飞机起落架液压系统设计(优秀含全套CAD图纸+设计说明书)
收藏
资源目录
压缩包内文档预览:(预览前20页/共54页)
编号:663035
类型:共享资源
大小:1.12MB
格式:RAR
上传时间:2016-06-13
上传人:hon****an
认证信息
个人认证
丁**(实名认证)
江苏
IP属地:江苏
30
积分
- 关 键 词:
-
飞机
起落架
液压
系统
设计
- 资源描述:
-
飞机起落架液压系统设计(优秀含全套CAD图)。本次设计飞机起落架液压系统设计主要包括下述内容: 1.1 液压系统工作原理设计 液压传动系统主要由供压部分(泵源回路)与工作部分(工作回路)所组成的。设计新的液压系统,首先根据飞机起落架总体对液压系统所提出的操纵要求,性能品质要求,可靠性要求选用合适的泵源回路与各操纵机构的液压工作回路组成整个起落架液压系统。 1) 液压系统方案原理图设计; 2) 液压原理方案说明书; 3) 典型工作剖面液压系统使用功率说明; 4) 液压系统可靠性、温度估算; 5) 方案总体评估说明。 1.2 确定液压系统主要参数 液压系统参数应满足标准化与规范化要求,为此进行系统参数设计前按总体要求首先确定: 1) 液压系统所用液压油; 2) 液压系统的工作压力等级; 3) 液压系统的工作范围; 根据机构执行系统工况,负载及性能要求 ,确定各工作回路所要求的输出功率及泵源回路应提供的功率,从而确定: 4) 液压装置的尺寸及性能; 5) 液压系统的额定流量; 6) 各管段的导管直径。 1.3 选择液压附件,开展对新研制附件的设计工作 根据工作原理图对附件的功能要求与所确定的系统主要参数选择定型的液压附件,对新研制的附件提出指标要求,同时开展对辅助附件的设计工作。 1.4 液压系统的安装调试 按液压系统的设计要求把整个系统在试验室里组装起来,通过1:1地面模拟试验,对液压系统进行全面的性能考核,通过模拟试验能在飞机试飞前考核液压系统性能,并对飞机产生过程中系统的重大更改作出鉴定,为进一步改进液压系统设计和提高系统安全性提供重要保证。
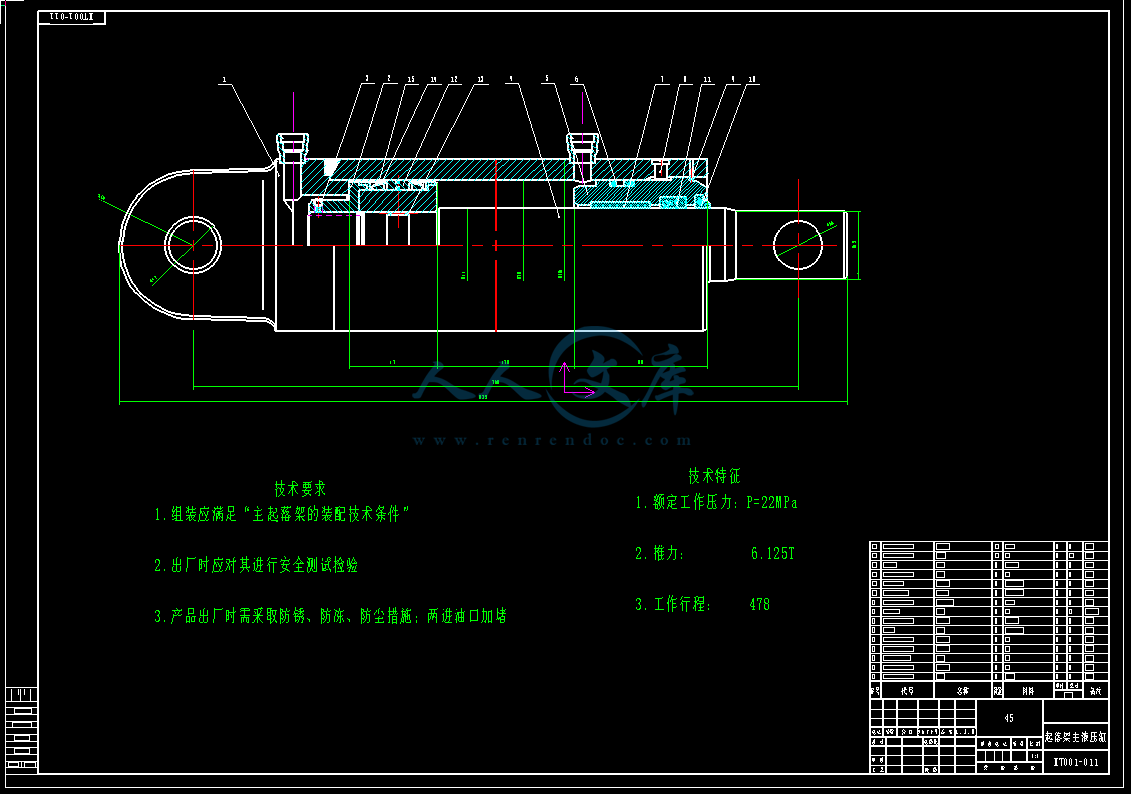




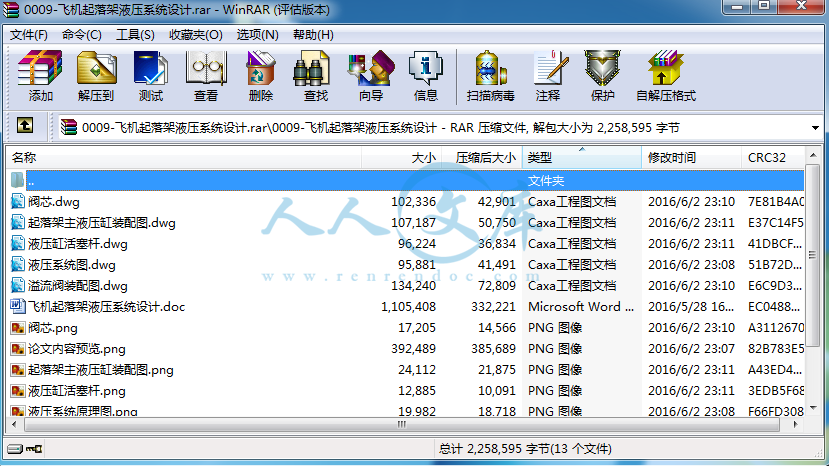


- 内容简介:
-
1 前言 任何人造的飞行器都有离地升空的过程,而且除了一次性使用的火箭导弹和不需要回收的航天器之外,绝大部分飞行器都有着陆或回收阶段。对飞机而言,实现这一起飞着陆功能的装置主要就是起落架。 起落架就是飞机在地面停放、滑行、起飞着陆滑跑时用于支撑飞机重力,承受相应载荷的装置。简单地说,起落架有一点象汽车的车轮,但比汽车的车轮复杂的多,而且强度也大的多,它能够消耗和吸收飞机在着陆时的撞击能量。概括起来,起落架的主要作用有以下四个: 1) 承受飞机在地面停放、滑行、起飞着陆滑跑时的重力; 2) 承 受、消耗和吸收飞机在着陆与地面运动时的撞击和颠簸能量; 3) 滑跑与滑行时的制动; 4) 滑跑与滑行时操纵飞机。 在过去,由于飞机的飞行速度低,对飞机气动外形的要求不十分严格,因此飞机的起落架都是固定的,这样对制造来说不需要有很高的技术。当飞机在空中飞行时,起落架仍然暴露在机身之外。随着飞机飞行速度的不断提高,飞机很快就跨越了音速的障碍,由于飞行的阻力随着飞行速度的增加而急剧增加,这时,暴露在外的起落架就严重影响了飞机的气动性能,阻碍了飞行速度的进一步提高。 因此,人 们便设计出了可收放的起落架,当飞机在空中飞行时就将起落架收到机翼或机身之内,以获得良好的气动性能,飞机着陆时再将起落架放下来。 然而,有得必有失,这样做的不足之处是由于起落架增加了复杂的收放系统,使得飞机的总重增加。但总的说来是得大于失,因此现代飞机不论是军用飞机还是民用飞机,它们的起落架绝大部分都是可以收放的,只有一小部分超轻型飞机仍然采用固定形式的起落架 。 所以说设计设计一种安全可靠性能良好和轻便的飞机起落架液压控制系统是十分必要的。本次设计就一这论题展开设计。 2 1 绪论 液压技术是一门古老而又 兴起的学科 ,随着技术的不断革新近百年来又长足的进展。它被广泛的应用在各行各业中 ,诸如 ,机床液 压 、矿山机械、石油化工、冶炼技术 以及航天航空等方面。可以说液压技术的发展 ,密切关系着我国计民生的许多方面。 正确合理的设计和使用液压系统 ,对于提高各类液压机械装置的工作品质和技术经济性能更具有重要意义。 飞机液压系统设计可以说是极具代表性能的液压系统设计 ,现在就以飞机起落架液压系统作为本次设计。 本次设计 飞机起落架液压系统设计主要包括下述内容 : 压系统工作原理设计 液压传动系统主要由供压部分 (泵源回路 )与工作 部分 (工作回路 )所组成的 。 设计新的液压系统 , 首先根据飞机起落架总体对液压系统所提出的操纵要求 ,性能品质要求 ,可靠性要求选用合适的泵源回路与各操纵机构的液压工作回路组成整个起落架液压系统 。 1) 液压系统方案原理图设计 ; 2) 液压原理方案说明书 ; 3) 典型工作剖面液压系统使用功率说明 ; 4) 液压系统可靠性、温度估算 ; 5) 方案总体评估说明 。 定液压系统主要参数 液压系统参数应满足标准化与规范化要求 ,为此进行系统参数设计前按总体要求首先确 定 : 1) 液压系统所用液压油 ; 2) 液压系统的工作压 力等级 ; 3) 液压系统的工作范围 ; 根据机构执行系统工况 ,负载及性能要求 ,确定各工作回路所要求的输出功率及泵源回路 应提供的功率 ,从而确定: 4) 液压装置的尺寸及性能; 5) 液压系统的额定流量; 6) 各管段的导管直径 。 3 择液压附件 ,开展对新研制附件的设计工作 根据工作原理图对附件的功能要求与所确定的系统主要参数选择定型的液压附件 ,对新研制的附件提出指标要求 ,同时开展对辅助附件的设计工 作 。 压系统的安装调试 按液压系统的设计要求把整个系统在试验室里组装起来,通过 1:1 地面模拟试验 ,对液压系统进行全面的性能考核,通过模拟试验能在飞机试飞前考核液压系统性能,并对飞机产生过程中系统的重大更改作出鉴定,为进一步改进液压系统设计和提高系统安全性提供重要保证。 4 2 液压系统设计指标及要求 用方面要求 一个液压系统往往包括多个工作部分,对它们各自都有不同的使用要求,大致可分为以下几方面: 同的操纵特点 工作部分液压部件的操纵特点基本上可以划分为两类型:一类是传动系统,它们有得要求完成一位或多位得方向控制,有得要求进行一级或多级的压力控制 ,有的要求进行一速或多速控制;另一类是伺服系统,它们要求液压部件跟随操纵指令变化而动作,常用的有机液伺服与电液伺服两类系统。 同的操纵顺序 按照整个系统的要求,了解整个使用过程中各液压部件操纵的先后顺序,哪些是单独工作的,哪些复合运动的。对影响安全的液压部件,还应了解在应急情况下有关部件的操纵情况。 对不同的飞机还会有一些不同的使用要求。上述要求对液压系统的布局与参数选择有很大的影响。例如对伺服系统要求供压泵源保持恒压,而流量有变化要小。对某些危机及安全的液压部件应采用冗余措施,应备有应急操纵系 统和应急泵源。 作环境要求 系统工作环境如最高与最低温度、振动频率与幅值、冲击强度、过载大小、湿度大小、噪音强度、污染和腐蚀情况对系统影响都比较大,所以应注意。 载荷 作用在液压装置上的外载荷基本有下述几种类形 : 1) 质量力 作用在作动部件活动部分的重心上,它包括作动部件的重量和因飞机作加速运动或作动部件本身加速运动时产生的惯性矩。 2) 外力(接触力) 作用在作动部件表面上的力,例如飞机操纵面上作用的气动力,压紧机构的压紧 力等。除了上述的主要载荷外,对液压作动部件本身有上开锁 力, 轴承与密封装置产生的摩擦力 5 及粘性阻尼力等。但这些力一般都比较小,在计算时通常按基本载荷的百分之几加以估算。 能要求 飞机总体对各动作部件所提出的性能要求时液压系统 设计的主要原始依据,它包括:动作部件的行程(或转角),运动速度 范围,加速度范围,动作部件的位置误差和同步动作的时间误差等。 下面列举飞机液压系统各个动作部件的收放时间的大致要求 : 表 2放时间表 -1 in 型 收放起落架时间 (s) 收放减速板时间 (s) 刹车时间 (s) 歼击机 7 8 2左右 线轰炸机 20 远程轰炸机 25 靠 性要求 可靠性指标是液压系统的一项重要指标 ,它往往被设计者忽略 ,液压系统在使用过程中是较容易发生故障的系统之一 ,如果液压系统的可靠性低 ,会使系统失去其使用价值。液压系统可靠性指标有 : 1) 系统基本可靠性 系统可靠性用平均无故障工作时间 该指标主要反应对系统使用维护及修理后与后勤保障方面的要求。 2) 工作寿命 系统的返修期 与报废期 ,系统经合理维修与更换附件其工作寿命应与整系统同寿。 3) 系统故障容错要求 除了提高组成系统附件可靠性 外 ,还应该对系统的结构冗余组成提出故障容错要求。对关键液压系统的泵源部分应满足一次故障工作 ,二次故障安全的故障容错要求。这样对泵源最少有三套独立系统。对关键工作部分应满足故障安全的容错要求。 应有正常与应急两套相互独立系统。 量要求 对飞机上的液压系统重量指标应控制在整机重量的 1左右,这个指标是比较严的,在实际中往往要超过这个数字的 。 按实际 系统 设计而定。 6 3 液压系统原理图设计与参数初步 估算 根据整个液压系统所提出的要求 ,选择合适的工作回路与泵源回路组成液压系统。工作部分要满足各动作部件功能、可靠性能 等方面的需要 ;泵源部分应满足与工作部分协调一致。液压系统工作部分工作时 ,系统泵源应能立即提供所要求的功率 ;液压系统停止工作时候应能自动转入卸荷状态。 选择好的原理方案,是设计出高质 量液压系统的基础。下面原理是经过几个方案比较比较实际实用的一种, 本次设计就以本系统展开 。 理图 参照以前资料将液压系统设计为下图所 示 : 图 3压系统 图 7 压系统原理方案说明 起落架收放系统的功能应保证 ;再收起位置锁紧起落架与舱门起落架放下后锁紧起落架与舱门 ;再收起落架过程中开锁 ,起落架及轮舱收放与上锁等动作顺序应协调 前起落架收放回路基本上采用两种类型 :一种用行程开关和电磁阀的顺序回路 ;另一种用顺序液压缸和触动式顺序阀的顺序回路。 本次设计即用顺序液压缸和触动式顺序阀的回路 ,供压部分来的高压油通到电磁阀1。当驾驶员将舱内起落架开关置于放下位置时 ,电磁阀切换至右位 ,高压油管先进入开锁液压缸 2(顺序 液压缸 )的无杆腔内推动活塞向外运动 ,打开上位锁 ,同时也打开了中间油路。从中间油路流出的高压油分成两路 :一路经应急活门 3 进入机轮护板液压缸的左腔 ,推动活塞向右运动 ,打开机轮护板 ;另一路经液压锁 4进入主起架液压缸左腔 ,推 (右腔 )出口处安装有一单向节流阀 5,起落架放下过程中单向阀处在关闭位置 ,回油只能经过节流阀流出 ,减少了起落架 缓和了撞击 还可以使起落架放下速度比机轮护板打开速度慢些 ,起延时作用 ,以防止起落架撞坏机轮护板。起落架放下后 ,驾驶员把收放开关放回中立位置 ,电磁阀断电 , 阀芯恢复到中 立位置。此时 ,液压缸收起起落架锁在放下位置 ,起双套保险作用。为防止放下腔内被锁闭的油液因油温升膨胀超压 ,和单向液压锁一起并联安置了热安全阀 6。 为了保证放下的可靠 ,再一般飞机上 ,应急放起落架都应采用压缩空气作为应急能源。应急放下起落架时 ,驾驶员首先用手拉开上位锁 ,然后再打开应急放起落架冷气开关 ,储存再冷气瓶中的高压气体通过应急活门 3进入起落架与机轮护板液压缸放下腔 ,将机轮护板打开并放下起落架 电磁阀切换至左位 ,高压油通到收上管路。一方面高压油进入开锁液压缸 ,使起落架上位锁 锁钩复位 ;另一方面进入起落架液压缸右腔使起落架收起 采用了处动式顺序回路。当起落架收起后 ,触动按压式顺序阀 7,使高压油进入机轮护板液压缸右腔 ,将机轮护板收上 防止由于活门不气密机轮护板过早收上。 统基本可靠性估算 可根据附件类型,工作环境条件,从非电子附件可靠性手册中查出附件的失效率,下表给出一般液压附件失效率数据,查出失效率,查出有关附件的失效率,乘上环境因子 按下式估算出系统的平均无故障工作时间。 8 故障时 间公式 : 1li i B (3式中 某类的附件数目 ; L为附件种类数目 ; i某附件的失效率 ; K 环境因子取 80。 表 3他阀选取表 压系统原理放案最后通过评比确定,目前常用的评比办法是记分法,把评比的内容按其重要性的主次给以一定分值,总分值最高的方案为当选方案。用这样方法所选定的方案能够比较全面的满足总体提出要求。 附件名称 故障次数 10-6/h 下限 平均 上限 顺序阀 动泵 定节流孔 流阀 通电磁阀 压缸 9 4 系统主要参数的确定与估算 择系统所用液压油 系统液压油选择一般 按飞机的总体要求确定 ,本次设计选取 10号航空专用液压油 。 下面是其性能指标 : 表 4指标表 il 取系统工作压力等级与系统工作温度范围 统压力确定 液压系统工作压力是系统的最基本参数之一,它对整个系统的性能有很大影响,随着液压系统输出功率增大,系统工作压力等级有日益提高的趋势。 现研究主要着眼于寻求最轻液压系统重量的所谓最佳压力 8结果表明在现有的材料条件下把现有的 2185 42统重量分别比原来轻 5%,6%和 以认 为系统的最佳压力为 附件加工精度高 ,附件生产成本高 ,发热量加大可靠性和寿命降低 8于要设计起落架根据材料选取 22 压力选取具体参照下图: 项目 质量指标 实验方法 外观 红色通明液体 目测 运动黏度 256 50 C 不小于 10 C 不大于 1250 机械杂质 无 511 油膜质量( 65 C+1 C) 合格 264 密度( 20 C) 850 1884 10 图 4力 曲线 图 of 系统主参数给定 液压系统主要参数应满足标准化与规范化的要求 ,在此进行系统参数设计设定。 1) 泵的输出压力 2 2) 主起落架液压缸的输入压力为 3) 溢流阀工作压力 P= 4) 液压系统的工作温度范围: C 70 C。 定执行机构的参数 现在以起落架主起液压缸 和溢流阀 为设计实例 : 压缸设计 1) 液压缸的设计通常要求满足下述最基本技术要求: (1) 承受最大的负载力,即输出力 P=104N; (2) 输出动作时间 T 7s; (3) 最大工作行程 L=。 以上数据是由 被操作对象的要求提出来的。例如起落架收放液压缸的负载力 落架本身的重量以及惯性等来确定的。最大速度或动作时间 大工作行程 11 起落架传动图从收起位置到放下位置之间的运动范围提出的。 为了满足所提出的技术要求,设计液压缸最基本的内容在于保证其一定的有效面积,强度和不漏油,并满足性能指标及使用要求。 2) 设计步骤和方法 (1) 液压缸的输入压力 液压缸的输入压力 通常有三种不同的观点: 其一,按最小重度观点。经理论计算和实验检验,航空液压系统总重量与系统工作压力有关,目前系统认为的最佳压力应为 2以,液压缸的输入压力 : 2 二,按最佳强度观点,此观点在本质上还是为了减小元件的尺寸和重量,不过是以材料强度为依据罢了,其结果形式为: 1 p ( 4 式 中 为液压缸缸壁材料的许用应力。这就是说,此种方法是按照液压缸材料来确定压力的 ,其壁厚应满足筒内外径比值0三,按液压泵的实际工作压力确定液压缸的最大输入压力。即 1 0 .9 4 这种方法不能满足最佳性能的要求,但却 是一种按具体问题采取具体解决的方法。式子种的系数,是考虑到传输管路和控制阀的压力损失。 (2) 确定有效面积 和杆径 d 以双面活塞杆液压缸为例,根据经验数据取回油腔的压力为 么输入力公式变为: P=(=(= ( 4 则有效面积的计算公式为: F=P/2/( 10 ( 4 为了确定液压缸内径 d,按经验引入一个结构系数即 m=d/D= ( 4 取 m=中 速小负载下取小反之取大值,由得下式 12 24(1 ) ; d= ( 4 将 F=10; m= 得 D= ; d= ; (3) 确定壳体壁厚和外径 据( 16D/ 3)计算公式 1( 2 . 3 )P ( 4 式中 为强度系数,(无缝钢管 =1), 2 7 . 8 0 . 2( 2 . 3 7 2 . 9 1 9 . 8 ) 1 =统计,飞机液压缸一般属于中等壁厚,故推荐用中等壁厚公式。 壁厚确定后,按下式确定外径 w=D+2 = ( 4 (4) 确定密封装置的型式和尺寸 液压缸的密封装置广泛地采用圆界面橡胶圈。这种形式结构简单,装卸方便,寿命长,在 30封装置按不同的工作条件来选择。 表 4下表为圆截面橡胶密封圈的 各 项要求 or 封形式 圆截面橡胶密封圈 密封原理 基于密封圈和被密封表面间的接触压力和侧压力作用而加强密封性 密封材料 硅橡胶;氟橡胶四塑料 特殊技术要求 要正确的计算和选择压缩率,正确选择槽宽度配合精度和光度在超过 15般增设保护挡圈,性能更可靠 优缺点及应用 结构简单装卸方便成本低可用于 3560 3000内工作在飞机液压系统中得到广泛应用 关于密封装置得原理理论计算在设计中修正了圆截面橡胶密封圈得 经验公式 : 13 图 4塞密封圈示意 图 of b = (1 d ;= 1 .2 c m= 0 c m ;C = 0 .8 d = 0 .2 c m= 0 c m ; s = ( 0 . 1 0 . 0 0 1 ) m m ( 4 式 中的 一般可用二级配合,压力越高, 。 (5)确定液压缸长度 缸未伸出长度为 L;活塞宽度2l;行程长3l;导向长度4l;结构长度1l;导向套长度5( 4 式 中 将 式中的已知量带入得:(见图) 图 4结构尺寸示意 图 4 7 8 4 4 4 5 . 92 0 2l m m ; ( 4 2 0 . 6 0 . 6 7 8 4 7l d m m ( 4 14 25 8 0 4 7 6 3 . 522ll ; ( 4 4 7 4 7 8 8 0 2 4 0 8 4 5L m m ( 4 (6) 验算活塞杆纵向弯曲强度和稳定性 在一般情况下当杆与杆径之比小于 15时候,可不用验算活塞杆纵向弯曲强度和 稳定性比值大时候,可按下式公式进行验算: 2 d ( 4 式中的 444444()643 . 1 4( 0 . 1 0 4 2 0 . 0 7 8 )640 . 1 5 1 0a a 4 4 53 . 1 4 0 . 0 4 4 0 . 1 8 1 06 4 6 4 m 因为 4 7 4 7 8 8 0 9 5 7 0 04 4 ; 1 5 . 9 1 5l m m 杆杆径径 则 k=所以需要验算 1 1 4253 . 1 4 2 . 1 1 0 0 . 1 5 1 00 . 1 81 . 3 1 33 . 2 8 1 0 P=104N 故满足条件。 (7) 缸体与缸盖的焊缝强度计算 其焊缝应力公式为: 22w()4( 4 式子 5390 . 7 ; 1 3 4 . 7 544 b M P a 带入可得: 15 442226 . 1 2 5 1 0 6 . 1 2 5 1 0 2 3 . 5 80 . 0 0 2 6( 0 . 1 0 4 2 0 . 0 7 8 ) 0 . 74 P ( 4 故符合要求。 定液压泵参数 液压泵的两个主 要参数为所承受的最大压力于应提供的最大流量 液压泵应提供的流量可按下述步骤确定 : 1) 计算液压缸所需提供的流量 已知液压缸尺寸及其收放或收方速度要求 ,可按照下式计算液压缸所需要的流量 : i U F ( 4 式中 : 2) 确定所有工作部分所需用的流量 ( 4 主起落架收 放液压缸与工作容积为7 . 8 4 . 4 ) 4 7 . 8 1 5 6 04 起落架收放液压缸与工作容积为6 . 0 3 . 5 ) 2 7 . 6 5 1 74 据总体要求 ,起落架收起时间为 7S,这起落架收放系统所需用的流量 . 5 2 4 3 1 . 2 m i nZ q LQ 3) 确定液压泵供油量 16 液压泵供油量根据上面算出 的式子有以下公式可得 : (1) 液压系统存在内部泄漏 (2) 带动液压泵的发动机转速下降时 ,液压泵的流量下降 (3) 长期使用液压泵使供油量下降 (4) 系统中有些控制阀直接流回油箱 因此 ,液压泵的供油量应为 : Q ( 4 3 1 . 2 5 3 6 . 2 m i Q 故液压泵的供油量为 36.2 选取泵 型号 : 论排量 /r( 力 /定 : 22 压力 /高 : 25 转速 /r 额定 : 2000 转速 /r 最高 : 3000 转速 /r 最低 : 600 容积效率 /%: 91 总效率 /%: 82 驱动功率 /定工作状况 ): 31 液压系统的主要参数就是压力和流量,他们是设计液压系统,选择液压元件的主要依据。压力决定与外载荷。流量取决于液压执行元件的运动速度和结构尺寸。 流阀设计 溢流阀的设计,通常式根据其工作所要求的压力和流量选择阀的基本结构形式,根据最大流量并按经验确定阀的各部分尺寸,根据静态特性要求确定弹簧系数,然后计算静态特性。即按静态性能要求进行设计,之后 可对动态特性能如压力超调量,阀的自振频率等进行校验。下面我们对先导溢流阀为例来介绍溢流阀的设计。 以下为尺寸示意图 : 17 图 4结构尺寸示意 图 of ) 设计要求 一般提出以下设计要求: (1) 额定压力 2) 额定流量 3 6 .2 m Q (3) 调压范围1 m i n 1 m a x 2 6 . 44) 背压 0 0p (5) 调成最高调成压力1阀的开启压力2 1 m 918 (6) 调成最高调成压力1阀的开启压力1 1 m a 9 5 (7) 调成最高调成压力1阀的闭合压力1 1 m 9 (8) 卸荷压力 ) 主要的结构尺寸的初步确定 (1) 进油口尺寸确定 按照额定流量和允许流速来决定则: 4 ( 4 式 中 m/L;定流量,将已知量带入可得: 4 3 6 . 2 7 . 6 9 2 . 7 76 3 . 1 4d 2) 主阀芯直径 1d 按经验取 1 ( 0 . 5 0 . 8 2 ) 1 . 6 6 ( 4 (3) 主阀芯活塞直径 01(1 . 6 2 . 3 ) 1 . 6 6 2 3 . 2 2 ( 4 0上式选取0额定流量小的阀选较大的值。 (4) 主阀芯上段直径 2D 按经验取主阀芯活塞下边面积3 根据上式子可得: 34340 0 4()422012202( D - d )D - d 19 211 0 023344( ) 11 20 . 7 53 . 3 2 1 1 . 5 20 . 9 5D ( 4 活塞下边面积稍小于上边面积,主阀关闭时的压紧力主要靠这个面积差形成液压力作用在主阀芯上。主阀弹簧只是在低压和无压力时使主阀关闭,因此主阀弹簧刚度可以很小。 (5) 主阀芯半锥角 1 ,主阀座半锥角 1 和扩散 角 2 按经验取: 1 46 1 43 2 2 2 3 5 1稍大于1,使主阀芯与主阀座近似为线接触(接触线的直径近似于1d),密封性较好。 (6) 尾碟(消振尾)直径4d、长度4l、过度直径5尺寸4d、4l、5尾碟时,作用在主阀芯上的液动力方向向上;有了尾碟时,液动力方向向下。 (7) 节流孔直径0d、长度0 0 0 . 0 8 0 . 2 0 . 1d ( 4 00( 7 1 9 ) 1 . 0 ( 4 节流孔的尺寸0果节流孔太大或太短,则节流作用不够,将使阀的启闭特性变差,而且工作中会出现较大的压力振摆;反之,如果节流孔太小或太长,则阀的动作会不稳定,压力超调量液会加大。按上式取0额定流量小的阀选较小的值。要求通过节流孔的流量小于或等于额定流量的 1时所造成的压降足 20 以使主阀开始打开。因此,要通过静态特性计算对选定的0 (8) 导阀芯的半锥角2按经验取 : 2 20 2取得小一些,密封性能较好 但太小使阀芯与阀座得接触应力加大,影响使用寿命。 (9) 导阀座孔的孔径2 20( 2 5 ) 0 . 4 ( 4 6 ( 4 2尺寸加大;取得太小又影响阀的稳定性能。 6则容易发生尖叫和振动。 (10) 主阀芯溢流口的直径3免产生的压差太大,不利于主阀的开启。 (11) 主阀座的孔径1 11 ( 0 . 1 0 . 2 ) 1 . 5 6D d c m ( 4 (12) 阀体沉割直径3D、沉割宽度1 30 ( 0 . 1 1 . 5 ) 3 . 5D D c m ( 4 1保证进油口直径的要求。 本设计中取 1 0 . 4 3 . 1 7S d c m ( 4 (13) 主阀芯与阀盖的间距22 (14) 导阀弹簧的装配长度5 0 . 1 0 . 2 )l L c m( 4 21 式 中的2了使溢流阀能够卸荷,调节手轮全松开时应使导阀弹簧恢复其自由长度2L, 留有 12间隙 (15) 主阀弹簧的装配长度1 1l L h( 4 式中 1L主阀弹簧的自由长度; 1h主阀弹簧的预压缩量 ,1 3) 静态特性计算 (1) 基本方程式 先导式溢流阀的静态特性决定于导阀、主阀和节流口结构参数。因此,计算静态特性时要列写流量方程式和力平衡方程式,作为计算静态特性的基础。 如图所示主口示意图: 图 4阀口示意图 1 1 1 1 22 ()Q C f p p(4式中 1Q 通过主阀的流量 ; 1C 主阀流量系数 ; 1f 主阀节流面积。 22 将式子整理得: 1 1 1 1 1s i n ( s i n 2 ) s i x D D x 主阀芯轴线方向所受的作用力包括弹簧力、重力、摩 擦力、主阀芯溢流孔3 腔压力的作用力、阀口溢流时产生的液动力。如主阀芯等速上升,则可列出受力平衡方程式为 : 1 3 2 4 1 1 1 2 1 p F K h x G P P P (4式中 1K 主阀弹簧刚度; 1h 主阀弹簧预压缩量; G 主阀芯重量; 1P 主阀芯所受的摩擦力; 2P 主阀芯溢流孔 3d 压降引起的作用力; 1主阀芯所受的液动力; 根据图所示液流情况,1 1 1 2 1 1c o v v (4式中 1v 阀口流速; 2v 尾碟处液体流出速度2 因为尾碟附近过流面积远大于阀口截面积,而且尾碟与主阀芯轴线垂直。所以,尾碟附近流速的轴向分量接近于零,即2v 0。 阀口流速1 112 1 21v p p (4在局部阻力系数 0 时,流速系数 1 。因此可得: 1 1 11 1 1 1 1 1 11 1 1 1c o i n c o ss i n 2 D p D p x 23 由式可知,1向于1相同。计算出来的稳态液动力略为偏大一些。 若尾碟过大,出口通道过小,即尾碟附近截流面积减小,则2加大。这样,实际液动力会比计算出来的小,若主阀开度较大则使得1过小2以,设计尾碟和选取半锥角1时要加以注意。 将上式联立可得主阀芯平衡方程式: 1 3 2 4 1 2 1 1 1 1 1( ) s i n 2p F P F K h x G P P C D P x (4当截流孔中流动为层流时,流过节流孔的流量02成正比;当节流口中的流动为紊流时,流量0212(p 成比例。实际上节流孔中的流动多处于从流层到紊流的 过渡状态,所以0312(p 成比例。0中的单位必须是米、公斤、秒制。 22 120 330 0 1 222 0( ) ( )14f p (4式 中 0Q 通过节流孔的流量; 0f 节流孔截面积; 油的运动粘度; 油的重度 。 由式 (4: 2 2 2 2 32 ()Q C f p p(4式中 2 2 2 24 2 2 2 2 2s i n ( s i n 2 ) s i y d d y (4式 中 y 导阀得开度。 将3 : 2 2 2 2 22s i d y p(4导阀芯轴线方向所受得作用力有弹簧力、液动 力、导阀前腔 力平衡方程为: 2 2 2 2() K h y P (4式中 22K导阀弹簧刚度 ; 2h 导阀弹簧预压缩量 ; 2阀芯所受的液动力 。 液动力2 : 2 2 2 2 2 2 2( ) s i n 2 K h y C d (4式 (4的流量系数1C、2格的说,在 阀的不同工作情况下,流量系数又不同的数值。通常将流量系数看成常数,带来的误差并不大,却可以大大地减化计算。主阀与导阀的阀口处的流量系数可分别取为: 静态特性计算的目的,一方面是根据对静态特性设计要求,求出主阀弹簧和导阀弹簧的刚度和预压缩量,作为进行弹簧设计的依据;另一方面是校核上面所确定的主要结构尺寸,看能否满足对静态特性的要求 ,并进行必要的调整与复算,直到特性满足要求为止。 (2)弹簧刚度和预压缩量计算 25 由式子 ( 4,可得当主阀刚要打开,还未打开时 可得: 1 3 2 4 1 1 1 2p F p F K h G P P (41 1 1 3 2 4 1 2K h p F p F G P P 31 1 2 4 1 24 ( 1 ) Fp p p F G P 利用上式可求出1必须先做以下工作: (a)主阀刚要打开,还未打开, 1p 为主阀的开启压力 取1 : 1 2 1 m a 9 5p p p(41 0 . 9 5 2 6 . 4 2 5 . 0 8p M P a , 此时候流量为 : 0 . 0 1 0 . 0 1 3 6 . 2 0 . 3 6 2 m i (b)由 ( 4节流孔流量方程式求2得 : 0210 0 014 d f f (4将已知量带入: 6 2 11 0 1 0 g 62 2 200 3 . 1 4 0 . 0 0 2 3 . 1 4 1 044f d m 可得: 5 3 32 1 0 1 03223 6 . 2 3 6 . 21 4 8 5 0 9 . 8 1 0 0 . 0 1 1 0 1 06 0 6 02 5 . 0 89 . 8 0 . 0 0 2 3 . 1 4 1 0 3 . 1 4 1 02 5 . 0 8 7 . 0 7 1 02 5 . 0 7 3 P a (4 26 (c)主阀芯摩擦力1表示为 : 1 2 0fP (4式中 f 2 0 侧压力与缝隙两端压力差 p 、缝隙长度 l 、 圆柱直径 D 成正比。将其他因数用系数 取摩擦系数 ,则1 1 2 2 2 3 0 0 1 20 . 1 0 . 1P K D l p p K D l p p (4将压力3 : 1 2 2 2 0 0 1 20 . 1 0 . 1P K D l p K D l p p (42 2 6 2 30 . 1 0 . 2 1 . 5 2 1 0 0 . 8 1 0 2 5 . 0 3 7 1 0 0 . 1 0 . 2 3 . 3 2 1 0 7 . 0 7 1 0 20 . 6 1 1 0 4 . 7 1 0 61 47 108N 式中 K 为系数, ,直径小、接触长度短时取 大值。 (d)求主阀芯溢流孔3沿程阻力和进口、出口处的局部阻力所组成。 可表示为 : 23333 2 (4式中 f 进口处局部阻力系数; c 出口处局部阻力系数; 沿程阻力系数。 27 通过主阀芯溢流孔的流量等于通过导阀的流量2Q,取近似2 于是, 主阀芯溢流孔流速为 : 23 22334 0 . 0 14 (4雷诺数的 表示式为 : 33 234R v v d 由于2阀芯溢流孔内流动为层流,可以 0 0 , ,2e 。于是,由压降 3p 引起的作用力为 : 222 332 2 3342 (4 2 22 32 2 34433210 e 2 222344 32 0 . 0 30 . 2 2 0 . 0 41 0 3 . 1 4 0 . 0 0 4 23 22443 6 . 22 8 5 0 1 0600 . 0 1 5 2 0 . 0 0 4 2 . 2 0 . 31 0 3 . 1 4 0 . 0 0 4 (e)求出主阀最大开度过额定流量阀由最大开度, 由 此 可得 : m a 12s i p (43263 6 . 2 106020 . 8 3 . 1 4 1 . 5
- 温馨提示:
1: 本站所有资源如无特殊说明,都需要本地电脑安装OFFICE2007和PDF阅读器。图纸软件为CAD,CAXA,PROE,UG,SolidWorks等.压缩文件请下载最新的WinRAR软件解压。
2: 本站的文档不包含任何第三方提供的附件图纸等,如果需要附件,请联系上传者。文件的所有权益归上传用户所有。
3.本站RAR压缩包中若带图纸,网页内容里面会有图纸预览,若没有图纸预览就没有图纸。
4. 未经权益所有人同意不得将文件中的内容挪作商业或盈利用途。
5. 人人文库网仅提供信息存储空间,仅对用户上传内容的表现方式做保护处理,对用户上传分享的文档内容本身不做任何修改或编辑,并不能对任何下载内容负责。
6. 下载文件中如有侵权或不适当内容,请与我们联系,我们立即纠正。
7. 本站不保证下载资源的准确性、安全性和完整性, 同时也不承担用户因使用这些下载资源对自己和他人造成任何形式的伤害或损失。

人人文库网所有资源均是用户自行上传分享,仅供网友学习交流,未经上传用户书面授权,请勿作他用。