!【包含文件如下】【夹具工艺课程设计类】CAD图纸+word设计说明书.doc【需要咨询购买全套设计请加QQ97666224】.bat
Φ38孔定位轴.dwg
夹具体.dwg
工序卡.doc
工艺过程卡.doc
支架.dwg
机械制造技术基础课程设计.doc
装配图.dwg
设计说明书.doc
钻模板.dwg
目 录
一. 序言 .............................................. 1
二. 零件分析 ....................................... . 3
1. 零件的作用 ..........................................3
2. 零件的工艺分析 ................................. .....3
三. 选择坯 ..............................................4
1. 确定毛坯的成形方法 ............................. ....4
2. 铸件结构工艺性分析 ................................. 4
3. 铸造工艺方案的确定 ............................. ....4
4. 铸造工艺参数的确定 ............................. ....4
四. 工艺规程设计 ...................................... 5
1. 定位基准的选择 ................................. .....5
2. 工件表面加工方法的选 ........................... ....5
3. 制定工艺路线 ................................... .....6
4. 机械加工余量、工序尺寸及毛坯配尺寸的确定 ....... .....8
5. 确定切削用量及基本工时 ........................ .....11
五. 夹具设计 ......................................... .16
1. 确定设计方案 .................................... .....16
2. 机械加工工序卡片 .............................. .......18
六. 参考文献 ......................................... 19
七. 总结............................................... 20
一. 序言
机械制造工艺课程设计是在我们完成了全部基础课、技术基础课、大部分专业课以及参加了生产实习之后进行的。这是我们在进行毕业设计之前对所学各课程的一次深入的综合性的复习,也是一次理论联系实际的训练,因此,它在我们四年的大学生活中占有重要的地位。
通过本次课程设计,应该得到下述各方面的锻炼:
1) 能熟练运用机械制造工艺设计中的基本理论以及在生产实习中学到的实践知识,正确地解决一个零件在加工中的定位、夹紧以及工艺路线安排、工艺尺寸确定等问题,保证零件的加工质量。
2) 提高结构设计的能力。通过设计夹具的训练,应当获得根据被加工零件的加工要求,设计出高效、省力、经济合理而且能保证加工质量的夹具的能力。
3) 会使用手册及图表资料。掌握与本设计有关的各种资料的名称、出处、能够做到熟练运用。
就我个人而言,通过这次设计,基本上掌握了零件机械加工工艺规程的设计,机床专用夹具等工艺装备的设计等。并学会了使用和查阅各种设计资料、手册、和国家标准等。最重要的是综合运用所学理论知识,解决现代实际工艺设计问题,巩固和加深了所学到的东西。并在设计过程中,学到了很多课堂上没有学到的东西。
二. 零件分析
(一) 零件的作用
支架是机床上用于支撑轴的机构,支架以Φ22孔套在轴上。
本设计任务给定的零件转支架即传递运动并保持其他零件正确工作方式,和保持互相之间的正确位置。其对加工平面,平行度,加工孔,垂直度,等有一定的要求,由于零件比较复杂,不成规则,故加工过程中需要用到复杂的夹具。



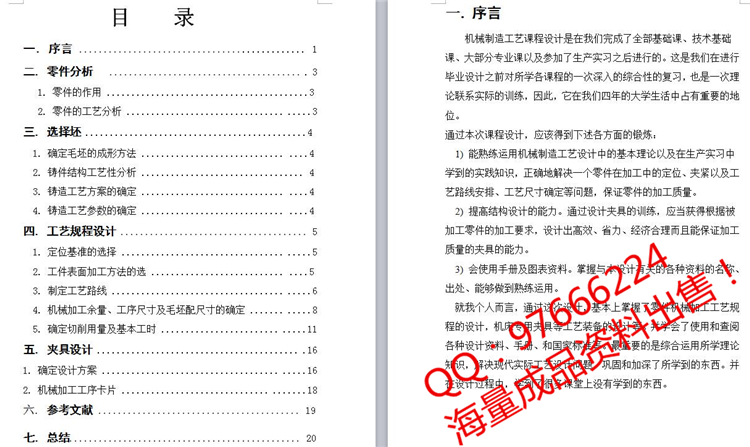
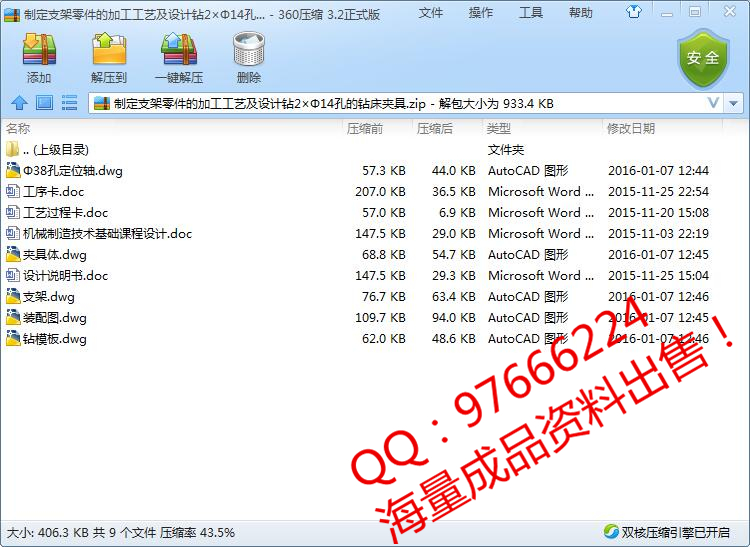
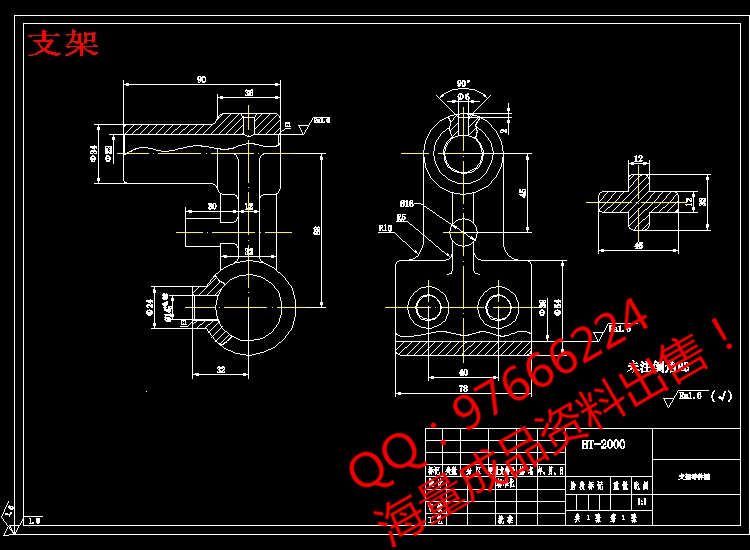
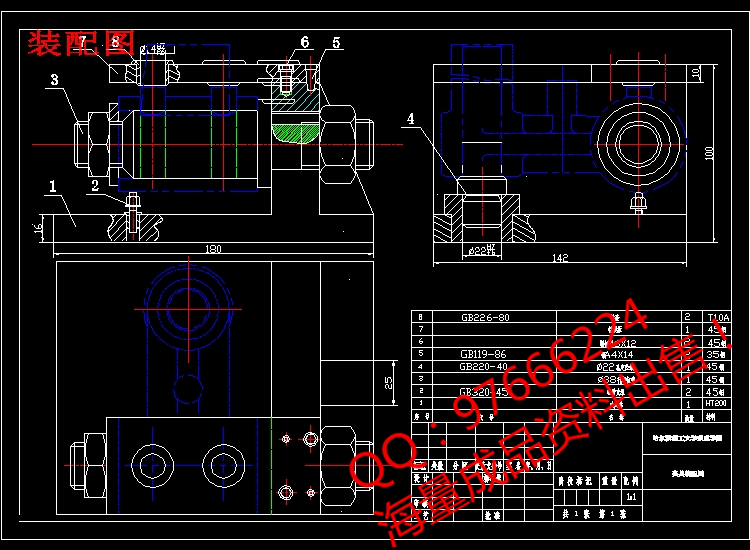