资源目录
压缩包内文档预览:(预览前20页/共42页)
编号:6041382
类型:共享资源
大小:554.33KB
格式:ZIP
上传时间:2017-10-29
上传人:小***
认证信息
个人认证
林**(实名认证)
福建
IP属地:福建
50
积分
- 关 键 词:
-
垫片
工序
模具设计
- 资源描述:
-
!【包含文件如下】【冲压模具设计类】CAD图纸+word设计说明书.doc【需要咨询购买全套设计请企鹅97666224】.bat
A1装配图.dwg
凸凹模固定板,上垫板4.dwg
凸模5.dwg
凸模,打杆,推板,卸料橡胶,推杆3.dwg
卸料板1.dwg
模座.dwg
落料凹模6.dwg
设计说明书.doc
顶件块7.dwg
目 录
1 绪论 1
1.1 冲压的概念、特点及应用 1
1.2 冲压的基本工序及模具 2
1.3 冲压技术的现状及发展方向 3
1.3.1 冲压成形理论及冲压工艺方面 3
1.3.2 冲模是实现冲压生产的基本条件 4
1.3.3 冲压设备和冲压生产自动化方面 5
1.3.4 冲压标准化及专业化生产方面 6
1.4 设计要求 7
2 冲裁工艺设计 8
2.1 冲裁件的工艺分析 8
2.1.1 材料特性分析 8
2.1.2 冲裁件的结构工艺性分析 8
2.2 冲压工艺方案的确定 9
3 排样设计及材料利用率计算 11
3.1 排样方案的确定 11
3.2 搭边的选取 11
3.3 送料步距、条料宽度及导料销与条料间距计算 12
3.4 材料利用率的计算 13
4 冲裁工艺计算 14
4.1 冲裁力和压力中心的计算 14
4.1.1 冲裁力的计算 14
4.1.2 卸料力、推料力和顶件力的计算 15
4.1.3 压力中心的计算 16
4.1.4压力机的选择 17
4.1.5 曲柄压力机的主要技术参数 18
4.1.6曲柄压力机的选用 19
4.2 凸凹模刃口尺寸的计算 19
4.2.1 落料刃口尺寸的计算 21
4.2.2 冲孔刃口尺寸计算 22
5 模具主要零部件结构和设计 24
5.1 卸料装置 24
5.1.1 橡胶的选用 25
5.2 出件装置 28
5.3 定位零件 28
5.4 凹模的设计 29
5.5 凸凹模的设计 31
5.6 凸模的设计 31
5.7 模架 32
5.7.1 模板 32
5.7.2 导向零件 33
5.8 联接与固定零件 34
5.8.1 模柄 34
5.8.2 凸模固定板与垫板 34
5.8.3 螺纹紧固件 34
5.8.4 圆柱销 35
6 确定装配基准 37
7 总结 38
参考文献 39
1 绪论
1.1 冲压的概念、特点及应用
冲压是利用安装在冲压设备(主要是压力机)上的模具对材料施加压力,使其产生分离或塑性变形,从而获得所需零件(俗称冲压或冲压件)的一种压力加工方法。冲压通常是在常温下对材料进行冷变形加工,且主要采用板料来加工成所需零件,所以也叫冷冲压或板料冲压。冲压是材料压力加工或塑性加工的主要方法之一,隶属于材料成型工程术。

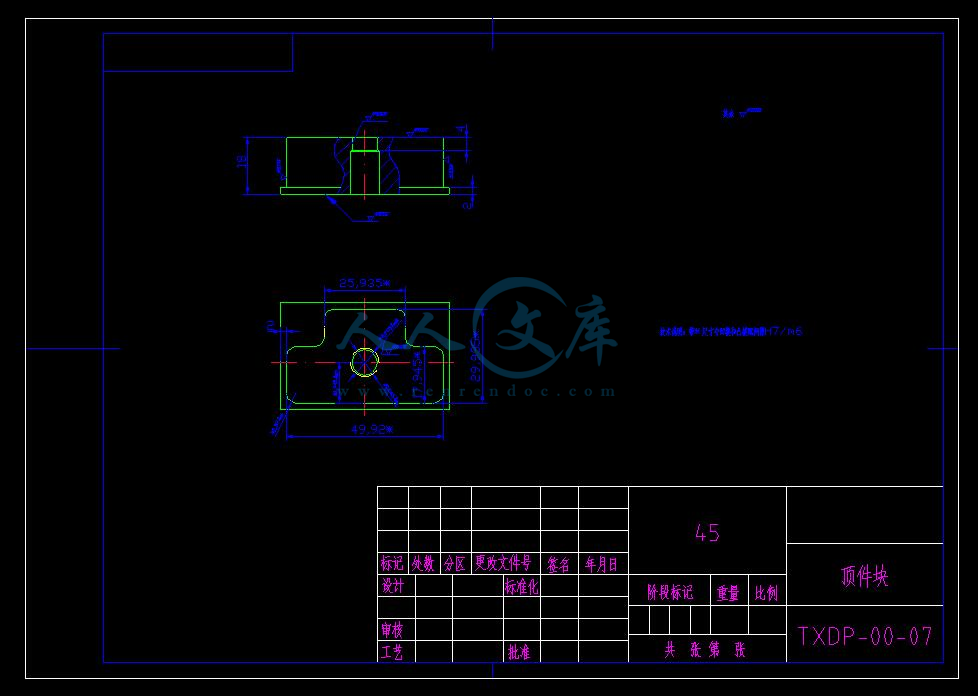





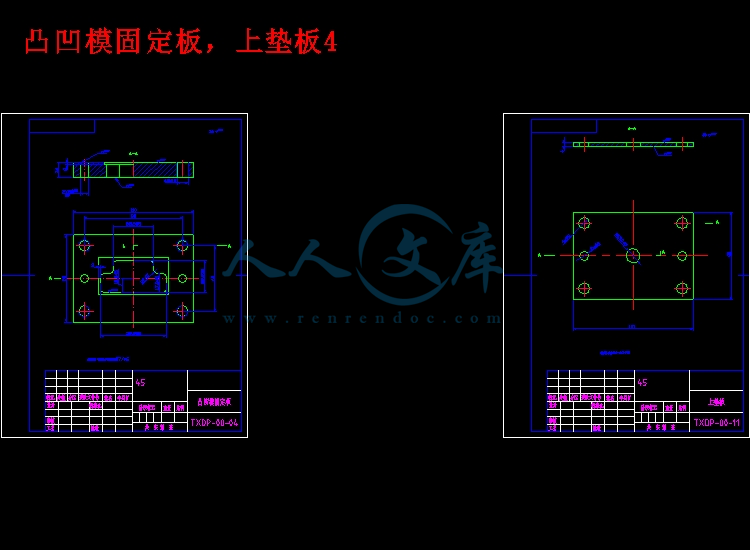



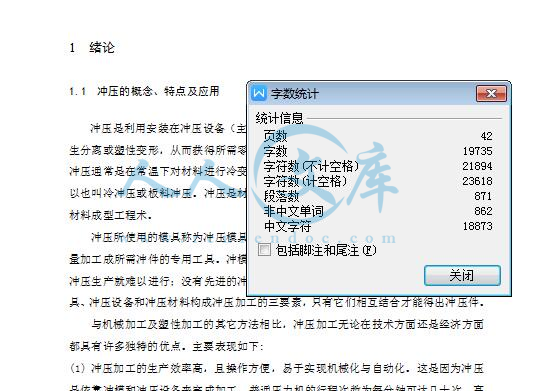
- 内容简介:
-
目 录1 绪论 .11.1 冲压的概念、特点及应用 .11.2 冲压的基本工序及模具 .21.3 冲压技术的现状及发展方向 .31.3.1 冲压成形理论及冲压工艺方面 .31.3.2 冲模是实现冲压生产的基本条件 .41.3.3 冲压设备和冲压生产自动化方面 .51.3.4 冲压标准化及专业化生产方面 .61.4 设计要求 .72 冲裁工艺设计 .82.1 冲裁件的工艺分析 .82.1.1 材料特性分析 .82.1.2 冲裁件的结构工艺性分析 .82.2 冲压工艺方案的确定 .93 排样设计及材料利用率计算 .113.1 排样方案的确定 .113.2 搭边的选取 .113.3 送料步距、条料宽度及导料销与条料间距计算 .123.4 材料利用率的计算 .134 冲裁工艺计算 .144.1 冲裁力和压力中心的计算 .144.1.1 冲裁力的计算 .144.1.2 卸料力、推料力和顶件力的计算 .154.1.3 压力中心的计算 .164.1.4 压力机的选择 .174.1.5 曲柄压力机的主要技术参数 .184.1.6 曲柄压力机的选用 .19 4.2 凸凹模刃口尺寸的计算 .194.2.1 落料刃口尺寸的计算 .214.2.2 冲孔刃口尺寸计算 .225 模具主要零部件结构和设计 .245.1 卸料装置 .245.1.1 橡胶的选用 .255.2 出件装置 .285.3 定位零件 .285.4 凹模的设计 .295.5 凸凹模的设计 .315.6 凸模的设计 .315.7 模架 .325.7.1 模板 .325.7.2 导向零件 .335.8 联接与固定零件 .345.8.1 模柄 .345.8.2 凸模固定板与垫板 .345.8.3 螺纹紧固件 .345.8.4 圆柱销 .356 确定装配基准 .377 总结 .38参考文献 .39 11 绪论1.1 冲压的概念、特点及应用冲压是利用安装在冲压设备(主要是压力机)上的模具对材料施加压力,使其产生分离或塑性变形,从而获得所需零件(俗称冲压或冲压件)的一种压力加工方法。冲压通常是在常温下对材料进行冷变形加工,且主要采用板料来加工成所需零件,所以也叫冷冲压或板料冲压。冲压是材料压力加工或塑性加工的主要方法之一,隶属于材料成型工程术。冲压所使用的模具称为冲压模具,简称冲模。冲模是将材料(金属或非金属)批量加工成所需冲件的专用工具。冲模在冲压中至关重要,没有符合要求的冲模,批量冲压生产就难以进行;没有先进的冲模,先进的冲压工艺就无法实现。冲压工艺与模具、冲压设备和冲压材料构成冲压加工的三要素,只有它们相互结合才能得出冲压件。与机械加工及塑性加工的其它方法相比,冲压加工无论在技术方面还是经济方面都具有许多独特的优点。主要表现如下:(1) 冲压加工的生产效率高,且操作方便,易于实现机械化与自动化。这是因为冲压是依靠冲模和冲压设备来完成加工,普通压力机的行程次数为每分钟可达几十次,高速压力要每分钟可达数百次甚至千次以上,而且每次冲压行程就可能得到一个冲件。(2)冲压时由于模具保证了冲压件的尺寸与形状精度,且一般不破坏冲压件的表面质量,而模具的寿命一般较长,所以冲压的质量稳定,互换性好,具有“一模一样”的特征。(3)冲压可加工出尺寸范围较大、形状较复杂的零件,如小到钟表的秒表,大到汽车纵梁、覆盖件等,加上冲压时材料的冷变形硬化效应,冲压的强度和刚度均较高。(4)冲压一般没有切屑碎料生成,材料的消耗较少,且不需其它加热设备,因而是一种省料,节能的加工方法,冲压件的成本较低。但是,冲压加工所使用的模具一般具有专用性,有时一个复杂零件需要数套模 2具才能加工成形,且模具 制造的精度高,技术要求高,是技术密集形产品。所以,只有在冲压件生产批量较大的情况下,冲压加工的优点才能充分体现,从而获得较好的经济效益。冲压地、在现代工业生产中,尤其是大批量生产中应用十分广泛。相当多的工业部门越来越多地采用冲压法加工产品零部件,如汽车、农机、仪器、仪表、电子、航空、航天、家电及轻工等行业。在这些工业部门中,冲压件所占的比重都相当的大,少则 60%以上,多则 90%以上。不少过去用锻造=铸造和切削加工方法制造的零件,现在大多数也被质量轻、刚度好的冲压件所代替。因此可以说,如果生产中不谅采用冲压工艺,许多工业部门要提高生产效率和产品质量、降低生产成本、快速进行产品更新换代等都是难以实现的。1.2 冲压的基本工序及模具由于冲压加工的零件种类繁多,各类零件的形状、尺寸和精度要求又各不相同,因而生产中采用的冲压工艺方法也是多种多样的。概括起来,可分为分离工序和成形工序两大类;分离工序是指使坯料沿一定的轮廓线分离而获得一定形状、尺寸和断面质量的冲压(俗称冲裁件)的工序;成形工序是指使坯料在不破裂的条件下产生塑性变形而获得一定形状和尺寸的冲压件的工序。上述两类工序,按基本变形方式不同又可分为冲裁、弯曲、拉深和成形四种基本工序,每种基本工序还包含有多种单一工序。在实际生产中,当冲压件的生产批量较大、尺寸较少而公差要求较小时,若用分散的单一工序来冲压是不经济甚至难于达到要求。这时在工艺上多采用集中的方案,即把两种或两种以上的单一工序集中在一副模具内完成,称为组合的方法不同,又可将其分为复合-级进和复合-级进三种组合方式。复合冲压在压力机的一次工作行程中,在模具的同一工位上同时完成两种或两种以上不同单一工序的一种组合方法式。级进冲压在压力机上的一次工作行程中,按照一定的顺序在同一模具的不同工位上完面两种或两种以上不同单一工序的一种组合方式。复合-级进在一副冲模上包含复合和级进两种方式的组合工序。冲模的结构类型也很多。通常按工序性质可分为冲裁模、弯曲模、拉深模和成形 3模等;按工序的组合方式可分为单工序模、复合模和级进模等。但不论何种类型的冲模,都可看成是由上模和下模两部分组成,上模被固定在压力机工作台或垫板上,是冲模的固定部分。工作时,坯料在下模面上通过定位零件定位,压力机滑块带动上模下压,在模具工作零件(即凸模、凹模)的作用下坯料便产生分离或塑性变形,从而获得所需形状与尺寸的冲件。上模回升时,模具的卸料与出件装置将冲件或废料从凸、凹模上卸下或推、顶出来,以便进行下一次冲压循环。1.3 冲压技术的现状及发展方向随着科学技术的不断进步和工业生产的迅速发展,许多新技术、新工艺、新设备、新材料不断涌现,因而促进了冲压技术的不断革新和发展。其主要表现和发展方向如下。1.3.1 冲压成形理论及冲压工艺方面冲压成形理论的研究是提高冲压技术的基础。目前,国内外对冲压成形理论的研究非常重视,在材料冲压性能研究、冲压成形过程应力应变分析、板料变形规律研究及坯料与模具之间的相互作用研究等方面均取得了较大的进展。特别是随着计算机技术的飞跃发展和塑性变形理论的进一步完善,近年来国内外已开始应用塑性成形过程的计算机模拟技术,即利用有限元(FEM)等有值分析方法模拟金属的塑性成形过程,根据分析结果,设计人员可预测某一工艺方案成形的可行性及可能出现的质量问题,并通过在计算机上选择修改相关参数,可实现工艺及模具的优化设计。这样既节省了昂贵的试模费用,也缩短了制模具周期。研究推广能提高生产率及产品质量、降低成本和扩大冲压工艺应用范围的各种压新工艺,也是冲压技术的发展方向之一。目前,国内外相继涌现出精密冲压工艺、软模成形工艺、高能高速成形工艺及无模多点成形工艺等精密、高效、经济的冲压新工艺。其中,精密冲裁是提高冲裁件质量的有效方法,它扩大了冲压加工范围,目前精密冲裁加工零件的厚度可达 25mm,精度可达 IT1617 级;用液体、橡胶、聚氨酯等作柔性凸模或凹模的软模成形工艺,能加工出用普通加工方法难以加工的材料和复杂形状的零件,在特定生产条件下具有明显的经济效果;采用爆炸等高能效成形方法对 4于加工各种尺寸在、形状复杂、批量小、强度高和精度要求较高的板料零件,具有很重要的实用意义;利用金属材料的超塑性进行超塑成形,可以用一次成形代替多道普通的冲压成形工序,这对于加工形状复杂和大型板料零件具有突出的优越性;无模多点成形工序是用高度可调的凸模群体代替传统模具进行板料曲面成形的一种先进技术,我国已自主设计制造了具有国际领先水平的无模多点成形设备,解决了多点压机成形法,从而可随意改变变形路径与受力状态,提高了材料的成形极限,同时利用反复成形技术可消除材料内残余应力,实现无回弹成形。无模多点成形系统以 CAD/CAM/CAE技术为主要手段,能快速经济地实现三维曲面的自动化成形。1.3.2 冲模是实现冲压生产的基本条件在冲模的设计制造上,目前正朝着以下两方面发展:一方面,为了适应高速、自动、精密、安全等大批量现代生产的需要,冲模正向高效率、高精度、高寿命及多工位、多功能方向发展,与此相比适应的新型模具材料及其热处理技术,各种高效、精密、数控自动化的模具加工机床和检测设备以及模具 CAD/CAM 技术也在迅速发展;另一方面,为了适应产品更新换代和试制或小批量生产的需要,锌基合金冲模、聚氨酯橡胶冲模、薄板冲模、钢带冲模、组合冲模等各种简易冲模及其制造技术也得到了迅速发展。精密、高效的多工位及多功能级进模和大型复杂的汽车覆盖件冲模代表了现代冲模的技术水平。目前,50 个工位以上的级进模进距精度可达到 2 微米,多功能级进模不仅可以完成冲压全过程,还可完成焊接、装配等工序。我国已能自行设计制造出达到国际水平的精度达 25 微米,进距精度 23 微米,总寿命达 1 亿次。我国主要汽车模具企业,已能生产成套轿车覆盖件模具,在设计制造方法、手段方面已基本达到了国际水平,但在制造方法手段方面已基本达到了国际水平,模具结构、功能方面也接近国际水平,但在制造质量、精度、制造周期和成本方面与国外相比还存在一定差距。模具制造技术现代化是模具工业发展的基础。计算机技术、信息技术、自动化技术等先进技术正在不断向传统制造技术渗透、交叉、融合形成了现代模具制造技术。其中高速铣削加工、电火花铣削加工、慢走丝切割加工、精密磨削及抛光技术、数控测量等代表了现代冲模制造的技术水平。高速铣削加工不但具有加工速度高以及良好 5的加工精度和表面质量(主轴转速一般为 1500040000r/min),加工精度一般可达 10微米,最好的表面粗糙度 Ra1 微米) ,而且与传统切削加工相比具有温升低(工件只升高 3 摄氏度) 、切削力小,因而可加工热敏材料和刚性差的零件,合理选择刀具和切削用量还可实现硬材料(60HRC)加工;电火花铣削加工(又称电火花创成加工)是以高速旋转的简单管状电极作三维或二维轮廓加工(像数控铣一样) ,因此不再需要制造昂贵的成形电极,如日本三菱公司生产的 EDSCAN8E 电火花铣削加工机床,配置有电极损耗自动补偿系统、CAD/CAM 集成系统、在线自动测量系统和动态仿真系统,体现了当今电火花加工机床的技术水平;慢走丝线切割技术的发展水平已相当高,功能也相当完善,自动化程度已达到无人看管运行的程度,目前切割速度已达到 300mm/min,加工精度可达1.5 微米,表面粗糙度达 Ra=010.2 微米;精度磨削及抛光已2开始使用数控成形磨床、数控光学曲线磨床、数控连续轨迹坐标磨床及自动抛光等先进设备和技术;模具加工过程中的检测技术也取得了很大的发展,现在三坐标测量机除了能高精度地测量复杂曲面的数据外,其良好的温度补偿装置、可靠的抗振保护能力、严密的除尘措施及简单操作步骤,使得现场自动化检测成为可能。此外,激光快速成形技术(RPM)与树脂浇注技术在快速经济制模技术中得到了成功的应用。利用 RPM技术快速成形三维原型后,通过陶瓷精铸、电弧涂喷、消失模、熔模等技术可快速制造各种成形模。如清华大学开发研制的“M-RPMS-型多功能快速原型制造系统”是我国自主知识产权的世界惟一拥有两种快速成形工艺(分层实体制造 SSM 和熔融挤压成形 MEM)的系统,它基于“模块化技术集成”之概念而设计和制造,具有较好的价格性能比。一汽模具制造公司在以 CAD/CAM 加工的主模型为基础,采用瑞士汽巴精化的高强度树脂浇注成形的树脂冲模应用在国产轿车试制和小批量生产开辟了新的途径。1.3.3 冲压设备和冲压生产自动化方面性能良好的冲压设备是提高冲压生产技术水平的基本条件,高精度、高寿命、高效率的冲模需要高精度、高自动化的冲压设备相匹配。为了满足大批量高速生产的需要,目前冲压设备也由单工位、单功能、低速压力机朝着多工位、多功能、高速和数控方向发展,加之机械乃至机器人的大量使用,使冲压生产效率得到大幅度提高,各 6式各样的冲压自动线和高速自动压力机纷纷投入使用。如在数控四边折弯机中送入板料毛坯后,在计算机程序控制下便可依次完成四边弯曲,从而大幅度提高精度和生产率;在高速自动压力机上冲压电机定转子冲片时,一分钟可冲几百片,并能自动叠成定、转子铁芯,生产效率比普通压力机提高几十倍,材料利用率高达 97%;公称压力为 250KN 的高速压力机的滑块行程次数已达 2000 次/min 以上。在多功能压力机方面,日本田公司生产的 2000KN“冲压中心”采用 CNC 控制,只需 5min 时间就可完成自动换模、换料和调整工艺参数等工作;美国惠特尼公司生产的 CNC 金属板材加工中心,在相同的时间内,加工冲压件的数量为普通压力机的 410 倍,并能进行冲孔、分段冲裁、弯曲和拉深等多种作业。近年来,为了适应市场的激烈竞争,对产品质量的要求越来越高,且其更新换代的周期大为缩短。冲压生产为适应这一新的要求,开发了多种适合不同批量生产的工艺、设备和模具。其中,无需设计专用模具、性能先进的转塔数控多工位压力机、激光切割和成形机、CNC 万能折弯机等新设备已投入使用。特别是近几年来在国外已经发展起来、国内亦开始使用的冲压柔性制造单元(FMC)和冲压柔性制造系统(FMS)代表了冲压生产新的发展趋势。FMS 系统以数控冲压设备为主体,包括板料、模具、冲压件分类存放系统、自动上料与下料系统,生产过程完全由计算机控制,车间实现24 小时无人控制生产。同时,根据不同使用要求,可以完成各种冲压工序,甚至焊接、装配等工序,更换新产品方便迅速,冲压件精度也高。1.3.4 冲压标准化及专业化生产方面模具的标准化及专业化生产,已得到模具行业和广泛重视。因为冲模属单件小批量生产,冲模零件既具的一定的复杂性和精密性,又具有一定的结构典型性。因此,只有实现了冲模的标准化,才能使冲模和冲模零件的生产实现专业化、商品化,从而降低模具的成本,提高模具的质量和缩短制造周期。目前,国外先进工业国家模具标准化生产程度已达 70%80%,模具厂只需设计制造工作零件,大部分模具零件均从标准件厂购买,使生产率大幅度提高。模具制造厂专业化程度越不定期越高,分工越来越细,如目前有模架厂、顶杆厂、热处理厂等,甚至某些模具厂仅专业化制造某类产品的冲裁模或弯曲模,这样更有利于制造水平的提高和制造周期的缩短。我国冲模标准化与专业化生产近年来也有较大发展,除反映在标准件专业化生产厂家有较多 7增加外,标准件品种也有扩展,精度亦有提高。但总体情况还满足不了模具工业发展的要求,主要体现在标准化程度还不高(一般在 40%以下) ,标准件的品种和规格较少,大多数标准件厂家未形成规模化生产,标准件质量也还存在较多问题。另外,标准件生产的销售、供货、服务等都还有待于进一步提高。1.4 设计要求制件如图 1-1 所示,材料为 08F,材料厚度为 0.8mm,制件尺寸精度按图纸要求,大批量生产。图 1-1 82 冲裁工艺设计2.1 冲裁件的工艺分析冲裁件的的工艺性是指冲裁件对冲压工艺的适应性,即冲裁件在冲压加工中的难易程度。冲裁件的工艺是否合理,对冲裁件的质量、模具寿命和生产率有很大的影响,一般情况下对冲压件工艺性影响最大的是几何尺寸和精度要求。2.1.1 材料特性分析冲压所用的材料,不仅要满足工件的技术要求,同时也必须满足冲压工艺要求:(1)应有良好的塑性。在成形工序中,塑性好的材料,其容许的变形程度大。在分离工序中,良好的塑性才能获得理想的断面质量。(2)应具有光洁平整且无缺陷损伤的表面状态。表面状态好的材料,加工时不易破裂,也不容易擦伤模具,制成的零件也有良好的表面状态。(3)材料的厚度公差应符合国家标准。因为一定的模具间隙,适应于一定厚度的材料。本零件采用 08F 钢,08F 钢属于优质碳素结构钢,其中含 C 量为 0.05%0.11%,抗拉强度 ,屈服强度 。其韧性好,强度适中吻合加工的要Mpa295bMpas175求。2.1.2 冲裁件的结构工艺性分析(1)冲裁件的形状应尽量简单,最好是规则的几何形状或由规则的几何形状所组成。同时应避免冲裁件上过长的悬臂与凹槽,它们的宽度要大于料厚的(1.5 到 2)倍,该零件外形上接近于矩形,没有悬臂和凹槽,冲裁件的最小尺寸为 8mm 大于 1.5t。(2)一般情况下,冲裁件的外形和内孔应避免尖角,采用 的圆角。此零件设0.5Rt有 R3 的倒角。(3)冲孔时,因受凸模强度限制,孔的尺寸不宜过小。用一般冲模冲圆孔时,对硬 9钢,直径 ;对软钢和黄铜, ;对铝及锌, 。冲方孔时,对硬钢,1.3dt1.0dt0.8dt边长 ;对软钢及黄铜, ;对铝和锌, 。由于 08F 钢属于软钢。0a7a5a而 。所以该条件也满足。8.(4)孔与孔之间的距离或孔与零件边缘之间的距离 a,因受模具强度和冲裁件质量的限制,其值不能过小,一般应取 a.2t(3-4mm),如使用级进模,而且对零件精度要求不高时,a 可适当减小,但也不宜于小于板厚。孔与零件边缘的最短距离为11.5mm。(5)冲裁件的精度一般可达 IT10-IT12,高精度可达 IT8-IT10 级,冲孔比落料的精度约高一级。该零件没有标准公差,则对于非圆形件按国家标准非配合尺寸的公差数值 精度来处理,冲模则可按 精度制造。14IT1IT2.2 冲压工艺方案的确定该工件有两道加工工序:冲孔、落料。可以有以下三种方案:方案一:先落料后冲孔,采用简单模生产;方案二:落料和冲孔连续加工,采用级进模生产;方案三:落料和冲孔复合加工,采用复合模生产。三种方案比较见表 1-1表 1-1 三种方案的比较简单模 级进模 复合模冲裁件精度 较低 高 一般生产效率 低 较高 高生产批量 批量小或试制冲裁件 大批量 大批量模具复杂程度 简单 较复杂 复杂模具制造成本 较低 较高 高模具的结构特点 结构简单安装容易 结构较复杂制造麻烦 结构较复杂模具种类比 较项目 10模具的制造精度 较低 较高 高模具制造周期 较快 较长 长冲压设备能力 较小 中等 较大工作条件 一般 较好 好方案一虽然模具结构简单,尺寸较小,重量较轻,模具制造简单,成本低廉。模具依靠压力机导轨导向,模具的安装调整麻烦,很难保证上、下部分对正,从而难以保证凸、凹模之间的间隙均匀,冲裁件精度差,模具寿命低,操作也不安全,需要两套模具,生产率较低而且不适合大批量生产。方案二级进模是多工序冲模,在一副模具上能完成多道工序,使用级进模可以减少模具和设备数量,提高生产效率。级进模容易实现冲压生产自动化。但是,级进模比简单模结构复杂,制造麻烦,成本增加。级进模的条料的准确定位的问题不好解决。方案三复合模也是多工序冲模,在一副模具中一次送料定位可以同时完成几个工序。和级进模相比,冲裁件的内孔和外缘具有较高的位置精度,条料的定位精度要求较低,冲模轮廓尺寸较小,复合模适合于生产批量大、精度要求高的冲裁件,且零件的形位精度容易保证,条料的定位精度要求较低,生产效率较高。综上分析应该选择第三方案进行加工。 113 排样设计及材料利用率计算 3.1 排样方案的确定冲裁件在条料或板料上的布置方法叫排样。排样的合理与否直接关系到材料利用率的高低,而冲压件的成本中,材料费用一般占 60%以上,因此合理排样对提高材料利用率降低成本具有十分重要的意义。根据材料的合理利用情况,条料的排样方法可以分为三种:(一)有废料排样:沿工件全部外形冲裁,工件四周都留有搭边。可由搭边补偿误差,因而能保证冲裁件的精度和质量,冲模寿命也较高,但材料利用率低。(二)少废料排样:沿工件部分外形冲裁,局部有搭边和余料。因受剪裁条料质量和定位误差的影响,其冲件质量稍差就会影响模具的寿命,但材料利用率高,冲模结构简单。(三)无废料排样:工件由条料顺次切下,直接获得零件,无任何搭边。冲件的质量较差,模具寿命低,但材料利用率高。采用少、无废料排样,对节省材料有重要意义。同时,因冲切周边减小,可降低冲压力并简化冲模结构。但采用少、无废料排样也存在一些缺点,如工件所能达到的质量与精度都较差,同时模具寿命也较低。此外,少无废料排样中,工件的毛刺也不在同一方向。无论是有废料、少废料或无废料排样,其排样的型式均可分为直排、斜排、直对排、斜对排、混合排和多行排等。综上分析,根据零件的形状、尺寸、材料,选取有废料排样,采用直排的形式。3.2 搭边的选取排样时工件之间以及工件与条料侧边之间留下的余料叫搭边。搭边虽然形成废料,但在工艺上却有很大的作用。搭边的作用是补偿定位误差,保证冲出合格的零件。搭边还可以保证条料有一定的刚度,利于送进。 12搭边值要合理确定。搭边值过大,材料利用率低;搭边值过小,在冲裁中有可能被拉断,使零件产生毛刺,严重时会拉入凸模与凹模间隙之中,损坏模具刃口。搭边值的大小通常与材料的机械性能、工件的形状和尺寸、材料厚度以及送料和挡料方式等因素有关。硬材料的搭边值比软材料的搭边值可小一些;工件尺寸大或是有尖突的复杂形状时,搭边值取大些,厚材料的搭边值应取大些;用手工送料,有侧压装置,搭边值可取小些。目前搭边值的大小是由经验确定的。表 3-1 是常用以确定搭边值的参考数表。 表 3-1 搭边 a 和 a1的数值材料厚度tmm圆件及圆角 r2t 矩形件边长L50mm矩形边长 L50mm或圆角 r2t工件间a1沿边 a 工件间 a1 沿边 a 工件间 a1 沿边 a0.25 以下 1.8 2.0 2.2 2.5 2.8 3.00.250.50 1.2 1.5 1.8 2.0 2.2 2.50.50.8 1.0 1.2 1.5 1.8 1.8 2.00.81.2 0.8 1.0 1.2 1.5 1.5 1.8根据零件矩形形状最长边长为 50mm,厚度为 0.8mm,所以 a1=1.5mm,沿边a=1.8mm。3.3 送料步距、条料宽度及导料销与条料间距计算1. 送料步距:两次冲裁间板料在送料方向移动的距离 L,其值等于冲裁件相应部分的宽度加上工件间搭边值 a,即(3-1) maDL5.31.012. 条料宽度及导料销与条料间距的计算条料宽度的计算(3-2) 1.4).82()2( 00blB查得 .所以排样图如图 3-1:。m5.,.0 13图 3-13.4 材料利用率的计算查板材标准应选 900mm1000mm 的钢板,每个钢板可剪裁成 18 个条料(53.6mm900mm),每张条料可加工 27 个零件,则材料的利用率为(3-3) %6310902486%1BLnAn-一张板料上冲件的数量A-零件的实际面积B-板料的宽度L-板料的长度即每张板材的材料利用率为 63% 144 冲裁工艺计算4.1 冲裁力和压力中心的计算4.1.1 冲裁力的计算冲裁力是指冲裁时,材料对凸模的最大抵抗力,它是选择冲压设备和校核模具强度的重要依据。用平刃冲裁模冲裁时,其冲裁力的计算公式为(4-1) FkLt-冲裁力(N)-冲裁件的周长(mm)-板料的厚度(mm)t-材料的抗剪强度( 2)Nm-系数。K这一公式是对冲裁区的变形进行简化,认为是纯剪变形得到的。变形区的实际变形情况比较复杂,因此,采用系数 加以修正,一般可取 =1.3。KK抗剪强度 的数值,取决于材料的种类和状态,可取 。 0.8b为了计算方便,也可以用下式估算冲裁力:(4-2)bLFt式中: -材料的抗拉强度b经查机械设计手册得 08F 钢的抗拉强度 b=295MPa.由此可以得出:KNLb264.958.0124t落 dtFb 8.1冲.6.9冲落 154.1.2 卸料力、推料力和顶件力的计算冲模过程中,材料由于弹性变形和摩擦使带孔部分的板料紧箍在凸模上,而冲落部分的板料紧卡在凹模洞口内。为了继续下一步的冲裁工作,必须将箍在凸模上的板料卸下,将卡在凹模洞口的板料推出,从凸模上卸下紧箍着的板料叫卸料,所需的力叫卸料力;顺着冲裁方向将卡在凹模洞口内的板料推出叫推件,所需的力叫推件力;有时需要将卡在凹模洞口内的板料逆着冲裁方向顶出,这就叫顶件,顶件所需的力叫顶件力。影响卸料力、推件力和顶件力的因素有很多,主要有材料的机械性能、材料厚度、模具间隙、零件的形状和尺寸以及润滑条件等。要准确计算这些力是很难的,生产中常用以下经验公式进行计算:推件力 (4-1FnK3)顶件力 (4-24)卸料力 (4-3FK5)式中:n-同时卡在凹模洞口内的零件数-冲裁力(N)、 、 -推件力、顶件力和卸料力系数,其值见下表、1K23表 4-1 推件力系数、顶件力系数和卸料力系数料 厚 K1 K2 K3钢0.10.10.50.52.52.56.56.50.10.0630.0550.0450.0250.140.080.060.050.030.0650.0750.0450.0550.040.050.030.040.020.03铝、铝合金紫铜、黄铜0.030.070.030.090.0250.080.020.06 16注:卸料力系数 在冲多孔和轮廓复杂冲裁件时取上限。3K查表可有: , =0.14, =0.0751.023NF186.1冲 094.2落 KK.0753落总冲压力 总冲压力是各种冲压工艺的总和,由于本模具采用弹性卸料装置,总则: 59.481.2094186.2.4321 FF总在冲裁高强度材料或厚度大、周边长的工件时,所需冲裁力如果超过现有压力机吨位,就必须采取降低冲裁力。一般采用如下几种方法:(1)材料加热红肿。材料加热后抗剪强度可以大大降低,从而降低冲裁力。但材料加热后产生氧化皮,故此法一般只适用于厚板或工件表面质量及精度要求不高的零件。(2)在多凸模冲模中,将凸模作阶梯形布置,即将凸模刃口制成不同高度,使各凸模冲裁力的最大值不同时出现,这样就能降低总的冲裁力。(3)用斜刃口模具冲裁。用普通的平刃口模具冲裁时,其整个刃口平面都同时压入材料中,故在冲裁大型或厚板工件时,冲裁力往往很大,若将凸模刃口平面做成与其轴线倾斜一个角度,冲裁时刃口就不是全部同时切入,而是逐步冲切材料,这就等于减少了剪切断面积,因而能降低冲裁力。斜刃冲模虽然降低了冲裁力,但增加了模具制造和修磨的困难,刃口也容易磨损,故一般情况下尽量不用,只用于大型工件冲裁及厚板冲裁。4.1.3 压力中心的计算冲裁力合力的作用点称为冲模压力中心。为保证冲模正确平衡地工作,冲模压力中心必须通过模柄轴线而和压力机滑块的中心线相重合,以免滑块受偏心载荷,从而减少冲模和压力机导轨的不正常磨损,提高模具寿命,避免冲压事故。冲模压力中心的计算,是采用空间平行力系合力作用线的求解方法,即根据“合力对某轴之力矩等于各分力对同轴力矩之和”的力学原理求得。 17对于任何形状,不论单个图形(敞开或封闭的轮廓)或多个图形(如多凸模、复合模和级进模)冲裁,其计算方法相同。首先将组成图形的轮廓线划分为若干基本线段,分别计算其冲裁力 (对于多凸iF模,分别计算各凸模图形的冲裁力) ,这些即为分力,由各分力之和算出合力。然后,任意选定直角坐标系 ,确定各线段或各图形的重心坐标 ,按上述定理列式,XOY(,)ixy即可求出压力中心的坐标 。0()xy由于线段的长度或图形的轮廓周长与冲裁力成正比,所以可以用线段的长度或图形轮廓的周长 代替 ,这时压力中心坐标公式如下:iLiF(4-6)1210.niniLxxL(4-1210.niniLyLy7) 由此可算得 0x my 2.10814.32035.)18925( 所以压力中心为(0,10.22)4.1.4 压力机的选择冲压工作是在冲压设备上进行的,目前应用较多的有曲柄压力机、摩擦压力机和液压机。曲柄压力机可用于各类冲模,其中偏心机床尤其适用于导柱、导套不脱开的模具(如导板模) ,摩擦压力机和液压机主要用于校正模、压铸模等,同时也适用于挤压模。这里简单介绍一下生产中最普遍适用的压力机。 18曲柄压力机包括各种结构的偏心冲床和曲柄冲床,其基本工作机构都是曲柄连杆机构。偏心冲床也称开式曲柄压力机,启动后,电动机通过小齿轮和大齿轮及离合器将动力传给偏心轴,偏心轴在轴承中作回转运动。连杆把偏心轴的回转运动转变为滑块的直线运动,滑块在床身的导轨作上下往复运动。模具的上模固定于滑块上,模具的下模固定在工作台上。为了控制滑块的运动和位置设有离合器和制动器。离合器的作用是:电动机在飞轮不停的运转下,使曲柄机构开动或停止。工作时,主要踩下脚踏开关,离合器啮合,偏心轴转动,即可带动滑块作上下往复运动,进行冲压。制动器的动作与离合器的动作密切配合,在离合器脱开后,制动器同时将曲柄连杆机构停止在一定的位置上。床身是所有运动部分的支承体,并将压力机的全部机构联接成一个整体。4.1.5 曲柄压力机的主要技术参数曲柄压力机的主要技术参数是反映一台压力机工作能力、所能加工零件的尺寸范围以及有关生产率的指标,分述如下。(1)公称压力曲柄压力机的公称压力,是指曲柄旋转到下死点前某一特定角度(此角度称为公称压力角,约为 30 度)时,滑块所能容许的承受的最大作用力。它是反映压力机工作能力的重要指标,生产中不容许冲压力大于公称压力。(2)滑块行程滑块行程是指滑块从上死点到下死点所走的距离,它为曲柄半径的两倍。(3)闭合高度闭合高度又称装模高度,是指滑块在下死点位置时,滑块下表面到工作台垫板上表面的距离。当闭合高度调节装置将滑块调整到最上位置时,闭合高度达到最大值,称为最大闭合高度;当闭合高度调节装置将滑块调整到最下位置时,闭合高度达到最小值,称为最小闭合高度。 19(4)滑块行程次数滑块行程次数是指滑块每分钟从上死点到下死点,然后再回到上死点所往复的次数。4.1.6 曲柄压力机的选用确定压力机的规格时,一般应遵循以下原则。(1)压力机的公称压力不小于冲压工序所需的压力。(2)压力机滑块行程应满足工件在高度上能获得所需的尺寸,并在冲压后能顺利地从模具上取出工件。(3)压力机的闭合高度、工作台尺寸和滑块尺寸等应能满足模具的正确安装。表 4-2 开式压力机的主要结构参数公称压力(KN) 63 160 400 630滑块离下死点的距离 3.5 5 7 8滑块的行程 50 70 100 120行程次数 160 115 80 70固定式和可倾式 170 220 300 360最低 300 400 460最大封闭高度(mm)活动台位置 最高 160 200 220封闭高度调节量(mm) 40 60 80 90滑块中心到床身的距离(mm) 110 160 220 300左右(工作台尺寸)(mm) 315 450 630 710前后(工作台尺寸)(mm) 200 300 420 480前后(工作台孔尺寸) (mm) 70 110 150 180直径(工作台孔尺寸) (mm) 110 160 200 230立柱间的距离(mm) 150 220 300 340模柄孔尺寸(mm) 30 50 50工作台板厚度(mm) 40 60 80 90倾角( 。 ) 30 30 30 30 20该模具的行程为 7mm 所以选用 JB 23-6.3 型压力机。4.2 凸凹模刃口尺寸的计算模具刃口尺寸及其公差是影响冲裁件精度的首要因素,模具的合理间隙也要靠模具刃口尺寸及其公差来保证。因此,正确确定冲裁模凸模和凹模刃口的尺寸及其公差,是冲裁模具设计的重要内容。凸模和凹模刃口尺寸及其公差的确定,必须考虑到冲裁变形的规律、冲裁件的精度要求、冲模的磨损和制造特点等多方面的情况。实践证明,落料件的尺寸和冲孔时孔的尺寸都是以光亮带尺寸为准的,而落料件上光亮带的尺寸等于凹模刃口尺寸,冲孔时孔的光亮带尺寸等于凸模刃口尺寸。因此,计算刃口尺寸时,应按落料和冲孔两种情况分别处理,其原则如下:(1)设计落料模时,因落料尺寸等于凹模刃口尺寸,故应先
- 温馨提示:
1: 本站所有资源如无特殊说明,都需要本地电脑安装OFFICE2007和PDF阅读器。图纸软件为CAD,CAXA,PROE,UG,SolidWorks等.压缩文件请下载最新的WinRAR软件解压。
2: 本站的文档不包含任何第三方提供的附件图纸等,如果需要附件,请联系上传者。文件的所有权益归上传用户所有。
3.本站RAR压缩包中若带图纸,网页内容里面会有图纸预览,若没有图纸预览就没有图纸。
4. 未经权益所有人同意不得将文件中的内容挪作商业或盈利用途。
5. 人人文库网仅提供信息存储空间,仅对用户上传内容的表现方式做保护处理,对用户上传分享的文档内容本身不做任何修改或编辑,并不能对任何下载内容负责。
6. 下载文件中如有侵权或不适当内容,请与我们联系,我们立即纠正。
7. 本站不保证下载资源的准确性、安全性和完整性, 同时也不承担用户因使用这些下载资源对自己和他人造成任何形式的伤害或损失。

人人文库网所有资源均是用户自行上传分享,仅供网友学习交流,未经上传用户书面授权,请勿作他用。