反力式汽车制动试验台设计
45页 25000字数+说明书+开题报告+4张CAD图纸【详情如下】
减速器壳体A0.dwg
制动试验台A0.dwg
反力式汽车制动试验台设计开题报告.doc
反力式汽车制动试验台设计说明书.doc
蜗杆A1.dwg
蜗轮A1.dwg
摘 要
汽车制动性能的检验是机动车安全技术检验的重要内容之一,随着我国汽车保有量快速增长,汽车对环境的影响受到人们的普遍关注。汽车制动性能的好坏直接关系到人们的生命安全。因此有必要研究出快捷、准确地检测汽车制动性能的方法和工具。本论文的内容就是对汽车制动试验台的关键技术进行研究。首先论文对国内外汽车制动试验台的现状和今后发展方向进行了综述。通过对汽车制动过程的分析,提出检测汽车制动性能的方法,比较了各种检测方法的特点,分析了评价汽车性能的指标及国家标准。对汽车在制动试验台上的受力情况进行了分析,提出检测汽车制动性能的原理,分析了影响制动性能检测的因素。对汽车制动试验台总体结构进行了分析,提出选择试验台滚筒尺寸,转速及表面材料的方法,给出选择试验台电机、减速器等主要部件的依据。
关键词:汽车制动试验台;制动性能;检测;滚筒;反力式
目 录
摘要………………………………………………………………………………………Ⅰ
Abstract………………………………………………………………………………Ⅱ
第1章 绪论……………………………………………………………………………1
1.1 课题研究的目的和意义…………………………………………………………1
1.1.1 课题研究的目的…………………………………………………………1
1.1.2 课题研究的意义…………………………………………………………1
1.2 国内外相关领域研究现状及发展方向…………………………………………2
1.2.1 平板式制动试验台………………………………………………………2
1.2.2 反力滚筒式制动试验台…………………………………………………3
1.2.3 发展方向…………………………………………………………………4
1.3 论文主要研究内容及技术途径…………………………………………………4
1.3.1 课题主要研究内容……………………………………………………… 4
1.3.2 技术途径与方法………………………………………………………… 4
第2章 反力式滚筒试验台与平板式试验台对比分析…………………………5
2.1 反力式滚筒制动性能试验台的结构及工作原理………………………………5
2.1.1 结构…………………………………………………………………… 5
2.1.2 工作原理…………………………………………………………………5
2.2 平板式制动性能试验台的结构及工作原理……………………………………6
2.2.1 平板式制动试验台结构…………………………………………………6
2.2.2 工作原理…………………………………………………………………6
2.3 反力式滚筒试验台与平板式试验台优缺点分析………………………………7
2.3.1 反力式滚筒试验台………………………………………………………7
2.3.2 平板式制动试验台………………………………………………………8
2.4 本章小结…………………………………………………………………………8
第3章 汽车制动试验台总体方案…………………………………………………9
3.1 引言……………………………………………………………………………9
3.2 汽车制动试验台总体构成………………………………………………………9
3.3 制动试验台工作原理……………………………………………………………12
3.4 制动试验台力学分析……………………………………………………………14
3.5 影响制动性能检测的因素分析…………………………………………………15
3.6 本章小结…………………………………………………………………………16
第4章 汽车制动试验台结构设计………………………………………………17
4.1 引言………………………………………………………………………………17
4.2 设计依据和要求 …………………………………………………………………17
4.3 滚筒设计…………………………………………………………………………18
4.4 滚筒式制动试验台测试能力分析………………………………………………21
4.5 制动力测量装置主要参数的选择………………………………………………22
4.6 减速箱设计及零件选择…………………………………………………………24
4.6.1 蜗轮蜗杆的设计…………………………………………………………24
4.6.2 轴的设计…………………………………………………………………27
4.7 本章小结…………………………………………………………………………28
结论………………………………………………………………………………………29
参考文献…………………………………………………………………………………30
致谢………………………………………………………………………………………31
附录………………………………………………………………………………………32
表4.1 汽车制动试验台主要技术参数
序号技术参数参数值
1允许最大轴载质量Kg10000
2测量范围N0-30000
3分辨率N10
4滚筒直径mm245
5滚筒长度mm1000
6滚筒中心距450
7滚筒转速r/min54
8电动机功率Kw11
9最大外形尺寸(长×宽×高)mm1150×950×720
10示值误差%±5
第1章 绪 论
1.1 课题研究的目的和意义
1.1.1 课题研究的目的
汽车制动试验台的结构参数对制动性能的测量结果有着重要关系。只有合理选择制动试验台的设计参数,才能提高试验台测试的准确性与可靠性,以及耐用性和使用经济性。本课题所研究的汽车制动试验台主要是检测各类中小型汽车(最大轴重10吨)的制动性能。应能同时对同一轴上的左右两个车轮进行测量。制动试验台主要结构有滚筒、电动机、减速器等。
1.1.2 课题研究的意义
汽车制动性能的检验是机动车安全技术检验的重要内容之一,也是汽车保修企业进行故障和调试修理的科学依据。近年来,随着不解体检在线检测技术的发展,汽车制动性能的检测与诊断己由经验定性型向仪器化的定量与定性相结合方向发展,由路试向台架检测发展。用制动试验台检测汽车的制动性能,不仅可以测出每个车轮的制动力和制动力协调时间,通过计算求出汽车的单位制动力。而且可以测出同一轴两车轮的制动力差和制动力上升时间差,制动器内部阻力和制动完全释放时间。这种方法可以免除用路试检测制动性能的一些弊病[1]。
汽车制动试验台的型式有滚筒式和平板式。平板式制动试验台在测试时,汽车要有一定的初速度,这就需要有助跑道。而滚筒式制动试验台则相反,其占地面积小,可以在台上对制动系边试验边调整,又便于分析故障,因此容易按使用部门所接受。滚筒式制动试验台的测试方法是:在汽车处于停火状态下,测定车轮的制动力或制动距离等与制动性能有关的参数。它又可分为反力式和惯性式。惯性式别动试验台是测每个车轮的制动距离,这种试验台的试验车速高,较接近于实际情况。但由于在国家规定的制动性能标准中没有车轮制动距离这一项,只有汽车制动距离的标准。如果将测试的车轮制动距离换算成整车制动距离,有一定误差,要使换算结果精确,需要作大量对比试验,而不同的车型都要有对比,这是较难做到的,因此惯性式制动试验台不容易被使用部门所接受。而反力式制动试验台的工作原理是当被检车辆驶上试验台后,车轮置于两滚筒之间,这时左、右两电机启动,带动滚筒旋转。当转速达到稳定值后,通知驾驶员迅速踏制动器(或拉手制动器),这时车轮的转速降低。车轮与滚筒之间产生了相对滑移,此时,与车辆制动力大小相等、方向相反的力作用在试验台上,由测力装置可测量出其值,并记录制动曲线。当车轮速度降低到某值时,为了减少轮胎磨损,电机自动停转。反力式制动试验台结构筒单,测试方便,耗电小,使用成本低。在国内外被广泛采用。我国的《机动车安全运行技术条件》中对台试车轮制动力也给予承认。因此,国内交通、公安车管部门广泛使用的几乎都是反力式制动试验台。
室内汽车制动试验台一般只根据一些检测数据判定汽车制动性能合格与否,至于故障原因往往无法予以诊断分析,这是目前检测技术存在的一个缺陷。随着科学技术的发展,应用先进技术对在用车辆实行技术状况监控与预测非常必要。在汽车制动检测制动方面,应用故障机理的解析技术确定和预测汽车制动状况的动态特性;应用诊断参数信息的识别和传感技术。建立故障模式;充分利用计算机技术,分析诊断多数信息,提高诊断精确度。开发预测故障专家系统,提高诊断预测水平,使车辆保持良好的技术状况,并将检测、诊断和预测融为一体,是今后汽车检测技术的发展方向。
1.2 国内外相关领域研究现状及发展方向
目前在我国的汽车制动性能检测中,普遍采用反力滚筒式制动试验台,而平板式制动试验台近几年开始引入我国。GB7258- 2004 《机动车运行安全技术条件》规定制动性能检测可用平板式制动试验台, 也可以使用反力式滚筒制动试验台。平板式制动试验台是在汽车运行状态下检测制动性能, 与汽车实际行驶中的制动相似, 是一种动态检测; 而反力式滚筒制动试验台是提高为测定作用在测力滚筒上车轮制动力的反力, 检测车辆制动性能的装置,是一种稳态检测方式[2]。下面分别介绍这两种试验台:
1.2.1 平板式制动试验台
早期的汽车检测设备,既有滚筒式又有平板式,由于当时还没有电子计算机,平板式检测设备的传感器和采样系统难以满足检测要求。但是,由于近年来电子技术的大量应用,平板式检测设备的数据采集系统(含各种传感器)都采用微电子技术和计算机控制。因此,新一代的平板式设备各方面的性能都有了质的飞跃。从原理上来看,平板式制动试验台是主动、动态的检测,它是在汽车行驶制动状态下进行检测的,只要保证力传感器能准确无误地把测试平板上受到的水平制动力与垂直力测量下来,平板式制动试验台就完全可以如实地把汽车制动过程(力系及变化)检测出来。平板式制动试验台具有以下优点:
(1)在测试平台的台面上。焊有由钢板冲压制成的钢网,具有远高于良好路面的
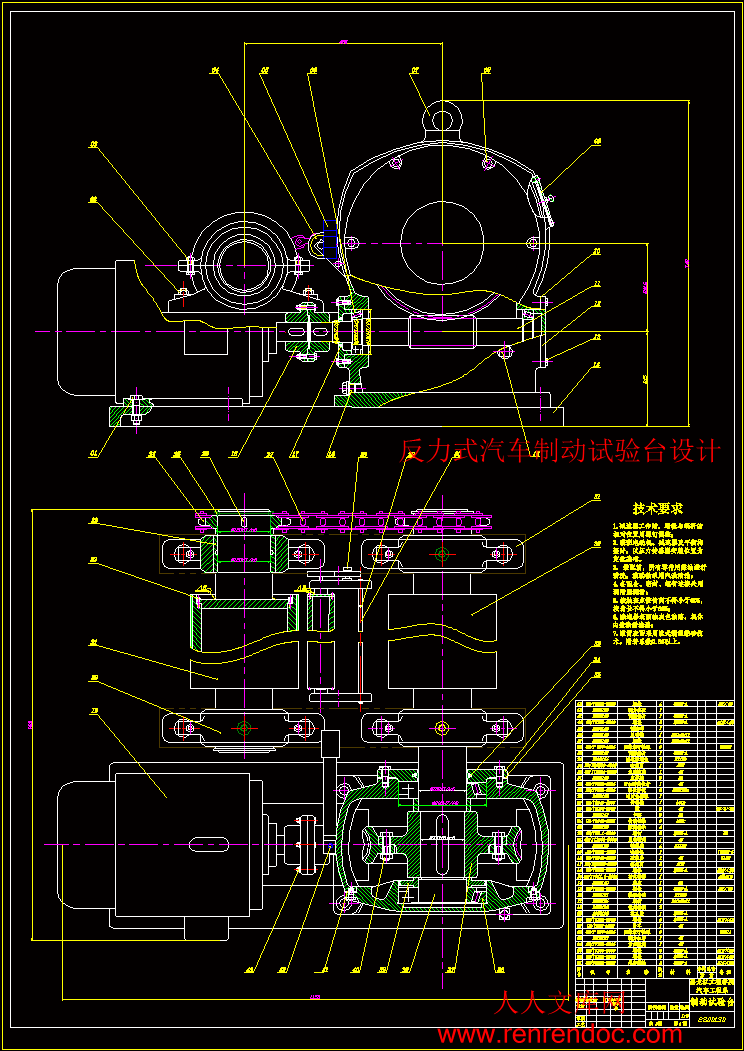
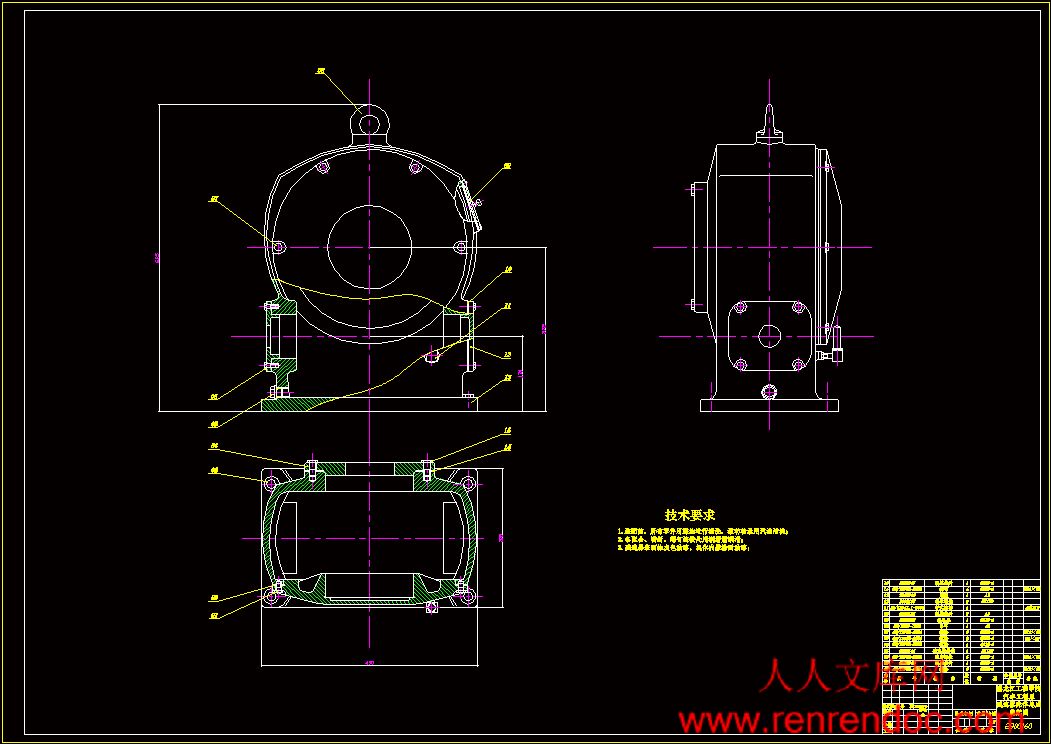