互感器现场试验智能辅助装置机构设计【包含三维建模和仿真】
收藏
资源目录
压缩包内文档预览:
编号:1376726
类型:共享资源
大小:30.04MB
格式:RAR
上传时间:2017-07-08
上传人:机****料
认证信息
个人认证
高**(实名认证)
河南
IP属地:河南
30
积分
- 关 键 词:
-
互感器
现场
试验
实验
智能
辅助
装置
机构
设计
包含
包括
包孕
蕴含
三维
建模
以及
仿真
- 资源描述:
-













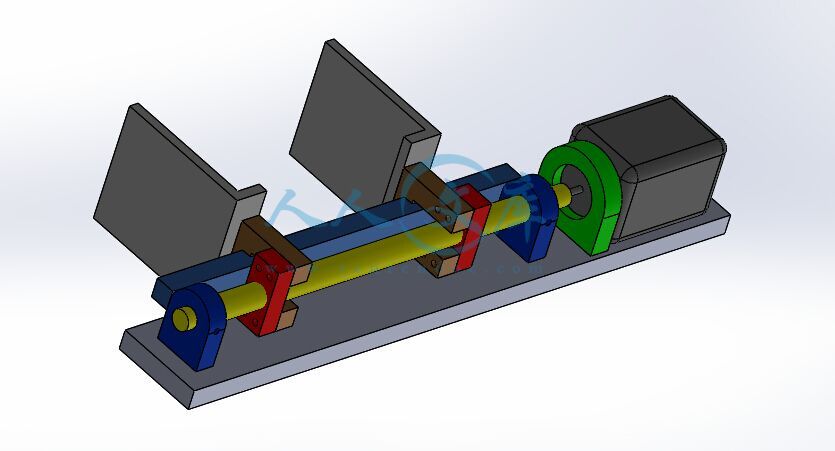
- 内容简介:
-
Optimal Mechanism Design of In-pipe Cleaning Robot Chang Doo Jung, Won Jee Chung, Jin Su Ahn, and Myung Sik Kim Gi Soo Shin, and Soon Jea Kwon Dept. of Mechanical Design and Manufacturing Engineering Deputy General Manager Robot Valley Co., Ltd Changwon National University Dept. of Mechanical Engineering Pu Kyung National University 9, Sarim-dong, Changwon, Gyeongnam Republic of Korea 125-1, Shinchon-ding, Changwon, Gyeongnam Republic of Korea Bukyong National Univ., Yongdang-dong, Nam-gu, Busan, Republic of Korea raita110, wjchungchangwon.ac.kr, lycosjinsu, and thtkajgo shings75, and sjkwonpknu.ac.kr Abstract Recently, interests on cleaning robots workable in pipes (termed as in-pipe cleaning robot) are increasing because Garbage Automatic Collection Facilities (i.e, GACF) are widely being installed in Seoul metropolitan area of Korea. So far research on in-pipe robot has been focused on inspection rather than cleaning. In GACF, when garbage is moving, we have to remove the impurities which are stuck to the inner face of the pipe (diameter: 300mm or 400mm). Thus, in this paper, by using TRIZ (Inventive Theory of Problem Solving in Russian abbreviation), we will propose an in-pipe cleaning robot of GACF with the 6-link sliding mechanism which can be adjusted to fit into the inner face of pipe using pneumatic pressure(not spring). The proposed in-pipe cleaning robot for GACF can have forward/backward movement itself as well as rotation of brush in cleaning. The robot body should have the limited size suitable for the smaller pipe with diameter of 300mm. In addition, for the pipe with diameter of 400mm, the links of robot should stretch to fit into the diameter of the pipe by using the sliding mechanism. Based on the conceptual design using TRIZ, we will set up the initial design of the robot in collaboration with a field engineer of Robot Valley, Inc. in Korea. For the optimal design of in-pipe cleaning robot, the maximum impulsive force of collision between the robot and the inner face of pipe is simulated by using RecurDyn when the link of sliding mechanism is stretched to fit into the 400mm diameter of the pipe. The stresses exerted on the 6 links of sliding mechanism by the maximum impulsive force will be simulated by using ANSYS Workbench based on the Design Of Experiment(in short DOE). Finally the optimal dimensions including thicknesses of 4 links will be decided in order to have the best safety factor as 2 in this paper as well as having the minimum mass of 4 links. It will be verified that the optimal design of 4 links has the best safety factor close to 2 as well as having the minimum mass of 4 links, compared with the initial design performed by the expert of Robot Valley, Inc. In addition, the prototype of in-pipe cleaning robot will be stated with further research. Index Terms In-pipe Cleaning Robot, 6-link Sliding Mechanism, TRIZ, Optimal Design, RecurDyn, Design Of Experiment (DOE), ANSYS Workbench I. INTRODUCTION Recently, interests on cleaning robots workable in pipes (we will call this category of robots in-pipe cleaning robot hereinafter) are increasing because Garbage Automatic Collection Facilities (i.e, GACF) are widely being installed in Seoul metropolitan area of Korea. Even though Korean GACF is in the initial stage according to survey 1 so far, residents satisfaction level was reported to be high by solving environmental problems (including the beauty of apartments) resulted from existing manual pickup way. However the GACF still has the problems such as expensive facility installation charges, high operating expenses, decline of both pickup rate of food waste and recycling rate, etc. This means that the technical skills for improving stable operation are needed for GACF. So far the way of Korean garbage pickup is as follows; when we put garbage in plastic bags and leave at a certain place, a pickup vehicle goes around that area and picks up the garbage. Usually the garbage is exposed on a road and often dogs, cats or rats, etc. can damage the garbage bag. As a result, the beauty of city can be made marred, especially in summer. Moreover the garbage bags can result in stench of flies or harmful insects. Therefore this garbage disposal system can be concluded to be unsanitary. In comparison with this inconvenient and unsanitary way of current Korean garbage disposal and pickup system, the GACF has a garbage-only slot installed at regular intervals. In GACF, pipes are constructed underground, into which make users be able to throw garbage bags. After the garbage is stored temporarily at the bottom of the slot, it is picked up at a storage area connected to the pipes. Thus GACF does not need any manpower picking up garbage and further is an environment-friendly system that the garbage is not exposed outside. In contrast to the existing pickup way by manpower and vehicles, GACF has a central-collected facility with about 6070km/h high-speed running air in a constructed pipe underground. The GACF can put the garbage into a trash burner in accordance with the type of garbage (inflammable or not inflammable). The processed garbage can be carried to a 1327978-1-4244-8115-6/11/$26.00 2011 IEEEProceedings of the 2011 IEEEInternational Conference on Mechatronics and AutomationAugust 7 - 10, Beijing, Chinafinal disposal site by a container vehicle. Fig. 1 shows the key map of GACF. Fig.1 Key map of GACF As mentioned above, GACF can collect household garbage fast and clean. Moreover GACF can carry household garbage to the final disposal site, i.e., trash burner. In specific, when residents throw away household waste into an input slot of GACF, the garbage is transported through a pipe connected with a collected site. At the collected site, GACF operates an air blower connected with the pipe and inhales air from an air-intake port as shown in Fig.1. At this moment, according to air flow, GACF collects household garbage. In order to stably maintain GACF for a long period, in-pipe cleaning is important. In the near future, an in-pipe cleaning robot with autonomous movement needs to be developed for making the pipe clean. The usage of in-pipe cleaning robot can make the aging of pipe delayed so that pipe replacement costs can be reduced. So far research on in-pipe robot has been focused on inspection rather than cleaning. For example, Roh et al. 2 has developed a differentially driven in-pipe inspection robot for underground gas pipeline. Besides, Choi et al. 3 has developed the in-pipe inspection/cleaning robot which can be stuck on the inner face of pipe by using wheels with springs, as shown in Fig. 2. This robot has a severe drawback that the robot could be separated from the inner face of pipe when one wheel would be not effective at branching point of pipe. Fig. 2 in-pipe inspection/cleaning robot (Choi et al. 3) In GACF, when garbage is moving, we have to remove the impurities which are stuck to the inner face of the pipe (diameter: 300mm or 400mm). Thus, in this paper, we will develop an in-pipe cleaning robot of GACF with the sliding mechanism which can be adjusted to fit into the inner face of pipe using pneumatic pressure (not spring). The proposed in-pipe cleaning robot for GACF can have forward/backward movement itself as well as rotation of brush in cleaning. The robot body should have the limited size suitable for the smaller pipe with diameter of 300mm. In addition, for the pipe with diameter of 400mm, the links of robot should stretch to fit into the diameter of the pipe by using the sliding mechanism. The robot has a camera at its front and a spinning brush, which can perform both cleaning and inspection simultaneously. Also it can raise cleaning efficiency by making two brushes spinning inversely each other. This paper is organized as follows. Section II explains the conceptual design of the proposed in-pipe cleaning robot by using TRIZ (Inventive Theory of Problem Solving in Russian abbreviation) 4. Based on this conceptual design, we will set up the initial design of the robot in collaboration with the field engineer of Robot Valley, Inc. in Korea. For the optimal design of in-pipe cleaning robot, in Section III, the maximum impulsive force of collision between the robot and the inner face of pipe will be simulated by using RecurDyn when the link of sliding mechanism is stretched to fit into the 400mm diameter of the pipe. In Section IV, the stresses exerted on the 6 links of sliding mechanism by the maximum impulsive force will be simulated by using ANSYS Workbench based on the Design Of Experiment(in short DOE). Finally the optimal dimensions including thicknesses of 4 links will be decided in order to have the best safety factor as 2 in this paper as well as having the minimum mass of 4 links. Section V will draw conclusions. II. BASIC DESIGN OF IN-PIPE CLEANING ROBOT USING TRIZ The conceptual design of the proposed in-pipe cleaning robot is performed by using the 6SC 5 of TRIZ as follows: A. (The 1st Step of 6SC) Problem Statement in Picture Figure 3 shows a simple design of in-pipe cleaning robot. The problem is that the robot cannot fit into a pipe with 300mm/400mm in diameter because it does not have any changeable mechanism according to two types of pipe (300mm or 400mm in diameter). Fig. 3 Simple design of in-pipe cleaning robot B. (The 2nd Step of 6SC) System Functional Analysis To cope with the problem suggested above, we first perform system functional analysis as shown in Fig. 4, based 1328on the goal that the robot should be designed to fit into two types of pipe (300mm or 400mm in diameter). In this figure, maintaining the diameter of robot means keeping the status of robot fit into a pipe. Fig. 4 System functional analysis C. (The 3rd step of 6SC) Ideal Final Result (IFR) As IFR, we suggest the robot be designed to fit into the smaller diameter (i.e., 300mm) of pipe and then fit into the larger diameter (i.e., 400mm) in a stretchable form. D. (The 4th step of 6SC) Principle of Contradiction and Separation The following sentence can be expressed in contradiction: “ Two robot bodies should be designed to fit into two types of pipe (300mm or 400mm in diameter), respectively. And, the robots should be designed as one body.” To find a solution of the contradiction problem, we apply the principle of separation in the following sentence: “ Each robot body for two types of pipe is designed separately and then the two robot bodies are put together into one robot body.” E. (The 5th Step of 6SC) Elements-Interaction Analysis Figure 5 shows the elements-interaction analysis. In this problem, the elements are “ Body of Robot” and “ Diameter of Pipe.” This figure suggests that the body of robot is designed to fit into two standardized diameters (300mm and 400mm) of pipe as a variable mechanism. Fig. 5 Elements-interaction analysis F. (The 6th Step of 6SC) Problem Solution and Appraisal The tentative solution of problem can be drawn as follows: the diameter of robot needs to be changeable for both two types of standardized pipes (300mm or 400mm). As shown in Fig. 6, the final problem solution proposed in this paper is 6-link sliding mechanism to fit into a pipe with 300mm/400mm in diameter. Especially, in this solution, pneumatic pressure is used for making the sliding mechanism fit into the inner face of pipe. Consequently the robot has three 6-link sliding mechanisms for one slider as shown in Fig. 7. As shown in this figure, the in-pipe cleaning robot has total six 6-link sliding mechanisms, i.e., 3 for the front slider and 3 for the rear slider. Fig. 6 6-link sliding mechanism Fig. 7 Three 6-link sliding mechanisms for one slider The appraisal of this problem solution can be made as follows: when one of three 6-link mechanisms falls in a branching point of pipe, 6-link sliding mechanism using pneumatic pressure can escape the branching point by maintaining the diameter of robot (in other words, the status of robot fit into a pipe), and can move stably because two of three 6-link mechanisms can be fixed as shown in Fig. 8. Fig.8 Appraisal of 6-link sliding mechanism using pneumatic pressure at a branching point III. DYNAMIC SIMULATION USING RECURDYN Based on the conceptual design of in-pipe cleaning robot explained in Section II, the initial design of 6-link sliding mechanism using pneumatic pressure is proposed in Fig. 9, in collaboration of Robot Valley, Inc. in Korea. Especially Table 1 shows the lengths and thicknesses for the initial design of links 1 to 4, which have come from the empirical knowhow of design expert at Robot Valley. For the optimal design of in-pipe cleaning robot, the maximum impulsive force of collision between the robot and the inner face of pipe is simulated in this section by using RecurDyn (multi-body dynamics 1329simulation program) when the link of sliding mechanism is stretched to fit into the 400mm diameter of the pipe. Especially the 400mm diameter of pipe is selected rather than the 300mm diameter of pipe because it has been assumed that the former has bigger acceleration and longer displacement than the latter. Fig. 9 6-link sliding mechanism using pneumatic pressure TABLE 1 INITIAL DESIGN OF LINKS Links 1 2 3 4 Length (mm) 91 91 37 145 Thickness (mm) 10 5 5 10 When the 6-link sliding mechanism with the initial dimensions of lengths, and thicknesses of Table 1 is stretched to fit into the 400mm diameter of the pipe owing to pneumatic pressure (which pushes the sliding link, i.e. link 5), it collides with the inside wall of the pipe. At that time, the multi-body dynamics simulation program, i.e., RecurDyn is used to find the maximum impulsive force of collision between the robot and the inner face of pipe. At the first step for this dynamic simulation, the 3-dimensional modeling of 6-link sliding mechanism using SolidWorks (as shown in Fig. 9) is imported into RecurDyn. The constraints considered in this simulation using RecurDyn are gravity, joint, fixed condition, contact, and spring force condition. The gravity is supplied by g = 9.81m/s2 in the direction shown in Fig. 10. 6 joints are set up as Revolute Joints in RecurDyn as shown in Fig. 10. The lower part connected to Joint 1 is fixed, while the lower part connected to Joint 2 doesnt need constraint so that it can slide. Fig. 10 Constraints of joint and fixed condition In collision of six 6-link sliding mechanisms of robot with the inner face of pipe, only one 6-link sliding mechanism is considered in RecurDyn for convenience. 2 wheels of 6-link sliding mechanism is given by “ solid contact” with the inner side of side as shown in Fig. 11. Also, the solid contact condition is given against collision of the fixed part (connected to Joint 1) with the sliding part (connected to Joint 2). Fig.11 Contact constraint The sliding movement of 6-link mechanism is actuated by pneumatic pressure. But there is no pneumatic pressure constraint in the RecurDyn program. In this simulation, we have assigned pneumatic pressure to spring force. In case of pneumatic pressure, the 6-link mechanism slides at the acceleration of 2 m/s2. Through the dynamic simulation of RecurDyn as shown in Fig. 12, the spring force condition with spring constant 5 N/mm and spring displacement 40 mm makes the 6-link mechanism slide with 1.97m/s2 acceleration. Thus pneumatic pressure can be replaced by spring force with constant 5 N/mm and displacement 40 mm. Fig.12 Spring force condition Figure 13 shows the impulsive force simulated by using RecurDyn when the 6-link sliding mechanism collides with the inner side of pipe (diameter 400 mm). As shown in this figure, the mechanism slides for 1 second (from the instant that spring force condition works). Then we can see the maximum impulsive force as about 100N. 1330 Fig. 13 Simulation result of impulsive force using RecurDyn IV. OPTIMAL DESIGN OF 6-LINK SLIDING MECHANISM Now we deal with the optimal design of 6-link sliding mechanism for the in-pipe cleaning robot in this section. First, the maximum impulsive force, i.e., 100N obtained by the dynamic simulation using RecurDyn in the previous section, is loaded on the point of wheel 1 for the 6-link sliding mechanism, as shown in Fig. 14 (3-D model of ANSYS Workbench). We have assumed that wheel 1 collides with the inner side of pipe earlier than wheel 2 in the dynamic simulation because wheel 1 has shorter distance from the 6-link mechanism than wheel 2. Then static analysis using ANSYS Workbench is performed based on DOE (that is, Design Of Experiment) in order to obtain the optimal dimensions of 4 design variables, i.e., thicknesses of 4 links as shown in Fig. 15. Fig.14 3-D model of ANSYS Workbench Fig.15 6-link sliding mechanism (top view) DOE 6 is usually used to extract the maximum information by performing the minimum simulations (or experiments) for a given design (or performance testing) problem. The DOE can be helpful in figuring out quantitative effect regarding each design (or experiment) factor (or variable) in the problem. This leads to find the optimal values of design (or experiment) variables. At design of 6-link mechanism, the number of design variables (control factors in statistical terms) is four of four levels as shown in Table 2. Table 2 shows each factor s levels which has come from the design experience of field engineer at Robot Valley, Inc. For this 6-link mechanism, the orthogonal array(L16) of four-level four design variables is generated by using DOE (specifically MINITAB), instead of full 256 (44). TABLE 2 LEVEL OF DESIGN VARIABLES LevelFactor1 2 3 4 Link1 Thickness(mm)5 10 3 8 Link2 Thickness(mm)5 10 3 8 Link3 Thickness(mm)5 10 3 8 Link4 Thickness(mm)5 10 3 8 Based on the orthogonal array (L16) of Table 3, the static analysis for the 6-link sliding mechanism is performed in 16 times using ANSYS Workbench. The optimal values of 4 design variables can be selected according to the criterion: (1) the safety factor of 6-link sliding mechanism should be as much as 2 (the best safety factor is recommended as 2 by field engineers in the design of robots), (2) the mass of the mechanism should be minimized. The criterion can be specified in a similar manner to a multi-objective problem. Thus this multi-objective criterion is given by equation (1). Here sf1 and sf2 indicate scaling factors. Moreover, w1 and w2 are weighting factors. The proper values of weight and scale factors are selected according to equation (1). Since the multi-objective criterion has to be a linear combination function, the value of 0.5 has been assigned to both w1 and w2. In the meanwhile, the constants of sf1 and sf2 are given by 0.5 and 0.5, respectively, in order to impose the ceiling value of the maximum value of objective criterion on 1. According to DOE, the 16 times of analyses have been carried out. Fig. 16 shows on of 16 results performed by the static analysis using ANSYS Workbench. Consequently the last column of Table 3 shows the optimal (corresponding to the minimum value of objective function) design variables underlined in red, compared to the other 15 set of design variables. Thus the optimal thicknesses of link 1, 2, 3, and 4 are all 5mm s, while the initial ones of link 1, 2, 3, and 4 are 10mm, 5mm, 5mm, 10mm, respectively, as shown in Table 1. Finally it can be noticed that the optimal design (or optimal thicknesses) has the value (i.e., 0.09653) of objective function including safety factor 2.7065 and mass 0.145kg much smaller than the case of initial design with the value (i.e., 0.27631) of objective 1331function including safety factor 3.6751 and case of initial mass 0.241kg as shown in row 17 (underlined in blue) of Table 3. Especially the material of links is AL 7075-O(ss) with heat-treated specially. Therefore we can conclude that y the optimal design of 4 links has the best safety factor close to 2 as well as having the minimum mass of 4 links, compared with the initial design performed by the expert of Robot Valley, Inc. The prototype of in-pipe cleaning robot including the 6-link sliding mechanism with these optimal dimensions is shown in Fig. 17. This prototype is under cleaning test in collaboration with Robot Valley, Inc. TABLE 3 ORTHOGONAL ARRAY Fig.16 One result of static analysis using ANSYS Workbench Fig.17 Prototype of in-pipe cleaning robot including 6-link sliding mechanism with optimal dimensions V. CONCLUSION Recently, interests on in-pipe cleaning robot are increasing because Garbage Automatic Collection Facilities (i.e, GACF) are widely being installed in Seoul metropolitan area of Korea. In GACF, when garbage is moving, we have to remove the impurities which are stuck to the inner face of the pipe (diameter: 300mm or 400mm). Thus, in this paper, by using TRIZ (Inventive Theory of Problem Solving in Russian abbreviation), we have proposed an in-pipe cleaning robot of GACF with the 6-link sliding mechanism which can be adjusted to fit into the inner face of pipe using pneumatic pressure (not spring). The proposed in-pipe cleaning robot for GACF can have forward/backward movement itself as well as rotation of brush in cleaning. The robot body should have the limited size suitable for the smaller pipe with diameter of 300mm. In addition, for the pipe with diameter of 400mm, the links of robot should stretch to fit into the diameter of the pipe by using the sliding mechanism. Based on this conceptual design, we have set up the initial design of the robot in collaboration with the field engineer of Robot Vall
- 温馨提示:
1: 本站所有资源如无特殊说明,都需要本地电脑安装OFFICE2007和PDF阅读器。图纸软件为CAD,CAXA,PROE,UG,SolidWorks等.压缩文件请下载最新的WinRAR软件解压。
2: 本站的文档不包含任何第三方提供的附件图纸等,如果需要附件,请联系上传者。文件的所有权益归上传用户所有。
3.本站RAR压缩包中若带图纸,网页内容里面会有图纸预览,若没有图纸预览就没有图纸。
4. 未经权益所有人同意不得将文件中的内容挪作商业或盈利用途。
5. 人人文库网仅提供信息存储空间,仅对用户上传内容的表现方式做保护处理,对用户上传分享的文档内容本身不做任何修改或编辑,并不能对任何下载内容负责。
6. 下载文件中如有侵权或不适当内容,请与我们联系,我们立即纠正。
7. 本站不保证下载资源的准确性、安全性和完整性, 同时也不承担用户因使用这些下载资源对自己和他人造成任何形式的伤害或损失。

人人文库网所有资源均是用户自行上传分享,仅供网友学习交流,未经上传用户书面授权,请勿作他用。