【温馨提示】 购买原稿文件请充值后自助下载。
以下预览截图到的都有源文件,图纸是CAD,文档是WORD,下载后即可获得。
预览截图请勿抄袭,原稿文件完整清晰,无水印,可编辑。
有疑问可以咨询QQ:414951605或1304139763
摘 要
冲压模具主要是将板料分离或成形而得到制件的加工方法。因为模具的生产主要是大批量的生产,而且模具可以保证冲压产品的尺寸精度和产品质量,模具的设计与制造主要考虑到模具的设计能否满足工件的工艺性设计,能否加工出合格的零件,以及后来的维修和存放是否合理等。
本文阐述了冲压复合模的结构设计及工作过程,通过工艺分析,采用落料冲孔工序,通过冲裁力、顶件力、卸料力等计算,确定模具类型。该模具采用后侧导柱模架,左右两边的导柱和导套采用同一型号。落料凹模采用整体结构,废料从凸凹模的开槽中卸出。本模具性能可靠,运行平稳,提高了产品质量和生产效率,降低劳动强度和生产成本。
关键字:冲压;落料冲孔;复合模;模具结构
目 录
摘 要 3
第一章、绪论 6
第二章、冲压件工艺性分析及冲裁方案的确定 7
2.1.材料分析 7
2.2.冲裁件的结构工艺性 7
2.3.冲裁件尺寸精度和表面粗糙度要求 7
2.4.冲裁方案的确定 8
第三章、排样图的设计及材料利用率的计算 9
3.1.排样的设计 9
3.2.搭边的选取 9
3.3.材料利用率的计算 11
第四章、冲裁工艺力的计算 12
4.1.冲裁力的计算 12
4.1.1.冲裁力的计算公式 12
4.2.卸料力、推件力的计算 12
4.3.冲压压力中心计算 13
第五章、冲压设备的选择 15
5.1.冲压设备选择 15
第六章、冲裁模工作部分设计计算 16
6.1.冲裁间隙 16
6.2.模具刃口尺寸的计算 16
6.2.1.落料部分刃口设计计算 17
6.2.2.冲孔部分刃口设计计算 18
第七章、卸料零件计算 20
7.1.卸料装置的选择 20
第八章、主要零部件设计 21
8.1.落料凹模设计 21
8.1.1.落料凹模刃口形式 21
8.1.2.落料凹模外形和尺寸的确定 22
8.1.3.落料凹模的结构形式 22
8.2.凸凹模设计 23
8.2.1.模具的结构形式和固定方法 23
8.2.2.凸凹模长度的确定 24
8.2.3.凸凹模结构设计 24
8.3.冲孔凸模 25
8.3.1.冲孔凸模的固定形式 25
8.3.2.凸模强度校核 25
第九章、标准件的选择 26
9.1.模架及模柄的选择 26
9.2.凸模固定板及垫板的选择 26
9.3.模具闭合高度的校核 26
9.4.卸料螺钉 27
9.5.螺钉及销钉的选择 27
总 结 28
参考文献 29
第一章、绪论
我国模具近年来发展很快,我国模具无论是从品种数量还是精度方面都有了大幅度 的提高模具对工业产品的生产的影响也越来越大我过模具也由过去靠进口都逐步自行设计制造使模具加工工艺手段上升一个台阶同时为先进工艺发展奠定了坚实的基础特别是模具成型表面的特种加工工艺的研究和发展使模具加工精度和粗糙度都有了很大的改善。过去,我过只能制造简单的,容易加工的模具,目前我国发展迅速,已经可以制造大型的,高精度的模具,而且模具寿命长。例如,在冲压模具方面,我国制造的电机定转子硅钢片硬质合金多工位自动级进模,电子电器行业用的50余位工位的硬质合金多工位自动级进模,都已经超过国际同类模具产品的技术水平。我国模具制造业近十余年的年工业产值持续以 15%的增长速度在迅猛发展,已经成为国民经济的一个非常重要的工业分支。
改革开放以来,随着国民经济的高速发展,模具工业企业的所有制成分也发生了巨大变化,除国有专业模具厂外,集体、合资、独资和私营也得到了快速发展,尤其是私营企业,迅猛发展。浙江宁波和黄岩,余姚等地素有“模具之乡”之称。
近年来,我国冲压模具水平已有很大提高。大型冲压模具,单套模具生产能力已能生产单套重量达50多吨的模具。中档轿车配套的覆盖件模具内也能独立生产。精度达到1~2μm,寿命2亿次左右的多工位级进模在国内,江苏,这两等地已有多家企业能够生产。表面粗糙度达到Ra≦1.5μm的精冲模,大尺寸(φ≧300mm)精冲模及中厚板精冲模国内也是发展很快,引进国外先进技术,也已达到相当高的水平。
第二章、冲压件工艺性分析及冲裁方案的确定
2.1.材料分析
冲裁材料为Q235,查文献[1] :属于普通碳素结构钢,屈服点σs=240MPa,抗拉强度σb=380-470MPa,,抗剪强度τ=310-380MPa,延伸率不小于21-25%,塑性好,焊接性好,适合冲裁。
2.2.冲裁件的结构工艺性
冲裁件的结构形状应尽可能简单、对称、避免复杂形状的曲线,在许可的情况下,把冲裁件设计成少、无废料排样的形状,以减少废料,矩形孔两端宜用圆弧连接,以利于模具加工。从产品形状看,产品属于圆形,四周是圆弧的,这样凹模不会因为热处理应力集中而导致开裂。
冲裁件凸出或凹进的部分不能太窄,尽可能避免过长的悬臂和窄槽,如图2-2所示。最小宽度b一般不小于1.5t,若冲裁材料为高碳钢,b≥2t, ,当材料厚度t<1mm时,按1mm计算。该工件凸出部分的宽度为9mm。9mm≥1.5t=1.5×2=3mm,满足条件。
冲裁件的孔径因受冲孔凸模和刚度的现在,不宜太小,否则容易折断和压弯,冲孔的最小尺寸取决于冲压材料的力学性能,凸模强度和模具结构。该冲裁件的孔径d=4mm≥1.5t=1.5×2=3mm,查文献[2]:P75表2-18,用无保护套凸模冲孔。
2.3.冲裁件尺寸精度和表面粗糙度要求
表2-2 冲裁件孔中心距公差 (mm)
材料厚度t 普通冲孔公差 高级冲孔公差
孔距中心尺寸
≤50 50~150 150~300 ≤50 50~150 150~300
≤1 ±0.1 ±0.15 ±0.2 ±0.03 ±0.05 ±0.08
1~2 ±0.12 ±0.2 ±0.3 ±0.04 ±0.06 ±0.1
2~4 ±0.15 ±0.25 ±0.35 ±0.06 ±0.08 ±0.12
4~6 ±0.2 ±0.3 ±0.40 ±0.08 ±0.10 ±0.15
2.4.冲裁方案的确定
冲裁工序按工序的组合程度可分为单工序冲裁、复合冲裁和级进冲裁。
复合冲裁是在压力机的一次行程中,在模具的同一位置同时完成两个或两个以上的工序;级进冲裁是把一个冲裁件的几个工序,排列成一定顺序,组成级进模,在压力机的一次行程中,模具的不同位置同时完成两个或两个以上的工序,除最初几次冲程外,每次冲程都可完成一个冲裁件。该工件包括外形落料、中间冲孔两个基本工序,可以有以下三种工艺方案:
方案一:先落料,后冲孔。工序分开,采用单模生产。
方案二:落料和冲孔复合冲压。工序复合,采用复合模生产。
方案三:先冲孔,后落料级进冲压。采用相对复杂的级进模生产。
方案一结构简单,但需两道工序、两副模具才能完成,生产效率也低,如此则浪费了人力、物力、财力,从经济性的角度来考虑不妥当,难以满足大批量的生产要求。
方案二采用倒装复合模生产,与方案一相比,倒装复合模具把凸凹模放在下模,虽然模具结构较方案二简单,可冲工件的孔边距也较大,但是工件的平整性较方案一差。
方案三采用冲孔落料级进模具生产,也只需要一副模具,制造精度高,先冲孔后落料,但是其模具结构复杂,生产周期长,成本高。
通过上述三种方案的分析比较,该工件的冲压生产采用方案二为佳。
第三章、排样图的设计及材料利用率的计算
3.1.排样的设计
冲裁件在板、条等材料上的布置方法称为排样。合理的工序排样,直接影响到材料的经济利用率,还会影响到模具结构设计、生产效率、产品的质量、生产操作是否方便与安全等,因此,排样是冲裁工艺设计与模具结构设计中任何一项都是很重要的工作。
1.结构废料 由于工件结构形状的需要,如工件内孔的存在而产生的废料称为结构废料,它取决于工件的形状,一般不能够改变。
2.工艺废料 工件之间和工件与条料边缘之间存在的搭边,定位需要切去的料边与定位孔,不可避免的料头和料尾废料称为工艺废料,它决定于冲压方式和排样方式。
合理的排样方法,应是将工艺废料减到最少。考虑到该工件的外形特征和材料的利用情况,此采用以上的的排样方式。


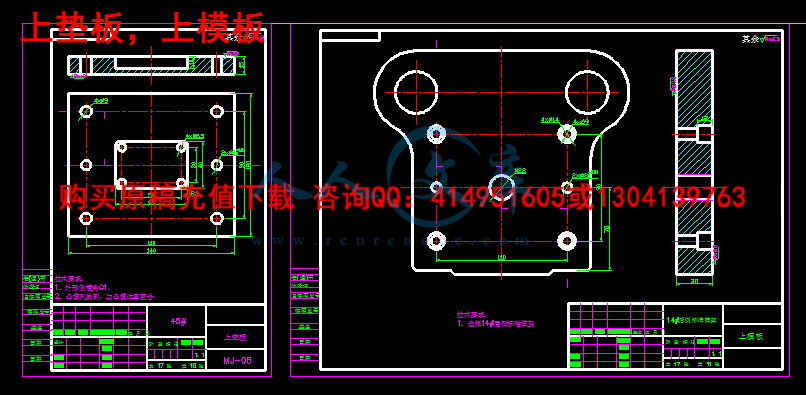






