普通车床C6163横向进给传动机构的数控化改造设计【机床数控改造】


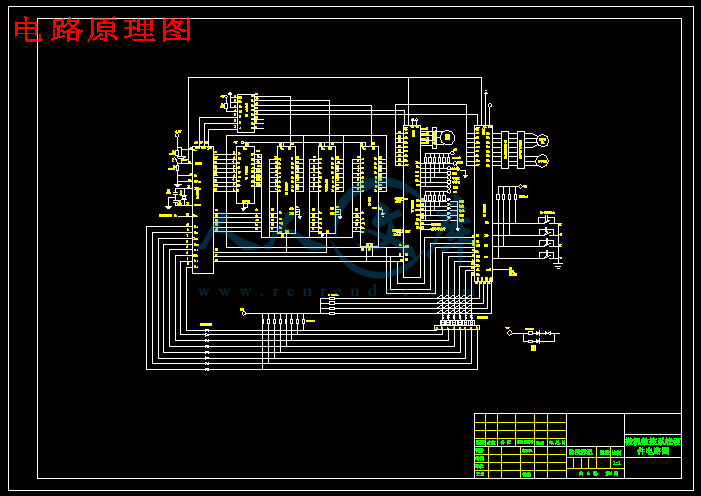

40页 14000字数+论文说明书+3张CAD图纸【详情如下】
C6163经济型数控改造机床总装图.dwg
C6163车床横向进给系统CAD装配图.dwg
普通车床C6163横向进给传动机构的数控化改造设计论文.doc
电路原理图.dwg
1 引言
1.1 机床数控改造的意义
随着当今工业设备对精密程度的要求越来越高,加工设备的机械加工设备的加工的精密程度也要求越来越高。而在中国的机械加工设备的车床中普通车床占了很大比例。这已经越来越制约着当今工业的发展。而数控机床由于价格昂贵,且需要较高技术的加工工人。所以对机床进行自动化改造很是必要。改造后的数控通机床相比有如下优点:
(1) 节省资金
机床的数控改造同购置新机床相比一般可节省60%左右的费用,大型及特殊设备尤为明显。一般大型机床改造只需花新机床购置费的1/3。即使将原机床的结构进行彻底改造升级也只需花费购买新机床60%的费用,并可以利用现有地基。
(2) 性能稳定可靠
因原机床各基础件经过长期时效,几乎不会产生应力变形而影响精度。
(3) 提高生产效率
机床经数控改造后即可实现加工的自动化效率可比传统机床提高 3至5倍。对复杂零件而言难度越高功效提高得越多。且可以不用或少用工装,不仅节约了费用而且可以缩短生产准备周期[1]。
1.2 数控机床的优点和应用
数控机床与普通机床相比,其主要有以下的优点:
(1)适应性强,适合加工单件或小批量的复杂工件;在数控机床上改变加工工件时,只需重新编制新工件的加工程序,就能实现新工件加工。
(2)加工精度高;
(3)生产效率高;
(4)减轻劳动强度,改善劳动条件;
(5)良好的经济效益;
(6)有利于生产管理的现代化。数控机床已成为我国市场需求的主流产品,需求量逐年激增。我国数控机机床近几年在产业化和产品开发上取得了明显的进步,特别是在机床的高速化、多轴化、复合化、精密化方面进步很大。但是,国产数控机床与先进国家的同类产品相比,还存在差距,还不能满足国家建设的需要。随着数控机床越来越多的普及应用,数控机床的技术经济效益为大家所理解。在国内工厂的技术改造中,机床的微机数控化改造已成为重要方面。许多工厂一面购置数控机床一面利用数控、数显、PC技术改造普通机床,并取得了良好的经济效益。我国经济资源有限,国家大,机床需要量大,因此不可能拿出相当大的资金去购买新型的数控机床,而我国的旧机床很多,用经济型数控系统改造普通机床,在投资少的情况下,使其既能满足加工的需要,又能提高机床的自动化程度,比较符合我国的国情[2]。
1.3 国内外数控机床发展情况现状
在美国、日本和德国等发达国家,它们的机床改造作为新的经济增长行业,生意盎然,正处在黄金时代。由于机床以及技术的不断进步,机床改造是个"永恒"的课题。我国的机床改造业,也从老的行业进入到以数控技术为主的新的行业。在美国、日本、德国,用数控技术改造机床和生产线具有广阔的市场,已形成了机床和生产线数控改造的新的行业。在美国,机床改造业称为机床再生(Remanufacturing)业。从事再生业的著名公司有:Bertsche工程公司、ayton机床公司、Devlieg-Bullavd(得宝)服务集团、US设备公司等。美国得宝公司已在中国开办公司。在日本,机床改造业称为机床改装(Retrofitting)业。从事改装业的著名公司有:大隈工程集团、岗三机械公司、千代田工机公司、野崎工程公司、滨田工程公司、山本工程公司等。
我国从1958年开始研究数控机床,一直到20世纪60年代中期还处于研制、开发时期。当时,一些高等院校、科研单位研制出试验性样机,是从电子管起步的。
进入20世纪90年代以来,我国数控机床生产企业都经历了结构调整、转变机制的艰苦磨砺过程。近期,国家为扩大内需,通过加大技改投资和基础设施建设投资的措施来拉动国内市场消费。在20余年间,数控机床的设计和制造技术有较大提高,但对关键技术的试验、消化、掌握及创新却较差。至今许多重要功能部件、自动化刀具、数控系统依靠国外技术支撑,不能独立发展,基本上处于从仿制走向自行开发阶段,与日本数控机床的水平差距很大。存在的主要问题包括:缺乏像日本“机电法”、“机信法”那样的指引;严重缺乏各方面专家人才和熟练技术工人;缺少深入系统的科研工作;元部件和数控系统不配套;企业和专业间缺乏合作等等众多问题。
2 总体方案的设计
2.1 设计任务
对普通车床C6163横向进行数控化改造,其中包括:对横向传动机构的改造,选择传动机构的结构类型,并对传动部件进行计算;设计一个开环的控制系统,该系统包括8位的CPU、扩展存贮器、报警电路、电机控制电路及用8155芯片实现显示及键盘电路等。
2.2 总体方案的论证
对于普通机床的经济型数控改造,在确定总体设计方案时,应考虑在满足设计要求的前提下,对机床的改动应尽可能少,以降低成本。
2.2.1 传动机构类型的选择
(1)在机械设备中,常用的传动机构主要有以下几种:
(a)齿轮传动机构:齿轮机构应用在中心距较小,传动精度较高等各种不同传递动力范围的场合。
(b)螺旋传动机构:在许多机械设备中大量应用着螺旋机构(又称丝杠传动),它主要用于将回转运动转变为直线运动。
(c)带传动与链传动:带传动及链传动多用于中心距较大的传动。
(d)连杆传动机构:连杆机构结构简单、易于制造,在机械设备及日常生活中有大量应用。
(e)凸轮传动机构:凸轮机构可以精确实现要求的运动规律,在自动机械中有广泛的应用,但它是高副接触,因而这种机构重要用于传递运动[4]。
由以上分析可见,本设计此次采用的为第二种螺旋机构。
螺旋传动主要用来把旋转运动变为直线运动,或把直线运动变为旋转运动。其中,有以传递能量为主的传力螺旋,有以传递运动为主,并要求有较高传动精度的传动螺旋,还有调整零件相互位置的调整螺旋。螺旋传动机构又有滑动丝杠螺母、滚珠丝杠螺母和液压丝杠螺母机构。
在经济型数控车床的进给系统中,螺旋传动主要用来实现精密进给运动,并广泛采用滚珠丝杠副传动机构。
滚珠丝杠副传动是在具有螺旋滚道的丝杠和螺母间放入适当数量的滚珠。这些滚珠作为中间传动件,使螺杆和螺母之间的摩擦由滑动摩擦变为滚动摩擦的一种传动装置。它由丝杠、螺母、滚珠及滚珠循环返回装置等四个部分组成。当螺杆转动螺母移动时,滚珠则沿螺杆螺旋滚道面滚动,在螺杆上滚动数圈后,滚珠从滚道的一端滚出并沿返回装置返回另一端,重新进入滚道,从而构成闭和回路。
(2)滚珠丝杠副传动的特点
(a)传动效率高,摩擦损失小。
(b)给予适当预紧,可消除丝杠和螺母的螺纹间隙,反向时就可以消除空程死区,定位精度高,刚度好。
(c)启动力矩小,运动平稳,无爬行现象,传动精度高,同步性好。
(d)有可逆性,可以从旋转运动转换为直线运动,也可以从直线运动转换为旋转运动,即丝杠和螺母都可以作为主动件。
(e)磨损小,使用寿命长,精度保持性好。
(f)制造工艺复杂。滚珠丝杠和螺母等元件的加工精度要求高,表面粗糙度值别小,故制造成本高。
(g)不能自锁。特别是对于垂直丝杠,由于中立的作用,下降时当传动切断后,不能立刻停止运动,所以需要添加制动装置。
(3)滚珠丝杠副的支承方式
为了满足高精度、高刚度进给系统的需要,必须充分重视滚珠丝杠副支承的设计。
(a)一端固定 一端自由
a)丝杠的静态稳定性和动态稳定性都很低。
b)结构简单
c)轴向刚度小
d)适用于较短的滚珠丝杠安装和垂直的滚珠丝杠安装
(b)两端铰支
a)结构简单
b)轴向刚度小
c)适用于对刚度和位移精度要求不高的滚珠丝杠安装
d)对丝杠的热伸长较敏感
e)适用于中等回转速度
(c)一端固定 一端铰支
a)丝杠的静态稳定性和动态稳定性都较高,适用于中等回转速度
b)结构稍复杂
c)轴向刚度大
d)适用于对刚度和位移精度要求较高的滚珠丝杠安装
e)推力球轴承应安置在离热源(步进电机)较远的一端
(d)两端固定
a)丝杠的静态稳定性和动态稳定性最高,适用于高速回转
b)结构复杂,两端轴承均调整预紧,丝杠的温度变形可转化为推力轴承的预紧力
c)轴向刚度最大
d)适用于对刚度和位移精度要求高的滚珠丝杠安装
e)适用于较长的丝杠安装[5]
综上所述,本设计中滚珠丝杠副支承方式由原来的一端固定、一端悬空,变为一端固定,一端径向支承。
(4)滚珠丝杠副轴向间隙的调整
滚珠丝杠的传动间隙是轴向间隙。为了保证反向传动精度和轴向刚度,必须消除轴向间隙。消除间隙的方法采用双螺母结构,利用两个螺母的相对轴向位移,使两个滚珠螺母中的滚珠分别贴紧在螺旋滚道的两个相反的侧面上。用这种方法预紧消除轴向间隙时,应注意预紧力不宜过大,预紧力大会使空载力矩增加,从而降低传动效率,缩短使用寿命。此外,还要消除丝杠安装部分和驱动部分的间隙[6]。