帕萨特B5五档变速器结构设计【手动变速箱设计全套含有CAD图纸三维建模】
收藏
资源目录
压缩包内文档预览:(预览前20页/共59页)
编号:10048703
类型:共享资源
大小:73.49MB
格式:ZIP
上传时间:2018-04-23
上传人:机****料
认证信息
个人认证
高**(实名认证)
河南
IP属地:河南
50
积分
- 关 键 词:
-
帕萨特
b5
五档
变速器
结构设计
手动
变速箱
设计
全套
含有
cad
图纸
三维
建模
- 资源描述:
-








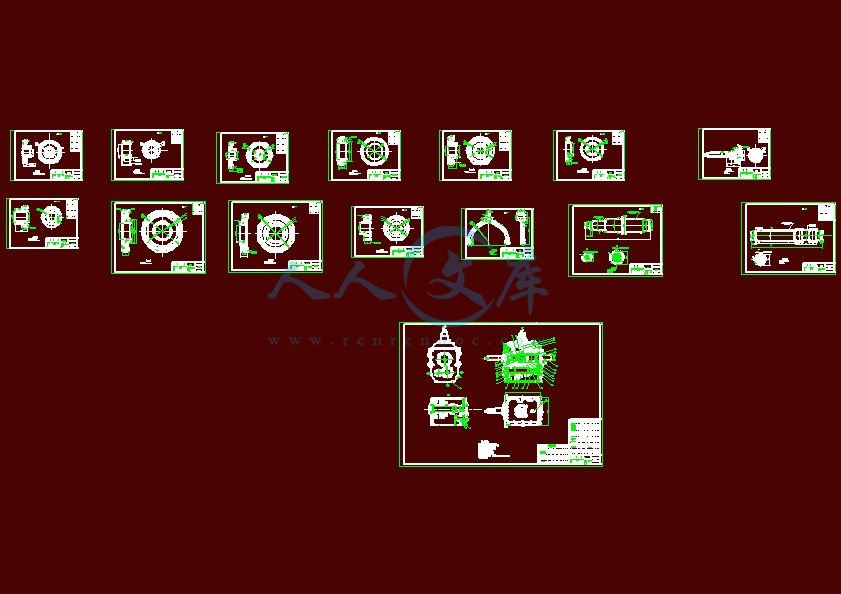
- 内容简介:
-
摘 要 本次设计以五档三轴手动档汽车的一些整车参数和发动机参数为设计依据,进行手动档变速器的设计。设计的主要内容包括变速器传动机构布置方案的确定,变速器主要参数如挡数、传动比范围、中心距、各挡传动比、齿轮参数、各挡齿轮齿数的选择,齿轮、轴的设计校核,同步器、操纵机构及箱体的设计。关键词:变速器;齿轮;轴;设计;计算机辅助设计 ABSTRACTThe transmission is designed based on engine parameters and vehicle parameters of Fiveof three axismanualin this text. The main design contents include the layout program of transmission drive-mechanism, the selection of main transmission parameters such as shifts, the range of gear ratio, center-spacing, each gear ratio, gear parameters and the numble of each gear, the design and verification of gears and shafts, the design of synchronizer, manipulation-framework and gearbox. Keywords: Transmission;Gear;Shaft;Design;Computer Aided Design 目 录第 一 章 绪论1 1.1 课题研究的现状1 1.2 课题研究的目的和意义21.3 设计完成的主要内容21.4 车型基本参数2第 二 章 变速器传动机构布置方案4 2.1 传动机构布置方案分析4 2.1.1两轴式和中间轴式变速器4 2.1.2倒档的形式和布置方案42.2 零、部件布置方案分析5 2.2.1齿轮形式5 2.2.2换档的结构形式6 2.2.3变速器轴承62.3本章小结7第 三 章 变速器主要参数的选择及设计计算8 3.1变速器的档位数、传动比和中心距的确定8 3.1.1档数8 3.1.2传动比范围8 3.1.3确定最低档传动比8 3.1.4初步确定其他各档传动比11 3.1.5初选中心矩113.2齿轮参数的确定11 3.2.1齿轮的模数12 3.2.2压力角12I 3.2.3螺旋角12 3.2.5 齿轮的变位系数的选择原则12 3.2.6齿顶高系数13 3.2.7 各档传动比及其齿轮齿数的确定13 3.2.8变速器齿轮的几何尺寸计算18 3.3本章小结21第 四 章 变速器主要结构元件的设计与计算224.1 齿轮损坏的原因及形式224.2 轮齿强度计算22 4.2.1轮齿弯曲强度计算23 4.2.2轮齿接触应力计算274.3 变速器齿轮材料的选择及热处理314.4轴的设计计算31 4.4.1初选轴的直径32 4.4.2轴的刚度验算32 4.4.3 轴的强度计算404.5本章小结43第 五 章 同步器的选择445.1 惯性式同步器44 5.1.1 锁环式同步器的结构44 5.1.2锁环式同步器的工作原理44 5.1.3锁环式同步器主要尺寸的确定455.2主要参数的确定46 5.2.1摩擦因数f 46 5.2.2同步环主要尺寸的确定46 5.2.3锁止角48 5.2.4同步时间48 5.2.5转动惯量的计算48II 5.3本章小结48结论49致谢50参考文献51III 第一章 绪 论1.1 课题研究的现状汽车变速器是汽车的重要部件之一,用来改变发动机传到驱动轮上的转矩和转速,目的是在原地起步、爬坡、转弯、加速等各种行驶工况下,使汽车获得不同的牵引力和速度,同时使发动机在最有利的工况范围内工作。变速器设有空档,可在起动发动机、汽车滑行或停车时使发动机的动力停止向驱动轮传输。变速器设有倒档,使汽车获得倒退行使能力。汽车变速器技术的发展历史:手动变速器(MT:Manual Transmisson)主要采用了齿轮传动的降速原理。变速器内有多组传动比不同的齿轮副,而汽车行驶时的换挡工作,也就是通过操纵机构使变速器内不同的齿轮副工作。自动变速器(AT:Automatic Transmisson)是由液力变矩器,行星齿轮和液压操纵系统组成,通过液力变矩器和齿轮组合的方式来达到变速变矩。AMT是在传统干式离合器和手动齿轮变速器的基础上改造而成,主要改变了手动换挡操纵部分。即在MT总体结构不变的情况下改用电子控制来实现自动换挡。无级变速器(CVT:Continuously Variable Transmission),又称为连续变速式机械变速器。金属带式无级变速器主要包括主动轮组,从动轮组,金属带和液压泵等基本部件。主要靠主动轮,从动轮和传动带来实现速比的无级变化,传动带一般用橡胶带,金属带和金属链等。无限变速式机械无级变速器(IVT:Infinitely Variable Transmisson)采用的是一种摩擦板式变速原理。IVT的核心部分由输入传动盘,输出传动盘和Variator传动盘组成。它们之间的接触点以润滑油作介质,金属之间不接触,通过改变Variator装置的角度变化而实现传动比的连续而无限的变化。计算机辅助设计(Computer Aided Design,简称CAD),泛指设计者以计算机为主要工具,对产品进行设计、绘图、工程分析与编撰技术文档等设计工作的总称,是一项综合性的技术。其中工程分析泛指包括有限元分析、可靠性分析、动态分析、优化设计及产品的常规分析等内容,亦称计算机辅助工程分析(Computer Aided Engineering,简称CAE)。Pro/ENGINEER (简称Pro/E)是美国Paramatric Technology Corporation公司开发的机械设计自动化软件,也是最早实现参数化技术商业化的软件。其功能是非常强大的,利用它可以进行零件设计、产品装配、数控加工、钣金件设计、铸造件设计,机构分析、有限元分析和产品数据库管理、应力分析、逆向造型和优化设计等。1.2 课题研究的目的和意义为了缩短设计周期和降低开发成本,通过CAD软件平台实现汽车变速器的辅助设计。使产品的设计阶段以较少的时间和精力进行虚拟装配并对装配结果进行验证,得到了可靠的装配检验结果。减少建模时间,增加模型可信度,提高产品质量,加快产品上市的时间。变速器是汽车的重要部件之一,主要是在汽车行进过程中改变传动比,从而改变汽车的行驶速度和驱动轮上的转矩,以适应变化的行驶条件;或利用倒档实现汽车的倒向行驶;在发动机不熄火的情况下利用空挡中断动力传递,便于汽车起动、怠速、换挡、和动力输出。它由几十个零件组成,零件之间的装配关系复杂。因此变速器的设计需要较长的时间和反复的实验。为了缩短设计周期和降低成本,基于CAD软件平台实现变速器的辅助设计是现代制造技术的必要手段。通过本毕业设计可以充分复习所学知识,能提高计算机及软件使用水平,为以后的工作打下坚实基础。1.3 设计完成的主要内容1、了解汽车变速器的研究现状;2、掌握汽车变速器结构及工作原理,绘出结构原理简图;3、确定主要零部件(齿轮、轴等)主要设计参数,并对关键部位进行校核;4、确定零部件结构尺寸;5、使用AutoCAD完成工程图纸;利用Pro/E建立体图;6、编写设计说明书。1.4 车型基本参数根据五档三轴手动档重型货车汽车的一些主要技术参数来设计变速器。通过网络查找此车型的基本参数,见表1.1 。表1.1 车型基本参数名 称数 据总质量mm=9000kg最大道路阻力系数=0.417最大扭矩=700/1500rpm最大功率P/nP = 155kw/3000rpm传动系机械效率=0.93最大爬坡度=16.5最高车速前、后轮胎规格215/65 R16第二章 变速器传动机构布置方案2.1 传动机构布置方案分析变速器由变速器传动机构和操纵机构组成。变速传动机构可按前进档数或轴的不同分类,分为固定轴式和旋转轴式两大类,而前者又分为两轴式,中间轴式和多中间轴式变速器等。2.1.1 两轴式和中间轴式变速器现代汽车大多数都采用固定轴式变速器,而两轴式和中间轴式应用最为广泛。其中,两轴式变速器多用于发动机前置前轮驱动的汽车上。中间轴式变速器多用于发动机前置后轮驱动的汽车和发动机后置后轮驱动的客车上。在设计时,究竟采用哪一种方案,除了汽车总布置的要求外,还要考虑以下几个方面:与中间轴式变速器比较,两轴式变速器因轴和轴承数少,所以有结构简单,轮廓尺寸小和容易布置等优点,此外,各中间档位因只经一对齿轮传递动力,故传动效率高,同时噪声也低。因两轴式变速器不能设置直接档,所以在高档工作是齿轮和轴承均承载,不仅工作噪声增大,且易损坏。还有,受结构限制,两轴式变速器的一档速比不可能设计的很大。对于前进档,两轴式变速器输入轴的转动方向与输出轴的转动方向相反;而中间轴式变速器的第一轴与输出轴的转动方向相同。中间轴式变速器可以设置直接档,在使用直接档时,变速器的齿轮和轴承及轴承均不承载,发动机转矩经变速器第一轴和第二轴直接输出,此时变速器的传动效率高,可达90以上,噪声低,齿轮和轴承的磨损减少。因为直接档的利用率高于其他档位,因而提高了变速器的使用寿命。在除直接档以外的其他档位工作时,中间轴式变速器的传动效率略有降低,这是它的缺点。对于本设计,采用如图2.1所示的传动方案,即中间轴式变速器。2.1.2 倒档的形式和布置方案图2.2为常见的布置方案。通过对汽车设计资料的查找总结以下方案:图2.2(b)方案的优点是倒挡利用中间轴上的1档齿轮,缩短了中间轴的长度,但换档时两对齿轮必须同时啮合,致使换档困难;图2.2(c)方案能获得较大的倒档速比,缺点是换档程序不合理;图2.2(d)方案针对前者的缺点做了修改;图2.2(e)方案中,将中间轴上的一档和倒档齿轮做成一体,其齿宽加大;图2.2(f)方案采用了全部齿轮副均为常啮合齿轮,换档更为轻便;综合考虑以上因素,为了换挡轻便舒适,减小噪声,倒挡传动采用图2.2(f)所示方案。图2.1中间轴式变速器传动方案图2.2倒档布置方案2.2 零、部件布置方案分析2.2.1 齿轮形式变速器用齿轮有直齿圆柱齿轮和斜齿圆柱齿轮两种。与直齿圆柱齿轮比较,斜齿圆柱齿轮有使用寿命长、运转平稳、工作噪声低等优点;缺点是制造时稍复杂,工作时有轴向力,这对轴承不利。变速器中的常啮合齿轮均采用斜齿圆柱齿轮,尽管这样会使常啮合齿轮数增加,并导致变速器的质量和转动惯量增大。直齿圆柱齿轮仅用于一档和倒档。2.2.2换档的结构形式变速器换档机构形式分为直齿滑动齿轮、啮合套和同步器换档三种。1、滑动齿轮换档通常采用滑动直齿轮换档,也有采用斜齿轮换档的。滑动直齿轮换档的优点是结构简单、紧凑、容易制造。缺点是换挡时齿面承受很大的冲击,会导致齿轮过早损坏,并且直齿轮工作噪声大,所以这种换档方式一般仅用于一档和倒档。2、啮合套换档用啮合套换档,可将构成某传动比的一对齿轮,制成常啮合的斜齿轮。用啮合套换档,因同时承受换档冲击载荷的接合齿齿数多,而轮齿又不参与换档,它们都不会过早损坏,但不能消除换档冲击,所以仍要求驾驶员有熟练的操纵技术。此外,因增设了啮合套和常啮合齿轮,使变速器的轴向尺寸和旋转部分的总惯性力矩增大。因此,这种换档方法目前只在某些要求不高的档位及重型货车变速器上应用。3、同步器换档现代大多数汽车的变速器都采用同步器能保证迅速,无冲击,无噪声换档,而与操纵技术熟练程度无关,从而提高了汽车的加速性、经济性和行车安全性。同上述两种换档方法相比,虽然它有结构复杂,制造精度要求高,轴向尺寸大。同步环使用寿命短缺等缺点,但仍然得到广泛应用。由于同步器的广泛应用,寿命问题已得到基本解决。上述三种换档方案,可同时用在一变速器中的不同档位上,一般倒档和一档采用结构较简单的滑动直齿轮或啮合套的形式;对于常用的高档位则采用同步器换挡。2.2.3 变速器轴承作为旋转运动的变速器轴支承在壳体或其他部位的地方以及齿轮与轴不做固定连接处应安置轴承。变速器轴承常采用圆柱滚子轴承,球轴承,滚针轴承,圆锥滚子轴承,滑动轴套等。至于何处应当采用何种类型的轴承,受结构限制并随所承受的载荷特点不同而不同。近年来,变速器的设计趋势是向轻量化方向发展。圆锥滚子轴承在一些变速器上得到应用。其主要优点如下:直径较小,宽度较宽,因而容量大,可承受高负荷和通过对轴承预紧能消除轴向间隙及轴向窜动等。滚针轴承主要用于齿轮与轴不是固定连接,并要求两者有相对运动的地方。滚针轴承有滚动摩擦损失小,传动效率高,径向配合间隙小,定位及运转精度高,有利于齿轮啮合等优点。2.3 本章小结本章对变速器传动机构的布置方案和零、部件结构方案进行了系统的分析,并给出了此次设计的具体方案,即设计中间轴式变速器,倒档布置方案如图2.1(f)所示,前进档除了一档外皆为斜齿圆柱齿轮,倒档为直齿圆柱齿轮,采用全同步器换挡和啮合套形式,轴承选取滚针轴承、圆锥滚子轴承。第三章 变速器主要参数的选择及设计计算3.1 变速器的档位数、传动比和中心距的确定3.1.1 档数变速器的档数可在320个档位范围内变化,通常变速器的档数在6挡以下,当档数超过6档以后,可在6档以下的主变速器基础上,再行配置副变速器,通过两者的组合获得多档变速器。增加变速器的档数,能够改变汽车的动力性和燃油经济性以及平均车速。档数越多,变速器的结构越复杂,并且使轮廓尺寸和质量加大,同时操纵机构复杂,而且在使用时换档频率增高并增加了换档难度。在最低档传动比不变的条件,增加变速器的档数会使变速器相邻的低档与高档之间的传动比比值减小,使换档工作容易进行。要求相邻档位之间的传动比值在1.8以下,该值越小换档工作越容易进行。因高档使用频繁,所以又要求高档区相邻档位之间的传动比比值,要比低档区相邻档位之间的传动比比值小。近年来,为了降低油耗,变速器的档数有增加的趋势。目前,商用车一般用45个档位的变速器。发动机排量大的乘用车变速器多用5个档。对于皮卡汽车,选用5个前进档和1个倒档的变速器。3.1.2 传动比范围变速器的传动比范围是指变速器最低挡传动比与最高挡传动比的比值。最高挡通常是1.0,有的变速器最高挡是超速挡,传动比为0.70.8。影响最低挡传动比选取的因素有:发动机的最大转矩和最低稳定转速所要求的汽车最大爬坡能力、驱动轮与路面间的附着力、主减速比和驱动轮的滚动半径以及所要求达到的最低稳定行驶车速等。本次设计的变速器最高档位超速档。3.1.3 确定最低档传动比应依据汽车最大爬坡度,驱动车轮与路面间的附着力,汽车的最低稳定车速,以及主减速比和驱动车轮的滚动半径等综合考虑确定。汽车在最大上坡路面上行驶时,最大驱动力应能克服轮胎与路面间滚动阻力及上坡阻力。由于汽车上坡行驶时车速不高,故忽略空气阻力。这时, + (3.1) = =式中, 最大驱动力;滚动阻力;最大上坡阻力; 汽车总质量;g 重力加速度;驱动车轮滚动半径;发动机最大转矩;主减速器传动比;传动系传动效率;滚动阻力系数;变速器一档传动比;道路最大上坡角;分动器传动比。代入式(3.1):=式中 最大道路阻力系数由发动机转速与汽车行驶速度之间的关系式:求得: =4.8所以 =3.8所以,由最大爬坡度要求的变速器一档传动比为:=3.9根据驱动车轮与路面的附着条件: (3.2)求得变速器一档传动比为:=6式中, 汽车满载静止于水路平面时驱动桥给地面的载荷 道路的附着系数,计算时取=0.70.8所以 3.86在一般汽车的传动比范围内3.84.6之间。3.1.4 初步确定其他各档传动比变速器的最高档位直接档,所以=0.75,取=5.7。根据经验公式,按等比级数分配, (3.3)几何级数的公比所以,=3.43,=2.06,=1.24。3.1.5 初选中心矩对中间轴式变速器,是将中间轴与第二轴轴线之间的距离成为变速器的中心矩。它的大小不仅对变速器的外形尺寸,体积和质量大小有影响,而且对轮齿的接触强度有影响,所以,最小允许的中心距应当由保证轮齿有必要的接触强度来确定。中间轴式变速器初选中心距时,可根据经验公式计算: = (3.4)式中, 中心距系数,对商用车=8.69.8,所以,=154mm乘用车变速器的中心距约在80170范围内变化,经过圆整后取中心距=154mm。3.2 齿轮参数的确定3.2.1 齿轮的模数齿轮模数是一个重要参数,并且影响它的选取因素又很多,如齿轮的强度、质量、噪声、工艺要求等。应该指出,选取齿轮模数时一般要遵守的原则是:在变速器中心距相同的条件下,选取较小的模数,就可以增加齿轮的齿数,同时增加齿宽可以使齿轮啮合的重合度增加,并减少齿轮噪声,所以为了减少噪声应合理减少模数,同时增加齿宽;为使质量小些,应该增加模数,同时减少齿宽;从工艺方面考虑,各挡齿轮应该选用一种模数,而从强度方面考虑,各挡齿轮应有不同的模数;减少乘用车齿轮模数对工作噪声有较为重要的意义,因此齿轮的模数应选得小些;变速器低档齿轮应选用大些的模数,其他挡位选用另一种模数。少数情况下,汽车变速器各挡齿轮均选用相同的模数,变速器用齿轮法向模数的范围如表3.1。表3.1 汽车变速器齿轮的法向模数车型乘用车的发动机排量V/L货车的最大总质量/t1.0V1.61.6V2.56.014.014.0模数/mm2.252.752.753.003.504.504.506.00所选模数值应符合国家标准GB/T13571987的规定。故本设计选取模数为:常啮齿轮Mn=5,一档Mn=4,二档Mn=5,三档Mn=5,五档Mn=5,倒挡Mn=4。3.2.2 压力角齿轮压力角较小时,重合度较大并降低了轮齿刚度,为此能减少进入啮合和退出啮合时的动载荷,使传动平稳,有利于降低噪声;压力角较大时,可提高轮齿的抗弯强度和表面接触强度。试验证明:对于直齿轮,压力角为28时强度最高,但是超过28强度增加不多;对于斜齿轮,压力角为25时强度最高。因此,理论上对于乘用车,为加大重合度以降低噪声应取用14.5、15、16、16.5等小些的压力角;对商用车,为提高齿轮承载能力应选用22.5或25等大些的压力角。3.2.3 螺旋角斜齿轮在变速器中得到广泛应用。选取斜齿轮的螺旋角,应注意它对齿轮工作噪声、轮齿的强度和轴向力有影响。在齿轮选用大些的螺旋角时,使齿轮啮合的重合度增加,因而工作平稳、噪声降低。试验还证明:随着螺旋角的增大,齿的强度也相应提高。不过当螺旋角大于30时,其抗弯强度骤然下降,而接触强度仍继续上升。因此,从提高低档齿轮的抗弯强度出发,并不希望用过大的螺旋角,以1525为宜;而从提高高档齿轮的接触强度和增加重合度着眼,应选用较大的螺旋角。斜齿轮螺旋角可在下面提供的范围内选用:两轴式变速器为2025中间轴式变速器为2234货车变速器:18263.2.4 齿宽在选择齿宽时,应该注意齿宽对变速器的轴向尺寸、质量、齿轮工作平稳性、齿轮强度和齿轮工作时的受力均匀程度等均有影响。通常是根据齿轮模数来确定的。直齿 为齿宽系数, 取=4.58.0斜齿 为齿宽系数, 取=6.08.5b为齿宽(mm)。采用啮合套或同步器换挡时,其接合齿的工作宽度初选时可取为24 mm。第一轴常啮合齿轮副的齿宽系数可取大些,使接触线长度增加,接触应力降低,以提高传动平稳性和齿轮寿命。对于模数相同的各挡齿轮,挡位低的齿轮的齿宽系数取得稍大。齿宽的选择既要考虑变速器的质量小,轴向尺寸紧凑,又要保证轮齿的强度及工作平稳性要求。3.2.5 齿顶高系数齿顶高系数对重合度、轮齿强度、工作噪声、轮齿相对滑动速度、轮齿根切和齿顶厚度等有影响。若齿顶高系数小,则齿轮重合度小、工作噪声大;但因轮齿受到的弯矩减少,轮齿的弯曲应力也减少。因此,从前因齿轮加工精度不高,并认为轮齿上受到的载荷集中作用到齿顶上,所以曾采用过齿顶高系数为0.750.80的短齿制齿轮。在齿轮加工精度提高以后,短齿制齿轮不再被采用,包括我国在内,规定齿顶高系数为1.00。3.2.6 各档传动比及其齿轮齿数的确定在初选中心距、齿轮模数和螺旋角以后,可根据变速器的档数、传动比和传动方案来分配各档齿轮的齿数。应该注意的是,各档相互啮合的齿轮的齿数最好为质数,以使齿面磨损均匀。如图3.1是本次设计的变速器的传动方案。1、确定一档齿轮齿数一档的传动比为: = (3.5)又因为,所以,所以,为了使/尽量大些,应将取得尽量小些,这样,在已定的条件下,/的传动比可小些,以使第一轴常啮合齿轮可分配到较多的齿数,以便在其内腔设置第二轴的前轴承,的最少齿数受到中间轴轴颈的限制,因此,的选定应与中间轴轴颈的确定因素统一考虑。为避免发生根切,增强刚度,一档小齿轮应为变位齿轮。商用车中间轴式变速器的=3.86时,则在1518内选择。取=18。则图3.1中间轴式变速器传动方案2、修正中心矩A因为 A=m(z9+z10)/2所以 A=m(z9+z10)/2=3(18+59)/2=154mm初定中心矩应为: =154mm 3、确定常啮合齿轮副的齿数由式 = 求得常啮合传动齿轮的传动比: (3.6)而常啮合齿轮中心距与一档齿轮的中心距相等, = (3.7) 初选=解联立式(3.6)和式(3.7)得:=19.98,= 34.56取整后:= 20,=35所以,一档实际传动比为=5.74,与原传动比相差不大,符合要求。螺旋角=arcos=4、确定其他各档位的齿数二档齿轮:二档齿轮是斜齿轮,螺旋角与常啮合齿轮的不同时,由 = (3.8) = (3.9)初选=解联立式(3.8)和式(3.9)得:=38.1,= 21.3取整后:= 38,=21所以,二档实际传动比为=3.16,与原传动比相差不大,符合要求。螺旋角=arcos=从抵消或减少中间轴上的轴向力出发,必须满足下列关系式: (3.10)把 ,及 分别代入式(3.10)的左右两边:=1.21=1.7方程左右两边近似满足轴向力平衡关系,所以符合条件。三档齿轮:三档齿轮是斜齿轮,螺旋角与常啮合齿轮的不同时,由 = (3.11) = (3.12)初选=解联立式(3.11)和式(3.12)得:=29.93,= 28.7取整后:= 29,=29所以,三档实际传动比为=1.75,与原传动比相差不大,符合要求。螺旋角=arcos=从抵消或减少中间轴上的轴向力出发,必须满足下列关系式: (3.13)把 ,及 分别代入式(3.13)的左右两边:=1.21=1.27方程左右两边近似满足轴向力平衡关系,所以符合条件。四档齿轮,即为常啮齿轮五档齿轮是斜齿轮,螺旋角与常啮合齿轮的不同时,由 = (3.14) = (3.15)初选=解联立式(3.14)和式(3.15)得:=16.7,= 38.3取整后:= 16,=37所以,四档实际传动比为=0.76,与原传动比相差不大,符合要求。螺旋角=arcos=从抵消或减少中间轴上的轴向力出发,必须满足下列关系式: (3.16)把 ,及 分别代入式(3.16)的左右两边:=1.21=0.91方程左右两边近似满足轴向力平衡关系,所以符合条件。通常倒档采用直齿轮,模数=4mm。倒档传动比与一档传动比比较接近,因为=5.7,取=5.2。中间轴倒档传动齿轮的齿数比一档主动齿轮10相近,取=18,倒档轴齿轮13的齿数取,取=21。 由 = (3.17)所以=53.4,取整后=53。由此,中间轴与倒档轴之间的中心距: (3.21)倒档轴与输出轴之间的中心距: (3.22)3.2.7 变速器齿轮的几何尺寸计算表3.3直齿圆柱齿轮的几何尺寸计算序号计算项目计算公式(高度变位齿轮)1变位系数2分度圆直径3齿顶高4齿根高5齿全高6齿顶圆直径7齿根圆直径8中心距9周节10基节11分度圆弧齿厚12基圆直径表3.4直齿圆柱齿轮的几何尺寸齿数5318351859中心矩=106mm =176mm变位系数00000分度圆直径212mm72mm140mm72mm236mm齿顶高4mm4mm4mm4mm4mm齿根高5mm5mm5mm5mm5mm齿全高9mm9mm9mm9mm9mm齿顶圆直径220mm80mm148mm80mm244mm齿根圆直径199.21mm62mm130mm62mm226mm周节12.56mm12.56mm12.56mm12.56mm12.56mm基节11.79mm11.79mm11.79mm11.79mm11.79mm分度圆弧齿厚6.28mm6.28mm6.28mm6.28mm6.28mm基圆直径202mm67.6mm131.56mm67.6mm221.77mm表3.5斜齿圆柱齿轮的几何尺寸计算 序号计算项目计算公式(高度变位齿轮)1理论中心距2分度圆直径3齿顶高4齿根高5齿全高6齿顶圆直径7齿根圆直径8法向基节9基圆直径10法面分度圆弧齿厚表3.6斜齿圆柱齿轮的几何尺寸齿数2035163729293821理论中心距155mm155mm155mm155mm端面啮合角22.1722.9321.1320.80中心距154mm154mm154mm154mm变位系数00000000分度圆直径112mm196mm92.98mm215mm154mm154mm198.4mm109.63mm齿顶高5mm5mm5mm5m5mm5mm5mm5mm齿根高6.25mm6.25mm6.25mm6.25mm6.25mm6.25mm6.25mm6.25mm齿全高11.25mm11.25mm11.25mm11.25mm11.25mm11.25mm11.25mm11.25mm齿顶圆直径122mm206mm102.98mm225mm164mm164mm208.4mm119.63mm齿根圆直径99.5mm183.5mm80.48mm202.5mm141.5mm141.5mm182.87mm97.13mm3.3 本章小结本章主要介绍了变速器主要参数的选择,包括确定档数、传动比范围,根据最大爬坡度和驱动轮与地面的附着力确定一档传动比,进而确定其它各档传动比,选择中心距以及齿轮参数,根据变速器的传动示意图确定各档齿轮齿数,进行各档齿轮变位系数的分配。最后列出了各档齿轮的几何尺寸。为以后齿轮、轴的设计计算做了准备。第四章 变速器主要结构元件的设计与计算4.1 齿轮损坏的原因及形式变速器齿轮的损坏形式主要有:轮齿折断、齿面疲劳剥落(点蚀)、齿面胶合以及移动换档齿轮端部破坏。齿轮在啮合过程中,轮齿根部产生弯曲应力,过渡圆角处又有应力集中,故当齿轮受到足够大的载荷作用,其根部的弯曲应力超过材料的许用应力时,轮齿就会断裂。这种由于强度不够而产生的断裂,其断面为一次性断裂所呈现的粗粒状表面。在汽车变速器中这种破坏情况很少发生。而常见的断裂是由于在重复载荷作用下使齿根受拉面的最大应力区出现疲劳裂缝而逐渐扩展到一定深度后产生的折断,其破坏断面在疲劳裂缝部分呈光滑表面,而突然断裂部分呈粗粒状表面。变速器低档小齿轮由于载荷大而齿数少、齿根较弱,其主要的破坏形式就是这种弯曲疲劳断裂。齿面点蚀是常用的高档齿轮齿面接触疲劳的破坏形式。齿面长期在脉动的接触应力作用下,会逐渐产生大量与齿面成尖角的小裂缝。啮合时由于齿面的相互挤压,使充满了润滑油的裂缝处油压增高,导致裂缝的扩展,最后产生剥落,使齿面上形成大量的扇形小麻点,即所谓点蚀。点蚀使齿形误差加大而产生载荷,甚至可能引起轮齿折断。通常是靠近节圆根部齿面处的点蚀较靠近节圆顶部齿面处的点蚀严重;主动小齿轮较被动大齿轮严重。对于高速重载齿轮,由于齿面相对滑动速度高、接触压力大且接触区产生高温而使齿面间的润滑油膜破坏,使齿面直接接触。在局部高温、高压下齿面互相熔焊粘连,齿面沿滑动方向形成撕伤痕迹的损坏形式称为齿面胶合。在一般的汽车变速器中,产生胶合损坏的情况较少。增大轮齿根部齿厚,加大齿根圆角半径,采用高齿,提高重合度,增多同时啮合的轮齿对数,提高轮齿柔度,采用优质材料等,都是提高轮齿弯曲强度的措施。合理选择齿轮参数及变位系数,增大齿廓曲率半径,降低接触应力,提高齿面硬度等,可提高齿面的接触强度。采用黏度大、耐高温、耐高压的润滑油,提高油膜强度,选择适当的齿面表面处理和镀层等,是防止齿面胶合的措施。4.2轮齿强度计算与其它机械设备用变速器比较,不同用途汽车的变速器齿轮使用条件相似,此外,汽车变速器齿轮用的材料,热处理的方法,加工的方法,精度级别,支承方式也基本一致。因此,比用计算通用齿轮强度公式更为简化一些的计算公式来计算汽车齿轮,同样可以获得较为准确的结果3。 4.2.1 轮齿弯曲强度计算直齿轮弯曲应力 = (4.1) 式中,弯曲应力(M);计算载荷(Nmm);应力集中系数;=1.65;摩擦力影响系数,主、从动齿轮在啮合上的摩擦力的方向不同,对弯曲应力影响也不同:主动齿轮=1.1,从动齿轮=0.9;m模数;y齿形系数,如图4.1所示;齿宽系数:直齿=4.58.0。斜齿轮弯曲应力 = (4.2) 式中, 计算载荷(Nmm);斜齿轮螺旋角();应力集中系数;=1.50;z 齿数;法面模数;y齿形系数,可按当量齿数=在图4.1中查得;重合度影响系数,=2.0; 齿宽系数:斜齿=6.08.5,取=7。图4.1齿形系数图当计算载荷取作用到变速器第一轴上的最大转矩时,对商用车常啮合齿轮和高档齿轮,许用应力在180350M范围,即=180350M,一档、倒档直齿轮许用应力在400850 M,即=400850M3。1、一档主从动齿轮弯曲应力一档主动齿轮弯曲应力=627.19 M一档从动齿轮弯曲应力=178.92M2、二档主从动齿轮弯曲应力二档主动齿轮弯曲应力=104.41M二档从动齿轮弯曲应力=60.34 M3、 三档主从动齿轮弯曲应力三档主动齿轮弯曲应力 =79.58 M三档从动齿轮弯曲应力=79.58 M4、四档主从动齿轮弯曲应力四档主动齿轮弯曲应力=65.94 M四档从动齿轮弯曲应力=116.94 M5、五档主从动齿轮弯曲应力五档主动齿轮弯曲应力=59.87 M五档从动齿轮弯曲应力=129.09 M6、倒档主从动齿轮弯曲应力倒档主动齿轮弯曲应力=842.3 M倒档从动齿轮弯曲应力=401.01 M=240.98 M4.2.2 轮齿接触应力计算轮齿接触应力 =0.418 (4.3)式中,轮齿的接触应力(M);F齿面上的法向力(N),F=;圆周力,=;计算载荷(Nmm);d 节圆直径(mm);节点处压力角();齿轮螺旋角();E齿轮材料的弹性模量(M),钢材E=2.110M;b齿轮接触的实际宽度(mm);、为主、从动齿轮节点处的曲率半径(mm),直齿轮=,=,斜齿轮=,=;、为主、从动齿轮节圆半径(mm)。将作用在变速器第一轴上的载荷作为计算载荷时,变速器齿轮的许用接触应力如下:渗碳齿轮:一挡和倒挡=19002000M,常啮合齿轮和高档=13001400M。一档主从动齿轮接触应力一档主动齿轮接触应力=0.418= 0.418=354.73 M一档从动齿轮接触应力=0.418= 0.418=195.92 M二档主从动齿轮接触应力二档主动齿轮接触应力 =0.418 = 0.418 =273.39M二档从动齿轮接触应力 =0.418 = 0.418 =203.39 M三档主从动齿轮接触应力三档主动齿轮接触应力 =0.418 = 0.418 =221.38 M三档从动齿轮接触应力 =0.418 = 0.418 =221.38 M四档主从动齿轮接触应力四档主动齿轮接触应力 =0.418 = 0.418 =237.42 M四档从动齿轮接触应力 =0.418 = 0.418 =314.08 M五档主从动齿轮接触应力五档主动齿轮接触应力 =0.418 = 0.418 =203.88 M五档从动齿轮接触应力 =0.418 = 0.418 =310.08 M倒档主从动齿轮接触应力倒档主动齿轮接触应力 =0.418 = 0.418 =382.46M倒档从动齿轮接触应力 =0.418 = 0.418 =274.26 M =0.418 = 0.418 =222.88 M4.3 变速器齿轮材料的选择及热处理现代汽车变速器齿轮大都采用渗碳合金钢制造,使轮齿表层的高硬度与轮齿心部的高韧性相结合,以大大提高其接触强度、弯曲强度及耐磨性。在选择齿轮的材料及热处理时也应考虑到其机械加工性能及制造成本。国产汽车变速器齿轮的常用材料是20CrMnTi(过去的钢号是18CrMnTi),也有采用20Mn2TiB,20MnVB,20MnMOB的。这些低碳合金钢都需随后的渗碳、淬火处理,以提高表面硬度,细化材料晶面粒。为消除内应力还要进行回火。变速器齿轮轮齿表面渗碳深度的推荐范围如下:3.5,渗碳深度0.81.2mm;3.55,渗碳深度0.91.3mm;5,渗碳深度1.01.6mm。渗碳齿轮在淬火、回火后,要求轮齿的表面硬度为HRC5863,心部硬度为HRC3348。 对于本设计中的齿轮材料,选用20CrMnTi。4.4 轴的设计计算变速器在工作时,由于齿轮上有圆周力、径向力和轴向力作用,变速器的轴要承受转矩和弯矩。要求变速器的轴应有足够的刚度和强度。因为刚度不足轴会产生弯曲变形,结果破坏了齿轮的正确啮合,对齿轮的强度、耐磨性和工作噪声等均有不利影响。因此,在设计变速器轴时,其刚度大小应以保证齿轮能有正确的啮合为前提条件。设计阶段可根据经验和已知条件先初选轴的直径,然后根据公式进行有关刚度和强度方面的验算。4.4.1 初选轴的直径轴的径向及轴向尺寸对其刚度影响很大,且轴长与轴径应协调,变速器轴的最大直径与支承间的距离可按下列关系式初选:对第一轴及中间轴: = 0.160.18, (4.4)对输二轴: = 0.180.21 (4.5)中间轴式变速器第二轴与中间轴的最大直径d可根据中心距A(mm)按下式初选: d(0.450.60)A (4.6)第一轴花键部分直径可根据发动机最大转矩按下式初选 d(44.6) (4.7)初选的轴径还需根据变速器的结构布置和轴承与花键,弹性档圈等标准以及轴的刚度与强度验算结果进行修正2。经过计算得:第一轴花键部分直径: d=42mm中间轴的最大直径: =66mm支承间的距离: =420mm第二轴的的最大直径: =67.5mm支承间的距离: =380mm4.4.2 轴的刚度计算对齿轮工作影响最大的是轴在垂直面内产生的挠度和轴在水平面内的转角。前者使齿轮中心距发生变化,破坏了齿轮的正确啮合;后者使齿轮相互歪斜,如图4.2所示,致使沿齿长方向的压力分布不均匀。 (a)轴在垂直面内的变形 (b)轴在水平面内的变形图4.2变速器轴的变形示意简图轴的挠度和转角可按材料力学的有关公式计算。计算时,仅计算齿轮所在位置处轴的挠度和转角。第一轴常啮合齿轮副,因距离支承点近,负荷又小,通常挠度不大,故可以不必计算。变速器齿轮在轴上的位置如图4.3所示时,若轴在垂直面内挠度为,在水平面内挠度为和转角为,可分别用下式计算 (4.8) (4.9) (4.10)式中,齿轮齿宽中间平面上的径向力(N);为齿轮齿宽中间平面上的圆周力(N);弹性模量(MPa),=2.1105 MPa;惯性矩(mm4),对于实心轴,;轴的直径(mm),花键处按平均直径计算;、为齿轮上的作用力距支座、的距离(mm);支座间的距离(mm)。图4.3变速器轴的挠度和转角轴的全挠度为 mm (4.11)轴在垂直面和水平面内挠度的允许值为=0.050.10mm,=0.100.15mm。齿轮所在平面的转角不应超过0.002rad3。1、第一轴的刚度=12500N=5164.6 N变速器工作时,=0.014mm=0.034mm=0.037mm=0.0002rad2、中间轴的刚度(1)一档工作时的刚度计算用的齿轮啮合的圆周力,径向力及轴向力,可按下式求出:=53240.5N=19377N=22599N一档工作时,=0.056mm=0.15mm=0.15mm=0.0001rad(2)二档工作时的刚度计算用的齿轮啮合的圆周力,径向力,可按下式求出:=40353N=15956N二档工作时,=0.072mm=0.182mm=0.19mm=0.0002rad(3)三档工作时的刚度计算用的齿轮啮合的圆周力,径向力,可按下式求出:=15909N=6290N三档工作时,=0.047mm=0.12mm=0.12mm=0.0002rad(4)五档工作时的刚度计算用的齿轮啮合的圆周力,径向力,可按下式求出:=5428.5N=2431N四档工作时,=0.008mm=0.02mm=0.022mm=0.0002rad(5)倒档工作时的刚度计算用的齿轮啮合的圆周力,径向力,可按下式求出:=51302N=18672N倒档工作时,=0.019mm=0.053mm=0.056mm=0.003rad3、第二轴的刚度(1)一档工作时的刚度计算用的齿轮啮合的圆周力,径向力及轴向力,可按下式求出:=33813N=13369N=14352N一档工作时,=0.032mm=0.082 mm=0.088mm=0.0001rad(2)二档工作时的刚度计算用的齿轮啮合的圆周力,径向力,可按下式求出:=22298N=8817N二档工作时,=0.026mm=0.067mm=0.072mm=0.00002rad(3)三档工作时的刚度计算用的齿轮啮合的圆周力,径向力,可按下式求出:=15909N=6290N三档工作时,=0.018mm=0.040mm=0.044mm=0.0005rad(4)五档工作时的刚度计算用的齿轮啮合的圆周力,径向力,可按下式求出:=11292N=4465N四档工作时,=0.044mm=0.11mm=0.118mm=0.0002rad(5)倒档工作时的刚度计算用的齿轮啮合的圆周力,径向力,可按下式求出:=51302N=8672N倒档工作时,=0.006mm=0.036mm=0.036mm=0.0009rad4.4.3 轴的强度计算作用在齿轮上的径向力和轴向力,使轴在垂直面内弯曲变形,而圆周力使轴在水平面内弯曲变形。在求取支点的水平垂直面内的支反力之后,计算相应的弯矩、。轴在转矩和弯矩的同时作用下,其应力为 = (4.12)式中 M合成弯矩,(Nmm);d轴的直径(mm),花键处取内径;W抗弯截面系数(mm)。在低档工作时,500MPa。除此之外,对轴上的花键,应验算齿面的挤压应力。变速器的轴用与齿轮相同的材料制造2。1、第一轴强度校核第一轴常啮合齿轮副,因距离支撑点近,负荷又小,通常扰度不大,可以不必计算。 2、中间轴强度校核中间轴一档工作时强度校核:=53240N,=19377N, =22599N,求H面内支反力、和弯矩输出轴受力如图4.6(a)所示,则 += (4.19) = (4.20)由式(4.19)和式(4.20)可得:=17174N,=36065N,=1916.6Nm求V面内支反力、和弯矩输出轴受力如图4.6(b)所示,则 += (4.21) =+ (4.22)由式(4.21)和式(4.22)可得:=8166N,=11211N,=12130Nm=12300Nm=435 (a)中间轴水平方向受力图 (b)中间轴垂直方向受力图图4.6中间轴受力图弯矩图如图4.7所示: (a)中间轴水平弯矩图 (b)中间轴垂直弯矩图图4.7中间轴弯矩图2、第二轴强度校核第二轴一档工作时强度校核:=33813N,=13369N, =14352N,求H面内支反力、和弯矩输出轴受力如图4.8(a)所示,则 += (4.23) = (4.24)由式(4.23)和式(4.24)可得:=11579N,=22233N,=1075.6Nm求V面内支反力、和弯矩输出轴受力如图4.8(b)所示,则 += (4.25) =+ (4.26)由式(4.25)和式(4.26)可得:=9031N,=4338N,=715.6Nm=1469Nm=31.53 (a)第二轴水平方向受力图 (b)第二轴垂直方向受力图图4.8第二轴受力图弯矩图如图4.8所示。 (a)第二轴水平弯矩图 (b)第二轴垂直弯矩图图4.9第二轴弯矩图4.5 本章小结本章介绍了齿轮的损坏原因及形式,简要阐述了齿轮材料的热处理方法,重点对各档齿轮进行了校核,包括对各挡齿轮弯曲应力、接触应力的计算。计算了轴在垂直面内产生的挠度和轴在水平面内的转角以及轴在合成弯矩作用下的应力。第五章 同步器的选择同步器有常压式、惯性式和惯性增力式三种。常压式同步器结构虽然简单,但有不能保证啮合件在同步状态下(即角速度相等)换挡的缺点,现已不用。得到广泛应用的是惯性式同步器。5.1 惯性式同步器惯性式同步器能做到换挡时,在两换挡元件之间的角速度达到完全相等之前不允许换挡,因而能很好地完成同步器的功能和实现对同步器的基本要求。按结构分,惯性式同步器有锁销式、滑块式、锁环式、多片式和多锥式几种。虽然它们结构不同,但是它们都有摩擦元件、锁止元件和弹性元件。5.1.1 锁环式同步器的结构如图5.1所示,锁环示同步器的结构特点是同步器的摩擦元件位于锁环1或4和齿轮5或8凸肩部分的锥形斜面上。作为锁止元件是在锁环1或4上的齿和做在啮合套7上的齿的端部,且端部均为斜面称为锁止面。弹性元件是位于啮合套座两侧的弹簧圈。弹簧圈将置于啮合套座花键上中部呈凸起状的滑快压向啮合套。在不换挡的中间位置,滑快凸起部分嵌入啮合套中部的内环槽中,使同步器用来换挡的零件保持在中立位置上。滑快两端伸入锁环缺口内,而缺口的尺寸要比滑快宽一个接合齿。图5.1锁环式同步器1、4-锁环;2-滑块;3-弹簧圈;5、8-齿轮;6-啮合套座;7-啮合套5.1.2 锁环式同步器的工作原理换档时,沿轴向作用在啮合套上的换档力,推啮合套并带动滑快和锁环移动,直至锁环锥面与被接合齿轮上的锥面接触为止。之后,因作用在锥面上的法向力与两锥面之间存在角速度差,致使在锥面上有摩擦力矩,它使锁环相对啮合套和滑块转过一个角度,并由滑快予以定位。接下来,啮合套的齿端与锁环齿端的锁止面接触,使啮合套的移动受阻,同步器处在锁止状态,换档的第一阶段工作至此已完成。换档哪个力将锁环继续压靠在锥面上,并使摩擦力矩增大,与此同时在锁止面处作用有与之方向相反的拨环力矩。齿轮与锁环的角速度逐渐接近,在角速度相等的瞬间,同步过程结束,完成了换档过程的第二阶段工作。之后,摩擦力矩随之消失,而拨环力矩使锁环回位,两锁止面分开,同步器解除锁止状态,啮合套上的接合齿在换档力的作用下通过锁环去与齿轮上的接合齿啮合,完成换档。锁环式同步器有工作可靠、零件耐用等优点,但因结构布置上的限制,转矩容量不大,而且由于锁止面在锁环的接合齿上,会因齿端磨损而失效,因而主要用于乘用车和总质量不大的货车变速器中。5.1.3 锁环式同步器主要尺寸的确定接近尺寸,同步器换挡第一阶段中间,在滑块侧面压在锁环缺口侧边的同时,且啮合套相对滑块作轴向移动前,啮合套接合齿与锁环接合齿倒角之间的轴向距离,称为接近尺寸。尺寸应大于零,取=0.20.3mm。分度尺寸,滑块侧面与锁环缺口侧边接触时,啮合套接合齿与锁环接合齿中心线间的距离,称为分度尺寸。尺寸应等于1/4接合齿齿距。尺寸和是保证同步器处于正确啮合锁止位置的重要尺寸,应予以控制。滑块转动距离,滑块在锁环缺口内的转动距离影响分度尺寸。滑块宽度、滑块转动距离与缺口宽度尺寸之间的关系如下 (5.1)滑块转动距离与接合齿齿距的关系如下 (5.2)式中 滑块轴向移动后的外半径(即锁环缺口外半径);接合齿分度圆半径。滑块端隙,滑块端隙系指滑块端面与锁环缺口端面之间的间隙,同时,啮合套端面与锁环端面之间的间隙为,要求。若,则换挡时,在摩擦锥面尚未接触时,啮合套接合齿与锁环接合齿的锁止面已位于接触位置,即接近尺寸0,此刻因锁环浮动,摩擦面处无摩擦力矩作用,致使啮合套可以通过同步环,而使同步器失去锁止作用。为保证0,应使,通常取=0.5mm左右。锁环端面与齿轮接合齿端面应留有间隙,并可称之为后备行程。预留后备行程的原因是锁环的摩擦锥面会因摩擦而磨损,并在下来的换挡时,锁环要向齿轮方向增加少量移动。随着磨损的增加,这种移动量也逐渐增多,导致间隙逐渐减少,直至为零;此后,两摩擦锥面间会在这种状态下出现间隙和失去摩擦力矩。而此刻,若锁环上的摩擦锥面还未达到许用磨损的范围,同步器也会因失去摩擦力矩而不能实现锁环等零件与齿轮同步后换挡,故属于因设计不当而影响同步器寿命。一般应去=1.22.0mm。在空挡位置,锁环锥面的轴向间隙应保持在0.20.5mm。5.2 主要参数的确定5.2.1 摩擦因数f 汽车在行驶过程中换档,特别是在高档区换档次数较多,意味着同步器工作频繁。同步器是在同步环与连接齿轮之间存在角速度差的条件下工作,要求同步环有足够的使用寿命,应当选用耐磨性能良好的材料。为了获得较大的摩擦力矩,又要求用摩擦因数大而且性能稳定的材料制作同步环。另一方面,同步器在油中工作,使摩擦因数减小,这就为设计工作带来困难。摩擦因数除与选用的材料有关外,还与工作面的表面粗糙度、润滑油种类和温度等因数有关。作为与同步环锥面接触的齿轮上的锥面部分与齿轮做成一体,用低碳合金钢制成。对锥面的表面粗糙度要求较高,用来保证在使用过程中摩擦因数变化小。若锥面的表面粗糙度值大,则在使用初期容易损害同步环锥面。同步环常选用能保证具有足够高的强度和硬度、耐磨性能良好的黄铜合金制造,如锰黄铜、铝黄铜和锡黄铜等。早期用青铜合金制造的同步环,因使用寿命短已遭淘汰。由黄铜合金与钢材构成的摩擦副,在油中工作的摩擦因数f取为0.1。摩擦因数对换挡齿轮和轴的角速度能迅速达到相同有重要作用。摩擦因数大,则换挡省力或缩短同步时间;摩擦因数小则反之,甚至失去同步作用。为此,在同步环锥面处制有破坏油膜的细牙螺纹槽及与螺纹槽垂直的泄油槽,用来保证摩擦面之间有足够的摩擦因数。5.2.2 同步环主要尺寸的确定1、同步环锥面上的螺纹槽如果螺纹槽螺线的顶部设计得窄些,则刮去存在于摩擦锥面之间的油膜效果好。但顶部宽度过窄会影响接触面压强,使磨损加快。实验还证明:螺纹的齿顶宽对的影响很大,随齿顶的磨损而降低,换挡费力,故齿顶宽不易过大。螺纹槽设计得大些,可使被刮下来的油存在于螺纹之间的间隙中,但螺距增大又会使接触面减少,增加磨损速度。通常轴向泄油槽为612个,槽宽34mm。2、锥面半锥角摩擦锥面半锥角越小,摩擦力矩越大。但过小则摩擦锥面将产生自锁现象,避免自锁的条件是。一般取=68。=6时,摩擦力矩较大,但在锥面的表面粗糙度控制不严时,则有粘着和咬住的倾向;在=7时就很少出现咬住现象。3、摩擦锥面平均半径设计得越大,则摩擦力矩越大。往往受结构限制,包括变速器中心距及相关零件的尺寸和布置的限制,以及取大以后还会影响同步器径向厚度尺寸要取小的约束,故不能取大。原则上是在可能的条件下,尽可能将取大些。4、锥面工作长度b缩短锥面长度,可使变速器的轴向长度缩短,但同时也减小了锥面的工作面积,增加了单位压力并使磨损加速。设计时可根据下式计算确定 (5.3)式中 摩擦面的许用压力,对黄铜与钢的摩擦副,=1.01.5MPa;Mm摩擦力矩;摩擦因数;摩擦锥面的平均半径。上式中面积是假定在没有螺纹槽的条件下进行计算的。 5、同步环径向厚度与摩擦锥面平均半径一样,同步环的径向厚度受结构布置上的限制,包括变速器中心距及相关零件特别是锥面平均半径和布置上的限制,不易取得很厚,但必须保证同步环有足够的强度。乘用车同步环厚度比货车小些,应选用锻件或精密锻造工艺加工制成,这能提高材料的屈服强度和疲劳寿命。锻造时选用锰黄铜等材料。有的变速器用高强度、高耐磨性的钢与钼配合的摩擦副,即在钢质或球墨铸铁同步环的锥面上喷镀一层钼(厚约0.30.5),
- 温馨提示:
1: 本站所有资源如无特殊说明,都需要本地电脑安装OFFICE2007和PDF阅读器。图纸软件为CAD,CAXA,PROE,UG,SolidWorks等.压缩文件请下载最新的WinRAR软件解压。
2: 本站的文档不包含任何第三方提供的附件图纸等,如果需要附件,请联系上传者。文件的所有权益归上传用户所有。
3.本站RAR压缩包中若带图纸,网页内容里面会有图纸预览,若没有图纸预览就没有图纸。
4. 未经权益所有人同意不得将文件中的内容挪作商业或盈利用途。
5. 人人文库网仅提供信息存储空间,仅对用户上传内容的表现方式做保护处理,对用户上传分享的文档内容本身不做任何修改或编辑,并不能对任何下载内容负责。
6. 下载文件中如有侵权或不适当内容,请与我们联系,我们立即纠正。
7. 本站不保证下载资源的准确性、安全性和完整性, 同时也不承担用户因使用这些下载资源对自己和他人造成任何形式的伤害或损失。

人人文库网所有资源均是用户自行上传分享,仅供网友学习交流,未经上传用户书面授权,请勿作他用。