( A plate ) and the ejector mold ( B plate ) , as shown in Fig. 2-3. Plastic resin enters the mold through a sprue in the injection mold, the sprue bush is to seal tightly against the nozzle of the injection barrel of the molding machine and allow molten plastic to flow from the barrel into the mold , also known as cavity. The sprue bush directs the molten plastic to the cavity images through channels that are machined into the faces of the A or B plates. These channels allow plastic to run along them, so they are referred to as runners. The molten plastic flows through the runner and enters one or more specialized gates and into the cavity geometry to form the desired part.The amount of resin required to fill the sprue, runner and cavities of a mold is a shot. Trapped air in the mold can escape through air vents that are grinded into the parting line of the mold. If the trapped air is not allowed to escape , it is compressed by the pressure of the incoming material and is squeezed into the corners of the cavity , where it prevents filling and causes other defects as well . The air can become so compressed that it ignites and burns the surrounding plastic material. To allow for removal of the molded part from the mold , the mold features must not overhang one another in the direction that the mold opens , unless parts of the mold are designed to move from between such overhangs when the mold opens ( utilizing composnents called Lifters ). Three-plate Mold A simple mold of this type is shown in Fig .2-5,and a descripsion of the design and of theopening sequence follows.The mold consists of three basic prats ,namely :the moving half ,the floating cavity plate and the feed plate ,respectively. The moving half consists of the moving mold plate assembly,support blocks,backing plate,ejector assembly and the pin ejection system .Thus the moving half in this design is identical with the moving half of basic molds . The floating cavity plate ,which may be of the integer or insert-bolster design, is located on substantial guide pillars (not shown)fitted in the feed plate . These guide pillars must be of sufficient to perform the function of alignment between the cavity and core when the mold is being closed .Guide bushes are fitted into the moving mold plate and the floating cavity plate respectively . The maximum movement of the floating cavity plate is controlled by stop bolt assembly .The moving mold plate is suitably bored to provide a clearance for the stop bolt assembly . The stop bolts must be long enough to provide sufficlient space between the feed plate and the floating cavity plate for easy removal of the feeding system .The minimum space provided for should be 65 mm, just sufficient for an operator to remove the feed system by hand if necessary . The desired operating sequenc is for the first daylight to occur between the floating cavity plate and the feeding plate. This ensure the sprue is pulled from the sprue bush immediatel the mold is opened. To achieve this sequence, springs may be incorporated between the feed plate and the floating cavity plate. The springs should be strong enough to give an initial impetus to the floating plate to ensure it moves away with the moving half. It is normal practice to mount the springs on the guide pillars(Fig.2-6) and accommodate them in suitable pockets in the floating cavity plate. The major part of the feed system (runners and sprue ) is accommodated in the feed plate and to facilitate automatic operation the runner should be of a trapezoidal form so that once it is pulled from the feed plate it can easily be extracted. Note that if a round runner is used ,half the runner is formed in the floating cavity plate ,where it would remain ,and be prevented from falling or being wiped clear when the mold is opened . Now that we have consided the the mold assembly in some detail,we look at the cycle of operation for this type of mold. The impressions are filled via the feeding system and ,after a suitable dwell period ,the machine platens commence to open .A force is immediately exerted by the compression springs ,which causes the floating cavity plate to move away with the moving half as previously discussed .The sprue is pulled from the sprue bush by the sprue puller .After the floating cavity plate has moved a predetermined distance it is arrested by the stop bolts .The moving half continues to back and the molding ,having shrunk on to the cores , are withdrawn from the cavities .The pingate breaks at its junction with the runner . The sprue puller ,being attached to the moving half ,is pulled through the floating cavity plate and thereby releases the feed system which is then free to fall between the floating cavity plate .The moving half continues to move back until the ejector system is operated and the moldings are ejected. When the mold is closed the respective plates are returned to their molding position and the cycle is repeated. Mold Cavities and CoresThe cavity and core give the molding its external and internal shapes respectively, the impression imparting the whole of the form to the molding.We then proceeded to indicate alternate ways by which the cavity and core could be incorporated into the mold and we found that these alternatives fell under two main headings,namelythe integer method and the insert method.Another method by which the cavity can be incorporated is by means of split inserts or splits.When the cavity or core is machined from a large plate or block of steel,or is cast in one piece,and used without bolstering as one of the mod plates ,it is termed an integer cavity plate or integer core plate. This design is preferred for single-impression molds because of characteristics of the strength,smaller size and lower cost. It is not used as mush for multi-impression molds as there are other factors such as alignment which must be taken into consideration.Of the many manufacting processes available for preparing molds only two are normally used in this case. There are a direct machining operation on a rough steel forging or blank using the conventional machine tools, or the precision invstment casting technique in which a master pattern is made of the cavity and core. The pattern is then used to prepare a casting of the cavity or core by a special process.A 4.25%nickel-chrome-molybdenum steel(BS 970-835 M30) is normally specified for integer mold plates which are to be made by the direct machining method.The precision investment casting method usually utilizes a high-chrome steel.For molds containting intricate impressions, and for multi-impression molds, it is not satisfactory to attempt to machine the cavity and core plates from single blocks of steel as with integer molds. The machining sequences and operation would be altogether too complicated and costly. The insert-bloster assembly method is therefore used instead.The method consists in machining the impression out of small blocks of steel.These small blocks of steel are known,after machininf, as inserts, and the one which forms the male part is termed the core insert and, conversely, the one which forms the female part the cavity insert. These are the inserted and securely fitted into holes in a substantial block or plate of steel called a bloster. These holes are either sunk part way or are machined right through the bolster plate. In the latter case there will be a plate fastened behind the bolster and this secures the inserts in position.Both the integer and the insert-bolster methods have their advantages depending upon the size, the shape of the molding, the complexity of the mold, whether a single impression or a multi-impression ;old is desired,the cost of making the mold, ect. It can therefore be said that in general, once the characteristics of the mold reqired to do a particular job which have been weighed up, the decision as to which design to adopt can be made. Some of these considerations have already been discussed under various broad headings, such as cost, but to enable the reader to weigh them up more easily, when faced with a particular problem, the comparison of the relative advantages of each system is discussed under a number of headings. Unquestionably for single impression molds the integer design is ti be preferred irrespective of whether the component form is a simple or a complex one. The resulting mold will be stronger, smaller, less costly, and generally incorporate a less elaborate colling system than the insert-bolster design. It should be borne in mind that local inserts can be judiciously used to simplify the general manufactureof the mold impression.For multi-impression molds the choices is not so clear-cut. In the majority of cases the insert-bolster method of construction is used, the case of manufacture, mold alignment, and resulting lower mold costs being the overriding factors affecting the choices. For compenents of very simple form it is often advantangeous to use one design for one of the mold plates and the alternative design for the other. For example, consider a multi-impression mold for a box-type compenent. The cavity plate could be of the integer design to gain the advantages of strength, thereby allowing a smaller mold plate, while the core plate couls be of the insert-bolster design which will simplify machining of the plate and allow for adjustments for mold alignment. 注塑模具和注塑机注塑成型是将热塑性和热固性塑料加工成零件的制造过程。材料被入加热筒中,混合后压入模腔,冷却硬化成它们的形状。通常工业设计师或工程师设计完一个产品后,模具制造师(或工人)就会用金属,通常为刚或铝,制造模具,且精加工以达到理想效果。从最小的部件到整个汽车的面板,注塑成型广泛应用于各种零部件的制造。 如图Fig.2-1, 模具注塑机由一个料斗、注射活塞或螺旋式活塞以及一个加热装置构成。他们也被称为压力机,内含零部件形成的模具。压力机以吨位来衡量,表示机器可以施加的锁模力。锁模力保障模具在注塑的过程中是封闭的。吨位可以从少于5t到6000t,较高的吨位应用于相对少量的生产中。需要多少锁模力取决于零件的投影面积。每平方英寸的投影面积要乘以2-8t的锁模力。根据经验法则,每平方英寸的投影面积对应4-5t的锁模力,即可应用于大部分产品。如果塑料很硬,它需要更多的压力来填充模具,因此需要更多的锁模力来保障模具的封闭性。所需的压力也取决于使用的材料及零件的大小,越大的零件需要的锁模力越大。实际的注射成型是2-2图。注塑或冲模是描述注塑中用于制造塑料零件的工具的常用术语。传统上,模具制造一直很昂贵。它们通常只使用于成千上万的大批量零件的生产。模具通常由淬火钢、预硬钢、铝或铍铜合金制成。选择制造模具的原料首先要考虑经济因素,钢模具成本较高,但使用寿命较长。在用完之前,钢模能制造更多的零件,这会抵消最初的高成本投入。预硬钢模具不耐磨,适用于小批量生产或制造较大的零件。钢的硬度通常是38-45HRC,淬硬钢模具加工后要进行热处理。这类模具在耐磨性和使用寿命方面具有较强的优势,其典型的硬度范围介于50-60HRC之间。铝模具成本大幅度减少,利用现代计算机设备设计与加工,对于注塑成千上万个零件来说是经济的。铍-铜合金使用于制造需快速去热或消除产生的热能的模具。这类模具可利用数控加工或电火花加工来生产。标准的两板模具包括:型芯和型腔所在的模具内部,其余的则为五个不同的典型模具结构。模具有两个主要部分构成:合模(A板)和出模(B板)。塑料树脂通过注塑模具浇道进入模具,浇口套密封紧接在注塑机注射料筒的喷嘴处,让熔化的塑料从料筒流到模具,也就是型腔。浇口套通常加工成A、B板的管道引导熔化的塑料流向型腔。这些管道使塑料沿着他们流动,进入几何形状的型腔,形成所需的零件。填充模具浇口套、流道和型腔的大量树脂是一瞬间。模具里积存的空气可以通过模具分型线的通风口排出。如果积存的空气不能排出,进料的压力会把它们挤压到型腔的角落,这会妨碍填充并导致其他问题。空气压缩到一定程度会被引燃,导致周围的塑料燃烧。为了消除成型模具某个部分,模具不能彼此悬垂于模具打开的方向,除非该模具部分设计成模具打开时悬空一定(所用的组件称为侧抽芯)。模具基本结构这种简单的模具结构图2-5所示,磨具设计和开模顺序在以下的篇幅中论述。模具又三个基本部分组成,分别是动模部分、浮动型腔和定模板。动模部分包括动模板组件、支撑块、支撑板、推出结构和顶杆推出系统。这样设计的动模部分与最基本的模具结构中的动模部分相同。浮动型腔板通过导柱(图2-5没有示出)固定在定模板上,设计形式可以是整体式,也可以是嵌入式。导柱必须有足够的长度,以便模具工作时支撑浮动型腔板完成开合动作,并在模具合模时完成对型腔和型芯的找正。导套分别安装在动模板和浮动型腔板上。浮动型腔板的最大运动距离由限位钉或类似装置控制。在动模板的适当位置钻孔,以便安装限位钉。限位钉必须有足够的长度,为定模板和浮动型腔板之间提供足够的空间,从而使浇注系统凝料顺利脱落。如果必须使用手动方式取出凝料,开模时取出凝料所需的最小距离应为65mm。模具的开模顺序是:浮动型腔板和定模板先分开,确保模具打开时浇注系统凝料立即从浇口套中脱出。为实现这样的顺序,动模板和浮动型腔板之间装有弹簧。弹簧的弹力必须足够大,以确保在初始推力的作用下浮动型腔板跟随动模部分一起运动。弹簧套在到导柱上,一同装在浮动型腔板上相应的弹簧座处,这种形式再弹簧装配中十分常见。 浇注系统的主要部分开设在定模板上,为便于自动操作,分流道应采用梯形截面,以便于脱出浇注系统凝料。注意,如果采用圆形分流道,分流道的一半开设在浮动型腔板上,将阻碍凝料的脱。现在我们将详细讨论模具的装配,先看这类模具的生产循环过程。 熔体经过浇注系统充满型腔后,经过适当的保压过程,注塑机带动模具开模。压塑弹簧的弹力立即释放出来,推动浮动型腔板和动模部分一起移动,如同前面论述的一样。主流道凝料被拉料杆从浇口套中拉出。浮动型腔板移动预定距离后,被限位钉限位。动模部分继续后移,塑件由于收缩作用包紧再型芯上而从型腔中脱出。点浇口再接合处拉断,与分流道脱离。 安装在动模部分的拉料杆脱离浮动型腔板,浇注系统凝料由此脱下,然后在浮动型腔板和定模板之间自由落下。冬末部分继续后退,直到推出机构开始运动,退出塑件。合模时,模具的各模板回到成型位置,重复下一个注塑循环。 型腔和型芯模具的型腔和型芯分别形成塑件内部和外部形状,型腔形状决定了塑件形状,接下来我们简要说明选择那种型腔和型芯安装在模具中。这些方式可以归纳为两大类,即整体形式和镶拼形式。另一种组成型腔的方式是加入拼块或滑块。 当型腔或型芯由一块大的钢板或钢块加工而成,或是铸成一体,不需要使用支撑件而形成一块模板时,就构成整体式模腔板或型芯板。这种设计因具有强度高,尺寸小和成本低的特性,而主要应用在单型腔模具中。整体式型腔和型芯一般不用在多型腔模具中,因为多型腔模具设计时必须考虑一些其他因素,例如安装组合镶件等。在模具制造的众多方法中,用于加工整体式型腔板或型芯板的方法主要有两种:使用传统机床对粗段钢材料直接加工,或是利用精确的熔模铸造技术将坯料加工成型腔和型芯。用于制造型腔和型芯的坯料经常需要特殊工艺的处理。 通常,4.25%的镍镉钼合金钢是生产整体式模板的指定材料,选用这种材料时采用直接的机加工方式。 精确的熔模铸造常常用来加工高铬钢。 对于成型部位复杂的模具和多腔模具,也像整体式模具那样用一块钢材加工型腔和型芯并不容易。如果采用整体式结构,则加工顺序和操作过程将变得非常复杂,成本也高,因此镶拼式装配方式替代了整体式。 镶拼式型腔由小钢块加工而成。加工后的小钢块作为镶件,形成型芯部分的称为型芯嵌件,相反地,形成型腔部分的成为型腔嵌件。然后,把这些镶件牢固地安装在被称为垫板的孔中,垫板由实心钢板或钢块加工而成。这些安装孔有的是由垫板的局部凹陷形成,有的是在垫板上直接加工而成。在后一种方式中,垫板后部还要增加一块模板,起加固作用,确保镶件安装到位。 整体式和镶拼式结构均有优点,这取决于塑件尺寸和形状,模具的复杂程度,所需的是单型腔模具还是多型腔模具以及模具制造成本等。通常,塑件的形状,尺寸等特性确定后,采用哪种形式的型腔和型芯就已经确定了。 在不同的章节中,我们已经讨论过型腔和型芯的暗黑族昂方式所涉及的问题,例如成本等,但为使读者在处理特殊问题时更容易知道重点所在,我们将用一定的章节再次讨论每种结构优缺点的对比。 毫无疑问,对于单型腔模具,无论是简单还是复杂,整体式型腔是首选方式。若选择整体式,则模具的强度高,体积小,成本低,而冷却系统的设计却比镶拼式简单,方便。设计时需要常记于心的是,适当地使用镶件可以简化模具型腔的加工制造难度。 对于多型腔模具,选择哪种方式不是很明显。大多数型腔模具采用镶拼式结构,这种结构加工简单,装配容易,模具成本低,这些是影响选择哪种结构形式的重要因素。一种非常简单且具有很多优点的设计是采用一种形式设计模板,而采用另一种形式设计模具的其他部分。例如,采用箱形组件设计多型腔模具。型腔板设计成小型整体式模板,以满足模具高强度的要求;型芯板则设计成镶拼式,可因简化模板加工过程,并且能根据模具需要进行调整。Die basics with eight basic componentsA stamping die is a special, one-of-a-kind precision tool that cuts and forms sheet metal into a desired shape or profile. Most dies are constructed of several basic components, including die plates, shoes, die sets, guide pins, bushings, heel blocks, heel plates, screws, dowels, and keys. Dies also need stripper, pressure, and drawing pads, as well as the devices used to secure themspools, shoulder bolts, keepers, and retainers; and gas, coil, or urethane springs.A stamping die is a special, one-of-a-kind precision tool that cuts and forms sheet metal into a desired shape or profile. The dies cutting and forming sections typically are made from special types of hardenable steel called tool steel. Dies also can contain cutting and forming sections made from carbide or various other hard, wear-resistant materials.Most stamping dies are constructed of several basic components, including die plates, shoes, die sets, guide pins, bushings, heel blocks, heel plates, screws, dowels, and keys. Dies also need stripper, pressure, and drawing pads, as well as the devices used to secure them: spools, shoulder bolts, keepers, and retainers, as well as gas, coil, or urethane springs.1. Die Plates, Shoes, and Die SetsDie plates, shoes, and die sets are steel or aluminum plates that correspond to the size of the die. They serve as the foundation for mounting the working die components. These parts must be machinedmilled or groundso that they are parallel and flat within a critical tolerance. Although grinding is the most popular, a milled surface now can be obtained that is as accurate as a ground surface.Most die shoes are made from steel. Aluminum also is a popular die shoe material. Aluminum is one-third the weight of steel, it can be machined very quickly, and special alloys can be added to it to give it greater compressive strength than low-carbon steel. Aluminum also is a great metal for shock adsorption, which makes it a good choice for blanking dies.The upper and lower die shoes assembled together with guide pins create the die set. The lower die shoe often has machined or flame-cut holes that allow slugs and scrap created in the die to fall freely through the die shoe onto the press bed. The holes also may serve as clearances for gas springs and other die components.The die shoe thickness is based on how much force can be expected during cutting and forming. For example, a coining die, one that compresses metal by squeezing it between an upper and lower die section, requires a much thicker die shoe than a simple bending die.2. Guide Pins and BushingsGuide pins, sometimes referred to as guide posts or pillars, function together with guide bushings to align both the upper and lower die shoes precisely. They are precision-ground components, often manufactured within 0.0001 in. Although numerous specialty mounting methods can be used to install these components, there are only two basic types of guide pins and bushingsfriction pins and ball bearing-style pins.Friction pins are precision-ground pins that are slightly smaller than the guide bushings inside diameter. Pins are made from hardened tool steel, while bushings often are made from or lined with a special wear-resistant material called aluminum-bronze. The aluminum-bronze may contain graphite plugs that help to reduce friction and wear that occur to the pins and bushings.Friction pins also help to heel the die shoes and prevent them from moving from side to side.Precision or ball bearing-style guide pins comprise precision-hardened pins, ball cages, ball bearings, and bushings. Unlike friction pins, these pins ride on a series of ball bearings contained in a special aluminum ball cage that permits the bearings to rotate without falling out. These pins have several advantages. First, friction is reduced so the die can run at faster speeds without generating excessive friction and heat. Second, they allow the diemaker to separate the upper and lower die shoes easily. Third, because they use ball bearings, they can be manufactured with greater accuracy than friction pins.Remember, guide pins are meant to align the upper and lower die shoes, not to align a poorly maintained or sloppy ram in a press! Some companies try to compensate for a poorly maintained press by adding oversized guide pins or grinding the guide pin ends to a cone shape. Care must be taken when flipping die shoes over so that the guide pins are not bent. 3. Heel Blocks and Heel PlatesHeel blocks are special steel blocks that are precision-machined, screwed, doweled, and often welded to both the upper and lower die shoes. They contain components called wear plates and function to adsorb any side thrust that may be generated during the cutting and forming processes. They are especially important if the generated force is one-directional. Too much force generated from one direction only can cause the guide pins to deflect, which results in misalignment of critical cutting and forming components.Most heel blocks have steel heel plates, and the heel block on the opposite shoe has a wear plate made from aluminum-bronze or some other dissimilar metal. The plate selection process is critical. Using two opposing plates made of the same metal type can result in high friction, heat, and eventually galling or cold welding of the wear plates. Heel blocks can be used to heel the die in any or all directions. Box heels often are used to heel the die in all directions.4. Screws, Dowels, and KeysScrews fasten and secure the working components to both the upper and lower die shoes. The socket head cap screw is the most popular fastener used in stamping dies. This hardened tool steel screw, often referred to as an Allen head screw, offers superior holding power and strength.Dowels are hardened, precision-ground pins that precisely locate the die section or component in its proper location on the die shoe. Although dowels have much heeling ability, their main function is to locate the die section properly.Keys are small, rectangular blocks of precision-ground steel that are inserted into milled pockets in the die shoes and sections called keyways. Keys locate and heel die sections and components.5. PadsA pad is simply a pressure-loaded plate, either flat or contoured, that holds, controls, or strips the metal during the cutting and forming processes. Several types of pads are used in stamping dies. Depending on their function, pads can be made from soft low-carbon steel or hardened tool steel. Contoured pads must fit very closely to the mating die section. Precision requirements determine whether the pads are positioned with guide pins and bushings or left unguided.Stripper Pads/Plates. Stripper pads are flat or contoured spring-loaded plates that pull, or strip, the metal off the cutting punches (see Figure 1). When it is cut, metal naturally tends to collapse around the body or shank of the cutting punches; this is especially true during piercing. The stripper pad surrounds the cutting punches and mounts to the upper die shoe. As the punch exits the lower die, the spring-loaded pad holds the metal down flush with the lower die section, which allows the cutting punches to withdraw from the sheet metal or piece part.Figure 1Keys locate and heel die sections and components.Often stripper pads are inserted with a small block of steel called a pad window. This pad window usually is small and lightweight and can be removed easily to allow the die maintenance technician to remove the ball lock-style pierce punch from the retainer without removing the entire stripper pad. Stripper pads also function to hold the metal flat or to the desired shape during the cutting process.Pressure Pads/Plates. During the wipe bending process, the metal must be held down tightly to the lower die section before the forming punch contacts the metal. Pressure pads must apply a force that is at least equivalent to the bending force . Most pressure pads use high-pressure coil or gas springs. When loaded with very high-pressure springs, contoured or flat pads also can form sheet metal. These pad types often are referred to as power punches.Draw Pads. Draw pads control metal flow during the drawing process (see Figure 2). In drawing, the amount of pressure, or downward force, exerted on the sheet metal determines how much metal is allowed to flow and enter the draw die cavity. Too much pressure may stop the metal from flowing and cause splitting; too little downward force may allow excess metal to flow inward and cause loose metal or wrinkling.Figure 2Draw pads control metal flow during the drawing process.Draw pads, often referred to as binders or blank holders, usually are made from hardened tool steel. They can be flat or contoured, depending on the piece part shape. Most drawing dies use a single draw pad; however, in special cases, some use two.6. Spools, Shoulder Bolts, and KeepersSpools, shoulder bolts, and keepers are used to fasten pads to the die shoes while allowing them to move up and down. They are secured to either the top or bottom die shoe with screws and often dowels for precision location. Of all of the components used for securing pads, spools are the most common, especially in larger dies.7. RetainersRetainers hold or secure cutting or forming die components to both the upper and lower die shoes. One of the most popular retainers is a ball-lock retainer, a high-precision, accurately manufactured die component that secures and aligns both cutting and forming punches. It uses a spring-loaded ball bearing to locate and secure the punches, which feature a precisely machined teardrop or ball seat. The spring-loaded ball bearing locks into the teardrop shape and prevents the punches fro
- 温馨提示:
1: 本站所有资源如无特殊说明,都需要本地电脑安装OFFICE2007和PDF阅读器。图纸软件为CAD,CAXA,PROE,UG,SolidWorks等.压缩文件请下载最新的WinRAR软件解压。
2: 本站的文档不包含任何第三方提供的附件图纸等,如果需要附件,请联系上传者。文件的所有权益归上传用户所有。
3.本站RAR压缩包中若带图纸,网页内容里面会有图纸预览,若没有图纸预览就没有图纸。
4. 未经权益所有人同意不得将文件中的内容挪作商业或盈利用途。
5. 人人文库网仅提供信息存储空间,仅对用户上传内容的表现方式做保护处理,对用户上传分享的文档内容本身不做任何修改或编辑,并不能对任何下载内容负责。
6. 下载文件中如有侵权或不适当内容,请与我们联系,我们立即纠正。
7. 本站不保证下载资源的准确性、安全性和完整性, 同时也不承担用户因使用这些下载资源对自己和他人造成任何形式的伤害或损失。

人人文库网所有资源均是用户自行上传分享,仅供网友学习交流,未经上传用户书面授权,请勿作他用。