JT提升绞车设计【含10张AD图纸、说明书】
收藏
资源目录
压缩包内文档预览:
编号:15969991
类型:共享资源
大小:6.73MB
格式:ZIP
上传时间:2019-03-10
上传人:机****料
认证信息
个人认证
高**(实名认证)
河南
IP属地:河南
50
积分
- 关 键 词:
-
含10张AD图纸、说明书
提升绞车设计
JT提升绞车
jt提升绞车】jt提升绞车
- 资源描述:
-
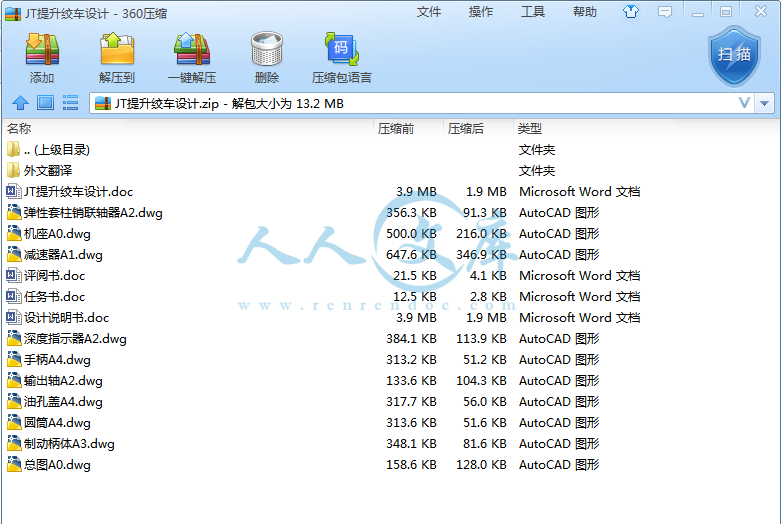
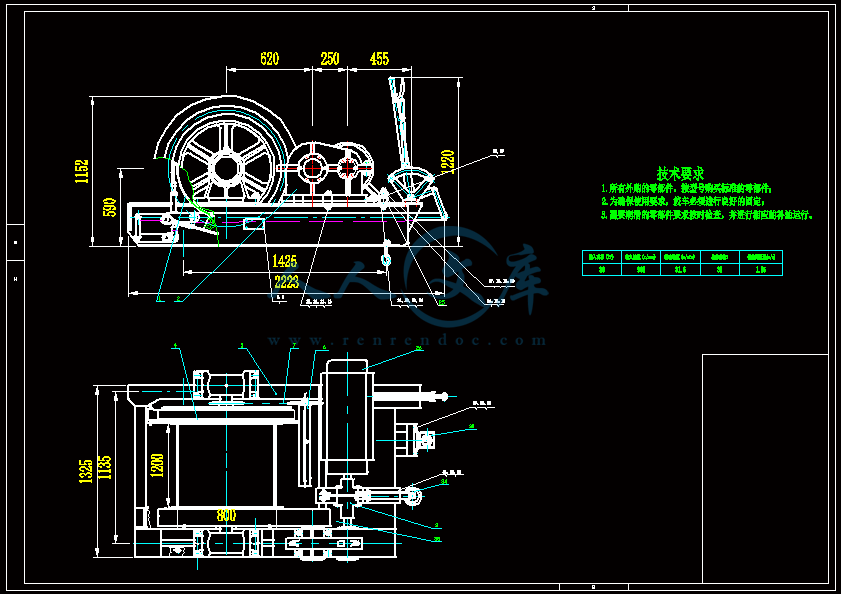
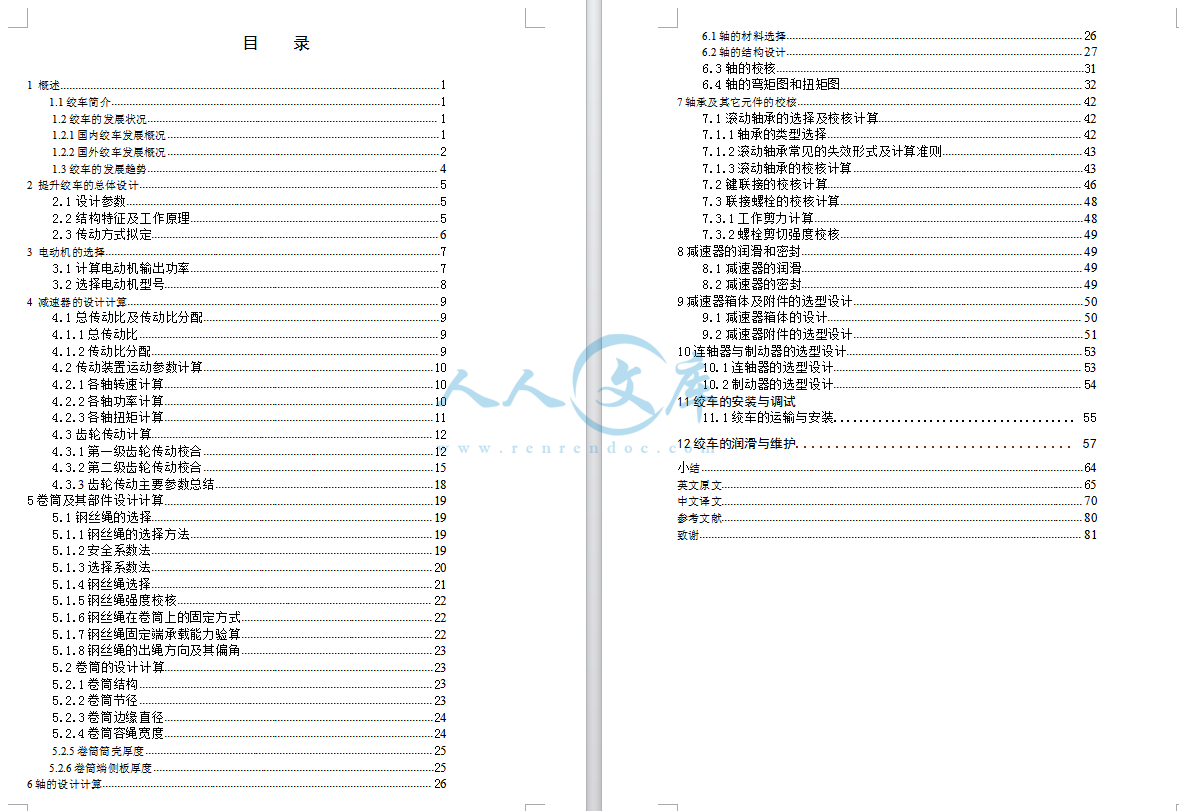


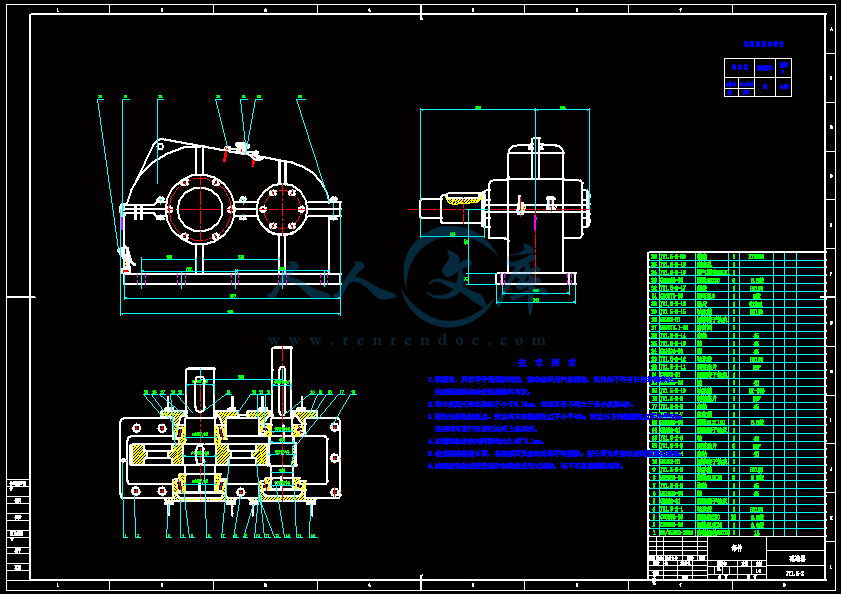






- 内容简介:
-
Proceedingsofthe 2009 IEEE International Conference on Mechatronics and Automation August 9 - 12, Changchun, China Study on theCNC Internal Gear Form Grinding Technology Ren Xiaozhong, Su Jianxin and Deng Xiaozhong SchoolofMechatronics Engineering Henan UniversityofScience2-Vertical pillar;3,8-CNCslide; 4-Grindingwheel support;5-CNCrotating table;6-wheel dresser;9-Mechanical slide;I0- Manual driving unit; II - Bed III.CONTROL OF INDEXINGACC URACY A CNC rotating table is used in the internal gear form grinding machine mentioned above to index tooth. Therefore, the accumulative pitch error depends mainly on the indexing precision of rotating table. Because the resolutionofthe rotating table is limit after all, when the decimal digit placeof the included angle between adjacent teethofgear goes beyond the resolutionofthe rotating table, the rounding error would be produced. The error is not very clear when the numberof indexed teeth is relatively small. But when the numberof indexed teeth is quite large, the larger accumulative error would be produced. The larger indexing error would cause the ground gear rejected. Therefore, measures should be taken to reduce or eliminate it. A new gear grinding method called “jumping division“ is proposed in this article. So called jumping division means grinding once every several teeth in gear grinding. The ideal index interval, called optimal tooth numbers jumped over, should make the roundingerror minimum, which is produced when the decimal fraction part ofthe included angle formed by the several teeth goes beyond theresolutionoftherotatingtable,thushavingthe accumulative error decreased to minimum. The index interval should not be divided out by the tooth number z to avoid repeat grinding among the several teeth. 4524 Suppose an internal gear with 124 teeth is to be ground by meansofan internal gear form grinding machine, which is equipped with a CNC rotating table with indexing accuracy 0.001. Ifjumping division is not used, then the included angle between adjacent teeth is 2/3=360/124 =2.903226 where /3 is tooth profile angleofa tooth slot on pitch circle.Itcan be seen that the rounding error produced in grinding 124teeth is 0.000226xI24=0.028= 1.68“ Suppose the index interval is 9, the rotating table should tum 26.129032 for once grinding. Then the rounding error is 0.000032. After the 124 teeth are completely ground, the total rounding error is 0.000032xI24=0.004=0.24“ Clearly, the error is very small. IV.DRESSING OF INVOLUTEPROFILEWHEEL Gear form grinding has many advantages over gear generationgrinding. The tooth profile accuracy depends mainly on the profile accuracyofform wheel to be dressed. Based on the dressing principle, there are two kindsof dressing methods: generation and interpolation. The wheel dressing can be done by meansofdiamond pen and diamond wheel. CNC wheel dressing by meansofgenerating method needs high level CNC system. And with the increaseofbase circle diameterofa gear to be machined, the size and manufacture costofwheel dresser becomes larger. When dressing wheel by diamond pen, the height and uneven wear ofpen point have largely an influence on the dressing accuracy. Therefore, a CNC wheel dressing device with diamond wheel based on interpolation principle is developed. And form wheel dressing program is also prepared. A. Involute wheel dressing principle in interpolation To dress involute profile wheel by meansofinterpolation is to find a seriesofnode in the involute according to the basic parameters of involute. The straight segments connected by two adjacent node are used to fit the involute approximately, consequently,realizingtheinterpolationofinvolute. Specifically, interpolating movement can be done by moving two CNC slides along two orthogonal coordinates separately, as shown in Fig. 2. Therefore, a 2-D coordinates system is set up by taking base circle center as origin, and the connection lineofthe center to the starting pointofinvolute as Y axis, as shown in Fig.3. Suppose the spread angle at any point Aofinvolute is e. e as a variable increases in tum by takingDe as initial increment. The corresponding coordinates points can be found by substituting e into the equations as follows. The coordinatesofpoint A is: XA=rbsinerbecose YA=rbcose+ rbesine(1) Authorized licensed use limited to: CHINA UNIVERSITY OF MINING AND TECHNOLOGY. Downloaded on April 19,2010 at 03:05:34 UTC from IEEE Xplore. Restrictions apply. Fig. 2 Involute interpolating principle x x B. The coordinatesofpoint B can be found by substituting oe+eintoequation(1).Bysubstitutingstraightline segmentABfor involute segmentAB,the maximum error 8 appears in the midpoint Nofstraight line segmentAB.By making a tangent NM to base circle and extending MN to intersection point M with involute, then the spread angleofM in base circle is: eM=arctg(xn/Yn)+ arccosrr, / ON)(5) Then MM rb x eM (6) ON =“;xn2+ Yn2 (7) xll=(XA+xB)/2 YII=(YA+YB)/2 (8) The lengthofMN is MN=.JON2+rb2 (9) Then, the maximum error in the normal directionof involute is: o= MN= MM- MN To check whether 8 can meet the interpolation precision.If 8 can not meet the requirement, then the new node should be calculated again by decrease the increment byhalfin order to reduce interpolation error.If8 can meet the requirement, but 8 is over small, then 20 e is taken to calculate the new node so as to improve interpolating efficiency. B. Analysisofdressing error How to choose the magnitudeofDe is the key in whole interpolatingprocess.OverlargeDewouldcauselarger interpolation error, and over-small De would cause lower interpolating efficiency.IfDe is determined according to machining accuracy, then the normal allowable error can be thoughtofinterpolation accuracy index. The denseness degree ofinterpolation points can be changed by changing the value ofDe, having the numbersofinterpolation points not only meetinterpolationprecisionbutincreaseinterpolation efficiency. As shown in Fig.3, the spread angle at point A is e, the corresponding coordinates point in base circle is A. The coordinatesofpoint A can be found by substituting e into equation(1).When base circle turns to point B by adding De to e, the corresponding coordinates point in involute is point Fig. 3 Mathematical model of involute interpolation The radiusofbase circle is: rb=mzcosa/2 The polar radiusofpoint A is: rA = rb/cosaA The spread angleofpoint A is: e=tgaA where m-moduleofgear; z-toothnumberofgear; a-pressureangleofgear in pitch circle; aA-pressureangleofpoint A. (2) (3) (4) 4525 C.Programmingfordressing involute wheelandsimulation Involute grinding wheel dressing program is prepared by using VC+ as developing tool. The wheel dressing software system is supposed to be four modules: gear parameters input and calculation; interpolation error calculation and control; involute dressing route simulation; and NC code output. FigA shows the flow chart for preparing wheel dressing program. The input is the gear parameters and the involute interpolation accuracy. The output is the Cartisian valueofinterpolation pointofinvolute. The CNC machining code generated is input intotheCNCunitthroughRS232interfacetorealize automatic dressing. The CNC machining code can also be used to imitate the wheel dressing action before real dressing. Fig.5 shows the simulationofwheel dressing.Itcan be used to verify the continuity and correctnessofthe program. V.INVOLUTE PROFILEWHEELDRESSING DEVICE Fig.6 illustrates a grinding wheel dressing with diamond wheel. The dressing is done by meansofthe roundcomer between the cylindrical surface and faceofdiamond wheel.It can be seen from Fig. 3 thatifthe traceofarc center in diamond wheel is a partofinvolute curve along the grinding wheel, the curvature radiusofgrinding wheel profile formed by dressing is different from thatofthe traceofarc center. The profileofform grinding wheel is a convex for internal gear grinding, its profile radius is less than thatoftraceofarc center. The case is on the contrary for the form grinding wheel usedfor external gear grinding. Theuseoftool radius Authorized licensed use limited to: CHINA UNIVERSITY OF MINING AND TECHNOLOGY. Downloaded on April 19,2010 at 03:05:34 UTC from IEEE Xplore. Restrictions apply. Fig.4 Flow chartofwheel dressing program Base Slide Servo motor Drive assembly Spindle assembly 1“-Diamond wheel Fig. 6 Sketch mapofwheel dressing The 3D drawingofwheel dressing device with diamond wheel is shown in Fig.7.Itconsistsofspindle assembly, drive assembly, feed assembly and base etc. The whole device is installed on the CNC slide of gear grinding machine, as shown in Fig.l. The rotationofdiamond wheel is driven by electrical motor. The feed movement along the spindle axis is realized by means of the CNC slide in X axis of gear grinding machine, and the other feed movement perpendicular to the spindle axis is driven by a servo motorofitself. The involute interpolation is accomplished by controlling the two feed movements. Fig.? Grinding wheel dressing device VI.WHEELDRESSING AND G EARGRINDINGEXPERIMENTS A. Wheel dressing Install the wheel dressing device on the form gear grinding machine.Adjustcorrectlytherelativepositionbetween diamond wheel and grinding wheel to be dressed. Start CNC system and servo motors. Then, the diamond wheel is driven by two slides in X axis and V axis separately to dress grinding wheel following the prepared programIO. Fig.8 shows that the wheel dressing device was on dressing condition. N Output all coordinates and save program code Fig.5 Wheel dressing simulation :t#q).tIl) l!)MltI Q I)!litlAlUI IDIfl af- compensation instruction in NC part programming can make the dressed profile be consistent with the theoretical profile 9. 4526 Authorized licensed use limited to: CHINA UNIVERSITY OF MINING AND TECHNOLOGY. Downloaded on April 19,2010 at 03:05:34 UTC from IEEE Xplore. Restrictions apply. Fig.8 wheel dressing device on dressing condition B. Gear grinding The gear to be ground is an internal gear with z=80, m=3, u=20, and tooth width b=70mm. Firstly, the wheel dressing device, workpiece, centerofrotating table, and grinding wheel frame etc. should be set to proper position so that the grinding wheel would not interfere with wheel dressing device in whole gear grinding process. Secondly, the grinding wheel should be dressed with the same profile as the tooth form before gear grinding. Thirdly, by inputting machining program through the operation panel, the unloading trial run must be done in order to ensure the grindingtrack correct.Lastly, gear grinding can be carried out. The internal gear grinding process is shown in Fi .9. Fig.9.Aninternal gear being ground The ground gear is inspected by a special gear inspection unit with Gleason gear inspection instrument. The precision with grade 6 can be met whether in tooth error, or tooth alignment error and pitch error. VII.CONCLUSION I) Based on developed CNC internal gear form grinding machine, jumping division is used for internal gear grinding. This methodis beneficialto ensure the toothindexing accuracy and reduce the accumulative pitch error. 2) Based on theinvoluteinterpolationprinciple, the mathematical modelofinvolute profile is established. Taking the spread angleofinvolute as variable and the normal allowance as a constrained condition, a interpolation method is proposed. 4527 3) By analyzing the dressing motions, a form wheel dressing device is designed, and wheel dressing program is prepared. 4) Gear grinding and wheel dressing experiments are carried out successfully. The result of internal gear grinding experiment validates the grinding technology proposed in this article. The gear grinding technology provides an effective way to improve the machining accuracyofinternal gears. ACKNOWLEDGMENT This topic of research is supported by National Natural Science FoundationofChina, No. 50575068, and by the Open Foundation of Henan Key Laboratory of Modern Mechanical Design And Transmission System, No. KFJZ200706. REFERENCES PVan Sijian, Han Cuichan. “Design and Manufacture of Involute planetary gearing“, China Machine Press, 2000. 2Shang Xiangdong, Jin Jiaqi, Fu JingShun. “Gear Machining Accuracy“, China Machine Press, 200I. 3 Zhou Pei, Zhao Jun, Xu Baolong, et al. “German CNC Gear Form GrindingMachineandGearGrindingTechnology“,Current Manufactuing Engineering, no.9, pp. 91-92, September 2002. 4 Ren Xiaozhong, Den Xiaozhong,
- 温馨提示:
1: 本站所有资源如无特殊说明,都需要本地电脑安装OFFICE2007和PDF阅读器。图纸软件为CAD,CAXA,PROE,UG,SolidWorks等.压缩文件请下载最新的WinRAR软件解压。
2: 本站的文档不包含任何第三方提供的附件图纸等,如果需要附件,请联系上传者。文件的所有权益归上传用户所有。
3.本站RAR压缩包中若带图纸,网页内容里面会有图纸预览,若没有图纸预览就没有图纸。
4. 未经权益所有人同意不得将文件中的内容挪作商业或盈利用途。
5. 人人文库网仅提供信息存储空间,仅对用户上传内容的表现方式做保护处理,对用户上传分享的文档内容本身不做任何修改或编辑,并不能对任何下载内容负责。
6. 下载文件中如有侵权或不适当内容,请与我们联系,我们立即纠正。
7. 本站不保证下载资源的准确性、安全性和完整性, 同时也不承担用户因使用这些下载资源对自己和他人造成任何形式的伤害或损失。

人人文库网所有资源均是用户自行上传分享,仅供网友学习交流,未经上传用户书面授权,请勿作他用。