摘 要
这份报告主要研究的是作为汽车零部件之一的活塞销的流动缺陷。在联合冷挤压制活塞销的工艺中,起皱就是一种流动缺陷,它是由死金属区引起的。具有这种缺陷的部件带有很明显的外部特征,特征是被一微小而且厚的块状物嵌入材料中,这种缺陷对保证尺寸精度和降低材料损失是不利的,活塞销的这种缺陷对于其强度和疲劳寿命也有不利的影响。因此,在工艺设计的早期预测并防止这种缺陷是非常重要的。防止其产生的最好方法就是通过控制材料流动来限制或减少死金属区。有限元模拟分析方法被应用于流动缺陷研究分析当中,这份研究报告提出了通过去除死金属区防止产生流动缺陷的新工艺方法——有限元分析法。将有限元分析的结果与实验结果做比较,结果表明有限元分析的结果与实验结果相符合。
关键词:流动缺陷;活塞销钉;材料流动控制;前后双向冷挤压;死金属区;有限元分析
ABSTRACT
A flow defect of a piston-pin for automobile parts are investigated in this study. In the combined cold extrusion of a piston-pin, a lappingdefect, which is a kind of flow defect, appears by the dead metal zone. This defect is evident in products with a small thickness to be piercedand is detrimental to dimensional accuracy and decrease of material loss. The flow defect that occurs in the piston-pin has bad effects onthe strength and the fatigue life of the piston-pin. Therefore, it is important to predict and prevent the defect in the early stage of processdesign. The best method that can prevent the flow defect is removing or reducing dead metal zone through the control of material flow.Finite element simulations are applied to analyze the flow defect. This study proposes new processes which can prevent the flow defect byremoving the dead metal zone. Then the results are compared with the results of experiments for verification. These FE simulation results
are in good agreement with the experimental results.
? 2003 Elsevier Science B.V. All rights reserved.
Keywords: Flow defect; Piston-pin; Material flow control; Forward–backward extrusion; Dead metal zone; FE simulation
目 录
1 前言 5
1.1玻璃升降器的功用及拉深模的设计要求 5
2 冲裁工艺设计 7
2.1 冲裁工艺计算 7
2.1.1 工艺力和功的计算 7
2.1.2 压力机的选择 9
2.2 模具总体设计 9
2.2.1 模具类型的确定 10
2.2.2 操作方式的确定 10
2.2.3 定位、联接型式的确定 10
2.2.4 模具压力中心的确定 11
2.2.5 模具精度的确定 11
2.2.6模具闭合高度的初定 11
2.3 定位装置 11
2.4 卸料装置 11
2.4.1 卸料装置的选择 12
2.4.2 弹性元件的设计 12
2.5 落料凹凸模的设计 13
2.5.1 凸模结构的确定 13
2.5.2 凹模结构确定 14
2.5.3 凹凸模工作部分尺寸设计 14
2.5.4 凸凹模工作表面技术要求 16
2.5.5 凸凹模材料 16
2.6 导向装置 16
2.6.1 导向装置的选择 16
2.6.2 导向装置尺寸确定 16
2.7 模具其它主要零部件的设计 18
2.7.1 板料定位装置的设计 18
2.7.2螺栓和销钉的选用 19
3工艺方案选择 21
3.1 冲压件的工艺确定 21
3.1.1 冲压件的工艺分析 21
3.1.2 零件材料的分析 23
3.1.3确定工艺方案和模具形式 24
3.1.4落料尺寸的计算 25
3.2确定排样方案 26
3.2.1确定排样、裁板方案 26
3.3计算拉深次数 28
3.4拉深冲压力的计算 29
3.4.1落料过程 29
3.4.2、拉深过程 30
3.4.3成型过程 31
3.5冲压设备的选择 32
3.6 分析比较和确定工艺方案 33
3.6.1计算毛坯尺寸需先确定翻边前的半成品尺寸。 33
3.6.2计算拉深次数 34
3.6.3.确定工序的合并与工序顺序 35
4 主要工艺参数的计算 39
4.1 确定各中间工序尺寸 39
4.2计算各工序压力,选用压力机 40
4.3 模具设计 44
4.3.1 模具结构形式选择 44
4.3.2 卸料弹簧的选择 45
4.3.3 模具工作部分尺寸和公差计算 45
4.3.4模具其它零件的结构尺寸计算 47
4.4 工作原理: 48
4.4.1首次拉深 48
4.4.2 二次拉深 48
4.4.3 三次拉深 48
4.4.4.冲压工艺过程卡的编写 48
结论 50
致 谢 51
1 前言
1.1玻璃升降器的功用及拉深模的设计要求
现在许多轿车门窗玻璃的升降(关闭和开启)已经抛弃了摇把式的手动升降方式,一般都改用按钮式的电动升降方式,即使用电动玻璃升降器来控制,也就是常说的“电动门窗”。轿车用的电动玻璃升降器多是由电动机、减速器、导绳、导向板、玻璃安装托架等组成。因导绳的材料或制作工艺方式不同,又分为绳轮式、软轴式和塑料带式三种电动玻璃升降器。前二种是用钢丝绳做为导绳,后一种是用塑料带做为导绳。
以普遍使用的绳轮式电动玻璃升降器为例,它是由电动机、减速器、钢丝绳、导向板和玻璃安装托架等零部件组成,安装时门窗玻璃固定在玻璃安装托架上,玻璃导向槽与钢丝绳导向板平行。
开启电动机,由电动机带动减速器输出动力,拉动钢丝绳移动玻璃安装托架,迫使门窗玻璃作上升或下降的直线运动。而塑料带式电动玻璃升降器的导绳采用塑料带,带上有孔,用来移动和定位塑料带,控制门窗玻璃的升降。
电动玻璃升降器结构的关键是电动机和减速器,这两者是组装成一体的,其中电动机采用可逆性永磁直流电动机,电动机内有两组绕向不同的磁场线圈,通过开关的控制可做正转和反转,也就是说可以控制门窗玻璃的上升或下降。
电动机是由双联开关按钮控制,设有升、降、关等三个工作状态,不操纵时开关自动停在“关”的位置上。操纵电路设有总开关(中央控制)和分开关,两者线路并联。总开关由驾车者,控制全部门窗玻璃的开闭,而各车门内把手上的分开关由乘员分别控制各个门窗玻璃的开闭,操作十分便利。
电动机的质量直接关系到电动玻璃升降器的正常工作,它一定要具有体积小、重量轻、防护等级高、噪声低、电磁干扰小、运行可靠等特点。现代轿车已广泛应用微电子技术,电机工作会发射电磁波干扰其它电器件的工作;前几年通用汽车公司一篇售后分析报告显示,近40%的电动玻璃升降器故障是由电动机密封性差引起的。因此,减少电磁干扰和解决电机密封性问题巳成为近年汽车电机技术的热门话题。
90年代中期以来,电动玻璃升降器的控制机构技术发展很快,电子模块控制形式大量应用于批量装车,并设有安全保护装置。例如博世公司生产的电动玻璃升降器系统,在电动机中埋植磁环,感应电机转速,在电子模块中埋植霍尔元件,感应电流,并通过电子模块控制对电动机的过流、过压及过热保护,而且当玻璃上升途中遇到人力障碍时会自动识别而反向运行,防止乘员夹伤。

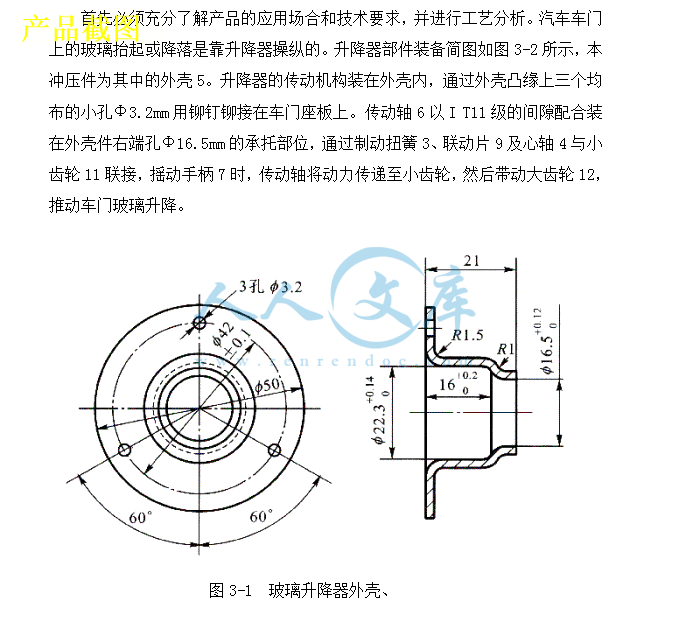
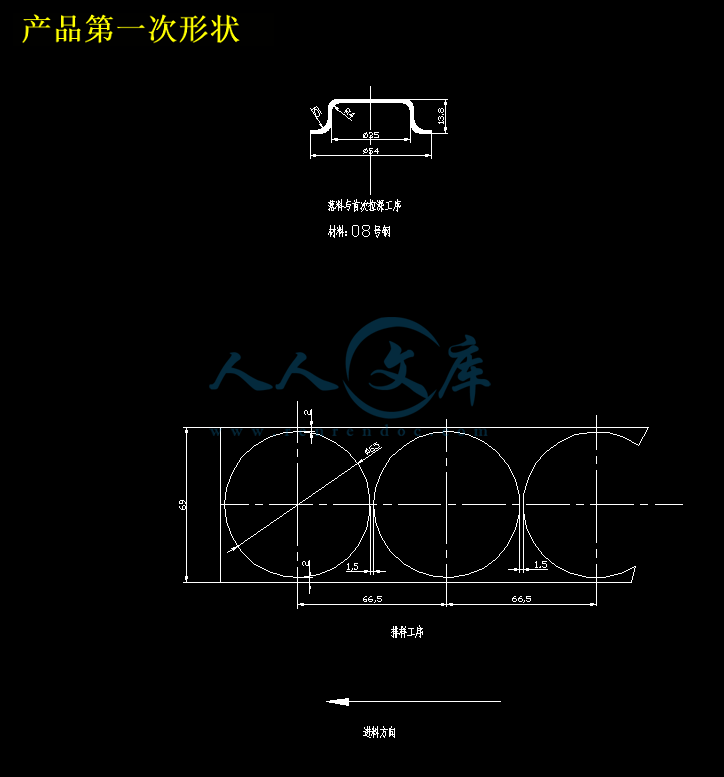



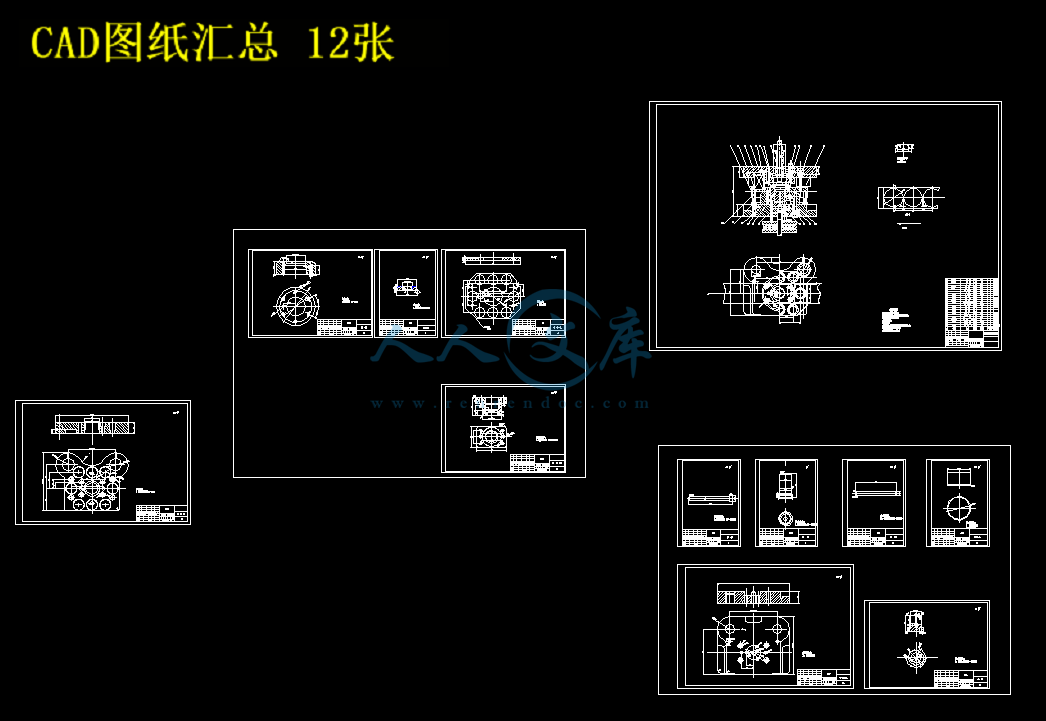
