摘 要
本文主要介绍了三向侧抽芯的固定式管架注塑模的结构设计,包括塑件工艺的分析,型腔排列的确定,分型面的确定,浇注系统、推出机构和冷却系统的设计,模架的选择,注塑机的选用,以及最重要的成型零部件的设计,侧向抽芯的设计等。根据塑件结构的复杂程度,同时考虑生产效率和批量的要求,采用一模两腔、侧浇口形式的单分型面注射模结构以及斜导柱侧抽机构。在此基础上,借助CAD/CAE技术,利用有限元分析软件完成注射成型模拟,以分析结果辅助该塑件一模多腔的浇注系统设计;借助UG三维软件对整套模具进行模拟装配。
关键词:斜导柱侧抽芯;注射成型;模具设计;CAD/CAE
ABSTRACT
This paper describes a fixed direction core drawn tube frame injection mold structure design, including the analysis of the process of plastic parts, cavity arranged to determine, the determination of the parting surface, gating system, the introduction of agencies and cooling system design,formwork selection, the selection of the injection molding machine, and most importantly, molded parts of the design, the side core design.According to the complexity of the structure of the plastic parts, taking into account the requirements of the production efficiency and volume, the use of a mold cavity, the side gate in the form of a single parting surface injection mold structure and Bevel Pillar side of the pumping mechanism. On this basis, with the help of CAD / CAE technology, complete injection molding simulation using finite element analysis software to analyze the results assisted the plastic parts of a multi-cavity mold gating system design; With UG three-dimensional software to simulate the entire mold assembly.
Key Words:Bevel Pillar side core;Injection molding;Mold design;CAD/CAE
目 录
1 引 言 1
1.1 概述 1
2 塑件的工艺分析 2
2.1 塑件材料性能分析 材料:PVC-U 2
2.2 塑件结构特征及用途分析 2
2.3 综合分析塑件结构 3
2.4 塑件的Moldflow分析 3
3 模具总体结构设计 6
3.1 确定型腔数目以及排列形式 6
3.2 确定分型面 6
3.3 确定浇注系统结构 8
3.3.1 确定最佳浇口形式及浇口位置、数量 8
3.3.2 流道布置 8
3.4 确定推出机构 9
3.4.1 脱模推出机构的设计原则 9
3.4.2 塑件推出的基本方式 9
3.5 确定导向机构 9
3.6 确定温度调节系统 10
3.6.1加热系统 10
3.6.2冷却系统 10
3.7 确定排气系统 11
3.8 确定模具支撑零件结构 11
4 模具零件结构尺寸设计 12
4.1 初选设备 12
4.1.1 计算塑件体积和重量 12
4.1.2 根据容量初选注射机 12
4.1.3 根据容量初选注射机 12
4.1.4注射机主要参数 12
4.1.5 校核注射机的有关参数 13
4.2 设计浇注系统 13
4.2.1 主流道设计 13
4.2.2 设计计算分流道尺寸 13
4.2.3 设计计算浇口尺寸 14
4.3 设计推出机构 14
4.3.1 推杆推出机构 14
4.3.2 确定推杆位置、形状、尺寸及数量 14
4.3.3 推杆安装、固定及配合 14
4.3.4 推出机构复位方式的确定 14
4.4 动、定模导向机构设计 14
4.5 成型零件工作尺寸的计算 15
4.6 侧向分型抽芯机构的设计 16
4.6.1 抽芯距与抽拔力的计算 16
4.6.2 斜导柱设计 17
4.6.3 侧滑块与导滑槽设计 18
4.6.4 楔紧块的设计 18
4.7 模架的确定和标准件的选用 18
5 注塑机的校核 21
5.1 注射容量的校核 21
5.2 锁模力校核及注射压力校核 21
5.3 成型面积的校核计算 21
5.4 注射压力的校核计算 21
5.5 模高的校核 22
5.6 模具最大尺寸的校核 22
5.7 开模行程的校核 22
结 论 23
致 谢 24
参考文献 25
1 引 言
1.1 概述
塑料是20世纪才发展起来的新材料,目前世界上塑料的体积产量已经赶上和超过了钢材,成为当前人类使用的一大类材料。我国的塑料工业正在飞速发展,塑料制品的应用已深入到国民经济的各个部门。塑料制品的普及应用事毕要求塑料模具得到快速发展。
近年来,我国塑料模具已得到快速发展,主要有如下成果:大型塑料模具已能生产单套重量达到50t 以上的注塑模,精密塑料模具的精度已达到2um,制件精度很高的小模数齿轮模具及达到高光学要求的车灯模具等也已能生产,多腔塑料模具已能生产一模7800 腔的塑封模;高速模具方面已能生产挤出速度达6m/min 以上的高速塑料异型材挤出模具及主型材双腔共挤、双色共挤、软硬共挤、后共挤、再生料共挤出和低发泡钢塑共挤等各种模具。从生产手段上, 模具企业设备数控化率已有较大提高, CAD/CAE/CAM技术的应用面已大为扩展,高速加工及RP/RT 等先进技术的采用已越来越多, 模具标准件使用覆盖率及模具商品化率都已有较大幅度的提高, 热流道模具的比例也有较大提高,内热式或外热式热流道装置得以采用,少数单位采用了具有世界先进水平的高难度针阀式热流道模具,完全消除了制件的浇口痕迹。气体辅助注射技术已成功得到应用。
同时,塑料模具对设计人员的先进设计思维,创新意识的培养也越来越重要,所以掌握叫多的加工技术以及加工工艺是非常必要的。塑料模具的毕业设计在其中发挥了重要的作用,让作为学习塑料模具的学生得到了实践,体会到设计塑料模具的过程,也更加巩固了我们的理论基础与专业知识。了解模具行业,了解塑料模具产品从设计到生产的详细过程。
虽然,塑料模具在国内发展较为迅速,但由于我国模具行业本身起步较晚,相比国外发达国家的模具设计制造水平,我国还存在很大问题,比如说发展不平衡, 产品总体水平较低。工艺装备落后, 组织协调能力差。大多数企业开发能力弱, 创新能力明显不足。供需矛盾一时还难以解决。体制和人才问题的解决尚待时日。
为此,学习、研究塑料模具有其实在意义。通过本次毕业设计,对塑料模具相关知识进行进一步的巩固和学习。通过分析塑料分型面、浇口位置,推件板推出机构等一系列问题,对模具结构进行设计,并结合相关软件的应用,实现了优化模具设计。
2 塑件的工艺分析
2.1 塑件材料性能分析 材料:PVC-U
PVC塑料一般可分为硬质与软质两大类。硬制品中可不加增塑剂,有时加入冲击改性剂以改善其韧性,软制品需加入大量增塑剂。两者均加着色剂、稳定剂、润滑剂等塑料助剂。 结合本次研究的塑件,应选用硬质PVC(PVC-U)。由于塑件是大批量生产,塑件结构带有侧抽芯,所以选择注射成型。

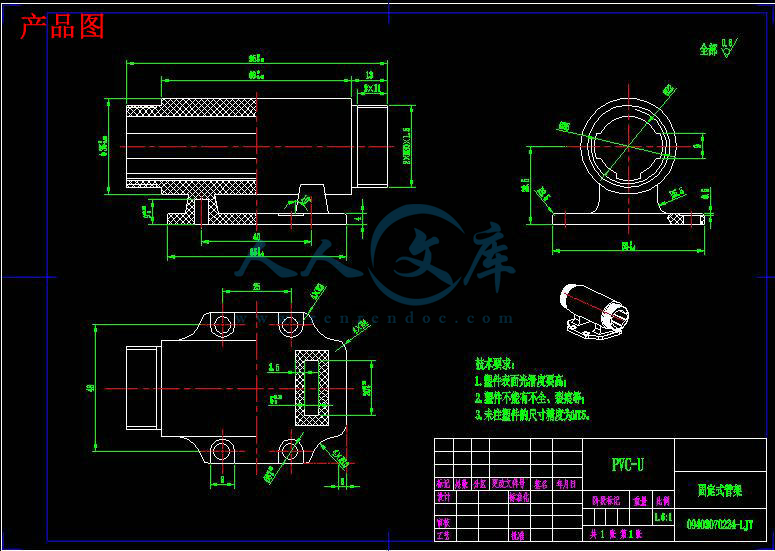








