【温馨提示】 购买原稿文件请充值后自助下载。
以下预览截图到的都有源文件,图纸是CAD,文档是WORD,下载后即可获得。
预览截图请勿抄袭,原稿文件完整清晰,无水印,可编辑。
有疑问可以咨询QQ:414951605或1304139763
摘要
本文是在摇杆的图样分析后进行摇杆的机械加工工艺路线的设计,同时按照其中的加工工序的要求设计夹具。
摇杆的主要加工内容是表面和孔。其加工路线长,加工时间多,加工成本高,零件的加工精度要求也高。按照机械加工工艺要求,遵循先面后孔的原则,并将孔与平面的加工明确划分成粗加工和精加工阶段以保证加工精度。基准选择以底面作为粗基准,以底面与两个工艺孔作为精基准,确定了其加工的工艺路线和加工中所需要的各种工艺参数。
在零件的夹具设计中,主要是根据零件加工工序要求,分析应限的自由度数,进而根据零件的表面特征选定定位元件,再分析所选定位元件能否限定应限自由度。确定了定位元件后还需要选择夹紧元件,最后就是确定专用夹具的结构形式。
关键词:摇杆;加工工艺;工序;专用夹具
Abstract
This paper is the design of mechanical machining process route of rocker rocker in pattern analysis after, at the same time according to the design process requirements of the fixture.
The main contents of the rocker is processing surface and the hole. The processing route long processing time, high processing cost, the machining precision is high. In accordance with the requirements of the machining process, follow the principle of the surface after the first hole, and the hole and the plane processing clearly divided into roughing and finishing stages of processing to ensure accuracy. Reference to the bottom as the benchmark crude, the bottom with two holes as a precision technology base, a variety of process parameters to theprocessing technology and processing were determined..
Keywords: rocker; process; process; special fixture
目 录
摘要 I
Abstract II
1 序言 1
2 零件的分析 2
2.1零件的作用 2
2.2 零件图 2
2.3零件的工艺分析 3
2.4工艺规程设计 3
2.4.1确定毛坯种类 3
2.4.2基面的选择 4
2.4.3制定工艺路线 6
2.4.4机械加工余量工序尺寸及公差的确定 6
2.4.5确定切削用量及时间定额 7
3 钻孔专用夹具设计 13
3.1问题的指出 13
32定位基准的选择 13
3.3夹具方案的设计 13
3.4.切削力和夹紧力计算 14
3.5夹紧力的计算 14
3.6定位误差分析 15
3.7 零、部件的设计与选用 16
3.8 确定夹具体结构尺寸和总体结构 17
总 结 19
致 谢 20
参 考 文 献 21
1 序言
机械制造技术基础学是以机械制造中的工艺问题为研究对象,实践性较强的一门学科,通过对此门学科的毕业设计,使我在下述各方面得到了锻炼:
⒈能熟练运用机械制造技术基础课程中的基本理论以及在生产实习中学到的实践知识,正确的解决一个零件在加工中的定位、夹紧以及工艺路线的安排、工艺尺寸的确定等问题,保证零件的加工质量。
⒉提高结构设计能力。通过设计夹具的训练,获得根据被加工零件的加工要求,设计出高效、省力、既经济合理又能保证加工质量的夹具的能力。
⒊学会使用手册及图表资料。
⒋培养了一定的创新能力。
通过对拔叉的工艺及夹具设计,汇总所学专业知识如一体(如《互换性与测量技术基础》、《机械设计》、《金属切削机床概论》、《机械制造工艺学》、《金属切削原理与刀具》等)。让我们对所学的专业课得以巩固、复习及实用,在理论与实践上有机结合;使我们对各科的作用更加深刻的熟悉与理解,并为以后的实际工作奠定坚实的基础!
2 零件的分析
2.1零件的作用
题目所给的零件是车床的摇杆铣床叉。它位于车床床变速机构中,主要起换档,使主轴回转运动按照工作者的要求工作,获得所需的速度和扭矩的作用。
2.2 零件图
2.3零件的工艺分析
零件的材料为HT200,灰铸铁生产工艺简单,铸造性能优良,但塑性较差、脆性高,不适合磨削,为此以下是摇杆需要加工的表面以及加工表面之间的位置要求
1.小头孔以及与此孔相通的键槽
2.大头圆孔Ф36
3.小头孔端面、大头圆孔上下Ф60端面。
由上面分析可知,可以粗加小头孔端面,然后以此作为粗基准采用专用夹具进行加工,并且保证位置精度要求。再根据各加工方法的经济精度及机床所能达到的位置精度,并且此摇杆零件没有复杂的加工曲面,所以根据上述技术要求采用常规的加工工艺均可保证
2.4工艺规程设计
2.4.1确定毛坯种类
1零件材料为HT200,零件结构较简单,中等批量生产,选择砂型铸造毛坯,查《机械制造工艺设计简明手册》,表2-2-5,选用铸件尺寸公差等级为CT-12。
2确定加工余量及形状
加工余量
36上端面 3
36下端面 3
60上端面 3
60下端面 3
36 孔 3
15 孔 实心
3绘制铸件毛坯图
2.4.2基面的选择
定位基准是影响摇杆零件加工精度的关键因素。基准选择得合理可以使加工质量得到保证,生产率得以提高。否则,加工过程中将问题百出,更有甚者,造成零件的大批报废,使生产无法正常进行。
(1)粗基准的选择。对于零件而言,尽可能选择不加工表面为粗基准。而对有若干个不加工表面的工件,则应以与加工表面要求相对位置精度较高的不加工表面作粗基准。
(2)精基准的选择。主要应该考虑基准重合的问题。当设计基准与工序基准不重合时,应该进行尺寸换算,这在以后还要专门计算,应该进行尺寸互算。
(3)加工阶段的划分
该摇杆加工质量要求较高,可将加工阶段划分成粗加工、精加工和精加工几个阶段。
(4)工序的集中和分散
本摇杆选用工序集中原则安排摇杆的加工工序。该摇杆的生产类型为成批生产,可以采用万能型机床配以专用工装、夹具,以提高生产率;而且运用工序集中原则使工件的装夹次数少,不但可缩短辅助时间,而且由于在一次装夹中加工了许多表面,有利于保证加工表面之间的相对位置精度要求。
(5) 加工原则:
1)遵循“先基准后其他”原则,首先加工基准——摇杆下端面
2)遵循“先粗后精”原则,先安排粗加工工序,后安排精加工工序。
3)遵循“先主后次”原则.
4)遵循“先面后孔”原则.
2.4.3制定工艺路线
制定工艺路线得出发点,应当是使零件的几何形状、尺寸精度及位置精度等技术要求能得到合理的保证,在生产纲领已确定的情况下,可以考虑采用万能性机床配以专用夹具,并尽量使工序集中来提高生产率。除此之外,还应当考虑经济效果,以便使生产成本尽量下降。
工艺路线方案:







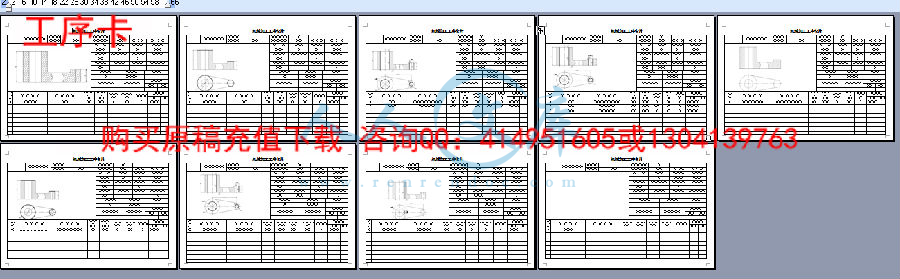
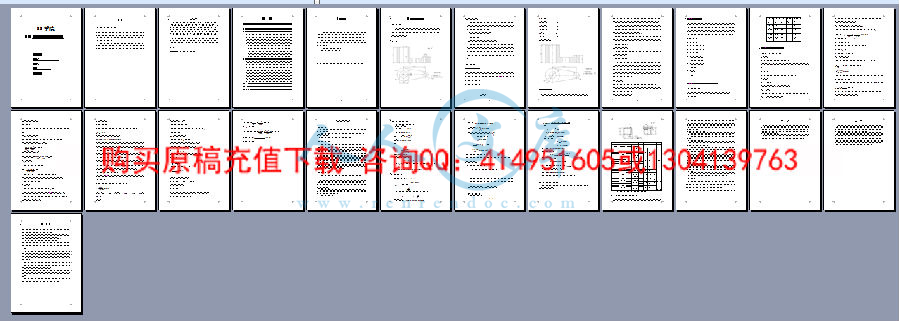