摘要:本设计题目为回油管夹片成形工艺与模具设计,体现了板类冲压零件的设计要求、内容及方向,有一定的设计意义。通过对该零件模具的设计,进一步加强了设计者冲压模具设计的基础知识,为设计更复杂的冲压模具做好了铺垫并吸取了更深刻的经验。
本设计运用冲压成型工艺及模具设计的基础知识,首先分析了工件的成形工艺及模具成形结构对制件质量的影响。介绍了回油管夹片模具设计时要注意的要点,通过对制件进行工艺分析,可确定制件的成形加工用一套冲孔落料复合模和一套弯曲模。从控制制件尺寸精度出发,对回油管夹片模具的各主要尺寸进行了理论计算,以确定各工作零件的尺寸,从模具设计到零部件的加工工艺以及装配工艺等进行详细的阐述,并应用CAD进行各重要零件的设计。
关键词:复合模;弯曲模;工艺分析;模具零部件的加工工艺。
Oil return pipe die design
Abstract:The topic for the Oil return pipe die design reflect the sheet metal stamping parts of the design for the requirements content and the direction,Have a significance of the design.Through the design of the die parts to further enhance design of a oil return pipe enlarge the basic knowledge for the designer and put the way for the designer of more profound experience
The design use the basic knowledge of the die design, First there is an analysis for the shape of the workpiece forming and die structure of the parts quality. Introducedthe key point of the oil return pipe design that we should be noted , Through the process of analysis for the die, we can identify the parts of the forming punch is a blanking die and a set of composite bending die.Size the precision parts of the control of the key point,and calculat of all the major theoretical I carried out the the size of the working parts、the parts from the mold design process and the assembly process,AndI carry out CAD to design important parts of the oil return pipe die.
Key words:compound die; Blending dies;process analysis;processing of die parts
目 录
1 绪 论………………………………………………………………………1
1.1国内模具的现状和发展趋势………………………………………………1
1.1.1国内模具的现状……………………………………………………1
1.1.2国内模具的发展趋势………………………………………………4
1.2 国外模具的现状和发展趋势……………………………………………4
1.3回油管夹片模具设计与制造方面…………………………………………5
1.3.1回油管夹片模具设计的设计思路…………………………………5
1.3.2回油管夹片模具的设计进度………………………………………5
2 冲裁的毕业设计…………………………………………………………………6
2.1冲裁件的工艺分析…………………………………………………………6
2.1.1材料的分析…………………………………………………………6
2.1.2制件的工艺性分析…………………………………………………6
2.2 冲裁工艺方案的确定……………………………………………………6
3模具主要零部件的设计……………………………………………………………8
3.1工作零件的结构设计………………………………………………………8
3.1.1落料凹模的结构设计……………………………………………… 8
3.1.2 冲孔φ7凸模的设计……………………………………………9
3.1.3凸凹模的结构设计…………………………………………………10
4 主要工艺参数计算…………………………………………………………………12
4.1排样的设计与计算…………………………………………………………12
4.1.1 确定搭边与搭肩值…………………………………………………12
4.1.2 计算送料步距和条料的宽度………………………………………12
4.1.3计算材料的利用率…………………………………………………13
4.2冲压力的计算并初步选取压力机的吨位…………………………………13
4.2.1冲裁力的计算………………………………………………………13
4.2.2 卸料力、推件力及顶件力的计算………………………………14
4.2.3 总冲压力F总………………………………………………………15
4.3 压力机的公称压力的确定…………………………………………………15
4.4压力中心的确定……………………………………………………………16
4.5 工作部分的尺寸计算………………………………………………………17
4.5.1计算凸凹模工作部分的尺寸(冲孔)并确定其公差……………17
4.5.2外形落料凸模、凹模刃口尺寸的计算……………………………18
5.模具总体设计……………………………………………………………………19
5.1 定位方式的选择……………………………………………………………19
5.2 导向方式的选择……………………………………………………………20
5.3 卸料方式的选择……………………………………………………………20
5.3.1上模推件装置的设计………………………………………………20
5.3.2 下模部分卸料装置的设计………………………………………21
5.4连接与固定装置的设计……………………………………………………22
5.4.1模柄的设计…………………………………………………………22
5.4.2 固定板的设计……………………………………………………23
5.4.3 垫板的设计………………………………………………………24
5.4.4 螺钉与销钉的设计………………………………………………24
5.6 模架及组成零件的确定…………………………………………………24
5.6.1 模架的选用…………………………………………………………24
5.6.2 模座的确定……………………………………………………… 24
6.压力机有关参数的校核……………………………………………………………25
7.绘制模具总装图和非标零件工作图………………………………………………26
8.1 弯曲模设计的前期准备……………………………………………………27
8.2 阅读弯曲件产品图…………………………………………………………27
此弯曲件属于圆形弯曲,形状尺寸不算复杂,可一次弯曲成形……………27
8.3弯曲件的工艺分析…………………………………………………………27
8.4 工艺方案的确定…………………………………………………………28
9.弯曲模工艺计算……………………………………………………………………28
9.1弯曲件展开尺寸长度的计算………………………………………………28
9.1.1变形区中性层曲率半径ρ…………………………………………28
9.1.2毛坯尺寸〔中性层长度〕…………………………………………29
9.2 弯曲模工作部分尺寸计算………………………………………………30
9.2.1.弯曲模工作部分尺寸计算…………………………………………30
9.2.2.弯曲回弹的计算……………………………………………………31
9.2.3.弯曲力的计算………………………………………………………31
9.2.4.压力机的选择………………………………………………………32
10.模具总体设计……………………………………………………………………35
10.1模具的类型确定……………………………………………………………35
10.2定位方法的选择……………………………………………………………35
10.3卸料方法的选择……………………………………………………………35
10.4导向方式的选择……………………………………………………………35
10.5主要零部件的设计…………………………………………………………35
10.5.1工作零部件的设计…………………………………………………35
10.5.2 紧固螺钉的选用…………………………………………………37
10.5.3 模架及其他零部件的设计………………………………………37
11.模具的总装图、零件图及工作原理……………………………………………39
11.1 模具的总装图……………………………………………………………39
11.2 模具的零件图……………………………………………………………39
11.3工作原理……………………………………………………………………39
结束语…………………………………………………………………………………40
致谢……………………………………………………………………………………41
参考文献………………………………………………………………………………42
1 绪 论
目前,我国冲压技术与工业发达国家相比还相当的落后,主要原因是我国在冲压基础理论及成形工艺、模具标准化、模具设计、模具制造工艺及设备等方面与工业发达的国家尚有相当大的差距,导致我国模具在寿命、效率、加工精度、生产周期等方面与工业发达国家的模具相比差距相当大。
1.1国内模具的现状和发展趋势
1.1.1国内模具的现状
一、我国冲压模具无论在数量上,还是在质量、技术和能力等方面都已有了很大发展,但与国发经济需求和世界先进水平相比,差距仍很大,一些大型、精度、复杂、长寿命的高档模具每年仍大量进口,特别是中高档轿车的覆盖件模具,目前仍主要依靠进口。一些低档次的简单冲模,已趋供过于求,市场竟争激烈。
现将2004年我国冲压模具市场情况简介如下:
据中国模具工业协会发布的统计材料,2004年我国冲压模具总产出约为220亿元,其中出口0.75亿美元,约合6.2亿元.
根据我国海关统计资料,2004年我国共进口冲压模具5.61亿美联社元,约合46.6亿元.从上述数字可以得出2004年我国冲压模具市场总规模约为266.6亿元.其中国内市场需求为260.4亿元,总供应约为213.8亿元,市场满足率为82%.在上述供求总体情况中,有几个具体情况必须说明:一是进口模具大部分是技术含量高的大型精密模具,而出口模具大部分是技术含量较低中的中低档模具,因此技术含量高的中高档模具市场满足率低于冲压模具总体满足率,这些模具的发展已滞后于冲压件生产,而技术含量低的中低档模具市场满足率要高于冲压模具市场总体满足率;二是由于我国的模具价格要比国际市场低格低许多,具有一定的竟争力,因此其在国际市场前景看好,2005年冲压模具出口达到1.46亿美元,比2004年增长94.7%就可说明这一点;三是近年来港资、台资、外资企业在我国发展迅速,这些企业中大量的自产自用的冲压模具无确切的统计资料,因此未能计入上述数字之中。
二、冲压模具水平状况
近年来,我国冲压模具水平已有很大提高。大型冲压模具已能生产单套重量达50多吨的模具。为中档轿车配套的覆盖件模具内也能生产了。精度达到1~2μm,寿命2亿次左右的多工位级进模国内已有多家企业能够生产。表面粗糙度达到Ra≤1.5μm的精冲模,大尺寸(φ≥300mm)精冲模及中厚板精冲模国内也已达到相当高的水平。
1、模具CAD/CAM技术状况
我国模具CAD/CAM技术的发展已有20多年历史。由原华中工学院和武汉733厂于1984年共同完成的精神模CAD/CAM系统是我国第一个自行开发的模具CAD/CAM系统。由华中工学院和北京模具厂等于1986年共同完成的冷冲模CAD/CAM系统是我国自行开发的第一个冲裁模CAD/CAM系统。上海交通大学开发的冷冲模CAD/CAM系统也于同年完成。20世纪90年代以来,国内汽车行业的模具设计制造中开始采用CAD/CAM技术。国家科委863计划将东风汽车公司作为CIMS应用示范工厂,由华中理工大学作为技术依托单位,开发的汽车车身与覆盖模具CAD/CAPP/CAM集成系统于1996年初通过鉴定。在此期间,一汽和成飞汽车模具中心引进了工作站和CAD/CAM软件系统,并在模具设计制造中实际应用,取得了显著效益。1997年一汽引进了板料成型过程计算机模拟CAE软件并开始用于生产。
21世纪开始CAD/CAM技术逐渐普及,现在具有一定生产能力的冲压模具企业基本都有了CAD/CAM技术。其中部分骨干重点企业还具备各CAE能力。
模具CAD/CAM技术能显著缩短模具设计与制造周期,降低生产成本,提高产品质量,已成为人们的共识。在“八五”、九五“期间,已有一大批模具企业推广普及了计算机绘图技术,数控加工的使用率也越来越高,并陆续引进了相当数量CAD/CAM系统。如美国EDS的UG,美国Parametric Technology公司 Pro/Engineer,美国CV公司的CADSS,英国DELCAM公司的DOCT5,日本HZS公司的CRADE及space-E, 以色列公司的Cimatron 还引进了AutoCAD CATIA 等软件及法国Marta-Daravision公司用于汽车及覆盖件模具的Euclid-IS等专用软件。国内汽车覆盖件模具生产企业普遍采用了CAD/CAM技术/DL图的设计和模具结构图的设计均已实现二维CAD,多数企业已经向三维过渡,总图生产逐步代替零件图生产。且模具的参数化设计也开始走向少数模具厂家技术开发的领域。
在冲压成型CAE软件方面,除了引进的软件外,华中科技术大学、吉林大学、湖南大学等都已研发了较高水平的具有自主知识产权的软件,并已在生实践中得到成功应用,产生了良好的效益。
快速原型(RP)传统的快速经济模具相结合,快速制造大型汽车覆盖件模具,解决了原来低熔点合金模具靠样件浇铸模具,模具精度低、制件精度低,样样制作难等问题,实现了以三维CAD模型作为制模依据的快速模具制造,它标志着RPM应用于汽车身大型覆盖件试制模具已取得了成功。
围绕着汽车车身试制、大型覆盖件模具的快速制造,近年来也涌现出一些新的快速成型方法,例如目前已开始在生产中应用的无模多点成型及激光冲击和电磁成型等技术。它们都表现出了降低成本、提高效率等优点。
2、模具设计与制造能力状况
在国家产业政策的正确引导下,经过几十年努力,现在我国冲压模具的设计与制造能力已达到较高水平,包括信息工程和虚拟技术等许多现代设计制造技术已在很多模具企业得到应用。
虽然如此,我国的冲压模具设计制造能力与市场需要和国际先进水平相比仍有较大差距。这一些主要表现在高档轿车和大中型汽车覆盖件模具及高精度冲模方面,无论在设计还是加工工艺和能力方面,都有较大差距。轿车覆盖件模具,具有设计和制造难度大,质量和精度要求高的特点,可代表覆盖件模具的水平。虽然在设计制造方法和手段方面基本达到了国际水平,模具结构周期等方面,与国外相比还存在一定的差距。
标志冲模技术先进水平的多工位级进模和多功能模具,是我国重点发展的精密模具品种。有代表性的是集机电一体化的铁芯精密自动阀片多功能模具,已基本达到国际水平。
但总体上和国外多工位级进模相比,在制造精度、使用寿命、模具结构和功能上,仍存在一定差距。





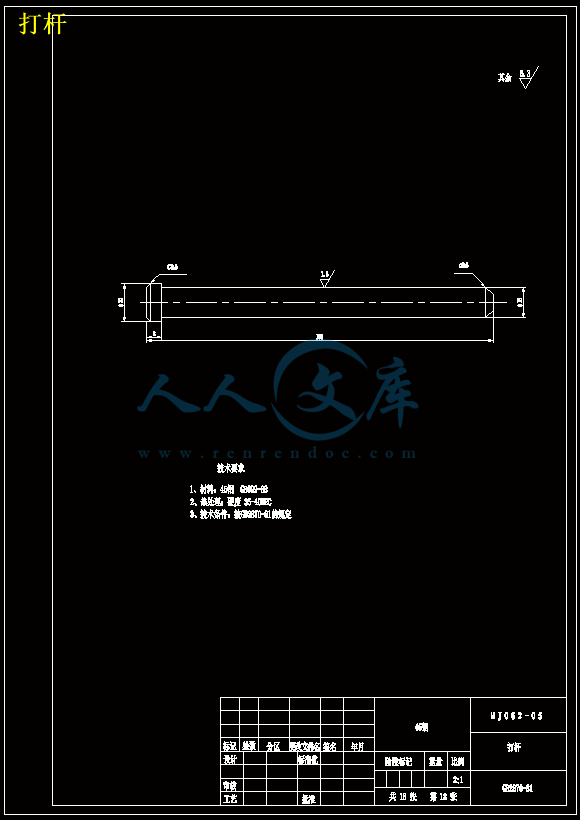














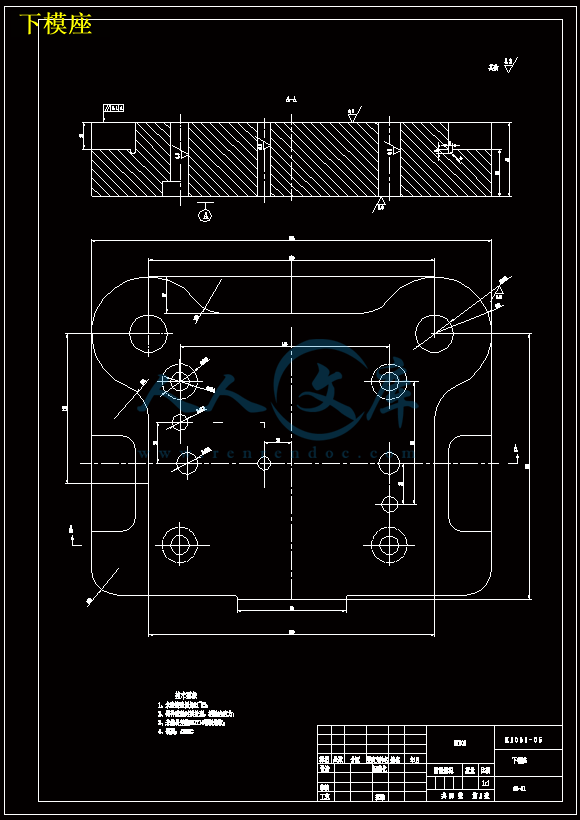

