手机旅行充电器上夹板注塑模具设计
56页 18000字数+说明书+答辩稿+开题报告+11张CAD图纸
手机旅行充电器上夹板注塑模具设计开题报告.doc
手机旅行充电器上夹板注塑模具设计答辩稿.ppt
手机旅行充电器上夹板注塑模具设计说明书.doc
目录.doc
A0装配图.dwg
A1动模座版.dwg
A1动模板.dwg
A1定模座板.dwg
A1定模板.dwg
A2型腔.dwg
A3主流道固定 衬套.dwg
A3型芯.dwg
A3型芯镶块 斜导柱.dwg
A3导套 导柱.dwg
A3导滑槽.dwg
手机旅行充电器上夹板注塑模具
目 录
摘 要……………………………………………………………………1
ABSTRACT……………………………………………………………...2
第一章 绪论……………………………………………………………..3
第二章 拟定模具结构形式……………………………………………5
2.1确定型腔数量及排列方式 ………………………………………5
2.1.1 塑件成型工艺性分析 ………………………………………5
2.1.2 脱模斜度 ……………………………………………………6
2.1.3 型腔数目及排列方式 ……………………………………6
2.2 模具结构形式的确定…………………………………………….8
第三章 注射机型号的确定……………………………………………8
3.1 注射量的计算 …………………………………………………8
3.2 塑件和流道凝料在分型面上的投影面积及所需锁摸力……8
3.3 注射机有关参数的校核 ………………………………………9
第四章 分型面位置的确定 …………………………………………10
第五章 浇注系统形式和浇口的设计…………………………………12
5.1 主流道设计……………………………………………………12
5.1.1 主流道尺寸…………………………………………………12
5.1.2 主流道衬套的形式…………………………………………13
5.1.3 主流道剪切速率校核………………………………………13
5.1.4 主流道衬套的固定…………………………………………14
5.2 分流道设计……………………………………………………14
5.2.1 分流道的布置形式…………………………………………14
5.2.2 分流道长度…………………………………………………15
5.2.3 分流道的形状、截面尺寸以及凝料体积…………………15
5.3 浇口的设计……………………………………………………17
5.4 排气槽的设计…………………………………………………18
第六章 模架的确定……………………………………………………19
第七章 成型零件的设计与计算………………………………………21
7.1 成型零件钢材选用……………………………………………21
7.2 凹模的结构设计………………………………………………22
7.3 凸模的结构设计………………………………………………22
7.4 成型零件工作尺寸的计算……………………………………23
7.5 模具强度的校核………………………………………………30
7.5.1 整体式矩形型腔侧壁厚度计算 …………………………30
7.5.2 整体式矩形型腔底板厚度计算……………………………32
第八章 导向机构的设计 ……………………………………………33
8.2 导柱导向机构…………………………………………………33
8.1.1 导柱…………………………………………………………33
8.1.2 导套 ………………………………………………………35
第九章 脱模机构、复位机构的设计…………………………………37
9.1 推出机构的组成 ………………………………………………37
9.2 本模具的推出机构 ……………………………………………39
9.3 脱模阻力的计算 ………………………………………………40
9.4 复位机构设计 …………………………………………………41
第十章 侧向分型与抽芯机构的设计 ………………………………42
10.1 抽拔距与抽拔力及机构组成 ………………………………42
10.1.1 抽拔距 ……………………………………………………42
10.1.2 抽拔力 ……………………………………………………43
10.1.3 斜导柱驱动的结构组成 …………………………………44
10.2 斜导柱的长度和最小开模行程的计算 ……………………47
10.3 斜导柱的受力分析 …………………………………………48
第十一章 总结…………………………………………………………50
参考文献………………………………………………………………..51
致谢……………………………………………………………………..53
附件
摘 要
通过对手机旅行充电器夹板工艺的正确分析,设计了一副一模四腔的塑料模具。在本套模具设计过程中详细地叙述了模具成型零件包括定模板、前模仁、动模板、后模仁、镶块、导杆、斜导柱、滑块等的设计过程,重要零件的工艺参数的选择与计算,及推出机构、浇注系统以及侧向分型、抽芯机构的设计过程,利用当今业界广泛应用的绘图软件pro/E、AutoCAD分析了各方案可行性,并绘出了整套模具,并对成型零件进行了计算。分析并选择了各个成型零件的材料,对其刚度,强度进行了校核,并对试模与产品缺陷作了介绍,最后进行了对模具工艺性与经济性分析。
关键词:侧向分型;多型腔。
采用CAD技术设计塑料模具,设计者能够在电脑上直接建立产品的三维模型,在计算机上对整个注塑成型过程进行模拟分析,准确预测熔体的填充,保压,冷却情况,以及制品中的应力分布,分子和纤维取向分布,制品的收缩和翘曲变形等情况,不仅能快速提高设计效果,还可动态仿真分析在注塑模腔内的注射过程流动情况,分析温度压力变化情况等,检查模具结构的合理性,流动状态的合理性,以便设计者能尽早发现问题,及时修改制件和模具设计,将错误消除在设计阶段,而不是等到试模以后再返修模具,从而提高一次试模成功率,避免模具返修报废,保证质量,降低成本.模具中许多标准件都可采用CAD造型设计方法进行设计,既可实现数据共享,又可满足用户的随时修改,使模具的设计分析快速,准确,高效.这是模具设计方法的突破,具有重大的技术经济意义.
近年来,为提升竞争力,我国许多塑模企业纷纷加大了对模具制造的投入,引入新技术,建立制造中心,但CAD技术使用仍不广泛,这使过内高档,精密,大型塑料模具生产严重不足,造成这些模具每年仍需大量进口,但技术含量不高的中低档塑料模具却供过于求.
纵观发达国家的塑模生产,早已实现了无图化,靠CAD/CAE/CAM等电脑设计方法,实现了精密快速的模具生产模式,CAD技术已经形成了巨大的生产力.改革传统的设计理念和运行模式,以先进的CAD/CAE/CAM技术改造传统技术,提高塑料模具设计制造水平,赢是我国塑料模具企业改变现行产品结构的必然趋势.
为了做好这次毕业设计,本人查阅了大量模具设计与制造方面的相关资料,再结合以前课堂上所学的知识,本人对模具的设计有了一定程度的了解.
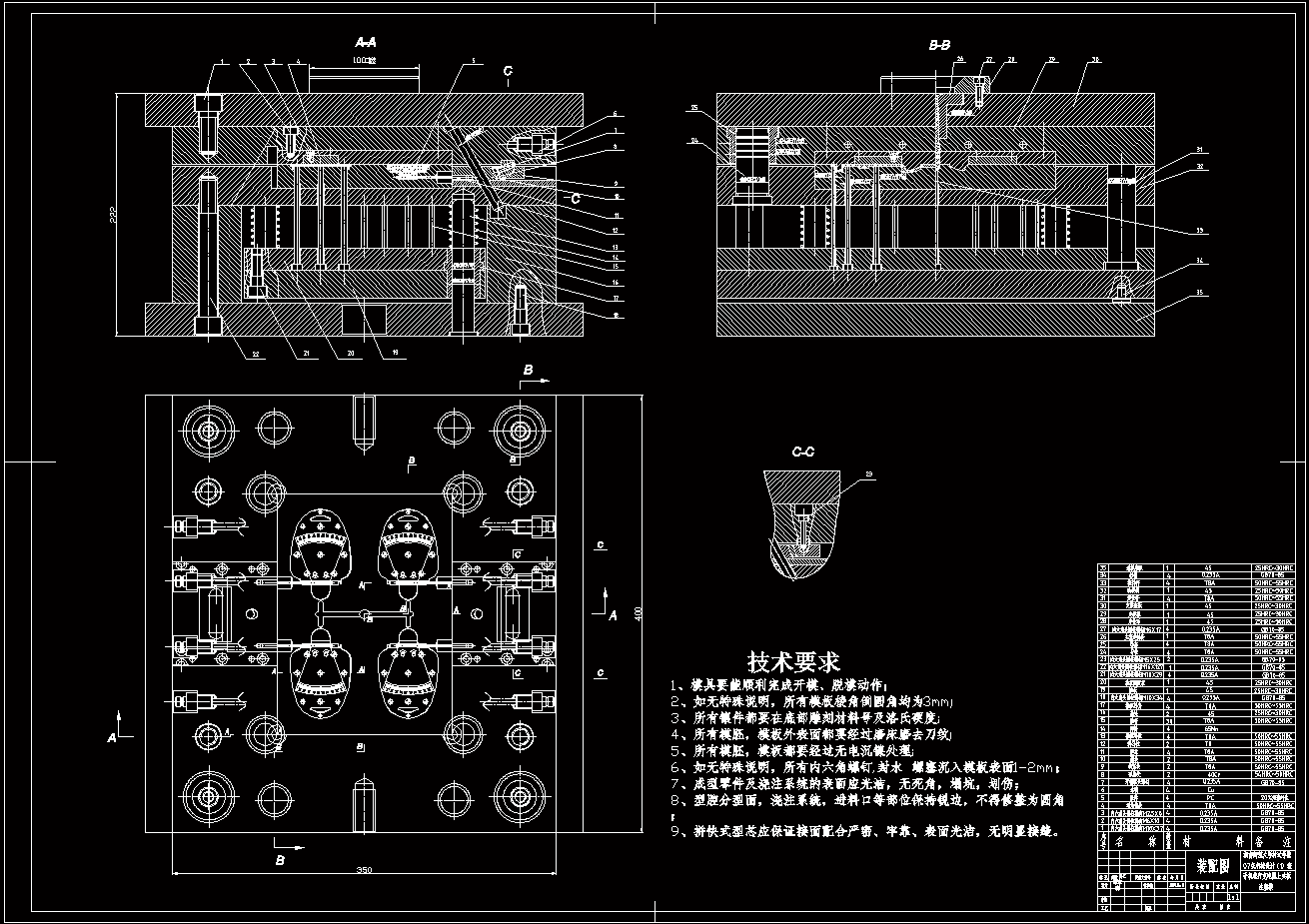
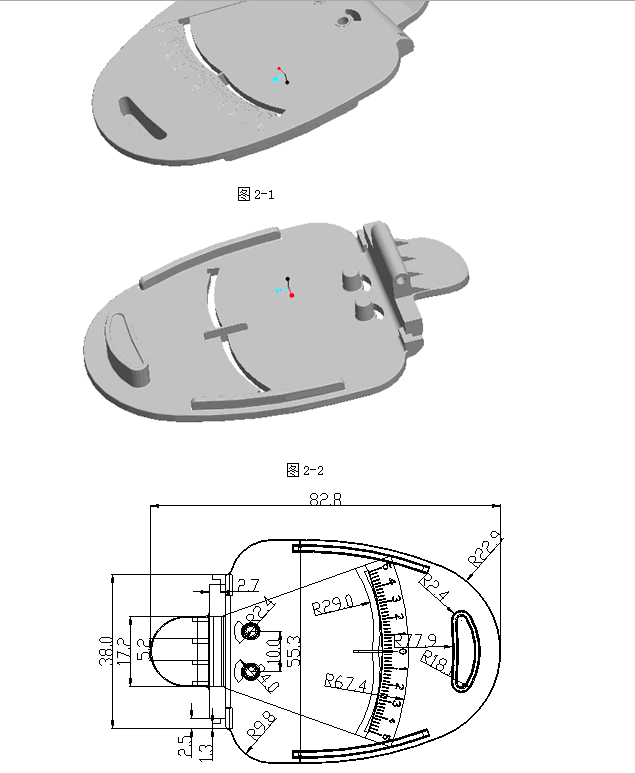