资源目录
压缩包内文档预览:
编号:272227
类型:共享资源
大小:1.07MB
格式:RAR
上传时间:2014-04-11
上传人:上***
认证信息
个人认证
高**(实名认证)
江苏
IP属地:江苏
35
积分
- 关 键 词:
-
诱导
引诱
支架
铸造
锻造
工艺
设计
图纸
- 资源描述:
-
左诱导轮支架铸造工艺设计
46页-13000字数+说明书+开题报告+任务书+7张CAD图纸
4#芯盒图.dwg
中期报告.doc
任务书.doc
合箱图.dwg
工艺图.dwg
左诱导轮支架铸造工艺设计开题报告.doc
左诱导轮支架铸造工艺设计论文.doc
毛坯图.dwg
1#芯盒图.dwg
2#芯盒图.dwg
3#芯盒图.dwg
目 录
摘 要I
AbstractII
第1章 绪论1
1.1 研究目的及意义1
1.2 国内外铸造发展的状况1
1.2.1 国内铸造工艺发展情况1
1.2.2 国外铸造工艺发展情况2
1.3 ZG32MnMo的性能及铸造工艺特点3
1.4 本设计的具体内容4
1.5 本章小结4
第2章 ZG32MnMo左诱导轮支架的性能分析5
2.1 ZG32MnMo的化学成分及力学性能5
2.2 ZG32MnMo的熔炼工艺5
2.3 ZG32MnMo左诱导轮支架的技术要求6
2.3.1 零件实体图6
2.3.2 主要技术要求8
2.4本章小结9
第3章 铸造工艺方案的确定10
3.1 零件结构的铸造工艺性10
3.1.1左诱导轮支架的结构工艺性10
3.1.2铸件质量对零件结构要求10
3.2 造型、造芯方法的选择11
3.3浇注位置的确定12
3.4分型面的选择13
3.5 砂箱中铸件数目的确定14
3.6 本章小结14
第4章 砂芯设计及铸造工艺参数设计15
4.1 砂芯、芯头的设计15
4.1.1 砂芯数量的确定15
4.1.2 砂芯的固定和定位16
4.1.3 1#砂芯的设计与校核16
4.1.4 2#砂芯的设计与校核18
4.1.5 3#砂芯的设计与校核20
4.1.6 4#砂芯的设计与校核21
4.1.7 5#砂芯的设计与校核23
4.2 铸造工艺设计参数24
4.2.1 铸件尺寸公差25
4.2.2 机械加工余量25
4.2.3 铸造收缩率26
4.2.4 起模斜度26
4.2.5 最小铸出孔及槽27
4.2.6 分型负数27
4.3 本章小结29
第5章 浇注系统及冒口的设计30
5.1 浇注系统的类型及选择30
5.2 浇注时间的确定30
5.3 确定浇口比及各浇道的设计与计算31
5.3.1 确定浇口比31
5.3.2 阻流截面积计算32
5.3.3 各浇道的设计与计算32
5.4 冒口的设计与计算34
5.5 本章小结35
第6章 铸造工艺装备的设计36
6.1 模样的设计36
6.1.1 模样材料的选择36
6.1.2 模样的尺寸和等级36
6.1.3 木模的坯料拼接37
6.2 芯盒的设计37
6.2.1 芯盒材料的确定及结构形式37
6.2.2 木质芯盒的结构设计37
6.3 砂箱的确定38
6.4 铸件的后续处理38
6.5 本章小结38
结 论39
致 谢40
参考文献41
摘 要
本文进行了左诱导轮支架零件的铸造工艺设计。
ZG32MnMo左诱导轮支架选用砂型铸造,该铸件为两件小批量生产的大型件,且其形状、结构较复杂。通过分析该铸件结构,为简化铸造工艺,合理选择分型面。分型面的选择与浇注位置保持一致,避免合型后翻转砂箱。同时砂芯的形状、尺寸及在砂型中的位置符合铸件要求,在铸件形成的过程中砂芯所产生的气体能及时的排出型外,保证铸件的质量。
为提高零件铸造的可行性、保证充型顺利,特开设一组直浇道、两组横浇道及内浇道。通过AutoCAD平面绘图,并用Pro/E三维实体造型,最终设计出了最佳的铸造工艺方案。
关键词:工艺设计、铸造、实体造型、分型面
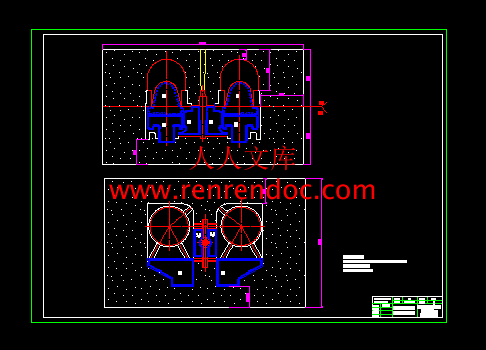
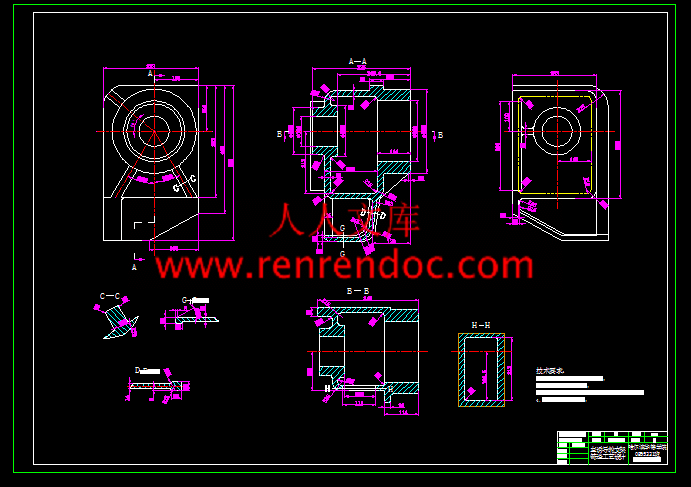
- 内容简介:
-
哈尔滨工业大学华德应用技术学院毕业设计(论文)中期报告题 目:左诱导轮支架铸造工艺设计系 (部) 机电工程系 专 业 材料成型及控制工程 学 生 唐北京 学 号 1089522123 班 号 0895221 指导教师 梁维中 中期报告日期 2011.11.24 哈工大华德学院说 明一、中期报告应包括下列主要内容:1论文工作是否按开题报告预定的内容及进度安排进行;2目前已完成的研究工作及成果;3后期拟完成的研究工作及进度安排;4存在的困难与问题;5如期完成全部论文工作的可能性。二、中期报告由指导教师填写意见、签字后,统一交所在系(部)保存,以备检查。指导教师评语: 指导教师签字: 检查日期: 第一章 已完成项目 1.铸造工艺设计 1.1左诱导轮支架的结构工艺性零件结构铸造工艺性是指零件的结构应符合铸造生产的要求,易保证铸件的品质,简化铸造工艺过程和降低成本。左诱导轮支架结构具有如下特点:壁厚合适,最小壁厚为14mm,满足表3-1所要求的最小壁厚。铸造时能有效的避免浇不到、冷隔等缺陷,保证有良好的充型。零件最大壁厚70mm,壁厚分布有利于实现顺序凝固,但在厚壁处热节太大,导致中心部分晶粒粗大,容易出现缩松和缩孔缺陷,降低力学性能。铸件没有长板,长箱体等易产生翘曲变形的结构,虽铸件收缩较大,但铸造时不用考虑变形。在铸件的壁厚处有圆角过渡,使铸件在凝固收缩时阻力较小,减小了热裂的产生 。1.2铸件质量对零件结构要求(1)铸件的最小壁厚查铸造手册(5)铸造工艺表3-2得知当铸件最大轮廓尺寸为400800mm时最小壁厚为12mm,而本课题中的最小壁厚为14,所以铸件可铸出。表2-1 砂型铸造时铸件的最小允许壁厚合金种类铸件的轮廓尺寸 mm2000低合金钢8991012162025(2)铸造斜度查铸造手册(5)铸造工艺表3-16得知斜度a:h 角度B 使用范围1:10-1:20 5度30分-3度 h=25-500mm的铸钢件1.3砂型选择根据农机左诱导轮在生产实际中的情况,选择树脂砂。树脂砂强度高、硬化快、效率高、粉尘少,一般不需要烘干。适用于中型钢、铁、铝、铜铸件单体或者批量生产。1.4模样材料选择选择塑料模造型:模样轻、造型方便、因有脆性,修复不便,铸件尺寸精度较高,适用寿命也较长,用于大量、成批生产的中小简单件。砂型成型紧实方式:手工造型,两箱造型。1.5浇注位置的选择铸件的浇注位置是指铸件在铸型内浇注时的所处的位置。浇注位置是根据零件的结构特点、尺寸、重量、技术要求、铸造合金特性、铸造方法及生产车间的条件决定的。正确的浇注位置应能保证获得健全的铸件,并使造型、造芯和清理方便。浇注位置的选择,主要是保证铸件质量为出发点。因此在铸件工艺设计时,要根据技术要求,先找出铸件质量要求高的部位和容易产生缺陷的部分,将这些部分放在有利的位置,保证其质量要求。经分析铸件的结构,根据合金的凝固理论的研究和生产的经验确定该铸件的浇注位置有以下图2-1和图2-2两种方案: 图2-1方案一 图2-2方案二 分析:方案一的顶部上表面是一个类似于圆台的结构,在铸后要机械加工,所以能保证铸件质量,且表面结构简单,有益于冒口的安放,有益于实现顺序凝固。而方案二的顶部上表面为非加工面,且不平整,结构复杂,有凸台、凹坑等,所以若浇注位置选方案二,则上表面的质量无法保证,且将给机械加工带来很大的不便。方案一所示浇注位置较方案二有以下优点,综上所述:选择方案一所示浇注位置。1.6分型面的选择合理的选择分型面对于简化铸造工艺、提高生产率、降低成本、提高铸件质量等都有之直接关系。分型面的选择尽量与浇注位置保持一致,避免合型后翻转砂箱。根据分型面的选择原则与铸件的结构特征,分型面的选择考虑了图2-3所示的两种选择方案。1处分型面为方案一,2处分型面为方案二。 图2-3分型面选择的两种方案方案一特点:优点:(1)该平面有利于起模,便于造型;(2)铸件内部空腔通过砂芯解决,主要砂芯放在下半型中,有利于下芯、合型和检查型腔尺寸;(3)铸件的大部份置于同一半型内;(4)易于铸件清理。缺点:(1)在浇注时,金属液对垂直砂芯冲刷,容易发生偏芯。(2)砂箱高度较高,对起模有一定不利影响。方案二特点:优点:(1) 分型面为铸件横向最大平面。缺点:(1)铸件几乎平分于两个半型,对铸件的精度和铸件成分的同一性有不利影响;(2)分型面虽然是铸件横向的最大平面,但是由于1处凸台的影响,非常不利于起模,造型。对两种方案进行分析对比,在充分保证铸件质量的前提下,综合考虑以上两种分型,最终采用分型方案一。2.砂芯设计砂芯的功用是形成铸件的内腔、孔和铸件外形的不能出砂的部位。砂芯应满足以下的要求:砂芯的形状、尺寸及在砂型中的位置应符合铸件要求,具有足够的强度和刚度,在铸件形成的过程中砂芯所产生的气体能及时的排出型外,铸件收缩时阻力小及容易清砂。砂芯主要靠芯头固定在砂型上。本设计中总共用到4个砂芯,其位置与形状大致如图2-4所示:图2-4 铸件所需用砂芯的形状2.1砂芯类别的选择及制造方法选用树脂砂芯,利用芯盒手工造芯。用芯盒内表面形成砂芯的形状,此种方法使砂芯尺寸精确,且可制造小而复杂的砂芯。2.2砂芯的固定和定位 一般用芯头来固定,也有用芯撑或铁丝来固定。本设计中的1、2、3、4号砂芯都为垂直砂芯,采用以下固定形式:1用上芯头固定,2、3、4用下芯头固定如图2-43.浇注时间的计算查公式: 式中 浇注时间(s) m 铸件重量(kg) A,n系数,取决于铸件壁厚该铸件的体积为:15469.565685cm3,其密度为:7.810-3kg/cm3,所以铸件的质量为:15469.565685cm37.810-3kg/cm3=120.662612343kg查铸造工艺学表3-4-4得:A=1.5-2.35 n=0.5故当A取最小时=Amn=1.5120.660.5=16.5s当A取最大时=Amn=2.35120.660.5=25.85s所以的取值范围为16.525.85s浇注时间的校核型内金属液面上升速度V型 C-铸件(或某段)的高度 -浇注时间(或浇注某段铸件时间)从理论上看,存在着V型min(防止浇不到、冷隔和夹砂等缺陷)和V型max(保证型内排气和防止过度紊流)两个极限值,合适的浇注 时间应满足如下条件:存在着V型min(防止浇不到、冷隔和夹砂等缺陷)和V型max (保证型内排气和防止过度紊流)两个极限值,合适的浇注 时间应满足如下条件: 对于铸钢铸件,一般只核算最小上升速度,该铸件壁厚在14-25mm,相对整个铸件而言壁厚较厚,查铸造工艺学表3-4-7取为20mm/s,该铸件高度约为360mm,最大浇注时间为360/20=18s。根据本铸件的壁厚特点,为了减少充型期间对砂型上表面的热作用时间,防止夹砂结疤、粘砂、冷隔、浇不足等缺陷,该件选择快浇,而且对于铸钢件,快浇可充分利用共晶膨胀消除缩孔缩松缺陷。本铸件质量121Kg250,查表3-4-3,一般取1220秒,结合本铸件最终确定浇注时间为18秒。第二章 未完成项目1.确定浇口比2.铸造工艺出品率3.砂芯的校核第三章 未解决的难点基本按原计划完成该设计的进程。设计步骤已基本完成。存在的问题是铸件出品率太低,这一问题可以通过后续的减少冒口体积来改善。故本课题主要将设计方案尽量优化,以达到对实际生产有一定的指导意义。第四章 日程安排2011.11.252011.12.16 进行芯核的校核及铸造工艺设计参数的确定,绘制 工艺图、合箱图、芯核图。2011.12.172011.12.27 进行论文的撰写。2011.12.282012.01.01 准备毕业论文答辩。第五章 完成全部毕业设计的可能性根据日程和时间的安排,可以按时完成毕业设计哈尔滨工业大学华德应用技术学院毕业设计(论文) 题 目 左诱导轮支架铸造工 艺设计 专 业 材料成型及控制工程 学 号 1089522123 学 生 唐北京 指 导 教 师 梁维中 答 辩 日 期 2011年12月26日 哈工大华德学院哈工大华德学院毕业设计(论文)评语姓名: 唐北京 学号:1089522123 专业: 材料成型及控制工程 毕业设计(论文)题目: 左诱导轮支架铸造工艺设计 工作起止日期: 2011 年 10 月 9 日起 2011 年 12 月 20 日止指导教师对毕业设计(论文)进行情况,完成质量及评分意见:_指导教师签字: 指导教师职称: 评阅人评阅意见:_ _评阅教师签字:_ 评阅教师职称:_答辩委员会评语:_根据毕业设计(论文)的材料和学生的答辩情况,答辩委员会作出如下评定:学生 毕业设计(论文)答辩成绩评定为: 对毕业设计(论文)的特殊评语:_答辩委员会主任(签字): 职称:_答辩委员会副主任(签字): 答辩委员会委员(签字):_ _ _ _ _ _ _ _ _ _ _ _ _ _ _年 月 日哈工大华德学院毕业设计(论文)任务书 姓 名:唐北京 院 (系):机电与汽车工程学院 专 业:材料成型及控制工程 班 号:0895221 任务起至日期: 2011 年 10 月 9 日至 2011 年 12 月 20 日 毕业设计(论文)题目:左诱导轮支架铸造工艺设计 立题的目的和意义:在实际的铸造生产当中,铸造工艺设计非常重要。通过本次毕业设计,全面系统地掌握铸造工艺设计及工装设计的一般方法。能够正确合理地确定铸造分型面及浇注位置,并根据ZG32MnMo合金特点选择合理的浇注系统。掌握计算机辅助设计软件在铸造工艺设计中的应用。 技术要求与主要内容: 技术要求:1.未注铸造圆角半径为R3-R6.铸造尺寸公差为2,铸造斜度不大于3;2.热处理硬度255-302HB(压痕直径3.8-3.5);3.外加工表面上最大尺寸为10,深度达5不聚集疵孔不超过5个时允许不补焊;4.螺纹孔倒角120至螺纹外径;5.倒钝锐边;6.在112,216的圆柱表面上最大尺寸达10,深度达5不聚集疵孔不超过5个时允许不补焊;7.外表面T铁红C06-1IIYHG/T2009-1991;8.112孔壁在1/3圆周上允许减薄到18不小于15时允许补焊;9.螺纹孔12M201.5在20长度内允许有2扣断扣,孔数不多于2个;主要内容::左诱导轮支架铸造工艺性的分析;(2) 浇注位置的确定;(3) 结合分型面的选择原则,确定铸造分型面;(4) 造型、造芯方法的选择及砂芯的设计;(5) 铸造工艺设计参数的确定;(6)浇注系统设计;(7)铸造工装设计; 进度安排:第一阶段:开题 10月19日10月30日(2周)第二阶段:设计阶段(实验工作阶段) 11月2日12月18日(7周)第三阶段:撰写毕业设计论文与准备答辩 12月21日元月1日(2周) 同组设计者及分工:同组设计者:李唯、刘洪臣、王兴业、马俊峰分工:每人一个不同的设计任务,各自独立完成。指导教师签字_ 年 月 日 系(教研室)主任意见: 系(教研室)主任签字_ 年 月 日哈尔滨工业大学华德应用技术学院毕业设计(论文)开题报告题 目:左诱导轮支架铸造工艺设计系 (部) 材料工程系 专 业 材料成型及控制工程 学 生 唐北京 学 号 1089522123 班 号 0895221 指导教师 梁维中 开题报告日期 2010.10.16 哈工大华德学院说 明一、开题报告应包括下列主要内容:1通过学生对文献论述和方案论证,判断是否已充分理解毕业设计(论文)的内容和要求2进度计划是否切实可行;3是否具备毕业设计所要求的基础条件。4预计研究过程中可能遇到的困难和问题,以及解决的措施;5主要参考文献。二、如学生首次开题报告未通过,需在一周内再进行一次。三、开题报告由指导教师填写意见、签字后,统一交所在系(部)保存,以备检查。指导教师评语: 指导教师签字: 检查日期: 一、设计的内容、技术要求利用Pro/E设计软件,完成该铸件的三维实体造型设计,在查阅相关设计资料和分析该铸件铸造成型工艺性基础上进行总体的方案设计及可行性分析。在完成铸件参数计算和结构设计的基础上,利用CAD设计软件完成铸件的毛坯图、工艺图、合箱图、模板图及芯核图等;最后完成设计计算说明书的编写。 该毕业设计所要铸造的零件,如下图。材料:ZG32MnMo零件二维图 零件三维图(1) ZG32MnMo的性能及铸造工艺特点:1.性能:较高的强度、塑性及韧性,重型机械中用于制造承受大负荷的零件,如轧钢机机架、水压机底座等;在铁路车辆上用于制造受力大又承受冲击的零件如摇枕、侧架、车轮和车钩。但其流动性差,容易形成冷隔。钢水温度高,体收缩和线收缩比较大,易缩孔缩松,热烈冷冽倾向大,氧化吸气较大,易产生夹渣的气孔,粘砂比较严重2.工艺特点:(1) 型砂性能要求更高(如强度、耐火度、透气性等)。为防止粘砂,铸型表面应涂上一层耐火材料。 (2) 为使钢液顺利地流动、充型、补缩,使用更多的冒口和冷铁。 (3) 要严格控制浇注温度,避免过高(使钢液易氧化)或过低(使流动性降低)。赞同(2)技术要求:1.未注铸造圆角半径为R3-R6.铸造尺寸公差为2,铸造斜度不大于3;2热处理硬度255-302HB(压痕直径3.8-3.5);3.外加工便面上最大尺寸为10,深度达5不聚集疵孔不超过5个时允许不补焊;4.螺纹孔倒角120至螺纹外径;5.倒钝锐边;6.在112,216的圆柱表面上最大尺寸达10,深度达5不聚集疵孔不超过5个时允许不补焊;7外表面T铁红C06-1IIYHG/T2009-1991;8.112孔壁在1/3圆周上允许减薄到18不小于15时允许补焊;9.螺纹孔12M201.5在20长度内允许有2扣断扣,孔数不多于2个;二、目的和意义在实际的铸造生产中,铸造工艺设计十分重要。通过本次毕业设计来设计铸造出合格的左诱导轮支架,且铸件的外观尺寸符合要求,没有内部组织、力学性能和残余应力等缺陷,符合实际生产的需要。并全面的了解和掌握铸造工艺设计的过程和一般方法。铸造碳钢具有较高的强度、塑性和韧性,成本较低,在重型机械中用于制造承受大负荷的零件,如轧钢机机架等。采用合理的铸造工艺,可生产出性能更好的产品,提高生产率,降低生产成本,提高市场竞争力,扩大铸钢的应用范围。因此采用铸钢材料设计铸件具用十分重要的意义。三、综合论述 1、国内铸造工艺发展情况铸造生产是一种金属加工的方法,应用这种方法可以制成机器零件的毛坯、半成品甚至成品。铸造生产是机器制造中的头道工序,它直接影响到整体机器的生产它在汽车、 拖拉机、机床、飞机、船舶、工程机械设备等各种机器生产中都占有重要地位据统计,在一般设备中,铸件质量约占机械设备总质量的50%90%,一辆汽车中铸件质量约占40%60%,一台拖拉机中铸件质量约占70%以上,而一台机床中铸件质量约占70%85%等等1。可见铸造生产出的铸件在国民经济的各个部门都占有相当的比重。我国在铸造技术方面,已有5000多年的悠久历史,是世界上应用铸造技术最早的国家。我国古代铸造技术居世界前列,勤劳智慧的中华名族在铸造技术方面做出了伟大的贡献。但是解放前,由于三座大山的残酷统治下,我国工业生产水平大大的落后了,铸造生产也长期处于落后状态。解放后,我国工艺水平也有了很大的发展和提高,尤其是改革开放以来随着我国国民经济的大发展,铸造生产也突飞猛进2。中国是当今世界上最大的铸件生产国家,据资料介绍,我国铸造产品的产值在国民经济中约占1%左右。最近几年,铸件进出口贸易增长较快,铸件的产量已达到9%左右。我国铸造厂点多达2万多个,铸造行业从业人员达120万之多。“长三角”地区的铸件产量占全国的1/3,该地区主要以民营企业为主,汽车和汽车零部件行业的发展有力地拉动了铸造行业的发展3。轿车气缸体铸件能力。尤其山西有丰富的生铁、煤炭、铝镁、电力、劳力资源、使山西的铸造产业有得天独厚的优势,具有500个铸造企业,80%为民营企业。山西国际、河津山联、山西华翔年产量分别达4万t、2万t、12万t。“东三省”有一汽集团、哈飞集团等骨干汽车企业带动了汽车铸件产量的增长。一汽集团铸造公司,已经形成40万t铸件的生产能力。“珠江三角洲”压铸行业发达,有700多个压铸企业,年产量达20万t。东风日产、广州本田、广州丰田和零部件企业有力带动了压铸业的发展,轿车气缸体、气缸盖的压铸件产量逐年增长。 但是我国铸造行业中多数以上的铸造车间属于单件、小批量、多品种生产。 生产出的铸件尺寸精度低,表面质量差,能源和原材料消耗多,生产效率低,劳动强度大,企业的效益差4。2、国外铸造工艺发展情况近几年来,全球铸造业持续增长。巴西铸件产量增长最快,达到25.8%。而发达国家的铸件增长率普遍较低。美国铸件产量自2000年以来,已经退居到第2位。2004年美国铸件总产量为1231万t,其中灰铁件占35%、球铁件占33%、铸钢件占8.4%、铝合金件占16%。从需求上看,球铁铸件和铝铸件的需求在增长。2003年进口铸件占总需求的1 5%,进口铸件的价格比美国国内低20%50%5。近年来因铸造环保要求高、能源消耗大、劳动力昂贵等原因,美国大型汽车公司生产普通汽车铸件的铸造厂纷纷关闭,逐步将铸件的生产转向中国、印度、墨西哥、巴西等发展中国家。日本的铸造业不景气,其从业人员在减少。2004年日本铸件总产量为639万t,其中灰铁件占42%、球铁件占30%、铸钢件占4%、铝合金件占21%。从需求上看,球铁铸件和铝铸件的需求在增长。日本铸造界在技术创新方面作了大量工作,开发了球型低膨胀铸造砂、高减振铸铁材料、中硅耐热球铁等材料。其真空压铸的铸件能焊接和热处理,半固态铸造生产用于汽车铝轮毂,提高了强度和伸长率。镁合金压铸进一步发展,并取代重力铸造,其性能提高,成本降低。 发达国家总体上铸造技术先进、产品质量好、生产效率高、环境污染少、原辅材料已形成商品化系列供应,如在欧洲已建立跨国服务系统。生产普遍实现机械化、自动化、智能化(计算机控制、机器人操作)6。在大批量中小铸件的生产中,大多采用微机控制的高密度静压、射压或气冲造型机械化、自动化高效流水线湿型砂造型工艺。在铸造生产的过程中,从严执行技术标准,铸件的废品率仅为2%-5%。总体上国外铸造的机械化、智能化水平比较高7。四、研究的方法和手段首先了解铸件的材料,不同材质对铸造过程有着不同的程度影响,映射着该件易出现的问题。利用CAD和Pro/E绘图软件,了解铸件的尺寸、结构特点和技术要求等等。依据铸造相关的手册确定机械加工余量,绘制铸件图。正确选择浇注位置、合理的分型面,设计辅助砂芯,并给予最适合充型的浇注方式。最终确定左诱导轮支架铸造方案和工艺做到用最合适的工艺,铸出性能最好的铸件,避免缺陷的产生,实现较高的工艺出品率。五、可行性分析依据铸造手册,以及利用CAD和Pro/E绘图软件,对铸件的尺寸、公差、和技术要求等进行分析。依据理论知识和所提供的数据做出合理的铸造工艺方案,且根据学校提供的设备和资料以及时间进程的安排可知该课题切实可行六、设计进度安排1.第一阶段:开题 2011.10.192011.10.30(2周)1.理解和熟悉毕业设计题目,了解所要完成的工作任务;2.查阅与毕业设计题目相关的文献资料;3.书写开题报告2.第二阶段:设计阶段 2011.11.02-2011.12.18(7周)1.左诱导轮支架铸造工艺性分析2.浇注位置的确定;3.结合分型面的选择原则,确定铸造分型面;4.造型、造芯方法的选择及砂芯的设计;5.铸造工艺设计参数的确定;6.浇注系统设计;7.铸造工装设计3.第三阶段:撰写毕业设计论文与准备答辩 2011.12.21-2012.01.01(2周)1.撰写毕业设计论文2.结题验收3.毕业答辩 七、参考文献1.曲卫涛主编,铸造工艺学 西北工业大学出版社,19932.中国机械工程学会铸造专业学会,铸造手册.北京:机械工业出版社,19983.中国机械工程学会铸造分会编.铸造手册(第5卷)铸造工艺2.北京:机械工业出版社,20034.李弘英,赵成志主编.铸造工艺设计.机械工业出版社5.李魁盛主编.铸造工艺设计基础 北京.:机械工业出版社,19816.张丝雨主编.最新金属材料牌号、性能、用途及中外牌号对照速用速查实用手册.中国科技文化出版社.2005.3:1419-1455 7. /view/71485.htm哈尔滨工业大学华德应用技术学院毕业设计(论文)摘 要本文进行了左诱导轮支架零件的铸造工艺设计。ZG32MnMo左诱导轮支架选用砂型铸造,该铸件为两件小批量生产的大型件,且其形状、结构较复杂。通过分析该铸件结构,为简化铸造工艺,合理选择分型面。分型面的选择与浇注位置保持一致,避免合型后翻转砂箱。同时砂芯的形状、尺寸及在砂型中的位置符合铸件要求,在铸件形成的过程中砂芯所产生的气体能及时的排出型外,保证铸件的质量。为提高零件铸造的可行性、保证充型顺利,特开设一组直浇道、两组横浇道及内浇道。通过AutoCAD平面绘图,并用Pro/E三维实体造型,最终设计出了最佳的铸造工艺方案。关键词:工艺设计、铸造、实体造型、分型面AbstractThis induced wheel support for the left part of the casting process design.ZG32MnMo left inducer bracket used sand casting, the casting for the two large pieces of small batch production, and its shape, structure is more complex. By analyzing the structure of the casting, to simplify the casting process, a reasonable choice of parting. Sub-surface location is consistent with the casting choice, avoid closing overturned sand box. Sand core while the shape, size and location of the line in the sand casting requirements, in the casting process of the formation of the gases produced by sand core timely discharge type, but to ensure the quality of castings.To improve the feasibility of casting parts, to ensure a smooth filling, open a special set of sprue, runner and two groups within the runner. Plane through the AutoCAD drawing, and use Pro / E solid modeling, the final design of the best casting solution.Key words: process design, casting, the solid modeling, parting surf目 录摘 要IAbstractII第1章 绪论11.1 研究目的及意义11.2 国内外铸造发展的状况11.2.1 国内铸造工艺发展情况11.2.2 国外铸造工艺发展情况21.3 ZG32MnMo的性能及铸造工艺特点31.4 本设计的具体内容41.5 本章小结4第2章 ZG32MnMo左诱导轮支架的性能分析52.1 ZG32MnMo的化学成分及力学性能52.2 ZG32MnMo的熔炼工艺52.3 ZG32MnMo左诱导轮支架的技术要求62.3.1 零件实体图62.3.2 主要技术要求82.4本章小结9第3章 铸造工艺方案的确定103.1 零件结构的铸造工艺性103.1.1左诱导轮支架的结构工艺性103.1.2铸件质量对零件结构要求103.2 造型、造芯方法的选择113.3浇注位置的确定123.4分型面的选择133.5 砂箱中铸件数目的确定143.6 本章小结14第4章 砂芯设计及铸造工艺参数设计154.1 砂芯、芯头的设计154.1.1 砂芯数量的确定154.1.2 砂芯的固定和定位164.1.3 1#砂芯的设计与校核164.1.4 2#砂芯的设计与校核184.1.5 3#砂芯的设计与校核204.1.6 4#砂芯的设计与校核214.1.7 5#砂芯的设计与校核234.2 铸造工艺设计参数244.2.1 铸件尺寸公差254.2.2 机械加工余量254.2.3 铸造收缩率264.2.4 起模斜度264.2.5 最小铸出孔及槽274.2.6 分型负数274.3 本章小结29第5章 浇注系统及冒口的设计305.1 浇注系统的类型及选择305.2 浇注时间的确定305.3 确定浇口比及各浇道的设计与计算315.3.1 确定浇口比315.3.2 阻流截面积计算325.3.3 各浇道的设计与计算325.4 冒口的设计与计算345.5 本章小结35第6章 铸造工艺装备的设计366.1 模样的设计366.1.1 模样材料的选择366.1.2 模样的尺寸和等级366.1.3 木模的坯料拼接376.2 芯盒的设计376.2.1 芯盒材料的确定及结构形式376.2.2 木质芯盒的结构设计376.3 砂箱的确定386.4 铸件的后续处理386.5 本章小结38结 论39致 谢40参考文献4141第1章 绪论1.1 研究目的及意义在实际的铸造生产中,铸造工艺设计十分重要。通过本次毕业设计来设计铸造出合格的左诱导轮支架,且铸件的外观尺寸符合要求,没有内部组织、力学性能和残余应力等缺陷,符合实际生产的需要。并全面的了解和掌握铸造工艺设计的过程和一般方法。铸造碳钢具有较高的强度、塑性和韧性,成本较低,在重型机械中用于制造承受大负荷的零件,如轧钢机机架等。采用合理的铸造工艺,可生产出性能更好的产品,提高生产率,降低生产成本,提高市场竞争力,扩大铸钢的应用范围。因此采用铸钢材料设计铸件具用十分重要的意义。1.2 国内外铸造发展的状况1.2.1 国内铸造工艺发展情况铸造生产是一种金属加工的方法,应用这种方法可以制成机器零件的毛坯、半成品甚至成品。铸造生产是机器制造中的头道工序,它直接影响到整体机器的生产它在汽车、拖拉机、机床、飞机、船舶、工程机械设备等各种机器生产中都占有重要地位据统计,在一般设备中,铸件质量约占机械设备总质量的50%90%,一辆汽车中铸件质量约占40%60%,一台拖拉机中铸件质量约占70%以上,而一台机床中铸件质量约占70%85%等等1。可见铸造生产出的铸件在国民经济的各个部门都占有相当的比重。我国在铸造技术方面,已有5000多年的悠久历史,是世界上应用铸造技术最早的国家。我国古代铸造技术居世界前列,勤劳智慧的中华名族在铸造技术方面做出了伟大的贡献。但是解放前,由于三座大山的残酷统治下,我国工业生产水平大大的落后了,铸造生产也长期处于落后状态。解放后,我国工艺水平也有了很大的发展和提高,尤其是改革开放以来随着我国国民经济的大发展,铸造生产也突飞猛进2。中国是当今世界上最大的铸件生产国家,据资料介绍,我国铸造产品的产值在国民经济中约占1%左右。最近几年,铸件进出口贸易增长较快,铸件的产量已达到9%左右。我国铸造厂点多达2万多个,铸造行业从业人员达120万之多。“长三角”地区的铸件产量占全国的1/3,该地区主要以民营企业为主,汽车和汽车零部件行业的发展有力地拉动了铸造行业的发展2。轿车气缸体铸件能力。尤其山西有丰富的生铁、煤炭、铝镁、电力、劳力资源、使山西的铸造产业有得天独厚的优势,具有500个铸造企业,80%为民营企业。山西国际、河津山联、山西华翔年产量分别达4万t、2万t、12万t。“东三省”有一汽集团、哈飞集团等骨干汽车企业带动了汽车铸件产量的增长。一汽集团铸造公司,已经形成40万t铸件的生产能力。“珠江三角洲”压铸行业发达,有700多个压铸企业,年产量达20万t。东风日产、广州本田、广州丰田和零部件企业有力带动了压铸业的发展,轿车气缸体、气缸盖的压铸件产量逐年增长。 但是我国铸造行业中多数以上的铸造车间属于单件、小批量、多品种生产。生产出的铸件尺寸精度低,表面质量差,能源和原材料消耗多,生产效率低,劳动强度大,企业的效益差5。1.2.2 国外铸造工艺发展情况近几年来,全球铸造业持续增长。巴西铸件产量增长最快,达到25.8%。而发达国家的铸件增长率普遍较低。美国铸件产量自2000年以来,已经退居到第2位。2004年美国铸件总产量为1231万t,其中灰铁件占35%、球铁件占33%、铸钢件占8.4%、铝合金件占16%。从需求上看,球铁铸件和铝铸件的需求在增长。2003年进口铸件占总需求的15%,进口铸件的价格比美国国内低20%50%5。近年来因铸造环保要求高、能源消耗大、劳动力昂贵等原因,美国大型汽车公司生产普通汽车铸件的铸造厂纷纷关闭,逐步将铸件的生产转向中国、印度、墨西哥、巴西等发展中国家。日本的铸造业不景气,其从业人员在减少。2004年日本铸件总产量为639万t,其中灰铁件占42%、球铁件占30%、铸钢件占4%、铝合金件占21%。从需求上看,球铁铸件和铝铸件的需求在增长。日本铸造界在技术创新方面作了大量工作,开发了球型低膨胀铸造砂、高减振铸铁材料、中硅耐热球铁等材料。其真空压铸的铸件能焊接和热处理,半固态铸造生产用于汽车铝轮毂,提高了强度和伸长率。镁合金压铸进一步发展,并取代重力铸造,其性能提高,成本降低。发达国家总体上铸造技术先进、产品质量好、生产效率高、环境污染少、原辅材料已形成商品化系列供应,如在欧洲已建立跨国服务系统。生产普遍实现机械化、自动化、智能化(计算机控制、机器人操作)4。在大批量中小铸件的生产中,大多采用微机控制的高密度静压、射压或气冲造型机械化、自动化高效流水线湿型砂造型工艺。在铸造生产的过程中,从严执行技术标准,铸件的废品率仅为2%-5%。总体上国外铸造的机械化、智能化水平比较高5。1.3 ZG32MnMo的性能及铸造工艺特点1.性能:较高的强度、塑性及韧性,重型机械中用于制造承受大负荷的零件,如轧钢机机架、水压机底座等;在铁路车辆上用于制造受力大又承受冲击的零件如摇枕、侧架、车轮和车钩。但其流动性差,容易形成冷隔。钢水温度高,体收缩和线收缩比较大,易缩孔缩松,热烈冷冽倾向大,氧化吸气较大,易产生夹渣的气孔,粘砂比较严重。2.工艺特点:(1) 型砂性能要求更高(如强度、耐火度、透气性等)。为防止粘 砂,铸型表面应涂上一层耐火材料。(2) 为使钢液顺利地流动、充型、补缩,使用更多的冒口和冷铁。 (3) 要严格控制浇注温度,避免过高(使钢液易氧化)或过低(使流动性降低)。1.4 本设计的具体内容1、本文主要对ZG32MnMo左诱导轮支架铸造工艺进行设计。(1)审查零件结构,确定最佳的浇注位置和分型面;(2)选择最优的造型、制芯方法;(3)浇注系统的设计则采用新颖的砂箱式浇口杯来实现两组浇注系统的同注;2、在确定了铸造工艺方案后,对铸造工艺装备进行设计。经过对铸件及砂芯的结构形状的分析,为节约成本及简化工艺,模样与芯盒的设计则选择了木质材料,对木质模样及芯盒进行可行性的设计。3、利用计算机技术来辅助铸造工艺的设计。主要采用AutoCAD对ZG32MnMo左诱导轮支架零件进行平面图的绘制;利用Pro/E软件对该零件进行三维实体造型,更加直观的表达出设计内容。AutoCAD平面图主要包括:零件图,毛培图,工艺图,芯盒图。 1.5 本章小结本章主要对铸造的发展和ZG32MnMo的性能及铸造工艺特点进行分析,为下一章的设计奠定基础。第2章 ZG32MnMo左诱导轮支架的性能分析2.1 ZG32MnMo的化学成分及力学性能和锰钢相比,ZG32MnMo在高温下具有较高的屈服强度,室温下屈服强度和抗拉强度都比较高,无明显回火脆性和有较好的淬透性。铸造锰钼钢的化学成分和力学性能如表2-1和表2-2所示。表2-1 ZG32MnMo的化学成分(%)钢号 C Si Mn Mo S,PZG32MnMo 0.17-0.27 0.17-0.37 0.90-1.20 0.20-0.30 =0.04表2-2 ZG32MnMo的力学性能钢号 热处理 s b 5 k HBW (MPa) (MPa) (%) (%) (J/cm2) ZG32MnMo 调质 265 471 19 40 50 1562.2 ZG32MnMo的熔炼工艺熔炼工艺:用氧化法可以冶炼各种低、中合金钢,其冶炼方法与碳钢相似。在工艺上应注意掌握合金的加入和加入量。1 熔化期通电熔化用允许最大功率通电,熔化炉料。助熔推料助熔。熔化后期,加入适量的渣料造渣。炉料熔化60%-80%时,可吹氧助熔。取样扒渣炉料熔清后,充分搅拌钢液,取一号钢样,分析C、P,保持渣量3%左右。2氧化期脱碳当钢液温度达到1560以上时,可进行吹氧脱碳或吹氧-矿石脱碳操作。吹氧压力0.6-0.8MPa。估计钢液含碳量低至规格下线时,停止供氧,充分搅拌钢液,取二号钢液分析C、P、Mn。3还原期扒渣出去全部氧化渣,加入锰铁,并加入2%-3%渣料,造稀薄渣。还原稀薄渣形成后,加入还原渣料,恢复通电,进行还原。钢液在良好的还原渣下保持的时间一般不小于20min。取样充分搅拌,取三号样,分析C、Si、Mn、P、S并取渣样分析。调整成分根据钢样分析结果,调节钢样的化学成分。测温测量钢液的温度,并做圆环试样,检查钢液的脱氧情况。4出钢钢液温度符合要求,圆环试样收缩良好,停电,升高电极,插铝,出钢。其中出钢浇铸时要注意: 1)当钢液温度、化学成分、脱氧情况符合要求时,插铝终脱氧,停电清炉出钢。钢液出炉后在包内钢液表面上加覆盖剂,镇静3-5min后浇铸。 2)出炉后检测:勤观察炉况变化,用化学分析法与直读式光谱仪分析钢的化学成分,炉前浇铸圆环试样检查脱氧情况,用热电偶测量钢液温度,出钢温度1600-1620,浇铸温度1540-15609。2.3 ZG32MnMo左诱导轮支架的技术要求2.3.1 零件实体图ZG32MnMo左诱导轮支架为高强度优质件,其形状、结构如图2.1(a)、(b)所示。(a) (b)图2-1 ZG32MnMo左诱导轮支架的形状及结构2.3.2 主要技术要求1.未注铸造圆角半径为R3-R6.铸造尺寸公差为2,铸造斜度不大于3;2.热处理硬度255-302HB(压痕直径3.8-3.5);3.外加工表面上最大尺寸为10,深度达5不聚集疵孔不超过5个时允许不补焊;4.螺纹孔倒角120至螺纹外径;5.倒钝锐边;6.在112,216的圆柱表面上最大尺寸达10,深度达5不聚集疵孔不超过5个时允许不补焊;7.外表面T铁红C06-1IIYHG/T2009-1991;8.112孔壁在1/3圆周上允许减薄到18不小于15时允许补焊;9.螺纹孔12M201.5在20长度内允许有2扣断扣,孔数不多于2个;2.4本章小结 本章主要对ZG32MnMo左诱导轮支架的性能分析和零件技术要求的了解,为下一章铸造工艺方案的确定打下基础。第3章 铸造工艺方案的确定 根据ZG32MnMo的合金特性、左诱导轮支架的结构、产品质量要求和生产批量,合理选择铸造工艺方法,不仅要确保产品质量,还需要提高生产效率,降低成本,提其高经济效益。ZG32MnMo铸件通常采用砂型铸造和金属型铸造,由于左诱导轮支架尺寸较大,生产数量为2件,制作金属型的成本较高,工作不方便灵活,且砂型铸造的生产周期短、成本低,因此选用砂型铸造。砂型铸造工艺方案通常包括下列内容:审查零件结构的铸造工艺性,造型、造芯方法的选择,浇注位置的确定,分型面的选择。3.1 零件结构的铸造工艺性3.1.1左诱导轮支架的结构工艺性零件结构铸造工艺性是指零件的结构应符合铸造生产的要求,易保证铸件的品质,简化铸造工艺过程和降低成本。左诱导轮支架结构具有如下特点:壁厚合适,最小壁厚为14mm,满足表3-1所要求的最小壁厚。铸造时能有效的避免浇不到、冷隔等缺陷,保证有良好的充型。零件最大壁厚65mm,壁厚分布有利于实现顺序凝固,但在厚壁处热节太大,导致中心部分晶粒粗大,容易出现缩松和缩孔缺陷,降低力学性能。铸件没有长板,长箱体等易产生翘曲变形的结构,虽铸件收缩较大,但铸造时不用考虑变形。在铸件的壁厚处有圆角过渡,使铸件在凝固收缩时阻力较小,减小了热裂的产生 。3.1.2铸件质量对零件结构要求(1)铸件的最小壁厚查铸造手册(5)铸造工艺表3-1得知当铸件最大轮廓尺寸为400-800mm时最小壁厚为12mm,而本课题中的最小壁厚为14,所以铸件可铸出。表3-1 砂型铸造时铸件的最小允许壁厚合金种类铸件的轮廓尺寸 mm2000中合金钢8-99-10121620253.2 造型、造芯方法的选择ZG32MnMo左诱导轮支架为两件小批量生产的大型铸件,选用手工造型即可。手工造型能适应各种复杂的要求,比较灵活,不要求很高的工艺装备。考虑到该铸件为铸钢件,而且为大件,为提高其精度、减小铸造缺陷,选用生产效率高、节能、型砂强度高,落砂性能好的三乙胺气硬法树脂砂造型和造芯。虽然现在有更环保的无毒气硬冷芯盒树脂砂,但已研发出的几种无毒气硬冷芯盒树脂砂仍存在着一些问题6: (1)砂芯的常温强度较低,为了提高砂芯的常温强度,不得不增加树脂的加入量,而导致制芯成本提高;(2)吹气体不能够迅速凝胶,并建立起较高的初强度和终强度;(3)砂芯吸湿性较差。该铸件的型砂配方组成如表3-2所示。表3-2 ZG32MnMo左诱导轮支架的型砂配方原砂硅砂细度5060砂温2126含水量00.1%酸耗值尽量低粘结剂液态酚醛树脂和聚异氰酸酯1:1匹配占砂质量的1.0%固化剂体积分数6.5%的三乙胺载体气体氮气混制工艺:原砂酚醛树脂聚异氰酸酯混制卸砂10s 10s 50s混好的型(芯)砂应尽快使用,存放时间一般为23小时。3.3浇注位置的确定铸件的浇注位置是指铸件在铸型内浇注时的所处的位置。浇注位置是根据零件的结构特点、尺寸、重量、技术要求、铸造合金特性、铸造方法及生产车间的条件决定的。正确的浇注位置应能保证获得健全的铸件,并使造型、造芯和清理方便。浇注位置的选择,主要是保证铸件质量为出发点。因此在铸件工艺设计时,要根据技术要求,先找出铸件质量要求高的部位和容易产生缺陷的部分,将这些部分放在有利的位置,保证其质量要求。经分析铸件的结构,根据合金的凝固理论的研究和生产的经验确定该铸件的浇注位置有以下图3-1和图3-2两种方案: 图3-1方案一 图3-2方案二分析:方案一的顶部上表面是一个类似于圆台的结构,在铸后要机械加工,所以能保证铸件质量,且表面结构简单,有益于冒口的安放,有益于实现顺序凝固。而方案二的顶部上表面为非加工面,且不平整,结构复杂,有凸台、凹坑等,所以若浇注位置选方案二,则上表面的质量无法保证,且将给机械加工带来很大的不便。方案一所示浇注位置较方案二有以上优点,综上所述:选择方案一所示浇注位置。3.4分型面的选择合理的选择分型面对于简化铸造工艺、提高生产率、降低成本、提高铸件质量等都有之直接关系。分型面的选择尽量与浇注位置保持一致,避免合型后翻转砂箱。根据分型面的选择原则与铸件的结构特征,分型面的选择考虑了图3-3所示的两种选择方案。1处分型面为方案一,2处分型面为方案二。图3-3分型面选择的两种方案方案一特点:优点:(1)该平面有利于起模,便于造型;(2)铸件内部空腔通过砂芯解决,主要砂芯放在下半型中,有利于下芯、合型和检查型腔尺寸;(3)铸件的大部份置于同一半型内;(4)易于铸件清理;缺点:(1)在浇注时,金属液对垂直砂芯冲刷,容易发生偏芯。(2)砂箱高度较高,对起模有一定不利影响。方案二特点:优点:(1) 分型面为铸件横向最大平面。缺点:(1)铸件几乎平分于两个半型,对铸件的精度和铸件成分的同一性有不利影响。(2)分型面虽然是铸件横向的最大平面,但是由于1处凸台的影响,非常不利于起模,造型。对两种方案进行分析对比,在充分保证铸件质量的前提下,综合考虑以上两种分型,最终采用分型方案一。3.5 砂箱中铸件数目的确定在小批量生产中,ZG32MnMo左诱导轮支架的零件尺寸为323317527mm,其尺寸比较大,考虑到车间的起吊能力及吃砂量,节约成本、简便工艺,故选用标准砂箱,一箱两件。3.6本章小结 本章主要确定浇铸位置和飞型面,为下一章砂芯的设计提供有力的基础。第4章 砂芯设计及铸造工艺参数设计4.1 砂芯、芯头的设计砂芯的功用是形成铸件内腔、孔和铸件外形不能出砂的部位。砂芯应满足以下要求:砂芯的形状、尺寸以及在砂型中的位置应符合铸件要求,具有足够的强度和刚度,在铸件形成过程中砂芯所产生的气体能及时排除铸型外,铸件收缩时阻力小并且容易清砂。4.1.1 砂芯数量的确定砂芯主要靠芯头固定在砂型上。ZG32MnMo左诱导轮支架的内腔结构复杂,经过分析,最终确定由五个砂芯组成,即可实现形成其内腔和孔。本设计中总共用到5个砂芯,其位置与形状大致如图4-1(a)、(b)所示: (a) (b)图4-1 铸件所需用砂芯的位置及形状4.1.2 砂芯的固定和定位一般用芯头来固定,也有用芯撑或铁丝来固定。本设计中的1、2、3、4、5号砂芯都为垂直砂芯,1 用上芯头固定,2、3、4、5用下芯头固定。4.1.3 1#砂芯的设计与校核1#砂芯的CAD图如图4-2所示,实体图如4-3所示。 图4-2 1#砂芯CAD图 图4-3 1#砂芯实体图1#砂芯为垂直砂芯,芯头的斜度和水平芯头与芯座之间的间隙,以及芯头长度和防压环尺寸可查文献4铸造手册表3-92、表3-93和表3-94得出:砂芯长度为L=186mm(101200mm),芯头的横截面积尺寸分别为D1=330mm(301500mm),D2=206mm(151300mm),表4-1 1#砂芯的芯头尺寸芯头号芯头长度(mm)斜度及间隙(mm)S1S2S31401.01.52.0图4-4 芯头间隙和斜度示意图1#砂芯芯头承压面积的核算:芯头的承压面积S应满足公式 (4-1)式中,F芯计算的最大浮力或重力;k 安全系数,k=1.31.5,取1.3; 压铸型许用应力,干砂型可取0.60.8Mpa,本铸件为树脂砂,取0.7Mpa。F芯=F浮-G=金Vg-G=76Kg9.8N/Kg-65.86Kg9.8N/Kg=99.372N=1.399.372N/0.7Mpa=184.548mm2S=D1l1+D2l2=330mm40+206mm60mm=25560mm2经校核芯头S满足金属液浮力要求。F芯=G=65.86Kg9.8N/Kg=645.428N=1.3645.428N/0.7Mpa=1198.652mm2经校核芯头S满足重力要求。4.1.4 2#砂芯的设计与校核2#砂芯的CAD图如图4-5所示,实体图如4-6所示。 图4-5 2#砂芯CAD图 图4-6 2#砂芯实体图2#砂芯为垂直砂芯,芯头的斜度和水平芯头与芯座之间的间隙,以及芯头长度和防压环尺寸可查文献5铸造手册表3-92、表3-93和表3-94得出:砂芯长度为L=151mm(101200mm),芯头的横截面积尺寸分别为D1=102mm(101150mm),D2=247mm(151300mm),表4-2 2#砂芯的芯头尺寸芯头号芯头长度(mm)斜度及间隙(mm)S1S2S31401.01.52.02#砂芯芯头承压面积的核算:芯头的承压面积S应满足公式 (4-1)式中,F芯计算的最大浮力或重力;k 安全系数,k=1.31.5,取1.3; 压铸型许用应力,干砂型可取0.60.8Mpa,本铸件为树脂砂,取0.7Mpa。F芯=F浮-G=金Vg-G=42Kg9.8N/Kg-35.6Kg9.8N/Kg=62.72N=1.362.72N/0.7Mpa=116.48mm2S=18900mm2经校核芯头S满足金属液浮力要求。F芯=G=35.6Kg9.8N/Kg=348.88N=1.3348.88N/0.7Mpa=647.92mm2经校核芯头S满足重力要求。4.1.5 3#砂芯的设计与校核3#砂芯的CAD图如图4-7所示 图4-7 3#砂芯CAD图砂芯长度为L=323mm(301500mm),芯头的横截面积尺寸分别为D1=131mm(101150mm),D2=146mm(101150mm)。表4-3 3#砂芯的芯头尺寸芯头号芯头长度(mm)斜度及间隙(mm)S1S2S31552.03.04.02401.01.52.03#砂芯芯头承压面积的核算:芯头的承压面积S应满足公式 (4-1) 式中,F芯计算的最大浮力或重力;k 安全系数,k=1.31.5,取1.3; 压铸型许用应力,干砂型可取0.60.8Mpa,本铸件为树脂砂,取0.7Mpa。F芯=F浮-G=金Vg-G=52Kg9.8N/Kg-42.16Kg9.8N/Kg=96.432N=1.396.432N/0.7Mpa=179.088mm2S=14000mm2经校核芯头S满足金属液浮力要求。F芯=G=42.16Kg9.8N/Kg=413.168N=1.3413.168N/0.7Mpa=767.312mm2经校核芯头S满足重力要求。4.1.6 4#砂芯的设计与校核4#砂芯的CAD图如图4-8所示 图4-8 4#砂芯CAD图砂芯长度为L=323mm(301500mm),芯头的横截面积尺寸分别为D1=50mm(3160mm),D2=186mm(151300mm)。表4-4 4#砂芯的芯头尺寸芯头号芯头长度(mm)斜度及间隙(mm)S1S2S31502.03.04.02551.01.52.04#砂芯芯头承压面积的核算:芯头的承压面积S应满足公式 (4-1)式中,F芯计算的最大浮力或重力;k 安全系数,k=1.31.5,取1.3; 压铸型许用应力,干砂型可取0.60.8Mpa,本铸件为树脂砂,取0.7Mpa。F芯=F浮-G=金Vg-G=40.2Kg9.8N/Kg-30.3Kg9.8N/Kg=97.02N=1.397.02N/0.7Mpa=194.04mm2S=D1l1+D2l2=410mm40+149mm60mm=13160mm2经校核芯头S满足金属液浮力要求。F芯=G=30.3Kg9.8N/Kg=296.94N=1.3296.94N/0.7Mpa=551.46mm2经校核芯头S满足重力要求。4.1.7 5#砂芯的设计与校核5#砂芯的CAD图如图4-9所示 图4-9 5#砂芯CAD图砂芯长度为L=329mm(301500mm),芯头的横截面积尺寸分别为D1=55mm(3160mm),D2=162mm(151300mm)。表4-5 5#砂芯的芯头尺寸芯头号芯头长度(mm)斜度及间隙(mm)S1S2S31602.03.04.02401.01.52.05#砂芯芯头承压面积的核算:芯头的承压面积S应满足公式 (4-1) 式中,F芯计算的最大浮力或重力;k 安全系数,k=1.31.5,取1.3; 压铸型许用应力,干砂型可取0.60.8Mpa,本铸件为树脂砂,取0.7Mpa。F芯=F浮-G=金Vg-G=90.2Kg9.8N/Kg-76.2Kg9.8N/Kg=137.2N=1.3137.2N/0.7Mpa=178.36mm2S=11920mm2经校核芯头S满足金属液浮力要求。F芯=G=76.2Kg9.8N/Kg=746.76N=1.3746.76N/0.7Mpa=1386.84mm2经校核芯头S满足重力要求。4.2 铸造工艺设计参数工艺参数选取的准确、合适,才能保证铸件尺寸精确,使造型、制芯、下芯、合箱方便,提高生产率,降低成本。由于工艺参数的选取与铸件尺寸、重量、验收条件有关,把铸件的尺寸和重量公差也在此说明。4.2.1 铸件尺寸公差 铸件的尺寸精度取决于工艺设计及工艺过程控制的严格程度,其主要考虑因素有:铸件结构复杂程度;铸件设计及铸造工艺设计水平;造型、制芯设备及工装设备的精度和质量;造型、制芯材料的性能和质量;铸造金属和合金种类;铸件热处理工艺;铸件清理质量;铸件表面粗糙度和表面质量;铸造厂的管理水平等。该铸件为铸钢两件小批量生产的大型铸件,采用树脂砂手工造型,按照GB6414-86铸件尺寸公差制最终选取公差等级为CT12。4.2.2 机械加工余量为保证铸件加工面尺寸和零件精度,应留有加工余量,即在铸件工艺设计时预先增加的,而后在机械加工时又被切去的金属层厚度。加工余量过大浪费金属和加工工时;过小,不能完全去除表面缺陷,甚至达不到设计要求3。该铸件按GB/T11350-89铸件机械加工余量规定的加工余量的数值和确定方法,与GB6414铸件尺寸公差配合最终选取,具体位置如图4.10,具体数值见表4-6。图4.10 机械加工部位表4-6 机械加工余量具体数值序号基本尺寸(mm)加工余量等级数值(mm)铸件尺寸1317K83252110K81023247H1.5248.54317K103275216K102066145J41497128G171114.2.3 铸造收缩率铸造收缩率K定义为: (4-2)式中,LM模样工作面的尺寸; LJ铸件尺寸;查铸造工艺设计表1-14常用铸造合金线收缩率(%),得出铸造碳钢自由收缩率1.62.2%,受阻收缩率1.51.7%,选取其收缩率为1.6%。4.2.4 起模斜度为了方便起模,在模样及芯盒的出模方向应有一定起摸斜度,起模斜度的形式有三种,如图4.11所示。本铸件的大部分壁厚为18-30mm,所以采用第三种减少铸件壁厚的形式即可,由于本铸件采用树脂砂而且是采用木模,所以查铸造工艺设计表1-15,确定a=3.8mm。图4-11 起模斜度形式(JB/T5105-1991)4.2.5 最小铸出孔及槽零件上的孔是否铸出,必须即考虑铸出孔的可行性,又要考虑到铸出孔的必要性和经济性。铸钢铸件最小铸出孔直径如表4-7所示,实体图如4-12所示。 表4-7铸刚件最小铸出孔尺寸 (单位:mm)孔深H孔壁厚度2526-5051-5776-100101-150151-200201-300300铸孔最小直径10060607080100120140160101-20060708090120140160190201-4008090100110140170190230401-600100110120140170200230270601-10001201301501702002302703001000140160170200230260300330 图4.12 铸孔的位置表4-8 左诱导轮支架铸出孔情况序号数量尺寸(mm)深度铸出情况1122030不铸出231012不铸出316512不铸出综合考虑各方面因素,最终确定本铸件不铸出这几种孔,其他的孔则铸出。4.2.6 分型负数为了保证铸件尺寸精度,抵消铸件在分型面部位的增厚,在模样上相应减去的尺寸称为分型负数。具体数值参照表4-9后,分型负数选取3mm。表4-9分型负数选取原则砂箱长度/mm10001001-20002001-35003501- 50005000分型负数/mm干型23457表干型123464.3 本章小结 本章主要进行了铸造工艺参数的设计,为下一章的浇注系统和冒口的设计做准备。第5章 浇注系统及冒口的设计5.1 浇注系统的类型及选择浇注系统是砂型中引导液态金属进入型腔的通道。应满足以下要求:(1)控制金属流动的速度和方向,并保证充满型腔;(2)有利于铸件温度的合理分布;(3)金属液在型腔中的流动应平稳、均匀,以避免夹带空气、产生金属氧化物及冲刷砂型;(4)浇注系统应具有除渣功能;本铸件选取开放式中间注入式浇注系统,具有金属液进入型腔时液流速度小,充型平稳,冲刷力小,金属氧化轻等优点。5.2 浇注时间的确定查公式得:=Amn (5-1) 式中 浇注时间(s) m 铸件重量(kg) A,n系数,取决于铸件壁厚该铸件的体积为:15469.565685cm3,其密度为:7.810-3kg/cm3,所以铸件的质量为:15469.565685cm37.810-3kg/cm3=120.662612343kg查铸造工艺学表3-4-4得:A=1.5-2.35 n=0.5故当A取最小时=Amn=1.5120.660.5=16.5s当A取最大时=Amn=2.35120.660.5=25.85s所以的取值范围为16.525.85s浇注时间的校核型内金属液面上升速度V型 (5-2)C-铸件(或某段)的高度 -浇注时间(或浇注某段铸件时间)从理论上看,存在着V型min(防止浇不到、冷隔和夹砂等缺陷)和V型max(保证型内排气和防止过度紊流)两个极限值,合适的浇注 时间应满足如下条件:存在着V型min(防止浇不到、冷隔和夹砂等缺陷)和V型max (保证型内排气和防止过度紊流)两个极限值,合适的浇注 时间应满足如下条件: (5-3)对于铸钢铸件,一般只核算最小上升速度,该铸件壁厚在14-25mm,相对整个铸件而言壁厚较厚,查铸造工艺学表3-4-7取为20mm/s,该铸件高度约为360mm,最大浇注时间为360/20=18s。根据本铸件的壁厚特点,为了减少充型期间对砂型上表面的热作用时间,防止夹砂结疤、粘砂、冷隔、浇不足等缺陷,该件选择快浇,而且对于铸钢件,快浇可充分利用共晶膨胀消除缩孔缩松缺陷。本铸件质量121Kg250 Kg,查表3-4-3,一般取1220秒,结合本铸件最终确定浇注时间为18秒。5.3 确定浇口比及各浇道的设计与计算5.3.1 确定浇口比本设计采用阶梯式浇注系统,此种浇注系统为开放式浇注,根据浇道系统类型,初步确定浇口比为:S直:S横:S内=1:1.2:1。5.3.2 阻流截面积计算由奥赞公式 (5-4)-阻流截面积 m通过阻流浇道的金属液质量(kg)-金属液密度,取7.810-3kg/cm3 -充填型腔时间(S)-浇注系统的流量损耗系数,对于四组元件而言取0.48 -重力加速度,取9.810-3kg/cm3p-充填型腔时的平均计算压力头高度(1) m计算根据铸件质量和预计工艺出品率估算型内的钢液的质量,该铸件为特别重要中等件,大部分壁厚大于18mm,采用暗冒口,初步定为70%,则有m型=m/70%=1212kgm=345.7kg(2) Hp 的计算Hp=上层砂箱高度-铸件上砂箱高度=400-114=286mm所以有:5.3.3 各浇道的设计与计算根据上述阻流截面的面积得到 , 。该浇注系统有1个主直浇道,2个分直浇道,1个横浇道,4个底内浇道,4个上内浇道。根据铸造手册-铸造工艺-表3-224得到:主直浇道:分直浇道:每个分直浇道:同理取横浇道:, 根据铸造手册-铸造工艺-表3-225得:底内浇道: 根据铸造手册-铸造工艺-表3-227得:上层内浇道:根据铸造手册-铸造工艺-表3-227得: 则实际浇口比为:各个浇注系统的尺寸如图5-1。 图5-1 各浇注系统尺寸5.4 冒口的设计与计算冒口是在铸型内认为设置贮存金属液的结构,用以补偿铸件形成过程中产生的收缩,冒口的设计的基本原则有:(1)冒口的凝固时间应不小于铸件被补缩部分在凝固过程中的收缩时间;(2)冒口所能提供的补缩液量应不小于铸件的液态收缩、凝固收缩和型腔扩大量之和;(3)冒口和铸件需要补缩部分之间的整个补缩过程中应存在通道;(4)冒口体内要有足够的补缩压力;(5)冒口和铸件连接形成的热节应不大于铸件的几何热节;本铸件最后凝固部位出现在中间的壁厚部分,虽然铸件外侧部位不是加工表面,但为了保证铸件的尺寸及减少铸造缺陷,决定在铸件中心加冒口,由于冒口上侧是浇口杯,所以选用暗冒口,并且为了能顺利起摸,所以设计最终冒口的形状和尺寸如图5-2所示。图5-2 冒口的形状及尺寸5.5 本章小结 本章主要确定浇注系统和冒口的设计,为工艺装备的选择做准备。第6章 铸造工艺装备的设计6.1 模样的设计6.1.1 模样材料的选择左诱导轮支架铸件是两件小批量手工造型生产,根据铸件所要求的尺寸精度、生产成本、制模周期和使用寿命等考虑,采用轻便、容易加工、价格低廉的木质模样。其经济合理,使用方便,同时能满足工艺要求,保证产品质量8。6.1.2 模样的尺寸和等级ZG32MnMo左诱导轮支架选用木质模样。木质模样的生产,一般由制模工人直接依照铸造工艺图进行制作,很少进行模样设计。只需在铸造工艺卡片上填写模样的结构形式等级。木质模样的分模面与铸件的分型面一致。根据木质模样和芯盒使用的次数对铸件精度的要求不同分为三级。经过分析,该铸件选用级模样。其原则为:(1)铸件的尺寸精度和表面质量有一定要求或尺寸精度和表面质量要求不高,但均是多次使用的模样和芯盒;(2)铸件的尺寸精度和表面质量要求较高,但使用次数不多的模样和芯盒;(3)树脂砂用模样和芯盒,铸件产量不多于5件的。(满足以上情况之一即可选用级木质模样和芯盒);该铸件所有砂芯所要形成的部位为铸件的侧孔和内腔,其尺寸精度和质量要求不高
- 温馨提示:
1: 本站所有资源如无特殊说明,都需要本地电脑安装OFFICE2007和PDF阅读器。图纸软件为CAD,CAXA,PROE,UG,SolidWorks等.压缩文件请下载最新的WinRAR软件解压。
2: 本站的文档不包含任何第三方提供的附件图纸等,如果需要附件,请联系上传者。文件的所有权益归上传用户所有。
3.本站RAR压缩包中若带图纸,网页内容里面会有图纸预览,若没有图纸预览就没有图纸。
4. 未经权益所有人同意不得将文件中的内容挪作商业或盈利用途。
5. 人人文库网仅提供信息存储空间,仅对用户上传内容的表现方式做保护处理,对用户上传分享的文档内容本身不做任何修改或编辑,并不能对任何下载内容负责。
6. 下载文件中如有侵权或不适当内容,请与我们联系,我们立即纠正。
7. 本站不保证下载资源的准确性、安全性和完整性, 同时也不承担用户因使用这些下载资源对自己和他人造成任何形式的伤害或损失。

人人文库网所有资源均是用户自行上传分享,仅供网友学习交流,未经上传用户书面授权,请勿作他用。