资源目录
压缩包内文档预览:(预览前20页/共54页)
编号:830925
类型:共享资源
大小:29.99MB
格式:ZIP
上传时间:2016-10-08
上传人:牛***
认证信息
个人认证
霍**(实名认证)
辽宁
IP属地:辽宁
30
积分
- 关 键 词:
-
wj066
轻型
卸车
整体
总体
设计
- 资源描述:
-
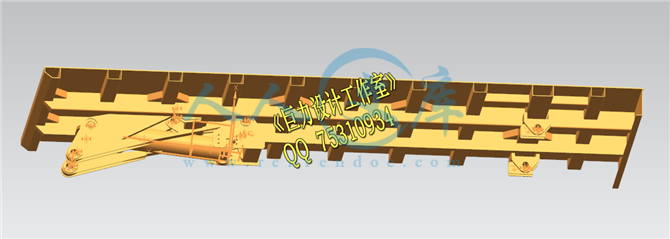








- 内容简介:
-
设计的轻量级复合材料汽车身体使用新材料性能指数和防撞性薄壁梁的材料选择的考虑 崔鑫涛 , 张宏伟 , 王舒新 , 张连宏 , 天津一汽夏利汽车股份有限公司 ,天津 300190 天津大学机械工程学院 ,天津 300072 工业和管理系统工程系 ,布拉斯加 林肯 ,美国东北 68588 文摘 目前 ,汽车的身体构造通常使用一个单一的材料 ,如钢或铝。 但是,相比于单一材料的车身而言,采用复合材料的车身可以允许 最优材料在每个结构组件选择更高的产品性能和更低的成本。 研究报告 提出 的 新材料性能指标和程序开发指导系统 可以对复合材料车身的材料选择提供依据。 这些新指数可以描述薄壁梁性能 ,以防产生弧垂 。所以复合材料车身的体内设计得根据材料类型而定。 本文还说明了这些性能指标的应用程序和程序设计 就可以设计 一个轻量级 复合 汽车车身。这些程序将有助于设计一个轻量级的 车身,以至于完全可以得到 汽车工业的青睐 ,从而减少燃料消耗和温室气体 的 排放。 汽车减重被认为是一个最重要的解决方案来提高燃油经济性和减少有害排放。近年来 ,由于汽车数量的急剧增加而使得过多的 油耗和污染 引起的担忧 的越来越多 , 汽车行业 也因此承受了 巨大的压力减少燃料消耗和排放 方面 。 这些问题的一个解决方案是降低车辆的重量 , ,因为 每 减少 57 公斤 车 重相当于每公升油耗增加 行程 。 这些减少是至关重要的特别是在最近这比较敏感的时间里。 由于燃料成本上升 ,对气候的担忧 也 正在增 多 。 人们认为汽车 可以通过使用复合材料去减重而不需要担心它会增加成本。有很多 轻型汽车的车 身已经开发使用高强度钢 ,铝合金和复合材料。这些特殊的材料可以提供更轻的车身重量。然而 ,这些特殊材料的高价格 却成为 它们 取代钢材 的 一个主要障碍。因此 ,一些研究 人员 认为复合 车身是解决这些问题的办法。 此外,除了他们的宏观意义,材料车身总成的性能指标还可以解决 单一材料 车身性能方面的问题。 基于多材料车身优化设计需对新材料特性进行研究,以确定结构复杂的车身部件使用多材料后优劣。多材料应用指在合适的部位应用合适的材料实现产品功能。大量的研究材料选择方法已经被提出来。 一般来说, 材料 的 选择问题 是需要进行广泛的研究的。为此,有很多专著是专门提供材料选择及其过程的。材料选择的基础知识还作为了介绍同步工程的背景的角色。车身平衡梁的结构优化是要考虑到环境因素和材料本身性质的材料选择。 一些研究提出了材料刚性和轻型汽车车身总成的性能指标。这些研究可以 调查材料的减重与刚度常数替换。然而 ,对于更全面的绩效评估 ,进一步的研究需要考虑 其他方面的车身性能如防撞性和材料成本。 本文 提出了新颖的性能指标和程序为轻量级的和具有成本效益的 复合 汽车机构材料 的 选择。 2. 防撞性设计性能指标 本节介绍了薄壁结构件的材料性能指标有一 般截面最优材料选择考虑防撞性。在这项研究中 ,给出了 组件的拓扑结构 ,在材料的选择过程中材料厚度是可以改变的 。 压碎负荷 在本节中一个通用的公式表达 薄壁梁结构的平均压缩载荷 。 位于驾驶室较远距离的前面部分,是压缩载荷组件的位置,用于吸收碰撞能量 。平均压碎负荷是一个被广泛 被 接受的设计参数用来评估薄壁结构组件吸收碰撞能量的能力。 义为能量吸收变形长度的比率。 在分析以及实验研究 中 19, 20和 21,平均 压缩载 荷的公式 是基于简化的薄壁梁结构建立的,包含了 组件几何参数和材料性能。 9提出了 矩形 架平均压缩载荷 方程 (1) )0 . 3 2= 3 2 6 8 (1) f 4 是完全塑性的时刻 , 流动压力 ,B=(C+D)/ 2 中, C 和 D 是一个 矩形框柱的长度 ,t 是壁厚 。 et 圆管 实验 20开发了一个轴向负荷公式 方程 (2) )0 . 3 2= 3 2 f 6 (2) D 是管 直径 , t 是管 平均 厚度。 表达式意味着压碎载荷的上流部分的结构 21。 方程 (3) )1 / 3= 3 f (3) t 壁厚 ,L=2w+2h+4f。 h,w 和 f 分别是截面载荷 的高度 ,截面载荷的宽度和 凸缘 的 宽度 。 可以观察到在上面的公式中 ,如果 是 拓扑 形状的薄壁梁 ,平均负荷 以表示为一个函数的平均流压力和壁厚 , 一个常数 , t 是壁厚。 一般来说 ,塑性变形能量取决于 塑性 拉伸 ( )或 塑性 弯曲 ( )。 b 横截面的宽度。 此外 ,当薄壁结构在 塑性 拉伸载荷和弯矩 作用下的时候 ,平均负载 以表示为 21方程 (4) (4) 指数在 1 和 2 之间的差异。 可以观察到在上面的公式中 ,如果是拓扑 形状的薄壁梁 ,平均负荷 以表示为一个函数的平均流压力和壁厚 方程 (5) f (5) C 是一个常数 ,f 是 平均流动应力 , t 是壁厚 。 平均流动应力 22 方程 (6) f =(Y +U )/2 (6) Y 和 U 分别是产量和极限应力。 评价材料的薄壁结构指数 在本节中 ,提出了材料平均压缩载荷评价指标 ,及其 计算过程。考虑 到 两个组件 (梁 )由两种不同的材料但是 其 形状 相同, 让下标 “1”表示 两种材料的参考材料和 下标 “2”的材料 为 设计 考虑使用材料 。如果两个组件具有相同的平均 压缩载荷, 然后 根据公式 方程 (7) 1 / Q (7) 薄壁梁的质量 方程 (8) m=8) 用 公式 5 取代 公式 8 中的 t。 ,薄壁梁的质量由 总坡度 ,材料属性和几何参数 m表示。预定义的梁几何 总坡度 ( C)1 / Q 在 常数。因此 ,适当的 (轻量级 )材料是那些小 q= q 的 。换句话说 ,大量的材料性能指标定义在低于 范围 将更适合 Mc指数 q 性能指标 的 计算。注意指数 Q 在方程式 中 ,不能纯粹的 用 分析方法计算 。这是因为 非线性薄壁复杂的几何图形。因此 ,有限元 (拟可以用来获得平均压碎载荷 F,它可 以迭代计算和 对 有限元分析 进行 帮助。 公式 两边的 两种不同的厚度值 但具有 同样的材料 ,因此 ,估计误差引起的均压碎负荷误差图 1 显示了一个示例 由 估计误差引起的 5%的误差平均压碎负荷评估。当 t 的值 是 意味着压碎 负荷 从简单的有限元计算软件使用 变成了 计算机辅助设计(数据。 方程 (9) m=(1/(9) 一个预定义 薄壁梁 和 压碎载荷的公式 , ()1/Q 。 (9)是常数。 因此 ,适当的 (轻量级 )材料具有较小的值 /1/1/ 。 (9)。 换句话说 ,复合 材料性能指标定义在E(10)下面将会更合适。 方程 (10) 1/(10) 指数性能指标可以计算如下。 注意 ,该指数在方程式 (5)和 (10)不能由一个纯粹的分析方法计算由于非线性薄壁复杂的几何图形。 因此 ,有限元 (拟可以用来获得平均负载 F,在此帮 助下可以计算迭代有限元分析。 方程 (11) m)=f)+t) (11) (11)两个不同的厚度值 t 和 t 和同样的材料 ,可以表示为 方程 (12) Q=m)m)t)t)=m/Fm)t/t) (12) (12)对两个厚度的各种组合 ,可以作为和平均值估计。 值得 注意的 是 准确数值计算取决于平均压碎负荷从有限元模拟和准确性 t /t 比率。 此外 ,更大的区别 t 和t 如下描述。 假设有一个薄壁梁它的 破碎力 和厚度是 t 。 方程 (13) Q=Fm+Fm)/Fm)lg(t/t)=1+Fm/Fm)(Fm/Fm)lg(t/t)=+Fm/Fm)lg(t/t)+m/Fm)lg(t/t)=+Fm/Fm)lg(t/t)+Q (13) 因此 ,估计误差均压碎负荷误差造成的 Fm 是 +Fm/Fm)lg(t/t)+F/F)lg(t/t)。图 1显示的一个例子 , 估计误差引起的 5%的误差平均压碎负荷评估。 时 值 t/ tt/t是 时的值 t/ tt/t是 差降低到 图 1。 估计偏差引起的误差为 5% 3 应用程序的单个组件的材料选择的性能指标 本节描述如何将性能指标 用于确定单个组件的材料。 考虑刚度 一般来说 ,薄壁结构的刚度设计性能指标可以被定义为 中 E 是弹性模量。梁刚度的性能指标根据设计目的 可 分为三类 , 指数派生组件用简单的几何图形基于经典弹性梁理论。对 于复杂的结构如汽车车身配件 可 以 用 值 1、 2 或 3 来表示 。 方程 (14) 1/E1/2/E1/14) m 是质量 ,下标 1和 2表示两种材料。 图 2 显示了相同刚度 的钢制梁 和铝 制梁的质量比 。 它们的 材料特性 可以 参考表 1。它可以观察到由铝代替钢 减重 的效果对不同的 q 值是不同的。 对于 一个 比较 大的 q 而言 ,铝可以提供显著的减重。 而对于比较 小 的 q 值 , 铝会导致 较小的减重 。 图 2。 表 1 材料属性 材料 弹性模量 密度 价格 y 07 7840 80 300双铝 207 7840 10 500铝6 0 6 3 207 7840 50 800铝6 0 1 0 70 2720 0 压碎负荷的意义考虑与分析 方程 (15) 1/E1/1/15) 图 3 显示了由可硬化的 (强度钢和铝合金 6063 制成的 梁 的 压碎负荷。这些材料都是表1中给出的属性。有趣的是看到从图 3 值增加 ,而铝梁的质量下降。对于一个比较大的 q,铝似乎 是一个更好的选择 ,因为它可以实现更大的减重。 较 小 的 q 值 ,高 强度钢材可以优先考虑 ,因为高强度钢提供了一个类似的减重 ,但可以降低整体成本。 图 3。 (下标 x 表示高强度钢或铝 6063。 ) 4 成本评价模型 汽车身体的 复合 材料应满足相互冲突的需求 ,如最小重量和最低成本 ,同时确保刚度高、防撞性好。 为了 处理这些目标序列 ,本研究采用了一个价值函数 。 方程 (16) V=1 m+ C m=1 m+1 + p ) m (16) V 代表一个复合客观价值 , V 值的变化对单位增加 ,p 是单位原材料价格 (美元 /公斤 )。 变 换有关的常数的值可以找到质量和成本 最合适于家庭用车 的 制车材料 ,例如 ( 公斤美元 23。可以通过选择材料 而得到 最好的设计方案 ,从而获得 最小的 V。如第 2 部分中所述 ,( C)1 / 恒定的。因此 ,对于一个给定的压碎载荷 ,最好的材料设计 是获得最小的 q。同样 ,集中刚度 设计 ,很容易获得最好的材料的最小值 。 方程 (17) V=(1+p)(1/(17) 方程式 (18)和 (19)可以用于单个组件防撞性和刚度设计。应用方程式 (18)和 (19)为整个车身所有组件 防撞行的 优化配。 方程 (18) 1+p)(/1/(18) 0)代表了目标函数 ,词风投 ,j 代表结构成员的值函数防撞性。变量的值 且仅当一个材料选择成员 j,否则为零。约束 (21)表示防撞性和刚度条件。直流代表全球防撞性标准外 ,整个车身和 全刚度要求。防撞性和刚度有限元计算软件对整个车身 用于 约束 22)确保为每个成员独特的材料 提供 选择 从而 约束 (23)表示二进制条件变量。 它 是高度非线性的 ,因为涉及到非线性有限元模拟计算。 V s=(1+p)(/ q ) (19) 因此 ,不可以用 传统的优化方法 。但是可以使用可以代替的方法, 一种方法是使用一个迭代的方法。 即 获得的价值首先不考虑全身防撞性和刚度。然后对每个成员的材料选择 ,查是否满足约束。然后 ,组件的材料更新迭代 ,直到找到可行的解决方案。另一种方法是使用近 似 主要防撞设计或刚度设计的组件。许多组件相关 于 防撞性和刚度 ,但车身设计 的知识可以显示每个组件防撞性或刚度的主要贡献。然后 ,用 独评估使用每个组件组。详细的优化方法 得 结合其他解决方案 ,该 过程超出了本文的范围 ,应 用 在未来的研究中 ,因为本文的主要目标是开发材料的性能指标。 方程 (20) j (20) 方程 (21) fC( , ,DC fS( , ,21) 方程 (22) (22) , j 方程 (23) 0,1 (23) 5. 案例研究 本节说明了应用程序的性能指数和轻型汽车车身结构材料选择的设计过程。 问题描述 最优材料选择 将 每个身体 的 主要框架结构设计尽可能 的低成本 和 轻质 。 如 车身的有限元模型图 4 所示。该有限元模型得到来自美国国家公路交通安全管理局 (25许可使用 从而进行研究。 5 个候选材料是 从 表 1 中列出 的 。 车 身最初由低碳钢 (轻度 )和 防撞 钢 制造的 。 车身结构分解为 20 个 主要结构 , 组成如表 2 所示。 全球静态抗弯刚度 的 影响对汽车材料的选择。 该 影响是一个模拟额对刚性墙碰撞速度 h。事故分析是由 示 动态有限元代码。静态抗弯刚度分析 ,四个加载 1000 N 分别应用在前方和后方的座位安装。后方在纵向约束 ,横向和垂直方向 ,和前面防震安装限制只有在垂直方向。抗弯刚度被评估为平均负载应用程序点的变形量。静态弯曲的分析是由有限元分析软件 件 来完成的 。 图 4。 案例研究汽车车身结构 25。 主要成员 的 最优材料选择 20 个 主结构组件根据 它 们的目的分为两组。在发生正面碰撞 ,将有由 正面成员 , 包括摇篮 ,上层 前 为能量吸收器。这三个部分而被选为防撞性设计、材料选择和抗弯刚度的设计。 并对这 三个主要组件 的 碰撞能量吸收、材料的性能指标以及使用 数 Q 进行了评估和有限元分析。三个正面成员与初始轴向单独模拟 ,并 与刚性墙碰撞 。 速度 48 公里 /小时由有限元分析 出为 有限元模型 ,大量元素附加到结构的一端为粉碎提供足够的能量。表 2列出了计算 Q 值 。 静态抗弯刚度的情况下 ,一阶的概念分析是用来确认每个主帧和加载条件。 激光校准 型代表整个身体结构构造。在这个模型中 ,梁元素有详细的横截面信息。每一个主要成员可以由 激光校准 有限元模型使用成员力量和时间 对 局部弯曲边界和加载 进行 条件决定。表 2 显示了指数 q 值的性能指标抗弯刚度设计 ,用来 评估究车身刚度。 基于计算性能指标 ,优化材料选择为每个主要成员使用的最小值方程式。交换常数 公斤。所有主要组件的最佳材料表 由 2 中列出。注意 ,在这个案例研究中相关的 “最优 ”是唯一的 V 值说明目的和 “最优 ”的含义实践中根据目标函数的选择可以是不同的。 验证材料的选择 验证车身最优材料的性能选择 ,整个车辆的面前崩溃的模拟进行了原始的身体结构 (全钢体 )和优化设计 , 采用表 2 中的材料组合。三个正面成员防撞性设计厚度是用 定的。图 5显示了原始的身体碰撞 , 车身变形设计和优化设计。 可以 观察到 , 两个设计的整体变形形状几乎没有区别。图 6 显示了三个成员的正面的总能量吸收 的 原始和优化设计。虽然差别不大 ,但优化设计显示比最初的设计 能 更好的能量吸收。加速度在 b 并给出优化设计在图 7 中。这是观察到加速度曲线的形状 ,峰值大小和平均减速两种情况没有显著的不同。 最佳选材也验证了全球抗弯刚度有限元弯曲刚度模拟 的 原始和最优材料 得 选择。抗弯刚度分析的结果表明 ,优化设计的刚度非常接近原来的车身设计。两 种 米和 米。 在这项研究中进一步验证 ,最 严谨 的选材也 得以 检查了材料选择方面的最大价值 q。除了三个主要 防撞载荷 吸收组件。这种严重的弯曲挠度设计是 米。虽然最糟糕的设计是比原来的车身设计略硬 ,但 边缘 也 是有区别的。 图 5。 车身的碰撞变形 :原始体设计 (a)和 (b)的优化设计。 图 6。 组件正面 能量吸收的原始和优化设计。 图 7。 6。 讨论 本节讨论的结果和有效性的 最优 复合材料 车身 案例研究结果表明 ,使用 先进的 方法导致了新的设计优于原设计。如 所示 , 选择最优材料替代原始材料至少 是有 一样好的防撞性性能。抗弯刚度的优化设计也非常类似于 车身 的其他设计。所有这些性能值实现了更少的重量和成本值。 比较不同的详细设计 ,等效抗弯刚度的设计更新。几个组件的厚度稍微修改为最优和最差的身体设计 ,两具 车身 有等效抗弯刚度原体设计。表 3 比较了结构重量、材料成本和 V 的原始值和最优和最差的身体设计更新。从表 3 可以看出 ,最优 复合材料 达到体重减少 斤 而增加材料成本只有 元。这种优化设计了一个轻量级的和具有成本效益的身体组装 ,可以提供高燃油经济性和支付能力。最糟糕的设计的 V 是 从最初的设计体重减少 斤 ,但材料成本增加了 元。这是由于大量使用轻质但昂贵 的 铝合金。如图所示 ,这些比较 ,这些不同的设计会导致完全不同的产品性能。 表 3。车身结构 抗弯刚度 车重 成本 V 价值原始设计 24 偏差在固定负载下的负载应用点。 先进 指数和过程的有效性 案例研究结果还表明 ,这项研究提供了有效的 复合材料 车身和加强现有的材料 的 程序 , 公式和 选择方法。 首先 , 在较薄的结构发达指数允许评估不同材料的优点和缺点。特别是 , 防撞性性能指数很容易考虑。这是可能通过使用新材料的性能指数防撞性 计算 数 来实现的 。 即 轻松地使用基于 序。这些新指标和计算程序 可以 扩展先前在刚度和简单的结构的研究 , 包括复杂的防撞梁。 第二 ,开发的成本评价方法允许实现 在 汽车的 车身 刚度和防撞性约束 下 最好的轻量级的和具有成本效益的设计。案例研究结果 表明 车身 可以 显著的减重 30 公斤左右 ,同时也可以 减少材料成本。这是可能 实现的 成本评估方法 ,如 第四节所示。因此 , 克服材料价格问题的开发过程可以用来取代主要障碍之一 的钢架 结构对燃料 消耗 效率 的问题 。通过优化每个主要结构部 件材料的选择 ,很有可能要充分利用每个材料的优势 ,实现最优产品性能。车身设计 以 这样一种方式吸引客户和制造 商 ,因为 钱只会花在如 重量轻 的 材料 这样 正确的地方 。 7 结论 本文开发 的是 新材料薄壁结构零件的防撞性能指数设计。这些新的性能指标使描述较薄结构组件在汽车身体的机械性能和材料成本 的方面,有了 根据。因此 ,索引允许我们选择最佳的材料系统的结构部分。此外 ,该指数的概念是为方便开发评价和平面图的案例 , 研究表明新的指数帮助实现 了 大幅降低材料成本 , 与同类产品 相比 显著减少 了车重但并 没有显著的增加成本。 这项研究表明 ,通过 复合材料 建设和最优材料选择为每个结构 组件 在汽车的 车 身轻量级和高结构性能 的提升上 没有 造成 成本增加。这些新的指数设计 了 一个轻量级的和负担得起的 车身,从而得到了 汽车行业和消费者的青睐 ,并将有助于减少燃料消耗和温室气体 的 排放。 在未来的研究中 ,制造过程也可以被考虑 进去。 汽车车身的 复合材料 建设 将高科技 加入 到生产 流程 这件事也需要考虑到经济方面的因素 。例如 ,加入不同的材料可能导致更多昂贵的过程或设备。这些 方面的 扩展是值得进一步调查的 。 引用 1汉 拉克 身工程生命周期成本 :钢铁和铝。 7 1995;(5):。 2r . 铁 汽车。 术论文。 2001,2001 3李 Y,Z,重量轻 ,高强度钢板的使用 汽车防撞的身体。 4:177 2003;82 年。 4士 ,国设计 对铝 制 车辆前影响安全的平台。 的影响 0:1055 2004;79 年。 5卡尔 D,布朗特 g 铝作为替代材料的适用性 车身。 0:267 1999;72 年。 林 6李 Y,Z 材料冲击性能和轻量级的车身分析。 2004;25:579 - 85。 7斯 R,克拉克 j 铝是一种 替代钢 的 经济 材料 3 2001;(8):28 8尔 m 料。板牙 997;18:203 9哈恩 O,R r : 中德超轻型研讨会。中国 ,北京 ,2001。 10崔 X,年代 ,胡 车车身的优化设计方法 装配使用 设。板牙 008;29(2):381 - 7。 11阿什比 械设计中材料选择。 2005 年。 12巴顿 R,爱德华 m 估计减重效果的材料 替换与常数刚度关节。 术论文。 2002,2002 李 13巴顿 R、 F,爱德华 m 重 效果的材料替换在常数 刚度组件。 薄墙结构体 2004;42:613 14法毫米。工程设计的材料选择。普伦蒂斯霍尔 ,1997。 15M。以知识为基础的系统材料选择机械 工程设计。 001;22(8):687 - 95。 16S,卡斯特罗 V。 004;25(8):689 - 98。 17S,斤 ,。材料选择结合 2002;23(5):459 - 70。 18罗西 ,k 数值模拟的轴向的崩溃 薄壁管多边形部分。薄壁结构 2005;43:1646 - 61。 19,w 结构。 J:机械 1983;50:727 20R,路克 ,H。准静态轴向压缩的薄壁 圆形铝管。 001;43:2103 陆 21G,X。结构和材料的能量吸收。瑞斯 出版有限公司 ,2003 年。 22 a 静态和实验和数值研究 动态轴向破碎的圆形铝管。薄壁结构 2004;42:1103 23阿什比 材料设计和多目标优化选择。学报 2000;48:359 - 69。 24江顾防 。 撞防撞结构的优化 设计。 010;31(3):1085 - 95。 25国家高速公路交通安全管理。 (2007 年 ) 26代 ,小岛菊池 新的汽车车身 具设计师。 术论文。 2001,2004 1. 太原理工大学现代科技学院 毕业设计(论文)任务书 第 1 页 毕业设计(论文)题目: 轻型 自卸车设计 原始 参数 : 外形尺寸(长 宽 高) 4770 1800 1980(轴距 2800距(前 /后) 1555/1530(前悬 1100悬 1455近角 24 离去角 14 最小离地间隙 185业设计(论文)主要内容: 自卸车主要性能参数的选择 自卸车车厢的结构与 设计 自卸举升机构的设计 液压系统设计 副车架的设计 三维建模 二维平面成图 第 2 页 主要参考文献 : 1 李少东,张根志 . 宽体矿用自卸车液压系统油压特性分析与结构优化 J. 农业装备与车辆工程 , 20132013 年 12 期 ):932 史凯,贾敏 . 举升报警联锁制动系统的研制与改进 J. 矿山机械 , 20142014 年 02期 ):413 王涛 . 矿用自卸车车架静动态性能分析 J. 专用汽车 , 2010(第 3 期 ). 4 陈艳娟 , 王朋波 . 某重型自卸车车架结构强度有限元分析 J. 专用汽车 , 2011(第 11 期 ):705 刘永香 . 重型前顶自卸车副车架设计 J. 拖拉机与农用运输车 , 20092009 年 04期 ):546 赵衍平 . 自卸车副车架与底盘主车架几种联接方式的对比分析 J. 专用汽车 , 2011, 3(第 3期 ):787 屈葵林 . 基于 自卸车车架有限元分析及优化设计 J. 装备制造技术 , 20122012 年 06 期 ):348 唐昊 . 重型 8 4 自卸车转向系统设计 J. 专用汽车 , 20122012 年 05 期 ):249 陈树勋,黄宁,刘金禄 . 矿用重型自卸车结构分析与轻量化设计 J. 工程机械 , 20112011 年 04 期 )2610 邓华忠 . 自卸车车厢防洒漏改造实践 J. 机电信息 , 2011(第 9 期 ):6411 冯建伟 . 件在自卸车货箱设计中的应用 J. 专用汽车 , 2010(第 3 期 ). 12 董志 明 ;郭海全 ;潘艳君 ;丁浩然 . 有限元技术在矿用自卸车设计中的应用 J. 计算机辅助工程 , 2011(第 4 期 ):6313 仲学华 . 基于 自卸车上装参数化及模块化设计 J. 汽车实用技术 , 2012(第 3期 ):3414 李立顺 , 孟祥德 , 詹隽青 , 吕萌 . 整体自装卸车 制系统设计 J. 起重运输机械 , 2006(第11 期 ):1915 田海英 . 某专用自卸车液压举升机构基于 有限元分析 J. 工程机械 , 20132013 年 04 期 ):2116 张桢华 . 自卸车前置举升机构快速设计计算 J. 专用汽车 , 2009(第 1期 ):52. 17 张桢华 . 自卸车举升缸下支座疲劳分析 J. 专用汽车 , 2009(第 12期 ):5118 梁冲 . 高强度钢板在自卸车轻量化设计上的应用研究 J. 装备制造技术 , 2010(第 9期 ):5519 . 2011, 104(5): 2620 , , . of of on 004;42: 3637. 学生须提交的文件: 1. 开题报告一份: 不少于 5 千字,查阅文献 20 篇(其中 2 篇英文)以上,格式符合学院要求; 2. 外文文献原 文与翻译一份:文献应与课题相关, 1 2 篇, 原文字符数不少于 1 万(对应译文汉字约 5 千字) ,装订在设计说明书最后。 3. 设计说明书一本:打印,不少于 2 万字,格式符合教务处要求; 4. 工程设计图:折合成 幅不少于 2 张; 5. 三维设计图:应用三维设计软件进行设计、计算与绘图,至少进行一个中等复杂度零件的三维建模。 进度安排: 第四周 第六周:翻译外文文献,写开题报告。 第七周 第八周: 对设计机构及零件进行相关设计计算及 手工绘制草图。 第九周 第十五周:进行毕业设计图纸绘制及三维建模,并撰写说明书,第十周进行中期检查。 第 十六周:上交毕业设计文件,教师评阅,并进行修改。 第十七周:详细认真准备毕业设计答辩。 第十八周:进行毕业设计答辩。 专业班级 车辆 10 学生 连鹏程 设计(论文)工作起止日期 指导教师签字 日期 专业(系)主任签字 日期 7 010to 2,3, 4,5 6. of of to 7. 5,810 to in of in of In on 11,14. of in of 15of of 16 +1 402 472 3495; +1 402 472 2 (2011) 815821J. as of to In by of is to to is to a s kg is km 1. is as on is be by of of of is in 1113. 11 a on to of of do is a to - 211 2010 to of in to of by a a by to 010 of to 2 0105 010to in of of o., 00190, 00072, 8588, a or 0 is B =(c + d)/2 c d of a t is et 20an of by 72:32 18:075282 is t is of 21 52:2 13:053t is =2w +2h +4f h, w of of on or ), b is of In a of a 17. 12,13 by is to of as of in to in A to of a of of In of is to be be in of a is of a In to is a to of to 18. of to as as 1921, of in 19of a 38:27M 9:5675r 1816 X. et be 21 be if of a is be as a of is a t is 22 6of is to is of 1” to of 2” If q. (5) of 2is 7of a 8 is of a t is q is q. (5) to t q. (8) of a is by f!9a ()1/QA q. (9) is of q=q. (9). In of a q.(10) be in be (5) 10) by a to be to , be E on q. (5)q. (11), Q be 00000to 2011) 815821 be q. (12) of be on t0/ as is a 0is 0m. 001 000000m0 13of q1=m is 3 063 a of . It is to 3of H as of At , to be a it a (2011) 815821 81712 be 1=1=m is 2 q. (14) of . It be of by is by 01 an of by a 5% of a of t0= of t0=he to (1) to 2) be E of of be of of be 1=q=q 12,13, is q is q is an 11 on (1) =(2) E=q 3) =q on as q , 2 12,13t1. by a 5% to q At a q, q a of q. (9), a al st kg/)Pa)07 7840 80 30007 7840 10 50007 7840 50 800063 70 2720 0 172010 70 2720 70 290 3. H 063 as (x or 063.)4. of as a V, a 23 16m is $), in to in m, p is $/ of of if if i is j, q. (21) to be by E q. (22) q. (23) is E of be is to an of z is . et 2 (2011) 815821be in (23. be by q. (9) q. (16)V f!A 17As ,()1/QA is is it is to is 1=(18) 19) be 18) 19) be as to:.;.; .;.;1; 8 j 221(20) in c,of j 4. to as as E of is 4. E S 25 to . of BH)0 as of a at if in is to to on s to or be 24 of be in a of is of of of 25A to In th 现代科技学院 毕业设计(论文)开题报告 毕业设计(论文)题目 : 轻型 自卸车设计 学 生 姓 名 : 连鹏程 指 导 教 师 姓 名 : 王 铁 专 业: 车辆工程 2014 年 4 月 4 日 1. 课题名称: 轻型 自卸车设计 2. 课题研究背景: 自卸车是装有由本车发动机驱动的液压举升机构,能将车厢卸下,或将车厢倾斜一定角度卸货,并靠车厢自行回位的专用汽车。利用该车发动机动力驱动液压举升机构(变速器一取力器一液压泵一分配器一举升油缸 ), 将车厢举升到一定角度卸货,并依靠车厢自重使其复位的专用汽车。后方倾卸采用双缸直推式液压举升机构。该自卸汽车主要由底盘、货箱、副梁、液压举升机构、液压系统等部件组成。随着生产力的发展,货物运输合理化和装卸机构机械化的要求,使自卸车得到了很快的发展,并且日趋完善。 机械制造行业的应用最早使用也最为广泛。目前其最主要的应用涉及到机械,电子, 建筑等工程领域。世界各大航空,航天及汽车等制造业巨头不但广泛应 术进行产品设计,而且投入大量的人力,物力及财力进行 件的开发,以保持行己技术上的领先地位和国际市场上的优势。 在复杂机械工程中应用,这样不但可以提髙设计质量,缩短工程周期,还 可以节约大量的建设投资。 传统的卸车设计与开发,一般在完成概念设计、方案论证和产品设计后 ,还要进行样机试制及验证。随着三维 拟样机技术逐渐成熟起来,借此工程技术人员可以在计算机上建立自卸车的三维模型,模拟在现实环境下自卸车举升机构的运动和动力特性,并根据仿真结果 进行优化设计,确定举升机构的布置方案,以在设计早期确定关键的设计 参数,达到缩短开发周 期,降低成本,提高产品质量的期望。 近年来,自卸车逐渐成为市场热点,其产销量大幅度增长,据统计,自卸车在中重型卡车市场需求量上约占百分之四十的份额,成为卡车市场的兵家必争之地。我国目前自卸车的发展向重型化和轻型化两极发展。 2013 年上半年,国内重卡市场增长远远好于年初的预期。国家的政策支持也使得在 3、 4 月份工程类重卡走俏。 4 月中下旬之后 ,工程类重卡新增和更新需求逐渐放缓 ,重卡市场步入了以牵引车销售为增长动力的行情阶段。 8 月份,重卡销售 5. 68 万辆,环比增长 5. 93%,同比增长 71. 84%。半 挂牵引车销量继续好转。从短期看来,重卡业还将受益于计重收费带来的卡车重型化深度变迁中,国家积极的财政政策将带来重卡业的渐进式复苏。目前 ,各项宏观经济指标显示物流回暖 ,出口亦有复苏 ,重卡业形势良好。预计 2014 年汽车全行业销售 1347 万辆 , 同比增长 33%左右。其中 :重卡销售 57 万辆,环比增长 5. 5%。随着重卡销量快速回升。利润增长主要来自于毛利率的提高。因此行业将完全恢复正常。 国务院推出了拉动内需的 4 万亿投资计划,其中大部分资金投向了基础设施建设领域。政府提出的十项规划中强调要加快保障性安居工 程建设、加快农村基础设施建设、加快铁路及公路和机场等重大基础设施建设等要求。这些项目的建设将需要相当数景的重型卡车,这对于重卡 行业尤其是重型自卸车来说,产生了明显的拉动作用。随着自 2009 年以后基础建社的开工和灾后重建工作的逐步完工,对重型自卸车的需求是逐月增加。近几年虽然重型货车总销景平均在前 5 个月出现以 3 月为最大值,开口向下的抛物线状,但是重型自卸车逐月不降反升,对重型货车的贡献度是逐月增大。目前我国有重型自卸货车生产企业 90 多家,但主要的生产企业仅有十多家,这十多家企业占据着市场 85%的份额,这十 多家企业中最大部分企业仅有一个重卡品牌,所以企业的高度集中必然带来品牌的髙度集中。我国的重型自卸货车品牌主要集中在福田、东风等前 12 个品牌上,这 12 个品牌占据着该行业 80%以上的市场份额。 其余品牌占据着市场不到 20%的市场份额。由于重卡市场的起伏与国民经济的发展脉搏几乎同步,因此,重卡的销售走势,背后反映出国内 投资指数的逐渐复苏。 3. 课题研究意义: 选取卸车设计会项目贯穿机械的多方面,为我们了解技术研发、产品 生产过程、参加生产性实习提供了很好的媒介实例,同时为了解车辆专业的新工艺、新技术、新方法提供了一个很好的平台。并且也把三维 术应用到了机械的实际设计开发中。 目前有许多研究人员在从事专用自卸车的设计,国内对宽体自卸车液压系统油压特性分析与结构优化的研究主要集中在采矿单位,李少东,张根志的文章对该问题作了具体的阐述。他们通过模拟宽体矿用自卸车卸货模式,建立了举升模型和计算模型,计算出多级缸各临界工作位置的系统油压 ,并绘制了油压特性曲线,分析了系统最大油压出现的位置点 ,为液压系统与货箱结构的合理匹配提供了一种设计方法 1。 自卸车厂家在货箱举升控制系统和车辆制动系统的设计上是互相独立的,驾驶员如果按照操作标准严格操作,即等待货箱完全落回到副车架后行驶,便不会出现货箱拉断架空管道、电缆等恶性事故。但是,一方面由于日常工作中人为因素的影响,比如驾驶员忘记关闭取力开关、举升操纵阀,使取力装置运行,举升状态未改变;另一方面车辆本身举升取力系统老化或出现故障,机构不分离,均可导致车辆在货箱处于举升状态下行驶,拉断管道、电缆的恶性事故屡禁不止。史凯,贾敏对这个安全盲区进行了改良。在举升控制系统和制动气路间建立联锁控制装置,使自卸车工作时做 到本质化安全。史凯,贾敏在设计中一方面使车辆的举升状态控制在制动状态,杜绝在货箱举升状态时行驶而引发事故,实现本质化安全;另一方面在卸车过程中,实现驾驶员手动操作联锁装置,使车辆在货箱举升的状态下能够实现短距离移动,方便卸车 2。 车架作为汽车底盘的基础件,其结构形式直接影响着底盘各零部件的布置安装。同时,作为底盘及整车的主要承载件,车架对整车的各项性能起着至关重要的作用。王涛对某型矿用自卸车车架进行了有限元分析和模态分析,通过 究该车架静态和动态性能,了解 该车架的整体受力状况,以此为设计依据对车架的局部的应力集中区域进行了结构改进 3。陈艳娟 , 王朋波 利用有限单元法对一款冲压铆接自卸车车架进行了仿真分析,计算得到该车架在典型极限工况下的变形和应力,从而对该车架的结构进行了分析4。 2011 年,刘永香介绍了主副一体自卸专用车架的设计过程,着重介绍了该车 架的结构形式和特点,并论述了车架结构形式的确定、纵梁的设计校核、横梁的布置及结构设计、横梁与纵梁连接形式及自卸结构的布局设计,对自卸车专用车架的设计有一定的指导作用。并介绍了副车架主要结构的设计原则 5。赵 衍平 通过自卸车副车架与底盘主车架几种连接方式的对比和分析,选出了最佳的方案并在设计和生产中得到了应用 6。屈葵林用 限元分析法对自卸车车架进行了分析,找出了自卸车车架在应用中比较容易出现问题的部位,提出了改进的建议 7。 唐昊根据重型自卸车的使用特点,进行了重卡自卸车双前桥转向系统的设计。应用 件建立了转向系统的三维模型,并应用 件从运动学的角度,对转向系统进行设计校核和优化,设计出适应重型 8 4 自卸车使用要求的转向系统 8。 陈树勋,黄宁和刘金禄利用结构有限 元分析软件 某矿用重型自卸车进行结构参数化建模并对该模型在 8 种运载卸料工况载荷作用下的变形与应力分布进行有限元分析计算。采用以 分析器的结构优化导重法对该矿用重型自卸车结构进行轻量化设计。结果表明,在保证结构强度的前提下,结构优化后整车质量由 9 324t 减轻为 6 862t实现了轻量化目标。为保证矿用自卸车的使用可靠性和寿命,降低设计成本,缩短设计周期,董志明介绍了矿用自卸车的结构特点,论述对其进行有限元分析时的软件模块选取、单元选取、网格精度控制、材料定义、实常数定义、求解和结果处理 等环节中的要点。他以驾驶室变形分析和后桥总成强度分析为例说明采用有限元技术可以定量地掌握矿用自卸车的各方面性能,从而为设计提供了参考 9。 自卸车的货箱设计在近些年得到了很快的发展。三钢汽运公司的邓华忠对专用自卸车货箱的现状及存在问题做了详细概述,通过顶盖密闭系统改造,斯太尔自卸车防洒漏总体设计,车厢的后门锁止结构设计及后门钩气路设计改造等使自卸车运输达到了安全环保经济的要求 10。 冯建伟 基于 列零件设计方案及自卸车货箱结构设计特点对其进行参数化驱动,从而自动生成指定规格的自卸车货箱图纸,实现合乎要求的自动化设计 11。 为保证矿用自卸车的使用可靠性和寿命,降低设计成本,缩短设计周期,介绍矿用自卸车的结构特点,论述对其进行有限元分析时的软件模块选取、单元选取、网格精度控制、材料定义、实常数定义、求解和结果处理等环节中的要点董志明以驾驶室变形分析和后桥总成强度分析为例说明采用有限元技术可以定量地掌握矿用自卸车的各方面性能,从而为设计提供参考 12 仲学华基于参数化、人机交互 人性化和模块化的思想对 件进行了二次开发,对自卸车上装各部分进行快速建模。缩短自卸车上装的设计周期,提高设计效率 13。 李立顺以整体自装卸车的功能和工作原理为依据,设计了以工程车辆专用可编程控制器为核心的电气控制系统,给出了硬件结构和软件流程图 14。 在近几年有非常多的研究人员研究从事于自卸车的举升机构。 田海英对某专用汽车有限公司的 自卸车液压举升机构,开发了该机构的参数化设计系统,并建立了基于 有限元分析参数化设计分析模型,为自卸车举升 机构系统的快速及优化设计提供了平台 15。 此外,张桢华据多年的工作经验,摸索出了一套适用于前置举升机构的快速设计方法,通过计算验证了设计的合理性,并快速计算自卸汽车举升系统的各必要参数 16。他还对汽车设计过程中常用的疲劳分析方法一名义应力法与局部应力应变法进行了分析、对比和总结,给出了进行疲劳分析的一般性的步骤,并对有限元法在疲劳分析中的作用进行了阐述。通过以举升缸下支座分析为例,详细论述了以通用有限元软件和疲劳分析软件为平台,对汽车零件进行疲劳分析的过程 17。 由于石油、钢材价格的大幅上 涨,以及道路计重收费政策的实施,给市场用户增加了营运成本,给自卸车生产厂家带来很大的成本压力,基于此,为了轻量化车身重量, 梁冲就高强度钢板在自卸车上进行强度等代设计,进行了研究,用有限元法分析了原结构的强度、刚度。讨论了不同强度的钢板替代方案,最后对典型产品进行了强度等代设计,使其自身总质量减小了约 1000得良好的轻量化效果 18。 普利司通公
- 温馨提示:
1: 本站所有资源如无特殊说明,都需要本地电脑安装OFFICE2007和PDF阅读器。图纸软件为CAD,CAXA,PROE,UG,SolidWorks等.压缩文件请下载最新的WinRAR软件解压。
2: 本站的文档不包含任何第三方提供的附件图纸等,如果需要附件,请联系上传者。文件的所有权益归上传用户所有。
3.本站RAR压缩包中若带图纸,网页内容里面会有图纸预览,若没有图纸预览就没有图纸。
4. 未经权益所有人同意不得将文件中的内容挪作商业或盈利用途。
5. 人人文库网仅提供信息存储空间,仅对用户上传内容的表现方式做保护处理,对用户上传分享的文档内容本身不做任何修改或编辑,并不能对任何下载内容负责。
6. 下载文件中如有侵权或不适当内容,请与我们联系,我们立即纠正。
7. 本站不保证下载资源的准确性、安全性和完整性, 同时也不承担用户因使用这些下载资源对自己和他人造成任何形式的伤害或损失。

人人文库网所有资源均是用户自行上传分享,仅供网友学习交流,未经上传用户书面授权,请勿作他用。