摘 要
连杆是柴油机的主要传动件之一,本文主要论述了杆的加工工艺及其夹具设计。连杆的尺寸精度、形状精度以及位置精度的要求都很高,而连杆的刚性比较差,容易产生变形,因此在安排工艺过程时,就需要把各主要表面的粗精加工工序分开。逐步减少加工余量、切削力及内应力的作用,并修正加工后的变形,就能最后达到零件的技术要求。
就我个人而言,我希望能通过这次课程设计,了解并认识一般机器零件的生产工艺过程,巩固和加深已学过的技术基础课和专业课的知识,理论联系实际,从中锻炼自己分析问题、解决问题的能力,为今后的毕业设计以及工作打下一个良好的基础。
Abstract
The connecting rod is one of the main driving medium of diesel engine, this text expounds mainly the machining technology and the design of clamping device of the connecting rod. The precision of size, the precision of profile and the precision of position , of the connecting rod is demanded highly , and the rigidity of the connecting rod is not enough, easy to deform, so arranging the craft course, need to separate the each main and superficial thick finish machining process. Reduce the function of processing the surplus , cutting force and internal stress progressively , revise the deformation after processing, can reach the specification requirement for the part finally .
To my own opinion, I hoped that can through this curriculum project, understand and know the common machine part the technique of production process, consolidated and the deepening has studied the technical basic course and the professional course knowledge, the apply theory to reality, exercises itself to analyze the question, to solve the question ability, as well as will work for present's graduation project builds a good foundation.
.
目 录
1零件的工艺分析及生产类型的确定-----------------1
1.1汽车连杆的用途-------------------------------1
1.2汽车连杆的技术要求---------------------------1
1.3汽车连杆的生产类----------------------------2
2 确定毛坯、绘制毛坯简图------------------------2
2.1选择毛坯------------------------------------2
2.2确定机械加工余量-----------------------------2
2.3确定毛坯尺寸叉工艺路线-----------------------2
2.4设计毛坯------------------------------2
3选择加工方法,确定工艺路线----------------------3
3.1定位基准的选择-------------------------------3
3.2零件表面加工方法的选择-----------------------3
3.3制定工艺路线------------------------------4
4工序设计--------------------------------5
4.1选择加工设备与工艺装备-----------------------5
4.2确定工序尺寸---------------------------------5
5确定切削用量及基本时间-------------------------5
5.1基本时间tm的计算-------------------------5
6夹具设计---------------------------------7
6.1定位方案-------------------------7
6.2夹紧机构---------------------------------7
6.3导向装置-------------------------7
6.4夹具与机床连接机构-------------------------7
6.5夹具体----------------------------7
7设计体会---------------------------------8
参考文献-------------------------9
1 零件的工艺分析及生产类型的确定
1.1 汽车连杆的用途
汽车连杆的功用是连接活塞与曲轴。连杆小头通过活塞销与活塞相连,连杆大头与曲轴的连杆轴颈相连。并把活塞承受的气体压力传给曲轴,使活塞的往复运动转变成曲轴的旋转运动。
连杆工作时,承受活塞顶部气体压力和惯性力的作用,而这些力的大小和方向都是周期性变化的。因此,连杆受到的是压缩、拉伸和弯曲等交变载荷。这就要求连杆强度高,刚度大,重量轻。连杆一般都采用中碳钢或合金钢经模锻或辊锻而成,然后经机加工和热处理,连杆分为三个部分:即连杆小头,连杆杆身和连杆大头(包括连杆盖)。连杆小头与活塞销相连。
1.2 汽车连杆的技术要求
按表形式将该连杆的全部技术要求列表中
连杆技术要求表
加工表面 尺寸及偏差/mm 公差及精度等级 表面粗糙度Ra/μm 形位公差/mm
连杆大端上下端面 38-0.170 -0.233 IT7 0.8
连杆小端上下端面 38-0.05 -0.30 IT10 6.3
连杆小端孔 ?28+0.007 -0.003 IT8 0.5 ⊥ 0.00125
∥ 100:0.04 A
∥ 100:0.06 A
连杆大端孔 ?65.5+0.019 0 IT8 0.5
(1)两端面:大头两端面的尺寸公差等级为IT7,表面粗糙度Ra不大于0.8μm 需精铣。小头两端面的尺寸公差等级为IT10,表面粗糙度Ra不大于6.3μm。
(2)小头孔:公差等级为IT8,表面粗糙度Ra应不大于0.5μm。 。
(3)Φ12.2H8螺栓孔:公差等级为IT12,表面粗糙度为Ra6.3,。
(4)大头孔Φ65.5:公差等级为IT5,表面粗糙度Ra 为0.5μm。
1.3 确定连杆的生产类型
依设计题目知:N=4000件/年,该连杆的生产类型为中批量生产。
2 确定毛坯、绘制毛坯简图
2.1 选择毛坯
该零件材料为55号钢,零件结构比较简单,生产类型为中批生产,为使零件有较好的力学性能,保证零件工作可靠,故采用模锻成形。这从提高生产效率保证加工精度上考虑也是应该的。
2.2 确定机械加工余量
根据锻件质量、零件表面粗糙度、形状复杂系数查表得,单边余量在厚度方向为1.5-2.0mm,水平方向亦为1.5-2.0mm。锻件孔的单面余量查表得2.0mm.
2.3 确定毛坯尺寸
毛坯尺寸只需将零件的尺寸加上所查得的余量值即可。
2.4 设计毛坯
(1)确定圆角半径
查表得:
外圆角半径 r=2.5mm
内圆角半径 R=8mm
(2)确定模锻斜度
查表得:
模锻斜度为:5°~10°。
(3)确定分模位置
选择在主视图中连杆上端面为分模面,分模线为直线,属平直分模线。
(4)确定毛坯的热处理方式
钢质毛坯经锻造后应安排正火,以消除残余的锻造应力,并使不均匀的金相组织通过重新结晶而得到细化、均匀的组织,从而改善加工性。
3 选择加工方法,制定工艺路线
3.1 定位基准的选择
粗基准的选择:按有关基准的选择原则,即当零件有不加工表面时,应以这些不加工表面作粗基准;若零件有若干不加工表面时,则应以与加工表面要求相对位置精度高的不加工表面作粗基准。现以零件的端面为主要的定位粗基准。
精基准的选择:考虑要保证零件的加工精度和装夹准确方便,依据“基准重合”原则和“基准统一”原则,选择以圆柱体的Φ28小孔和端面为精基准。
3.2 零件表面加工方法的选择
根据连杆零件图上各个加工表面的尺寸精度和表面粗糙度,确定加工件表面的加工方法,如下表所示。
连杆各表面加工方案
加工表面 尺寸精度等级 表面粗糙度Ra/μm 加工方案 备注
连杆大端上下端面 IT7 0.8 粗铣—半精铣—精铣 表1-8
连杆小端上下断面 IT10 6.3 粗铣—半精铣 表1-8
连杆小端?28孔 IT8 0.5 钻—扩—铰 表1-7
连杆大端?65.5孔 IT8 0.5 粗镗—半精镗—精镗 表1-7
3.3 制定工艺路线
连杆工艺路线及设备、工艺的选用
工序号 工序名称 机床设备 刀具 量具
1 钻、扩、铰?28孔 四面组合钻床 四面组合钻床 卡尺、塞规
2 粗铣连杆大端上下面 立式铣床
X5 立式铣床 游标卡尺
3 半精铣连杆大端上下面 立式铣床
X5 立式铣床 游标卡尺
4 精铣连杆大端上下面 立式铣床
X5 立式铣床 游标卡尺
5 粗、精磨连杆大端侧定位面 平面磨床 游标卡尺
6 粗铣连杆小端上下面 立式铣床
X5 立式铣床 游标卡尺
7 半精铣连小大端上下面 立式铣床
X5 立式铣床 游标卡尺
8 粗镗、半精镗、精镗、精磨连杆大端Ф65.5mm孔 镗床
9 钻、铰连杆螺栓孔 四面组合钻床 卡尺、塞规
10 铣切连杆盖、体 切断铣床
11 精磨连杆接合面 平面磨床
12 钻小端孔旁通孔 四面组合钻床
13 去毛刺 钳工台 钳工台
14 中检 塞规、百分表、卡尺等
15 热处理 淬火机等
16 清洗 清洗机
17 终检 塞规、百分表、卡尺等
4 工序设计
4.1选择加工设备与工艺装备
镗床T2115、专用夹具、扩孔钻、内径千分尺、专用镗杆、YT15 、百分表。
4.2 确定工序尺寸
大头孔各工序尺寸及其公差(铸造出来的大头孔为55 mm)
工序名称 工序基
本余量 工序经济
精度 工序尺寸 最小极限尺寸 表面粗糙度
精镗 0.4 65.4 65.4 0.8
半精镗 1 65 65 1.6
粗镗 2 64 64 6.3
扩孔 5 60 59
5 确定切削用量及基本时间
5.1 基本时间tm的计算
5.1.1扩大头孔
选用钻床床Z3080 刀具:扩孔钻
根据《机械制造工艺设计手册》表2.4—54选取数据
扩孔钻直径D = 60 mm 切削速度V = 1.29 m/s
进给量f = 0.50 mm/r 切削深度ap =3.0 mm 走刀次数I = 1
则主轴转速n = 1000v/D=410 r/min
根据表3.1—41 按机床选取n=400 r/min
则实际切削速度V=Dn/(1000×60)=1.256 m/s

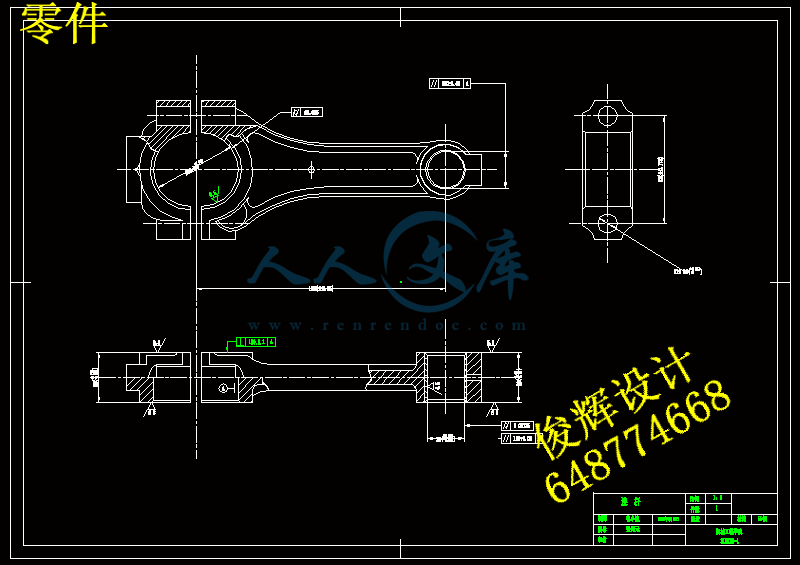
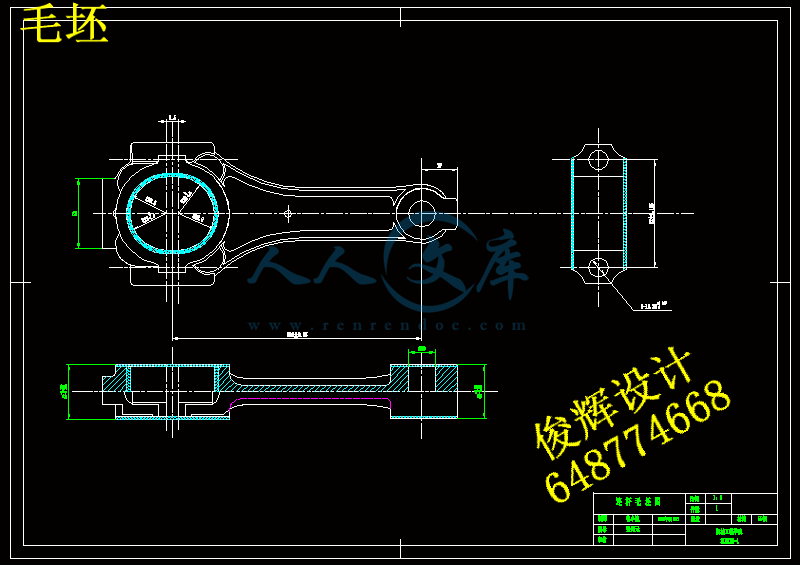
