【铣床夹具】杠杆臂加工工艺及夹具设计(含全套CAD图纸)
收藏
资源目录
压缩包内文档预览:(预览前20页/共30页)
编号:999799
类型:共享资源
大小:3.49MB
格式:RAR
上传时间:2017-01-24
上传人:机****料
认证信息
个人认证
高**(实名认证)
河南
IP属地:河南
20
积分
- 关 键 词:
-
铣床
夹具
杠杆
加工
工艺
设计
全套
cad
图纸
- 资源描述:
-




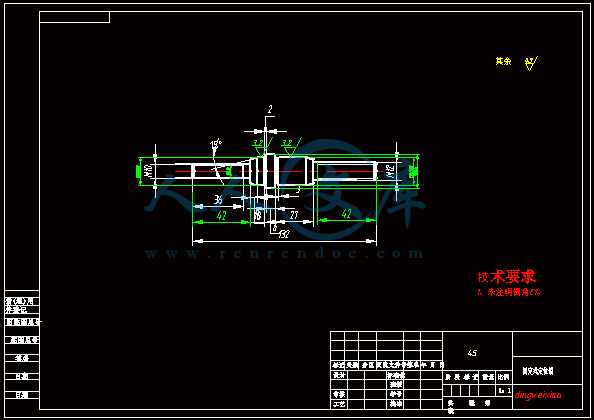

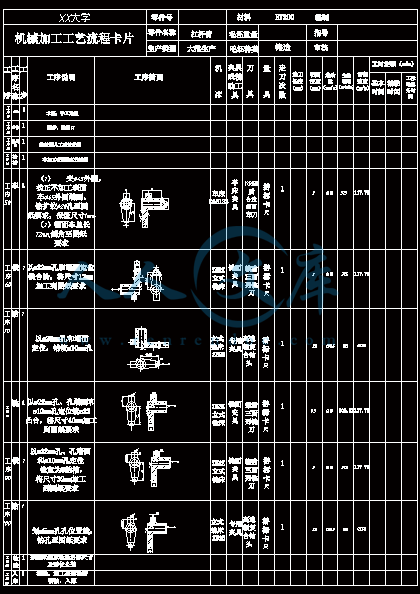







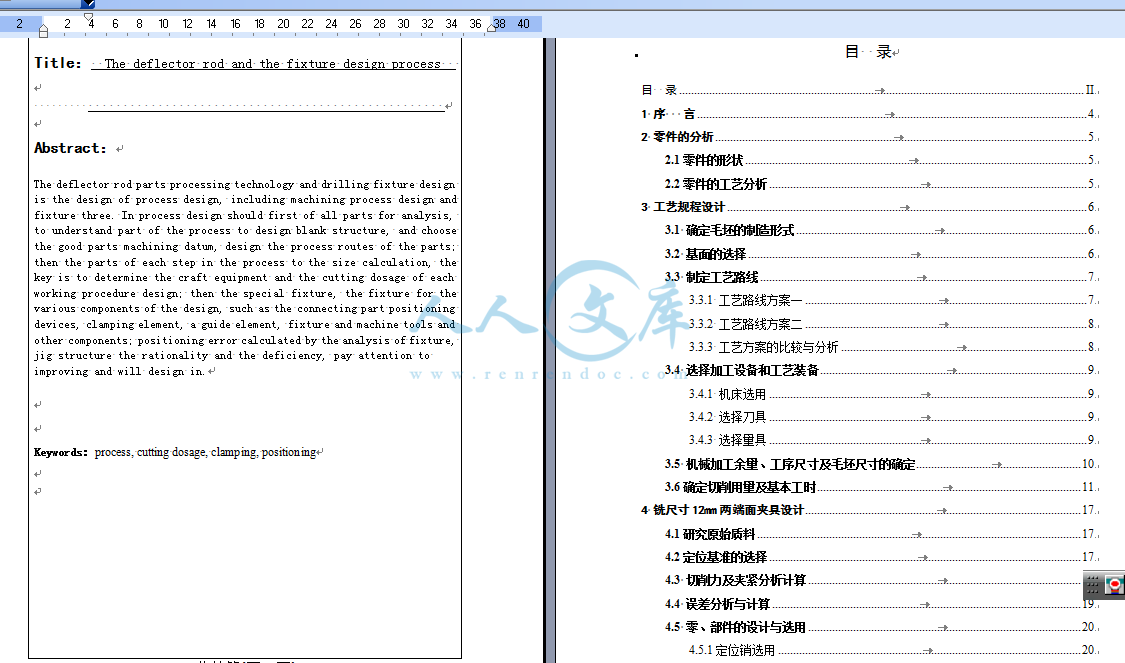






- 内容简介:
-
夹具夹紧力的优化及对工件定位精度的影响 什伍德拉夫机械工程学院,佐治亚理工学院,格鲁吉亚,美国研究所 由于 夹紧和加工 , 在工件和夹具的 接触部位会产生局部弹性变形, 使工件尺寸发生变化, 进而影响工件的最终加工质量。这种效应可通过最小化夹具 设计 优化 , 夹紧力 是一个重要的设计变量,可以得到优化,以减少工件的位移 。本文提出了一种确定多夹紧夹具受到准静态加工部 位 的最佳夹紧 力的新方法。该方法采用弹性接触力学模型代表夹具与工件接触,并涉及制定和解决方案的多目标优化模型的 约束。夹紧 力的 最优化对工件定位精度的影响通过 3铣夹具的例子进行了分析。 关键词:弹性 接触 模型 夹具 夹紧力 优化 前言 定位和 夹紧 的工件加工中的两个关键因素。 要实现夹具的这些功能,需将工件定位到一个合适的基准上 并夹紧,采用的夹紧力必须足够大,以抑制工件在加工过程中产生的移动 。然而,过度的夹紧力可诱导工件产生更大的弹性变形 ,这会影响它的位置精度,并反过来影响零件质量。 所以有必要确定最佳夹紧力,来减小 由于弹性变形对工件的定位误差 ,同时满足 加工的要求。在夹 具分析和综合领域上的研究人员使用了有限元模型的方法或 刚体模型的方法。大量的工作都以有限元方法为基础被报道 参考文献 1随着得墨忒耳 8,这种方法 的限制是 需要 较大的模型和计算成本。 同时 , 多数的 有限元 基础 研究人员一直 重点 关注的夹具布局优化和夹紧力的优化还没有得到充分讨论, 也有少数的研究人员通过对刚性模型 9夹紧力进行了优化, 刚型模型几乎被近似为一个规则完整的形状。 得墨忒耳 12, 13用螺钉理论解决的最低夹紧力,总的问题是制 定一个线性规划,其目的是尽量减少在每个定位点调整夹紧力强度的法线接触力。接触摩擦力的影响被忽视,因为它较法线 接触力 相对较小 , 由于这种方法是基于刚体假设, 独特的三维夹具可以处理超过 6 个自由度的装夹,复和倪 14也提出迭代搜索方法 ,通过假设已知摩擦力的方向 来 推导 计算最 小 夹紧力 ,该刚体分析的主要限制因素是当出现六个以上的接触力是使其静力不确定, 因此,这种方法无法确定工件移 位 的唯一性。 第 1 页 共 15 页 这种限制可以通过计算夹具 工件系统 15的弹性来克服,对于一个相对严格的工件,该夹具在机械加工工件的位置 会受夹具点的局部弹性变形的 强烈影响。 得墨忒耳 16使用经验的接触力变形的关系(称为元功能),解决 由于夹紧和 准静态加工力 工件刚体位移。同一作者还考察了加工工件夹具位移对设计参数的影响 17。桂 18 等 通过工件的夹紧力的优化定位精度弹性接触模型对报告做了改善,然而,他们没有处理计算夹具与工件的接触刚度的方法,此外,其算法 的应用没有讨论机械加工刀具路径负载有限序列。李和 19和乌尔塔多和 20用接触力学解决由于在加载夹具夹紧点弹性变形产生的接触力和工件的位移,他们还 使用此方法 制定了优化方法夹具布局 21和 夹紧力 22。 但是,关于 统及其对工件精度影 响的夹紧力的优化并没有在这些文件中提到 。 本文提出了一种新的算法,确定了 具工件系统受到准静态加载的最佳 夹紧力为基础的弹性方法。 该法旨在尽量减少影响由于工件夹紧位移 和加工荷载通过系统优化 夹紧 力的一部分定位精度。 接触力学模型,用于确定接触力和位移,然后再用做夹紧力优化 ,这个问题被作为多目标约束优化问题提出和解决。 通过两个 例子 分析 工件夹紧力的优化 对 定位精度的影响, 例子涉及的铣削夹具 3局 。 1 夹具 工件联系模型 1 1 模型假设 该加工夹具 由 L 定位器 和 带有 球形 端的 c 形 夹 组 成 。 工件和夹具 接触的地方是线性的 弹性 接触, 其他地方完全 刚性 。 工件 夹具系统由 于夹紧和加工受到准静态负载。夹紧力可假定为在加工过程中保持不变, 这个假设是有效的 ,在对液压或气动夹具使用。 在实际 中,夹具工件接触区域是弹性 分布, 然而, 这种模式的发展, 假设 总 触刚度(见图 1) 第 i 夹具 接触力 局部变形如下: i i ij j jF k d(1) 其中 j=x, y, z)表示,在当地子坐标系切线和法线方向的接触刚度 第 2 页 共 15 页 图 1 弹簧夹具 工件接触模型。 i i 接触处的坐标系 j=x, y, z)是对应沿着 别 ( j= x, y, z)的代表 , 1 2 工件 夹具的接触刚度模型 集中遵守 一个球形尖端定位 , 夹具和工件的接触并 不是线性的, 因为接触半径 与随法线力呈 非线性变化 23。 由于 法线 力 触变形 作用于 半径 平面工件表面之间,这可从封闭 赫兹的办法解决缩进一个球体弹性半空间 的 问题 。对于这个问题, 法线 的变形 , 在 文献 23 第 93 页 中 给出如下: 1 / 32291 6 *( 2) 其中 22*111 E 式中 和 工件和夹具的弹性模量, w 、 f分别是工件和材料的泊松比。 切向变形 或 者沿着硅业切力距 或 者有以下形式 文献 23 第 217 页 8i wi f G ( 3) 其中 1 / 31314i fG、一个合理的接触刚度的线性可以近似 从最小二乘获得适合式 ( 2), 这就产生了以下线性化接触刚度值:在计算上述的线性近似, 第 3 页 共 15 页 1 / 32*168 . 8 29( 4) 1*2 24 ji i y k G (5) 正常的力 被假定为从 0到 1000N,且最小二乘拟合相应的 2 夹紧 力优化 我们的目标是确定最优 夹紧 力,将尽量减少 由于工件刚体运动过程中,局部的夹紧和加工负荷引起的弹性变 形,同时保持在准静态加工过程中夹具 工件系统平衡,工件的位移 减少,从而减少定位误差。实现这个目标是通过制定一个多目标约束优化问题的问题,如下描述。 标函数配方 工件旋转 , 由 于 部 队 轮 换 往 往 是 相 当 小 17 的 工 件 定 位 误 差Tw w w Y Z 假设为确定其刚体翻译基本上 ,其中 、 、 和 是 沿 xg,图 2)。 图 2 工件刚体平移和旋转 工件的定位误差归于装夹力,然后可以在该刚体位移的2 第 4 页 共 15 页 2 2 2ww w Y Z ( 6) 其中 表示一个向量二级标准。 但是作用在工件的夹紧力会影响定位误差。 当多个夹紧力作用于工件,由此产生的夹紧力为 R Y P P ,有如下形式: P ( 7) 其中夹紧力 1 . P 是矢量, 夹紧力的方向 1 . L CR n n矩阵, c o s c o s c o s TL i L i L i L 是 夹紧力是矢量的方向余弦, 、 和 是第 i 个夹紧点夹紧力 在gX、向量角度 ( i=1、 2、 3.,C) 。 在这个文件 中,由于接触区变形造成的工件的定位误差,被假定为受的作用力是法线 的,接触的摩擦力相对较小,并在进行分析时忽略了加紧力对工件的定位误差的影响。 意指正常接触刚度比是 通过i( i=1, 2 L)和 最小的所有定位器正常 刚度并假设工件xN、yN、gY、自的 等效接触刚度 可有下式1 1 1,X Y Ns s sz i z i z ii i ik k k 和计算得出(见 图3),工件刚体运动 ,归于夹紧行动现在可以写成: 111X Y Y i z i z (8) 工件有位移,因此,定位误差的减小可以通过 尽量减少 产生的夹紧力 向量 2因此,第一个目标函数可以写为: 最小化 X Y Y N + + ( 9) 要注意,加权因素是与等效 接触刚度成正比的在gX、通 第 5 页 共 15 页 过使用最低总能量互补 参考文献 15, 23的原则求解弹性力学接触问题得出 A 的组成部分是唯一确定的,这保证了夹紧 力和相应的定位反应是“真正的”解决方案,对接触问题和产生 的“真正”刚体位移, 而且工件保持在静态平衡,通过夹紧力的随时调整。因此,总能量最小化的形式为补充的夹紧力优化的第二个目标函数,并给出: 最小化 2 2 2i i C L + C L + 1 1 1F F =2 k k i ii i ix y z 12 ( 10) 其中 *U 代表机构的弹性变形应变能互补, *W 代表由外部力量和力矩配合完成, Q 1 1 1. L C L C L Cx y z x y zc c c c c c是 遵 守 对 角 矩 阵 的 , 1和111 . L C L Cx y z x y F F F F 是所有接触力的载体。如图 3 擦和静态平衡约束 在( 10)式优化的目标受到一定的限制和约束, 他们中最重要的是在每个接触处的 静摩擦力约束。 库仑摩擦力的法律规定 22i i i ix y s F( 静态摩擦系数) ,这方面的一个非线性约束 和线性化版本可以使用,并且 19有: i i i ix y s F ( 11) 假设准静态载 荷 ,工件的静力平衡由下列力和力矩平衡方程确保 (向量形式): 内蒙古科技大学 本科生毕业设计(外文翻译) 第 6 页 共 15 页 0F 0M (12) 其中包括 在法线和切线方向的力和力矩的机械加工力 和工件重量。 接触力 由于夹具 工件接触是单侧面的,法 线的接触力 能被压缩。 这通过以下的 约束表 0( i=1, 2 ,L+C) ( 13) 它假设 在 工件 上的法线力 是 确定的,此外,在一个法线的接触压 力不能超过压 工件材料的 屈服强度( 。 这个约束可写为: i A ( i=1, 2, ,L+C) (14) 如果i 个工件 夹具的接触处的接触面积,完整的夹紧力优化模型,可以写成: 最小化 1212 (15) 3 模型 算法求解 式 ( 15) 多目标优化问题 可以通过 求解约束 24。 这种方法将确定的目标作为首要职能之一,并将其转换成一个约束对 。 该补充(1f)的主要目的是处理功能,并由此得到夹紧 力(2f)作为约束 的加权范数2对1保选中一套独特可行的夹紧力 , 因此,工件 夹具系统驱动到一个稳定的状态(即最低能量状态),此状态也表示有最小的夹紧力下的加权范数2L。2个指定的加权范数2 , 其中 是 2假设 最初所有夹紧力不明确,要确定一个合适的 。在定位和夹紧点的接触力的计算只考虑第一个目标函数(即1f)。虽 然有这样的接触力,并不一定产生最低的夹紧力, 这是一个“真正的”可行的解决弹性力学问题办法,可完全抑制工件在夹具中的位置。这些夹紧力的加权 系数2L, 通过计算并作为 初始值 与 比较 ,因此,夹紧力式( 15)的优化问题可改写为 : 内蒙古科技大学 本科生毕业设计(外文翻译) 第 7 页 共 15 页 最小化1 12 ( 16) 由: RC (11)(14) 得。 类似的算法寻找一个方程根的二分法来确定最低的 RC 通过尽可能降低 上限,由此产生的最小夹紧力的加权范数2L。 迭代次数 K,终止搜索取决于所需的预测精度 和 ,有 参考文献 15: y i i ix y i id d d Y Z 2K lo g ( 17) 其中 表示上限的功能,完整的算法在如图 4 中给出。 内蒙古科技大学 本科生毕业设计(外文翻译) 第 8 页 共 15 页 图 4 夹紧力的优化算法(在示例 1 中使用)。 图 5 该算法在示例 2 使用4 加工过程中的 夹紧力的优化 及 测定 上一节介绍的算法可用于确定 单负载作用于工件的载体的 最佳夹紧 力 , 然而,刀具路径随磨削量和切割点的不断变 化而变化。因此,相应 的夹紧力和最佳的加工负荷获得将 由图 4 算法获得 , 这大大增加了 计算负担,并要求为选择的夹紧 力提供标准, 将获得满意和适宜的整个刀具轨迹 ,用保守的办法来解决 下面将被讨论的问题,考虑一个有限的数目(例如 m)沿相应的刀 具 路径 设置的 产生m 个最佳夹紧 力 , 选择记为 123每个采样点, 考虑 以下四个最坏加工负荷向量: 内蒙古科技大学 本科生毕业设计(外文翻译) 第 9 页 共 15 页 m a x 1 1m a x Y F F 2 m a x 2m a x Y F F 3 3 m a xm a x Y F F 444m a x Y F F (18) gX、大 值 , 2, 3 分别代替对应的 且有: 2 2 2m a x m a Y F F 虽然 4 个 最坏情况加工负荷向量不会 在 工件 加工的 同一时刻出现 , 但 在每 次常规的进给速度中 ,刀具旋转一次出现一次,负载向量引入的 误 差可忽略 。 因此,在这项工作中,四个载体负载适用于同一 位置, (但不是同时)对工件 进行 的采样 , 夹紧力的优化算法 图 4,对应于每个采样点 计算最佳的夹紧力。夹紧力的最佳形式有: m a x 1 2 . Ti i i ij j j c C C (i=1,2, ,m) (j=x,y z,r) (19) 其中体, =1, 2, C)是每个相应的夹具在第 i 个样本点和第 j 负荷情况下力的大小。后 的结果, 一套 简单的 “最佳”夹紧力必须从所有的样本点和装载条件里发现,并在 所有的最佳夹紧力中选择。 这是通过 在所有负载情况和采样点 排序,并选择夹紧点的最高值的最佳的 夹紧 力 , 式 ( 20): ik ( k=1, 2, , C) ( 20) 只要这些具备,就得到一套 优化的夹紧力 Tm a x m a x m a C. C C , 验证这些力,以确保工件夹具系统的静态平衡。否则, 会出现 更多采样点和重复上述程序。 在这种方式中,可为整个刀具路径确定“最佳”夹紧力 5 总结了刚才所描述的算法。请 注意,虽然这种方法是保守的,它提供了一个确定的夹紧力,最大限度地减少工件的定位误差的一套系统方法。 5影响工件的定位精度 它 的兴趣在于 最 早 提出了 评价夹紧力的 算法 对工件的定位精度 的影响 。 工件首先放在与夹具 接触 的 基板上,然后 夹紧力使 工件 接触 到 夹具, 因此,局部变形发生在每个工件夹具接触处,使工件在夹具上移位和旋转。随后,准静态加工负内蒙古科技大学 本科生毕业设计(外文翻译) 第 10 页 共 15 页 荷应用造成工件在夹具的移位。 工 件刚体运动的定义是由它 在gX、 移位 Td w w w Z 和自转 y z (见图 2), 如前所述,工件刚体位移产生于在每个夹紧处的局部变形 Ti i i ix y zd d d d ,假设 Ti i i Y Z 为相对于工件的质量中心的第 i 个位置矢量 定位点, 坐标变换定理可 以 用 来 表 达 在 工 件 的 位 移 d w w w Z 以 及 工 件 自 转x y z 如下 : 1d Ti w wi i r d r (21) 其中 1描述当地在第 是一个旋转矩阵确定工件 相对于全球的坐标系 的定位 坐标系。 假设夹具夹紧工件旋转,由于旋转 w 很小,故 也可近似为: w ( 22) 方程( 21)现在可以改写为: 1 B q( 23) 其中 0 0 1 0 Z 0 1 Y X 0是 经方程 ( 21) 重新编排后 变换得到 的 矩阵式, Z Tw w w w w 是夹紧和加工导致的工件刚体运动矢量 。 工件与夹具单方面接触性质意味着工件与夹具接触处没有拉力的可能。因此,在第i 装夹点接触力 能与 关系如下: ,00,i i d t h e r w i s e ( 24) 其中 是在第 i 个 接触点由于 夹紧和加工负荷 造成的变形 , 0 意味着净压缩变形,而负数则代表拉伸变形 ; i i i ix y zK d i a g k k k 是表示在本地坐标系第 i 个接触刚度矩阵, 0 0 1 是单位向量 . 在这项研究中假定液压 /气动夹具,根据对外加工负荷,故在法线方向的夹紧力的强度保持不变,因此, 必须内蒙古科技大学 本科生毕业设计(外文翻译) 第 11 页 共 15 页 对方程 ( 24) 的 夹紧点 进行修改 为: i i F p ( 25) 其中 在第 i 个夹紧点的夹紧力,让 1矢量。并结合方程( 23) ( 25)与静态平衡方程,得到下面的方程组: 1L + i i F ( 26) 其中, 其中 表示相乘。由于夹紧和加工工件刚体移动, q 可通过求解式( 26)得到。工件的定位误差 向量, r r r r Zm m m m (见图 6), 现在可以计算如下: r q( 27) 其中 r Tm m Y Z 是 考 虑 工 件 中 心 加 工 点 的 位 置 向 量 , 且1 0 0 00 1 0 00 0 1 Y 0 6模拟工作 较早前提出的算法是用来确定最佳夹紧力及其对两例工件精度的影响例如 : 1 适用于工件单点力。 2 应用于工件负 载准静态铣削序列 内蒙古科技大学 本科生毕业设计(外文翻译) 第 12 页 共 15 页 如左图 7 工件夹具配置中使用的模拟研究 16L gX、 3具 图 7 所示,是用来定位 并控制 7075 - 合金( 127 毫 米 127 毫 米 米) 的 柱状块。假定为球形布局倾斜硬钢定位器 /夹具 在表 1 中给出 。工件 夹具材料 的摩擦静电 对系数 为 使用伊利诺伊大学开发 序 参考文献 26 对 加工瞬时铣削力条件进行了计算 , 如表 2 给出 例( 1),应用工件在点( 米, 米, 米)瞬时加工力, 图 4 中表 3 和表 4列出了初级夹紧力 和 最佳夹紧 力 的算法 。 该算法如图 5 所示 , 一个 米铣槽使用 行了数值模拟, 以减少 起 步 ( 米, 米, 米)和结束时( 米, 米, 米)四种情况下加工负荷载体 , 内蒙古科技大学 本科生毕业设计(外文翻译) 第 13 页 共 15 页 内蒙古科技大学 本科生毕业设计(外文翻译) 第 14 页 共 15 页 (见图 8)。 模拟计算铣削力 数据在 表 5 中给出。 图 8 最终铣削过程模拟 例如 2。 内蒙古科技大学 本科生毕业设计(外文翻译) 第 15 页 共 15 页 表 6 中 5 个 坐标列出了为模拟抽样调查点。 最佳 夹紧力 是 用前面讨论过的排序算法计算每个采样点和负载载体 最后的 夹紧力 和负载 。 7结果与讨论 例如算法 1 的绘制最佳夹紧力收敛图 9,图 9 对于固定夹紧装置在图示例假设(见图 7), 由此得到的夹紧力加权范数2 2 2 2/ 2 / 3R R R Y P P 佳夹紧 力 所述加工条件下有比初步夹紧力强度低得多的加权 范数2L, 最初的夹紧 力是通过减少工件的夹具系统补充能量算法 获得 。 由于夹紧 力和 负载造成的工件的定位误差,如表7。结果表明工件旋转小, 加工点减少错误从 等。在这种情况下, 所有加工条件 改善不是很大,因为从最初 通过互补势能 确定的最小化的夹紧力值已接近最佳夹紧力。 图 5 算法 是用第二例在一个序列应用于铣削负载到工件, 他 应 用 于 工 件 铣 削 负 载 一 个 序 列 。 最 佳 的 夹 紧 力, m a x m a x m a x m a x m a x, , ,i i i i ij x y z P P P ,对应列 表 6 每个样本点,随着最后的最佳夹紧力每个采样点的加权范数2 10, 在每个采样点的内蒙古科技大学 本科生毕业设计(外文翻译) 第 16 页 共 15 页 加权范数2 结果表明,由于每个具有最高的加权范数2L。 如图 10 所示,如果在每个夹紧点最大组成部分是用于确定初步夹紧力,则夹紧力需相应设置,上述模拟结果表明, 该方法可用于优化夹紧 力相对于初始夹紧力的强度,这种做法将减少所造成的夹紧力的加权范数2L,因此将提高工件的定位精度。 图 10 8结论 该文件提出了关于确定多钳夹具,工件受准静态加载系统的优化加工夹紧力的新方法。夹紧力的优化算法是基于接触力学的夹具与工件系统模型,并寻求尽量减少应用到所造成的工件夹紧力的加权范数2L,得出工件的定位误差。该整体模型,制定一个双目标约束优化问题,使用 算法通过两个模拟表明,涉及 3,二夹铣夹具的例子。今后的工作将解决在动态负载存在夹具与工件在系统的优化,其中惯性,刚度和阻尼效应在确定工件夹具系统的响应特性具有重要作用。 9 参考资料: 内蒙古科技大学 本科生毕业设计(外文翻译) 第 17 页 共 15 页 1、 J. D. L. S. 柔性夹具系统的有限元分析 交易美国 程杂志工业 : 134 。 2、 W. S. J. J. X. “柔性钣金夹具:原理,算法和模拟”,交易美国 造科学与工程杂志 : 1996 318。 3、 P. S. M. R. E. S. G. 负载对表面平整度的影响”工件夹具 制造科学研讨会论文集 1996,第一卷 : 146。 4、 R. J. V. R. 适用于选拔夹具设计与 优化方法 , 美国业工程杂志: 113 、 4121991。 5、 A. J. C. C. J. 计算机辅助夹具分析中的应用有限元分析和数学优化模型 , 1995 序, 777 。 6、 S. N. S. M. R. E. S. G. J. “基于 加工过程仿真 的加工装置作用 力系统 研究” , 207214 页 , 1995 7、“考虑工件夹具,夹具接触相互作用布局优化 模拟的结果” 3411998。 8、 E. C. 快速支持布局优化 ,国际机床制造, 硕士论文 1998。 9、 Y. V. M. M. 加工夹具机械构造的数学算法:分析和合成, 美国 程学报工业 “: 1989 299 。 10、 S. H. M. R. 具有摩擦性的夹具规划 美国 业工程学报 : 1991, 320327 页。 11、 S. L. W. 最小夹紧 力分析”,国际机床制造, 硕士论文 1995 年。 12、 E. C. 加工夹具的性能的 最小 最大 负荷标准 美国 业工程杂志 : 1994 13、 E. C. 加工夹具最大 负荷 的性能优化 模型 美国 业工程杂志 1995。 14、 和 .“核查和工件夹持的夹具设计”方案优化,设计和制造,4,硕士论文: 3071994。 15、 T. H. 埃利斯 霍伍德 应力能量方法分析 , 1977。 16、 M. J. . C. 对工件准静态分析功能位移 在加工夹具 的 应用程序 , 制造科学杂志与工程 : 325331 页 , 1996。 2001) 17:1041132001 Li . N. . to is to is a be a to of a of is a 32-1 of in A by to be to in it is to in . N. . 0332E 18. 8, a of is of on on 911. as 12, 13 to as a to at by of is on it D 14 by a of is it is As a be by be by of 15. a of in is by at 16to to of on 17. et 18an of In a of a Li 9 20 05by at 21 2. a on a on a to to to by A is to a of is as a of on is a 32-1 a in is to to to be or of is in is 1). at be as )j = x,y,z) in of xi,yi,1. A zi,at j = x,y,z) xi,j = x,j,z) of at a is 23. to of a be to of a an 23, p. 93:9(16*)2(2)1 - - s to a i(= 23, p. 217: - )3 - of be a q. (2). *)29(4)E* - )In to 000 N, 2of to . is to of . Li . N. by in in is by as a as to is 17 is to by , g, 2)to be in of 2of as (+ (+ () (6)ii 2of a on to , )C= .C= .nL+i= iaL+i, bL+i, gL+by at g, i = 1,2,. . .,C)to is to be by at at is is of on of to i = 1,. . .,L), X, of in g,2. in be 3). to be )by 2of be 11)to in g, by of 15, 23. to is in by at of is U* - W*) =12i=1(L+(L+(0)= 3. of 07* of W* by Q = z is ( 1, l = zof q. (10) is to is at s (+() #A of be is 19: 1)is by in 0 (12) 0of in is be by i:0(i = 1, . . ., L + C) (13)it is at a of is i# i = 1, . . .,L+C) (14)at f =5)(11)(14)q. (15) by 24. of as a In of is as 2of is as a of a of is As a to a 2of a 2to be or to e, an on To a e,at of it is a “to 2of as of e. q. (15) 16)e, (11)(14)to of an is to By e as 2of is of K, on d is 25:K =7) I in be a to of an to be a a of be A to a m) of m of 1.,At . Li . N. 4. in )(18)g, of , 2, 3 (+(+()on at At by at be in at on to 4 is to (i = 1, . . .,m)(j = x,y,z,r)(19)of k = 1,. . .,C)is at to be of is at a as q. (20):k = 1,. . .,C) (20)is a of is to of In be is a of a of is of to of on is on in to at f机械加工工序卡 产品型号及规格 图 号 名 称 工艺文件编号 3/5 杠杆臂 材料牌号及名称 毛坯外型尺寸 杆臂 零件毛重 零件净重 硬 度 220 备 型 号 设 备 名 称 床 专 用 工 艺 装 备 名 称 代 号 专用夹具 机动时间 单件工时定额 每合件数 51 技 术 等 级 冷 却 液 中 工序号 工步号 工 序 及 工 步 内 容 刃 具 量 检 具 切 削 用 量 代 号 名 称 代 号 名称 切削速度(米 /分) 切削深度(毫米) 进给量( 毫米 /转) 转速(转 /分) 6 1 以 和端面定位铣台阶,将尺寸 12工到图纸要求 面铣刀 游标卡尺 80 编 制 校 对 会 签 复 制 修改标记 处 数 文件号 签 字 日 期 修改标记 处 数 文件号 签 字 日 期 院 课程设计 (论文)说明书 作 者: 学 号: 系 部: 专 业: 购买后包含有 纸和论文 ,咨询 题 目: 杠杆臂 加工工艺及 铣床 夹具设计 指导者: 评阅者: 2014 年 11 月 课程设计 (论文)中文摘要 杠杆臂 零件加工工艺及 钻床夹具设计 是包括零件加工的工艺设计、工序设计以及专用夹具的设计三部分。在工艺设计中要首先对零件进行分析,了解零件的工艺再设计出毛坯的结构,并选择好零件的加工基准,设计出零件的工艺路线;接着对零件各个工步的工序进行尺寸计算,关键是决定出各个工序的工艺装备及切削用量;然后进行专用夹具的设计,选择设计出夹具的各个组成部件,如定位元件、夹紧元件、引导元件、夹具体与机床的连接部件以及其它部件;计算出夹具定位时产生的定位误差, 分析夹具结构的合理性与不足之处,并在以后设计中注意改进。 关键词 工艺 , 工序 , 切削用量 , 夹紧 , 定位 , 误差 I 课程设计 (论文)外文摘要 is of In of to of to of of in to is to of of as a by of to 录 目 录 . 序 言 . 7 2 零件的分析 . 8 件的形状 . 8 件的工艺分析 . 8 3 工艺规程设计 . 9 定毛坯的制造形式 . 9 面的选择 . 9 定工艺路线 . 10 艺路线方案一 . 10 艺路线方案二 . 11 艺方案的比较与分析 . 11 择加工设备和工艺装备 . 12 床选用 . 12 择刀具 . 12 择量具 . 12 械加工余量、工序尺寸及毛坯尺寸的确定 . 13 定切削用量及基本工时 . 14 4 铣尺寸 12 端面夹具设计 . 20 究原始质料 . 20 位基准的选择 . 20 削力及夹紧分析计算 . 20 差分析与计算 . 22 、部件的设计与选用 . 23 位销选用 . 23 向键与对刀装置设计 . 23 具设计及操作的简要说明 . 25 总 结 . 26 参考文献 . 27 致 谢 . 28 1 序 言 机械制造业是制造具有一定形状位置和尺寸的零件和产品,并把它们装备成机械装备的行业。机械制造业的产品既可以直接供人们使用,也可以为其它行业的生产提供装备,社会上有着各种各样的机械或机械制造业的产品。我们的生活 离不开制造业,因此制造业是国民经济发展的重要行业,是一个国家或地区发展的重要基础及有力支柱。从某中意义上讲,机械制造水平的高低是衡量一个国家国民经济综合实力和科学技术水平的重要指标。 杠杆臂 零件加工工艺及 钻床夹具设计 是在学完了机械制图、机械制造技术基础、机械设计、机械工程材料等 的基础下,进行的一个全面的考核 。正确地解决一个零件在加工中的定位,夹紧以及工艺路线安排,工艺尺寸确定等问题,并设计出专用夹具, 保证尺寸 证零件的加工质量。 本次设计也要培养自己的自学与创新能力。因此本次设计综合性和实践性强、涉及知识面广。 所以在设计中既要注意基本概念、基本理论,又要注意生产实践的需要,只有将各种理论与生产实践相结合,才能很好的完成本次设计。 本次设计水平有限,其中难免有缺点错误,敬请老师们批评指正。 8 2 零件的分析 件的形状 题目给的零件是 杠杆臂 零件 ,主要作用是 起 传动连接 作用。 零件 的实际形状如上图所示, 从零件图上看,该零件是典型的零件,结构比较简单 。 具体尺寸,公差如下图所示 。 件的工艺分析 由零件图可知,其材料为 材料为 灰铸铁 ,具有较高强度,耐磨性,耐热性及减振性,适 用于承受较大应力和要求耐磨零件。 杠杆臂 零件主要加工表面为: 面粗糙度.2 m 。 表面粗糙度.2 m 。 合面 ,表面粗糙度.2 m 。 2.5 m ,法兰面粗糙度.3 m 。 杠杆臂 共有两组加工表面,他们之间有一定的位置要求。现分述如下: (1) 左端的加工表面: 这一组加工表面包括: 左端面。这一部份只有端面有 其要求并不高,粗车后半精车就可以达到精度要求。 (2) 这一组加工表面包括:右端面;粗糙度为 要求也不高,粗车可以达到精度要求。 3 工艺规程设计 本 杠杆臂 来自 假设 年产量为 12000 台,每台需要该零件 1个,备品率为 19%,废品率为 每日工作班次为 1班。 该零件材料为 虑到零件在工作时要有高的耐磨性,所以选择铸铁铸造。依据设计要求 Q=12000 件 /年, n=1 件 /台;结合生产实际,备品率和 废品率分别取19%和 入公式得该工件的生产纲领 N=+ )( 1+ )=17850 件 /年 定 毛坯 的制造形式 零件材料为 件的特点是液态成形,其主要优点是适应性强,即适用于不同重量、不同壁厚的铸件,也适用于不同的金 属,还特别适应制造形状复杂的铸件。考虑到零件在使用过程中起连接作用,分析其在工作过程中所受载荷,最后选用铸件,以便使金属纤维尽量不被切断,保证零件工作可靠。年产量已达成批生产水平,而且零件轮廓尺寸不大,可以采用砂型 铸造 ,这从提高生产效率,保证加工精度,减少生产成本上考虑,也是应该的。 面的选择 基面选择是工艺规程设计中的重要工作之一,基面选择的正确与合理,可以使加工质量得到保证,生产效率得以提高。否则,不但使加工工艺过程中的问题百出,更有甚者,还会造成零件大批报废,使生产无法正常进行。 粗基准的选 择,对像 杠杆臂 这样的零件来说,选好粗基准是至关重要的。对本零件 10 来说,如果外圆的端面做基准,则可能造成这一组内外圆的面与零件的外形不对称,按照有关粗基准的选择原则 (即当零件有不加工表面时,应以这些不加工表面做粗基准,若零件有若干个不加工表面时,则应以与加工表面要求相对应位置精度较高的不加工表面做为粗基准 )。 对于精基准而言,主要应该考虑基准重合的问题,当设计基准与工序基准不重合时,应该进行尺寸换算,这在以后还要专门计算,此处不在重复。 定工艺路线 制定工艺路线的出发点,应当是使零件的几何形状、尺寸精 度及位置精度等技术要求能得到合理的保证。在生产纲领已经确定为成批生产的条件下,可以考虑采用万能性机床配以专用夹具,并尽量使工序集中来提高生产率。除此以外,还应当考虑经济效果,以便使生产成本尽量下降。 艺路线方案一 1 铸造 木模,手工造型 2 冷作 清砂,浇冒口 3 热处理 人工时效 4 油漆 非加工表面涂红色底漆 5 车 ( 1) 夹 40外圆,找正不加工表面 。钻扩铰 至图纸要求,保证尺寸 1角 ( 2) 翻面车总长 72角至图纸要求 6 铣 以 尺寸 127 钻 以 铰 108 铣 以 端面和 01 22凸台,将尺寸 409 铣 以 端面和 01 的槽,将尺寸 3210 钻 划 5位置线,钻孔至图纸要求 11 检验 按图纸要求检验各部尺寸及形位公差 12 入库 清洗,加工表面涂防锈油,入库 艺路线方案二 艺方案的比较与分析 上述两个方案的特点在于:方案一的定位和装夹等都比较方便,但是要更换多台设备,加工过程比较繁琐,而且在加工过程中位置精度不易保证。方案二减少了 装夹次数,但是要及时更换刀具,因为有些工序在车床上也可以加工 等等,需要换上相应的刀具。因此综合两个 工艺方案,取优弃劣,具体工艺过程如下: 1 铸造 木模,手工造型 2 冷作 清砂,浇冒口 3 热处理 人工时效 4 油漆 非加工表面涂红色底漆 5 铣 ( 3) 夹 40外圆,找正不加工表面外圆端面。钻扩铰 至图纸要求,保证尺寸 1角 ( 4) 翻面铣总长 72倒角至图纸要求 6 铣 以 尺寸 127 钻 以 铰 108 铣 以 端面和 01 22凸台,将尺寸 409 铣 以 端面和 01 的槽,将尺寸 3210 钻 划 5位置线,钻孔至图纸要求 11 检验 按图纸要求检验各部尺寸及形位公差 12 入库 清洗,加工表面涂防锈油,入库 1 铸造 木模,手工造型 2 冷作 清砂,浇冒口 3 热处理 人工时效 12 择加工设备和工艺装备 床选用 0、 40、 50、 60、 70 是粗车、精车。各工序的工步数不多,成批量生产,故选用卧式车床就能满足要求。本零件外轮廓尺寸不大,精度要求属于中等要求,选用最常用的 考根据机械制造设计工工艺简明手册表 0、 90 是钻孔,选用 择刀具 一般选用硬质合金车刀和镗刀。加工刀具选用 硬质合金车刀,它的主要应用范围为普通铸铁、冷硬铸铁 、高温合金的精加工和半精加工。为提高生产率及经济性 ,可选用可转位车刀 ( 考机械加工工艺手册(主编 孟少农),第二卷表 择量具 本零件属于成批量生产,一般均采用通常量具。选择量具的方法有两种:一是按计量器具的不确定度选择;二是按计量器的测量方法极限误差选择。采用其中的一种方法即可。 4 油漆 非加工表面涂红色底漆 5 车 ( 5) 夹 40外圆,找正不加工表面。钻扩铰 至图纸要求,保证尺寸 1角 ( 6) 翻面车总长 72角至图纸要求 6 铣 以 尺寸 127 钻 以 钻铰 108 铣 以 端面和 01 22凸台,将尺寸 409 铣 以 端面和 01 的槽,将尺寸 3210 钻 划 5位置线,钻孔至图纸要求 11 检验 按图纸要求检验各部尺寸及形位公差 12 入库 清洗,加工表面涂 防锈油,入库 械加工余量、工序尺寸及毛坯尺寸的确定 “ 杠杆臂 ” 零件材料为 查机械加工工艺手册(以后简称工艺手册),表 种铸铁的性能比较, 灰铸铁 的硬度 43 269,表 铸铁 的物理性能, 3,计算零件毛坯的重量约为 2 表 3械加工车间的生产性质 生产类别 同类零件的年产量 件 重型 (零件重 2000 中型 (零件重1002000 轻型 (零件重 120250 、侧面 底 面 铸孔的机械加工余量一般按浇注时位置处于顶面的机械加工余量选择。 根据上述原始资料及加工工艺,分别确定各加工表面的机械加工余量、 工序尺寸及毛坯尺寸。 定切削用量及基本工时 切削用量一般包括切削深度、进给量及切削速度三项。确定方法是先是确定切削深度、进给量,再确定切削速度。现根据切削用量简明手册(第三版,艾兴、肖诗纲编, 1993 年机械工业出版社出版)确定本零件各工序的切削用量所选用的表格均加以 *号,与机械制造设计工工艺简明手册的表区别。 序 5 夹 40外圆,找正不加工表面 B。钻扩铰、 至图纸要求,保证尺寸 1角 翻面车总长 45角至图纸要求 所选刀具为 质合金可转位车刀。根据切削用量简明手册表 于 00表 故选刀杆尺寸 = 516 ,选择车刀几何形状为卷屑槽带倒棱型前刀面,前角 0V = 012 ,后角 0 = 06 ,主偏角090 ,副偏角 010 ,刃倾角 s = 0 ,刀尖圆弧半径 f 根据切削加工简明实用手册可知:表 刀杆尺寸为 ,pa 工件直径 10 400之间时, 进给量 f =1.0 按 9)在机械制造工艺设计手册可知: f =0.7 确定的进给量尚需满足机床进给机构强度的要求,故需进行校验根据表 1 30,530N 。 根据表 强度在 174 207,pa f 045 时,径向进给力: 950N 。 切削时.0,1.0, 2),故实际进给力为: 50 = ( 3 由于切削时进给力小于机床进给机构允许的进给力,故所选 f = 用。 根据切削用量简明使用手册表 刀后刀面最大磨损量取为 车刀寿命 T = 可直接有表中查出。 根据切削用量简明使用手册表 6质合金刀加工硬度 200 219pa f ,切削速度 V = 切削速度的修正系数为.0,故: 0V=tV 3 ( 3 m n =1000 =127481000 =120 ( 3 根据 0n=125 这时实际切削速度 0001000 125127 m( 3 16 切削时的功率可由表查出,也可按公式进行计算。 由切削用量简明使用手册表 160 245 ,pa f 切削速度 时, 切削功率的修正系数实际切削时间的功率为: = ( 3 根据表 n = ,机床主轴允许功率为 所选切削用量可在 后决定的切削用量为: f = n = V = 为了缩短辅助时间,取倒 角时的主轴转速与钻孔相同 换车刀手动进给。 . 计算基本工时 3 式中 L =l +y + , l = 由切削用量简明使用手册表 削时的入切量及超切量 y + = 则L =127 +1 = ( 3 工序 6 以 尺寸 12已知工件材料为 择高速钢圆柱铣刀直径 d=60数 z=10。根据资料选择铣刀的基本形状 ,0, 2, =45已知铣削宽度 削深度50机床选用 式铣床。 根据资料所知, 式卧式铣床的功率为 艺系统刚性为中等。查得每齿进给量 z、现取 z。 根据资料所知,铣刀刀齿后刀面的最大磨损量为 铣刀直径 d=60耐用度 T=180 根据资料所知,依据铣刀直径 d=60齿数 z=10,铣削宽度 削 深 度 a P =50 耐 用 度 T=180 查 取 98mm/s ,n=439r/f=490mm/s。 根据 式 铣床 主轴转速表查取, 00r/75mm/s。 则实际切削 : 10000 c=1000 =际进给量 : 0300475=z 根据 资料所知 ,铣削时的功率(单位 :当 z, 5090mm/削功率的修正系数 ,则 .8 根据 立式铣床 说明书可知:机床主轴主电动机允许的功率 此机床功率能满足要求。 基本时间 根据 资料所知高速钢圆柱铣刀 铣面基本时间为: tm=zc 2 6050(2 =18 工序 7 以 铰 10钻孔选用机床为 臂机床,刀具选用 柄短麻花钻,机械加工工艺手册第 2卷。 根据机械加工工艺手册第 2卷表 0钻孔进给量为 则取 确定切削速度,根据机械加工工艺手册第 2卷表 削速度计算公式为 m 3 查得参数为 , 具耐用度 T=35则 v = =1.6 所以 n =72 选取 所以实际切削速度为 1000 v =确定切削时间(一个孔) t = 28 工序 10 划 5置线,钻孔至图纸要求 本工序采用计算法。 表 3速钢麻花钻的类型和用途 标准号 类型 直径范围( 用途 柄麻花钻 各种机床上,用钻模或不用钻模钻孔 柄长麻花钻 各种机床上,用钻模或不用钻模钻孔 柄麻花钻 各种机床上,用钻模或不用钻模钻孔 柄长麻花钻 各种机床上,用钻模或 不用钻模钻孔 选用 机械加工工艺手册 孟少农 主编,查机表 用度为 4500,表 准高速钢麻花钻的直径系列选择锥柄长,麻花钻 25 ,则螺旋角 =300 ,锋交 2 =1180 ,后角 00 ,横刃斜角 =500 , L=197mm,116 表 3准高速钢麻花钻的全长和沟槽长度(摘自 径范围 直柄麻花钻 l 51 101 表 3用型麻花钻的主要几何参数的推存值(根据 ( ) d ( 2 f 0 118 12 40 60 表 3头、扩孔钻和铰刀的磨钝标准及耐用度 ( 1)后刀面最大磨损限度 具材料 加工材料 钻头 直径 20 高速钢 铸铁 2)单刃加工刀具耐用度 T 具类型 加工材料 刀具材料 刀具直径 11 20 钻头(钻孔及扩孔) 铸铁、铜合金及合金 高速钢 60 钻头后刀面最大磨损限度为 具耐用度 T = 60 查机械加工工艺手册 孟少农 主编,第二卷表 速钢钻头钻孔的进给量为 f=根据表 中可知,进给量取 f= 查机械加工工艺手册 孟少农 主编,表 铸铁 ( 19020 上钻孔的切削速度轴向力,扭矩及功率得, V=12 参考机械加工工艺手册 孟少农 主编,表 V=12 = ( 3 则 n = =131 ( 3 查表 可知, 取 n = 150 则实际切削速度 = =11.8 查机械加工工艺手册 孟少农 主编,表 孔时加工机动时间计算公式: ( 3 其中 2 5 2 3则: t= =4 铣尺寸 12端面夹具设计 究原始质料 利用本夹具主要用来粗、精 铣尺寸 12端面 ,该 尺寸 12端面 对孔 22 的中心线要满足对称度要求以及其 铣尺寸 12端面 两边的平行度要求。在铣此 铣尺寸12端面 时,为了保证技术要求,最关键是找到定位基准。同时,应考虑如何提高劳动生产率和降低劳动强度。 位基准的选择 由零件图可知:在对 铣尺寸 12端面 进行加工前,底平面进行了粗、精铣加工,孔 22 进行了钻、扩、铰加工。因此,定位、夹紧方案有: 铣该 铣尺寸 12端面 时其对孔的中心线 有对称度以及两边的平行度要求。为了使定位误差达到要 求的范围之内,采用一面一定位 销 两个左右支撑件 的定位方式,这种定位在结构上简单易操作。一面即为底平面; 削力及夹紧分析计算 刀具:错齿三面刃铣刀(硬质合金) 刀具有关几何参数: 00 15 00 10 顶 刃 0n 侧 刃 6 0010 15 30 25 1000 1000 40D 160d 22Z 0 /fa m m z p 由参考文献 55 表 1 2 9 可得铣削切削力的计算公式: 0 . 9 0 . 8 0 1 . 1 1 . 1 0 . 12335 a f D B z n 有: 0 . 9 0 0 . 8 0 1 . 1 1 . 1 0 . 12 3 3 5 2 . 0 0 . 0 8 2 8 2 0 . 5 2 2 2 . 4 8 3 6 . 2 4 ( ) 根据工件受力切削力、夹紧力的作用情况,找出在加工过程中对夹紧最不利的瞬间状态,按静力平衡原理计算出理论夹紧力。最后为保证夹紧可靠,再乘以安全系数作为实际所需夹紧力的数值,即: 安全系数 K 可按下式计算: 6543210 式中: 60 各种因素的安全系数,查参考文献 51 2 1 可知其公式参数 : 1 2 34 5 61 . 0 , 1 . 0 , , 1 . 0 ,1 . 3 , 1 . 0 , 1 . 0 K 由此可得: 1 . 2 1 . 0 1 . 0 1 . 0 1 . 3 1 . 0 1 . 0 1 . 5 6K 所以 8 3 6 . 2 4 1 . 5 6 1 3 0 4 . 5 3 ( ) F N 由计算可知所需实际夹紧力不是很大,为了使其夹具结构简单、操作方便,决定选用手动螺旋夹紧机构。 查参考文献 51 2 26 可知移动形式压板螺旋夹紧时产生的夹紧力按以下公式计算:螺旋夹紧时产生的夹紧力按以下公式计算 有: )( 210 z 式中参数由参考文献 5可查得: 901 0592 2 29 其中: 33( )L )(80 螺旋夹紧力: 0 4 7 4 8 ) 该夹具采用螺旋夹紧机构,用螺栓通过弧形压块压紧工件,受力简图如 由表 2621 得:原动力计算公式 0 01l 22 即: 00 4 7 4 8 . 2 3 3 0 . 9 8 9 0 3 2 . 7 5 ( )17K 由上述计算易得: W 由计算可知所需实际夹紧力不是很大,为了使其夹具结构简单、操作方便,决定选用手动螺旋夹紧机构。 差分析与计算 该夹具采用一面一定位 销 两个左右支撑件 的定 位方式,为了满足工序的加工要求,必须使工序中误差总和等于或小于该工序所规定的尺寸公差。 与机床夹具有关的加工误差 j ,一般可用下式表示: 由参考文献 5可得: 采用一面一定位 销 两个左右支撑件 的定位方式定位误差 : 11 1 m i D d 1 1 2 21 m i n 2 m i n. 2D d D a r c t g L 其中: 1 0 2D , 2 0D 1 0 1d , 2 0 3d 1 , 2 m 4 0 . 0 6 3DW . 0 . 0 0 3 2JW 夹紧误差 : c o s)( m i nm a x 其中接触变形位移值: 1( ) ( )1 9 . 6 2
- 温馨提示:
1: 本站所有资源如无特殊说明,都需要本地电脑安装OFFICE2007和PDF阅读器。图纸软件为CAD,CAXA,PROE,UG,SolidWorks等.压缩文件请下载最新的WinRAR软件解压。
2: 本站的文档不包含任何第三方提供的附件图纸等,如果需要附件,请联系上传者。文件的所有权益归上传用户所有。
3.本站RAR压缩包中若带图纸,网页内容里面会有图纸预览,若没有图纸预览就没有图纸。
4. 未经权益所有人同意不得将文件中的内容挪作商业或盈利用途。
5. 人人文库网仅提供信息存储空间,仅对用户上传内容的表现方式做保护处理,对用户上传分享的文档内容本身不做任何修改或编辑,并不能对任何下载内容负责。
6. 下载文件中如有侵权或不适当内容,请与我们联系,我们立即纠正。
7. 本站不保证下载资源的准确性、安全性和完整性, 同时也不承担用户因使用这些下载资源对自己和他人造成任何形式的伤害或损失。

人人文库网所有资源均是用户自行上传分享,仅供网友学习交流,未经上传用户书面授权,请勿作他用。