资源目录
压缩包内文档预览:(预览前20页/共26页)
编号:9103519
类型:共享资源
大小:605.09KB
格式:ZIP
上传时间:2018-02-28
上传人:机****料
认证信息
个人认证
高**(实名认证)
河南
IP属地:河南
50
积分
- 关 键 词:
-
连接
数控
工艺
编程
全套
cad
图纸
- 资源描述:
-
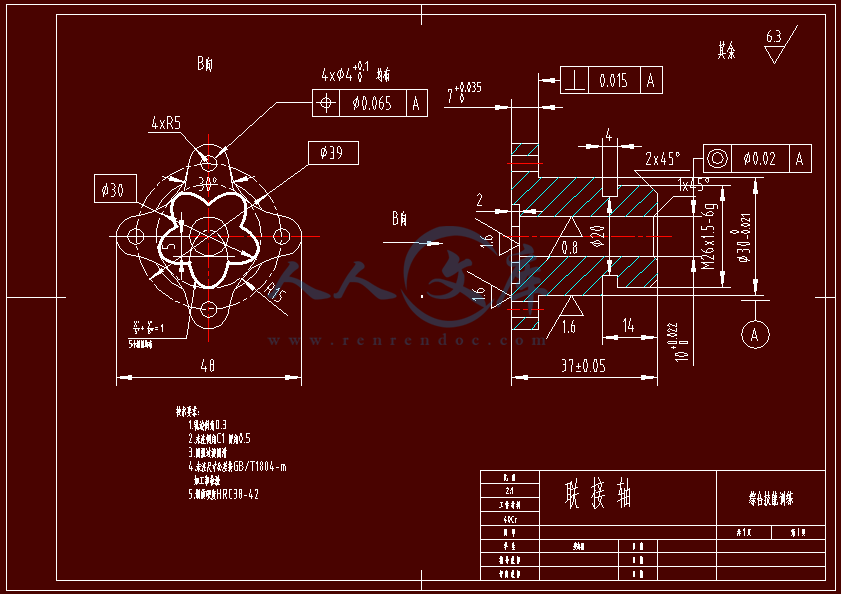
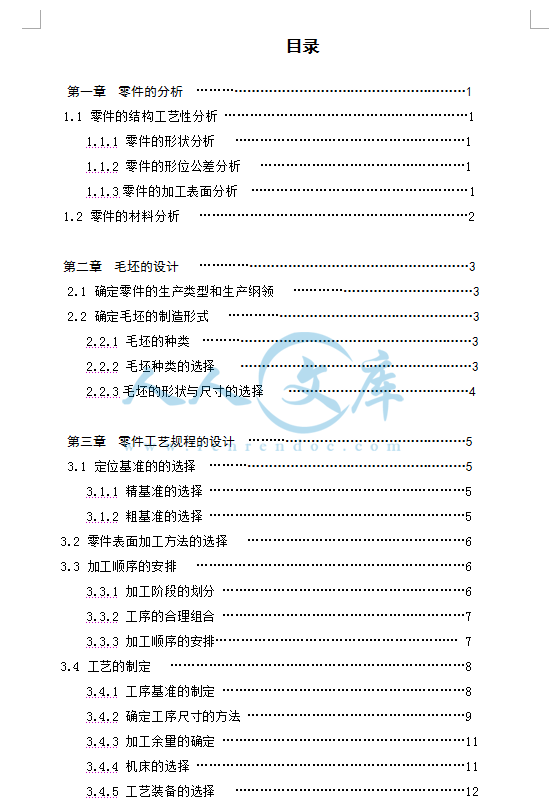



- 内容简介:
-
1前言毕业设计是培养我们实际工作能力的最后一个重要实践性学习环节,它不但是对我们三年来的学习与实践是一个很好的总结和考验,也是为以后从事专业技术工作做个强而有力的铺垫。本次我的设计题目是联接轴,在设计之前对此零件没有太多了解,经过多次调查研究和指导老师的细心指导下,使我能够很好的完成这次设计。此次设计不但培养了我们综合运用所学知识分析和解决本专业一般技术问题的能力,而且也进一步巩固扩大和深化了我们所学的基本理论、基本知识和基本操作技能,同时也培养了我们树立正确的设计思想和生产观念、经济观念、全局观念,养成了理论联系实际和严谨的工作作风,培养我们掌握机械加工的一般工艺规程和方法,独立正确的使用技术文献资料和正确的表达自己设计思想的能力。首先,我积极地查阅相关资料,对零件图进行了仔细的研究,了解了现场工作情况,然后,向老师认真的请教了加工工艺过程及方法等技术性问题,为自己进行毕业设计做好准备。通过以上学习,使我了解了联接轴的结构,生产纲领和生产条件,并确定其重要加工表面。老师的辅导与分析,让我能综合运用所学过的理论知识和方法,正确地制定一个零件的机械加工工艺规程,从而保证零件的加工质量、生产率和经济性;能较熟练地使用有关的手册,图表资料及技术参考书,也能够较熟练应用工艺计算的方法,正确地进行工艺计算,熟练掌握一般零件的数控编程方法,机床的操作以及零件的数控加工。最后,按要求通过数控机床加工了一个实际大小的零件,并以说明书来阐述了关于零件的有关内容及加工工艺过程等几个重要方面,认真地完成了整个设计的过程。在此,对给予我大力支持和热情帮助的老师们表示忠心的感谢。由于个人能力有限,经验欠缺,因此,文中错误,不妥之处在所难免,恳请各位领导及老师批评指正。2目录第一章零件的分析111零件的结构工艺性分析1111零件的形状分析1112零件的形位公差分析1113零件的加工表面分析112零件的材料分析2第二章毛坯的设计321确定零件的生产类型和生产纲领322确定毛坯的制造形式3221毛坯的种类3222毛坯种类的选择3223毛坯的形状与尺寸的选择4第三章零件工艺规程的设计531定位基准的的选择5311精基准的选择5312粗基准的选择532零件表面加工方法的选择633加工顺序的安排6331加工阶段的划分6332工序的合理组合7333加工顺序的安排734工艺的制定8341工序基准的制定8342确定工序尺寸的方法9343加工余量的确定11344机床的选择11345工艺装备的选择123346切削用量的选择13347时间定额的确定15第四章数控编程1741数控加工的特点1742数控编程方法及特点17421数控编程的分类17422编程零点及坐标系的选择17423对刀点的选择17424加工路线的确定1843数控加工程序的内容18431车床程序18432铣床程序20结束语23参考文献244第一章零件的分析11零件的结构工艺性分析零件的结构工艺性是指所设计的零件在能满足使用要求的前提下制造的可行性和经济性,它的涉及面广,因此有必要对零件进行结构工艺性分析,找出技术关键,以便在拟定工艺规程时采用适当的工作措施加以保证。111零件的形状分析联结轴的结果较为复杂,从外形上看零件左端椭圆花的轮廓并有4的通孔。外轮廓表面质量RE16,、内孔面表面质量RE08,加工难度较大。30外圆轴线与10的轴线的同轴度要求为002MM并与7的右端面垂直度要求为0015MM还与4通孔有0065的位置度要求。大体加工过程首先在车床上用车刀加工30的外圆,然后用切断刀加工槽,用螺纹刀加工螺纹。内孔先钻再绞。最后在铣床上加工左端面和4个4的通孔。112零件的技术要求分析零件图纸上标注的技术要求1锐边倒角032未注倒角C1圆角R053圆弧过渡光滑4未注尺寸公差按GB/T1804M加工和效验5调质硬度HRC3035113零件的加工表面的分析从零件图可以看出联结轴的主要加工表面是110的内孔它的表面粗糙度是RA08,尺寸要求严格,而且其轴心线是设计基准。2M26156G的螺纹此螺纹是一个标准螺纹,虽然没有特殊要求,但它在配合时起传递扭矩的作用,故其配合精度要求高。330外圆轴线与10的轴线的同轴度要求为002MM并与7的右端面垂直度要求为0015MM还与4通孔有0065的位置度要求。通过以上的分析可知,零件的结构较为简单,易于加工,具有一定的可行性。12零件的材料分析零件材料的选用是非常重要的,选材不当制成的零件不能满足使用要求,过早损伤5和破坏产生不良影响或经济效益差等。机械零件选材的一般原则是首先满足使用性能的要求,同时兼顾工艺性、经济性和环保性。对于轴类零件的选材应具有以下几点要求1优良的综合力学性能,即要求有高的强度和韧性,以防止由于过载和冲击而引起的变形和断裂。2高的疲劳极限,防止疲劳断裂。3良好的耐磨性。4在特殊条件工作时,还应有特殊要求。本零件的材料是40CR,它属于低淬透性合金调质钢,其力学性能是MPA,785SMPA,J。其化学成分是碳含量037045,铬685B95457KA含量0811,锰含量017037,硫含量0508,其中碳含量过高、过低均不能满足经调质后获得良好综合力学性能的要求,主加元素为铬,在配以硫、锰等合金元素,其作用是提高淬透性,强化铁素体和细化晶粒,因此,此钢的热处理变形小,废品率低,因而降低了工艺成本。其热处理特点是当原始组织为珠光体时,预先热处理可采用正火或退火处理;当当原始组织为马氏体时,预先热处理可采用高温回火处理,该类钢最终热处理均采用淬火后在500650的高温回火工艺,即调质处理工艺,调质处理可使材料具有良好的综合力学性能。6第二章毛坯的设计21确定零件的生产类型和生产纲领生产类型是指企业(或车间,工段,班组,工作地)生产专业化程度的分类,一般分为大量生产,成批生产和单件生产三种类型。它可根据生产纲领和产品及零件的特征或工作地每月担负的工序数来具体划分。生产纲领是指在计划期内应当生产的产品产量和进度计划。计划期常定为一年,所以生产纲领也称年产量。零件的生产纲领要计入备品和废品的数量,其计算式为NQN11N零件的年产量件/年Q产品的年产量台/年N每台产品中,该零件的数量件/台备品的百分率废品的百分率其中Q500N152所以N50015125355即536件/年由上所述,查机械制造工艺学中表13知该零件为中批生产。22确定零件毛坯的制造形式毛坯是根据零件所要求的形状,工艺尺寸等方面而制成的供进一步加工使用的生产对象。毛坯种类的选择不仅影响着毛坯制造的工艺装备及制造费用,对零件的机械加工工艺装备及工具的消耗,工时定额计算有很大影响。221毛坯的种类常用的毛坯种类有铸件、锻件、型材、焊接件、冷压件等。1铸件适用于形状复杂的毛坯。2锻件适用与零件强度较高,形状较简单的零件。尺寸大的零件因受设备限制,故一般用自由锻;中、小型零件可选模锻;形状复杂的刚质零件不宜用自由锻。3型材热轧型材的尺寸较大、精度低,多用作一般零件的毛坯;冷轧型材尺寸较小、精度较高,多用于毛坯精度要求较高的中小零件,适用于自动机床加工。4焊接件对于大件来说,焊接件简单方便,特别是单件小批生产可大大缩短生产周期,但焊接后变形大,需经时效处理。5冷压件适用于形状复杂的板料零件,大多用于中小零件的大批量生产。7222毛坯种类的选择选择毛坯种类需考虑的因素有以下几点1根据图纸规定的材料及机械性能选择毛坯。2根据零件的功能选择毛坯。3根据生产类型选择毛坯。4根据具体生产条件选择毛坯。223毛坯的形状和尺寸的选择确定毛坯的形状与尺寸的步骤是首先选取毛坯加工余量和毛坯公差,其次将毛坯加工余量叠加在零件的相应加工表面上,从而计算出毛坯尺寸,最后标注毛坯尺寸与公差。其总的要求是减少“肥头大耳”,实现少屑或无屑加工。因此,毛坯形状要力求接近成品形状,以减少机械加工的劳动量。本零件的大部分加工表面是回转体表面,根据本零件的生产纲领,年生产数量,经济价值及复杂程度,另外本零件为轴类零件,考虑其复杂程度,所以本零件毛坯为棒料。因为棒料的经济性好,加工余量小,而且成本较低。根据本零件的结构特征和尺寸要求及考虑到经济性,所以毛坯圆棒料的尺寸为50MM50MM。8第三章零件工艺规程的设计机械加工工艺规程是规定产品或零部件工艺过程和操作方法等的工艺文件,它是指导生产的主要技术文献,是组织和管理生产的基本依据,是新建和扩建工厂或车间的基本资料,是进行技术交流的重要手段。31定位基准的选择在制订零件的加工工艺规程时,正确地选择工件的基准有着很重要的意义。基准选择的好坏不仅影响零件的加工位置精度,而且对零件各表面的加工顺序也有很大的影响。基准有粗基准与精基准之分。选择定位基准时是从保证工件精度要求出发的,因而分析定位基准选择的顺序就应从精基准到粗基准。311精基准的选择1基准重合原则就是尽可能选用设计基准作为定位基准,这样可以避免定位基准与设计基准不重合而引起定位误差。2基准统一原则位置精度要求较高的某些表面加工时尽可能选用同一定位基准,这样有利于保证各加工表面的位置精度。3自为基准原则当某些表面精加工要求加工余量小而均匀时,选择加工表面本身作为定位基准,用于提高加工面本身的精度。4互为基准原则为了使加工面间有较高的位置精度,又为了使其加工余量小而均匀采取此原则。5保证工件定位准确、夹紧可靠、操作方便的原则。312粗基准的选择粗基准选择的要求应能保证加工面与非加工面之间的位置要求及合理分配加工表面的余量,同时,要为后续工序提供精基准。1为了保证加工面与非加工面之间的位置要求,应选非加工面作为粗基准。2合理分配各加工面的加工余量。3粗基准应避免重复使用,在同一尺寸方向上,通常只允许使用一次。4选作粗基准的表面应平整光洁,要避开锻造飞边和铸造浇冒口,分型面,毛刺等缺陷,以保证定位准确、夹紧可靠。由于本工件毛坯为棒料,所以采用50棒料的外圆柱面为粗基准,车削零件的右端,再以粗车后的外圆柱面为粗基准,车削零件的左端,然后再以粗车后的两端的外圆9柱面分别为基准,以长37两端面和零件的回转轴心线为精基准,分别对零件两端的外轮廓、沟槽、孔及螺纹进行加工,保证两端各个部位的尺寸精度及位置精度,最后以30的外圆和椭圆弧的端面为基准,铣削加工椭圆花和4个4的通孔。由以上分析可知本零件采用两种基准原则,一是基准重合原则,它是以零件的轴心线为定位基准也是设计基准,对零件的外圆、内孔、以及螺纹等表面进行切削加工;另一种是基准统一原则,它是多个加工表面都以一个基准作基准面加工定位的。32零件表面加工方法的选择零件表面的加工应根据这些表面的加工要求和零件的结构特点及材料性质等因素,而选用相应的加工方法。在选择某一表面的加工方法时,一般总是首先选定它的最终加工方法,然后再逐一选定各有关前道工序的加工方法。加工方法选择的原则如下1所选加工方法应考虑每种加工方法的经济加工精度范围要与加工表面的精度要求和表面粗糙度要求相适应。2所选加工方法能够确保加工面的几何形状精度,表面相互位置精度的要求。3所选加工方法要与零件材料的可加工性相适应。4加工方法要与生产类型相适应。5所选加工方法要与企业现有设备和工人技术水平相适应。通过以上原则,本零件各主要表面加工方法为1各回转表面、锥面、椭圆弧及槽车削加工2M26X156G的螺纹车削加工3外轮廓铣削加工4铣椭圆铣削加工54个4的孔钻削加工33加工顺序的安排331加工阶段的划分工件的加工质量要求较高时,应划分阶段。一般分为粗加工、半精加工和精加工三个阶段。粗加工阶段是从坯料上切除较多余量,所能达到的精度和表面质量都比较低的加工过程。半精加工阶段是在粗加工和精加工之间进行的切削加工过程。精加工是从工件上切除较少余量,所能达到的精度和表面质量都比较高的加工过程。划分加工阶段的作用是101避免毛坯内应力重新分布而影响获得的加工精度。2避免粗加工时较大的夹紧力和切削力所引起的弹性变形和热变形对精加工的影响。3粗精加工阶段分开,可较及时地发现毛坯的缺陷,避免不必要的损失。4可以合理使用机床,使精密机床能较长期地保持其精度。5适应加工过程中安排热处理的需要。332工序的合理组合确定加工方法后,就要按生产类型、零件的结构特点、技术要求和机床设备等具体生产条件,确定工艺过程的工序数目。确定工序数目有两种基本原则可供选择1工序集中所谓工序集中,就是零件的加工集中在少数工序内完成,而每一工序的加工内容却较多。其特点1采用高效专用设备及工艺装备,生产率高。2工件装夹次数减少,易于保证表面间位置精度,还能减少工序间运输量,缩短生产周期。3工序数目少,可减少机床数量,操作工人数和生产面积,还可简化生产计划和生产组织工作。4因采用结构复杂的专用设备及工艺装备,便投资大,调数和维修复杂,生产准备工作量大,转换新产品比较费时。2工序分散所谓工序分散就是将工件的加工分散在较多的工序内进行,每道工序的加工内容很少,最少时即每道工序仅一个简单工步。其特点1设备及工艺装备比较简单,调整和维修方便,工人容易掌握,生产准备工作量少,又易于平衡工序时间,易适应产品更换。2可采用最合理的切削用量,减少基本时间。3设备数量多,操作工人多,占用生产面积大。从生产批量或设备等方面考虑,本零件属于中批生产,虽然工序越集中,加工周期越短,加工的精度也高,但是,本零件部分加工在普通机床上无法加工,所以粗精加工必须在数控机床上一起完成,这样虽提高了生产率,但同时也提高了成本,也没有合理的使用机床,因此,此零件采用工序集中原则。333加工顺序的安排111机械加工工序的安排原则1对于形状复杂、尺寸较大的毛坯或尺寸偏差较大的毛坯,应首先安排划线工序,为精基准加工提供找正基准。2按“先基面后其它”的顺序,先加工精基准面。3在重要表面加工前,应对精基准进行修正。4按“先主后次,先粗后精”的顺序,对精度要求较高的各主要表面进行粗加工、半精加工和精加工。5对于与主要表面后位置精度要求的次要表面,应安排在主要表面加工之后加工。6对于易出现废品的工序,精加工和光整加工可适当提前,一般情况主要表面的精加工和光整加工应放在最后阶段进行。2热处理工序安排的原则调质的目的是为了提高工件的综合力学性能,减少工件的变形或为以后的表面热处理做好组织准备。因此,一般安排在粗加工后、精加工前进行,可以保证淬透性差的钢种表面调质层(回火索氏体)的组织不被切削掉。3辅助工序安排的原则1中间检验一般安排在粗加工全部之后,精加工之前,送往外车间加工的前后,花费工时较多和重要工序的前后。2荧光检验、磁力探伤等特种检验,主要用于表面质量的检验,通常安排在精加工阶段。荧光检验如用于检验毛坯的裂纹,则安排在加工前。3电镀、涂层、发蓝、氧化等表面处理工序,一般安排在工艺过程的最后进行。通过前面对定位基准的选择,零件表面加工方法的选择及加工顺序的安排的分析说明,再结合本零件的结构特点及制定工艺路线的出发点保证加工质量、提高生产率、降低成本,从而获得最好的经济性。所以,此零件制定的工艺路线是00下料05热处理10车加工15铣加工20打毛刺30清洗35最终检验1234工艺的制定341工序基准的选择工序基准是在工艺图上以标定被加工表面位置尺寸和位置精度的基准,所标定的位置尺寸和位置精度分别称为工序尺寸和工序技术要求。工序尺寸和工序技术要求的内容,在加工后应进行测量,测量所用的基准称为测量基准,通常工序基准与测量基准重合。对于设计基准尚未最后加工完毕的中间工序,应选各工序的定位基准作为工序基准和测量基准。在各表面的最后精加工时,当定位基准与设计基准重合时,虽然工序基准和测量基准就应选用这个重合的基准;当所选定位基准未与设计基准重合时,在这两种基准都能作为测量基准的情况下,工序基准的选择应注意以下几点1选设计基准作为工序基准时,对工序尺寸的检验就是对设计尺寸的检验,有利于减少检验工作量。2当本工序中位置精度是由夹具保证而不需进行试切调整的情况,应使工序基准与设计基准重合。3对一次安装下的加工出来的各个表面,各加工面之间的工序尺寸应选与设计尺寸一致。本零件在加工时,其轴向尺寸是以零件的两端作为工序基准,径向尺寸是以零件的轴心线作为工序基准。它的工序基准与设计基准重合,为加工和检测提供了方便。342确定工序尺寸的方法1对外圆和内孔简单加工的情况工序尺寸可由后续加工的工序尺寸加上(对被包容面)或减去(对包容面)公称工序余量而求得,工序公差按所加工方法的经济精度选定。2当工件上的位置尺寸精度或技术要求在工艺过程中是由两个甚至更多的工序所间接保证时,需通过尺寸链计算,来确定有关工序尺寸,公差及技术要求。3对于同一位置尺寸方向有较多尺寸,加工时定位基准又需多次转换加工的工件,由于工序尺寸相互联系的关系较复杂,就需要从整个工艺过程的角度用工艺尺寸链作综合计算,以求出各工序尺寸、公差及技术要求。根据本零件的加工工艺路线和技术要求,其工序尺寸确定如下工序10粗车右端外轮廓13工步一平端面此端面经过两次车削,粗车和精车。查表知,其轧制件端面加工余量为2MM,粗车余量为06MM,车削后达到的表面粗糙度为RA63。工步二粗车左端外轮廓本工序采用粗车半精车精车的加工方式,经查表知,其切削余量为2MM,故该工序车削后基本尺寸应为48250MM,与该尺寸对应的公差值分别是033MM,按入体原则标注,工序尺寸为MM,。035工序15工步一平端面此工步同工序10中工步一,但其加工余量是05MM。工步二粗车右端外轮廓此工步同工序10中工步二,其基本尺寸是30232MM,与该尺寸对应的公差值是033MM,按入体原则标注,工序尺寸为MM。032工步三精车右端外轮廓此工序是达到最后的加工要求,尺寸精度要符合要求。未注公差的尺寸按GB/T1804M查表知,分别为MM,1401MM,401MM,,要加工的总长度需0213进行计算,其结果是MM。57工步四切内槽此槽是作为加工螺纹时的退刀槽,查表知,其工序尺寸应为MM。032工步五车削外螺纹查表知,M26156G的螺纹EI0,中径公差是019MM,小径公差是03MM。工步六钻孔查表知,先钻一个98MM的孔。工步七镗孔表面粗糙度要求较高RE08。工序35工步一铣加工在加工中一次完成,表面粗糙度为RA16,尺寸要求不严格。工步二钻孔14查表知,其工序尺寸应为MM。1804343加工余量的确定加工余量是指加工过程中所切去的金属层厚度。其余量的大小对工艺过程有一定影响,余量不足不能保证零件的加工质量,不但增加了机械加工的劳动量,而且增加了刀具,能源及材料的消耗,从而增加了成本,降低了生产率,所以必需合理的安排加工余量。确定加工余量的方法有查表法、经验仿计法和分析计算法。本零件采用查表法,参照数控加工技术第二篇第四章加工余量表对本零件的加工余量所查结果如下表31加工表面加工方案余量(MM)粗车230外圆精车02切槽车2外螺纹车195椭圆花铣104孔钻10344机床的选择零件的加工精度很大程度上取决于所用机床,因此必须合理的选择机床,对于单件小批量生产一般选择通用机床;对于中批量则广泛采用专用机床、数控机床和组合机床。在选择机床时应注意以下几点1机床的加工尺寸范围与零件外形尺寸相适应。2机床精度与工件精度相适应。3与现有加工条件相适应。4机床的生产率应与工件的生产类型相适应。本零件尺寸小、重量轻、属中批生产,其毛坯是棒料,加工余量较大,为了合理的利用机床,故此零件在粗加工时选用普通机床,另外工件的某些部分在普通机床上很难加工出来,又因此次设计着重练习的是对数控机床的熟练程度,故精加工时选择数控机床,根据现有的生产条件,选择的机床型号是CA6140普通车床CJK6032A教学型数控车床15ZJK7532A数控铣钻床345工艺装备的选择工艺装备选择的合理与否,将直接影响工件的加工精度、生产效率和经济性。应根据生产类型、具体加工条件、工件结构特点和技术要求等选择工艺装备。1夹具的选择本零件是小批量生产,技术要求不太高,故采用通用夹具即可完成,因专用夹具的专用性能强、成本高、不易转变,不可长时间地使用,选用夹具时要保证夹具的坐标系方向相对固定,要协调零件和机床坐标系的尺寸关系夹具上各零件应不妨碍机床对零件各表面的加工。根据以上所述和现有生产条件,本零件车削与铣削时均采用三爪卡盘进行装夹。2刀具的选择在选择刀具方面,通常优先用通用夹具,对于不同材料的零件,一般都有适合将其切削的刀具。刀具的选择不仅影响机床的加工效率,而且直接影响加工质量,与传统的加工方法相比,数控加工对刀具的要求更高,不仅要求精度高、刚性好、耐用度高,而且要求尺寸稳定,安装方便,这就要采用新型优质材料制造数控教工刀具,并优选刀具参数。在选用刀具时应考虑工序种类,生产率,经济性,工件材料,生产批量,加工精度及表面粗糙度与所用机床的性能选用了标准刀具。刀具材料应当选择高硬度、高耐磨性、高耐热性的材料,并有足够的强度和韧性,较好的工艺。根据以上所述和现场加工条件,本零件选用YT类硬质合金刀具进行加工。3量具的选择量具的选择主要是根据生产类型和检测的精度来选择,一般选用通用量具,对于尺寸精度要求较高,检测不方便的选用专用量具,为了在机械加工过程中保证零件的加工尺寸精度和提高测量效率的要求,需要恰当合理地选择相应的各种通用及专用量具。此零件需选用的专用量具有椭圆花专用样板M26X156GM26螺纹塞环规椭圆弧专用样板其它尺寸选用050MM外径千分尺、050MM内径千分尺、0150MM游标卡尺即可。346切削用量的确定切削用量的合理选择,是指在保证加工质量的前提下,充分利用刀具和机床的性能,获得高生产效率和低加工成本的切削用量三要素的最佳组合。161粗加工时切削用量的选择粗加工时精度与表面粗糙度要求不高,毛坯余量较大,因此选择粗加工用量时,要尽可能保证较高的单位时间、金属切除量和必要的刀具耐用度,以提高生产率和降低成本。先考虑选择一个尽可能大的背吃刀量;其次选择一个较大的进给量F;最后确定PA一个适合的切削速度V。根据上述原则,选择粗加工切削用量,对于提高生产率、减少刀具消耗、降低加工成本是比较有利的。1)切削深度的选择应根据零件的加工余量和由夹具、机床、刀具和工件所组PA成的工艺系统的刚性来确定。2)进给量F的选择限制进给量,提高的因素主要是切削力。3)切削速度V的选择主要受刀具耐用度和机床功率的限制。2精加工时切削用量的选择精加工时的加工精度和表面质量要求较高,加工余量要小且均匀,因此选择精加工切削用量时,应着重考虑如何保证加工质量,并在此基础上尽量提高生产率。精加工时应选择较小的背吃刀量和进给量F,以保证加工精度和表面质量,同时满足生产率的PA要求。1)切削深度的选择应根据精加工留下的余量来确定。P2)进给量F的选择限制进给量,提高的主要因素是表面粗糙度。3)切削速度V的选择切削速度提高时,切削变形减小,切削力也有所减小,也不易产生积屑瘤和毛刺。根据以上切削用量的选择原则,及相关手册的数据,本零件的各工序的切削用量选择如下1平端面2MMF05MM/RPAVM/SVYXPMVKFTC607012810952607301确定机床主轴轴速计算转速R/MIN648/1504371SRDVNWS取机床实际转速R/MIN17则实际切削速度M/MIN197M/S5418075143WNDV2粗车外轮廓2MMF05MM/RV1M/SPAR/MIN取R/MIN17382501460WSDVN460WN则M/MIN120M/S31V3切槽B4F015MM/RV127M/S809R/S48535R/MIN取R/MIN50143270WSDVN460WN则M/MIN120M/S64钻98孔5MMF02MM/RV04M/SPAR/MIN取R/MIN37641036SN75WN则040M/S5WDV5精车外轮廓02MMV15M/SF02MM/RPAR/S95541R/MIN取R/MIN921530410WSDVN75WN则119M/S6766镗孔05MMV05M/SF03MM/RPA59527R/MIN取R/MIN051643106WSDVN460WN则M/S39601V7铣椭圆185MMZ365MM02MM/ZV05M/S0DPAF1910R/MIN取R/MIN51430610VNS160WN则M/S6WDV2347时间定额的确定时间定额不仅是衡量劳动生产率的指标,也是安排生产计划,计算生产成本的重要依据,还是新建或扩建工厂或车间时计算设备和工人数量的依据。因此,必须正确确定工时定额,过高和过低的工时定额都不利于生产。本零件的工时定额计算如下1平端面MIN11S190275022321IFNLLDTWJS780JF2粗车左端外轮廓MIN65S08154602921IFNLTWJS5JF3粗车右端外轮廓MIN21S350645023121IFNLTWJS5JF4切槽MIN4174S7034601523221IFNLLDTWJS405JF5钻孔MIN119S20175021IFNLTWJ19S9825JFT6镗孔MIN54S90463024321IFNLLWJS5JFT7铣椭圆054MIN3268S2316097821IZNALIVLWFFJS7825JFT20第四章数控加工程序的编制41数控加工的特点1采用数控机床加工零件可以提高加工精度,稳定产品的质量。2数控机床可以完成普通机床难以完成,或根本不能加工的复杂曲面的零件加工。3采用数控机床在生产效率上,可以比普通机床提高23倍,尤其对某些复杂零件的加工,生产效率可提高十倍甚至几十倍。4可以实现一机多用。5采用数控机床有利于向计算机控制与管理方面发展,为实现生产过程自动化创造条件。42数控编程方法及特点421数控编程的分类数控编程一般分为两种一种是手工编程,另一种是自动编程。手工编程是由分析零件图,确定工艺过程,数值计算,编写零件加工程序单,程序的输入和检验都是由工人完成的。特点对于加工形状简单的零件,计算比较简单,程序不是很多,采用手工编程(仍被广泛应用)较容易完成,而且经济,及时,因此在点位加工及直线与圆弧组成的轮廓加工中,手工编程仍广泛应用,但对于形状复杂的零件,特别是具有非圆曲线,列表曲线的零件,用手工编程就有一定的困难,出错的机率增大,有的无法编程序。自动编程用计算机编制数控加工程序的过程。特点计算机自动识图编程,编程准确,不易出错,安排走刀路线合理,从而使加工准确。本零件的凸轮加工就采用自动编程来完成的。422编程零点及坐标系的选择1所选的编程原点及坐标系应使程序编制简单。2编程原点应选在容易找正,并在加工过程中便于检查的位置。3引起的加工误差小。一般回转体零件的编程零点选在其加工面的回转轴线与端面交点处。423对刀点的选择对刀点是指在数控机床上加工零件时,刀具相对零件运动的起始点。对刀点应选择21在对刀方便、编程简单的地方。对于采用增量编程坐标系统的数控机床,对刀点可选择在零件孔的中心上,夹具上的专用对刀孔上或两垂直平面(定位基面)的交线(即工件零点)上,但所选的对刀点必须与零件定位基面有一定的坐标尺寸关系,这样才能确定机床坐标系与工件坐标系的关系。对于采用绝对编程坐标系统的数控机床,对刀点可选在机床坐标系的机床零点上或距机床零点有确定坐标尺寸关系的点上。因为数控装置可用指令控制自动返回参考点,不需要人工对刀,但在装夹零件时,工件坐标系与机床坐标系必须要有确定的尺寸关系。424加工路线的确定1尽量缩短进给路线,减少空走刀行程,提高生产率。2合理选取起刀点、切入点和切入方式,保证切入过程平稳,没有冲击。3保证加工零件精度和表面粗糙度的要求。4保证加工过程的安全性,避免刀具与非加工面干涉。5有利于简化数值计算,减少程序段数目和编制程序工作量。43数控加工程序的内容431车床程序O0001M03S900F200T0101(外圆车刀)G00X55Z2G71U1R2P1Q2X04Z04N1G01X0Z0X23X26Z15Z14X30N2Z30Z50T0100M06T0202(宽度为4的切断刀)G00X3022Z10G01Z14X20X40G00Z50T0200M06T0303(M26螺纹刀)G00X26Z2G82X257Z12F15X253X249X245X242X2405G00X40Z50T0300M0
- 温馨提示:
1: 本站所有资源如无特殊说明,都需要本地电脑安装OFFICE2007和PDF阅读器。图纸软件为CAD,CAXA,PROE,UG,SolidWorks等.压缩文件请下载最新的WinRAR软件解压。
2: 本站的文档不包含任何第三方提供的附件图纸等,如果需要附件,请联系上传者。文件的所有权益归上传用户所有。
3.本站RAR压缩包中若带图纸,网页内容里面会有图纸预览,若没有图纸预览就没有图纸。
4. 未经权益所有人同意不得将文件中的内容挪作商业或盈利用途。
5. 人人文库网仅提供信息存储空间,仅对用户上传内容的表现方式做保护处理,对用户上传分享的文档内容本身不做任何修改或编辑,并不能对任何下载内容负责。
6. 下载文件中如有侵权或不适当内容,请与我们联系,我们立即纠正。
7. 本站不保证下载资源的准确性、安全性和完整性, 同时也不承担用户因使用这些下载资源对自己和他人造成任何形式的伤害或损失。

人人文库网所有资源均是用户自行上传分享,仅供网友学习交流,未经上传用户书面授权,请勿作他用。