DG500型圆管带式输送机的设计
新型辅助运输设备机械课程毕业设计
圆管带式输送机的设计
DG500型圆管带式输送机的设计【优秀新型辅助运输设备机械课程毕业设计含13张CAD图纸】
【带任务书+外文翻译】【66页@正文30000字】【详情如下】【需要咨询购买全套设计请加QQ1459919609】
A0-总图.dwg
A1-头部清扫器.dwg
A2-圆形托辊组.dwg
A2-头部机架.dwg
A2-头部漏斗.dwg
A2-尾部机架.dwg
A2-支架.dwg
A2-螺旋张紧装置.dwg
A3-托辊支架.dwg
A3-支腿.dwg
A3-改向滚筒.dwg
任务书.docx
南非金矿的刮刀绞盘电机 -他们的失败调查外文文献翻译.docx
圆管带式输送机说明书.doc
张紧螺杆.dwg
改向滚筒组件.dwg
任务书
毕业设计题目:圆管带式输送机
毕业设计专题题目:
毕业设计主要内容和要求:
1、查阅有关资料、完成圆管带式输送机总体方案的设计;
2、完成驱动装置及总体结构设计;
3、完成电动滚筒设计;
4、机架及主要组件、零件图设计及零件加工工艺编制;
5、编写完成整机设计计算说明书、中英文翻译,包括图表不少于15000字;
6 完成不少于3000字的英译汉翻译;
7 完成机械图纸总量不少于3张0号图纸。
摘 要
DG500型圆管带式输送机是一种新型的辅助运输设备。该型运输机设计的目的主要应用于面粉厂两车间之间面粉的运输,同时也适应于清洁快速的连续短距离输送颗粒性的物品。
DG500型圆管带式输送机主要由电动滚筒、联轴器、改向滚筒、输送带、托辊、机架、拉紧装置、清扫器与给料系统等组成。
该型输送机采用封闭式运输可防止外部杂物混入输送物料,也能防止物料遭受雨淋、日晒,并可实现承载段和回程段完全封闭输送,原理上可以避免漏料、洒料等,可满足环保要求。
DG500型圆管带式输送机在运量上可以完成100t/h,运输量较大,并且采用更换机架的形式可以进行倾斜、垂直、转弯等一系列普通带式运输机所不能完成的运输方式。
该型输送机结构紧凑,结构为近似对称布置;输送距离短,方便移动;运转平稳,安全可靠,安装方便。
关键词:输送机; 封闭运输
ABSTRACT
DG500 pipe belt conveyor is a novel type of auxiliary transport equipment. It is designed to transport flour between the two workshops. Besides, it can be used to transport the clean and fast continuous short-range particles items. DG500 pipe belt conveyor mainly composed of electric drum, couplings, bend pulley, belt, roller, frame, tensioning device, cleaning device and feed system components. The bearing segment and return segment of this type of conveyor is complete closed transport. This characteristics can prevent transportation of materials from external debris. Meanwhile, it can prevent materials from rain and sun. So, in principle, this type of conveyor can avoid leakage, spilled materials, etc, and can meet the environmental requirements. DG500-type pipe belt conveyor transportation volume is large, and can finish the transportation volume of 100t / h, and through replace the rack, it can be used to tilted, vertical, turning transport which is the common mode of transport can not complete. This type of conveyor has the feature of compact in frame, approximately symmetrical arrangement of structure; transmission distance is short, easy movement; smooth running, safe and reliable, and easy installation.Keywords: conveyor; closed transport;
目 录
1概述1
1.1封闭输送带式输送机的分类1
1.1.1 圆管带式输送机1
1.1.2 吊挂带式输送机3
1.1.3 异型截面带式输送机4
1.1.4 各种密闭输送带式输送机的特点对比5
1.2 圆管带式输送机的特点6
1.2.1 优点6
1.2.2 缺点6
1.3 圆管带式输送机的发展7
1.3.1 圆管带式输送机的发展水平7
1.3.2 圆管带式输送机的理论研究8
1.4 圆管带式输送机的组成9
1.5 本文主要的工作9
2 圆管带式输送机的总体设计10
2.1 主体结构10
2.2 机架组合形式12
2.3 输送带13
2.3.1输送带类型13
2.3.2 成圆方式15
2.3.3密封方式16
2.3.4放置方式16
2.4 托辊17
2.5 机架18
2.6 附加部件18
2.7 驱动装置20
2.8 启动系统20
3 圆管带式输送机的总体计算21
3.1 设计的条件21
3.2 输送机横截面积A,带速v和管径D的计算21
3.3 输送机功率的估算22
3.4 张力计算23
3.4.1 有效张力计算23
3.4.2 最大张力计算24
3.5 成圆损失24
3.6 输送带下垂度24
3.7 输送带层数25
3.8 验算托辊载荷26
4 输送带的选择与设计28
4.1 输送带分类与结构28
4.1.1 输送带的分类28
4.1.2 输送带结构29
4.1.3 带芯30
4.1.4 编织方法对强度的影响31
4.1.5 圆管式输送带技术规格31
4.2 输送带宽度及滚筒直径的计算31
4.2.1 输送带宽度计算31
4.2.1 滚筒直径的计算32
4.3 输送带工作张力32
4.3.1最大工作张力32
4.3.2 输送带的安全系数33
4.3.3 额定拉断力33
4.3.4 输送带疲劳强度安全系数33
5 托辊的设计与选择35
5.1 托辊的选择35
5.1.1 缓冲托辊35
5.1.2 成圆托辊35
5.1.3 圆形托辊36
5.1.4 辊子载荷计算38
5.2 托辊轴承39
5.2.1轴承的选定与安装39
5.2.2 轴承的寿命40
5.2.3轴承的拆卸与清洗41
6 滚筒的设计与选择42
6.1 滚筒分类和形式42
6.1.1 按驱动方式分类42
6.1.2 按轴承内孔大小分类42
6.1.3 按外形区分42
6.1.4 按功能区分43
6.2 滚筒规格43
6.2.1 传动滚筒基本直径和长度43
6.2.2 改向滚筒外形尺寸44
6.3 滚筒的轴45
6.3.1 轴设计的程序46
6.3.2 轴的强度计算46
6.4 电动滚筒47
6.4.1 电动滚筒的作用47
6.4.2 电动滚筒功率计算48
6.4.3 电动滚筒转矩计算48
7 输送机的线路及机架的设计50
7.1 线路设计50
7.2 成圆段设计50
7.2.1 成圆段的长度50
7.2.2 过渡段托辊的布置52
7.3 机架的设计52
7.3.1 带式输送机布置准则52
7.3.2 圆管带式输送机机架设计53
8 给料系统、拉紧装置与清扫器的设计54
8.1 给料系统54
8.1.1 给料机的分类54
8.1.2 给料机的特点54
8.2拉紧装置55
8.2.1 拉紧装置的功能55
8.2.2拉紧装置的分类56
8.3 清扫器56
9 总结59
1概述
随着现代化发展的要求,环保成为当今时代一个日趋重要的问题,在世界范围内引起广泛关注。输送系统在工作中产生的粉尘和撒料,对环境污染已经引起世界各国输送机设计、制造和使用部门以及行政管理部门越来越多的关注。为了减少输送过程的污染,提倡环保无害化输送物料,从而导致人们对封闭输送的开发和研究。
封闭输送带式输送机是以特殊的机械结构,通过输送带的围包将散状物料包裹在输送带的内部进行输送。封闭输送带式输送机在某种程度上具有管道输送的特点,但是在宏观上物料和输送带没有相对运动,而是被输送带包裹着随输送带一起运行来完成物料的输送任务。
对该机种的研究与开发是从20世纪70年代开始,至今已经出现了多种形式的封闭型带式输送机,其基本形式有圆管带式,吊挂式,和其他异型管式(指断面形状而言)带式输送机等。
参考文献
[1] 成大先. 机械设计手册(第四版,第一卷).北京:化学工业出版社,2002
[2] 成大先. 机械设计手册(第四版,第二卷).北京:化学工业出版社,2002
[3] 成大先. 机械设计手册(第四版,第三卷).北京:化学工业出版社,2002
[4] 成大先. 机械设计手册(第四版,第四卷).北京:化学工业出版社,2002
[5] 成大先. 机械设计手册(第四版,第五卷).北京:化学工业出版社,2002
[6]张钺.新型圆管带式输送机设计手册.北京.化学工业出版社,2006
[7]张钺.皮带机设计原理和应用.贵阳.史州人民出版社.1980
[8]叶云岳.直线电机技术手册.北京.机械工业出版社.2003
[9]戴光皓.粮食输送机械.郑州:河南出版社.1991
[10]夏炽宁.胶带输送机在电厂应用情况与技术要求,连续输送技术.1991.(3-4):947
[11]美国输送设备制造商协会联合会编.散状物料输送机.北京.机械工业出版社.1985
[12]宋伟尉,张国伟,邓永胜.圆管带式输送机过渡段计算机仿真与设计,东北大学学报(自然科学版).2003, 24
[13]张安宁,李洪久.圆管带式输送机过渡段长度的确定.煤矿机械,1995.(4)115
[14]宋伟刚.带式输送机的动力学模型,连续输送技术.1995.(2).20
[15]徐振渡,付兴承,压带式无倾角带式输送机若干机理探讨.连续输送技术.1988.(2)130
[16]郭永存,张安宁,圆管带式输送机过渡段长度的确定.矿山机械.1995.(2);26
[17]宋伟刚,彭兆行.气垫带式输送机的设计与计算.矿山机械.1994.(6-7-8).43
[18]张钺,法国长距离带式输送机的设计特点.连续输送技术.1990.(1):41
[19]张钺,刘宇琦.国内外圆管带式输送机的新发展.矿山机械.2000.(8)。63
[20]张钺,刘宇琦.中间直线摩擦传动胶带输送机设计原理和应用,连续输送技术.1988,(1-2);17
[21]Horak R.M. Improved Idler Panel Design for Pipe conveyor. Bulk Solids Handling, 1997, (17):S21
[22] Marton A. E. Tubular Pipe ConVeyor Design Using a Standard Belt. Bulk Solids Handling, 2000, (20):39
[23] Marton A. E. Tubular Pipe Convcyor Design A review of cmss selection and belt selection Bulk Solids Handling,

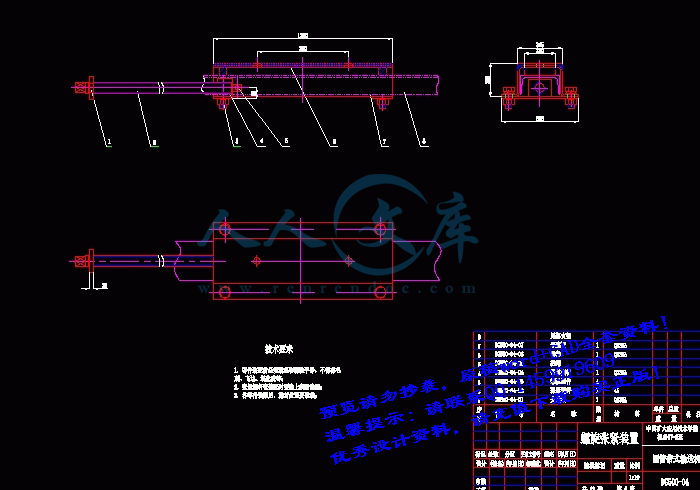


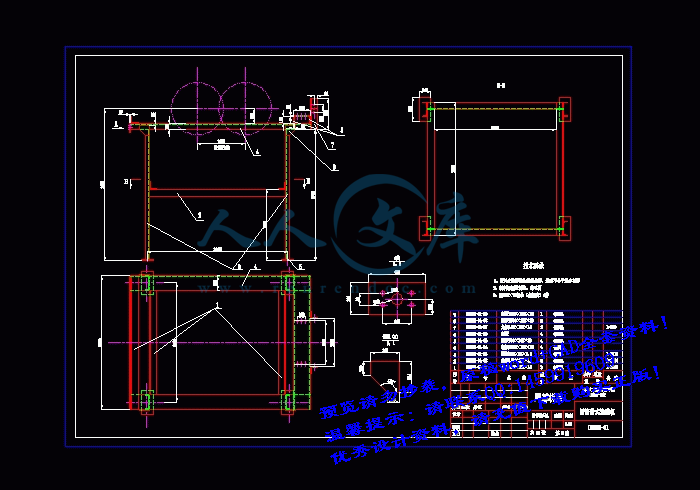


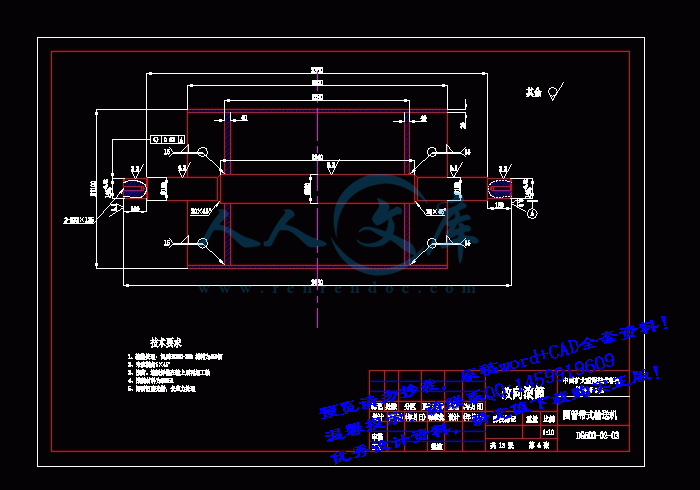
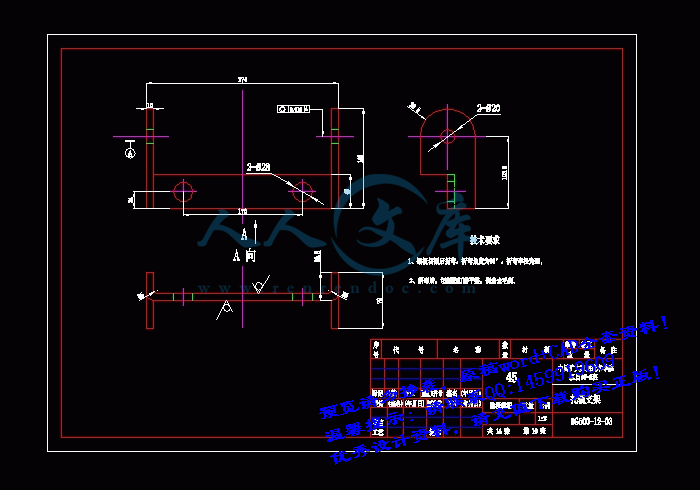


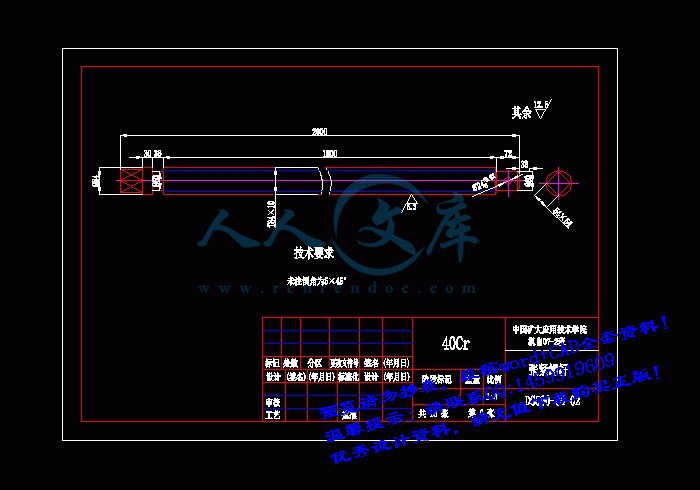

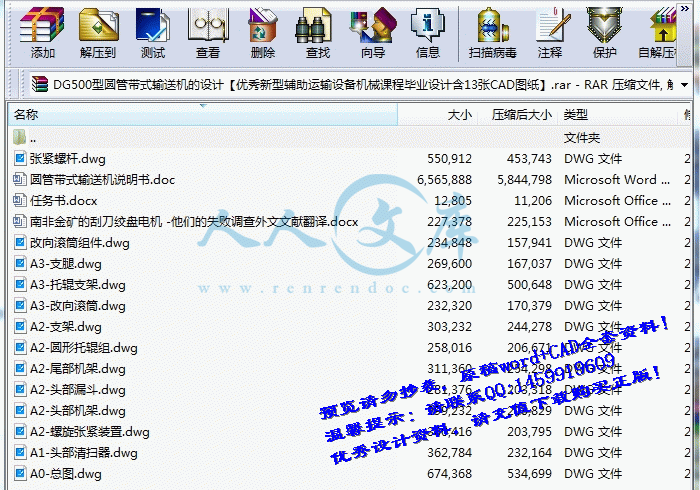
