直齿圆锥齿轮的挤压模具设计-[机械毕业设计论文A3146]
收藏
资源目录
压缩包内文档预览:(预览前20页/共39页)
编号:971017
类型:共享资源
大小:1.27MB
格式:RAR
上传时间:2017-01-04
上传人:木***
认证信息
个人认证
高**(实名认证)
江苏
IP属地:江苏
50
积分
- 关 键 词:
-
圆锥
齿轮
挤压
模具设计
机械
毕业设计
论文
a3146
- 资源描述:
-
文档包括:
说明书一份,40页,15100字左右.
翻译一份.
图纸共13张,如下所示
A0-装配图.dwg
A0-模筒.dwg
A1-底座.dwg
A3-冲头.dwg
A3-杠杆.dwg
A3-上模.dwg
A3-上模座.dwg
A3-下模.dwg
A3-支承板.dwg
A4-定位套.dwg
A4-上模模芯.dwg
A4-推杆.dwg
A4-下模模芯.dwg
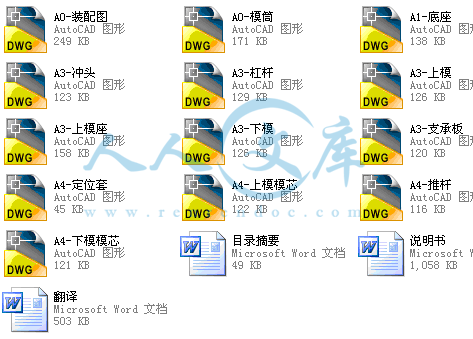

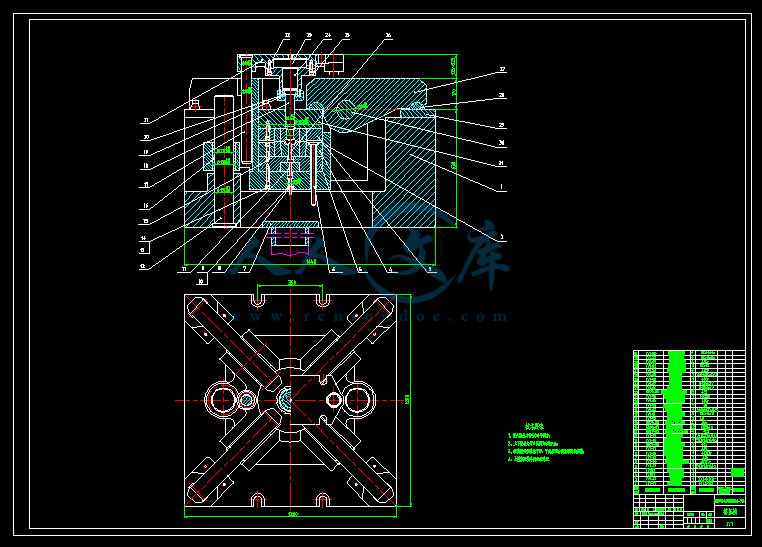
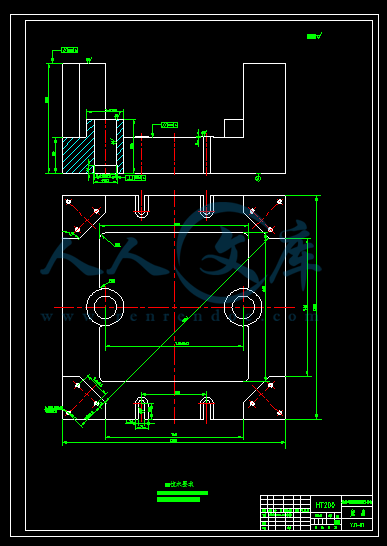
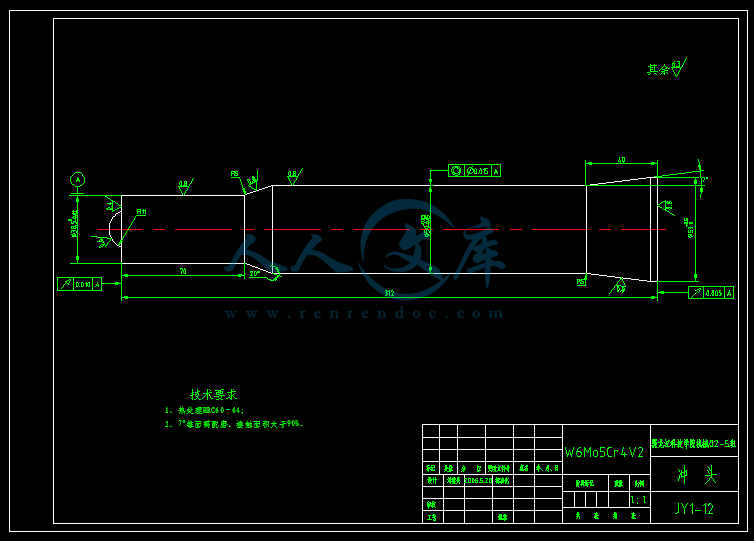
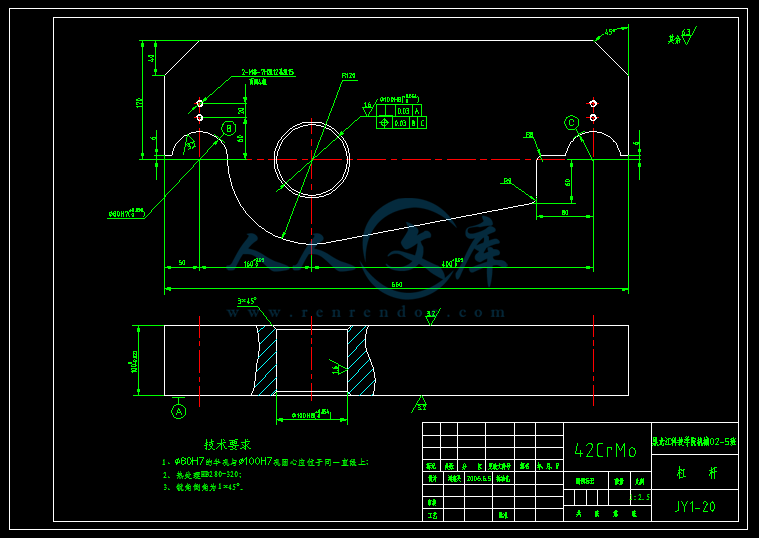







- 内容简介:
-
机 械 加 工 工 艺 过 程 卡 零件号 零 件 名 称 模 工序号 工 序 名 称 设 备 夹 具 刀 具 量 具 工 时 名 称 型 号 名 称 规 格 名 称 规 格 名 称 规 格 01 下料: 85360 自由锻 直尺 02 中心钻孔 50 铣床 虎钳 标准 麻花钻 游标卡 尺 03 粗铣:铣端面与圆周面 ,留单边余量 2床 虎钳 标准 面铣刀 游标卡 尺 04 粗铣:铣中心孔,留单边余量 2床 虎钳 标准 立铣刀 游标卡 尺 05 磨削:磨端面 ,留单边余量 床 磁力夹具、虎钳 砂轮 游标卡 尺 06 钳工:划线 ,按位置加工通孔,沉头孔 。 钻床 虎钳 钻刀、铰 刀 高度尺、游标卡尺 07 热处理:按热处理工艺 ,淬火回火达到 43 48热炉 火钳 08 精铣:铣中心孔 铣床 虎钳 标准 立铣刀 游标卡 尺 09 磨削:精磨上下平面及中心 圆锥 部分 至要求尺寸 磨床 磁力夹具、虎钳 砂轮 游标卡 尺 10 钳工:钳工精修、抛光 工作台 研磨工 具 游标卡 尺 11 钳工 :安装中套和模芯 工作台 水平仪 等 12 检验 检验 游标卡尺 高度尺 编制 校对 审核 批准 录 摘要 第 1 章 绪论 1 外的发展现状 1 内的发展现状 2 第 2 章 冷闭塞锻造概述 4 式挤压 4 闭塞锻造成形的优点 4 压件分类 6 第 3 章 直齿圆锥齿轮三维实体造型及参数分析 7 维实体造型软件介绍 7 齿圆锥齿轮几何尺寸计算 7 齿圆锥齿轮三维造型及计算其体积和质量 8 齿圆锥齿轮三维造型过程 8 算齿轮的体积和质 量 9 第 4 章 直齿圆锥齿轮冷闭塞锻造工艺方案确定 10 锻件设计 10 坯尺寸的确定 11 第 5 章 模具设计 12 压力的计算 12 闭塞锻造成形的特点 12 具工作零件设计 13 具设计前需要考虑的有关问题 13 模的设计 15 模的设计 17 杆的设计 21 向、顶出件设计 26 具总体结构设计 28 第 6 章 技术经济性分析 30 7 章 专题论文 31 结论 37 致谢 38 参考文献 39 附录 1 翻译(汉) 40 附录 2 翻译(英) 47 V 摘 要 冷闭塞锻造是国际上九十年代初出现的塑性加 工最新技术,是现代计算机技术、材料科学、精密加工、测量技术和计算力学与传统塑性成形技术相结合的产物。作为最先进的精密成形技术之一,冷闭塞锻造工艺以其精密、优质、高效、低消耗、低成本、大批量等生产特点,成为世界塑性加工技术发展的重要方向。长期以来,我国汽车生产,尤其在精密成形技术方面处于落后位置。随着我国汽车生产,尤其是轿车生产的大规模化与全球性竞争的日趋激烈,积极开发冷闭塞锻造成套技术并使之尽快产业化意义重大。本人设计的是用闭塞锻造的方法直接加工成形直齿圆锥齿轮,即通过挤压封闭腔中的坯料来加工成形直齿圆锥齿 轮,采用精锻(挤压)方法成形的齿轮有沿齿廓合理分布而连续的金属流线和致密组织,其齿轮的强度、齿面的耐磨能力、热处理变形量和啮合噪声等都优于切削加工的齿轮。与切削加工相比,精锻齿轮的强度可提高 20%、抗弯疲劳寿命提高 20%、热处理变形量比切削齿轮减少 30%、生产效率提高了 2 倍以上、生产成本降低 20%以上。生产批量在 300 500 件以上时,经济上更合理的。 关键字 :直齿圆锥齿轮、闭塞锻造、挤压、凹模、凸模 is on at 0s is of as by is so on of is in in in is by it as as My to so on as a of 0%, 0%, to 0%, 0%. 00 500, in 1 附录 1:翻译(汉) 冷锻技术的发展现状与趋势 摘要 : 冷锻技术是一种精密塑性成形工艺,具有切削加工不可比拟的优点,广泛应用于各种机械产品关键零部件的制造。本文从冷锻零件的形状、材料、工艺革新、生产率、数值模拟技术和数字化 /智能化设计技术应用、以及优化技术几个方面综合论述了冷锻技术的发展现状与趋势。 关键词 : 冷锻,工艺 /模具设计,数值模拟,基于知识的工艺设计,设计优化 。 冷锻工艺是一种精密塑性成形技术,具有切削加工无可比拟的优点,如制品的机械性能好,生产率高和材料利用率高,特别适合于大批量生产,而且可以 作为最终产品的制造方法( 在交通运输工具、航空航天和机床工业等行业具有广泛的应用。当前汽车工业、摩托车工业和机床工业的飞速发展,为冷锻这一传统的技术的发展提供了原动力,例如,我国 1999年摩托车的全国总产量就有 1126万多辆,而根据 2000年的初步估计,我国汽车的总需求量到 2005年将达到 330万辆,其中轿车 130汽车行业的锻件需求在 50锻技术在我国的起步虽然不算太晚 , 但发展速度与发达国家有很大的差距 。 到目前为止 , 我国生产的轿车上的冷锻件 重量不足 20相当于发达国家的一半 , 开发潜力很大 。 加强冷锻技术开发与推广应用是我国目前的一项紧迫任务。 1、 冷锻件的形状越来越复杂 冷锻零件的形状越来越趋于复杂,由最初的阶梯轴、螺钉 /螺母和导管等,发展到形状复杂的零件,如图 1所示为不同尺寸的摩托车花键轴与花键套,花键轴的典型工艺为:正挤压杆部 挤压花键;花键套的主要工艺为:反挤压杯形件 正挤压轴套。如图 2所示为汽车输出轴与输入轴,以及其他冷锻制品。如图 3所示为我国采用摆动碾压技术制成的各种汽车 /摩托车用锥齿轮、螺旋锥齿 轮和其他圆盘类零件,如图 4所示为日本某公司生产的冷锻零件,图 4所示的涡旋增压器,我国已经列入国家“十五”攻关项目。目前圆柱齿轮的冷挤压技术也成功用于生产。除黑色金属外,目前铜合金、镁合金和铝合金材料的冷挤压应用也越来越广泛。 2 2、 持续不断的工艺革新 冷精锻是一种 (近 )净形成形工艺。采用该方法成形的零件强度和精度高 ,表面质量好。当前国外一台普通轿车采用的冷锻件总量 40 45中齿形类零件总量达 10锻成形的齿轮单件重量可达 1形精度可达 7级。 持续不断的工艺创新推动了冷挤压技术的 发展, 80年代以来,国内外精密锻造专家开始将分流锻造理论应用于正齿轮和螺旋齿轮的冷锻成形。分流锻造的主要原理是在毛坯或模具的成形部分建立一个材料的分流腔或分流通道。锻造过程中,材料在充满型腔的同时,部分材料流向分流腔或分流通道。分流锻造技术的应用 ,使较高精度齿轮的少、无切削加工迅速达到了产业化规模。提出,对于长径比为 5的挤压件,如活塞销,采用轴向余料块的方法通过轴向分流可以实现冷挤压一次成形,而且凸模的稳定性很好;对于扁平类的直齿轮成形,采用径向余料块也可以实现产品的冷挤压成形。 闭塞锻造是在封闭凹模内通过 一个或两个冲头单向或对向挤压金属一次成形 ,获得无飞边的近净形精锻件。一些轿车精密零件如行星和半轴齿轮、星形套、十字轴等如果采用切削加工方法 ,不仅材料利用率很低 (平均不到40%),而且耗费工时多 ,生产成本极高。国外采用闭塞锻造技术生产这些净形锻件 ,省去绝大部分切削加工 ,成本大幅度降低。 冷锻技术的发展主要是开发高附加值的产品 ,降低生产成本 ,同时 , 它还在不断地向切削、粉末冶金、铸造、热锻、板料成形工艺等领域渗透或取而代之 , 也可以和这些工艺相结合构成复合工艺。提出的热锻 锻 成形技术是将热锻和冷锻结合起来的一种新的精密金属成形工艺,它充分利用了热锻和冷锻各自的优点:热态下金属塑性好,流动应力低,因此主要的变形过程用热锻来完成;冷锻件的精度高,因此零件的重要尺寸用冷锻工艺来最终成形零件。热锻 0世纪 80年代, 90年代以来取得了越来越广泛的应用,用该技术制造的零件,已取得了精度提高、成本降低的良好效果。 3 图 1 图 2 图 3 图 4 3、 数值模拟技术用于检验工艺和模具设计的合理性 用冷锻工艺成形零件时,由于金属在冷态下发生塑性变形,其变形抗力很大,因此,零件的变形比较困难,变形过程中容易出现金属充不满、锻件出现裂纹等缺陷。同时,过大的变形抗力会严重降低模具的使用寿命。长期以来 ,我国金属塑性成形的工艺设计和模具设计一直采用传统的凭经验、实验方法。这 种设计方法难以满足净形制造工艺的要求。 随着计算机技术的飞速发展和 70年代塑性有限元理论的发展,许多塑性成形过程中很难求解的问题可以用有限元方法求解。在冷锻成形工艺领域,通过建模和合适的边界条件的确定 , 有限元数值模拟技术可以很直观地得到金属流动过程的应力、应变、模具受力、模具失效情况及锻件可能出现的 缺陷情况。这些重要信息的获得对合理的模具结构 ,模具的选材、热处理及成形工艺方案的最终确定有着重要的指导意义。 目前的有效的数值模拟软件是以刚塑性有限元法为基础建立起来的 ,这 4 些软件有 :用有限元数值模拟技术可用于检验工艺和模具设计的合理性。如提出了一种由空心坯成形直齿圆柱齿轮的新工艺 : 预锻分流区 用三维有限元数值模拟软件行了数值模拟研究 , 得到了锻造载荷 变、速度分布等 , 并与传统的闭式镦挤工艺模拟的结果进行了比较。分析表明 , 传统的闭式镦挤成形直齿圆柱齿轮 , 成形载荷大 , 不利于齿形的充填。采用预锻分流区 可以大幅度降低成形载荷 ,并明显改善材料的充填性 , 可 以获得齿形角部饱满的齿轮。 用三维大变形弹塑性有限元法对齿轮冷精锻成形过程进行了数值模拟 ,对以闭式模锻为预锻和以闭式模锻、孔分流及约束分流为终锻的两步成形模式的变形流动情况进行了数值模拟分析。数值分析结果及工艺实验表明在终锻中采取分流 ,尤其是约束孔分流措施对于降低工作载荷和提高角隅充填能力等方面十分有效。 4、 数字化智能设计系统的应用 模具设计中的应用 为了适应现代生产对锻模开发的短周期、高质量、低成本要求,将先进的设计理论与方法以及计算机技术,尤其是 传统的锻模设计过程是锻模设计领域的必然趋势。模具 精度和高效益等优势正持续推动着传统的模具设计与制造方法的变革。 自 20世纪 70年代以来,国外许多单位开始对锻模 国 哥伦布实验室的 苏联的捷捷林等专家系统研究了模锻设计自动化和最优化原理,从方法学、算法模型等方面提出了全套的理论,并开发了回转体类锻件的自动化设计系统。 国内在这方面的起步较晚,上海交通大学、清华大学、华中理工大学、哈尔 滨工业大学和南昌大学等单位基于一定的平台,开发了适用于不同种类锻件的设计系统,但多数仅仅限于二维系统。到目前为止,虽然众多的研究人员先后开发了适用于不同零件的锻模设计系统,实现了工艺和模具设计若干环节的自动化和智能化,但是尚未有成熟的锻模 多工程设计人员只能采用通用的机械 于知识的设计技术及其在冷锻成形工艺 /模具设计中的应用 冷锻成形工艺和模具设计是知识和经验密集型的过程,模具设计人员 5 在长期工作中积累的经验与知识 (模具设计有着十分重要的影响。传统的 缺乏对设计过程知识的支持 ,难以胜任模具开发 高质量、短周期、低成本 的要求。因此 ,需要将传统的锻模实现这一飞跃的途径是将人工智能( 术、基于知识的工程( 术引入冷锻成形工艺 /模具设计领域,与传统的 发基于知识的设计支持系统。 基于知识的工程( 要指应用知识来解决各种工程问题,是人工智能技术在工程中的应用。由于冷锻成形工艺 /模具设计是一个包含了对知识的继承、集成、创新和管理的复杂过程,引入基于知识的设计方法以后,跨领域专家的经验与知识共享能够使得设计更加富有创造性和预见性,而且领域专家知识在整个产品的设计生命周期内的一致性保证了产品开发的成功率,大大节省了开发时间,提高了设计质量。从而使整个设计模式从经验设计向科学设计转变。 美国哥伦布贝特尔实验室开发出基于知识的预锻几何尺寸的设计系统,因设计预锻件的形状为 空间几何体,须对其几何形状进行操作,故不能单纯地用一般语言来描述推理过程。对于零件的几何信息,采用框架方法表示,在框架中用不同的槽,定义出组成零件的基本成分和它们之间的拓扑关系。设计规则是用产生式规则表示,用 J. C. . 分别建立了冷、热锻件工艺设计规则。 基于知识设计方法在冷锻成形工艺及模具的设计中的应用,将彻底改变塑性成形传统的依靠设计人员个人经验,设计过程中反复修改、设计效率不高的状态。它使用人工智能、模式识别 、机器学习等技术在设计过程中从系统知识库中提取合适的知识指导冷锻成形工艺及模具设计。目前,该项技术正在进一步发展之中,近年来,基于知识设计方法已成为锻造成形工艺 /模具设计智能化技术研究的一个热点课题。 5、 优化技术的引入 随着竞争的日益加剧,低成本、高质量和高效率是制造业所追求的目标。在锻造行业,为提高设计效率、降低制造成本和提高产品质量,必须对锻造工艺过程中影响锻件质量的各项工艺参数进行优化。由于锻造变形是一个十分复杂的问题,对于其工艺参数的优化采用传统的设计方法很难达到预 6 期的效果,随着计算机技术和塑性 有限元理论和技术的不断发展和日益完善,以有限元法为代表的数值模拟方法已广泛应用于各种金属成形问题的求解分析。因此,基于有限元分析的优化设计方法在冷锻成形工艺 /模具设计中的应用不仅是可能的,也是一种必然趋势。 从实际应用的角度来看,基于有限元分析的优化方法中最具代表性的方法有基于灵敏度分析的优化方法和基于目标函数值的拟合优化方法两种。 基于灵敏度分析的优化设计方法属于梯度型优化设计方法。该方法在具体实施时,首先确定目标函数和设计变量,然后找出它们之间的关系,推导目标函数对设计变量的灵敏度 导数公式,根据设计变 量的现有值求解出这些灵敏度信息,再利用优化算法确定设计变量的最优搜索方向,得到更优的设计变量,再求解灵敏度信息,如此反复,直到优化迭代收敛。 基于目标函数值的拟合优化方法来源于外推法。这种方法用简单的插值函数来近似逼近目标函数和设计变量之间的函数关系,通过求解这个近似函数的极值点来逼近真实函数的极值点。该方法用在锻造工艺参数优化时,目标函数值是通过有限元程序来实现的。目前,一些通用的有限元分析软件如(广泛应用于锻造成形过程的数值模拟,可十分方便地计算出应力、应变等信息,因此 ,基于目标函数值的拟合优化方法可使有限元程序与优化算法分离,适合不同的锻造成形工艺,对于锻造成形过程的参数优化比较方便。 虽然基于有限元分析的锻造工艺优化技术的研究与应用已取得了不少成果,但目前仍处于起步阶段。从目标函数的构建、优化设计变量的选取到优化方法的具体应用可以看出 ,该领域的研究还存在一些问题。 ( 1) 基于灵敏度分析的优化方法的研究和应用已取得了不少的成果,由于该方法属于梯度型优化方法,因此其收敛速度比较快。但它在实际的应用中还存在一些缺点:在优化设计过程中需要求解目标函数相对于优化设计变量的灵敏度 信息 (即导数 ),对于复杂的金属塑性成形过程的灵敏度信息的推导困难。该方法要求将求解灵敏度信息的程序代码嵌入到数值分析程序代码中,需要编写有限元分析代码和优化算法代码,编程工作量大。同时该方法优化程序通用性差。 ( 2) 基于目标函数值的拟合优化方法的优点是优化算法与有限元程序分离,可充分利用功能强大的商用有限元分析软件的优势,该方法的通用性较强。它的主要缺点是收敛速度比较慢,同时由于在拟合问题中,但设计变量取得 7 较多时,会出现许多复杂的问题如适定性问题,使得拟合过程失败。 ( 3) 锻造成形是一个复杂的过程,其理想锻 件不仅应具有符合设计要求的精确外形,而且应具有均匀的变形、合理分布的变形力和理想的质量(无宏观和微观缺陷)等。上述各个方面,都是锻造生产所追求的目标,因此对锻造过程优化设计进行多目标优化十分必要。目前这方面的研究比较少。 6、 结论 冷锻技术成形精度比温锻和热锻都要高 ,在精密成形领域有着其独特的优势。本文从冷锻零件的形状、材料、工艺革新、生产率、数值模拟技术和数字化 /智能化设计技术应用、以及优化技术几个方面综合论述了冷锻技术的发展现状、分析了冷锻技术目前存在的问题并指出了今后发展的方向。冷精锻是一种 (近 )净 形成形工艺,有着十分广阔的应用前景。 8 附录 2: 翻译(英) rt is a of to In of of is in of of is is in in so on 999 1 , 000 .3 005, 300 2 . in s So on 0s in is is a at 1、 is 9 to by he so to Is to to of he 1 , 15 3 . At in at is 2 、 he is is A is of is 0 0 to 0s, to to to in is a in or In to 10 or to to be to to 1 to u to be to a of is of u to be to is in up in is or to an so on if is 0%),is to is At It in to so on or 4 is of it is is in 980s, 0s 11 to 3 、 in in to in is to to be so on At to to on 0s in is 12 to be to to In to as so in 5 by to in as as so to on is of to in 6 on To as in by of of on 13 in to of to to in to so on is 4 、 AM in n n to to as as in AD be AD by so on is to 0th 0s, to AM so AD s so so on of is in so on in So AM to 14 AM on on in n in to AD to of of Is to to AD to on is on he AX on on to to of is in As a of he m I 第 1章 绪 论 直齿圆锥齿轮是应用极为广泛的重要传动零件。因其形状复杂,材质、尺寸精度、表面 质量及综合机械性能均要求很高,很难以常规的塑性加工技术生产 。 目前 , 加工直齿圆锥齿轮 主要还是以机械加工为主,而采用机械加工又费时、费料、效率低、工序长, 所以 本设计 采用 冷闭塞锻造 制坯再 进行少量 切削加工 (或无机加工) 的制造方法。 近年来,随着机械工业,尤其是汽车工业的飞速发展与国际竞争的激化,零部件及其设计与生产过程的高精度、高性能、高效率、低成本、低能耗、省资源已成为提高产品竞争力的唯一途径。常规切削加工技术和完 全 拘泥于传统的粗放型塑性加工制坯工艺难以满足要求,传统的塑性加工技术与现代高新技术全方位的密切结合,实现塑性加工的智能化、精密化、高效率低成本以及可持续发展,已成为现代塑性加工技术发展的普遍趋势和方向。 1 1 国外的发展现状 在汽车工业发达的国家,冷精密锻造技术迅速发展并发挥重要作用。冷精密锻造技术已经 从最初简单的自行车零件、农用机械零件、普通精度零件的应用向汽车高精度复杂锻件方向突破,其中最为引人注目的是以精密冷塑性成形技术作为基本支持的轿车复杂结构零件的产品设计。 冷闭塞锻造工艺是近 几 年发展起来 的先进制造技术。作为精密复杂零件生产的重要途径,冷闭塞锻造技术,又称为复动成形技术,因其精密、优质、高效、低消耗、低成本、大批量等生产特点而为汽车工业所瞩目。以智能化技术为应用背景的冷闭塞锻造工艺成为现代塑性体积成形技术发展的重要方向。 当前钢制零件的冷锻技术最为发达的国家 当首推日本和德国。德国自五十年代起就将冷锻技术应用于金属加工工业。曾被用于军工生产的冷锻技术现在主要的面向对象是汽车工业,其中 70%用于轿车业。在欧洲 ,轿车冷锻件总产量每年达到 20 万吨。这些零件代替了过去采用机加工或热锻成形的零件,广泛用 于变 速箱、差速器、发动机、驱动和转向系统。德国舒勒公司的统计结果表明: 德国冷锻件总产量的增加已远远高出轿车产量的增长,冷锻成形工艺的应用范围及其在轿车零件中的品种不断扩大。在轿车工业发达 2 的日本,冷锻技术受到特别重视,六十年代冷锻技术主要用于轴类、活塞销、回转体法兰、紧固件等简单零件;七十年代发展到形状复杂的产品;八十年代以后开发出伞齿轮、等速万向节、十字轴等高难度冷锻件。 当代国外的冷锻生产具有下列特点: ( 1)冷锻已由单工位发展到多工位生产, 以合理减少每工序的变形量,减轻模具负荷,增加模具寿命,提高工艺稳 定性。 ( 2)由冷锻发展到温锻进而又由温锻发展到温冷联合成形工艺,以适应大型高精度零部件的生产。 ( 3)闭塞锻造工艺的应用越来越广泛。由于可在一次变形工序中获得较大的变形量和复杂的型面,并且具有高效率及较高的模具寿命,因此闭塞锻造特别适合复杂零件的精密成形。现已发展了闭塞锻造专用压力机和在通用单动压力机实现闭塞锻造的专用模架。 ( 4)冷锻专业化生产程度越来越高,锻造专业厂、专业模具厂迅猛发展。 ( 5)冷锻设备得到充分的发展、高质量、高性能的多工位冷压力机、闭塞锻造专用压力机等获得广泛的应用。 ( 6)冷锻用钢 专门化。美国、德国、日本等都根据本国的资源情况发展了冷锻专用钢。如美国侧重于发展含硼的 冷锻钢,而日本、德国 主要发展含铬、钼的冷锻用钢。冷锻专用钢的开发和使用,不仅使冷锻生产效率有很大提高,更主要是从材料上充分满足了冷锻的工艺要求,提高了冷锻工艺水平,降低了冷锻成本。冷锻专用钢的发展和冷锻技术的发展互相促进,形成了良性循环。 ( 7)计算机应用技术得到广泛应用。由于冷锻零件复杂性及市场对于开发周期,制件质量及成本的要求,以有限元技术为先导与核心的数值模拟与分析技术已成为冷温成形研究与应用中的重要方面。 术已较多地应用于模具设计、工艺设计和模具失效分析方面。 ( 8) 成形零部件品种越来越多,体积越来越大,形状越来越复杂。冷锻部件由传统的活塞销、轮胎螺母、球头销等发展到等速万向节,发电机爪极,伞齿轮、十字轴、三销轴、变速器、螺旋传动齿轮、汽车后轮轴等。 ( 9)以计算机辅助技术为依托,冷锻生产由大批量向多品种小批量方面发展,顺应产品生产的个性化发展趋势。 1 2 国内的发展现状 3 在国内,由于各方面的原因,特别是由于汽车工业长期处于小批量生产,我国的冷锻技术未能得到健康的发展。至二十世纪八十年代,除了 少数自行车零件和汽车标准件以及活塞销等生产坚持冷锻工艺外,绝大部分汽车零件采用热锻 机加工工艺生产。建国以来,我国汽车生产主要围绕载重车进行发展,轿车作为奢侈品,在相当长的时间内没有得到发展。因此我国冷锻生产虽然起步较早,却迟迟未有发挥其巨大优势的用武之地。此外冷锻生产涉及成形工艺技术、 模具技术、材料科学、表面处理技术乃至质量管理等当代科技硬件和软件技术,相关工艺技术也制约了冷锻技术发展和工艺水平的提高。 近 几 年,随着我国汽车尤其是轿车工业的发展,国内企业界有识之士已充分认识到这一点。轿车工业高投入,大批量 和高技术含量的要求,其零部件结构复杂、精度高,使得采用纯切削加工方法引起的耗时、费料等诸多弊端已远不能令企业接受。国内一些专业生产厂如扬州第一汽车齿轮厂、扬州太平洋精密锻造公司、江苏森威集团,相继引进了日本冷锻技术和设备、瑞士冷摆碾设备等,用于包括轿车差速器伞齿轮、等速万向节 星形套、花键轴等冷精密复杂零件的研制。近年来,吉林大学辊锻所在国内率先开展了直齿圆拄齿轮冷精密锻工艺及其相关生产技术的研究,取得良好效果。目前正在自主研究开发轿车复杂零件冷闭塞锻造技术。 有关专家指出,以轿车工业的迅速发展为契机,推动我 国冷精密锻造及相关技术的发展与进步,使我国冷精密锻技术进入世界先进行列,是国内塑性加工业现在乃至未来数年的主攻目标。 4 第 2 章 冷 闭塞锻造概述 2 1 闭式挤压 冷闭塞锻造技术特别适合生产类似直齿圆锥齿轮、差速器伞齿轮、等速万向节星形套、十字轴、三销轴等形状复杂、性能要求高、加工难度大的关键零部件。 冷 闭塞锻造就是 在室温下通过 闭式挤压 坯料使之 直接成形为产品 零件。闭式挤压是金属压力加工的一种无切削加工工艺,将挤压模具装在压力机或液压机上,利用压力机或液压机的往复运动,在室温下使 金属在三向压应力状态下发生塑性变形,从而挤出所需尺寸、形状及性能的零件。 从金属塑性变形原理可知,当金属坯料处于三向应力状态下变形时,能大大提高金属的塑性,允许金属有较大的变形。因此,金属挤压工艺不仅可以成形各种复杂的零件,而且还使低塑性金属和合金有成形加工的可能性。由于闭式挤压坯件受三向不均匀压应力作用,故可得到坯件与挤压中凸模紧密贴合的高精度型腔。 但挤压所需的单位压力大,基准凸模受压力很大(高达 1800 3500因而降低了凸模的使用寿命。即使挤压中等尺寸的型腔,也需要很大的压力。闭式挤 压时,需采用容料坑或者减压穴的坯件,使被挤出的大部分金属流入其中,减小单位挤压力。 2 2 冷闭塞锻造成形的优点 在机械制造工艺领域内广泛采用挤压先进技术,取得了显著的成效。近年来,各种挤压工艺的发展,已使它成为金属压力加工中先进工艺之一,无论在技术上和经济上它都有很多的优点。 ( 1) 节约原材料,降低成本。复杂零件冷闭塞锻造技术可实现少无切削加工,显著提高了材料利用率,节省大量的优质钢材,大幅度降低了生产成本。以下图所示的接头为例:旧工艺用棒料直接车出零件,后改用挤压毛坯,使生产率提高了 ,材 料利用率提高 。 5 挤压件 车出件 ( 2) 省工时、 缩短生产周期 、 提高生产效率。在现代工业体系中,提高大量生产的水平实际上就等于降低了每个零件的价格。采用冷闭塞锻造工艺可一次成形 精密复杂汽车零件,省去了大量机加工工时,大幅度提高了生产效率。 ( 3) 降低能源消耗、节省了设备投资。冷闭塞锻造属无飞边、复动精密成形。工作压力小,总工序的减少带来了设备投资 、刀具消耗及燃料动力费用等的大幅度降低,节省了能源消耗。 ( 4) 成形件综合性能优良,提高了零件的机械性能。切削加工把金属内部的纤维割断,从而降低了零件的机械性能。冷闭塞锻造精密成形,在挤压的过程 中,金属是处于 三向应力状态,变形后能在成形零件内部形成致密均匀的材料纤维组织,金属流线 沿表面轮廓连续、且分布合理,形成表面加工硬化层 以及圆滑过度的圆角沟槽。由于冷闭塞锻造精密成形制件的主要轮廓(如齿轮齿面)不再进行机加工,这种合理的金属纤维及良好的表层组织并不破坏, 而且在挤压的过程中产生很高的温度,相当于对制 件进行了一次热处理, 从而大大提高零件的耐磨性、机械性能与疲劳寿命等 。 ( 5) 提高了 零件的精度及表面粗糙度并且模具寿命高。在挤压过程中,金属表面在高压下受到模具表面的熨平,因此零件的表面粗糙度很细,寸精度的公差范围最高可控制到 压工艺可以获得较理想的制件表面粗糙度与尺寸精度,有些零件经挤压之后不再进行切 6 削加工 。 ( 6) 可加工形状复杂的零件。在压力机的往复直线动作下完成复杂的加工工序,并可以制成形状复杂的零件,如锥齿轮、十字轴等。 2 3 挤压件分类 多数 挤压 件的外形以轴对称为主。由于零件的形状不同,挤压变形时应根据零件的变形方法及模具中金属流动方式不同。挤压件有 : 正挤压件 :挤压时金属流动方向与凸模运动方向相同; 反挤压件 :挤压时金属流动方向与凸模运动方向相反; 复合挤压件 :挤压时金属沿凸模运动方向和相反方向同时流动; 径向挤压件 :挤压时金属流动方向与凸模运动方向垂直。 另外还有 斜向挤压件及敦挤件。 而 闭塞锻造主要以反挤压件为主。 7 第 3 章 直齿圆锥齿轮三维实体造型及参数分析 3 1 三维实体造型软件介绍 通过应用软 件对零件特别是复杂零件进行三维造型,然后,通过软件自身的分析或其他功能可以直接得到零件的某些参数,如复杂零件的体积、质量 、 面积等 ,这样可以简化很多设计步骤,而且得到的结果更准确。现在流行的三维造型软件主要有 。 称 e)是美国参数公司推出的新一代 成化机械设计软件,由于其强大的功能,可为机械设计、分析、加工一体化提供一整套解决方案,很快得到普遍欢迎,并迅速成为当今世界应用最为广泛的 件之一。 e 软件 的特性 8 : e 独特的参数化设计概念,除了采用单一数据库的设计、支持同步工程的功能之外,还包括以下特性: ( 1) 3体模型。 e 摆脱了传统线创建、面创建,改用 3体架构,除了可以将模型真实地呈现在设计者的面前外,更可以轻易地计算出实体的表面积、体积、重量、惯性矩和重心等物理量,让用户更真实地了解产品的特性。 ( 2) 以特征为基础的参数式模型创建。 ( 3) 参数式设计。 e 配合其独特的单一数据库设计,将每个尺寸视为可变的参数,只要修改这些 参数的尺寸,相关的实体模型即会依照尺寸的变化重新产生,达到设计变更的一致性。借着参数化的设计,设计者可以运用逻辑关系式或数学运算方式建立尺寸与尺寸之间的关系式( 如此可以减少人工改图或计算所花费的时间并减少错误的产生。 3 2 直齿圆锥齿轮几何尺寸计算 直齿圆锥齿轮用于相交两轴之间的传动。 本次设计的直齿圆锥齿轮的几何参数为:齿数 z=10,模数 m=向齿形角 n=22 30,分锥角=32 ,根锥角 f =27 24, 锥齿轮精度为 圈跳动公差距极限偏差 8 该直齿圆锥齿轮的几何参数计算公式及结果如表 1 所示 。 表 1 直齿圆锥齿轮的几何参数计算公式及结果 参 数 名 称 计 算 公 式 计 算 结 果 分度圆直径 e=4 锥距 e=顶高*根高 (c*)m 端齿顶圆直径 a=a 度圆 齿厚 S S=2 之啮合齿轮齿数 2z 2z =z/16 3 3 直齿圆锥齿轮三维造型及计算其体积和质量 3 3 1 直齿圆锥齿轮三维造型过程 为了 节省时间,本次设计直接应用了 e 的参数化设计的功能,通过改变已有直齿圆锥齿轮的相关参数(如模数 m、齿数 z、分锥角 等) 而得到 所需齿轮的实体三维图,其具体过程如下: ( 1) 调用直齿圆锥齿轮。 在 e 环境下从零件库中调出直齿圆锥齿轮; ( 2) 改变参数。依次单击工具 程序 编辑设计,然后在弹出来的记事本窗口中输入相应的参数:模数 m=数 z=10、 齿宽 B=16、 啮合齿齿数 2z =16; ( 3) 完成三维图形。如图 3 1 所示 : 9 图 3 1 3 3 2 计算齿轮的体积、质量 由于冷闭塞锻造 对坯料的体积及质量要求 一般很 严格,大了容易损坏模具,小了金属不能充满型腔,所以必须精确计算出齿轮的体积和质量。而 在e 环境下可以直接应用 e 自身的模型分析功能得到三维图形的体积,并且在输入相应密度的情况下可以计算出零件的质量 ,而且由此得到的体积和质量很精确。通过应用 e 的模型分析对得到的直齿圆锥齿轮进行计算得到以下数据: 体积 V=密度 =3质量 M= 10 第 4 章 直齿圆锥齿轮冷闭塞锻造工艺方案确定 直齿圆锥齿轮冷闭塞是一种精密成形加工技术,精度要求一般都很高,所以 在考虑工艺方案的时候,要把达到要求的精度作为首要出发点。工艺设计是直齿圆锥齿轮闭塞锻造 模具设计的基础,它是模具设计的主要技术依据,工艺设计的好坏,直接影响到制件的质量、成本、生产效率和模具寿命等很多方面。 4 1 冷锻件设计 根据零件图 确定冷 锻件时,主要考虑如下方面 4 : ( 1) 分模面安置在锻件最大直径处,能锻出全部齿形和顺利脱模。 ( 2) 齿形和小端面不需机械加工、不留余量。背脊面是安装基准面, 挤 压时不能达到精度要求,预留 1械加工余量。 ( 3) 圆角半径不能太小,否则容易造成充不满。 产品零件图如 图 4 1 所示 。为了保证模锻后顺利脱模及齿形的完整性,将分模面选在零件的最大截面处,即图中的 A 处。 模 数m 5 . 4齿 数z 10齿 形 角 d e 54锥 距 R e 5 0 . 9 5分 度 角 32 ?齿 厚 B 16根 锥 角 27 ? 2 4 齿轮精度 G B 1 1 3 6 5 - 8 9齿轮跳动公差 F 0 1 822 ? 3 0 图 4 1 11 采用冷闭塞锻造技术,其目的是为了提高锻件的尺寸精度,生产尽量接近零件最终形状的产品,甚至提供或成品 零件。因此在制定锻件时,对其机械加工余量、公差和圆角半径应予以充分重视。由于本次设计的模具是一次加工成形直齿 圆锥齿轮,所以锻件图与零件图基本一致(如上零件图)。 4 2 毛坯尺寸的确定 毛坯的体积的大小直接影响到锻件充填结果的好坏。如果毛坯料尺寸过小,将导致模腔充不满;体积过大,则会导致模具和设备负载过大从而造成模具和设备的损坏 ,所以在必须准确确定毛坯料的体积。 本次设计采用圆柱形坯料,其直径 d=前述可知直齿圆锥齿轮的体积为 V= 则:由 V= 有: h=2 = =23选用直径 d= h=23圆柱形毛坯,其材料为 20 钢。 闭塞锻造是对传统机械加工方法的一次重大改革,它省去了齿形 部分的机加工,齿形可一次成形, 直齿圆锥齿轮 加工工艺流程 大致 如下: 下料 冷闭塞锻造成形 切削加工 热处理 检测 12 第 5 章 模具设计 5 1 挤压力的计算 挤压力是模具设计、模具材料和挤压设备吨位选择的依据。 确定挤压力包括两项内容:决定在凸模上所承受的单位挤压力,目前冷挤压模具钢所能承受的许用单位挤压力为 2500定此工序变形所需的总吨位。将凸模上承受的单位挤压力乘凸模的水平投影面积,即可算出变形所需要的总挤压力。 挤压力的确定方法很多,有图算法、公式计算法等。下面应用公式法来计 算闭塞锻造过程中所需要的挤压力。 计算过程如下: 由 3 有: 坯料拉伸强度挤压力: 1000P F 其中: P 挤压型腔所需的压力 凸模的投影面积 2 单位挤压力 模的投影面积为: F=42d (其中 d= F=4 =文献 5 有b=380由文献 3 表 9 5 有 则挤压力为:1 0 0 0 6 32 0 8 0P =13 5 2 冷闭塞锻造成形特点 冷闭塞锻造成形过程(见下图 5 1)如下:先将上下成型模具闭合并施加一定的工作载荷 1P 压紧,毛坯在封闭的模腔内产生一定的变形,再由复动式凸模施加压力 2P ,3P,使毛坯产生多向流动,从而在一道变形工序中齿轮零件冷精密塑性成形。 图 5 1 5 3 模具工作零件设计 5 3 1 模具设计前需要考虑的有关问题 1、综合情况考虑 ( 1) 挤压件的使用条件; ( 2) 挤压件的性能要求:如强度、硬度、冲击韧性等; ( 3) 挤压件的结构形状:如是否适合挤压工艺,脱模是否有困难; ( 4) 挤压件的精度要求:如尺寸精度,位置和形状等; ( 5) 挤压件的表面粗糙度要求; ( 6) 挤压件的生产量:包括批量及长远的需要情况 ; ( 7) 挤压件的成本费用。 14 2、挤压件的形状合理性 ( 1) 避免内锥体形状。挤压内锥体零件,模具寿命低。对此应加大余量,挤压后用切削加工得到。 ( 2) 避免径向有局部金属积聚或有辐板、十字筋等形状。因为这类零件成形时,在挤压方向上的金属流动不能局部积聚,金属流动困难。 ( 3) 避免锐角。因为锐角处金属流动困难,阻力升高,模具转角处容易磨损和开裂。在允许的情况下,应尽量将挤压件改为圆角。 ( 4) 避免零件壁上有环形槽 和径向孔。 3、冷挤压过程的关键问题 在冷挤压成形的过程中,通过冷挤压模具对挤压坯料作用挤压力而使其变形,而被挤压材料对模具施以反作用力以反抗变形。如果模具的承载能力大于挤压力,就可以顺利地将制件挤成,如果模具的承载能力小于挤压力将引 起模具损坏。 而且在挤压的过程中产生很大的开模力,如果不能克服开模力,制件也不能挤成。 在很多情况下(如本次设计冷挤压 20 钢),这是冷挤压能否正常进行的关键问题。 为了解决这个问题,使冷挤压技术能付诸生产实践,就必须设法降低压力,提高模具的承载能力,为此 考虑以下问题并给予解决: ( 1) 选用适合于冷挤压加工的材料,如本次所选材料 20钢; ( 2) 设计合理的、工艺性良好的被挤零件结构; ( 3) 采用合理的冷挤压工艺方案,使每道工序的挤压力均不超过模具的承载能力; ( 4)选用合理的毛坯软化 热处理规范; ( 5) 采用合理的毛坯表面处理方法与润滑剂; ( 6) 设计制造适合冷挤压特点的模具结构,既保证产品 质量,同时又具有较长的工作寿命,较高的生产率与工作上的安全可靠。如本设计采用 4个杠杆来克服开模力。 ( 7) 选择适合于冷挤压工艺特点的机器与设备。 4、模具设计要求 冷挤压时单位压力较大,模具应当符合以下要求: ( 1)凸凹模工作部分应当有较高的强度与较长的使用寿命; ( 2)凸凹模工作部分能简捷而可靠地固定在模架上; 15 ( 3)模具的易损部分拆换方便; ( 4)毛坯放置容易,定位 准确,在大量生产时有可能采用半自动或全自动送料。如本设计采用坯料外圆和冲头端面定位; ( 5)挤成的工件可以方便取出,本设计采用顶料杆将工件顶出; ( 6)模架能牢固地安装在压力机上,本设计采用四个紧固螺钉将模架 固定在液压机的 T 形底座上; ( 7)制造简单,成本费用低。 ( 9)保证操作工人安全。 与一般模具相比,冷挤压模具的特点是: ( 1)模具工作部分的材料选择较为严格; ( 2)模具工作部分应尽量采用光滑圆角过渡,防止由于大小直径剧烈变化应力集中而损坏模具; ( 3)模具工作部分与上下底板之间应当有足够的支 撑面积与足够厚度的淬硬垫板以承受压力,扩大承压面积,减小上下底板上的单位压力; 5 3 2 凸模(冲头)的设计 1、凸模材料的选择 承受很大的压力,(单位压力 ),为保证凸模在高压下工作,凸模应具有高的强度、硬度、足够的韧性和耐磨 凸模性,凸模的材料应有良好的淬硬性和淬透性,且淬火变形小。此外,模具材料还应具有良好的切削加工性,以便于模具的机械加工。 由 3 表 9 11 及单位挤压力 取凸模(冲头)材料为: 2、凸模 (冲头) 设计 凸模(冲头)承受最大的单位挤压力和最大的局部压力。所以,在设计凸模(冲头)时必须综合考虑其各个部分的受力情况,特别要注意集中应力的产生,否则会因某部分应力过大而导致冲头断裂。综合考虑采用图 5 2所示的冲头形式 5 ,它既可以减少单位压力,又可以保证壁厚均匀。 其中: d 为工作带直径且 d= d ) =( 16 =( d ; d)d 1 取 ; (d)(d 2 0( 取 。 图 5 2 由于在挤压的过程中,凸模承受很大的压力,所以在 R 处均采用圆角过渡,以防止在 R 处产生集中应力而使凸模开裂,从而可以延长凸模的使用寿 17 命。 最后得到冲头如 图 5 3 所示 ; 图 5 3 5、 3、 3 凹模的设计 3 冷挤压凹模承受很高的单位压力。 为了提高凹模的承载能力,有效延长模具的使用寿命,冷挤压凹模采用预应力压套加强的组合式凹模。 组合式凹模设计应包括预应力压套结构形式的确定,压套尺寸的设计及过盈的经验选取。 1、 组合模结构设计需要解决的问题 ( 1) 凹模强度 凹模强度与坯料的形状和尺寸、坯料材质、锻件的精度、模具结构及模具的材料性能等有关。 由 1 表 2 39,凹模模芯采用高强度、高韧性、耐磨性高、抗压强度大的材料 ( 2) 模具的弹性变形 由于冷锻件变形力很大,模具会产生一定的弹性变形,锻件出模后有弹性恢复现象,此因素是设计凹模型腔尺寸比较关键的问题。弹性变形估计过小,锻出的锻件尺寸过大,不符合锻件要求。弹性变形估计过大,会造成锻件尺寸过小,机械加工余量不足,尺寸精度超差,造成废品 。所以设计凹模型腔时必须严格按照产品零件图进行选择。 2、 组合式凹模的结构形式 设计 18 为了在凹模内壁产生足够大的预应力,可以采用一个或多个带有一定过盈量的预应力压套。压套数目在 1 3 个范围内,依单位压力数值的大小而定。当单位压力小于 1000,可以 采用整体式结构凹模,即不镶预应力压套;大于 1000小于 1600,采取一个压套单压配合的双层组合凹模;大于 1600小于 2200,选用两层压套 双重配合的三层组合凹模。 由于冷闭塞锻造变形力比较大,凹模承受较大的单位压力,同时凹模弹性变形较大, 由 3 表 9 5 且 20 钢的单位挤压力为 2080以采用 预应力 三层组合凹模 结构 , 以提高凹模的承载能力和减小弹性变形 , 如 图 5 4所示 : 其中: 1d 为 凹模内径即挤压件最大直径 1d = =1 30 由文献 3 表 6 4 有: 2d =(1d =( =(113.8) 2d =100 3d=(1d =( =(205.3)取3d=1704d =(4 6) 1d =(4 6) =(379.0)取 4d =350 19 图 5 4 综合 考虑零件的尺寸及结构形式并设计出型腔的结构,最后得到下凹模零件图如图 5 5 所示及上凹模零件图如图 5 6 所示。 图 5 5 20 图 5 6 3、组合凹模的装配 为了 装配方便和容易得到所需的过盈量,将配合面都做成 1 30的斜度如图 5 5 所示,此时轴向压 合量 C 由下式计算: C= 斜度; 径向过盈量; C 轴向压合量。 又: = d 由参考文献 3 表 6 4 有 2 =2d =100=d=170以: 2 = 22 d =00 =33 d=70 =此,模芯与中模的压合量为: 21 2C =中模与外套的压合量 为: 3C=组合式凹模的装配是生产中的重要环节,对于能否获得预期效果有直接影响,常见的装配方法有: ( 1)加热装配 利用热胀冷缩原理进行组装的一种方法。这种方法是将压套加热至一定温度后,再将镶块自由放入其中,使镶块在压套中处于浮动状态进行冷却,当压套冷却后便将镶块自然箍紧。 ( 2)室温下压入装配 在室温下,用油压机将镶块与压套沿着配合锥面进行压合 。 ( 3)配模装配 在室温下,先按要求加工出内孔,然后根据压合量一边磨外圆一边测量,进行试探性地装配。 5 3 4 杠杆的设计 采用 杠杆原理来克服开模力是本次设计的创新之处 。 1、开模力的计算 由前述可知,冲头的单位挤压力 P=2080上模型腔受力分析如图5 7 所示。 22 图 5 7 由参考文献 6 有: = 2 2s o 其中 如右图 : 斜面上的正应力 P ( x x 轴方向上的应力 58 y y 轴方向上的 应力 xy 切应力 横截面上的正应力 为 单位挤压力 P; 倾斜角 。 易知: P=2080058 , x, yP=2080则: P=58 23 = 0582c o = 43 0220 80 =用 e 的模型分析功能可以计算出 P 应力的作用 面 面积,即图 5 7 中的圆锥台的侧面积为: S=所以, 侧面的 1P 受力为 ; 1P = SP =10 =开模力为: F=1P 即: F= =、 杠杆尺寸的设计 根据模具底座的结构及其尺 寸以及杠杆的工作原理,采用 4 根对称分布 的杠杆来克服开模力,并初步定出杠杆的形状及尺寸如图 5 8 所示。 图 5 8 24 4、 校核 图 5 9 如 上 图 5 9 所示为 初步拟订的 模具结构的图 形 。 当 冲头 3 对毛坯 闭式挤压时 ,由于 金属 流动会产生三向应力, 所 以对上模将 会 产生侧向挤压力,从而导致开模力 F 的产生 ,由于本次设计采用 4 根杠杆来克服开模力,则为了克服开模力, 在杠杆与 压板 2 及半圆块接触的 A 处必须有向下的压力 根据力的传递性 ,当冲头 3 对毛坯施加挤压力 P 时,力通过下模 4 及垫板5 传递给模筒 6,而杠杆通过销轴作用在模筒 6 上 。所以,当模筒 6 受挤压力往下运动时,除了受冲头 3 传递的挤压力以外,还受到销轴 1 对它的 在 上的阻力 2F , 则由文献 6 及作用力与反作用力原理可知 ,在 A 处必有反作用力 1F ,在 B 处必有反作用力 2F ,在 C 处必有一个向上的力 即杠杆的受力情况如下: 25 由 前述易知 : 2F =4P=4 杠杆原理对 C 点取矩有: 22211 L(F 则有: 1F =212 F =333104 0 01 6 0 104 0 5 )(=以 4 根杠杆可用于克服开模力的总力为: 总F=4 1F =4 =为 : 总=杠杆可提供的压力大于开模力,所以可选用该杠杆,即该杠杆符合要求。 26 5 3 5 导向、顶出件设计 1、导向装置 由于本次挤压件的精度要求较高( 7 级),故 本模具结构采用导柱导套导向 2 。其设计原则是: ( 1) 在上止点或当凸模与工件接触时,导柱进入导套的深度不得小于15 18 ( 2) 在下止点,导柱的上端与模板之间的距离不得小于 10 12 ( 3) 为预防偏心载荷, 进一步提高导向精度和工作稳定性,导柱直径应适当加粗,一般取 40 60要时可取 80 120且要求导柱对称分布。 根据以上原则,本模具采用 2 根对称的导柱,导柱结构如图 5 10 所示。 图 5 10 2、 顶出与卸料装置 ( 1) 顶杆 2 本次设计采用如图 5 11 的顶杆推顶结构的顶杆,其材料为 40具有使用可靠,调整方便,便于加工和更换,经济合理耐用等优点。 27 图 5 11 ( 2)顶料杆 2 本设计采用如图 5 12 所示结构的顶料杆,其材料为 种结构的顶料杆前 端为圆弧形状,有利于金属流动,减小挤压件的底部毛刺,而且加工也方便。 图 5 12 28 ( 3)开模顶杆 图 5 13 本模具结构采用 3 个 120等分布的开模顶杆,顶杆结构如图 5 13 所示,其材料为 40 5 4 模具总体结构设计 图 5 14 1 底座 2 模筒 3 上模 4 下模 5 垫板 6 开模顶杆 7 顶板 8 顶杆 9 导 套 10 螺钉 11 垫块 12 导柱 13 螺钉 14 弹簧垫圈 15 螺钉 16 铜套 17 上导柱 18 冲头 19 螺母 20 定位套 21上模座 22螺钉 23承 29 压垫 24承压柱 25冲头座 26顶料杆 27杠杆 28半圆块 29支承板30销轴 31压块 综合前面所述,由于冷闭塞锻造变形力比较大,凹模承受较大的单位压力,同时凹模弹性变形较大,因此采用三层组合预应力结构, 以提高凹模的承载能力和减小弹性变形;为了提高锻件精度,便于调整模具,减少模具错移,采用四个导柱导向,其中两个为上导柱;为了防止冲头断裂,提高冲头的使用寿命,采用四个杠杆结构并通过销轴连接在模筒上来克服闭式挤压时产生的开模力,同时也减轻对了液压设备的选择要求,即可以选择相对吨位比较低的液压设备。由文献 13,设计出模具的结构如图 5 14 所示。 其工作过程大致如下:首先将毛坯从压块 31 的中心孔中放入,然后通过压力机对上模座 21 施加压力并通过上导柱 17 导向而向下运动,从而使冲头18 与毛坯接触而对毛坯施加挤压力以至毛 坯在型腔中成形。 30 第 6 章 技术经济性分析 用冷闭塞锻造挤压成形的 直齿圆锥齿轮比温、热模锻成形的直齿圆锥齿轮精度更高,一般热模锻件能达到精度为( 模锻件为( 冷锻件为( 20 23 10000通挤压液压机上仅只用一次挤压便能成形。成形后的零件无须或者只需少量机加工。 应用闭塞锻造加工成形的直齿圆锥齿轮其齿形表面精度可达 7 级,表面粗糙度 m,无飞 边,材料利用率为 90%以上,而且尺寸精确,宏观组织比机械加工的更致密,流线方向与锻件的轮廓形状一致。而且这种模具的优点是结构和紧固机械部分都比较简单且工作可靠。此外,该模具只需采用普通的液压设备就可以进行大批生产,具有设备投资少,模具成本低,发效快等优点。与热精锻加工的直齿圆锥齿轮齿形表面精度 8 级,表面粗糙度 m,锻坯需进行切边,钻孔等后续加工,材料利用率为 76%相比,经济效益十分显著:该直齿圆锥齿轮锻件按年产量 10 万件计算,每个锻件的才料可节省 每年节约材料 ;与切削加工相 比,精锻齿轮的强度可提高 20%、抗弯疲劳寿命提高 20%、热处理变形量比切削齿轮减少 30%、生产效率提高了 2 倍以上、生产成本降低 20%以上。 31 第 7 章 专题论文 齿轮在模锻后 ,如何解决齿不易充满型腔的问题 摘要: 由于直齿圆锥齿轮的尺寸精度与质量要求一般都很高,难以采用常规的塑性加工技术成形。冷闭塞锻造技术是近年发展起来的精密成形技术。然而,在采用冷闭塞锻造成形直齿圆锥齿轮时,金属能否充满型腔直接影响到直齿圆锥齿轮的尺寸精度和产品的加工质量。本文分析了成形过程中影响金属充满的一些情况 并采取了相应地解决措施。 关键字: 直齿圆锥齿轮、闭塞锻造、 模腔 of is in to to 随着机械工业的迅猛发展及外向型经济的日益扩大,对模锻行业的装备及工艺技术提出了更高的要求。采用新型模锻工艺 闭塞锻造工艺,金属坯料在模膛中成形 。闭塞锻造工艺又称复动式凸模在一个方向或多个方向施加不同的压力,使毛坯产生多向流动,从而可在一道变形工序中获得较大的变形量和复杂的型面, 可以锻造出几何形状更复杂、尺寸精度高、表面质量好的锻件。 冷闭塞锻造成形过程(见图 下:先将上下成型模具闭合并施加一定的工作载荷 1P 压紧,毛坯在封闭的模腔内产生一定的变形,再 由复动式凸模施加压力 2P ,3P,使毛坯产生多向流动,从而在一道变形工序中齿轮零件冷精密塑性成形。 32 图 1 与 开 式模锻相比,闭塞模锻可以显著提高金属材料的利用率和锻件精度。而冷闭塞锻造技术是国际上近年发展起来的先进制造技术。 闭塞锻造 作为精密复杂零件生产的重要途径,以其精密、优质、高效、低消耗、低成本、大批量等生产特点而为汽车工业所瞩目。直齿圆锥齿轮是应用极为广泛的重要 传动零件。因其形状复杂,材质、尺寸精度、表面质量及综合机械性能均要求很高,很难以常规的塑性加工技术生产,通常采用模锻制坯即采用闭塞锻造制坯然后再切削加工的制造方法。在此过程中,金属能否充满型腔直接影响到直齿圆锥齿轮的尺寸精度和加工质量,甚至导致 劣质产品 的产生 或 产品的报废。因此,分析加工过程中影响金属充满型腔的因素并寻求优化方法十分必要。 1、产品图分析 如 图 示为直齿圆锥齿轮。模数 m=数 z=10,法向齿形角n=22 30,大端分度圆直径 4,大端锥距 锥角 =32,根锥角 f=27 24其主要齿形精度为 89,齿圈跳动公差距极限偏差 料为 20 钢。 毛坯直径 d=成形该直齿圆锥齿轮的变形量在 80%以上,冷成形难度大,精度、表面粗糙度要求高,一般的成形工艺不易保证,尤其齿形的充填情况不容乐观,极有可能齿顶充填不满,有弧形内凹陷,或小端充填不饱满,有塌陷,齿面,齿根有折叠等缺陷。这就要求以齿形充填饱满、改善变形条件(降低金属沿 33 齿顶、齿向的流动阻力)为目的来设计模具结构和制定工艺方案。 图 2 2、模锻时型腔充填问题分析 闭塞 锻造时,引起金属充不满的原因可能是:在模膛深而窄的部分和端部圆角处由于阻力大不易充满;在模膛的某些部分(如齿的倒角处),由于金属很难流到而不易充满;制坯时某些部分坯料体积不足,或操作时由于放偏,某部分金属量不足引起充不满等。 2 1 毛坯对型腔充填的影响及坯料的设计 图 3 34 坯料形状、尺寸的确定应满足锻件图对坯料体积、质量的要求,遵循体积不变的原则 进行设计。闭式锻造 工艺对坯料的体积和重量要求较精确,大了,小了都不行,大了模具易 破损,小了不能充满,即不能满足成型,所以必须进行精确的计算。体积确定后还必须根据成形工艺的要求确定合理的高、径尺寸,及必要的工艺倒角、圆角、减荷穴等。在体积相等的条件下,坯料的高、径比不同对金属充填齿形的影响很大。另外
- 温馨提示:
1: 本站所有资源如无特殊说明,都需要本地电脑安装OFFICE2007和PDF阅读器。图纸软件为CAD,CAXA,PROE,UG,SolidWorks等.压缩文件请下载最新的WinRAR软件解压。
2: 本站的文档不包含任何第三方提供的附件图纸等,如果需要附件,请联系上传者。文件的所有权益归上传用户所有。
3.本站RAR压缩包中若带图纸,网页内容里面会有图纸预览,若没有图纸预览就没有图纸。
4. 未经权益所有人同意不得将文件中的内容挪作商业或盈利用途。
5. 人人文库网仅提供信息存储空间,仅对用户上传内容的表现方式做保护处理,对用户上传分享的文档内容本身不做任何修改或编辑,并不能对任何下载内容负责。
6. 下载文件中如有侵权或不适当内容,请与我们联系,我们立即纠正。
7. 本站不保证下载资源的准确性、安全性和完整性, 同时也不承担用户因使用这些下载资源对自己和他人造成任何形式的伤害或损失。

人人文库网所有资源均是用户自行上传分享,仅供网友学习交流,未经上传用户书面授权,请勿作他用。