DN4000水煤气洗涤塔设计(包含CAD图、说明书、开题报告、翻译)
收藏
资源目录
压缩包内文档预览:(预览前20页/共24页)
编号:17503317
类型:共享资源
大小:2.59MB
格式:ZIP
上传时间:2019-04-09
上传人:机****料
认证信息
个人认证
高**(实名认证)
河南
IP属地:河南
25
积分
- 关 键 词:
-
DN4000水煤气洗涤塔设计包含CAD图、说明
DN4000水煤气洗涤塔设计
DN4000 水煤气洗涤塔设计
设计说明书水煤气洗涤塔
水煤气洗涤塔
- 资源描述:
-





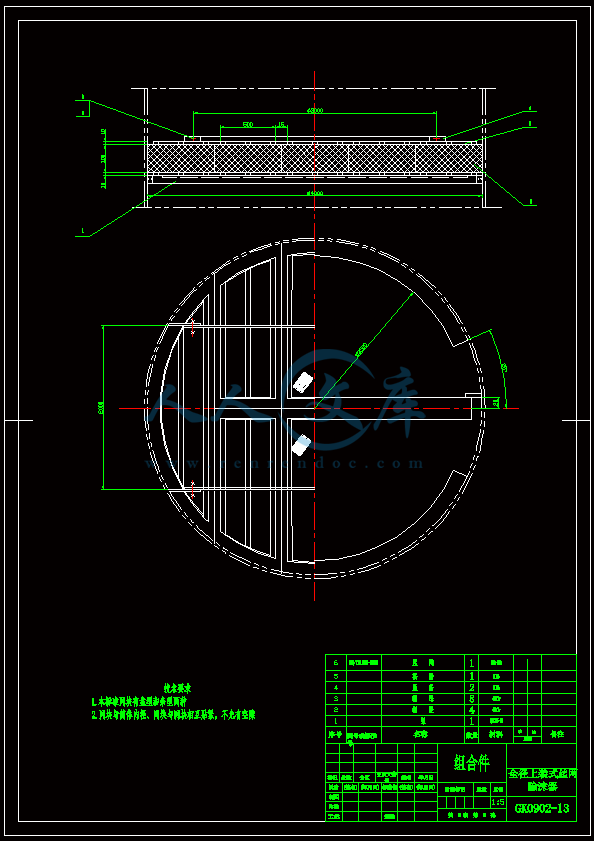




- 内容简介:
-
外文翻译一:Strain Strengthening Technology of Pressure Vessels of Austenitic Stainless SteelDENG Yangchun1, CHEN Gang1, YANG Xiaofeng2, XU Tong3(1EastChina University of Science and Technology, Shanghai,200237, China;2HubeiSpecialEquipmentSafety Inspection and Research Institute, Wuhan,430077, Hubei, China;3China Special Equipment Inspection and Research Institute, Beijing,100013, China )AbstractThe basic principle of strain strengthening was presented, and twomodels of the strain strengtheningOf pressure vessels of austenitic steelthe strain strengthening Avesta model at normal atmospheric temperatures and the strain strengthening Arde form model at low temperatures, were analyzed. Meanwhile, the selections of permissible stress of austenitic stainless steel were compared and analyzed in several pressure vessel standards. EN13445 Pressure VesselStandardchooses1. 0as the yield strength of austenitic stainless steel In this condition, the value of the safe factor of them aterials is low and practicalKeywordsPressure Vessel Austenitic Stainless Steel Strain Strengthening, Yield StrengthArticle Idz: TQ050 4 +1 Document code A Article ID 0254-6094 (2008) 01-0054-06The austenitic stainless steel having good high temperature performance, low temperature performance and corrosion resistance, and high tensile strength, but the yield strength is lower. By the standard of GB150 pressure vessel, material yield strength and tensile strength, respectively, divided by the safety factor to determine the material allowable stress values, whichever is less, often resulting in austenitic stainless steel allowable stress values low, can not give full play to the material carrying capacity. To this end, the researchers by strain hardening improve the yield strength of austenitic stainless steel, his article will make the technology to commentary. 1 Austenitic stainless steel strain hardening basic principlesShown in Figure 1, the deformation of the material exceeds the material yield strength, k reached after unloading is in elastic state, before re-applying a load to the material stress reaches the k, k equivalent material yield strength, apparently k 0 2. Figure 1 austenitic stainless steel unidirectional tensile FigureFor non-stable austenitic stainless steel, due to the strain generated martensite hardening rate gradually increases due to the increase of strain necking was postponed, up to a maximum elongation. In the same time, the martensite the merit-formed so that the stress concentration is relaxed, showing a phase transformation induced phenomena. Processed at room temperature for stable austenitic stainless steel is not formed martensite grain refinement, the lattice distortion and dislocation density will produce a hardening effect.Austenitic stainless steel strain hardening of this feature, widely used in the fields of bridges, buildings, parts of Europe has been used in the field of pressure vessel. Austenitic stainless steel pressure vessel strain hardening commonly used in two modes: the Avesta mode and Arde form mode.2 austenitic stainless steel pressure vessel at room temperature strain hardening - A-Vesta modeThe austenitic stainless steel pressure vessel at room temperature strain to enhance hydrostatic test to produce about 8% (maximum 10%) of plastic deformation, and can improve the yield and tensile strength of the austenitic stainless steel material, the method is usually called Avesta mode (Cold Stretched Forming). The pressure vessel using the media generally liquid nitrogen, liquid oxygen and liquid hydrogen, the main civilian use. Sweden Avesta Sheffield since 1959, has been engaged in the work of the austenitic stainless steel pressure vessel strain hardening, and applied for a patent in many countries 1. Avesta Sheffield in Sweden in 1959 by special permission, after 15 years of use of austenitic stainless steel strain hardening technology manufacturing pressure vessels, Swedish Pressure Vessel Technical Committee in 1974 austenitic stainless steel pressure vessel strain hardening technology, 1975 into the pressure vessel specific standards - strain hardening Pressure Vessel Code 2 (the Cold-stretching Direction - CSD). In 1977, Sweden, Finland, Norway, Germany, Australia, the Netherlands, the United Kingdom, Spain, Portugal, Czechoslovakia and South Africa and other countries have accepted austenitic stainless steel pressure vessel strain hardening technology 3. The Swedish strain hardening pressure vessel standards CSD, use of materials equivalent to 304 and 316L, the maximum thickness of 30 mm, maximum operating temperature of 400 C. Annealed materials 0 2 to about 210MPa, elongation greater than 35%. The enhanced yield strength about 410MPa, conventional methods of design as a new material, and then take k. Strain hardening hydraulic test pressure is determined by the following formula The Swedish CSD standards that uniaxial tensile specimens, up to 10% strain sufficient to ensure that the material yield strength k value. Plane stress Mises yield criterion, the corresponding strain according to Table 1 the ratio between the calculated.Table 1 stress, strain ratio between The Swedish CSD standard that ensure that new material yield strength k value, the cylindrical ring to the maximum strain is 8.7%; the Spherical maximum strain of 5.0%. The Swedish standard specifies a maximum strain of 10.0%. The actual cylinder maximum strain of 3% to 5%, mainly due to: a. Actual material s larger than the standard value; b actual thickness deviation and calculations rounded margin; c head, receivership strengthen effect. Another important problem is that the 1991 edition of the Swedish CSD standard no longer need to ensure that the new material yield strength k value, simply press the strain hardening k calculate the required pressure hydrostatic testing can be. Abandon the 1975 edition of k computing, the need to ensure the requirements of the minimum strain.The jonson J 1 pointed out that the strain hardening need to ensure the stability of the material organization, not because of the strain have martensite. Commonly stable and metastable austenitic small amount of strain conditions, does not produce martensite. 304L and 316 through 300 to 350 C, 000h aging tests showed that the strain hardening processing materials with no strain hardening material handling, small changes in yield strength and tensile strength values, can improve the use of strain hardening temperature. Strain hardening treatment material 550 to 650 C is still very good creep resistance, fatigue strength. Less than 10% strain hardening material, in a weak oxidizing media such as H2SO4, corrosive and strain hardening material; stress corrosion results. , 304L, 316 steel residual stress due to strain hardening to reduce or eliminate this stress corrosion tests confirmed.HesslingG 4 noted that the strain hardening material savings, with increasing temperature, the amount of material savings reduce BrautigamM 5 noted that the base material and the electrode of the pressure vessel with a stable austenitic stainless steel 304LN, when the strain hardening plasticity variable 20 % when used in liquid nitrogen (including enhanced), none of the base metal, weld and heat affected zone to produce martensite. 321 metastable austenitic 20% strain was generated martensite; liquid helium cryogenic, unfinished martensitic transformation; in 20 C, 250 cycles can accelerate the martensitic transformation, consider -196 C, the cycle of martensitic transformation. 20% strain on the stability of austenitic and the metastable austenitic material impact toughness are affected; does not produce martensite stable austenitic material Impact Toughness distorted crystal structure. Stable austenitic materials, 20% strain result in a material impact greater than the low temperature impact toughness decreases stable the austenitic and metastable austenitic materials; 20% strain at 20, -196, -269 , the impact toughness AD can meet the specifications and ASME Code pressure vessel strain; actual strain hardening only 8% to 10%, in the cryogenic liquid enough impact toughness. Ambrose S 6 1969 strain strengthen technological research, first enacted in 1969 the specification ME/1/69-134 strain hardening pressure vessel (for low temperature), 1999, included in the standard AS1210 Appendix 2. Material 304,316 L, etc.; strain limit of 5%, 10% of the local maximum, than Swedish standard conservative. Limit of 5%, mainly in order to meet the requirements of the the ISO/TC11 (1970). Strain hardening method has three advantages: a. The release of residual stress; B. In many cases, changing the shape, improve the anti-yielding capacity; c improve the fatigue performance. The standard EN13458 EU cryogenic pressure vessel Appendix C 7 strain hardening technology, recommended several materials can also use other stable austenite and metastable austenitic material, provided that they meet the technical requirements. Material maximum thickness of 30mm, the maximum temperature of 50 C, elongation greater than 35%. The annealed material strain hardening, the yield strength k than 0 2 increased up to about 200MPa. Design as a new material, and then the conventional method. Strain hardening required hydrostatic test pressure of 1.5 times the design pressure to ensure that in the course of container in the elastic state. The strengthening of the annealed container, the amount of deformation; materials to strengthen the container the (inadvertently reinforce or plate rolling intends to strengthen) refers to the process, the water pressure smaller deformation. Annealed container the maximum allowable 10% strain in a long time to keep the load in the case of allowable increase of 1% to 2% strain, in fact, generally cylindrical to 3% 5% strain. This strain hardening of the material after to maintain a higher elongation and impact toughness. Rana M D 8 of ISO/TC220 2000 on the low-temperature austenitic stainless steel containers, also accept strain hardening method, consistent with EN13458.3 austenitic stainless steel pressure vessel at low temperature strain strengthen-Arde form modeIn 1961, Arde-Portland annealed 301 austenitic stainless steel container? 196 C (liquid nitrogen) insulation, strain hardening hydraulic test, resulting in about 10% (maximum 13%) plastic deformation 301 steel yield and tensile strength, some then after 427 C, and 20h aging treatment, to further improve the yield and tensile strength of 301 steel 9, usually known as the method for Arde form mode (Cryogenic Stretch Forming). The austenitic stainless steel pressure vessels used in the aerospace field, the use of media for liquid nitrogen, liquid oxygen and liquid hydrogen. Of Arde-Portland company Alper RH 10 for a more detailed experimental study of Arde-form mode performance. Ball of the same size (301 steel),? 196 C after strain hardening, without aging treatment at room temperature for more than 2h? 196 C blasting, the yield stress ratio strain enhanced stress a small amount of the increase, indicating that at room temperature under certain aging effect; After 427 C, 20h aging treatment, yield stress ratio strain enhanced stress were significantly increased, and with a different strain hardening stress; stress closer to both blast. Annealed spherical? 196 C Blow, yield stress equivalent to the yield stress of the material at this temperature, which is generated starting strain hardening stress; blasting lower stress, but considering the material is thinned, according to the true stress calculation, blasting stress and strain hardening ball stress more consistent. The blasting experiments conducted at ambient temperature, not after the aging treatment the ball vary depending on the yield stress ball original strain hardening stress; higher yield stress after the aging treatment of the ball, and also higher rupture stress. At the same time, the use of smooth specimens subjected to a tensile test (uniaxial stress),? 196 C, with the strain to enhance stress increases, the room temperature tensile yield strength and tensile strength are increased; samples after aging treatment than without aging The treated samples have a higher yield strength and tensile strength. In order to study the biaxial stress, with notched specimens for tensile test at? 196 C, with the strain strengthen the stress increases, little change in the yield stress of aging sample; without aging treatment increased the yield stress of the specimen; Not after aging the yield stress of the treated samples than the original strengthen stress increases, further strengthening effect at room temperature. ? 196 C to a tensile test, notched specimen, and the tensile strength ratio smooth, without aging the sample, with the original strengthen the stress increases; However, after aging the sample, with the original strengthen when the stress increases. That is, the stress increases with the original strengthen the notch sensitivity increase. Test summary, the following conclusions: a low temperature can be used to strengthen to improve the strength, the manufacture of pressure vessels; b without limitation of strain hardening stainless steel? 196 C have a higher notch toughness; c strengthen the limitation of strain stainless steel,? 196 C and has high strength at room temperature; d in? 196 C generating strain hardening, requires a certain amount of stress. Arde-Portland Henderson SW 11: strain hardening and then after aging can improve strength; improve the material strain hardening creep resistance and notched strength; without the limitation of strain hardening stainless steel, high temperature performance is also good. Below the yield stress, in a strongly oxidizing environment, corrosion resistance and annealed pressure vessel. Summary of strain hardening main advantages: high strength; high creep strength; high notch toughness; distorted low temperature aging at 427 ; improve reliability, the the cylinder deformation of 12% to 14%, the ball deformation of 7% to 8%, testable ray undiscovered defects; reduce stress concentration; for the benefit of the weld, the weld and base metal; improve corrosion resistance.ArdePortland Arthur C 12 pointed out that, Arde form mode manufacturing pressure vessels mainly due to the non-proliferation of type face-centered cubic lattice into a body-centered cubic lattice, austenite into martensite, and after the aging , to further enhance its strength at room temperature. Its successful application in that three important factors: a chemical composition, the material has the best combination of strength and toughness, ease of welding; b welding will produce a contraction of 1%, strain hardening, and the strength of the base metal, It is essential that the welds smooth transition, these can not be achieved by the traditional method; deformation (c design, pressure vessel deformation amount of theoretical calculations mentioned earlier, this is completely unnecessary, pressure vessel deformation simply to or greater than the amount of deformation of the theoretical calculation of the pressure vessel can be). Also, strain hardening, the container to the most natural geometry changes, such as head shape to spherical.4 two austenitic stainless steel pressure vessel strain hardening modeTable 2 Comparison of two austenitic stainless steel strain hardening mode. Relatively, Arde form mode strain greater degree of enhancement, the adverse impact on the material properties are also relatively large, its high cost, the process is more complex, mainly for the aerospace field 13, few reports. Avesta method has been accepted in many European countries, EN13458 Appendix C has been adopted, with more experience.Table 2 austenitic stainless steel pressure vessel strain hardening Comparison5 types of pressure vessel standard austenitic stainless steel allowable stress value comparisonAustenitic stainless steel pressure vessel strain hardening upon the conventional approach to design, manufacturing process and select the material allowable stress values. Austenitic stainless steel pressure vessel unique strain hardening is to increase the allowable stress value and improve the sharpest increase the pressure vessel material yield strength. And the other to improve the austenitic stainless steel material allowable stress value is the yield strength to select and adjust the yield factor of safety, the material is not plastically deformed. United States ASME -1 and ASME VIII -2 required for the austenitic stainless steel materials, allowable stress values to allow a small amount of pressure vessel deformation occasions, the highest desirable design temperature 0 90 2 to it than 0 2/ns. Germany for austenitic stainless steel, the yield strength has value by 1. 0,. Usually, 1 than 0 2 high-40MPa, such as 304, the material will increase the yield strength value of 20%. 50 to 60 years in the last century the United Kingdom, Norway, Sweden, Australia and many other countries. EU EN13445 Pressure Vessel Code also used this approach. Of Pressure Vessel Code for austenitic stainless steel, conventional design standards GB150 and stress analysis and design standard JB4732 at temperatures greater than 100 C, Xu with stress value value with the U.S. ASME -1 and ASME -2 basically the same; lower than 100 C, austenitic stainless steel material allowable stress value varies with carbon steel allowable stress value value the same way. Due to the lower yield strength of austenitic stainless steel materials, the allowable stress values by the yield strength of material decisions, showing that of austenitic stainless steel material allowable stress value is very low. Seen from Table 3, with an austenitic stainless steel material,ASME VIII -1 and EN13445 austenitic stainless steel material allowable stress values than GB150 different degree, and the design pressure, the material of the above three criteria are in elastic state, no plastic deformation of the overall structure of the pressure vessel. EN13458 Appendix C strain hardening method (Avesta mode) material allowable stress values than three standard has greatly improved, the least amount of material, with greater economic value; design pressure, the material in a plastic state, the pressure The overall structure of the container has a significant plastic deformation occurs. , Arde form mode strain hardening better, mainly for the aerospace industry.Table 3 austenitic stainless steel pressure vessel design allowable stress values selected Table 4 lists several austenitic stainless steel material 0.2 1.0, k value. The jonson J 14 from room temperature to 400 C or less, the same kind of austenitic stainless steel pressure vessel standards allowable stress values, as shown in Figure 2. According to the type of material, EN13445 than ASME VIII -1 allowable stress value of 20% 35%; 200 C when the material savings of 2% to 20%. Table 4 several austenitic stainless steel yield strength values Figure 2 different standard the same austenitic stainless steel under the maximum allowable stress values6 Conclusion6.1 austenitic stainless steel pressure vessel technology can greatly save material strain hardening. Avesta mode has some experience, easy to implement, and has good application prospects.The yield strength of.6.2 EU EN13445 standard austenitic stainless steel pressure vessel by 1. 0 select, material safety factor lower value, to save material, the use of a wider range of manufacturing, no special requirements, very practical. References1Jonson J. Coldstretched Austenitic Stainless Steel Pressure Vessels. Second International Conference on Pressure Vessel Technology, PartMaterials, Fabricationand Inspection. 1973. 115711652Cold-Stretching Directions 1991. Swedish Pressure Vessel Standardization3Malstrom U. Design Criteria Involving Factors of Safety onTensile Strength. Yield Strength and Creep RuptureStress. 1977. 29344Hessling G. Design Criteria for Boilers and Pressure Vessels. Papers Presented at the Sixth International Conference on Pressure Vessel Technology. 1988. 67965Brauti gam M. Pressure Vessels for Cryogenic Service Some New Aspects of Materials and Construction. The Seventh International Conference on Pressure Vessel Technology. 1992. 8878996Ambrose S. Australian Practice with Cold Stretched Pressure Vessels. The Ninth International Conference on Pressure Vessel Technology. 2000. 991077Cryogenic vessels-Static Vacuum Insulated VesselsEN13458, 20008RanaM D. Development of ISO Standards for CryogenicVessels, Pressure Vessel and Piping Codes and Standards. ASME PVP453, 2005. 2252349Cryogenic Forming: New Process Stretches and Strengthens. The Iron Age, 1961, 188(8): 616310Alper R H. Cryogenically Stretch-Formed Type 301Stainless Steel for Cryogenic Service. Materials Research& Standards, 1964, 4(10): 52553211 Henderson S W. High Strength Pressure Vessels by Stretch Forming. Materials in Design Engineering,1964, 60(6): 10410612 ArthurC. Cryogenic Stretch Forming Improves Strength Of Vessels. Metal Progress, 1969, 96(1): 646713 HurllichA.Metals and Fabrication Methods used for the Atlas. Metal Progress, 1959, 76(5): 657314Jonson J. Comparison of New EN and ASME Pressure vessel Rules for Stainless Steel The Ninth International Conference on PressureVesselTechnology.2000, 5764外文翻译二: 奥氏体不锈钢压力容器的应变强化技术*邓阳春陈钢杨笑峰徐彤(华东理工大学) (湖北省特种设备安全检验检测研究院) (中国特种设备检验研究院)摘要介绍了应变强化基本原理,并分析奥氏体不锈钢压力容器应变强化两种模式常温应变强化Avesta模式和低温应变强化Ardeform模式。同时,分析比较几种压力容器标准关于奥氏体不锈钢材料的许用应力选取,其中欧盟EN13445压力容器标准奥氏体不锈钢屈服强度按1. 0选取,材料安全系数取值较低,非常实用。关键词压力容器奥氏体不锈钢应变强化屈服强度中图分类号TQ0504+1文献标识码A文章编号0254-6094(2008)01-0054-06奥氏体不锈钢材料具有很好的高温性能、低温性能和抗腐蚀性能,而且抗拉强度很高,但屈服强度却较低。按GB150压力容器标准,以材料屈服强度和抗拉强度为基准,分别除以相应的安全系数,取其小值来确定材料许用应力值的方法,往往导致奥氏体不锈钢材料许用应力值偏低,不能充分发挥材料承载能力。为此,研究人员通过应变强化实现了提高奥氏体不锈钢材料的屈服强度,本文将对该技术作以评述。1 奥氏体不锈钢应变强化基本原理 如图1所示,材料变形超过材料屈服强度,达到k后卸载,当重新施加载荷,材料应力到达k之前,处于弹性状态,k相当于材料的新屈服强度,显然k0. 2。 图1奥氏体不锈钢单向拉伸图 对于非稳定奥氏体不锈钢,因应变产生马氏体,使加工硬化率因应变的增加而逐渐增大,缩颈被推迟,故延伸率可达最大值。同时,马氏体变体的择优形成使应力集中被松驰,呈现了相变诱导现象。对于稳定奥氏体不锈钢,在室温下加工不会形成马氏体组织,但其晶粒细化、晶格扭曲和位错密度增大也会产生硬化效应。 奥氏体不锈钢应变强化这一特性,广泛用于桥梁、建筑领域,欧洲部分国家已用于压力容器领域。奥氏体不锈钢压力容器应变强化常用两种模式:Avesta模式和Ardeform模式。2奥氏体不锈钢压力容器常温应变强化A-vesta模式将奥氏体不锈钢压力容器在常温进行应变强化水压试验,产生8%左右(最大10% )塑性变形,可提高奥氏体不锈钢材料的屈服强度和抗拉强度,通常称该方法为Avesta模式(Cold StretchedForming )。该压力容器使用介质一般为液氮、液氧和液氢等,主要民用。瑞典Avesta Sheffield公司从1959年开始,一直从事压力容器奥氏体不锈钢应变强化工作,并在很多国家申请了专利1。Avesta Sheffield公司1959年在瑞典通过特别许可,在经过了15年采用奥氏体不锈钢应变强化技术制造压力容器后,于1974年瑞典压力容器技术委员会通过压力容器奥氏体不锈钢应变强化技术, 1975年纳入压力容器专门标准应变强化压力容器标准2(Cold-stretching DirectionCSD)。1977年,瑞典、芬兰、挪威、德国、澳大利亚、荷兰、英国、西班牙、葡萄牙、捷克斯洛伐克及南非等国已接受压力容器奥氏体不锈钢应变强化技术3。瑞典应变强化压力容器标准CSD,使用材料相当于304和316L等,最大厚度30mm,最高使用温度400。退火态材料0. 2为210MPa左右,延伸率大于35%。强化后,屈服强度取k为410MPa左右,作为新材料,再按常规方法进行设计。应变强化水压试验压力由下式确定瑞典CSD标准指出,单向拉伸试样,最大10%应变足够保证该材料新的屈服强度k值。平面应力按Mises屈服准则计算,相应的应变按表1的比例关系计算。表1应力、应变比例关系瑞典CSD标准指出,为保证材料新的屈服强度k值,对于圆筒环向最大应变为8. 7%;球罐最大应变为5. 0%。瑞典标准规定最大应变为10. 0%。实际圆筒最大应变为3% 5%,主要原因: a.实际材料s比标准值偏大; b.实际板厚偏差及计算圆整后有余量; c.封头、接管等有强化作用。另一个值得重视的问题是, 1991年版的瑞典CSD标准不再需要保证材料新的屈服强度k值,只需按应变强化k计算所需压力进行水压试验即可。摒弃了1975年版根据k计算,需保证最小应变的要求。 Jonson J1指出,应变强化需保证材料组织稳定,不因应变产生马氏体。常用稳定和亚稳定奥氏体在少量应变条件下,不会产生马氏体。304L和316经过300350、2 000h时效试验表明,应变强化处理材料与未应变强化处理材料一样,屈服强度值和抗拉强度值变化较小,说明可提高应变强化的使用温度。应变强化处理材料后,550650蠕变性能仍很好,疲劳强度提高。低于10%应变强化处理材料,在弱氧化性介质如H2SO4中,腐蚀性与未应变强化处理材料一样;应力腐蚀结果也一样。另外, 304L、316钢的残余应力由于应变强化减少或消除,这一点已被应力腐蚀试验证实。 HesslingG4指出,应变强化可节省材料,随温度升高,节省材料量降低BrautigamM5指出,压力容器母材和焊条采用稳定奥氏体不锈钢材料304LN,当应变强化塑性应变量为20%时(包括强化后在液氮下使用),母材、焊缝和热影响区均未产生马氏体组织。321为亚稳定奥氏体, 20%应变明显产生马氏体;在液氦低温使用一年,未完成马氏体转变;在20、250次循环可加速马氏体转变,需考虑-196,循环对马氏体转变的影响。20%应变,对稳定奥氏体和亚稳定奥氏体材料冲击韧性均有影响;对于不产生马氏体稳定奥氏体材料冲击韧性的影响可能是由于晶体结构扭曲造成的。包括稳定奥氏体材料, 20%应变导致材料冲击韧性降低比低温影响更大; 20%应变后稳定奥氏体和亚稳定奥氏体材料在20、-196、-269时,其冲击韧性均能满足AD规范和ASME规范等;实际应变强化压力容器应变只有8% 10%,在低温液体中有足够的冲击韧性。Ambrose S61969年开始进行应变强化技术研究, 1969年首次制定规范ME/1/69-134应变强化压力容器(用于低温), 1999年纳入标准AS1210附录2。材料采用304、316L等;应变限制在5%,局部最大10%,比瑞典标准保守。限制5%,主要为了满足ISO/TC11(1970)的要求。应变强化方法具有3个优点: a.释放残余应力; b.在很多情况下改变形状,提高抗屈服能力; c.提高疲劳性能。欧盟低温压力容器标准EN13458附录C7采用应变强化技术,推荐了几种材料,也可使用其它稳定奥氏体和亚稳定奥氏体材料,但需满足相应的技术要求。材料最大厚度30mm,最高使用温度50,延伸率大于35%。退火态材料应变强化后,屈服强度k比0. 2最多增加200MPa左右。作为新材料,再按常规方法进行设计。应变强化所需水压试验压力为设计压力的1. 5倍,保证在使用过程中容器处于弹性状态。退火态容器强化时,变形量较大;材料已强化的容器(指加工过程无意中强化或板材轧制的有意强化),水压变形量较小。退火态容器最大容许10%应变,在较长时间保持载荷情况下,可容许增加1% 2%应变,实际上,一般圆筒为3% 5%应变。这样应变强化后材料仍能保持较高的延伸率和冲击韧性。RanaM D8介绍了ISO/TC220 2000关于低温奥氏体不锈钢容器,也接受应变强化方法,与EN13458基本一致。3奥氏体不锈钢压力容器低温应变强化Ardeform模式 1961年,Arde-Portland公司将退火态301奥氏体不锈钢容器,在?196(液氮)保温,进行应变强化水压试验,产生10%左右(最大13% )塑性变形,提高了301钢的屈服强度和抗拉强度,有的再经过427、20h时效处理,进一步提高301钢的屈服强度和抗拉强度9,通常称该方法为Ardeform模式(Cryogenic Stretch Forming)。该奥氏体不锈钢压力容器用于航天领域,使用介质为液氮、液氧和液氢等。Arde-Portland公司的Alper R H10对Arde-form模式性能进行较为详细的实验研究。同一尺寸的球(301钢),在?196经过应变强化,不经过时效处理,但在室温放置2h以上,在?196爆破时,屈服应力比应变强化应力有少量的升高,说明室温下也有一定时效作用;经过427、20h时效处理,屈服应力比应变强化应力有很大的升高,并随不同应变强化应力而不同;但两者爆破时应力较接近。退火态的球罐,在?196爆破时,屈服应力相当于材料在该温度下的屈服应力,这也是产生应变强化的起始应力;爆破时应力较低,但是考虑材料减薄,按真应力计算,爆破时应力与经过应变强化球的应力较一致。在常温下进行爆破实验,未经过时效处理的球屈服应力取决于球原先应变强化应力;经过时效处理的球屈服应力较高,爆破应力也较高。同时,采用光滑试样进行拉伸实验(单向应力),在?196,随应变强化应力增大,室温拉伸屈服强度和抗拉强度均增加;经过时效处理的试样比未经时效处理的试样有较高的屈服强度和抗拉强度。为了研究双向应力,采用带缺口试样进行拉伸实验,在?196,随应变强化应力增大,时效试样的屈服应力变化不大;未经时效处理试样的屈服应力增大;未经时效处理试样的屈服应力比原先强化时的应力增大,进一步说明室温有强化效应。在?196进行拉伸试验,缺口试样与光滑试样的抗拉强度比值,未经时效试样,随原先强化时的应力增大而增大;然而,经时效试样,随原先强化时的应力增大而减小。也就是随原先强化时的应力增大,缺口敏感性增加。对试验总结,得出以下结论: a.可采用低温强化提高强度,制造压力容器; b.未经时效的应变强化不锈钢,在?196有较高的缺口韧性; c.经时效的应变强化不锈钢,在?196和室温有较高的强度; d.能在?196产生应变强化,需要一定的应力。Arde-Portland公司的Henderson S W11指出:应变强化后再经过时效可提高强度;应变强化提高材料抗蠕变性能和缺口强度;未经时效的应变强化不锈钢,高温性能也较好。在屈服应力以下,在强氧化剂环境,抗腐蚀性能与退火态压力容器一致。总结应变强化主要优点:高强度;高蠕变强度;高缺口韧性;低温427时效不产生扭曲;提高可靠性,筒体变形12% 14%,球变形7% 8%,可检验射线未发现的缺陷;减少应力集中;对焊缝有利,使焊缝与母材一致;提高抗腐蚀性能。Arde-Portland公司的Arthur C12指出,Arde-form模式制造压力容器主要是由于无扩散型面心立方晶格转化为体心立方晶格,奥氏体转化为马氏体,并经过时效,进一步提高其室温强度。其成功应用在于3个重要因素: a.化学成分,使材料具有强度和韧性最好的组合,便于焊接; b.焊接,将产生1%的收缩,应变强化时,与母材强度一致,更为重要的是使焊缝部位圆滑过渡,这些按传统的方法不可能实现; c.设计,压力容器变形量取理论计算的变形量(前面已提到,这一点完全没必要,压力容器变形量只需要不大于压力容器理论计算的变形量即可)。另外应变强化,使容器向最自然的几何形状变化,如封头形状向球形变化。4 两种奥氏体不锈钢压力容器应变强化模式 比较表2比较两种奥氏体不锈钢应变强化模式。相对来说,Ardeform模式应变强化程度更大,对材料性能造成的不利影响也相对较大,其成本较高,工艺更复杂,由于主要用于航天领域13,报道较少。Avesta法已被许多欧洲国家接受, EN13458附录C已采用,有较多使用经验。表2奥氏体不锈钢压力容器应变强化模式比较5几种压力容器标准奥氏体不锈钢
- 温馨提示:
1: 本站所有资源如无特殊说明,都需要本地电脑安装OFFICE2007和PDF阅读器。图纸软件为CAD,CAXA,PROE,UG,SolidWorks等.压缩文件请下载最新的WinRAR软件解压。
2: 本站的文档不包含任何第三方提供的附件图纸等,如果需要附件,请联系上传者。文件的所有权益归上传用户所有。
3.本站RAR压缩包中若带图纸,网页内容里面会有图纸预览,若没有图纸预览就没有图纸。
4. 未经权益所有人同意不得将文件中的内容挪作商业或盈利用途。
5. 人人文库网仅提供信息存储空间,仅对用户上传内容的表现方式做保护处理,对用户上传分享的文档内容本身不做任何修改或编辑,并不能对任何下载内容负责。
6. 下载文件中如有侵权或不适当内容,请与我们联系,我们立即纠正。
7. 本站不保证下载资源的准确性、安全性和完整性, 同时也不承担用户因使用这些下载资源对自己和他人造成任何形式的伤害或损失。

人人文库网所有资源均是用户自行上传分享,仅供网友学习交流,未经上传用户书面授权,请勿作他用。