摘 要
全面阐述了数控车床的结构原理,设计特点,详细介绍了数控车床的结构设计及校核,并进行了分析。另外汇总了有关技术参数。
数控车床主轴箱设计,主要包括三方面的设计,即:根据设计题目所给定的机床用途、规格、主轴极限转速、转速数列公比或级数,确定其他有关运动参数,选定主轴各级转速值;通过分析比较,选择传动方案;拟定结构式或结构网,拟定转速图;确定齿轮齿数及带轮直径;绘制传动系统图。其次,根据机床类型和电动机功率,确定主轴及各传动件的计算转速,初定传动轴直径、齿轮模数,确定传动带型号及根数,摩擦片尺寸及数目;装配草图完成后要验算传动件(传动轴、主轴、齿轮、滚动轴承)的刚度、强度或寿命。最后,完成运动设计和动力设计后,要将主传动方案“结构化”,设计主轴变速箱装配图及零件图,侧重进行传动轴组件、主轴组件、变速机构、箱体、润滑与密封、传动轴及滑移齿轮零件的设计。
关键词:车床,主轴箱、变速系统、主轴组件
Abstract
Comprehensively elaborated numerical control lathe structure principle, design feature, introduced in detail the structure of NC lathe design and verification, and analysis. In addition to collect the related technology parameters.
CNC lathe headstock design, mainly includes three aspects of design, namely: according to the design theme of the given machine uses, specifications, spindle speed limit speed ratio, sequence or series, identify other related movement parameters selected levels, spindle speed value; through analysis and comparison, selection of transmission scheme; drawing structures or structural network, protocol speed diagram; determine the number of gear teeth and belt wheel diameter; drawing drive system diagram. Secondly, according to the type of machine and electric motor power, determining the spindle and the transmission of the calculation speed, initial drive shaft diameter, the gear modulus, confirm the transmission belt type and number, size and number of friction plate; Assembly Sketches after checking transmission ( transmission shaft, shaft, gear, rolling bearing stiffness, ) intensity or life. Finally, complete the kinematic design and dynamic design of the main drive system, " structured ", the design of the spindle gear box assembly drawing and parts drawing, focusing on transmission shaft assembly, spindle assembly, transmission mechanism, box, lubrication and seal, the transmission shaft and the slip gear parts design.
Key words: lathe, spindle box, transmission system, spindle assembly
目 录
摘 要 II
Abstract III
目 录 IV
第1章 绪论 10
1.1数控机床及其特点 10
1.2数控机床的工艺范围及加工精度 10
1.3 数控机床的经济分析 11
1.4 数控机床的发展趋向 12
第2章 数控机床总体方案的制订及比较 15
2.1 总体方案比较 15
2.2 数控车床方案确定 15
第3章 确定切削用量及选择刀具 16
3.1刀具选择 16
3.2切削用量确定 17
3.3切削三要素 17
3.4加工精度和表面粗糙度 17
3.5刀具材料 21
第4章 Φ320mm的数控车床主轴箱设计计算 21
4.1.主动参数参数的拟定 21
4.2 变速结构的设计 22
4.2.1 主变速方案拟定 22
4.2.2 变速结构式、结构网的选择 23
4.3带轮的设计 27
4.4 传动轴的直径估算 29
4.4.1 确定各轴转速 29
4.4.2传动轴直径的估算:确定各轴最小直径 30
4.4.3 键的选择 31
4.5传动轴的校核 31
4.5.1 传动轴的校核 32
4.5.2 键的校核 32
4.6 各变速组齿轮模数的确定和校核 33
4.6.1 齿轮模数的确定 33
4.6.2 齿宽的确定 37
4.6.3 齿轮结构的设计 38
4.7 带轮结构设计 39
4.8 片式摩擦离合器的选择和计算 40
4.9 齿轮校验 42
4.9.1 校核a变速组齿轮 42
4.9.2 校核b变速组齿轮 44
4.9.3 校核c变速组齿轮 45
4.10 轴承的选用与校核 46
4.10.1 各轴轴承的选用 46
4.10.2 各轴轴承的校核 46
4.11 主轴组件设计 48
4.12 主轴的基本尺寸确定 48
4.12.1 外径尺寸D 48
4.12.2 主轴孔径d 49
4.12.3 主轴悬伸量a 50
4.12.4 支撑跨距L 50
4.12.5 主轴最佳跨距的确定 51
4.13 主轴刚度验算 53
4.13.1 主轴前支撑转角的验算 54
4.13.2 主轴前端位移的验算 55
致 谢 59
参考文献 60
第1章 绪论
1.1数控机床及其特点
数控机床是一种高效能自动加工机床,是一种典型的机电一体化产品。与普通机床相比,数控机床具有如下一些优点:
数控机床的机械结构主要由传动系统、支承部件、分度台等部分组成。传动系统的作用是把运动和力由动力源传递给机床执行件,而且要保证传递过程中有良好的动态特性。传动系统在工作过程中,经常受到激振力和激振力矩的作用,使传动系统的轴组件产生弯曲和扭转振动,从而影响机床的工作性能。随着机床切削速度的提高和自动化方向的发展,传动系统的结构组成越来越简单,但对其机械结构性能的要求却越来越高,从而使传统的设计方法远远达不到要求,这样,各种设计理论的研究和使用就得到了迅猛的发展。
数控机床是高精度和高生产率的自动化机床,其加工过程中的动作顺序、运动部件的坐标位置及辅助功能,都是通过数字信息自动控制的,操作者在加工过程中无法干预,不能像在普通机床上加工零件那样,对机床本身的结构和装配的薄弱环节进行人为补偿,所以数控机床几乎在任何方面均要求比普通机床设计得更为完善,制造得更为精密。为满足高精度、高效率、高自动化程度的要求,数控机床的结构设计已形成自己的独立体系,在这一结构的完善过程中,数控机床出现了不少完全新颖的结构及元件。与普通机床相比,数控机床机械结构有许多特点。
1.2数控机床的工艺范围及加工精度
随着机械制造生产模式的演变,对机械制造装备提出了不同的要求.在50年代“刚性”生产模式下,通过提高效率,自动化程度,进行单一或少品种的大批量生产,以“规模经济”实现降低成本和提高质量的目的。从90年代开始,为了对世界生产进行快速响应,逐步实现社会制造资源的快速集成,要求机械制造装备的柔性化程度更高,采用拟实制造和快速成形制造技术。
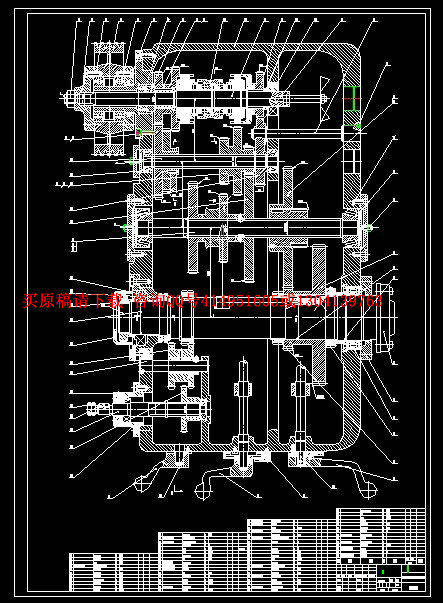
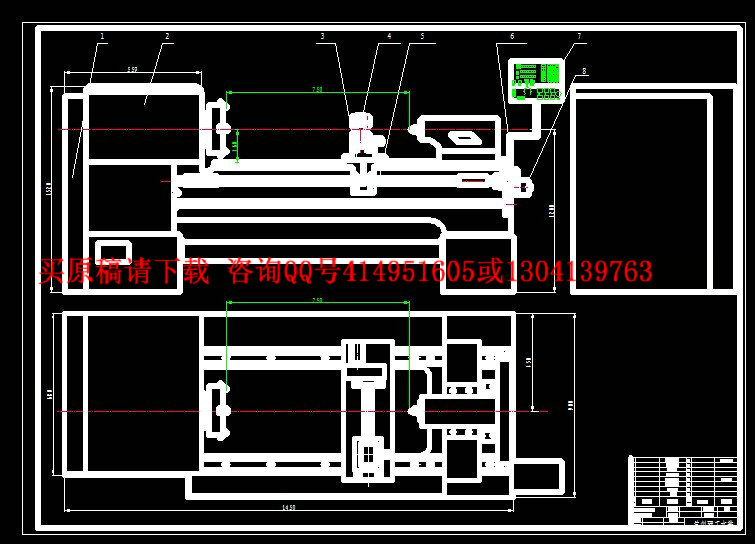


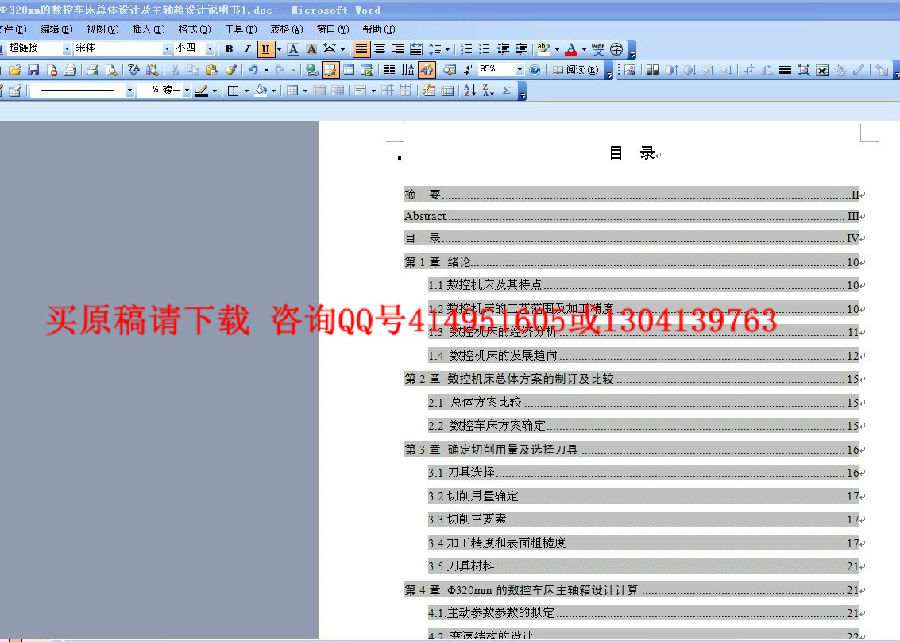


