资源目录
压缩包内文档预览:(预览前20页/共83页)
编号:7130222
类型:共享资源
大小:4.44MB
格式:RAR
上传时间:2018-01-09
上传人:优***
认证信息
个人认证
罗**(实名认证)
广西
IP属地:广西
80
积分
- 关 键 词:
-
收音机
外壳
模具设计
ug
三维
- 资源描述:
-


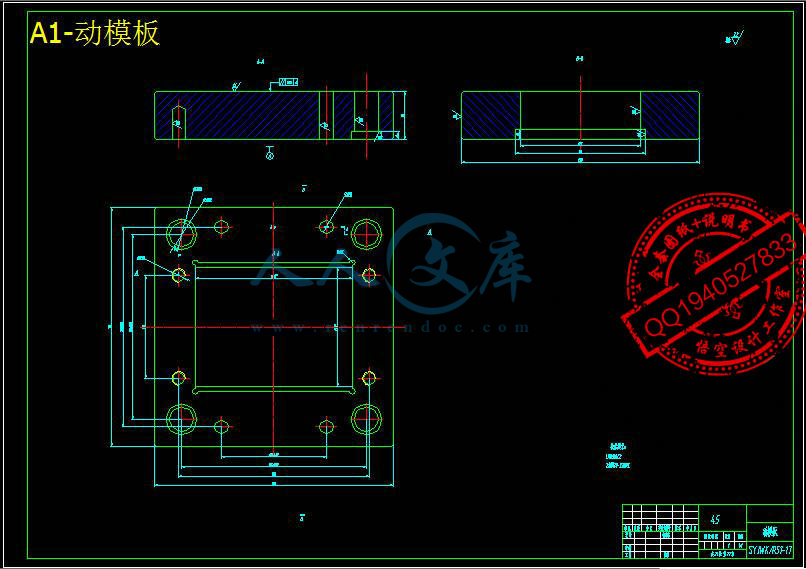


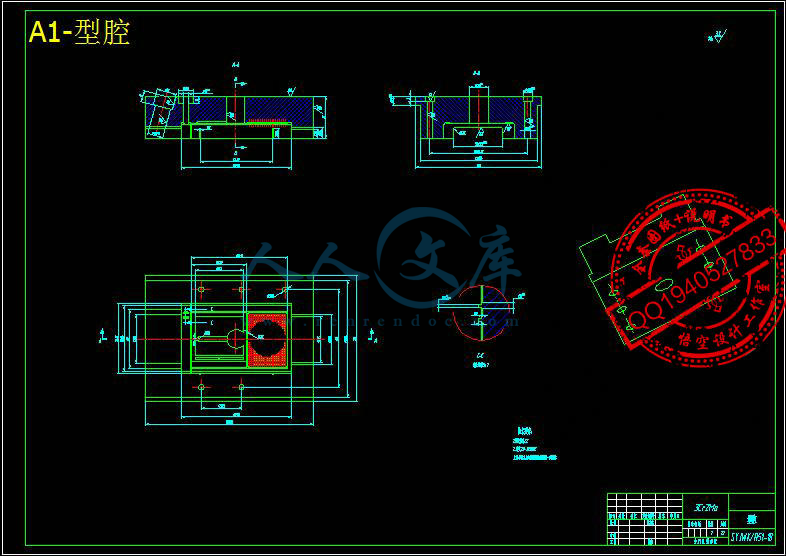













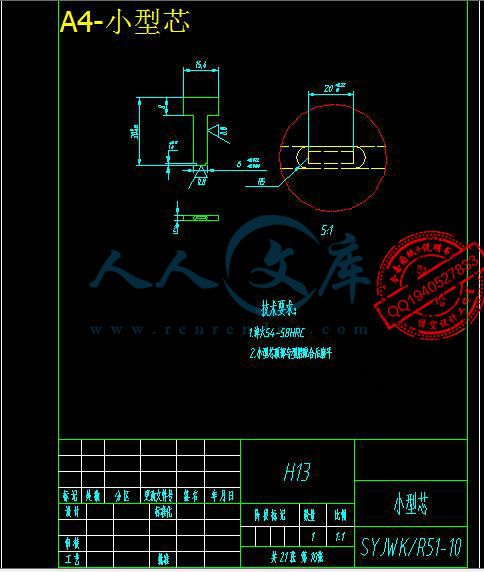





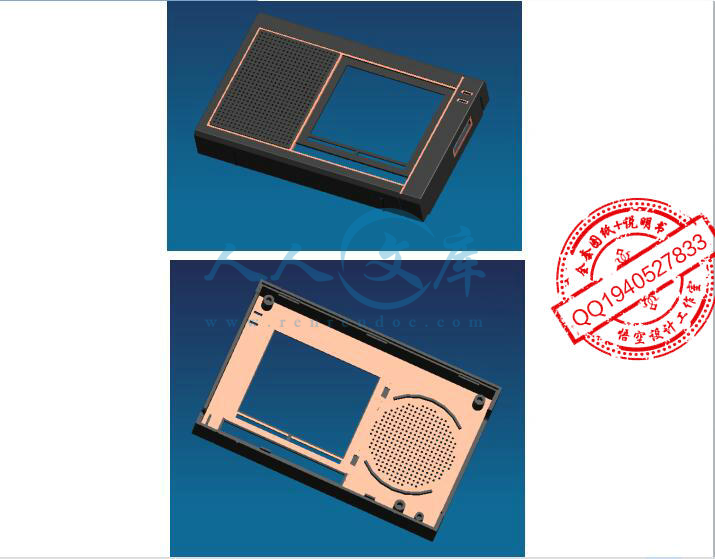
- 内容简介:
-
目录前言1第一章绪论211模具介绍212模具在加工工业中的地位213模具的发展趋势214设计在学习模具专业中的作用4第二章产品三维造型及MOLDFLOW分析521产品三维造型522CAE介绍623CAE分析8第3章塑件材料及工艺性1131材料分析1132工艺分析1133制件的成型方法及参数1134确定型腔数目12第4章浇注系统的设计1341制件在模具中的位置1342确定浇口形式及位置1343主流道的设计1444分流道设计1545冷料穴设计16第5章成型零部件的设计1751成型零部件的结构设计1752成型零部件工作尺寸计算1853成型零部件的强度与刚度计算19第6章结构零部件的设计2061选用标准注射模架2062定模板与动模板的设计2263合模导向机构的设计23第七章推出及抽芯机构的设计2471推出机构设计2472外侧抽芯机构设计2573内侧抽芯机构设计25第八章模具的工作原理29结论31致谢32参考文献33附件外文翻译34前言模具制造业是重要的基础装备,在国家发展中占有重要地位。塑料制品占模具中的80以上,所以对塑料模具进行设计具有重大的意义。设计模具能够综合运用所学的基础理论、基本知识和基本技能,亦检验出自己对模具设计的水平。也为今后工作中设计各种模具奠定良好的基础。本课题来自日常生活中常见的塑料制品。所选课题是高灵敏度收音机的外壳。包含了模具的基本结构,并有侧向分型和抽芯机构,属于中等难度的塑料模具。本设计介绍了注射成型的基本原理,特别是侧向分型与抽芯机构的结构与工作原理,对注塑产品提出了基本的设计原则。还分别介绍了塑料模具的一般设计方法、设计步骤、材料的选取、材料性能、结构和用途的分析等。详细介绍了注射模具的材料及工艺分析,浇注系统、主要零部件、侧向分型与抽芯机构、推出机构、温度调节系统和排气系统的设计过程,并对模具强度要求做了说明,以及模具的各种工艺参数的确定与校核等。亦介绍了模架选取的方法和校核注射机的各种工艺参数等。在模具制造中运用了现代先进的线切割、电火花成型加工和数控加工等加工技术。综合利用三维UG和二维AUTOCAD进行设计并绘制各种非标准零件图纸。在设计中附有大量的模具结构图和各种说明图片。说明书已详细地阐述设计的全过程。此次设计除文字叙述外,其计算公式及相关设计原则等资料均来自教材和图书馆丛书中查取,并采用国家标准。由于水平有限,本设计难免有不当和错误之处,恳请各位老师批评指正第一章绪论11模具介绍模具的作用是控制和限制材料(固态或液态)的流动,使之形成所需要的形体。用模具制造零件以其效率高,产品质量好,材料消耗低,生产成本低而广泛应用于制造业中。模具主要类型有冲模、锻摸、塑料模、压铸模、粉末冶金模、玻璃模、橡胶模、陶瓷模等。除部分冲模以外的上述各种模具都属于腔型模,因为它们一般都是依靠三维的模具型腔是材料成型。其中塑料模约占模具总数的35,分额最大而且有继续上升的趋势。塑料模主要包括压塑模,挤塑模,注射模,此外还有挤出成型模,泡沫塑料的发泡成型模,低发泡注射成型模,吹塑模等。塑料模具是随着塑料工业的发展而发展的。近年来,人们对各种设备和用品轻量化要求越来越高,这就为塑料制品提供了更为广阔的市场。塑料制品要发展,必然要求塑料模具随之发展。汽车、家电、办公用品、工业电器、建筑材料、电子通信等塑料制品主要用户行业近年来都高位运行,发展迅速,塑料模具也快速发展。12模具在加工工业中的地位模具是工业生产中的重要工艺装备,模具工业是国民经济各部门发展的重要基础之一,是国际上公认的关键工业。模具生产技术水平的高低是衡量一个国家产品制造水平高低的重要标志。它在很大程度上决定着产品的质量,效益和新产品的开发能力。模具工业既是高新技术产业的一个组成部分,又是高新技术产业化的重要领域。模具在机械,电子,轻工,汽车,纺织,航空,航天等工业领域里,日益成为使用最广泛的主要工艺装备,它承担了这些工业领域中6090的产品的零件,组件和部件的生产加工。振兴和发展我国的模具工业,正日益受到人们的关注。13模具的发展趋势20世纪80年代开始,发达工业国家的模具工业已从机床工业中分离出来,并发展成为独立的工业部门,其产值已超过机床工业的产值。改革开放以来,我国的模具工业发展也十分迅速。近年来,每年都以15的增长速度快速发展。许多模具企业十分重视技术发展。加大了用于技术进步的投入力度,将技术进步作为企业发展的重要动力。此外,许多科研机构和大专院校也开展了模具技术的研究与开发。模具行业的快速发展是使我国成为世界超级制造大国的重要原因。今后,我国要发展成为世界制造强国,仍将依赖于模具工业的快速发展,成为模具制造强国。4中国塑料模具无论是在数量上,还是在质量、技术和能力等方面都有了很大进步,但与国民经济发展的需求和世界先进水平相比,差距仍很大。一些大型、精密、复杂、长寿命的中高档塑料模具每年仍需大量进口。在总量供不应求的同时,一些低档塑料模具却供过于求,市场竞争激烈,还有一些技术含量不太高的中档塑料模具也有供过于求的趋势。我国塑料模具行业和国外先进水平相比,主要存在的问题1发展不平衡,产品总体水平较低。虽然个别企业的产品已达到或接近国际先进水平,但总体来看,模具的精度、型腔表面的粗糙度、生产周期、寿命等指标与国外先进水平相比尚有较大差距。包括生产方式和企业管理在内的总体水平与国外工业发达国家相比尚有10年以上的差距。2工艺装备落后,组织协调能力差。虽然部分企业经过近几年的技术改造,工艺装备水平已经比较先进,有些三资企业的装备水平也并不落后于国外,但大部分企业的工艺装备仍比较落后。更主要的是我们的企业组织协调能力差,难以整合或调动社会资源为我所用,从而就难以承接比较大的项目。3大多数企业开发能力弱,创新能力明显不足。一方面是技术人员比例低、水平不够高,另一方面是科研开发投入少,更重要的是观念落后,对创新和开发不够重视。模具企业不但要重视模具的开发,同时也要重视产品的创新。4供需矛盾一时还难以解决。近几年,国产塑料模具国内市场满足率一直不足74,其中大型、精密、长寿命模具满足率还要低,估计不足60。同时,工业发达国家的模具正在加速向我国转移,国际采购越来越多,国际市场前景看好。市场需求旺盛,生产发展一时还难以跟上,供不应求的局面还将持续一段时间。5体制和人才问题的解决尚待时日。在社会主义市场经济中,竞争性行业,特别是像模具这样依赖于特殊用户,需单件生产的行业,国有和集体所有制原来的体制和经营机制已显得越来越不适应。人才的数量和素质也跟不上行业的快速发展。虽然各地都在努力解决这两个问题,但要得到较好解决尚待时日。6近几年,原材料、能源、人工等成本持续上升,而模具价格却持续下降,因此模具企业的总体利润率不断下滑。为了发展,模具企业必须在改善管理、提高生产效率,特别是在创新上下功夫才行。从以前的经验型和模仿型设计向自主创新设计方向发展,以及积极采用高新技术已然成为一种趋势。尽管我国模具工业有了长足的进步,部分模具已达到国际先进水平,但无论是数量还是质量仍满足不了国内市场的需要,每年仍需进口10多亿美元的各类大型,精密,复杂模具。与发达国家的模具工业相比,在模具技术上仍有不小的差距。今后,我国第一章绪论3模4具行业应在以下几方面进行不断的技术创新,以缩小与国际先进水平的距离。(1)注重开发大型,精密,复杂模具;随着我国轿车,家电等工业的快速发展,成型零件的大型化和精密化要求越来越高,模具也将日趋大型化和精密化。(2)加强模具标准件的应用;使用模具标准件不但能缩短模具制造周期,降低模具制造成本而且能提高模具的制造质量。因此,模具标准件的应用必将日渐广泛。(3)推广CAD/CAM/CAE技术;模具CAD/CAM/CAE技术是模具技术发展的一个重要里程碑。实践证明,模具CAD/CAM/CAE技术是模具设计制造的发展方向,可显著地提高模具设计制造水平。(4)重视快速模具制造技术,缩短模具制造周期;随着先进制造技术的不断出现,模具的制造水平也在不断地提高,基于快速成形的快速制模技术,高速铣削加工技术,以及自动研磨抛光技术将在模具制造中获得更为广泛的应用。14设计在学习模具专业中的作用通过对模具专业的学习,掌握了常用材料在成型过程中对模具的工艺要求,掌握模具的结构特点及设计计算的方法,以达到能够独立设计一般模具的要求。在模具制造方面,掌握一般机械加工的知识,金属材料的选择和热处理,结合模具结构的特点,根据不同情况选用模具加工新工艺。毕业设计能够对以上各方面的要求加以灵活运用,综合检验大学期间所学的知识。4第二章产品三维造型及MOLDFLOW分析21产品三维造型如图21所示塑料制件,材料为ABS,收缩率0308。大批量生产。收音机外壳作为模具毕业设计产品,目的是通过本产品综合锻炼模具设计与制造的能力。图21塑件三维图422CAE介绍CAECOMPUTERAIDEDEXECUTION技术即计算机辅助工程技术,它是计算机辅助设计/计算机辅助制造CAD/CAM技术向纵深方向发展的要求。注塑成型CAE技术是根据高分子流变学、弹性力学、计算机技术,采用有限元计算方法来模拟整个注塑过程及这一过程对注塑成型产品质量的影响,它可以模拟塑料制品在注塑成型过程中的流动,保压和冷却过程以及预测制品中的应力分布、分子取向、收缩和翘曲变形等,帮助设计人员及早发现问题,及时修改模具设计,提高一次试模成功率,帮助企业缩短产品上市周期,增强市场竞争能力。美国上市公司MUDFLOW公司是专业从事注塑成型CAE软件和咨询公司,MUDFLOW公司是塑料成型分析软件的创造者,自1976年发行了世界上第一套流动分析软件以来,一直主导着塑料成型CAE软件市场。近几年,在汽车、家电、电子通讯、化工、日用品等领域得到了广泛应用。现代注塑成型CAE技术的作用在于1优化塑料制品设计塑件的壁厚、浇口数量、位置及流道系统设计等对于塑料制品的成败和质量关系重大。以往全凭制品设计人员的经验来设计,往往费力、费时,设计出的制品也不尽合理。利用MUDFLOW软件,可以快速地设计出最优的塑料制品。2优化塑料模设计由于塑料制品的多样性、复杂性和设计人员经验的局限性,传统的模具设计往往要经过反复试模、修模才能成功。利用MUDFLOW软件,可以对型腔尺寸、浇口位置及尺寸、流道尺寸、冷却系统等进行优化设计,在计算机上进行试模、修模,可大大提高模具质量,减少试模次数。3优化注塑工艺参数由于经验的局限性,工程技术人员很难精确地设置制品最合理的加工参数,选择合适的塑料材料和确定最优的工艺方案。MODFLOW软件可以帮助程技术人员确定最佳的注射压力、锁模力、模具温度、熔体温度、注射时间、保压压力和保压时间、冷却时间等,以注塑出最佳的塑料制品来近年来,CAE技术在注塑成型领域中的重要性日益增大,采用CAE技术可以全面解决注塑成型过程中出现的问题,由于计算机化的流动分析方法的出现使得更多的产品可以选择注塑成型作为生产的手段,计算机软件技术的进步也不断更新和提高流动分析的模型及其精确程度。CAE分析技术能成功地应用于三组不同的生产过程制品设计、模具设计、注塑成型。1制品设计,制品设计者能用流动分析解决下列问题61)制品能全部注满吗这一古老的问题仍为许多制品设计人员所注目,尤其是大型4制件如盖子、容器、家具等的设计者。2)制件实际最小壁厚是多少如能使用薄壁制件,就能大大降低制件的材料成本。减小壁厚还可大大降低制件的循环时间,从而提高生产效率,降低塑件成本。3)浇口位置合适吗采用CAE分析可使产品设计者在设计时具有充分的选择浇口位置的余地,确保设计的审美特性。2模具设计和制造,CAE分析可在以下诸方面辅助设计者和制造者,以期得到良好的模具设计。1)良好的充填形式对于任何的注塑成型来说,最重要的是控制充填的方式,以使塑件的成型可靠、经济。单向充填是一种好的注塑方式,它可以提高塑件内部分子单向和稳定的取向性。这种填充形式有助于避免因不同的分子取向所导致的翘曲变形。2)最佳浇口位置与浇口数量为了对充填方式进行控制,模具设计者必须选择能够实现这种控制的浇口位置和数量,CAE分析可使设计者有多种浇口位置的选择方案并对其影响做出评价。3)流道系统的优化设计实际的模具设计往往要反复权衡各种因素,尽量使设计方案尽善尽美。通过流动分析,可以帮助设计者设计出压力平衡、温度平衡或者压力、温度均平衡的流道系统,还可对流道内剪切速率和摩擦热进行评估,如此,便可避免材料的降解和型腔内过高的熔体温度。4)冷却系统的优化设计通过分析冷却系统对流动过程的影响,优化冷却管路的布局和工作条件,从而产生均匀的冷却,并由此缩短成型周期,减少产品成型后的内应力。5)减小返修成本提高模具一次试模成功的可能性是CAE分析的一大优点。反复地试模、修模要耗损大量的时间和金钱,此外,未经反复修模的模具,其寿命也较长。3注塑成型,注塑者可望在制件成本、质量和可加工性方面得到CAE技术的帮助。1)更加宽广更加稳定的加工”裕度”流动分析对熔体温度、模具温度和注射速度等主要注塑加工参数提出一个目标趋势,通过流动分析,注塑者便可估定各个加工参数的正确值,并确定其变动范围。会同模具设计者一起,他们可以结合使用更经济的加工设备,设定最佳的模具方案。2)减小塑件应力和翘曲,选择最好的加工参数使塑件残余应力最小。通常残余应力会使塑件在成型后出现翘曲变形,甚至发生失效。3)省料和减少过量充模,流道和型腔的设计采用平衡流动,有助于减少材料的使用和消除因局部过量注射所造成的翘曲变形。4)最小的流道尺寸和回用料成本流动分析有助于选定最佳的流道尺寸。对于注塑第二章产品三维造型及MOLDFLOW分析7者来说,这就意味着减少浇道部分塑料的冷却时间,就能缩短整个注射成型的时间,以及4减少浇道部分塑料的体积。23CAE分析(1)最佳浇口位置分析本文分析的制品为收音机外壳,首先在UG中创建实体模型,保存为IGS格式,再导入到MPIMOLDFLOWPLASTICSINSIGHT中。先用MOLDFLOW软件能根据几何模型自动地生成网格。只需输入模型划分网格的平均边长,系统就能自动地划分。该产品采用FUSION格式进行网格划分,输入平均边长为5MM。网格划分结果如图22所示。选择ABS材料后单击分析,电脑会对塑件的浇口位置进行分析。图23就是生成报告里面的最佳浇口位置的图片。图22网格划分图23最佳浇口分析由图片可以看出适合本塑件模具的最佳浇口应该在蓝色的部位,即中间地带。(2)模拟充填分析1)充填时间它主要通过不同的颜色显示了熔体流动时的形状变化以及充模过程,查看该结果可以知道型腔是否充满,充填过程是否平衡等。图24/25分别表示单浇口和双浇口充填时间的分析结果。图24单浇口充填分析图25双浇口充填分析分别比较单浇口和双浇口的充填时间可以发现单浇口的时间是1130秒,双浇口的充填时间为41275秒。单浇口的时间稍微少了一点。2平均速度单浇口和双浇口的平均速度分别如图26和27图26单浇口平均速度分析图27双浇口平均速度分析通过比较单浇口和双浇口的平均流动速度可以看到单浇口的速度快。但是ABS材料的流动并不均匀,容易导致充填不均匀使塑件达不到成型的效果。3)速度压力切换时的压力单浇口和双浇口的速度压力切换时的压力图分别如图28和29图28单浇口速度压力切换时的压图29双浇口速度压力切换时的压力分析从分析的到得结论以及综合考虑来看采用双浇口的方式更适合此塑件的成型。4)锁模力如图210/211所示图210单浇口锁模力4图211双浇口锁模力采用注射模CAE技术,在模具制造前对塑件的填充和冷却过程进行模拟,并进行翘曲分析,以便及时改进设计方案和工艺方案,从而有效提高了模具的设计效率和质量,降低了试模修模的费用和生产成本。4第3章塑件材料及工艺性31材料分析该产品的成型材料是ABS。基本特性ABS是由丙烯腈、丁二烯、苯乙烯共聚而成的。这三种组分的各自特性,使ABS具有良好的综合力学性能。丙烯腈使ABS有良好的耐化学腐蚀性及表面硬度,丁二烯使ABS坚韧,苯乙烯使它有良好的加工性和染色性能。ABS无毒、无味,呈微黄色,成形的塑料件有较好的光泽。密度为102105G/CM。ABS有极好的抗冲压强度,且在低温下也不迅速下降。有良好的机械强度和一定的耐磨性、耐油性、耐水性、化学稳定性和电气性能。ABS有一定的硬度和尺寸稳定性,易于成型加工。经过调色可配成任何颜色。其缺点是耐热性不高,连续工作温度为70C左右,热变形温度为93C左右。耐气候性差,在紫外线作用下变硬变脆;主要用途ABS广泛用于水表壳、纺织器材、电器零件、文教体育用品、玩具等;成型特点ABS在升温时粘度增高,所以成型压力比较高,塑料上的脱模斜度宜稍大,ABS易吸水,成型加工前应进行干燥处理;易产生熔接痕,模具设计时应注意尽量减少浇口对流道的阻力;在正常的成型条件下,壁厚、熔料温度及收缩率影响极小。要求塑件精度高时,模具温度可控制在5060C,要求塑件光泽和耐用时,应控制在6080C。32工艺分析(1)该塑件尺寸不大,一般精度等级。属于中等难度的塑料模具。包括了模具的基本结构,其中有一处外侧抽芯,内侧抽芯五处(五处内侧抽芯基本尺寸及结构均一致)。(2)为满足制品表面质量要求与提高成型效率采用侧浇口。(3)为了节约成本和方便加工与热处理,型腔和型芯均采用整体镶嵌式结构。(4)ABS在升温时粘度增高,所以成型压力较高,故塑件上的脱模斜度宜稍大,要有足够的脱模斜度防止顶角;ABS易吸水,成型加工前应进行干燥处理;ABS易5。产生熔接痕,模具设计时应注意尽量减少浇注系统对料流的阻力,要注意浇口位置防止和减少熔接痕;在正常的成型条件下,壁厚、熔料温度对收缩率影响极小。模具温度应控制在6080。第三章塑件材料及工艺性1133制件的成型方法及参数热塑性塑料指定采用注射成型,本设计选用热塑性塑料ABS,可用注射成型。4根据制品结构特点及选定的原料ABS,可拟定如下工艺参数)。塑料名称ABS密度(G/CM)102105计算收缩率()05模具温度()5060注射压力(MPA)60100成型时间(S)注射时间1560;加压时间03;冷却时间2090;总周期50160适应注射机类型螺杆式34确定型腔数目(1)计算制品的体积和重量通过三维制图UG软件测量得单件塑件面积S277652单件塑件体积V188373查有关资料可知ABS的密度为102105G/CM3则单件塑件重量约M20G。(2)型腔数目的确定主要参考以下几点来确定1)根据经济性确定型腔数目和总成型加工费用最小的原则,并略准备时间试生产原材料费用,仅考虑模具加工费和塑件成型加工费。2)根据注射机的额定锁模力确定型腔数目。3)根据注射机的最大注射量确定型腔数目,根据经验,每加一个型腔制品尺寸精度要降低4,对于高精度制品,由于多型腔模具难以保证各型腔的成型条件一致,故推荐型腔数目不超过4个。(3)根据本产品的生产批量及尺寸精度要求采用一腔一模由于单型腔模具具有塑料制件的形状和尺寸一致性好,成型工艺条件容易控制,模具结构简单紧凑、制造周期短等特点,并结收音机外壳,所以采用单型腔模具。4第4章浇注系统的设计41制件在模具中的位置(1)型腔的布置主要考虑制件在分型后能保留在动模上以便脱模,并结合制件的结构特征应将型腔设置在定模侧,型芯设置在动模侧。(2)分型面的选择由于分型面受到塑件在模具中的成型位置、浇注系统的设计、塑件结构工艺性及尺寸精度、嵌件的位置、塑件的推出、排气等多种因素的影响,因此在选择分型面时应综合分析,应遵循以下几项的设计则1)分型面应选择在塑件外形最大轮廓处2)分型面的选择应有利于塑件的顺利脱模3)分型面的选择应保证塑件的精度要求4)分型面的选择应满足塑件的外观质量要求5)分型面的选择要便于模具的加工制造6)分型面的选择应有利于排气除了以上这些基本原则以外,分型面的选择还要考虑到型腔在分型面上的投影面积的大小。为了保证侧向型芯的位置的放置及抽芯机构的动作顺利,应以浅的侧向凹孔或短的侧向凸台作为抽芯方向,而将较深的凹孔或较高的凸台放置在开合模方向。综合考虑以上的设计原则并结合该塑件的结构特点和质量要求,应采用阶梯分型面。如图41粗实线所示。图41分型面42确定浇口形式及位置对浇注系统进行设计时,一般应遵循如下基本原则4(1)了解塑料的成型性能(2)尽量避免或减少熔接痕(3)有利于型腔中气体排出(4)防止型芯的变形和嵌件的位移(5)尽量采用较短的流程充满型腔(6)流动距离比和流动面积比的校核为了提高成型效率和综合考虑以上的基本设计原则并结合制件质量要求,本模具应采用侧浇口,由两处浇口进料。浇口位置如图42所示浇口直径可以根据经验公式计算D(014020)4124A式中D浇口直径(MM)塑件在浇口处的壁厚(MM)A型腔的表面积2D(014020)134911MM415浇口直径也可根据经验值取D1MM浇口锥角取0浇口倾斜角取43主流道的设计主流道是连接注射机喷嘴与分流道的一段通道,通常和注射机喷嘴在同一轴线上,断面为圆形,带有一定锥度。1)主流道设计成圆锥型,其锥角为26,内壁粗糙度RA取04UM分流道截面设计成圆型截面,加工容易,且热量损失与压力损失均不大为常用形式。圆形截面分流道的直径可以根据塑料的流动性等因素确定,该塑料件采用ABS塑料,流动性为中等,所以选圆形截面。根具经验分流道的直径可以取D56MM。根据型腔在分型面上的排布情况设置分流道。2)主流道大端成圆角,半径R13MM,以减小料转向过度时的阻力。3)在模具结构允许的情况下,主流道尽可能短,一般小于60MM,过长则会影响流体的顺利充型。4)对于小型模具可将浇口套与定位圈设计成整体式,但在大多数情况下将浇口套与定位圈设计成两个零件,浇口套与定模板采用H7/M6过度配合与定位圈的配合采用H9/F9间隙配合。5)浇口套一般选用T10A制造,热处理强度为5054HRC。根据“常用塑4料直浇口尺寸”表,选主流道始端尺寸D35MM,大端尺寸D4MM,浇口套是标准件基本尺寸为20MM,始端半径R机床喷嘴小经D(051)1005111MM(标准件是15),锥角A3。其长度尺寸根据要求来定。主流道内壁抛光时要沿轴向进行。浇口套与定位圈采用H9/F9的配合。定位圈在模具安装调试时应插入注射机定模板的定位孔内,用于模具与注射机的安装定位。定位圈外径比注射机定模板上的定位孔径小02MM以下。浇口套与模板的配合为H7/M6。图42主流道44分流道设计分流道设计时应注意尽量减少流动过程中的热量损失与压力损失。1)分流道的形状与尺寸分流道的截面尺寸视塑料的品种、塑件是尺寸、成型工艺条件以及流道长短等因素来确定。通常圆形截面分流道直径为210。本制件采用的是ABS,由于ABS的流动性能较好且分流道长度教短时,因此分流道采用圆形截面。初选直径为3,具体尺寸由修模时修正。2)分流道的长度具体尺寸根据型腔的太小而定3)分流道的表面粗糙度由于分流道中与模具接触的外层塑料迅速冷却,只有内部的熔体比较理想,因此分流道的表面粗糙糙不能太低,一般RA取16UM这可增加对外层塑料熔体的流动阻力,使外层塑料冷却皮固定,形成绝热层。4)分流道在分型面的布置形式如图434图43分流道根据以上设计参数校核流动比42/ILT式中流动比距离LI模具中各段料流通道及各段型腔的长度(MM)TI模具中各段料流通道及各段型腔的截面厚度(MM)60/3537/545/52/2140/298MM3因为影响流动比的因素主要是塑料的流动性,ABS塑料的流动性为中等,经查有关资料可知ABS允许的流动比210110,所以45冷料穴设计冷料穴位于主流道正对面的动模板上,或处于分流道末端。其作用是容纳浇注系统流道中料流的前锋的“冷料”,以避免这些冷料注入型腔而影响塑件质量;还有便于在流道处设置主流道拉料杆的功能。开模时又可以将主流道的冷凝料拉出,冷料穴直径宜稍大于主流道大端直径,长度约为主流道大端直径。分流道冷料穴当分流道较长时,可将分流道的尽头沿料流前进方向延长作为分流道冷料穴,以贮存前锋冷料,其长度为分流道直径的152倍。4第5章成型零部件的设计51成型零部件的结构设计由于制件抽芯机构多且复杂,为了便于加工制造,型芯型腔均采用整体镶嵌式,只有型腔有两处镶嵌小型芯。(1)本制件有300个1的小浅通孔和260个1深1孔。由于现代制造技术的先进,那560个孔可以做成电极利用电火花来加工,没有必要分别制造560个小型芯镶件。(2)图51所示外侧通槽和一个凹面均采用斜导柱侧向分型与抽芯机构,把凹槽连大的凹面一起做成滑块成型。图51外抽芯(3)图52所示,五个内侧凹槽,采用常用的内侧抽芯,利用斜顶顶出机构。图52内抽芯(4)图53所示,两个小通槽,分别做成两个小型芯。图53小型芯槽第五章成型零部件的设计1752成型零部件工作尺寸计算(1)由于成型零件直接与高温高压的塑料熔体接触,它必须有以一些性能1)必须具有足够的强度、刚度,以承受塑料熔体的高压;2)有足够的硬度和耐磨性,以承受料流的摩擦和磨损。通常进行热处理,使其硬度达到HRC40以上;3)对于会产生腐浊性气体的塑料还应选择耐腐浊的合金钢理;4)材料的抛光性能好,表面应该光滑美观;5)切削加工性能好,热处理变形小,可淬性良好;6)熔焊性能要好,以便修理;7)成型部位应须有足够的尺寸精度。孔类零件为H8H10,轴类零件为H7H10。(2)型腔、型芯工作部位尺寸的确定经查有关资料可知ABS塑料的收缩率是0308平均收缩率为S(0308)/2055型腔工作部位的尺寸型腔径向尺寸51001ZZMSLSL型腔深度尺寸52H型芯径向尺寸53ZZSLL型芯高度尺寸5400MHH中心距尺寸55/21/2ZSZCSC式中L塑件外型径向基本尺寸的最大尺寸(MM)L塑件内型径向基本尺寸的最小尺寸(MM)H塑件外型高度基本尺寸的最大尺寸(MM)H塑件内型径向基本尺寸的最小尺寸(MM)C塑件中心距基本尺寸的平均尺寸(MM)X修正系数,取05075塑件公差(MM)模具制造公差,取(1/31/4)。各工作部位尺寸计算结果详见相应零件图纸所标明4通常,制品中1MM和小于1MM并带有大于005MM公差的部位以及2MM和小于2MM并带有大于01MM公差的部位不需要进行收缩率计算。53成型零部件的强度与刚度计算为了方便加工和热处理,其型芯整体镶嵌式,型腔为整体形式。因此,型腔的强度和刚度按型腔整体式计算。由于型腔壁厚计算比较烦,也可参考经验推荐数据。经查有关资料可知型腔侧壁厚S25MM。支承板厚度计算可以经过AUTOCAD的燕秀工具箱承板厚度计算器来计算。4第6章结构零部件的设计61选用标准注射模架(1)初选注射机1)注射量该塑料制件单件重量M148G浇注系统重量的计算可以根据浇注系统尺寸先计算浇注系统的体积V36013CM粗略计算浇注系统重量为360110535G61JJV总体积V塑件(188363601)22437623C总重量M2243710524G63聚苯乙烯的密度为1054G/CM3,ABS的密度为102105G/3CM满足注射量V机V塑件/080式中V机额定注射量()3CMV塑件塑件与浇注系统凝料体积和()3C280564243708塑件3或满足注射量M机M塑件12/08式中M机额定注射量(G)M塑件塑件与浇注系统凝料的重量和(G)聚苯乙烯的密度(G/CM3)1塑件采用塑料的密度(G/CM3)2G651405298608塑件2)注射压力P注P成型经查有关资料可知ABS塑料成型时的注射压力P成型7090MPA3)锁模力P锁模力PF式中P塑料成型时型腔的压力,ABS塑料的型腔压力P30MPAF浇注系统和塑件在分型面上的投影面积和()2M各型腔及浇注系统及各型腔在分型面上的投影面积F818752MPF3081875245625KN4根据以上的分析、计算,查教材第79页表51初选注射机型号为XSZY125,其有关技术参数如下额定注射容量(CM)104106125螺杆直径(MM)304542注射压力(MPA)150注射行程()160注射方式螺杆式合模力(KN)9105拉杆空间(MM)260360注射行程(MM)160最大模板厚度(MM)300最小模具厚度(MM)200喷嘴圆弧半径(MM)12喷嘴孔直径(MM)4最大开合模行程(MM)300动、定模板尺寸(MM)250280定位圈尺寸(MM)100(2)选标准模架根据以上分析、计算以及型腔尺寸及位置可确定模架的结构形式和规格。通过调用AUTOCAD的燕秀工具箱模架选用,如图61所示定模板厚度A45动模板厚度B50垫块厚度C80模具厚度H模245模具外形尺寸3002502504图61标准模架62定模板与动模板的设计本模具的模架是燕秀工具箱调出拉,已经设计好动定各模板的相关参数。如图62所示。图62图62动定模板的选取463合模导向机构的设计1为了使导柱能顺利地进入导套,导柱端部应做成锥形或半球形,导套的前端也应倒角。2导柱设在动模一侧可以保护型芯不受损伤,而设在定模一侧则便于顺利脱模取出塑件,因此可根据需要而决定装配方式。3一般导柱滑动部分的配合形式按H8/F8,导柱和导套固定部分配合按H7/K6,导套外径的配合按H7/K6。4除了动模、定模之间设导柱、导套外,一般还在动模座板与推板之间设置导柱和导套,以保证推出机构的正常运动。5导柱的直径应根据模具大小而定,可参考标准模架数据选取。一次分型导向机构设计导柱固定在固定模板上,与固定模板为H7/M6的过渡配合。导柱直径参考标准,取D12MM,导柱头部做成半圆形。导柱长度与主流导长度点浇口长度以及塑件长度等有关。第六章结构零部件的设计23第七章推出及抽芯机构的设计71推出机构设计注射成型每一循环中,塑件必须准确无误的从模具的凹模中或型芯上脱出,完成模具脱模。脱模机构设计应遵循下述原则1)塑件滞留于动模边,以便借助于开模力驱动脱模装置,完成脱模动作,致使模具结构简单。2)防止塑件结构变形或损坏,正确分析塑件对模腔的粘附力的大小及所部位,有针对性的选择合适的脱模装置,使推出重心与脱模阻力中心相重合。由于塑件收缩时包紧型芯,因此推出力作用点应尽量靠近型芯,同时推出力应施于塑件刚性和强度最大部位,作用面积也尽可能大一些,以防塑件变形或损坏。3)由于塑件收缩时包紧型芯,因此推出力作用点应尽量靠近型芯,同时推出力应施于塑件刚性和强度最大部位,作用面积也尽可能大一些,以防塑件变形或损坏。4)力求良好的塑件外观,在选择顶相互位置时,应尽量设在塑件内部或对塑件影响不大的部位。在采用推杆脱模时,尤其要注意这个问题。结构合理可靠,脱模结构应工作可靠,运动灵活,制造方便,更换容易,且有足够的强度和刚度。4根据制件的形状,本模具可才用顶杆顶出。复位杆长度尺寸L4L顶杆固定板L支撑板L型芯板1007115354040130MM复位杆径向尺寸参考标准见尺寸,取D15MM。推出结构的设计(1)推件力的计算推件力721COSINTFAPQA式中A塑件包络型芯的面积()2M塑件对型芯单位面积上的包紧力,P取0810712107PA脱模斜度大气压力009MPAQ塑件对钢的檫系数,约为0103;制件垂直于脱模方向的投影面积()1A2M查教材第70页可知道ABS的脱模斜度40,A10352M10351002COSSIN/0091715TF710,61116KN(2)确定顶出方式及顶杆位置根据制品的结构特点,确定在制品的四角上设置六根普通的圆顶杆。普通的圆形顶杆按GB41691984选用,均可满足顶杆刚度要求。经查相关资料,选用31555型号的圆型顶杆7根。由于塑件不大,推出装置可不设导向装置。72外侧抽芯机构设计外侧抽芯机构设计采用斜导柱侧向分型与抽芯机构,把两个凹槽连大的凹面一起做成成型滑块。(1)计算斜导柱倾斜角斜导柱倾斜角是决定斜导柱抽芯机构中工作效果的重要参数,大小对斜导柱的有效工作长度、抽芯距、受力状况等有直接影响。最常用的是。本模具12。采用中间值,则楔紧块的楔紧角。15。2,。3。(2)计算斜导柱直径D4由于计算比较复杂,为了方便,用查表的方法来确定斜导柱的直径。先按已经求得的抽拨力和选定的斜导柱倾斜角在教材第206页表91查出最大的弯曲力,CFWF然后根据和以及斜导柱倾斜角在表92中查出斜导柱直径D16。WH(3)计算斜导柱长度由燕秀工具箱计算斜导柱参数,如图71所示,具体尺寸详见零件图。图71斜导柱73内侧抽芯机构设计内侧抽芯机构由斜顶顶出。如图72所示,抽芯滑块具体尺寸详见零件图。4图72内抽芯机构4图73模具设计标准4第八章模具的工作原理收音机外壳模具(图81/82)工作原理注射结束开模时,动模一侧开始运动,滑块沿着斜导柱方向移动,一方面滑块跟随动模有向下的运动,一方面向左移动就使外抽芯开始向外抽动。当外抽芯完全抽出时候斜导柱下端离开动模板。此时,限位钉由弹簧顶到滑块上的限位钉槽,从而使滑块停止运动固定在动模板上,这个过程中拉料杆拉出滞留在流道中的废料。此过程结束后,推板开始推动推杆固定板运动,一方面5个内抽芯推杆推动推块,推块通过固定在上面的斜导杆沿导滑槽做斜向运动,斜导杆抽出内抽芯,同时斜导杆和另外5个推杆一起推出塑料件。待塑件推出时取出废料。合模时,动模一侧向定模运动,同时复位杆上的弹簧推动支撑板及动模板运动,型芯和型腔开始合模,型腔上面的推杆推动滑块,滑块拉动斜导杆复位。同时,斜导柱使滑块完成复位。整个合模过程完成,为下一次注射做好准备。图81主视图4图82左视图1动模座板2推板3内六角圆柱头螺钉4推杆固定板5垫板6推杆7支撑板8限位钉9水嘴10滑块11锲紧块12斜导柱13定模座板14小型芯15定位圈16内六角圆柱头螺钉17浇口套18防转销19冷却水管道20导套21导柱22推杆23拉料杆24推杆25长螺钉26型芯27动模板28型腔29定模板130内六角圆柱头螺钉31复位杆32斜导杆33推块34复位杆35弹簧4结论通过对收音机外壳成型模具的设计,对常用塑料在成型过程中对模具的工艺要求有了更深一层的理解,掌握了塑料成型模具的结构特点及设计计算方法,对独立设计模具具有了一次新的锻炼。在设计过程充分利用了各种可以利用的方式,浇口的位置设置时使用了MOLDFLOW对浇口的最佳位置进行了分析,并且分析了制件可能出现的缺陷如气泡、融接痕的位置及数量及填充质量。同时在反复的思考中不断深化对各种理论知识的理解,在装配的后阶段充分利用AUTOCAD的外挂燕绣工具箱,快速调出模架,及标准件,新的工具的利用,大大提高了工作效率。以计算机为手段,专用模具分析设计软件为工具设计模具。软件可直接调用数据库中模架尺寸,金属材料数据库及加工参数,通过几何造型及图形变换可得到模板及模腔与型芯形状尺寸迅速完成模具设计。模具CAD技术是模具传统设计方式的革命,大大提高了设计效率,尤其是系列化或类似注射模具设计效率更为提高。这次设计发现自己对模具设的流程已经清楚但对于细节的东西还是没有掌握经常要查参考资料大大的影响了设计速度。总之,通过毕业设计的又一次锻炼完全清楚充分利用CAD技术进行设计,在模具符合使要求的前提下尽量降低成本。同时在实际中不断的积累经验,以设计出价廉物美的模具。4致谢本次毕业设计是在某老师的精心指导和帮助下完成的。在毕业设计的过程中,我学到了非常多的东西,不仅仅是模具方面的专业知识,还有黄老师的敬业和职业道德以及对学生工作一丝不苟的精神。同时,我还得到了刘好老师的热心帮助和指导,在这一并表示感谢。另外,我要向大学四年来一直关心和支持我学习的领导、同学和朋友们表示衷心的感谢这次设计能顺利完成,得感谢某老师的精心指导及对模具结构优化提出了宝贵的意见。如果有不到不完善之处望批评指正。非常感激4参考文献1屈华昌主编塑料成型工艺与模具设计M北京高等教育出版社,20052李学峰主编塑料模具设计与制造M北京机械工业出版社,20033申开智主编塑料模具设计与制造M北京化学工业出版社,20064编写组编塑料模设计手册S北京机械工业出版社,20045温建民编PROENGINEER2003三维造型基础教程M北京机械工业出版社,20046陈立亮主编材料加工CAD/CAE/CAM技术基础M北京机械工业出版社,20077廖念钊主编互换性与测量技术基础M北京中国计量出版社,20068张甲敏等尼龙1010注塑制品工艺设计J塑料工业,2006年第9期9付秀娟等基于CAE分析的底座注射模设计J模具工业,2007年第5期10李林海等电池盒注射模设计J模具制造,2007年第1期11花杏华基于PRO/E的杯座注射模设计J模具制造,2007年第10期4附件外文翻译快速模具制造技术的发展摘要快速成形与制造()作为诞生仅十余年的先进制造技术,已成功地实现了快速原型制造,目前正向快速模具制造()方向迅速发展。主要介绍了快速制模尤其是快速金属模具制造()技术的现状和发展趋势,分析了模具快速制造的特点和问题,探讨了快速模具制造技术发展面临的关键问题及其应用前景。关键词快速成形RMT技术快速模具RT技术近年来,制造业市场的制造战略重点正在发生从成本与质量到时间与响应的重大转移。快速将多样化的产品推向市场是制造商把握市场先机而求生存的重要保障,快速响应制造已成为国际研究的热点,应运而生的快速成形/快速制模/快速制造技术为企业提高竞争力提供了一种先进的手段,逐渐成为业界的焦点。据有关媒体报道,传统制造业的战略是规模效益第一,二十世纪八十年代提出价格和质量第一,九十年代以来,已发展为市场响应第一。在制造业日趋国际化的状况下,缩短产品开发周期和减少开发新产品投资风险,成为企业赖以生存的关键。快速成形/快速制模/快速制造技术是基于材料累加成形的一种高新制造技术,被认为是20世纪制造领域的一次革命性突破,可制造注塑模、压铸模、冲压模等各类精密复杂模具,目前已广范应用于汽车、航空航天、船舶、家电、工业设计、医疗、建筑、工艺品制作以及儿童玩具等领域,并且随着这一技术本身的不断发展和完善,其应用范围将不断拓广。在汽车、家电制造业中,模具成形零件占到了制造工时的5070。模具制造是制约我国汽车、家电、轻工等行业发展的瓶颈和关键,随着快速成型软硬件设备与快速成型材料的不断发展和完善,快速原型件的强度和精度得到不断的提高,快速成型技术已经逐渐地深入到快速模具制造领域,基于快速成型方法制造各类简易经济快速模具已成为RPM应用的热点问题。一、模具快速制造4虽然快速成形技术问世时间不长,但由于它对制造业带来的巨一技术的应用日益广泛,特别是给模具的设计与制造带来了一次飞跃。快速原型技术可精确制作模具的型心和型腔,也可直接用于注射过程制作塑料样件,以便发现和纠正出现的错误。由于快速原型制造这一新技术的应用,使模具的设计与制造逐步趋向于数字化、快速化,使模具制造在缩短周期,降低成本的进程中,大大前进了一步。快速制模技术大都是依据快速成型制作的实体模型即样模母模采用拷贝方式如金属喷涂、电镀、复合材料浇注、精铸等来快速制造模具主要工作零件凸、凹模或模腔、模芯的,其制造周期一般为传统的数控切削方法的1/51/10,而成本却仅为其1/31/5。根据模具材料、生产成本、RP原型的材料、生产批量、模具的精度要求已开发出多种多样的工艺方法。目前的快速制模方法大致有间接制模法和直接制模法,基于RP快速制造模具的方法多为间接制模法。依据材质不同,间接制模法生产出来的模具有软模、桥模和硬模。软模SOFTTOOLING通常指的是硅橡胶模具。用SLA、FDM、LOM或SLS等技术制作的原型,再翻成硅橡胶模具后,向模中灌注双组份的聚氨酯,固化后即得到所需的零件。桥模BRIDGETOOLING通常指的是可直接进行注塑生产的环氧树脂模具。采用环氧树脂模具与传统注塑模具相比,成本只有传统方法的几分之一,生产周期也大大减少。模具寿命不及钢模,但比硅胶模高,可达10005000件,可满足中小批量生产的需要。硬模HARDTOOLING通常指的就是钢质模具,即用间接方式制造金属模具和用快速成形直接加工金属模具。企业间的竞争日益加剧,产品开发周期要求越来越短,为快速制模技术提供了发展机遇和发展空间。随着工业化生产的发展,快速制模技术越来越受到产品开发商和模具界广泛重视,对其研究正方兴未艾,新的技术成果不断涌现,呈现出生机勃勃的发展趋势,有着强大的生命力。二、注塑模快速制造技术金属喷涂制模法1、金属喷涂制模法简介金属喷涂制模法是将快速原型与热喷涂、快速凝固等方法相结合的间接制模法,其工艺是将熔融或半熔融的金属颗粒喷射到通过SLA、SLS或LOM方法制造的原型上,生成金属薄层,然后补强背衬并除去原型后得到模具产品。目前有两种形式,即雾化外文翻译35喷射4法(快速凝固工艺RSP)、喷涂法。当模具要求的寿命在3000件以下时,一般采用以原型作母模,将低熔点的熔化金属(如锌铝合金)充分雾化后以一定的速度喷射到母模的表面,形成模具型腔表面,充填背衬复合材料,制作锌铝合金软模具。金属喷涂制模法以样模为标准,模具型腔尺寸、几何精度完全取决于样模,型腔表面及其精细花纹一次同时形成,故制模速度快,制造周期短,模具寿命长,成本低,仅为数控法加工钢模的1/31/5。模具表面光洁度好,工艺简单,设备要求低,比较适合于注射成型模、压铸模、板料压延模的快速制造。2、金属喷涂制模法工序金属喷涂制模的工序大致可分为五个步骤(1)模型准备模型可由许多材料制成,包括塑料、石膏、橡胶、木材等。首先建立三维模型,然后对其进行分层切片,并由快速成型机制作出样模。模型准备中最重要的是清理模型表面和涂抹脱模剂。(2)金属喷涂模型脱模剂干燥后,选择最佳的喷涂参数,即可开始在模具上喷涂金属,喷涂时应保证使喷枪连续运动,防止涂层过热变形,涂层厚度一般可控制在23MM。(3)制作模具框架如果模具在工作中要受到内压力或模具必须安装在成型机上工作,模具必须有骨架结构且制成的骨架应带有填料。(4)浇注模具的填充材料应使填充材料具有较高的热导率和较低的凝固收缩率以及较高的抗压强度和耐磨性能。一般选择的填充材料为环氧树脂与铝粉、铝颗粒等金属粉末的混合物。(5)脱模及模具型腔表面抛光处理脱模后要把残留在金属涂层表面的脱模剂清洗干净,然后再根据不同的需要,对模4具进行抛光等后期制作。(6)组装试模3、喷涂设备与喷涂材料金属电弧喷涂工作系统一般由喷涂电源、送丝机构、喷枪和压缩气体等系统组成。XDP5型电弧喷涂设备工作稳定可靠,使用维护方便,能胜任繁重的喷涂工作,其基本参数为电源电压380V额定输入容量12KVA额定电流300A压缩空气使用压力06MPA压缩空气消耗量162M3/MIN送丝速度048M/MIN用于电弧喷涂制模的材料,在满足低熔点、低收缩率的情况下,应尽可能具有较好的力学性能和较致密的涂层组织。目前市场提供的电弧喷涂用丝材有铝、锌、铜、镍、不锈钢、铝青铜、巴氏合金、复合丝等许多品种。但高熔点金属,如钢、镍、铜等在喷涂时涂层收缩率、热应力、孔隙率都比较大,涂层易开裂、翘曲、剥落,所以目前只有低熔点的锌、铝丝材适合用于模具制造。三、金属喷涂快速制造注塑模技术的应用范例与发展金属喷涂方法制
- 温馨提示:
1: 本站所有资源如无特殊说明,都需要本地电脑安装OFFICE2007和PDF阅读器。图纸软件为CAD,CAXA,PROE,UG,SolidWorks等.压缩文件请下载最新的WinRAR软件解压。
2: 本站的文档不包含任何第三方提供的附件图纸等,如果需要附件,请联系上传者。文件的所有权益归上传用户所有。
3.本站RAR压缩包中若带图纸,网页内容里面会有图纸预览,若没有图纸预览就没有图纸。
4. 未经权益所有人同意不得将文件中的内容挪作商业或盈利用途。
5. 人人文库网仅提供信息存储空间,仅对用户上传内容的表现方式做保护处理,对用户上传分享的文档内容本身不做任何修改或编辑,并不能对任何下载内容负责。
6. 下载文件中如有侵权或不适当内容,请与我们联系,我们立即纠正。
7. 本站不保证下载资源的准确性、安全性和完整性, 同时也不承担用户因使用这些下载资源对自己和他人造成任何形式的伤害或损失。

人人文库网所有资源均是用户自行上传分享,仅供网友学习交流,未经上传用户书面授权,请勿作他用。